What Is Engineered Stone

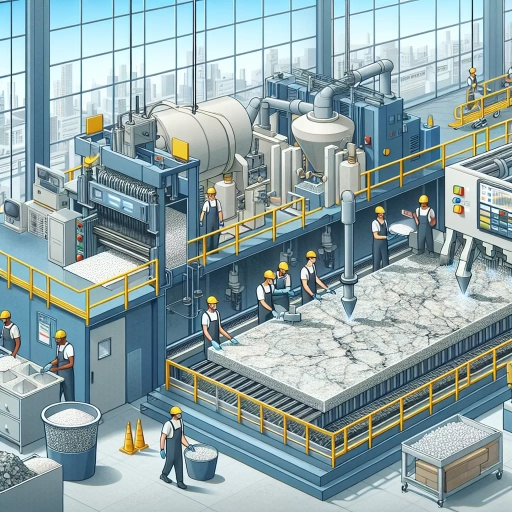
Engineered stone, a modern marvel in the world of construction and design, has revolutionized the way we think about building materials. This innovative product combines the natural beauty of stone with the durability and versatility of engineered materials. In this article, we will delve into the world of engineered stone, starting with an **Introduction to Engineered Stone**, where we explore its origins and evolution. We will then examine the **Composition and Manufacturing Process**, uncovering the intricate details of how this material is created. Finally, we will discuss the **Benefits and Applications of Engineered Stone**, highlighting its advantages and various uses in both residential and commercial settings. By understanding these key aspects, readers will gain a comprehensive insight into why engineered stone has become a preferred choice for architects, designers, and homeowners alike. Let's begin our journey into the realm of engineered stone with an **Introduction to Engineered Stone**.
Introduction to Engineered Stone
Engineered stone, a material that has revolutionized the construction and design industries, offers a blend of durability, aesthetic appeal, and versatility. This high-quality material is not just a modern innovation but has roots in historical developments that have shaped its current form. To understand engineered stone fully, it is essential to delve into its definition and origins, which set the foundation for its widespread adoption. Historically, the development of engineered stone has been a gradual process, influenced by technological advancements and changing market demands. From its early beginnings to the sophisticated manufacturing processes of today, engineered stone has evolved significantly. The market demand for engineered stone has seen substantial growth over the years, driven by its superior performance characteristics and the increasing need for sustainable building materials. As architects, designers, and homeowners seek materials that combine functionality with style, engineered stone has emerged as a preferred choice. To grasp the essence of engineered stone, we must first explore its **Definition and Origins**, which will provide a clear understanding of what this material is and how it came into being.
Definition and Origins
Engineered stone, a versatile and durable material, has its roots in the early 20th century when the concept of combining natural stone with advanced manufacturing techniques first emerged. The term "engineered stone" refers to a composite material that is primarily composed of natural stone particles, such as quartz, granite, or marble, which are bound together using a polymer resin. This innovative blend of natural and synthetic components enhances the physical properties of the stone, making it more resistant to scratches, stains, and heat compared to its purely natural counterparts. The origins of engineered stone can be traced back to the 1960s in Italy, where companies like Breton S.p.A. pioneered the development of this technology. Breton's founder, Marcello Toncelli, patented a process known as "BRETONSTONE," which involved mixing crushed stone with resin and then subjecting it to high pressure and heat. This process allowed for the creation of large slabs that could be used for countertops, flooring, and other architectural applications. Since its inception, engineered stone has evolved significantly due to advancements in technology and manufacturing processes. Modern engineered stone products often include additional materials such as pigments for coloration and other additives to enhance performance characteristics. The manufacturing process typically involves several stages: mixing the raw materials (stone particles and resin), compacting the mixture under high pressure, and then curing it in an oven or using UV light. The definition of engineered stone encompasses not only its composition but also its unique benefits. It is known for its uniformity in color and pattern, which contrasts with the natural variability seen in solid stone. Additionally, engineered stone is easier to maintain than natural stone because it is less porous and does not require periodic sealing. These attributes have made engineered stone a popular choice for both residential and commercial projects where durability and aesthetic appeal are paramount. In summary, engineered stone is a sophisticated material that leverages the best qualities of natural stone while overcoming some of its limitations through advanced engineering techniques. Its origins in Italy during the mid-20th century laid the groundwork for what has become a staple in modern construction and design. As technology continues to advance, engineered stone remains an innovative solution for those seeking a durable yet visually appealing material for various applications.
Historical Development
The historical development of engineered stone is a narrative of technological innovation and material evolution, spanning several decades. The concept of engineered stone emerged in the mid-20th century, driven by the need for durable, versatile, and aesthetically pleasing surfaces for architectural and design applications. Initially, the first engineered stones were developed in Italy in the 1960s by Breton S.p.A., a company that pioneered the use of resin to bind together natural stone particles. This breakthrough allowed for the creation of materials that combined the beauty of natural stone with enhanced strength and resistance to wear and tear. In the following decades, advancements in manufacturing processes and the introduction of new technologies further refined engineered stone. The 1980s saw significant improvements in the quality and variety of engineered stones, with companies like Caesarstone and Silestone entering the market. These brands introduced new production techniques that incorporated quartz, one of the hardest minerals found in nature, into their products. Quartz-based engineered stones quickly gained popularity due to their exceptional durability, low maintenance requirements, and wide range of color options. The 1990s and early 2000s witnessed a global expansion of the engineered stone industry, with companies from various regions contributing to its growth. This period also saw increased focus on sustainability and environmental responsibility, leading to the development of eco-friendly engineered stone products. Manufacturers began using recycled materials and implementing more energy-efficient production processes, appealing to consumers who valued both performance and environmental stewardship. Today, engineered stone continues to evolve with ongoing research and development. Modern manufacturing techniques allow for precise control over the composition and appearance of the final product, enabling the creation of highly customized surfaces that cater to diverse design needs. Additionally, advancements in resin technology have improved the chemical resistance and overall performance of engineered stones, making them suitable for a wide range of applications from residential kitchens to commercial spaces. The historical development of engineered stone is a testament to human ingenuity and the relentless pursuit of innovation. From its humble beginnings in Italy to its current global presence, engineered stone has transformed the way we design and build our environments, offering a unique blend of natural beauty, technological sophistication, and practical functionality. As technology continues to advance, it is likely that engineered stone will remain a cornerstone in the world of architecture and design for years to come.
Market Demand and Growth
The market demand for engineered stone has experienced significant growth in recent years, driven by several key factors. One primary driver is the increasing preference for durable and low-maintenance materials in both residential and commercial construction projects. Engineered stone, often made from a combination of natural stone particles and resin, offers superior durability and resistance to scratches, stains, and heat compared to natural stone. This makes it an attractive option for homeowners and businesses seeking long-lasting surfaces that require minimal upkeep. Another factor contributing to the growth is the expanding range of aesthetic options available. Modern manufacturing techniques allow for a wide variety of colors, patterns, and textures, enabling consumers to choose engineered stone that closely mimics the appearance of natural stone or offers unique designs not found in nature. This versatility appeals to architects, designers, and homeowners looking to create visually appealing spaces without compromising on functionality. The rise in global construction activities also plays a crucial role in boosting demand. As urbanization continues to grow, there is an increased need for high-quality building materials that can withstand the demands of modern living. Engineered stone meets these needs by providing a robust yet stylish solution for countertops, flooring, and other surfaces. Additionally, environmental concerns are influencing consumer choices, with many opting for materials that have a lower ecological footprint. Engineered stone is often seen as a more sustainable option compared to natural stone due to its reduced need for quarrying and transportation. This shift towards eco-friendly products further fuels the market's growth. Technological advancements in manufacturing processes have also improved the quality and affordability of engineered stone. Innovations such as automated production lines and advanced resin formulations have enhanced the product's performance while reducing production costs. This has made engineered stone more accessible to a broader market segment, contributing to its increased adoption. Finally, the growing awareness of health and hygiene has led to an increased demand for surfaces that are easy to clean and resistant to bacteria and other microorganisms. Engineered stone's non-porous nature makes it an ideal choice for kitchens and bathrooms where cleanliness is paramount. In summary, the market demand for engineered stone is driven by its durability, aesthetic versatility, growing construction needs, environmental benefits, technological improvements, and health considerations. These factors collectively contribute to the robust growth seen in this sector and position engineered stone as a preferred material in contemporary building and design projects.
Composition and Manufacturing Process
The composition and manufacturing process of any product are crucial elements that determine its quality, functionality, and overall performance. This intricate process involves several key stages, each playing a vital role in the final outcome. First, the selection and procurement of raw materials set the foundation for the entire production cycle. Understanding the properties and characteristics of these materials is essential to ensure they meet the required standards. Next, the manufacturing techniques employed can significantly impact the product's durability, efficiency, and aesthetic appeal. Advanced technologies and methodologies can enhance production efficiency while maintaining high standards. Finally, rigorous quality control measures are implemented to guarantee that the final product adheres to specifications and safety regulations. By focusing on these three critical aspects—raw materials used, manufacturing techniques, and quality control measures—manufacturers can produce high-quality products that satisfy consumer needs and expectations. Let's begin by examining the raw materials used in this process, as they are the building blocks upon which everything else is constructed.
Raw Materials Used
Engineered stone, a versatile and durable material, is crafted from a combination of raw materials that are carefully selected and processed to achieve its unique properties. The primary components include natural stone aggregates, such as quartz, granite, and marble, which provide the material's strength and aesthetic appeal. These aggregates are typically sourced from quarries around the world and are chosen for their quality and consistency. Another crucial raw material is resin, usually a polymer like polyester or epoxy, which acts as the binder that holds the stone particles together. This resin not only enhances the material's durability but also allows for the incorporation of pigments to create a wide range of colors and patterns. In addition to these main components, engineered stone may include other additives such as silica, calcium carbonate, and aluminum oxide to improve its performance characteristics. Silica, for instance, helps in enhancing the material's hardness and resistance to scratches, while calcium carbonate can contribute to its stability and workability. Aluminum oxide is often added to increase the material's abrasion resistance, making it suitable for high-traffic areas. The manufacturing process involves a meticulous blending of these raw materials in specific proportions, followed by a high-pressure and high-temperature treatment that compacts and cures the mixture. This process ensures that the engineered stone achieves optimal density and uniformity, resulting in a product that is both visually appealing and functionally superior. The precise control over the composition and manufacturing process allows for the creation of engineered stone products that meet specific industry standards and customer requirements, making it an ideal choice for various applications including countertops, flooring, and architectural features. By leveraging these carefully selected raw materials and advanced manufacturing techniques, engineered stone offers a blend of natural beauty and engineered performance that is hard to match with traditional natural stone products.
Manufacturing Techniques
In the realm of engineered stone, manufacturing techniques play a crucial role in transforming raw materials into durable, aesthetically pleasing products. The process begins with the selection of high-quality aggregates, typically quartz, granite, or marble, which are then mixed with resin binders and other additives. This mixture is subjected to a series of precise manufacturing steps. First, the raw materials are ground into fine particles to ensure uniformity and consistency. Next, these particles are combined with resin binders in a specific ratio, often involving advanced technologies like vacuum mixing to eliminate air pockets and enhance density. The mixture is then pressed into slabs using high-pressure presses, which can exert forces up to 100 tons per square inch. This pressure compacts the material, ensuring it is dense and free from defects. After pressing, the slabs undergo a curing process in controlled environments where they are exposed to heat and pressure to fully polymerize the resin. Once cured, the slabs are polished to a high gloss using diamond-coated polishing wheels, revealing the natural beauty of the aggregates while enhancing durability. Quality control measures are integrated throughout this process, including inspections for color consistency, texture uniformity, and structural integrity. Advanced manufacturing techniques such as CNC machining and digital printing can also be employed to create intricate designs and patterns on the surface of the engineered stone. These methods not only improve the aesthetic appeal but also allow for customization to meet specific architectural or design requirements. Overall, the combination of advanced materials science and sophisticated manufacturing processes results in engineered stone products that are not only visually stunning but also highly durable and resistant to wear and tear, making them ideal for various applications ranging from kitchen countertops to commercial flooring.
Quality Control Measures
Quality control measures are integral to the composition and manufacturing process of engineered stone, ensuring that the final product meets stringent standards of durability, aesthetics, and performance. At the outset, raw materials such as quartz, granite, and marble aggregates are meticulously selected and inspected for purity and consistency. These materials are then mixed with a binder, typically a polymer resin, and other additives to enhance strength and color uniformity. The mixture is subjected to rigorous testing for chemical composition and physical properties to guarantee adherence to specifications. During the manufacturing process, quality control is maintained through several checkpoints. First, the mixture is compacted under high pressure and heat in a vacuum environment to eliminate air pockets and ensure uniform density. This step is crucial as it directly impacts the stone's strength and resistance to cracks. Post-compaction, the slabs undergo a series of inspections for defects such as cracks, discolorations, or uneven surfaces. Advanced technologies like computer-aided quality control systems and optical scanners are often employed to detect even minor imperfections. Further quality assurance involves testing for mechanical properties such as flexural strength, compressive strength, and abrasion resistance. These tests simulate real-world conditions to ensure that the engineered stone can withstand various environmental and usage stresses. Additionally, chemical resistance tests are conducted to verify the stone's ability to resist stains from common household substances. The finishing process also includes stringent quality checks. The slabs are polished to a high gloss using diamond-coated tools, and their surface quality is evaluated for evenness and shine. Any slab that fails to meet these criteria is removed from production. Finally, before being shipped to customers, each slab undergoes a comprehensive visual inspection by trained quality control specialists who check for any visible defects or irregularities. This multi-layered approach to quality control ensures that every piece of engineered stone produced meets the highest standards of quality, reliability, and aesthetic appeal, making it a trusted choice for architects, designers, and homeowners alike. By integrating these rigorous quality control measures into every stage of the composition and manufacturing process, manufacturers can guarantee that their engineered stone products will perform exceptionally well over time.
Benefits and Applications of Engineered Stone
Engineered stone, a composite material made from natural stone particles and resin, offers a multitude of benefits and applications that make it a preferred choice in various industries. One of the primary advantages of engineered stone is its aesthetic and design flexibility, allowing for a wide range of colors, patterns, and finishes that can be tailored to suit any architectural or interior design vision. Additionally, engineered stone is renowned for its durability and ease of maintenance, making it an ideal material for high-traffic areas and everyday use. From a sustainability perspective, engineered stone also boasts a lower environmental impact compared to natural stone, as it reduces waste and conserves natural resources. These attributes collectively contribute to the versatility and appeal of engineered stone, making it a go-to option for designers, architects, and homeowners alike. As we delve deeper into the benefits of engineered stone, let's first explore its aesthetic and design flexibility, which sets it apart from other materials in the market.
Aesthetic and Design Flexibility
Aesthetic and design flexibility are among the most compelling benefits of engineered stone, making it a highly sought-after material in various applications. Engineered stone, often composed of natural stone particles bonded together with resin, offers an unparalleled range of design possibilities. Unlike natural stone, which is limited by its inherent patterns and colors, engineered stone can be manufactured to mimic any aesthetic. This versatility allows architects, designers, and homeowners to achieve precise color schemes and patterns that align perfectly with their vision. For instance, engineered stone can replicate the look of marble, granite, or quartz while offering superior durability and consistency. The manufacturing process of engineered stone involves mixing natural stone particles with resin and pigments, which can be tailored to produce a wide array of colors and textures. This flexibility extends to the creation of unique and custom designs that cannot be found in natural stone. Additionally, engineered stone can be fabricated into various shapes and sizes, making it ideal for complex architectural designs. The ability to produce large slabs with minimal seams further enhances its aesthetic appeal, providing a seamless look that is particularly desirable in high-end residential and commercial projects. Moreover, the design flexibility of engineered stone is not limited to its visual appeal; it also extends to its functional capabilities. Engineered stone can be engineered to have specific properties such as increased durability, resistance to scratches and stains, and ease of maintenance. This makes it an excellent choice for high-traffic areas like kitchens and bathrooms where both form and function are crucial. The material's adaptability also allows it to be used in a variety of applications beyond countertops, including flooring, wall cladding, and even furniture. In terms of sustainability, engineered stone offers another layer of design flexibility. By utilizing recycled materials and minimizing waste during production, engineered stone can contribute to more environmentally friendly building practices. This aligns well with modern design trends that emphasize eco-friendliness without compromising on aesthetics or performance. Overall, the aesthetic and design flexibility of engineered stone make it an indispensable tool for creatives seeking to bring their most ambitious projects to life. Whether it's achieving a specific color palette, creating intricate patterns, or ensuring durability and sustainability, engineered stone provides the perfect blend of form and function that meets the demands of contemporary design. Its versatility ensures that it remains a preferred choice across various sectors, from residential interiors to commercial spaces, where both beauty and practicality are paramount.
Durability and Maintenance
Engineered stone, a composite material made from natural stone particles and resin, offers exceptional durability and ease of maintenance, making it a highly sought-after choice for various applications. Its robust construction ensures that it can withstand the rigors of daily use without compromising on aesthetics. Unlike natural stone, which can be prone to cracking and staining, engineered stone is more resistant to scratches, heat, and chemicals. This durability translates into a longer lifespan for surfaces such as countertops, flooring, and wall cladding, reducing the need for frequent repairs or replacements. Maintenance of engineered stone is also remarkably straightforward. The non-porous nature of this material prevents the absorption of liquids, thereby minimizing the risk of stains and bacterial growth. Cleaning is as simple as wiping down the surface with a mild detergent and water, eliminating the need for specialized cleaning products or sealants that are often required for natural stone. Additionally, engineered stone does not require periodic sealing, which further reduces maintenance costs and effort over time. The combination of durability and low maintenance makes engineered stone an ideal choice for high-traffic areas such as commercial kitchens, restaurants, and public spaces. In residential settings, it provides homeowners with peace of mind knowing that their surfaces will remain pristine with minimal upkeep. This balance of performance and practicality underscores why engineered stone is increasingly preferred in both architectural and interior design projects, offering a blend of beauty, functionality, and long-term value.
Environmental Impact and Sustainability
Engineered stone, a composite material primarily made from natural stone particles and resin, offers significant environmental benefits and contributes to sustainability in several key ways. Unlike natural stone, which often requires extensive quarrying and processing that can harm ecosystems and deplete natural resources, engineered stone is manufactured using recycled materials and waste stone particles. This reduces the need for new raw material extraction, thereby minimizing the environmental impact associated with quarrying and transportation. Additionally, the production process of engineered stone is more energy-efficient compared to traditional stone processing, as it involves lower energy consumption and generates less waste. The use of engineered stone also promotes sustainable practices in construction and design by providing a durable and long-lasting material that reduces the need for frequent replacements and repairs, thus lowering overall resource consumption over time. Furthermore, engineered stone can be recycled at the end of its life cycle, further reducing waste and supporting a circular economy. Its versatility and aesthetic appeal make it an attractive choice for architects and designers seeking to balance functionality with environmental responsibility, making engineered stone a valuable component in sustainable building practices. By choosing engineered stone, consumers can support environmentally friendly manufacturing processes while enjoying the beauty and durability of a high-quality material.