What Is Kitec Plumbing

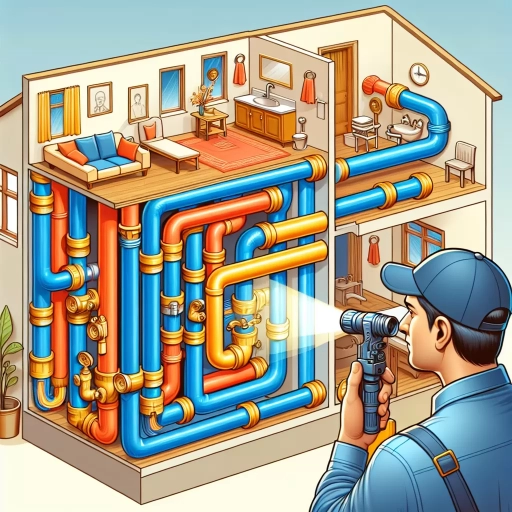
Kitec plumbing, a type of piping system introduced in the late 1990s, was marketed as a durable and cost-effective alternative to traditional copper and PVC pipes. However, over the years, it has become notorious for its propensity to fail, leading to significant water damage and financial losses for homeowners. This article delves into the intricacies of Kitec plumbing, starting with an **Introduction to Kitec Plumbing**, where we explore its history, composition, and initial benefits. We then examine **Common Issues and Failures with Kitec Plumbing**, highlighting the reasons behind its widespread problems. Finally, we discuss **Replacement, Repair, and Legal Considerations**, providing guidance on how to address these issues and potential legal recourse for affected homeowners. Understanding these aspects is crucial for anyone dealing with Kitec plumbing, and it begins with a thorough **Introduction to Kitec Plumbing**.
Introduction to Kitec Plumbing
Kitec plumbing, a system that was once hailed as a revolutionary alternative to traditional copper and PEX piping, has a complex and intriguing history. Introduced in the late 1990s, Kitec plumbing was designed to offer a more durable, flexible, and cost-effective solution for residential and commercial plumbing needs. This article delves into the key aspects of Kitec plumbing, starting with its **History and Development**, which outlines the origins and evolution of the system. We will also explore the **Key Components and Materials Used**, highlighting the unique properties of the polyethylene-aluminum-polyethylene (PE-AL-PE) pipes and fittings that characterized Kitec. Additionally, we will examine the **Initial Benefits and Marketing Claims** that made Kitec so appealing to consumers and builders at its inception. By understanding these foundational elements, readers can gain a comprehensive insight into what made Kitec plumbing so promising and why it remains a topic of interest today. Let's begin by tracing the roots of Kitec plumbing through its history and development.
History and Development of Kitec
Kitec plumbing, a brand synonymous with controversy and legal battles, has a history that spans several decades. Developed in the late 1990s by IPEX, a Canadian company, Kitec was marketed as a revolutionary alternative to traditional copper and PEX piping systems. The product consisted of flexible, cross-linked polyethylene (PEX) tubing and aluminum or copper fittings, designed to be more resistant to corrosion and easier to install. Initially, Kitec gained popularity due to its perceived advantages: it was lighter, more flexible, and required fewer connections compared to traditional piping materials. However, the early 2000s saw the emergence of significant issues with Kitec plumbing. Homeowners began reporting leaks, corrosion, and failures of the aluminum or copper fittings, which were prone to degradation when exposed to certain types of water. This led to widespread complaints and lawsuits against IPEX and other companies involved in the manufacturing and distribution of Kitec products. The problems were attributed to the interaction between the PEX tubing and the aluminum or copper fittings, which caused premature failure under certain conditions. By the mid-2000s, class-action lawsuits had been filed in multiple jurisdictions, alleging that Kitec plumbing was defective and had caused substantial property damage. In response to these legal challenges, IPEX agreed to a settlement in 2011 that established a fund to compensate homeowners affected by Kitec failures. Despite this settlement, many homeowners continued to experience issues with their Kitec plumbing systems, leading to ongoing legal disputes and a tarnished reputation for the brand. Today, Kitec plumbing is largely avoided by builders and homeowners due to its history of reliability issues and the associated legal and financial risks. The development and subsequent downfall of Kitec serve as a cautionary tale about the importance of rigorous testing and quality control in the construction industry. While innovative materials can offer significant advantages, they must be thoroughly vetted to ensure they meet long-term performance standards. The legacy of Kitec plumbing underscores the critical need for robust product testing and consumer protection measures to safeguard against similar failures in the future.
Key Components and Materials Used
Kitec plumbing, a type of piping system introduced in the late 1990s, is characterized by its unique components and materials. The key components include PEX (cross-linked polyethylene) tubing, fittings, and connectors. **PEX Tubing**: This is the primary material used in Kitec plumbing. PEX tubing is flexible, resistant to freezing temperatures, and can withstand high water pressure. It is also less prone to corrosion compared to traditional copper or galvanized steel pipes. **Fittings and Connectors**: Kitec fittings and connectors are typically made from a combination of brass and aluminum. These components are designed to be durable and resistant to corrosion, ensuring a secure connection between the PEX tubing segments. However, it is crucial to note that the brass fittings in Kitec systems have been a point of contention due to their propensity for corrosion when exposed to certain water conditions. **Other Materials**: The system also includes various other materials such as manifolds, valves, and adapters. Manifolds are central distribution points that allow for the branching off of multiple lines from a single source. Valves control water flow, while adapters facilitate connections between different types of pipes or fittings. **Installation Considerations**: The choice of materials in Kitec plumbing was intended to simplify installation processes. The flexibility of PEX tubing allows for easier routing around obstacles without the need for extensive cutting or bending. Additionally, the push-fit connectors reduce the necessity for soldering or gluing, making the overall installation faster and more straightforward. Despite these advantages, Kitec plumbing has faced significant criticism and legal issues due to premature failures and leaks attributed to the corrosion of brass fittings. This has led many homeowners and builders to reconsider its use in favor of other piping systems that offer greater reliability and longevity. Understanding the key components and materials used in Kitec plumbing is essential for evaluating its suitability for specific applications and addressing potential issues that may arise during its use.
Initial Benefits and Marketing Claims
When Kitec plumbing first emerged, it was hailed as a revolutionary alternative to traditional copper and PEX piping systems. The initial benefits and marketing claims surrounding Kitec were compelling, positioning it as a superior choice for plumbing installations. One of the primary advantages touted was its ease of installation. Kitec pipes and fittings were designed to be lightweight and flexible, making them simpler to handle and connect compared to rigid copper pipes. This flexibility also allowed for more creative routing options, potentially reducing labor costs and installation time. Another significant benefit highlighted was the resistance of Kitec to corrosion and scaling. Unlike copper, which can corrode over time due to water quality issues, Kitec pipes were made from a cross-linked polyethylene (PEX) material that was resistant to these problems. This promised longer system lifespan and reduced maintenance needs. Additionally, Kitec was marketed as being more resistant to freezing temperatures, which could help prevent bursts and leaks associated with frozen pipes. The marketing claims also emphasized the cost-effectiveness of Kitec plumbing. The material was generally cheaper than copper, and the simpler installation process could further reduce overall project costs. Furthermore, Kitec was promoted as an environmentally friendly option due to its lower energy requirements during manufacturing compared to traditional materials. In terms of performance, Kitec was advertised to offer consistent water pressure and flow rates, ensuring reliable service across various plumbing applications. The system's design included push-fit fittings that eliminated the need for soldering or gluing, making it easier for DIY enthusiasts and professional plumbers alike to work with. However, despite these initial benefits and marketing claims, Kitec plumbing has faced significant challenges and controversies over the years. Issues such as premature degradation of the pipe material, leading to leaks and failures, have led to numerous lawsuits and recalls. These problems have overshadowed many of the original advantages, making it crucial for homeowners and builders to carefully consider the risks associated with Kitec plumbing before making a decision. In summary, while Kitec plumbing was initially praised for its ease of installation, resistance to corrosion, cost-effectiveness, and environmental benefits, its long-term performance has been marred by serious reliability issues. Understanding these initial benefits and subsequent challenges is essential for anyone considering Kitec or evaluating its place in the broader context of plumbing solutions.
Common Issues and Failures with Kitec Plumbing
Kitec plumbing, once touted as a durable and efficient alternative to traditional copper piping, has been plagued by a multitude of issues that have led to significant problems for homeowners and builders alike. One of the primary concerns is the corrosion and degradation of Kitec pipes, which can lead to premature failure and costly repairs. Additionally, leakage and water damage incidents have become all too common, resulting in extensive property damage and health hazards. The severity of these issues has also prompted numerous lawsuits and class-action settlements, highlighting the widespread impact of Kitec's shortcomings. Understanding these common failures is crucial for anyone considering or already dealing with Kitec plumbing systems. This article delves into the specifics of these problems, starting with the critical issue of corrosion and degradation, which sets the stage for the broader discussion on the pitfalls associated with Kitec plumbing.
Corrosion and Degradation Problems
Corrosion and degradation are significant concerns in plumbing systems, particularly with materials like Kitec, which has been known to suffer from these issues. Corrosion occurs when the material reacts with its environment, leading to the deterioration of its structure and integrity. In the case of Kitec plumbing, which is made from a combination of polyethylene and aluminum, corrosion can manifest in several ways. The aluminum layer within Kitec pipes can corrode due to exposure to certain chemicals in the water supply, such as chlorine or chloramines, which are commonly used as disinfectants. This corrosion can weaken the pipe walls, leading to leaks and failures. Degradation, on the other hand, involves the breakdown of the material over time due to various factors such as temperature fluctuations, water pressure, and chemical interactions. Kitec pipes have been reported to degrade more rapidly than expected, especially when exposed to hot water or high water pressure. The polyethylene layer in Kitec pipes can become brittle and crack, while the aluminum layer can oxidize and lose its protective properties. This degradation not only compromises the structural integrity of the pipes but also increases the risk of leaks and ruptures. The combination of corrosion and degradation in Kitec plumbing systems can lead to serious consequences, including costly repairs, water damage, and even health risks if contaminated water is consumed. Homeowners with Kitec plumbing have reported frequent leaks, pipe failures, and significant financial burdens due to these issues. Furthermore, insurance claims related to Kitec plumbing failures have been substantial, highlighting the severity of these problems. In summary, corrosion and degradation are critical issues affecting Kitec plumbing systems. These problems arise from chemical reactions and environmental factors that weaken the material's structure, leading to leaks, failures, and significant maintenance costs. Understanding these issues is crucial for homeowners and builders to make informed decisions about plumbing materials and maintenance strategies to mitigate such risks.
Leakage and Water Damage Incidents
Leakage and water damage incidents are among the most common and severe issues associated with Kitec plumbing systems. Kitec, a type of flexible piping made from polyethylene and aluminum, was widely used in residential and commercial properties from the late 1990s to the mid-2000s due to its ease of installation and perceived durability. However, it has proven to be highly prone to failures that can lead to significant water damage. The primary cause of these leaks is the degradation of the pipe material over time, often due to factors such as high water pressure, chlorine levels in the water supply, and exposure to heat. When Kitec pipes degrade, they can develop cracks and fissures that allow water to escape, leading to sudden and unexpected leaks. These leaks can occur at any point in the system, including at fittings, connections, and along the length of the pipes themselves. The consequences of such leaks can be catastrophic. Water damage from Kitec failures can result in extensive structural harm to buildings, including warped flooring, damaged drywall, and compromised insulation. Additionally, water intrusion can lead to mold growth and create unhealthy living conditions. In many cases, homeowners have reported finding large amounts of water accumulating in their homes without any visible signs of leakage until significant damage has already occurred. Furthermore, the hidden nature of these pipes within walls and under flooring makes detection and repair particularly challenging. Homeowners may not be aware of a leak until it has caused substantial damage, making regular inspections crucial for early detection. The financial impact of these incidents can also be substantial, with repair costs often running into thousands of dollars. Given these risks, many homeowners and property managers have opted to replace Kitec plumbing entirely rather than risk ongoing maintenance and potential future failures. This proactive approach not only mitigates the risk of water damage but also provides peace of mind and protects the integrity of the property. In summary, leakage and water damage incidents are critical concerns for those with Kitec plumbing systems. The inherent flaws in this type of piping make it susceptible to degradation and failure, leading to costly repairs and potential health hazards. Regular monitoring and proactive replacement strategies are essential for minimizing these risks and ensuring the safety and value of affected properties.
Lawsuits and Class-Action Settlements
Lawsuits and class-action settlements have been a significant aspect of the Kitec plumbing saga, reflecting the widespread dissatisfaction and financial losses experienced by homeowners and property owners due to the product's failures. Kitec plumbing, known for its PEX (cross-linked polyethylene) tubing and fittings, was marketed as a durable and reliable alternative to traditional copper piping. However, it has been plagued by issues such as premature degradation, corrosion, and leaks, leading to extensive property damage and costly repairs. The legal landscape surrounding Kitec has been marked by numerous class-action lawsuits filed in various jurisdictions. These lawsuits typically allege that the manufacturers and distributors of Kitec plumbing systems failed to disclose the product's defects and misrepresented its durability and performance. Plaintiffs often claim that the companies involved in the production and sale of Kitec knew or should have known about the potential for failure but chose not to inform consumers, thereby causing significant financial harm. One of the most notable class-action settlements related to Kitec plumbing was reached in 2011. This settlement established a fund to compensate homeowners for repairs and replacements of the faulty plumbing systems. The settlement provided financial relief to thousands of affected property owners, although many have argued that the compensation did not fully cover the extent of their losses. Despite these settlements, issues persist. Homeowners continue to face challenges in obtaining adequate compensation for the full scope of damages incurred. Additionally, the process of filing claims and receiving payouts can be complex and time-consuming, often requiring extensive documentation and proof of damage. Furthermore, some homeowners have reported difficulty in finding qualified plumbers willing to work with Kitec systems due to their reputation for failure. The legal battles surrounding Kitec highlight broader issues within the construction and plumbing industries regarding product liability and consumer protection. They underscore the importance of rigorous testing and quality control measures before products are brought to market. Moreover, these cases emphasize the need for transparency and accountability from manufacturers and distributors to ensure that consumers are not misled about the performance and reliability of building materials. In summary, lawsuits and class-action settlements related to Kitec plumbing reflect a broader narrative of product failure, consumer dissatisfaction, and the ongoing quest for justice and compensation. These legal actions serve as a reminder of the critical importance of product integrity and the need for robust consumer protections in the construction industry.
Replacement, Repair, and Legal Considerations
When dealing with Kitec plumbing, homeowners face a complex array of challenges that span from identification and maintenance to legal implications. Understanding the nuances of Kitec plumbing is crucial for making informed decisions about replacement, repair, and potential legal recourse. This article delves into three key areas: identifying Kitec plumbing in your home, the costs and processes involved in replacement or repair, and the legal considerations and compensation options available. By grasping these elements, homeowners can navigate the often-daunting process of addressing Kitec plumbing issues effectively. To begin, it is essential to know how to identify Kitec plumbing in your home, which sets the stage for subsequent decisions on whether to replace or repair the system. This initial step is critical in determining the best course of action and ensuring that any necessary work is done correctly. Therefore, let's start by exploring the steps for identifying Kitec plumbing in your home.
Steps for Identifying Kitec Plumbing in Your Home
Identifying Kitec plumbing in your home is a crucial step, especially given the potential for leaks, corrosion, and other issues associated with this type of piping. Here are the steps to follow: 1. **Visual Inspection**: Look for distinctive orange or yellow fittings and pipes. Kitec plumbing is often marked with the brand name "Kitec" or "IPEX" on the pipes and fittings. 2. **Check Under Sinks and Around Water Heaters**: These areas are common places to find Kitec plumbing. Inspect the pipes under kitchen and bathroom sinks, as well as around water heaters and other plumbing fixtures. 3. **Inspect Behind Walls**: If possible, inspect areas behind walls where plumbing lines run, such as near bathrooms or kitchens. This may require removing drywall or accessing crawl spaces. 4. **Check for Corrosion**: Kitec pipes are prone to corrosion, especially at fittings and connections. Look for signs of rust, mineral buildup, or discoloration around these areas. 5. **Consult Home Inspection Reports**: If you have a home inspection report from when you purchased your home, check if it mentions Kitec plumbing. 6. **Contact a Plumber**: If you suspect you have Kitec plumbing but are unsure, hire a professional plumber to conduct a thorough inspection. They can provide a definitive identification and recommend necessary actions. 7. **Review Home Documents**: Check your home's construction documents or contact the builder if possible. Kitec plumbing was commonly used between 1995 and 2007, so homes built during this period are more likely to have it. 8. **Look for Class Action Settlement Information**: If your home has Kitec plumbing, you may be eligible for compensation under class action settlements. Research this to understand your legal options. By following these steps, you can accurately identify whether your home has Kitec plumbing and take appropriate measures for replacement, repair, or legal considerations to ensure your plumbing system remains safe and functional.
Costs and Processes for Replacement or Repair
When dealing with Kitec plumbing, one of the critical considerations is the cost and process involved in either replacing or repairing the system. Kitec plumbing, known for its polyethylene piping and brass fittings, has been plagued by issues such as corrosion, leaks, and premature failure. Here are the key points to consider: **Replacement Costs:** - **Material Costs:** Replacing Kitec plumbing with new materials like PEX, copper, or PVC can be expensive. The cost of new pipes, fittings, and other necessary components can range from $3 to $15 per foot, depending on the material chosen. - **Labor Costs:** Hiring a professional plumber is essential for a proper replacement. Labor costs can vary widely based on location and the complexity of the job but typically range from $50 to $200 per hour. - **Total Cost:** On average, a full replacement of Kitec plumbing in a single-family home can cost anywhere from $5,000 to $20,000 or more, depending on the size of the home and the extent of the replacement needed. **Repair Costs:** - **Temporary Fixes:** For minor leaks or issues, temporary repairs might be feasible. These can include patching leaks or replacing individual fittings. However, these repairs are often short-lived and may not address the underlying problems. - **Cost of Repairs:** The cost of repairs can vary significantly but generally falls between $500 to $2,000 for smaller jobs. However, repeated repairs over time can add up and may eventually exceed the cost of a full replacement. **Processes Involved:** - **Assessment:** Before any work begins, a thorough assessment of the plumbing system is necessary to determine the extent of the damage or deterioration. - **Shut-Off and Drainage:** Water supply lines must be shut off, and the system drained to prevent further damage during the replacement or repair process. - **Removal:** Old Kitec pipes and fittings must be carefully removed to avoid causing additional damage to surrounding structures. - **Installation:** New pipes and fittings are then installed according to local building codes and best practices. - **Testing:** After installation, the system must be thoroughly tested for leaks and proper function. **Legal Considerations:** - **Class Action Settlements:** Homeowners affected by Kitec plumbing issues may be eligible for compensation through class action settlements. These settlements can help offset some of the costs associated with replacement or repair. - **Warranty Claims:** Some homeowners may still have valid warranties on their Kitec systems. Checking the warranty status is crucial before proceeding with any work. - **Local Regulations:** Compliance with local building codes and regulations is mandatory during any plumbing work. Non-compliance can lead to fines and the need for additional repairs. In summary, while repairs might offer temporary relief, full replacement is often the most cost-effective and reliable solution for Kitec plumbing issues in the long run. Understanding the costs and processes involved helps homeowners make informed decisions about how to proceed with addressing their plumbing problems.
Legal Recourse and Compensation Options
When dealing with Kitec plumbing issues, understanding legal recourse and compensation options is crucial for homeowners and property owners. If you have suffered financial losses or property damage due to Kitec plumbing failures, several avenues are available to seek redress. 1. **Class Action Lawsuits**: Many homeowners have joined class action lawsuits against the manufacturers of Kitec plumbing systems. These lawsuits aim to hold the companies responsible for the defective products and seek compensation for damages incurred. Participating in a class action can be a cost-effective way to pursue legal action without the financial burden of individual litigation. 2. **Individual Lawsuits**: If you prefer not to join a class action or if your situation is unique, you can file an individual lawsuit against the manufacturer or installer of the Kitec plumbing system. This approach allows for more personalized attention and potentially higher compensation tailored to your specific circumstances. 3. **Insurance Claims**: Check your homeowner's insurance policy to see if it covers damages resulting from plumbing failures. While insurance may not cover the cost of replacing the entire Kitec system, it might cover repairs or damages caused by leaks or other failures. 4. **Manufacturer Settlements**: In some cases, manufacturers have established settlement funds to compensate homeowners for Kitec-related damages. These settlements can provide a quicker resolution compared to litigation but may require proof of ownership and documentation of damages. 5. **Homeowners Associations (HOAs) and Condominium Boards**: For properties managed by HOAs or condominium boards, these entities may also pursue legal action on behalf of their members. This collective approach can leverage greater negotiating power and shared resources. 6. **Government Assistance**: Depending on the jurisdiction, local or state government agencies might offer assistance programs for homeowners dealing with defective plumbing systems. These programs could include grants, loans, or other forms of financial aid. 7. **Professional Advice**: Consulting with a legal professional who specializes in product liability and consumer protection law is essential. They can help navigate the complexities of your case, advise on the best course of action, and ensure you receive fair compensation. In summary, if you are facing issues with Kitec plumbing, it is important to explore all available legal recourse and compensation options. Whether through class action lawsuits, individual litigation, insurance claims, manufacturer settlements, HOA/condominium board actions, government assistance programs, or professional legal advice, there are multiple paths to seek redress and mitigate financial losses. Understanding these options can help you make informed decisions and protect your investment in your property.