What Is A Lathe

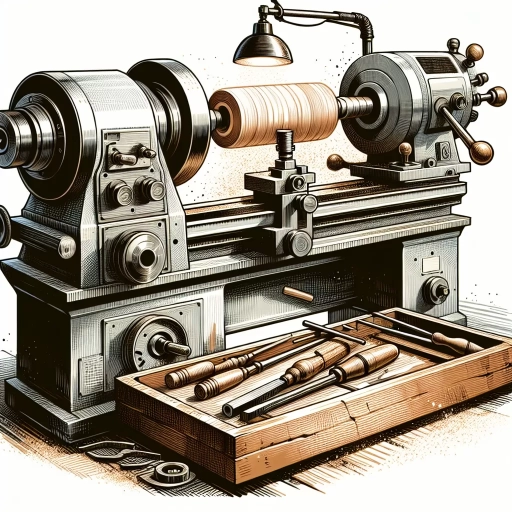
Introduction to Lathes
Lathes, powerful and versatile machines, are intriguing subjects to explore, significant to various facets of engineering and manufacturing. This article aims to delve into the world of lathes, offering a comprehensive introduction to their origin, core components, and the different types available today. We will begin by whisking you through time, highlighting the historical background of lathes, an immersive tale bursting with human innovation and discovery. Next, an in-depth examination of the basic components that make up a lathe follows, spotlighting the nuts and bolts of these engineering marvels. Lastly, an exploration of the various types of lathes awaits. Be it for metalworking, woodworking, or watchmaking, each lathe variant is unique in its functionality, demanding a closer look. So, buckle up for this intriguing journey. Let us now shift gears and commence our voyage by stepping back in history, looking into the fascinating historical background of this groundbreaking invention, the lathe.
Historical Background of Lathes
The history of lathes predates modern civilization and can be traced back to ancient times. Originally, this versatile tool was primarily used for woodworking. Ancient Egyptians leveraged it around 1300 BC to shape symmetrical objects. Their rudimentary design comprised two horizontal poles, tethered by a cord that spun the workpiece. The worker would then use a sharp tool to carve the spinning object, effectively laying down the founding principles of turning and creating a blueprint for future lathes. The Roman Empire, known for its advanced engineering feats, significantly improved the design of the lathe by incorporating a turning bow, which amplified operational efficiency. The Middle Ages brought significant strides in the evolution of lathes. The pole lathe, with its foot pedal, was a groundbreaking intervention – the foot pedal enabled the artisan to control the rotation of the workpiece with their foot, thereby freeing both hands for more precise work. During the industrial revolution in the 18th and 19th centuries, lathes morphed from a manually manipulated apparatus to a mechanically driven machine, courtesy of the steam engine power run by belts. It was Henry Maudslay's extraordinary invention in 1797, a screwed cutting lathe, which revolutionized the machinery industry. He innovatively incorporated a lead screw, which facilitated precision in workpiece advancement. The advent of the 20th century ushered in an era of electric motor-powered lathes, which offered simpler usage, increased productivity, and improved precision. In 1952, the numerical control (NC) lathe was developed by John Parsons and Frank Stulen, symbolizing a transformational leap in lathe automation. Following the path laid by NC lathes, computer numerical control (CNC) lathes arrived in the 1970s. The integration of computer technology within lathes empowered operators to program precise, complex designs directly into the machinery, enhancing production speed, consistency, and accuracy. Today, modern lathes have evolved remarkably from their ancient counterparts, boasting computerized control, automatic feed mechanisms, varied speed ranges, and the capability to produce complex shapes with extreme precision. They continue to be indispensable in various industries, from crafts to automobile production, reflecting the timeless relevance of this innovative machine. Every iteration of the lathe's historical timeline implies the ceaseless pursuit of human ingenuity to refine technology for making work easier and efficient. As we delve deeper into the era of advanced manufacturing, lathes will continue to be a pillar in the machinery industry, testifying to their historical essence and transformative potential.
Basic Components of a Lathe
In the realm of manufacturing and metalworking, lathes hold a pivotal place due to their versatility and precision. A lathe is basically a machine tool used to rotate a workpiece about an axis of rotation to perform various operations such as cutting, sanding, knurling, drilling, or deformation. Delving deeper into the dynamics of a lathe, it consists of several basic components which play a crucial role in its functioning. Leading the list is the 'bed', a solid base which serves as the backbone of the lathe. It provides support and stability to the lathe machine during operations, contributing to the accuracy of work. Mounted on the bed is the 'headstock', housing the main spindle and its driving gears. The main spindle, being the heart of a lathe, is responsible for the rotation of workpiece. In sync with the headstock is the 'tailstock'. Positioned on the opposite side of the headstock on the lathe bed, it can be adjusted along the bed to accommodate workpieces of varied lengths. The tailstock can hold tools like drill bits and serve as an additional support for the workpiece. Next in line is the 'carriage'. Serving as the control panel of the lathe, the carriage holds and moves the cutting tools against the rotating workpiece. It consists of ‘saddle’, ‘cross slide’, and ‘compound rest’, giving operators the freedom to maneuver tools in multiple directions – longitudinal, lateral, and angular. Likewise, the 'tool post' sitting on the carriage, holds the cutting tool in place. Attached to it is the ‘apron’ containing gears and controls to move the carriage or the cutting tool. A rotating 'chuck', attached to the spindle, grips and holds the workpiece securely in place. Lastly, we have the 'feed rod' and 'lead screw' which affect the motion of the carriage and the depth of the cut. While the feed rod is primarily for the automatic feeding of the cutting tool, the lead screw is for thread cutting operation. It's interesting to note how these basic components, while individually straightforward, come together in unison to make lathes one of the most prominently used tools in industries. Understanding these fundamental elements can give one a better grasp of lathes' functionality and operation, further enhancing their efficiency.
Types of Lathes
In understanding lathes, one of the fundamental aspects involves recognizing the different types available, each uniquely designed to perform specific functions. Firstly, there's the Engine lathe, renowned as the most versatile and commonly used type. Distinguished by its longevity, an engine lathe can perform numerous tasks like sanding, cutting, drilling, among others, across broad material types like wood, metal, and plastic. Secondly, we have the Bench lathe, a smaller variant of the engine lathe. Despite its small size, the Bench lathe offers impressive performance and is perfect for workshops with limited space. Turret lathes, on the other hand, carry a turret in place of a tailstock, thereby allowing for different types of tools to be mounted onto it. This feature makes turret lathes ideal for high-volume production processes since it reduces the time taken to change the tools. Another type worth mentioning is the Toolroom lathe, designed for high precision work, hence perfect for tool and die makers. This lathe type offers fine feed rates, high spindle speeds and closer tolerances, making it a favorite among detail-oriented craftsmen and engineers. In addition, Special Purpose Lathes, as their name implies, are built for specific tasks. These include Wheel lathes for machining railway carriage and locomotive wheels, Gap lathes designed with a removable bed section to accommodate larger diameter workpieces, and Multi-spindle lathes designed for mass production. Furthermore, we have the CNC lathes which are electronically controlled. CNC lathes have made manufacturing faster and more accurate as they allow for computer design of products eliminating human errors. For folks interested in woodworking, we have the WoodTurning Lathes. They are designed with functionalities that are optimal for shaping, carving, and sanding wood. Lastly, among the several types of lathes, we have the Metal lathe, specifically designed for shaping and creating metal objects. Metal lathes can produce almost any metallic object, from candlesticks to intricate watch parts. Understanding the different types of lathes is crucial to maximize output not only in production but also in resource allocation. By choosing the right lathe for the specifications at hand, one can streamline their production process and increase overall efficiency. From the versatile Engine lathes to the specialized Special Purpose Lathes, and from the magic of CNC lathes to the artistic abilities of WoodTurning lathes, there is an abundant spectrum of lathes designed to meet various needs and requirements.
How Lathes Work
is often struck in the minds of many people when it comes to the functionality of a machine like a lathe. To shed light on this; our article will delve deeply into the world of lathes. Guiding through the twists and turns of its complexity, this piece will equip you with knowledge on the operating principles and mechanisms of lathes, as these machines interestingly incorporate both simplicity and sophistication in their functionalities. Alongside, we would discover the key functions and operations performed by lathes, shaping different materials into desired forms and sizes with precision and efficiency. To add depth to your understanding, we would finally explore the various tools and accessories that are used with lathes to increase its productivity and versatility, transforming raw materials into finished goods. Now, let's start our journey by examining the operating principles and mechanisms of lathes, the heart of this mechanical marvel. While the lathe's design may appear intimidating at first sight, the principles that govern its operation are based on simple physics.
Operating Principles and Mechanisms
Understanding the operating principles and mechanisms of lathes can contribute significantly to grasping their overall functionality. Centrally, a lathe operates by holding a workpiece in place while the material spins rapidly around its axis. This rotation is powered by an electric motor that drives the lathe spindle. The specific spinning speed (RPM) can be manipulated by the operator to accommodate different types of workpieces and machining processes. One of the most significant components of a lathe is the chuck, a specialized form of clamp anchored to the spindle that's responsible for securing the workpiece. Precision is paramount in lathes: the chuck ensures accurate centre alignment, allowing tools to shape material with impressive precision. With the workpiece held securely, a cutting tool controlled by the operator intersects the spinning material to cut, shape, or modify the workpiece. Another unique feature inherent in lathes is the two types of feeds, longitudinal and transversal. The longitudinal feed allows the tool to move lengthways along the workpiece, while the transverse feed enables lateral movements. The tool's interaction and position with the workpiece via these feeds play a fundamental role in creating various shapes and finishes. The tool’s cutting speed and feed rate can be adjusted to protect against overheating and to enhance the finish quality. Lathes come with a tailstock, a movable component that supports the other end of the workpiece. This eliminates any form of sagging, especially for elongated work items. By adjusting the tailstock's position, the operator can control the depth of a hole during drilling operations. Safety is an imperative element that is taken into account in lathe operating principles. Many lathes are equipped with guards to protect operators from flying chips and spinning parts. Furthermore, emergency stop buttons, lockable isolation switches, and other safety measures are often featured in modern lathes. Finally, it is important to note that despite having similar operating principles, various types of lathes have unique features that enhance their suitability for distinct tasks. Some lathes specialize in working with wood, while others are crafted for metalwork. CNC lathes offer automated control, paving the way for mass production with intricated detailing. Regardless of the kind of lathe, a solid understanding of the machine’s operating principles and mechanics can significantly improve the efficiency and quality of the output. In conclusion, the operating principles and mechanisms of a lathe revolve around a perfect blend of motion (workpiece rotation), precision (chuck alignment), control(feed and speed adjustments) and safety. The versatility in its application across diverse materials and detailed design options showcases the impressive innovation and evolution entrenched in lathe mechanisms.
Key Functions and Operations
Lathes play an integral role in various machining operations, thanks to their diverse range of functions. Primarily, lathes operate by rotating a workpiece about an axis of rotation, performing numerous tasks that include cutting, sanding, drilling, turning, and facing among others. The process starts by securing and spinning the workpiece against a cutting tool, which trims excess material to shape the piece into specific proportions. Keeping in mind that this process's accuracy hinges on the lathe's stability, it's clear that rigidity plays a crucial role in a lathe operation. Advancements in technology have resulted in lathes with CNC capabilities, and these lathes can produce more precise workpieces. Their computer programming and automation allow for repeatable, high-quality production of complex shapes. Furthermore, lathes perform knurling--a process that creates a regularly spaced rough pattern on the workpiece to allow better handgrip. The application of this can be seen in tool handles, metal knobs, and mechanical control levers. Lathes are also used for deformation operations. For instance, metal spinning lathes deform a flat metal disk into a hollow, axially symmetrical part. The performance of these operations is controlled via the machine's controls and feeds, which adjust the lathe's speed, depth of cut, and path of the cutting tool. This control panel allows its operator to make precision modifications for achieving desired results. The versatility of a lathe also allows it to make radius cuts, perform boring tasks--enlarging or changing the shape of a pre-drilled hole--and tackle complex tasks like thread cutting. Lastly, the weighing up and down procedure is an essential operation conducted for balancing the workpiece. It reduces any potential vibrations during the operation, ensuring that the lathe works smoothly during operation. By understanding these key functions and operations, we can appreciate the complexity and versatility of lathe work, reaffirming the lathe's status as an indispensable piece of conducting precise machining work.
Tools and Accessories Used with Lathes
Lathes, as complex machinery, require a range of tools and accessories in order to function at maximum capacity and precision. These tools are indispensable, with their diversity and functionality allowing operators to meet the varying needs that different lathe projects may present. For instance, Lathe Chuck, one of the most commonly employed tools, is used to secure the workpiece in the machine. It has jaws that hold the piece in place, offering a firm grip that ensures safety during the operation. The types of Lathes Chuck can vary, including three jaws universal chuck, four jaws independent chuck, and collect chuck, all of which have unique functions depending on the workpiece's shape and size. A Carriage, another significant component, acts as a supportive bridge between the headstock and tailstock and enables precise control of the cutting tool. It works concurrently with the Cross Slide and Compound Rest to bring about desired alterations to the workpiece, particularly in terms of shaping and dimensioning. Moreover, many lathe operations require Drilling tools, which help create holes in the workpiece. Similarly, Boring tools are designed to enlarge existing holes while offering the right roundness, size, and surface finish. Tools like the Knurling tool are used for adding a pattern on the surface of a workpiece for extra grip, typically seen on tools, cookware, and other metal parts. When it comes to measurements and ensuring precision, Calipers and Micrometers are the go-to tools. These devices measure the dimensions of a workpiece in cases where accuracy is paramount. For intricate works where consistent profiling is crucial, Quick Change Tool Posts and Tool Holders come to rescue by holding the required tool in position for increased precision and efficient changes between tools. Other accessories that facilitate lathe work include Live Centers which provide support for longer workpieces, reducing deflection, and Lathe Dogs which drive workpieces held between centres. To maximize the precision and application of lathes, Cutting Tools are employed. They come in a variety of types such as parting off tool, thread cutting tool, facing tool, and more, each with distinct geometries and coatings for specific roles. A successful lathe operation does not merely involve the lathe machine; it's a whole suite of supportive tools and accessories working in harmony. This underlines the importance of mastering the use of these tools in conjunction with the lathe for a safe and efficient work process. These tools and accessories come together to bring the full potential of the lathe to life, making it a versatile and indispensable machine in both industrial and domestic spaces. This expanded grasp of lathe tools is integral to understanding the detailed workings of the lathe machinery itself and successfully navigating its complexities.
Applications and Uses of Lathes
Lathes, the long-serving workhorses of the industrial revolution, continue to play a critical role across various applications even in our modern dynamic world. This powerful tool has evolved and adapted, finding utility ranging from large-scale industrial applications to small-scale craftsmanship and hobbyist uses, while continuously being refined by modern technological advancements. The first and perhaps most significant use of lathes is in the manufacturing industry. Given its ability to precisely shape and manipulate materials, a lathe is indispensable in sectors such as automotive, aerospace, and heavy machinery. Secondly, the value of a lathe is no less for those engaged in crafting and hobby activities, where its functionality can transform pieces of wood or metal into works of art. Finally, technological innovation continues to expand the potential uses of lathes, integrating modern science to make the process more efficient and precise. Now, let's delve deeper, starting with its industrial applications in manufacturing where lathes prove to be the backbone for material forming processes.
Industrial Applications in Manufacturing
Lathes have broad industrial applications in various manufacturing industries, significantly enhancing productivity and efficiency through their multipurpose functions. Several manufacturing units heavily rely on these tools due to their ability to shape products accurately, create intricate designs, and deliver consistent performance. When discussing the industrial applications of lathes, one cannot ignore their extensive usage in the automotive industry. Lathes are used to shape various car parts such as brake drums, camshafts, and crankshafts. This ensures smooth functioning of the vehicles, contributes to the safety of the driver and passengers, and increases the car's overall lifespan. The aerospace industry also benefits immensely from using lathes. Given the critical safety standards in this industry, operating lathes for shaping and finishing components of aircraft offers an excellent degree of precision that is paramount. In the production of gears, pulleys, bushings, and several other intricate components, there is no match for the accuracy and consistency provided by lathes. Another vital area of application is in the metalworking industry, whether it's for making tools, parts for machinery or simple bolts and nuts. Metal lathes are specifically used to shape and design metals with high accuracy. Their ability to resist the brute force of dense metals without buckling under the pressure makes them an indispensable tool in metalworking workshops. Apart from this, lathes also find varied applications in crafting industries for making musical instruments, furniture, and even jewelry. They are used to create complex shapes and finishes that would be almost impossible to accomplish manually. The commercial production of glass works, creation of signboards, and creation of prototypes in scientific research are more examples where lathes are regularly put to effective use. Moreover, lathes are crucial in the manufacturing of various types of industrial tools and parts. They help cut, drill, knurl, and deform tools that are used in several other industries. This broadens the market scope for lathes, as they are required for the successful operation of every other manufacturing industry. In conclusion, the importance of lathes in industry cannot be overstated. They offer unmatched versatility, precision, and productivity, making them indispensable tools in manufacturing. Their diverse applications serve to underscore the fact that engineering and manufacturing would indeed be very difficult without the use of lathes. The continued refinement and development of lathes will undoubtedly lead to even greater efficiency and a broader scope of applications in the future. Through all these applications and uses, lathes contribute invaluably to the manufacturing industry and beyond.
Craftsmanship and Hobby Uses
Craftsmanship and hobby uses of lathes spotlight on the essential role these machines play not only in various industries but also in providing enthusiasts and crafters with a venue where they can express their creativity and technical skills. The lathe, revered as the mother of machine tools, offers a unique combination of power and precision that appeals to both professional craftsmen and hobbyists alike. For hobbyists, a lathe provides an avenue to create beautiful and intricate pieces of work at home such as pen bodies, bowls, bottle stoppers, and even jewelry. The application of lathes in woodturning, for instance, has surged in popularity due to its accessible learning curve, allowing even beginners to produce artistic and functional pieces that reflect their personal style and vision. The cornerstone for this is the ability of lathes to shape the workpiece with extreme precision, enabling the craftsman to bring their most intricate designs to life. From woodworkers shaping balusters for architectural millwork to jewellers spinning precious metals into refined jewelry pieces, lathes prove their versatility and importance time and time again. A lathe allows for creations to be replicated with exact accuracy, creating opportunities for small-scale production or bulk customization of crafted items. Additionally, using a lathe cultivates an intimate understanding of the properties and behavior of various materials. As craftsmen manipulate pieces on the lathe, they not only develop enhanced technical skills, but also a refined sense of intuition and deepened understanding of the medium they’re working with. Novices and experts alike can enjoy the therapeutic motion of turning, whittling away to reveal a smooth, polished end result. In the realm of craftsmanship, the lathe has become an iconic tool, a symbol of the intersection between creativity and mechanical technique, where human inspiration meets the rigidity of machine precision. In essence, the appeal of lathes in craftsmanship and hobby activities lies not just in the exquisite products that can be made, but also in the personal growth of abilities and understanding, as well as the innate satisfaction derived from making something by hand. For many hobbyists, using a lathe is not only about producing items, but it is also a fascinating journey of learning and self-discovery, culminating in the pride of crafting something tangible and beautiful. This special role of lathes in craftsmanship and hobbies demonstrates the timeless relevance of these machines, as they continue to bring joy and satisfaction to people with a passion for creating. And so, while notable for their industrial applications, the uses of lathes extend beyond, touching the realms of art, self-expression, and personal growth.
Modern Innovations and Advancements
In the modern world, scientific advancements and technological innovations have significantly transformed the use and application of lathes in various industries. A plethora of improvements have arisen, including computer numerical control (CNC) lathes, which have revolutionized precision manufacturing. Unlike traditional lathes that require manual operation, CNC lathes employ computer-aided design and manufacturing software, thereby exponentially increasing accuracy and reducing the need for human labor. Apart from the labor-saving advantage, CNC lathes also have a higher level of precision in creating intricate and complex shapes, enabling manufacturers to meet specific product design and output. Its repeatability feature is another remarkable innovation, allowing manufacturers to produce multiple pieces with the same specifications repeatedly without any variance. Moreover, the advancement in CNC technology has also opened doors to multi-axis lathes, where tools can be directed across the working piece on numerous axes, thereby creating sophisticated geometrical patterns that were once considered impossible. These machines have vastly improved efficiency in industries such as automobile, aerospace, military, and manufacturing, where precision and consistency are of utmost importance. The advent of laser cutting lathes is another remarkable milestone in the lathe technology. These employ high-powered lasers as the cutting tool, providing a higher degree of accuracy and speed in cutting through metals and other materials. Besides, laser cutting lathes produce a smoother cut surface, reducing the need for finishing work. The integration of Artificial Intelligence (AI) in modern lathes is testament to the tremendous strides in industrialization. AI in lathes allows for machine-learning capabilities, improved predictive maintenance, self-optimization, and increased productivity. The onset of this technology ensures fewer errors, shorter production times, and higher quality end products. In conclusion, the evolution of lathe technology, through modern innovations and advancements, has significantly transformed the industrial manufacturing landscape. This speaks volumes about the limitless opportunities and possibilities that the future of lathe machinery holds.