What Does Smd Mean In Text

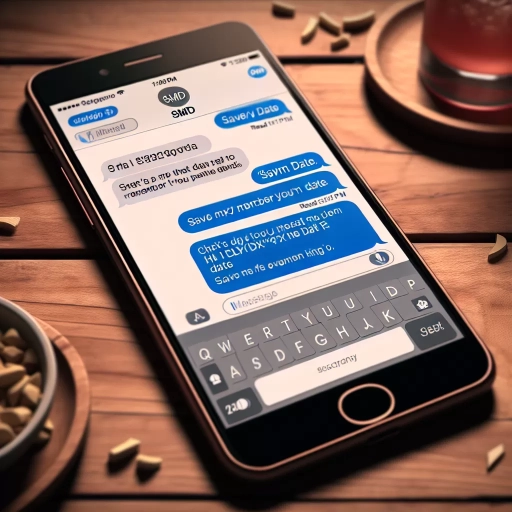
In the realm of modern electronics, the acronym SMD stands for Surface Mount Device, a term that has revolutionized the way electronic components are integrated into circuits. SMDs have become a cornerstone in the manufacturing of electronic devices, from smartphones and laptops to medical equipment and automotive systems. To fully appreciate the significance of SMDs, it is essential to delve into their fundamental principles, technical intricacies, and widespread applications. This article will explore the basics of SMDs, including their design and functionality, followed by a detailed examination of their technical aspects, such as soldering techniques and component specifications. Additionally, we will discuss the diverse applications and the profound impact SMDs have had on various industries. By understanding these facets, readers will gain a comprehensive insight into how SMDs have transformed the landscape of electronics. Let us begin by understanding the basics of SMDs, which form the foundation of their widespread adoption and innovative use.
Understanding the Basics of SMD
In the realm of modern electronics, Surface Mount Devices (SMDs) have revolutionized the way we design and manufacture electronic circuits. These tiny components, which are mounted directly onto the surface of a printed circuit board (PCB), have become indispensable in today's technology. To fully appreciate the significance of SMDs, it is crucial to delve into their definition and origin, understanding how they evolved from traditional through-hole components. Additionally, exploring their common usage in various texts and technical literature provides insight into their widespread adoption across different industries. Historical context is also vital, as it reveals the transformative impact SMDs have had on the electronics industry over the years. By examining these aspects, we can gain a comprehensive understanding of the basics of SMDs and their integral role in modern electronics. In this article, we will explore these key areas to provide a thorough understanding of SMDs, transitioning seamlessly into the core topic: Understanding the Basics of SMD.
Definition and Origin
**Definition and Origin** Surface Mount Devices (SMDs) are a cornerstone of modern electronics, revolutionizing the way components are integrated into circuit boards. The term "SMD" refers to electronic components that are mounted directly onto the surface of a printed circuit board (PCB) using soldering techniques, as opposed to the older through-hole technology where components were inserted into holes drilled in the board. This innovative approach has significantly reduced the size and weight of electronic devices, enhanced their reliability, and increased their performance. The origin of SMDs dates back to the 1960s when the first surface mount components were developed. However, it wasn't until the 1980s that SMD technology began to gain widespread acceptance and implementation. The driving force behind this shift was the need for miniaturization and improved manufacturing efficiency. As consumer electronics demanded smaller, lighter, and more powerful devices, manufacturers turned to SMDs as a solution. Today, SMDs are ubiquitous in everything from smartphones and laptops to automotive systems and medical devices. The definition of SMD encompasses a wide range of components including resistors, capacitors, inductors, diodes, transistors, and integrated circuits. These components are designed with flat leads or terminations that allow them to be soldered directly onto the PCB's surface. This design not only reduces the physical footprint but also simplifies the assembly process by eliminating the need for drilling holes. The use of SMDs has also led to advancements in automated assembly lines, further increasing production speed and reducing costs. Understanding the basics of SMDs is crucial for anyone involved in electronics design, manufacturing, or repair. Knowing how these components work and how they are integrated into PCBs can help engineers optimize their designs for better performance and reliability. Additionally, familiarity with SMDs is essential for troubleshooting and repairing modern electronic devices, where these components are often the heart of the system. As technology continues to evolve, the role of SMDs will remain pivotal in enabling the creation of smaller, smarter, and more efficient electronic devices.
Common Usage in Text
In the realm of digital communication, particularly in text messaging, social media, and online forums, "SMD" stands for "Sick My Dude," a slang term that has gained widespread usage. This acronym is often employed to express sympathy or solidarity with someone who is going through a tough time. For instance, if a friend shares news about a personal loss or a challenging situation, responding with "SMD" conveys empathy and support in a concise yet meaningful way. The term has become an integral part of internet culture, allowing users to quickly acknowledge and validate each other's emotions without needing to type out lengthy messages. The common usage of "SMD" highlights the evolving nature of language in the digital age. As communication becomes increasingly fast-paced and abbreviated, terms like "SMD" fill the gap by providing a shorthand way to convey complex emotions. This phenomenon is part of a broader trend where acronyms and abbreviations are used to streamline interactions, making them more efficient and accessible. For example, other popular abbreviations such as "LOL" (Laugh Out Loud) and "TBH" (To Be Honest) serve similar purposes, each contributing to a unique lexicon that is both informal and expressive. Understanding the basics of SMD and other such terms is crucial for effective communication in today's digital landscape. It not only helps in deciphering messages accurately but also fosters a sense of community and shared understanding among users. By recognizing and using these abbreviations appropriately, individuals can navigate online interactions with greater ease and build stronger connections with their peers. Moreover, being familiar with these terms can help bridge the gap between different age groups and cultural backgrounds, promoting a more inclusive and dynamic online environment. In summary, "SMD" is more than just an acronym; it represents a shift in how we communicate emotions and empathy in the digital era. Its widespread usage underscores the importance of staying updated with contemporary slang to ensure clear and meaningful interactions. As technology continues to shape our language, understanding terms like "SMD" becomes essential for anyone looking to engage fully in online discourse. By embracing these abbreviations, we can enhance our communication skills and foster deeper connections within the digital community.
Historical Context
Understanding the historical context of Surface Mount Devices (SMDs) is crucial for appreciating their significance and evolution in modern electronics. The journey of SMDs began in the 1960s, a period marked by rapid advancements in semiconductor technology and the need for more compact, efficient, and reliable electronic components. Initially, through-hole technology dominated the industry, where components were mounted on printed circuit boards (PCBs) using wire leads that passed through holes drilled in the board. However, this method had limitations, particularly in terms of space efficiency and manufacturing speed. The advent of SMDs revolutionized this landscape by allowing components to be mounted directly onto the surface of PCBs without the need for through-holes. This innovation was driven by the development of new materials and manufacturing techniques. In the 1970s and 1980s, SMDs started gaining traction due to their smaller size, lower weight, and improved thermal performance compared to traditional through-hole components. These advantages made SMDs ideal for applications requiring high density and miniaturization, such as in consumer electronics, automotive systems, and aerospace. The widespread adoption of SMDs was further accelerated by advancements in pick-and-place machines and reflow soldering techniques. These technological improvements enabled mass production with high precision and speed, making SMDs more cost-effective and accessible. By the 1990s, SMDs had become the standard in electronic manufacturing, transforming the way electronic devices were designed and built. Today, SMDs are ubiquitous in virtually all electronic products, from smartphones and laptops to medical devices and industrial control systems. The historical context also highlights the collaborative efforts between industry leaders, researchers, and manufacturers that drove these innovations. Standards organizations like the Institute for Printed Circuits (IPC) played a pivotal role in establishing guidelines for SMD design, manufacturing, and quality control. This collaborative environment ensured that SMD technology evolved consistently with industry needs, leading to the sophisticated and diverse range of SMDs available today. In summary, understanding the historical context of SMDs provides a rich backdrop for appreciating their impact on modern electronics. From their inception as a response to technological limitations to their current status as a cornerstone of electronic manufacturing, SMDs have revolutionized how we design, build, and use electronic devices. This historical perspective not only underscores the importance of SMDs but also serves as a foundation for exploring their technical aspects and applications in greater depth.
Technical Aspects of SMD
In the realm of modern electronics, Surface Mount Devices (SMDs) have revolutionized the way components are integrated into circuit boards. These tiny components offer a plethora of benefits over traditional through-hole technology, making them a cornerstone in contemporary electronic design. To fully appreciate the advantages of SMDs, it is crucial to delve into their technical aspects. This article will explore three key areas: **Component Types and Sizes**, which highlights the diverse range of SMD components available and their varying dimensions; **Mounting and Soldering Techniques**, which discusses the specialized methods required for securely attaching these components to PCBs; and **Advantages Over Through-Hole Technology**, which elucidates the significant improvements SMDs bring in terms of space efficiency, performance, and manufacturing ease. By understanding these technical facets, readers will gain a comprehensive insight into the world of SMDs, setting the stage for a deeper exploration of **Understanding the Basics of SMD**.
Component Types and Sizes
In the realm of Surface Mount Devices (SMDs), component types and sizes play a crucial role in the design, functionality, and reliability of electronic circuits. SMDs are categorized into various types based on their form factor, functionality, and application. One of the primary distinctions is between passive and active components. Passive components, such as resistors, capacitors, and inductors, do not require an external power source to operate and are often smaller in size compared to their through-hole counterparts. For instance, resistors come in sizes like 0201 (0.02 inches by 0.01 inches), 0402, 0603, and 0805, with each size denoting specific dimensions that cater to different design requirements. Active components, including integrated circuits (ICs), transistors, and diodes, require an external power source to function. These components are available in various package types such as QFN (Quad Flat No-Lead), TSSOP (Thin Shrink Small Outline Package), and BGA (Ball Grid Array). The choice of package type depends on factors like thermal dissipation, signal integrity, and space constraints. For example, BGAs are preferred for high-pin-count devices due to their compact footprint and superior thermal performance. The size of SMD components is critical for modern electronics design. Smaller components enable more compact board designs, which are essential for portable devices like smartphones and wearables. The 0201 resistor, for instance, is one of the smallest SMD resistors available, measuring just 0.02 inches by 0.01 inches. This miniaturization allows for higher component density on PCBs (Printed Circuit Boards), thereby reducing overall board size and weight. Moreover, the precision in component sizes is vital for automated assembly processes. Pick-and-place machines rely on accurate component dimensions to ensure correct placement during the manufacturing process. Any deviation in size can lead to misalignment or failure during assembly, highlighting the importance of precise component specifications. In addition to size, the type of component also influences the manufacturing process. Components with lead-free terminations are becoming increasingly popular due to environmental regulations like RoHS (Restriction of Hazardous Substances). These lead-free components require specific soldering profiles to ensure reliable joints, adding another layer of complexity to the manufacturing process. Understanding the various types and sizes of SMD components is essential for engineers and designers to optimize their designs for performance, reliability, and cost-effectiveness. By selecting the appropriate component type and size, designers can create more efficient, compact, and reliable electronic systems that meet the demands of modern technology. This knowledge also facilitates better communication between designers, manufacturers, and suppliers, ensuring that the final product meets all specifications and quality standards. In summary, the diversity in SMD component types and sizes offers a wide range of possibilities for electronic design, making it crucial to grasp these technical aspects to leverage the full potential of surface mount technology.
Mounting and Soldering Techniques
**Mounting and Soldering Techniques** In the realm of Surface Mount Devices (SMD), mounting and soldering techniques are crucial for ensuring the reliability and performance of electronic assemblies. SMDs, which stand for Surface Mount Devices, are components that are mounted directly onto the surface of a printed circuit board (PCB) without the need for through-hole mounting. The precision required in handling these tiny components necessitates specialized techniques. **Mounting Techniques:** 1. **Pick-and-Place Machines:** These automated systems are widely used in mass production to accurately place SMDs onto PCBs. They offer high speed and precision, significantly reducing human error. 2. **Manual Placement:** For smaller batches or prototyping, manual placement using tweezers or vacuum pickers is common. This method requires careful handling to avoid damaging the components. 3. **Stencil Printing:** A solder paste stencil is used to apply the correct amount of solder paste onto the PCB pads before component placement. This ensures uniform solder joints. **Soldering Techniques:** 1. **Reflow Soldering:** This is the most common method for SMDs. The PCB is heated in a reflow oven, causing the solder paste to melt and form strong bonds between the components and the PCB. 2. **Wave Soldering:** Although less common for SMDs, wave soldering can be used for mixed technology boards that include both through-hole and surface mount components. 3. **Hand Soldering:** For repair or small-scale production, hand soldering with a soldering iron is used. This requires skill and attention to detail to avoid overheating or damaging the components. **Key Considerations:** - **Thermal Profiles:** Ensuring the correct thermal profile during reflow soldering is critical to prevent component damage and ensure reliable solder joints. - **Solder Paste Quality:** The quality of the solder paste directly affects the reliability of the solder joints. It must be stored properly and used within its shelf life. - **Component Handling:** Static electricity can damage SMDs. Using anti-static equipment and following proper handling procedures are essential. By mastering these mounting and soldering techniques, manufacturers can produce high-quality electronic assemblies that meet stringent reliability standards. The precision and care involved in these processes underscore the importance of understanding the technical aspects of SMDs in modern electronics manufacturing.
Advantages Over Through-Hole Technology
The transition from through-hole technology to Surface Mount Technology (SMT) has revolutionized the electronics manufacturing industry, offering numerous advantages that enhance both the performance and efficiency of electronic devices. One of the most significant benefits of SMT is the dramatic reduction in size and weight of components. By mounting components directly onto the surface of a printed circuit board (PCB), SMT allows for much denser packaging compared to through-hole technology, where components are inserted into holes drilled in the PCB. This compact design enables the creation of smaller, lighter, and more portable electronic devices, which is particularly crucial in modern consumer electronics such as smartphones, laptops, and wearable technology. Another key advantage of SMT is its improved electrical performance. Surface mount components have shorter lead lengths, which reduce inductance and capacitance, leading to faster signal propagation and lower electromagnetic interference (EMI). This results in higher speed and reliability of the circuit, making SMT ideal for high-frequency applications like telecommunications and computing. Additionally, the smaller size of SMT components reduces thermal resistance, allowing for better heat dissipation and increased reliability under various environmental conditions. From a manufacturing perspective, SMT offers significant cost savings and increased production efficiency. The automated assembly process used in SMT is much faster than manual insertion required for through-hole components. This automation not only speeds up production but also reduces labor costs and minimizes human error, leading to higher quality and consistency in the final product. Furthermore, the use of reflow soldering in SMT allows for simultaneous soldering of all components on a PCB, streamlining the manufacturing process and reducing overall production time. In terms of design flexibility, SMT provides engineers with greater freedom to innovate. With the ability to mount components on both sides of the PCB and use smaller footprints, designers can create more complex and sophisticated circuits within a smaller space. This flexibility is essential for developing advanced electronic systems that require multiple functionalities while maintaining a compact form factor. Lastly, SMT enhances environmental sustainability by reducing material usage and waste generation. The smaller size of SMT components means less material is required for their manufacture, and the automated assembly process minimizes waste during production. This aligns with modern industry trends towards more sustainable and eco-friendly manufacturing practices. In summary, the advantages of SMT over through-hole technology are multifaceted, encompassing improvements in size, electrical performance, manufacturing efficiency, design flexibility, and environmental sustainability. These benefits collectively contribute to the widespread adoption of SMT in contemporary electronics manufacturing, enabling the development of more advanced, reliable, and compact electronic devices.
Applications and Impact of SMD
The advent of Surface Mount Devices (SMDs) has revolutionized the electronics industry, transforming the way we design, manufacture, and integrate electronic components. These tiny yet powerful devices have become ubiquitous in various sectors, driving innovation and efficiency. In this article, we will delve into the applications and impact of SMDs across three critical areas: **Electronic Devices and Gadgets**, where SMDs have enabled the creation of sleek, compact, and high-performance consumer electronics; **Industrial and Automotive Uses**, where they enhance reliability and durability in demanding environments; and **Future Trends and Innovations**, exploring how SMDs are shaping the next generation of technological advancements. By understanding these diverse applications, we can appreciate the profound impact SMDs have on modern technology. To fully grasp the significance of these advancements, it is essential to start with **Understanding the Basics of SMD**, which will provide a foundational knowledge necessary for appreciating their widespread influence and future potential.
Electronic Devices and Gadgets
The proliferation of electronic devices and gadgets has revolutionized modern life, transforming how we communicate, work, and entertain ourselves. At the heart of this technological advancement lies Surface Mount Devices (SMDs), which have significantly enhanced the performance, efficiency, and miniaturization of electronic components. SMDs are crucial in the production of smartphones, laptops, smart home devices, and wearable technology. These tiny components enable the creation of compact yet powerful devices that are integral to daily life. For instance, smartphones rely on SMDs to pack a multitude of features such as high-resolution cameras, GPS navigation, and advanced processors into a single handheld device. Similarly, smart home gadgets like smart thermostats and security systems leverage SMDs to offer real-time monitoring and control capabilities. The impact of SMDs extends beyond consumer electronics; they are also vital in medical devices, automotive systems, and industrial automation. In healthcare, SMDs are used in portable diagnostic equipment and implantable devices like pacemakers, improving patient care and outcomes. In the automotive sector, SMDs enhance vehicle safety features such as airbag systems and anti-lock braking systems (ABS). Furthermore, industrial automation relies on SMDs for precise control and monitoring of manufacturing processes. The miniaturization facilitated by SMDs has also led to the development of Internet of Things (IoT) devices, which interconnect various aspects of our lives through a network of sensors and actuators. Overall, the applications and impact of SMDs are far-reaching, driving innovation across multiple industries and enriching our daily experiences with smarter, more efficient technology. As technology continues to evolve, the role of SMDs will remain pivotal in shaping the future of electronic devices and gadgets.
Industrial and Automotive Uses
In the realm of industrial and automotive applications, Surface Mount Devices (SMDs) have revolutionized the landscape with their compact size, enhanced performance, and cost-effectiveness. These tiny components, which include resistors, capacitors, inductors, and integrated circuits, are pivotal in modern manufacturing due to their ability to miniaturize complex electronic systems. In industrial settings, SMDs enable the development of more efficient and reliable control systems. For instance, they are integral in the design of programmable logic controllers (PLCs) that manage and automate various industrial processes such as manufacturing lines, power distribution systems, and HVAC controls. The reduced footprint of SMDs allows for denser circuitry, which in turn increases the processing power and reduces the overall size of these control units. In the automotive sector, SMDs play a crucial role in enhancing vehicle safety, efficiency, and comfort. Modern vehicles rely heavily on sophisticated electronic systems for functions such as anti-lock braking systems (ABS), traction control systems (TCS), and advanced driver-assistance systems (ADAS). SMDs are used extensively in these systems due to their high reliability under harsh environmental conditions like extreme temperatures and vibrations. Additionally, they facilitate the integration of advanced features such as infotainment systems, navigation, and telematics. The use of SMDs also contributes to fuel efficiency by enabling the development of more precise engine control units (ECUs) that optimize fuel injection and ignition timing. Moreover, the automotive industry benefits from the reduced weight and increased durability offered by SMDs. This is particularly important as vehicle manufacturers strive to meet stringent emissions regulations while maintaining performance standards. The compact nature of SMDs allows for more flexible design options, enabling engineers to create complex electronic circuits within the limited space available in modern vehicles. Furthermore, the high-speed signal processing capabilities of SMDs support real-time data analysis essential for autonomous driving technologies. The impact of SMDs extends beyond functional improvements; they also contribute significantly to cost savings and environmental sustainability. By reducing the size and weight of electronic components, manufacturers can lower production costs associated with material usage and assembly processes. Additionally, the energy efficiency inherent in SMD designs helps reduce power consumption, which is critical for both industrial equipment and automotive systems. This not only minimizes operational costs but also aligns with global efforts to reduce carbon footprints and promote sustainable practices. In summary, SMDs have become indispensable in industrial and automotive applications by offering unparalleled advantages in terms of size, performance, reliability, and cost. Their widespread adoption has driven innovation across various sectors, enabling more efficient, safer, and environmentally friendly technologies that shape the future of both industries. As technology continues to evolve, the role of SMDs will only become more pivotal in driving advancements that meet the demanding needs of modern industrial and automotive applications.
Future Trends and Innovations
As we delve into the applications and impact of Surface Mount Devices (SMDs), it is crucial to explore the future trends and innovations that are set to revolutionize this field. The landscape of SMD technology is evolving at a rapid pace, driven by advancements in materials science, nanotechnology, and artificial intelligence. One of the most significant trends is the miniaturization of components, enabling the creation of smaller, more efficient devices. This trend is particularly evident in the development of micro-SMDs and nano-SMDs, which are poised to play a critical role in next-generation electronics such as wearable technology, IoT devices, and autonomous vehicles. Another key innovation is the integration of 3D printing techniques into SMD manufacturing. This allows for the rapid prototyping and production of complex geometries that were previously unfeasible with traditional methods. Additionally, advancements in flexible electronics are opening up new avenues for SMD applications in areas like biomedical devices and smart textiles. The incorporation of AI and machine learning algorithms into SMD design and manufacturing processes is also gaining traction, enabling real-time optimization and predictive maintenance capabilities. Sustainability is another critical aspect driving future trends in SMDs. There is a growing focus on using eco-friendly materials and reducing electronic waste through design-for-recyclability approaches. This shift towards green electronics not only aligns with global environmental goals but also offers significant cost savings and brand differentiation opportunities for manufacturers. Furthermore, the rise of Industry 4.0 and smart manufacturing is transforming how SMDs are produced and integrated into larger systems. Automated assembly lines equipped with advanced robotics and vision systems are enhancing precision and throughput while reducing labor costs. The integration of SMDs with other emerging technologies such as quantum computing and 5G networks will further amplify their impact across various sectors including healthcare, aerospace, and consumer electronics. In conclusion, the future of SMDs is marked by exciting innovations that promise to enhance performance, reduce size, and improve sustainability. As these trends continue to unfold, they will have profound implications for the applications and impact of SMDs across diverse industries, shaping the technological landscape of tomorrow. By embracing these advancements, manufacturers can stay ahead of the curve and unlock new possibilities for innovation and growth.