What Are Mirrors Made Out Of

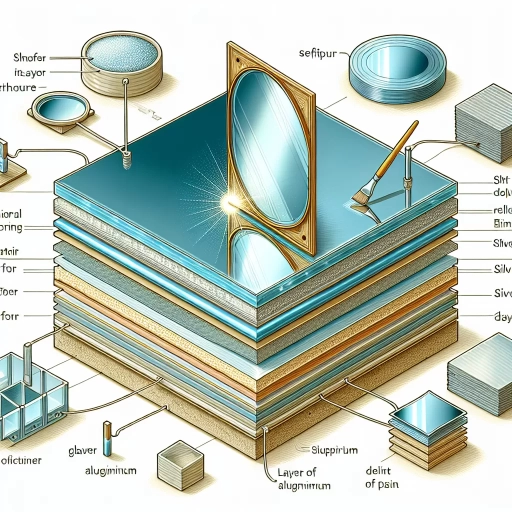
Mirrors, a staple in both everyday life and scientific applications, have a rich history and diverse composition. From ancient civilizations to modern times, the materials used in mirror construction have evolved significantly, reflecting advancements in technology and understanding of materials science. This article delves into the fascinating world of mirror materials, exploring their historical development, common modern uses, and advanced specialty applications. We begin by tracing the historical development of mirror materials, from polished metal surfaces to the introduction of glass and silvered coatings. This historical context sets the stage for understanding how modern mirrors are made, using materials such as glass, aluminum, and silver. Finally, we examine advanced and specialty mirror materials that cater to specific needs, such as telescopic mirrors and laser mirrors. By understanding these different facets of mirror materials, we gain a deeper appreciation for the complexity and innovation behind something as seemingly simple as a mirror. Let us start our journey through time with the historical development of mirror materials.
Historical Development of Mirror Materials
The historical development of mirror materials is a fascinating narrative that spans thousands of years, marked by significant advancements and innovations. From the earliest use of polished metals to the introduction of glass mirrors and finally, the evolution to modern materials, each phase has contributed to the mirrors we use today. In the early stages, humans relied on polished metals such as copper, bronze, and silver to create reflective surfaces, laying the groundwork for future improvements. The introduction of glass mirrors revolutionized the field by offering a more durable and versatile material, leading to widespread use in various settings. However, it was the evolution to modern materials like silvered glass, aluminum-coated mirrors, and advanced coatings that truly transformed the industry, providing higher reflectivity and durability. This journey from primitive metals to sophisticated modern materials highlights human ingenuity and the relentless pursuit of better technology. Let us begin by exploring the **Early Use of Polished Metals**, which set the stage for all subsequent developments in mirror technology.
Early Use of Polished Metals
The early use of polished metals marks a significant milestone in the historical development of mirror materials. Long before the advent of glass mirrors, ancient civilizations recognized the reflective properties of certain metals and leveraged them to create primitive mirrors. One of the earliest recorded uses of polished metal for reflective purposes dates back to ancient Mesopotamia around 4000 BC, where people used polished copper to create mirrors. Similarly, in ancient Egypt around 2900 BC, polished bronze mirrors were common among the elite, often decorated with intricate designs and symbols. These early metal mirrors were not only functional but also held cultural and symbolic significance, reflecting the status and wealth of their owners. In ancient Greece and Rome, polished metal mirrors continued to evolve. The Greeks used polished bronze and silver to create more sophisticated mirrors, while the Romans further refined these techniques by using polished silver and gold. These metals were chosen for their high reflectivity and durability. However, the process of polishing these metals was labor-intensive and time-consuming, making metal mirrors a luxury item accessible only to the wealthy. The use of polished metals for mirrors also extended beyond the Mediterranean region. In Asia, particularly in China and Japan, polished metal mirrors were integral to both practical and ceremonial uses. For instance, the Chinese used polished bronze mirrors as early as the Han Dynasty (206 BC – 220 AD), which were often inscribed with astrological symbols and used for divination purposes. These mirrors not only served as tools for personal grooming but also played roles in spiritual practices and rituals. Despite their widespread use, metal mirrors had several limitations. They were prone to tarnishing, which reduced their reflectivity over time, and they could not be made as large or as thin as glass mirrors would later be. However, the technological advancements in metalworking during these periods laid the groundwork for future innovations in mirror-making. The transition from metal to glass mirrors began with the Romans, who discovered that applying a thin layer of metal to the back of a pane of glass could create a more durable and larger reflective surface. This technique, known as the "silvering" process, would eventually become the standard method for producing mirrors in the Middle Ages and beyond. Thus, while polished metals were the first materials used to create mirrors, their limitations paved the way for the development of more advanced mirror materials, ultimately leading to the modern glass mirrors we use today. In summary, the early use of polished metals in mirror-making represents a crucial chapter in the historical development of mirror materials. From ancient Mesopotamia to medieval Europe, these early mirrors not only served practical purposes but also held significant cultural and symbolic value. Their evolution and eventual limitations set the stage for subsequent technological innovations that would transform how we perceive and interact with reflective surfaces.
Introduction of Glass Mirrors
The introduction of glass mirrors marked a significant milestone in the historical development of mirror materials, transforming the way people perceived and interacted with their reflections. Prior to the advent of glass mirrors, reflective surfaces were crafted from polished metals such as bronze, copper, and silver, which offered limited clarity and durability. The breakthrough came in the late 14th century when Venetian glassmakers discovered a method to apply a thin layer of metallic coating, typically made from tin or mercury, to the back of a pane of glass. This innovative technique, known as the "silvering process," involved coating the glass with a reflective metal alloy, creating a mirror that was not only clearer but also more durable than its metallic predecessors. The production of these early glass mirrors was highly labor-intensive and expensive, making them accessible only to the wealthy. However, as techniques improved and manufacturing processes became more refined, the cost decreased, and glass mirrors began to find their way into more homes. By the 18th century, the development of the silvering process had been further refined by German chemist Justus von Liebig, who introduced the use of a silver nitrate solution to coat the glass. This advancement significantly enhanced the quality and longevity of glass mirrors. The widespread adoption of glass mirrors had profound social and cultural impacts. Mirrors became integral to interior design, reflecting light and creating the illusion of larger spaces in homes. They also played a crucial role in the development of various arts, including painting and photography, by providing artists with accurate reflections for self-portraits and still-life compositions. Additionally, the availability of high-quality mirrors contributed to changes in personal grooming habits and fashion trends, as people could now examine themselves with greater precision. From a scientific perspective, the introduction of glass mirrors facilitated significant advancements in optics and physics. Mirrors were essential for the construction of telescopes and microscopes, enabling scientists to study the universe and microscopic life with unprecedented detail. The reflective properties of glass mirrors also made them crucial for experiments involving light and its behavior, contributing to our understanding of optics and the nature of light itself. In conclusion, the introduction of glass mirrors was a pivotal moment in the historical development of mirror materials. It not only revolutionized personal grooming and interior design but also had far-reaching impacts on science, art, and culture. The evolution from polished metal to silvered glass mirrors set the stage for further innovations in mirror technology, ultimately leading to the modern mirrors we use today. As we continue to explore new materials and technologies for mirrors, it is important to appreciate the foundational role that glass mirrors have played in shaping our understanding of reflection and our interaction with the world around us.
Evolution to Modern Materials
The evolution to modern materials in mirror manufacturing has been a transformative journey, marked by significant technological advancements and innovative discoveries. Historically, mirrors were first made from polished metal surfaces, such as copper and bronze, dating back to ancient civilizations around 4000 BC. These early mirrors were crude and reflective quality was poor due to the inherent properties of the metals used. The next major leap came with the Romans, who developed mirrors made from polished silver, offering a slight improvement in reflectivity but still far from modern standards. The real breakthrough occurred in the late 14th century with the invention of glass mirrors in Venice. Craftsmen applied a thin layer of metallic tin-mercury amalgam to the back of a pane of glass, creating a more reflective and durable mirror. This technique remained the standard for centuries until the late 19th century when German chemist Justus von Liebig introduced the silvering process. By depositing a thin layer of pure silver onto the back of glass using a chemical reduction method, Liebig's mirrors achieved higher reflectivity and became the gold standard for mirror production. The 20th century saw further innovations with the introduction of aluminum and silver-coated mirrors. In the 1950s, aluminum replaced silver as the preferred reflective material due to its lower cost and easier application process. Aluminum-coated mirrors were produced using vacuum deposition techniques, where aluminum was evaporated and deposited onto the glass surface in a vacuum chamber. This method allowed for mass production and improved durability. In recent years, advancements in nanotechnology and thin-film coatings have led to the development of even more sophisticated mirror materials. Dielectric mirrors, for instance, use layers of dielectric materials to achieve high reflectivity without the need for metals. These mirrors are particularly useful in laser technology and optical instruments where high precision is required. Additionally, the use of silicon dioxide and titanium dioxide coatings has enhanced mirror durability and resistance to environmental factors such as moisture and UV light. Modern mirrors also incorporate advanced materials like silver-gallium alloys and indium tin oxide (ITO) for specialized applications. For example, ITO-coated mirrors are used in smart glass technology where they can switch between reflective and transparent states based on electrical signals. These advancements not only improve the aesthetic appeal but also expand the functional capabilities of mirrors beyond simple reflection. In summary, the evolution of mirror materials from ancient polished metals to modern nanotechnology-based coatings reflects human ingenuity and technological progress. Each innovation has significantly improved reflectivity, durability, and versatility, transforming mirrors from simple reflective surfaces into sophisticated tools with diverse applications across various industries. This historical development underscores the continuous quest for better materials and manufacturing techniques that drive innovation in mirror technology.
Common Materials Used in Modern Mirrors
Modern mirrors are crafted from a variety of materials, each contributing to their reflective quality, durability, and aesthetic appeal. At the heart of mirror technology are the coatings that provide the reflective surface. This article delves into the common materials used in modern mirrors, focusing on three key areas: Aluminum and Silver Coatings, Glass and Acrylic Substrates, and Specialty Mirrors: Dielectric and Metallic Coatings. Aluminum and Silver Coatings are pivotal in creating the reflective layer of mirrors. These metals are chosen for their high reflectivity and ability to be thinly applied, ensuring a clear and distortion-free reflection. The choice between aluminum and silver often depends on the intended use of the mirror, with silver offering higher reflectivity but being more expensive and prone to tarnishing. Glass and Acrylic Substrates serve as the base material for most mirrors. Glass is the traditional choice due to its smooth surface and durability, while acrylic substrates offer a lighter and shatter-resistant alternative, making them ideal for safety mirrors. Specialty Mirrors, such as those with Dielectric and Metallic Coatings, are designed for specific applications like laser technology and telescopes. These coatings enhance the mirror's performance by minimizing absorption and maximizing reflectivity in particular wavelengths. Understanding these materials is crucial for appreciating the complexity and innovation behind modern mirror manufacturing. Let's begin by exploring the role of Aluminum and Silver Coatings in creating the reflective surfaces that define our mirrors today.
Aluminum and Silver Coatings
In the realm of modern mirror manufacturing, aluminum and silver coatings play pivotal roles due to their reflective properties and durability. Aluminum coatings, for instance, are widely used in mirrors because of their cost-effectiveness and high reflectivity. When applied to the back of a pane of glass, aluminum creates a reflective surface that is both durable and resistant to corrosion. This process involves sputtering or evaporation techniques to deposit a thin layer of aluminum onto the glass. While aluminum mirrors offer excellent value for money, they have a slightly lower reflectivity compared to their silver-coated counterparts, typically around 85-90% versus silver's 95-98%. However, this difference is often negligible for general use, making aluminum-coated mirrors a popular choice for residential and commercial applications. Silver coatings, on the other hand, are renowned for their superior reflectivity and are often used in high-quality mirrors where optimal light reflection is crucial. The process of applying silver involves electroplating or chemical deposition methods to ensure a uniform and thin layer. Silver's high reflectivity makes it ideal for applications requiring precise optical performance, such as in telescopes, laser mirrors, and other scientific instruments. Despite its superior reflective qualities, silver is more prone to tarnishing than aluminum due to its reactivity with air and moisture. To mitigate this issue, manufacturers often apply a protective clear coating over the silver layer to enhance its longevity. The choice between aluminum and silver coatings depends on the intended use of the mirror. For everyday purposes like bathroom mirrors or decorative pieces, aluminum-coated mirrors suffice due to their affordability and adequate reflectivity. However, for specialized applications where maximum light reflection is essential, silver-coated mirrors are the preferred option despite their higher cost and maintenance requirements. Both materials have contributed significantly to the advancement of mirror technology, offering a balance between cost, performance, and durability that caters to diverse needs across various industries. In addition to their reflective properties, both aluminum and silver coatings have undergone significant advancements in terms of manufacturing processes. Modern techniques such as magnetron sputtering and ion-assisted deposition have improved the uniformity and adhesion of these coatings, leading to mirrors with enhanced optical clarity and longer lifespans. These advancements have also enabled the production of mirrors with specialized coatings that offer additional benefits like anti-reflective coatings or coatings with specific spectral reflectance characteristics. Overall, aluminum and silver coatings remain integral components in the production of modern mirrors, each offering unique advantages that cater to different requirements. Whether it's the budget-friendly yet reliable option of aluminum or the high-performance capabilities of silver, these materials continue to drive innovation in mirror technology, ensuring that mirrors remain an essential part of our daily lives and scientific endeavors alike.
Glass and Acrylic Substrates
In the realm of modern mirrors, two substrates stand out for their durability, aesthetic appeal, and versatility: glass and acrylic. **Glass substrates** have been the traditional choice for mirrors due to their clarity, strength, and ability to provide a flawless reflective surface. When coated with a thin layer of metal, typically silver or aluminum, glass mirrors offer superior reflectivity and a crisp, undistorted image. The process involves applying the metal coating to the back of the glass using electroplating or sputtering techniques, ensuring a uniform and durable finish. Glass mirrors are widely used in both residential and commercial settings because they are easy to clean, resistant to scratches, and can withstand various environmental conditions. However, they can be heavy and may shatter upon impact, which has led to the development of alternative materials. **Acrylic substrates**, on the other hand, offer a lighter and more impact-resistant alternative to glass. Acrylic mirrors are made from polymethyl methacrylate (PMMA), a synthetic resin known for its transparency and flexibility. These mirrors are particularly useful in applications where safety is a priority, such as in children's rooms, gyms, and public spaces. Unlike glass, acrylic mirrors do not shatter into sharp pieces; instead, they may crack or break into larger, safer fragments. The reflective coating is applied similarly to glass mirrors but often involves additional layers to enhance durability and UV resistance. Acrylic mirrors also offer greater design flexibility due to their ability to be molded into various shapes and sizes. However, they may not provide the same level of reflectivity as glass mirrors and can be more prone to scratches and chemical damage. Despite these differences, both glass and acrylic substrates play crucial roles in modern mirror manufacturing. Glass remains the gold standard for high-quality mirrors due to its superior optical clarity and durability, while acrylic offers a practical solution for safety-conscious applications. The choice between these substrates often depends on the intended use of the mirror, with glass being ideal for decorative purposes and acrylic suited for functional or safety-driven needs. In summary, the combination of glass and acrylic substrates allows for a wide range of mirror types that cater to various needs, ensuring that there is a suitable option available for every context in which mirrors are used.
Specialty Mirrors: Dielectric and Metallic Coatings
Specialty mirrors, particularly those with dielectric and metallic coatings, play a crucial role in various advanced applications due to their unique properties and functionalities. **Dielectric mirrors** are designed with multiple layers of dielectric materials, typically oxides or fluorides, which are deposited on a substrate. These layers are carefully engineered to create a high-reflectivity surface through the principle of constructive interference. When light hits the mirror, the layers reflect specific wavelengths, allowing for precise control over the reflected spectrum. This makes dielectric mirrors indispensable in laser technology, where they are used as beam splitters, cavity mirrors, and output couplers. Their high reflectivity and durability under intense light conditions make them ideal for applications requiring minimal absorption and thermal stability. **Metallic mirrors**, on the other hand, utilize thin films of metals such as aluminum or silver to achieve high reflectivity. These metals are chosen for their excellent optical properties; aluminum offers a broad spectral range of reflectivity, while silver provides the highest reflectivity in the visible spectrum but is more prone to tarnishing. Metallic mirrors are widely used in telescopes, solar concentrators, and other optical instruments where high reflectivity is essential. However, they can suffer from thermal issues and may degrade over time due to environmental factors. To mitigate these issues, protective coatings are often applied to enhance durability without compromising reflectivity. The combination of dielectric and metallic coatings in some specialty mirrors further enhances their performance. For instance, a **dielectric-over-metallic mirror** can leverage the strengths of both technologies: the high reflectivity of metals and the spectral selectivity of dielectrics. This hybrid approach is particularly useful in applications requiring both broad spectral reflectance and specific wavelength control, such as in spectroscopy and interferometry. In addition to their technical advantages, specialty mirrors with dielectric and metallic coatings are also subject to stringent manufacturing processes. Advanced techniques like sputtering and evaporation are employed to deposit the thin layers with precise control over thickness and uniformity. Quality control measures, including interferometry and spectrophotometry, ensure that the mirrors meet the required specifications for their intended use. The versatility and performance of these specialty mirrors have expanded their use beyond traditional optics into fields such as medicine, aerospace, and telecommunications. For example, in medical applications, dielectric mirrors are used in laser-based treatments where precise control over the laser beam is critical. In aerospace, metallic mirrors are integral to solar concentrators that power satellites. In telecommunications, dielectric mirrors are used in optical switches and multiplexers to manage data transmission efficiently. In summary, specialty mirrors with dielectric and metallic coatings represent a pinnacle of modern mirror technology. Their unique properties and applications underscore the importance of material science and engineering in creating high-performance optical components. Whether in scientific research, industrial processes, or cutting-edge technologies, these mirrors continue to play a vital role in advancing various fields by providing unparalleled reflectivity and spectral control.
Advanced and Specialty Mirror Materials
Advanced and specialty mirror materials have revolutionized various fields by offering unique properties tailored to specific applications. These materials are not just reflective surfaces but sophisticated tools that enhance performance, precision, and functionality. For instance, dielectric mirrors are crucial for laser applications due to their high reflectivity and durability under intense light conditions. In contrast, metallic mirrors play a pivotal role in astronomical telescopes, providing the necessary reflectivity and stability for capturing distant celestial images. Additionally, smart mirrors with integrated technology are transforming everyday life by combining traditional reflective capabilities with advanced functionalities such as touch screens, sensors, and display capabilities. Each of these specialty mirrors addresses distinct challenges and opportunities, contributing significantly to their respective domains. As we delve deeper into the world of advanced mirror materials, let's first explore the critical role of dielectric mirrors in laser applications, where their precision and resilience are paramount.
Dielectric Mirrors for Laser Applications
Dielectric mirrors are a cornerstone in laser technology, offering unparalleled performance and durability for high-intensity applications. Unlike traditional metallic mirrors, which can suffer from thermal damage and absorption losses, dielectric mirrors leverage the properties of thin-film coatings to achieve superior reflectivity and stability. These mirrors are constructed by depositing multiple layers of dielectric materials, such as silicon dioxide and titanium dioxide, onto a substrate. The precise control over the thickness and refractive indices of these layers allows for the creation of mirrors with tailored optical properties, including high reflectivity across specific wavelength ranges and minimal absorption. The key advantage of dielectric mirrors in laser applications lies in their ability to withstand high power densities without degradation. This is crucial for lasers used in industrial processes like cutting and welding, where the mirror's integrity directly impacts the system's efficiency and lifespan. Additionally, dielectric mirrors can be designed to operate over a broad spectral range, making them versatile components for various laser systems, from ultraviolet to infrared wavelengths. Their low absorption coefficients ensure that the majority of the incident light is reflected rather than absorbed, reducing the risk of thermal damage and maintaining the mirror's optical quality over time. In advanced laser systems, such as those used in spectroscopy and interferometry, the precision of dielectric mirrors is particularly valuable. These mirrors can be engineered to have extremely high reflectivity (often exceeding 99.9%) and flatness, which are essential for maintaining the coherence and stability of laser beams. Furthermore, dielectric mirrors can be coated with protective layers to enhance their resistance to environmental factors like humidity and contaminants, ensuring consistent performance even in challenging operating conditions. The manufacturing process of dielectric mirrors involves sophisticated techniques such as ion beam sputtering and electron beam evaporation, which allow for the deposition of uniform, defect-free layers. This level of precision is critical for achieving the desired optical characteristics and ensuring the longevity of the mirror. In summary, dielectric mirrors represent a significant advancement in mirror technology, providing a robust and reliable solution for demanding laser applications. Their unique combination of high reflectivity, thermal stability, and versatility makes them an indispensable component in modern laser systems.
Metallic Mirrors for Astronomical Telescopes
Metallic mirrors play a crucial role in astronomical telescopes, offering unique advantages that complement traditional glass mirrors. Unlike glass, which is often used for its optical clarity and durability, metallic mirrors are crafted from materials such as aluminum, silver, or gold. These metals are chosen for their high reflectivity and ability to maintain their reflective properties over a wide range of wavelengths, including infrared and ultraviolet light. One of the primary benefits of metallic mirrors in astronomy is their lightweight nature compared to traditional glass mirrors. This makes them ideal for space-based telescopes where weight is a critical factor. For instance, the James Webb Space Telescope features a segmented primary mirror made of beryllium coated with a thin layer of gold. The use of beryllium allows for a significant reduction in weight while maintaining structural integrity, which is essential for the telescope's precise optics and its ability to operate in the harsh environment of space. Another advantage of metallic mirrors is their ease of fabrication and maintenance. Unlike glass mirrors, which require extensive polishing to achieve the necessary optical quality, metallic mirrors can be produced using simpler techniques such as sputtering or evaporation. This process involves depositing a thin layer of metal onto a substrate, which can be done with high precision and uniformity. Additionally, metallic coatings can be easily reapplied if they degrade over time, extending the lifespan of the mirror without the need for extensive refurbishment. The choice of metal also influences the performance of the mirror. Aluminum, for example, offers high reflectivity in the visible spectrum but can degrade when exposed to air due to oxidation. Silver, on the other hand, has even higher reflectivity across a broader range of wavelengths but tarnishes more easily than aluminum. Gold is often used for its excellent reflectivity in the infrared and its resistance to tarnishing, making it particularly suitable for telescopes focused on infrared astronomy. In terms of application, metallic mirrors are particularly useful in specialized astronomical instruments such as spectrographs and interferometers. These instruments require mirrors that can handle a wide range of wavelengths and maintain their reflective properties under varying conditions. For example, the Atacama Large Millimeter/submillimeter Array (ALMA) uses aluminum-coated mirrors to observe the universe in millimeter and submillimeter wavelengths, providing insights into cold interstellar gas and dust. In summary, metallic mirrors offer a versatile and efficient solution for astronomical telescopes by combining high reflectivity with lightweight construction and ease of maintenance. Their ability to operate across various wavelengths makes them indispensable tools in modern astronomy, enabling scientists to explore the universe with greater precision and depth than ever before. As technology continues to advance, the role of metallic mirrors in astronomical research is likely to expand further, contributing significantly to our understanding of the cosmos.
Smart Mirrors with Integrated Technology
Smart mirrors with integrated technology represent a significant leap forward in the evolution of mirrors, transforming them from simple reflective surfaces into multifunctional devices that enhance daily routines and lifestyles. These advanced mirrors are part of a broader category of specialty mirror materials that incorporate cutting-edge innovations to provide users with a range of benefits. Equipped with features such as touch screens, voice assistants, and internet connectivity, smart mirrors offer a seamless blend of functionality and aesthetics. One of the key features of smart mirrors is their ability to display information in real-time. Users can check the weather forecast, news updates, and even their schedules without needing to glance at their smartphones or tablets. This integration is often achieved through built-in displays or projection technology that overlays digital information onto the mirror's surface. For instance, some smart mirrors come with augmented reality capabilities, allowing users to try on virtual outfits or see how different hairstyles would look without actually making any changes. Another significant advantage of smart mirrors is their health and wellness monitoring capabilities. Many models include sensors that track vital signs such as heart rate, blood pressure, and even skin health. These mirrors can also offer personalized recommendations for skincare routines based on the user's skin type and condition. Additionally, some smart mirrors feature built-in LED lighting that adjusts color temperature and brightness according to the time of day, helping to regulate circadian rhythms and improve sleep quality. From a practical standpoint, smart mirrors also enhance the user experience through voice control and gesture recognition. Users can adjust lighting settings, play music, or access various apps using voice commands or simple hand gestures. This hands-free operation makes it easier to get ready in the morning or unwind before bed without having to physically interact with multiple devices. The design and construction of smart mirrors also reflect their advanced nature. They often feature sleek, minimalist designs that fit seamlessly into modern bathrooms or bedrooms. The materials used are typically high-quality glass with anti-fog coatings and scratch-resistant surfaces, ensuring durability and longevity. Some models even include anti-reflective coatings to minimize glare and provide a clearer view. In terms of privacy and security, smart mirrors are designed with robust safeguards to protect user data. Many models come with encryption protocols and secure data storage to ensure that personal information remains confidential. Users can also customize privacy settings to control what data is shared and how it is used. Overall, smart mirrors with integrated technology exemplify the innovative spirit behind advanced and specialty mirror materials. By combining traditional reflective capabilities with modern technological advancements, these mirrors not only enhance functionality but also contribute to a more convenient, informed, and healthier lifestyle. As technology continues to evolve, it is likely that smart mirrors will become even more sophisticated, further blurring the lines between mirrors and interactive devices.