What Is The Purpose Of Whmis?

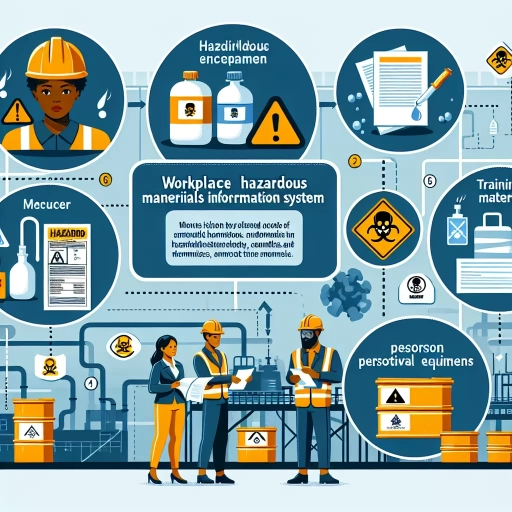
The Workplace Hazardous Materials Information System (WHMIS) is a critical component of occupational health and safety in Canada, designed to protect workers from the hazards of chemicals in the workplace. At its core, WHMIS serves multiple purposes that are integral to ensuring a safe working environment. First, it aims to educate workers about the potential dangers associated with hazardous materials through clear labeling and safety data sheets. This educational aspect is central to understanding WHMIS: its core objectives, which will be explored in detail. Additionally, WHMIS plays a pivotal role in chemical management by providing standardized procedures for handling, storing, and disposing of hazardous substances. This systematic approach helps in mitigating risks and preventing accidents. Furthermore, the implementation of WHMIS has a significant impact on occupational health and safety, reducing the incidence of chemical-related injuries and illnesses. By delving into these aspects, we can appreciate the comprehensive nature of WHMIS and its importance in safeguarding workplaces. To begin, let's delve into the foundational elements of WHMIS by understanding its core objectives.
Understanding WHMIS: Its Core Objectives
In the realm of workplace safety and chemical management, the Workplace Hazardous Materials Information System (WHMIS) stands as a cornerstone of regulatory compliance and employee protection. WHMIS is designed to ensure that workers are well-informed about the hazards associated with the chemicals they handle, thereby reducing the risk of accidents and health issues. At its core, WHMIS has three primary objectives that underpin its effectiveness. First, it focuses on **Ensuring Workplace Safety** by mandating the proper handling, storage, and use of hazardous materials. Second, it **Provides Hazard Information** through comprehensive data sheets and labels, enabling workers to understand the risks and take necessary precautions. Third, WHMIS **Standardizes Chemical Labeling**, ensuring consistency in how hazards are communicated across different workplaces. By understanding these core objectives, organizations can better implement WHMIS, fostering a safer and more informed work environment. This article delves into the intricacies of WHMIS, exploring its core objectives and how they collectively contribute to a safer workplace. **Understanding WHMIS: Its Core Objectives** is crucial for any organization dealing with hazardous materials, and this article aims to provide a detailed insight into its essential components.
1. Ensuring Workplace Safety
Ensuring workplace safety is a paramount objective of the Workplace Hazardous Materials Information System (WHMIS). This comprehensive system is designed to protect workers from the hazards associated with chemical products in the workplace. At its core, WHMIS aims to provide workers with the necessary information and training to handle hazardous materials safely. This involves several key components: classification of hazardous products, labeling of containers, and the provision of safety data sheets (SDSs). By classifying hazardous materials based on their physical and health hazards, WHMIS ensures that workers are aware of the specific risks associated with each product. Labels on containers provide immediate visual warnings and critical safety information, while SDSs offer detailed data on safe handling, storage, and emergency procedures. Additionally, WHMIS mandates that employers provide regular training to their employees, ensuring they understand how to use personal protective equipment, follow safe work practices, and respond effectively in case of emergencies. This holistic approach not only reduces the risk of workplace injuries and illnesses but also fosters a culture of safety and compliance. By empowering workers with the knowledge and tools they need to manage hazardous materials safely, WHMIS plays a crucial role in maintaining a safe and healthy work environment. Ultimately, the integration of WHMIS into workplace safety protocols is essential for protecting both employees and employers from the potential dangers posed by hazardous substances.
2. Providing Hazard Information
Providing hazard information is a cornerstone of the Workplace Hazardous Materials Information System (WHMIS), a critical component in ensuring the safety and health of workers who handle hazardous materials. At its core, WHMIS aims to educate and inform employees about the potential dangers associated with the chemicals they use, thereby enabling them to take necessary precautions to mitigate risks. This objective is achieved through several key mechanisms. Firstly, WHMIS mandates the use of standardized labels and safety data sheets (SDSs) for all hazardous products. These labels must include essential information such as the product identifier, hazard statements, precautionary statements, and pictograms that visually represent the type of hazard. For instance, a label might feature a flame pictogram to indicate flammability or a skull and crossbones to signify toxicity. This visual and textual information ensures that workers can quickly identify potential hazards even in high-pressure or emergency situations. Secondly, SDSs provide detailed information about each hazardous product. These documents are divided into 16 sections and cover everything from the product's composition and first aid measures to fire-fighting measures and disposal considerations. This comprehensive data empowers workers to understand how to safely handle, store, and dispose of hazardous materials, reducing the likelihood of accidents and exposure. Moreover, WHMIS training programs are designed to equip workers with the knowledge they need to interpret and apply the information provided on labels and SDSs. These training sessions cover topics such as recognizing hazards, understanding the classification system, and implementing safe handling practices. By ensuring that all employees are well-informed and trained, workplaces can foster a culture of safety where everyone is vigilant about potential hazards. In addition to these measures, WHMIS also emphasizes the importance of workplace-specific training. Employers are required to provide training that is tailored to the specific hazards present in their workplace. This includes teaching workers how to respond in case of emergencies, such as spills or leaks, and how to use personal protective equipment (PPE) effectively. Overall, providing hazard information through WHMIS is not just a regulatory requirement but a vital step in protecting worker health and safety. By ensuring that all stakeholders have access to accurate and comprehensive information about hazardous materials, WHMIS helps prevent injuries, illnesses, and fatalities in the workplace. This proactive approach underscores the commitment to creating safer working environments where employees can perform their duties with confidence and minimal risk.
3. Standardizing Chemical Labeling
Standardizing chemical labeling is a crucial component of the Workplace Hazardous Materials Information System (WHMIS), a comprehensive framework designed to ensure the safe handling, use, and storage of hazardous materials in Canadian workplaces. The core objective of standardizing chemical labeling under WHMIS is to provide clear, consistent, and easily understandable information about the hazards associated with each chemical product. This standardization is achieved through the use of Safety Data Sheets (SDSs) and labels that adhere to specific guidelines. SDSs are detailed documents that contain critical information about a chemical's properties, hazards, safe handling practices, emergency procedures, and first aid measures. These documents are structured in a uniform manner to facilitate quick access to essential information. Labels, on the other hand, provide immediate visual warnings and key details about the hazards of a chemical. They include pictograms, signal words (such as "Danger" or "Warning"), hazard statements, precautionary statements, and supplier information. The standardization of chemical labeling ensures that all stakeholders—workers, employers, and emergency responders—can quickly identify and understand the risks associated with a particular chemical. This uniformity helps in preventing accidents and reducing the risk of exposure to hazardous substances. For instance, pictograms on labels serve as universal symbols that convey specific types of hazards (e.g., flammability, toxicity) without requiring language proficiency. This visual consistency is particularly important in workplaces where employees may speak different languages or have varying levels of literacy. Moreover, standardized labeling facilitates compliance with regulatory requirements and enhances workplace safety culture. Employers are mandated to ensure that all hazardous materials in their workplaces are properly labeled and that SDSs are readily available to workers. This not only helps in meeting legal obligations but also fosters an environment where safety is prioritized through clear communication and awareness. In summary, standardizing chemical labeling under WHMIS is essential for maintaining a safe and informed workplace. By providing consistent and accessible information through SDSs and labels, WHMIS helps protect workers from the risks associated with hazardous materials, supports regulatory compliance, and promotes a culture of safety and awareness. This standardized approach ensures that everyone involved in handling chemicals can do so with confidence and understanding, thereby reducing the likelihood of accidents and enhancing overall workplace safety.
The Role of WHMIS in Chemical Management
In the realm of chemical management, the Workplace Hazardous Materials Information System (WHMIS) plays a pivotal role in ensuring the safety and well-being of workers. WHMIS is a comprehensive system designed to provide critical information about hazardous materials, thereby reducing the risks associated with their handling, use, and disposal. This article delves into the multifaceted role of WHMIS, exploring three key aspects: **Classifying Hazardous Materials**, which involves categorizing substances based on their potential dangers; **Training and Education**, which equips workers with the knowledge and skills necessary to handle these substances safely; and **Compliance and Regulatory Framework**, which outlines the legal requirements and standards that must be adhered to. By understanding these components, we can appreciate the core objectives of WHMIS and its significance in maintaining a safe and compliant workplace environment. Transitioning to **Understanding WHMIS: Its Core Objectives**, we will examine how these elements collectively contribute to a robust chemical management system.
1. Classifying Hazardous Materials
Classifying hazardous materials is a critical component of the Workplace Hazardous Materials Information System (WHMIS), a cornerstone in chemical management. This process involves categorizing substances based on their potential to cause harm, ensuring that workers, employers, and emergency responders are well-informed about the risks associated with these materials. Under WHMIS, hazardous materials are classified into two main categories: physical hazards and health hazards. Physical hazards include substances that can cause immediate harm through explosion, fire, or other physical means. For instance, flammable liquids and gases fall under this category due to their potential to ignite and cause fires. On the other hand, health hazards encompass substances that can cause adverse health effects either immediately or over time. This includes toxic substances, carcinogens, and mutagens which can lead to serious health issues such as cancer or genetic mutations. The classification process is rigorous and involves evaluating the intrinsic properties of the substance as well as its potential impact on human health and the environment. For each hazardous material, a Safety Data Sheet (SDS) is prepared which provides detailed information about the substance's classification, safe handling practices, emergency procedures, and first aid measures. Additionally, labels are affixed to containers of hazardous materials to provide quick visual cues about the nature of the hazard. These labels include pictograms, hazard statements, and precautionary statements that alert users to the potential dangers. The classification system under WHMIS is aligned with the Globally Harmonized System of Classification and Labelling of Chemicals (GHS), ensuring international consistency and facilitating safer global trade of chemicals. This alignment enhances the clarity and effectiveness of hazard communication, making it easier for workers to understand and respond appropriately to chemical hazards regardless of their geographical location. In summary, classifying hazardous materials under WHMIS is essential for maintaining a safe work environment. By accurately categorizing these substances and providing comprehensive information through SDSs and labels, WHMIS empowers workers with the knowledge they need to handle chemicals safely and respond effectively in emergency situations. This systematic approach to hazard classification is a key element in the broader framework of chemical management, underscoring the critical role that WHMIS plays in protecting public health and safety.
2. Training and Education
Training and education are pivotal components in the effective implementation of the Workplace Hazardous Materials Information System (WHMIS). WHMIS is designed to ensure that workers are aware of the hazards associated with the chemicals they use, handle, or are exposed to in their workplaces. To achieve this, comprehensive training programs are essential for equipping employees with the knowledge and skills necessary to handle hazardous materials safely. These training programs typically cover several key areas. First, they introduce workers to the WHMIS system itself, including its history, purpose, and legal requirements. This foundational knowledge helps employees understand why WHMIS is crucial and how it fits into broader occupational health and safety regulations. Next, training focuses on the classification of hazardous products, which involves understanding the different categories of hazards such as flammable liquids, corrosive substances, and toxic gases. Employees learn how to identify these hazards through labels and safety data sheets (SDSs), which are critical resources for obtaining detailed information about each chemical product. Another critical aspect of WHMIS training is the proper use of personal protective equipment (PPE) and emergency procedures. Workers are taught how to select and use appropriate PPE for handling specific chemicals, as well as how to respond in case of spills, leaks, or other emergencies involving hazardous materials. This includes understanding first aid procedures and knowing when to evacuate the area or call for professional assistance. Moreover, WHMIS training emphasizes the importance of safe handling practices and storage procedures. Employees learn about proper ventilation requirements, safe disposal methods, and how to prevent accidents through good housekeeping practices. The training also covers workplace-specific procedures that are tailored to the unique hazards present in their particular work environment. Regular updates and refresher courses are also integral parts of WHMIS training. As new chemicals are introduced into the workplace or as regulations evolve, ongoing education ensures that workers remain informed and compliant. This continuous learning approach helps maintain a culture of safety within organizations by reinforcing best practices and updating knowledge on emerging hazards. In summary, training and education under WHMIS are not one-time events but ongoing processes that are fundamental to chemical management in the workplace. By providing workers with comprehensive knowledge on hazardous materials classification, safe handling practices, emergency response protocols, and continuous updates, organizations can significantly reduce the risks associated with chemical use and create a safer working environment for all employees. This robust educational framework supports the broader purpose of WHMIS by ensuring that workers are equipped to handle chemicals responsibly and safely.
3. Compliance and Regulatory Framework
Compliance with the regulatory framework is a crucial aspect of chemical management, and WHMIS (Workplace Hazardous Materials Information System) plays a pivotal role in ensuring adherence to these standards. The WHMIS system is designed to provide workers with the necessary information to safely handle hazardous materials in the workplace. At its core, WHMIS compliance involves several key components: classification, labeling, safety data sheets (SDS), and worker training. **Classification** is the first step in the WHMIS framework, where hazardous materials are categorized based on their physical and health hazards. This classification system ensures that materials are identified and managed according to their specific risks. **Labeling** follows classification, requiring that each hazardous product be labeled with specific information such as the product identifier, hazard statements, precautionary statements, and pictograms. These labels serve as immediate visual warnings to workers about the potential dangers associated with a product. **Safety Data Sheets (SDS)** are detailed documents that provide comprehensive information about a hazardous product's properties, safe handling practices, emergency procedures, and first aid measures. SDSs are essential for employers to develop safe work practices and for workers to understand how to handle chemicals safely. The SDS must be readily available to all workers who may be exposed to the hazardous material. **Worker Training** is perhaps the most critical component of WHMIS compliance. Employers are mandated to educate workers on the safe use, handling, and storage of hazardous materials. This training includes understanding the classification system, interpreting labels and SDSs, and knowing emergency procedures. Effective training ensures that workers can recognize hazards and take appropriate actions to mitigate risks. In addition to these core elements, the regulatory framework surrounding WHMIS is enforced by various government agencies and standards organizations. In Canada, for example, Health Canada and the Canadian Centre for Occupational Health and Safety (CCOHS) are key bodies that oversee WHMIS compliance. These agencies ensure that employers adhere to the regulations by conducting inspections and providing guidelines for implementation. Overall, the compliance and regulatory framework of WHMIS is designed to protect workers from the risks associated with hazardous materials. By ensuring accurate classification, clear labeling, detailed SDSs, and comprehensive worker training, WHMIS helps create a safer work environment. This integrated approach not only meets legal requirements but also fosters a culture of safety and responsibility within workplaces that handle chemicals. As such, WHMIS remains a cornerstone of chemical management practices, underscoring the importance of regulatory compliance in safeguarding worker health and safety.
Impact of WHMIS on Occupational Health and Safety
The Workplace Hazardous Materials Information System (WHMIS) has been a cornerstone of occupational health and safety in Canada, significantly impacting the way workplaces manage hazardous materials. Since its inception, WHMIS has played a crucial role in reducing chemical-related injuries by ensuring that workers are well-informed about the hazards associated with the substances they handle. This system enhances emergency preparedness by providing clear guidelines and protocols for handling and responding to chemical incidents. Furthermore, WHMIS promotes a culture of safety within organizations, fostering an environment where safety is a shared responsibility among all employees. By understanding the core objectives of WHMIS, we can appreciate how these elements collectively contribute to a safer and healthier work environment. In this article, we will delve into the specific ways WHMIS achieves these outcomes, exploring its impact on reducing chemical-related injuries, enhancing emergency preparedness, and promoting a culture of safety. Understanding WHMIS: Its Core Objectives will provide a comprehensive framework for appreciating the system's multifaceted benefits.
1. Reducing Chemical-Related Injuries
Reducing chemical-related injuries is a paramount objective of the Workplace Hazardous Materials Information System (WHMIS), a cornerstone of occupational health and safety in Canada. By mandating the classification, labeling, and provision of safety data sheets (SDSs) for hazardous materials, WHMIS empowers workers with critical information to handle chemicals safely. This comprehensive system ensures that employers and employees alike are aware of the potential dangers associated with specific substances, enabling them to take proactive measures to mitigate risks. For instance, WHMIS requires that all hazardous products be labeled with standardized symbols and phrases that clearly indicate the nature of the hazard, whether it be flammable, toxic, or corrosive. This immediate visual warning alerts workers to potential dangers, prompting them to follow appropriate safety protocols and use personal protective equipment (PPE) as necessary. Additionally, SDSs provide detailed information on safe handling practices, emergency procedures, and first aid measures, further reducing the likelihood of accidents. The education and training components of WHMIS are equally crucial; they ensure that workers understand the hazards they may encounter and know how to respond effectively in case of an emergency. This holistic approach not only protects workers from immediate harm but also fosters a culture of safety within the workplace, where chemical handling is managed with diligence and caution. By reducing chemical-related injuries, WHMIS contributes significantly to a safer work environment, aligning with broader occupational health and safety goals and ultimately enhancing the well-being of all workers involved in handling hazardous materials.
2. Enhancing Emergency Preparedness
Enhancing emergency preparedness is a critical aspect of occupational health and safety, and the Workplace Hazardous Materials Information System (WHMIS) plays a pivotal role in this endeavor. By providing comprehensive information about hazardous materials, WHMIS equips workers with the knowledge they need to handle emergencies effectively. Here’s how WHMIS enhances emergency preparedness: WHMIS mandates that all hazardous materials be labeled and accompanied by Safety Data Sheets (SDSs), which contain detailed information on the safe handling, use, storage, and disposal of these substances. This information is crucial during emergency situations such as spills, leaks, or fires. For instance, if a chemical spill occurs, workers can quickly refer to the SDS to understand the appropriate response measures, including personal protective equipment (PPE) requirements, containment procedures, and first aid instructions. This immediate access to critical information helps in mitigating the risks associated with hazardous materials and ensures a swift and safe response. Moreover, WHMIS training programs are designed to educate workers on recognizing hazards, understanding safety protocols, and implementing emergency procedures. These training sessions cover topics such as hazard classification, safe work practices, and emergency response strategies. By ensuring that all employees are well-trained in WHMIS protocols, workplaces can significantly reduce the likelihood of accidents and improve their overall emergency preparedness. For example, trained workers can identify potential hazards before they escalate into emergencies and take proactive steps to prevent them. Additionally, WHMIS fosters a culture of safety within organizations by promoting continuous awareness and vigilance among workers. Regular updates and reviews of SDSs and labels ensure that workers stay informed about any changes in hazard classifications or safety procedures. This ongoing education empowers workers to be proactive in identifying potential risks and taking preventive measures, thereby enhancing the overall emergency preparedness of the workplace. In summary, WHMIS is instrumental in enhancing emergency preparedness by providing essential information through labels and SDSs, ensuring comprehensive worker training, and fostering a culture of safety. These measures collectively contribute to a safer work environment where workers are better equipped to handle emergencies effectively, thereby protecting their health and safety. By integrating WHMIS into their safety protocols, organizations can significantly improve their ability to respond to emergencies and reduce the risk of occupational injuries and illnesses.
3. Promoting a Culture of Safety
Promoting a culture of safety is a crucial aspect of the impact of the Workplace Hazardous Materials Information System (WHMIS) on occupational health and safety. WHMIS, by its very nature, fosters an environment where workers are well-informed about the hazards associated with the chemicals they handle. This system ensures that every employee understands the risks and knows how to mitigate them, thereby creating a proactive and vigilant workforce. The core components of WHMIS—labels, safety data sheets (SDS), and training—serve as the foundation for this safety culture. Labels on hazardous materials provide immediate visual warnings, alerting workers to potential dangers. Safety Data Sheets offer detailed information on safe handling, storage, and emergency procedures, equipping employees with the knowledge they need to handle chemicals safely. Training programs mandated by WHMIS ensure that workers are educated on how to read labels and SDSs, use personal protective equipment (PPE), and follow established safety protocols. This comprehensive approach not only reduces the risk of accidents but also empowers workers to take responsibility for their own safety and that of their colleagues. A culture of safety promoted through WHMIS extends beyond compliance with regulations; it becomes an integral part of the workplace ethos. When employees feel confident in their ability to identify and manage hazards, they are more likely to report potential risks and suggest improvements. This open communication fosters a collaborative environment where safety is everyone's responsibility. Moreover, a strong safety culture enhances employee morale and reduces turnover rates, as workers feel valued and protected by their employers. The impact of WHMIS on occupational health and safety is also reflected in the reduction of workplace injuries and illnesses. By providing clear guidelines and ensuring that all stakeholders are aware of the risks associated with hazardous materials, WHMIS helps prevent accidents that could result in serious harm or even fatalities. This proactive approach not only protects workers but also minimizes downtime due to accidents, thereby maintaining productivity and reducing economic losses. In summary, promoting a culture of safety through WHMIS is pivotal in enhancing occupational health and safety. By educating workers about chemical hazards, providing them with the tools to manage these risks, and fostering an environment of open communication and shared responsibility, WHMIS contributes significantly to creating safer workplaces. This holistic approach ensures that safety becomes an ingrained part of daily operations, ultimately leading to a healthier and more secure work environment for all employees.