What Is Rc210 Slip

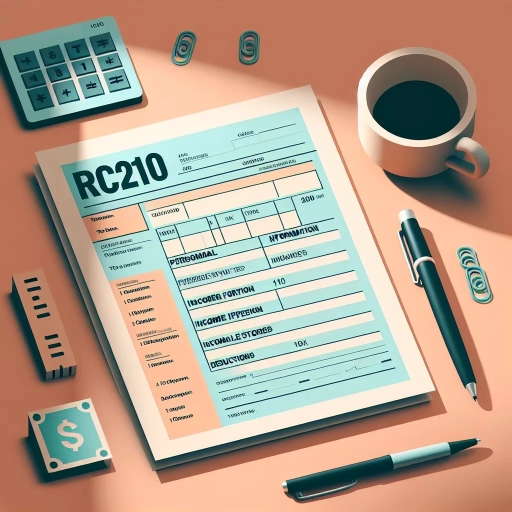
In the realm of construction, particularly in the context of concrete and masonry projects, the term "RC210 slip" has become increasingly significant. This specialized material plays a crucial role in ensuring the structural integrity and durability of buildings. To fully appreciate its importance, it is essential to delve into what RC210 slip is, its definition, and the context in which it is used. Understanding RC210 slip involves recognizing its unique properties and how it differs from other materials. Beyond its definition, it is vital to explore the importance of RC210 slip in construction, where it serves as a critical component in maintaining the stability and longevity of structures. However, working with RC210 slip also presents challenges that must be addressed through best practices to ensure optimal results. By examining these aspects, we can gain a comprehensive understanding of RC210 slip and its indispensable role in modern construction. Let's begin by Understanding RC210 Slip: Definition and Context.
Understanding RC210 Slip: Definition and Context
Understanding RC210 Slip is a multifaceted topic that requires a comprehensive approach to fully grasp its significance. At its core, RC210 Slip is a specific type of ceramic slip used in various industrial applications, but its importance extends beyond its technical specifications. To delve into the essence of RC210 Slip, it is crucial to explore its historical background, technical specifications, and industry applications. Historically, the development of RC210 Slip was influenced by the need for high-quality ceramic materials in manufacturing processes, reflecting broader trends in industrial innovation. Technically, RC210 Slip adheres to strict standards that ensure its consistency and reliability across different uses. In terms of industry applications, it plays a vital role in sectors such as ceramics, construction, and engineering due to its unique properties. By examining these aspects, we can gain a deeper understanding of how RC210 Slip has evolved and why it remains a critical component in modern manufacturing. Let us begin by tracing the historical background of RC210 Slip, which sets the stage for understanding its current significance and widespread use.
Historical Background of RC210 Slip
The RC210 slip, a critical component in the realm of construction and engineering, has a historical background that underscores its evolution and importance. The concept of slips, or more broadly, formwork systems, dates back to ancient civilizations where builders used wooden molds to shape concrete and stone structures. However, the modern RC210 slip, specifically designed for reinforced concrete (RC) construction, emerged during the 20th century as a response to the increasing demand for efficient and durable building techniques. In the early 20th century, as urbanization accelerated and cities expanded, there was a pressing need for faster and more reliable construction methods. The introduction of reinforced concrete revolutionized the industry by offering a strong, versatile material that could be molded into various forms. The RC210 slip was developed as part of this innovation wave, designed to facilitate the creation of complex shapes and structures with precision and speed. The term "RC210" itself refers to specific dimensions and standards within the industry. The "RC" denotes reinforced concrete, while "210" typically indicates the slip's dimensions or capacity. This standardization was crucial for ensuring uniformity and interoperability across different construction projects and regions. During the post-World War II era, there was a significant surge in infrastructure development and urban renewal projects. This period saw the widespread adoption of RC210 slips as they became integral to the construction of high-rise buildings, bridges, and other large-scale infrastructure. The slips allowed for the rapid casting of concrete sections, enabling builders to meet the high demand for housing and public works. Technological advancements in materials science and engineering further enhanced the functionality of RC210 slips. Improvements in steel reinforcement, concrete mixtures, and formwork materials led to stronger, more durable structures that could withstand various environmental conditions. Additionally, innovations in hydraulic systems and mechanized formwork enabled faster setup and dismantling processes, reducing labor costs and project timelines. Today, the RC210 slip remains a cornerstone in modern construction practices. Its historical development reflects the continuous quest for efficiency, durability, and innovation within the industry. As construction techniques continue to evolve with advancements in technology and materials science, the RC210 slip stands as a testament to the ingenuity of past engineers and builders who laid the groundwork for contemporary architectural marvels. Understanding the historical background of the RC210 slip provides valuable context for appreciating its role in contemporary construction. It highlights how this seemingly mundane component has been shaped by centuries of technological progress and societal needs, ultimately contributing to the robust infrastructure that underpins modern society. This context is essential for anyone seeking to grasp the full significance of the RC210 slip in both its definition and practical application.
Technical Specifications and Standards
When delving into the intricacies of the RC210 slip, it is crucial to understand the technical specifications and standards that govern its use and application. Technical specifications are detailed descriptions of the requirements and characteristics that a product or system must meet to ensure it performs as intended. In the context of RC210 slips, these specifications typically include dimensions, material properties, tensile strength, and surface finish. For instance, the RC210 slip might be specified to have a certain diameter, wall thickness, and material composition that adheres to industry standards such as those set by the American Society for Testing and Materials (ASTM) or the International Organization for Standardization (ISO). Standards play a pivotal role in ensuring consistency and reliability across different manufacturers and applications. They provide a common language and framework that helps in the design, production, and testing of components like the RC210 slip. Compliance with these standards not only ensures safety but also facilitates interoperability between different parts of a system. For example, if an RC210 slip is designed to meet specific torque and pressure standards, it can be confidently used in various mechanical assemblies without compromising performance or safety. Moreover, technical specifications and standards are often developed through collaborative efforts involving industry experts, regulatory bodies, and research institutions. This collaborative approach ensures that the specifications are based on best practices and reflect the latest advancements in technology. In the case of RC210 slips, adherence to these standards might involve rigorous testing protocols to validate their performance under various conditions such as temperature, pressure, and wear. Understanding these technical specifications and standards is essential for engineers, manufacturers, and users alike. It allows them to make informed decisions about the suitability of the RC210 slip for specific applications. For instance, knowing that an RC210 slip meets certain standards can provide assurance about its durability and reliability in high-stress environments. This knowledge also facilitates maintenance and repair processes by ensuring that replacement parts are compatible and meet the required specifications. In summary, the technical specifications and standards surrounding the RC210 slip are foundational elements that ensure its proper function, safety, and compatibility. By adhering to these standards, manufacturers can produce high-quality components that meet industry benchmarks, while users can rely on consistent performance and reliability. This alignment with technical specifications and standards is a critical aspect of understanding the RC210 slip in its broader context within mechanical systems.
Industry Applications and Uses
In the realm of industrial applications, the RC210 slip plays a pivotal role in ensuring the safety and efficiency of various processes. This specialized slip, defined by its unique characteristics and context, is integral to industries where precise control over materials and surfaces is crucial. For instance, in the manufacturing sector, RC210 slips are used to prevent slipping and falling hazards on floors and walkways, particularly in areas where oils, chemicals, or water may be present. This is especially important in facilities such as chemical plants, oil refineries, and food processing units where spills are common and can lead to dangerous conditions. In construction, RC210 slips are often applied to scaffolding and ladders to enhance grip and stability, reducing the risk of accidents among workers. The automotive industry also benefits from these slips as they are used in garages and service stations to prevent vehicles from slipping on ramps or lifts. Additionally, in healthcare settings, RC210 slips can be applied to hospital floors and patient care areas to minimize the risk of patient falls, which is a significant concern given the vulnerability of hospital populations. The agricultural sector leverages RC210 slips in barns and livestock facilities to ensure that animals do not slip on wet or dirty surfaces, thereby preventing injuries and maintaining animal welfare. Furthermore, in public spaces such as stadiums, arenas, and shopping malls, these slips are applied to stairs and walkways to enhance safety during events or heavy foot traffic. The versatility of RC210 slips extends into marine environments as well. They are used on boat decks and piers to provide traction even when surfaces are wet or slippery due to water or sea spray. This application is critical for ensuring the safety of both crew members and passengers. From a broader perspective, the use of RC210 slips aligns with regulatory compliance and safety standards across various industries. By adhering to these standards, businesses not only protect their employees but also mitigate potential legal liabilities associated with workplace accidents. The economic benefits are also significant as reduced downtime due to accidents translates into higher productivity and lower operational costs. In summary, the RC210 slip is an indispensable tool across multiple industrial sectors due to its ability to enhance safety, improve operational efficiency, and comply with stringent safety regulations. Its widespread application underscores its importance in maintaining a safe working environment and ensuring the smooth operation of diverse industrial processes.
The Importance of RC210 Slip in Construction
In the realm of construction, the RC210 slip plays a pivotal role that extends beyond mere functionality to encompass critical aspects of structural integrity, safety, and economic efficiency. This essential component is not just a minor detail but a cornerstone that ensures buildings stand the test of time and adhere to stringent safety standards. The importance of RC210 slip can be understood through three key lenses: its role in ensuring structural integrity, its impact on building safety and compliance, and its economic benefits and cost efficiency. By examining how RC210 slip contributes to the overall stability and durability of structures, we can appreciate its significance in preventing potential failures and ensuring that buildings remain safe for occupants. Additionally, compliance with regulatory standards is heavily influenced by the proper use of RC210 slips, which helps in avoiding legal and financial repercussions. Finally, the economic benefits derived from using high-quality RC210 slips include reduced maintenance costs and extended lifespan of the structure, making it a cost-efficient choice in the long run. Understanding these facets begins with a deep dive into the role of RC210 slip in ensuring structural integrity, which forms the foundation of all other benefits.
Role in Ensuring Structural Integrity
Ensuring structural integrity is a critical aspect of construction, and the role of RC210 slip is pivotal in this context. Structural integrity refers to the ability of a building or structure to withstand various loads and stresses without failing, thereby ensuring the safety and durability of the edifice. RC210 slip, a specialized type of slip-resistant coating, plays a significant role in maintaining this integrity by providing a robust and reliable surface finish. Firstly, RC210 slip enhances the safety of structures by reducing the risk of slips and falls. In environments where moisture, oil, or other substances can compromise surface traction, RC210 slip ensures that floors and walkways remain secure. This is particularly important in industrial settings, warehouses, and public facilities where heavy foot traffic and potential hazards are common. By maintaining a slip-resistant surface, RC210 slip helps prevent accidents and injuries, thereby safeguarding both workers and users. Secondly, RC210 slip contributes to the longevity of structures by protecting them from wear and tear. The coating acts as a barrier against chemical spills, heavy machinery traffic, and other forms of mechanical stress that could otherwise degrade the surface over time. This protective layer not only extends the lifespan of the structure but also reduces maintenance costs associated with frequent repairs and replacements. Moreover, RC210 slip is designed to be durable and resistant to various environmental conditions. It can withstand extreme temperatures, UV exposure, and chemical corrosion, making it an ideal choice for both indoor and outdoor applications. This durability ensures that the structural integrity of the building remains uncompromised even under harsh conditions. In addition to its functional benefits, RC210 slip also offers aesthetic advantages. It is available in a range of colors and finishes, allowing architects and builders to integrate it seamlessly into their design plans. This versatility makes it possible to maintain a consistent look while ensuring that all surfaces meet safety standards. From a regulatory standpoint, using RC210 slip can help construction projects comply with safety standards and regulations. Many jurisdictions mandate specific slip-resistance requirements for certain types of buildings, especially those that are open to the public. By incorporating RC210 slip into their designs, builders can ensure that their projects meet these legal requirements, avoiding potential fines or legal issues. In conclusion, the role of RC210 slip in ensuring structural integrity is multifaceted and crucial. It enhances safety by reducing slip hazards, extends the lifespan of structures through its protective properties, and offers durability against various environmental factors. Additionally, its aesthetic flexibility and compliance with regulatory standards make it an indispensable component in modern construction practices. As such, RC210 slip is not just an accessory but a fundamental element in maintaining the overall integrity and functionality of buildings.
Impact on Building Safety and Compliance
The implementation of RC210 slips in construction significantly enhances building safety and compliance, playing a crucial role in ensuring the structural integrity and durability of concrete structures. These slips, designed to facilitate the smooth and efficient placement of concrete, contribute to several key aspects of building safety. Firstly, they help in achieving uniform concrete distribution, which is essential for maintaining the structural strength and stability of the building. By preventing uneven settling or air pockets within the concrete, RC210 slips reduce the risk of cracks and weaknesses that could compromise the structure's overall safety. Moreover, the use of RC210 slips aligns with various building codes and standards, such as those set by the American Concrete Institute (ACI) and the International Building Code (IBC). Compliance with these regulations is paramount for ensuring that buildings are constructed to withstand various environmental and structural stresses. For instance, proper concrete placement facilitated by RC210 slips helps in meeting the required compressive strength and durability standards, thereby safeguarding against potential hazards like collapse or damage from natural disasters. Additionally, the precision and control offered by RC210 slips during the concrete placement process minimize the likelihood of human error, which is a common factor in construction accidents. By streamlining the workflow and reducing manual handling, these slips contribute to a safer working environment for construction workers. This not only protects the workforce but also helps in maintaining a consistent quality of construction, which is vital for long-term building safety. In terms of long-term maintenance and sustainability, RC210 slips also play a significant role. High-quality concrete placement ensures that the structure remains resilient over time, reducing the need for costly repairs and renovations. This resilience is particularly important in regions prone to extreme weather conditions or seismic activity, where buildings must be able to withstand significant stresses without compromising safety. In conclusion, the integration of RC210 slips into construction processes is a critical factor in enhancing building safety and compliance. By ensuring uniform concrete distribution, aligning with regulatory standards, minimizing human error, and contributing to long-term structural resilience, these slips are indispensable tools in modern construction practices. Their importance underscores the necessity of adopting advanced technologies and methodologies to safeguard both the integrity of buildings and the safety of occupants and workers alike.
Economic Benefits and Cost Efficiency
The integration of RC210 slip in construction projects offers significant economic benefits and enhances cost efficiency, making it a crucial component in modern building practices. One of the primary advantages is the reduction in labor costs. RC210 slip, with its pre-fabricated design, simplifies the installation process, allowing for faster assembly times compared to traditional methods. This streamlined approach minimizes the need for extensive on-site labor, thereby reducing overall project timelines and associated labor expenses. Additionally, the precision engineering of RC210 slip ensures a high degree of accuracy, which reduces the likelihood of errors and rework, further optimizing resource allocation. Another key economic benefit lies in the material savings. The precise fit and finish of RC210 slip components eliminate unnecessary material waste, a common issue in traditional construction methods. By using exactly what is needed, contractors can avoid over-ordering materials, which not only saves money but also contributes to a more sustainable building practice. Furthermore, the durability and longevity of RC210 slip components mean fewer replacements are required over the life of the structure, leading to long-term cost savings on maintenance and repairs. From a cost-efficiency perspective, RC210 slip also enhances project predictability. With standardized components, contractors can better estimate costs and manage budgets more effectively. This predictability reduces the risk of cost overruns and allows for more accurate financial planning, which is essential for maintaining project viability. Moreover, the use of RC210 slip can lead to earlier project completion, enabling developers to generate revenue sooner. This accelerated return on investment is particularly valuable in commercial and residential projects where timely completion directly impacts profitability. In addition to these direct economic benefits, RC210 slip contributes to improved safety standards, which indirectly affect project costs. By reducing the complexity of on-site work and minimizing the need for manual adjustments, RC210 slip lowers the risk of workplace accidents. Lower accident rates translate into reduced insurance premiums and fewer legal liabilities, further enhancing cost efficiency. Moreover, safer working conditions boost worker morale and productivity, contributing to a more efficient and effective construction process. In conclusion, the incorporation of RC210 slip into construction projects is a strategic decision that yields substantial economic benefits and enhances cost efficiency. Through reduced labor costs, material savings, improved project predictability, and enhanced safety standards, RC210 slip plays a pivotal role in optimizing construction processes. As the construction industry continues to evolve, leveraging innovative solutions like RC210 slip will remain crucial for achieving both financial success and operational excellence.
Challenges and Best Practices for Working with RC210 Slip
Working with RC210 Slip, a high-performance material used in various industrial applications, presents a unique set of challenges and opportunities. To ensure successful integration and optimal performance, it is crucial to understand the common challenges and potential risks associated with this material. This article delves into three key areas: **Common Challenges and Potential Risks**, **Best Practices for Installation and Maintenance**, and **Case Studies and Real-World Examples**. By examining these aspects, professionals can better navigate the complexities of working with RC210 Slip. First, understanding the common challenges and potential risks is essential for mitigating issues that could arise during the lifecycle of a project. This includes addressing factors such as material compatibility, environmental conditions, and operational stresses. Next, adhering to best practices for installation and maintenance can significantly enhance the durability and efficiency of RC210 Slip applications. Finally, real-world case studies provide valuable insights into how these best practices have been successfully implemented in various scenarios. By exploring these three critical components, this article aims to equip readers with the knowledge necessary to overcome obstacles and maximize the benefits of using RC210 Slip. Let us begin by examining the common challenges and potential risks that arise when working with this material.
Common Challenges and Potential Risks
When working with RC210 slip, several common challenges and potential risks must be carefully considered to ensure safe and effective use. One of the primary challenges is the material's sensitivity to environmental conditions, such as temperature and humidity. RC210 slip, being a specialized ceramic material, can be prone to warping or cracking if exposed to extreme temperatures or moisture levels, which can compromise its structural integrity and performance. This necessitates strict control over the working environment and careful handling during storage and application. Another significant challenge is the risk of contamination. RC210 slip is highly susceptible to impurities, which can drastically alter its physical properties and affect the final product's quality. Ensuring a clean workspace and using appropriate protective gear are crucial to prevent contamination from dust, oils, or other substances. Additionally, the mixing process requires precise measurements and techniques to avoid inconsistencies in the slip's composition, which could lead to defects in the final ceramic product. Health and safety risks are also a major concern when handling RC210 slip. The material contains fine particles that can be hazardous if inhaled, leading to respiratory issues. Moreover, the chemicals used in the preparation and application of RC210 slip can be harmful if not handled properly. It is essential to follow strict safety protocols, including the use of respirators, gloves, and protective eyewear, to mitigate these risks. From a logistical standpoint, sourcing high-quality RC210 slip can sometimes be challenging due to supply chain disruptions or quality control issues from manufacturers. This underscores the importance of establishing reliable supplier relationships and conducting thorough quality checks before using the material. In terms of best practices, it is advisable to follow a standardized procedure for preparing and applying RC210 slip. This includes thorough mixing according to the manufacturer's instructions, consistent application techniques, and careful monitoring of drying times to prevent defects. Regular maintenance of equipment and tools used in the process is also vital to prevent contamination and ensure consistent results. Furthermore, continuous training and education for personnel working with RC210 slip are essential. Understanding the material's properties, potential risks, and best practices can significantly reduce the likelihood of errors and improve overall productivity. Implementing quality control measures at each stage of the process, from raw material inspection to final product testing, helps in identifying and addressing any issues promptly. By acknowledging these challenges and taking proactive steps to mitigate them, users of RC210 slip can optimize their workflows, enhance product quality, and ensure a safe working environment. This comprehensive approach not only addresses immediate risks but also fosters long-term reliability and efficiency in working with this specialized ceramic material.
Best Practices for Installation and Maintenance
When working with RC210 Slip, a specialized material used in various industrial applications, it is crucial to adhere to best practices for installation and maintenance to ensure optimal performance, safety, and longevity. **Installation** should begin with thorough preparation of the surface, ensuring it is clean, dry, and free from any contaminants or debris. This step is vital as any impurities can compromise the bonding process and lead to premature failure. Next, apply the recommended primer if necessary, followed by the RC210 Slip material itself. It is essential to follow the manufacturer's guidelines for application thickness and drying times to avoid uneven distribution or incomplete curing. During **maintenance**, regular inspections are key. Check for signs of wear, such as cracks or delamination, and address these issues promptly. Cleaning the surface regularly with appropriate solvents can prevent the buildup of dirt and chemicals that might degrade the material over time. Additionally, ensure that any equipment or machinery in contact with the RC210 Slip is properly aligned and functioning correctly to avoid unnecessary stress on the material. Another critical aspect is **environmental control**. RC210 Slip performs best within specific temperature and humidity ranges; exceeding these parameters can lead to degradation or failure. Therefore, it is important to monitor and control environmental conditions where the material is installed. Training personnel on proper handling and maintenance procedures is also essential to prevent human error, which can significantly impact the lifespan of the RC210 Slip. Moreover, **record-keeping** is a best practice that often gets overlooked but is highly beneficial. Maintaining detailed records of installation dates, maintenance activities, and any repairs can help in tracking the material's performance over time. This data can be invaluable for scheduling future maintenance and identifying potential issues before they become major problems. Finally, **compliance with safety standards** is paramount. Always wear appropriate personal protective equipment (PPE) during installation and maintenance tasks to protect against chemical exposure and physical hazards. Ensuring that all work is conducted in accordance with relevant safety regulations not only safeguards personnel but also helps in maintaining a safe working environment. By following these best practices for installation and maintenance, users of RC210 Slip can maximize its benefits, extend its lifespan, and minimize downtime due to repairs or replacements. This proactive approach not only enhances operational efficiency but also contributes to a safer and more reliable working environment.
Case Studies and Real-World Examples
When delving into the complexities of working with RC210 slip, a critical component of understanding its challenges and best practices is examining case studies and real-world examples. These practical illustrations provide invaluable insights into how this material behaves under various conditions, highlighting both the pitfalls and the successes. For instance, a case study on a manufacturing plant that transitioned to using RC210 slip for their production line revealed significant improvements in product durability and resistance to wear. However, it also underscored the importance of precise temperature control during the application process, as deviations led to inconsistent bonding strengths. Another example from the automotive industry showed how RC210 slip enhanced the performance of engine components by reducing friction and heat buildup, but it also necessitated specialized training for maintenance personnel to ensure proper handling and application. Real-world examples further emphasize the need for meticulous surface preparation before applying RC210 slip. A study on aerospace applications highlighted that even minor contaminants on the surface could compromise the adhesive properties of the slip, leading to catastrophic failures under stress. Conversely, a successful implementation in the medical device sector demonstrated that with thorough cleaning and priming, RC210 slip could achieve exceptional bonding results that met stringent regulatory standards. Moreover, these case studies and examples often reveal best practices that are not immediately apparent from theoretical knowledge alone. For example, one manufacturer found that using a specific type of applicator tool significantly reduced waste and improved uniformity in the application of RC210 slip, thereby enhancing overall efficiency. Another company discovered that implementing a quality control checklist at each stage of the process helped in identifying potential issues early on, thereby minimizing downtime and reducing costs associated with rework. In addition to these operational insights, real-world examples also shed light on environmental and safety considerations. A case study from an industrial setting highlighted the importance of proper ventilation when working with RC210 slip due to its potential for releasing harmful fumes during curing. This led to the implementation of enhanced ventilation systems and personal protective equipment protocols, ensuring a safer working environment for employees. By analyzing these case studies and real-world examples, practitioners can gain a deeper understanding of the multifaceted challenges associated with working with RC210 slip. They can also adopt proven strategies and best practices that have been tested in various scenarios, thereby optimizing their own processes and achieving superior outcomes. This holistic approach not only enhances the reliability and performance of products but also contributes to a safer, more efficient, and more sustainable work environment. Ultimately, integrating these practical lessons into daily operations can significantly mitigate the challenges inherent in working with RC210 slip, leading to improved productivity and product quality.