What Size Wire For 50 Amps

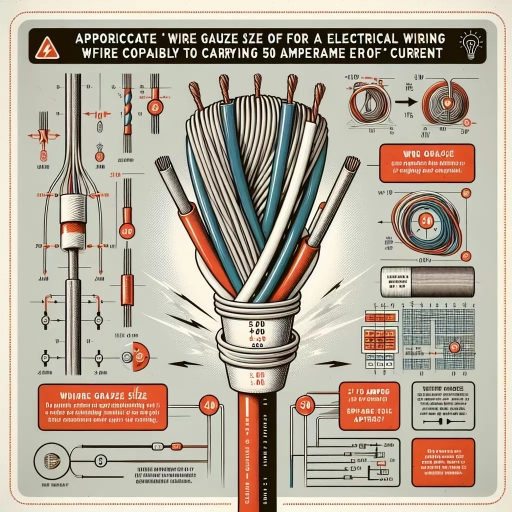
When it comes to electrical wiring, selecting the right wire size is crucial for safety, efficiency, and compliance with electrical codes. For applications requiring 50 amps, understanding the correct wire size is paramount to avoid overheating, electrical fires, and other hazards. This article delves into the essential aspects of wire sizing for 50 amps, starting with the foundational principles in "Understanding the Basics of Wire Sizing for 50 Amps." Here, we will explore how wire gauge, material, and insulation impact the overall performance and safety of your electrical system. We will then move on to "Calculating the Right Wire Size for 50 Amps," where we will discuss the formulas and factors involved in determining the appropriate wire size based on current, voltage, and distance. Finally, "Practical Applications and Safety Considerations" will provide real-world examples and critical safety tips to ensure your electrical setup is both functional and secure. By the end of this article, you will be well-equipped to make informed decisions about wire sizing for your 50-amp needs. Let's begin by understanding the basics of wire sizing for 50 amps.
Understanding the Basics of Wire Sizing for 50 Amps
Understanding the basics of wire sizing for a 50-amp electrical circuit is crucial for ensuring safety, efficiency, and reliability in electrical systems. When it comes to handling high currents, the correct wire gauge is not just a matter of convenience but a necessity. This article delves into three key aspects that highlight the significance of proper wire sizing: the importance of correct wire gauge, factors influencing wire size selection, and the consequences of incorrect wire sizing. Correct wire gauge is essential because it directly affects the flow of electrical current and the overall performance of the system. Incorrectly sized wires can lead to overheating, reduced efficiency, and even dangerous electrical fires. Factors such as the length of the wire run, the type of material used, and environmental conditions also play critical roles in determining the appropriate wire size. Additionally, understanding these factors helps in making informed decisions that prevent potential hazards. The consequences of incorrect wire sizing are severe and can include electrical shocks, fires, and equipment damage. Therefore, it is imperative to grasp these fundamental principles to ensure that electrical installations are safe and functional. By focusing on these critical aspects, individuals can better navigate the complexities of wire sizing and make informed decisions. In the following sections, we will explore each of these topics in detail, starting with the **Importance of Correct Wire Gauge**. This foundational understanding will provide a solid basis for appreciating the broader implications of wire sizing in electrical systems.
Importance of Correct Wire Gauge
The importance of using the correct wire gauge cannot be overstated, particularly when dealing with high current applications such as those requiring 50 amps. Wire gauge, measured in American Wire Gauge (AWG), is a critical factor in ensuring safe and efficient electrical transmission. Incorrectly sized wires can lead to a myriad of issues, including overheating, reduced system performance, and even catastrophic failures such as fires. When selecting a wire for a 50-amp circuit, it is essential to consider the wire's cross-sectional area and its ability to handle the current without excessive resistance. A smaller gauge number indicates a larger wire diameter, which is necessary for higher current loads. For instance, a 6 AWG wire is significantly larger than a 14 AWG wire and can safely carry more current over longer distances without significant voltage drop or heat buildup. Using a wire that is too small for the required current can result in increased resistance, leading to higher temperatures and potential damage to the wire insulation and surrounding components. This not only compromises the reliability of the electrical system but also poses serious safety risks. On the other hand, using a wire that is too large may be unnecessary and wasteful, as it will add unnecessary cost and bulk to the installation. In addition to safety and efficiency, correct wire sizing also affects the overall performance of the electrical system. Properly sized wires ensure minimal voltage drop, which is crucial for maintaining the operational integrity of connected devices. For example, in a 50-amp circuit powering sensitive equipment like motors or lighting systems, any significant voltage drop could result in reduced performance or premature failure of these devices. Moreover, local electrical codes and standards often mandate specific wire gauges for different current ratings to ensure compliance with safety regulations. Non-compliance can lead to failed inspections, costly rework, and legal liabilities. Therefore, understanding and adhering to these guidelines is paramount when designing or installing electrical systems. In summary, selecting the correct wire gauge is a fundamental aspect of electrical system design that directly impacts safety, efficiency, and performance. For a 50-amp circuit, choosing the appropriate wire gauge ensures reliable operation, minimizes risks associated with overheating or electrical fires, and complies with regulatory requirements. Always consult relevant standards and guidelines to determine the optimal wire size for your specific application to guarantee a safe and functional electrical system.
Factors Influencing Wire Size Selection
When selecting the appropriate wire size for a 50-amp electrical circuit, several critical factors must be considered to ensure safety, efficiency, and compliance with electrical codes. **Current Rating** is paramount; the wire must be capable of handling the maximum current without overheating, which could lead to a fire hazard. The **Voltage Drop** is another crucial factor, as excessive voltage drop can result in reduced system performance and increased energy losses. For instance, using a wire that is too small can cause significant voltage drop over long distances, leading to inefficient operation of connected devices. **Distance** between the power source and the load also plays a significant role. Longer distances require larger wires to minimize voltage drop and ensure reliable operation. **Ambient Temperature** affects wire sizing as well; higher temperatures reduce the wire's current-carrying capacity, necessitating larger wires in hotter environments. **Insulation Type** and its thermal rating are important considerations, as different types of insulation have varying temperature limits that affect the overall wire size selection. Additionally, **Bundle Size** or the number of wires in a bundle impacts wire sizing due to mutual heating effects. When multiple wires are bundled together, each wire's current-carrying capacity is reduced, requiring larger wires to compensate for this effect. **Conductor Material**, whether it is copper or aluminum, influences wire size due to differences in electrical conductivity and thermal properties. Copper wires generally have higher conductivity but are more expensive than aluminum wires. **Load Type**, whether it is continuous or intermittent, also influences wire size selection. Continuous loads require wires that can handle constant current flow without overheating, while intermittent loads may allow for smaller wires since they do not operate continuously. **Local Electrical Codes** and standards, such as those set by the National Electric Code (NEC), must be adhered to ensure compliance and safety. These codes often provide specific guidelines for wire sizing based on various factors including current rating, voltage drop, and environmental conditions. In summary, selecting the correct wire size for a 50-amp circuit involves a careful analysis of current rating, voltage drop, distance, ambient temperature, insulation type, bundle size, conductor material, load type, and adherence to local electrical codes. By considering these factors comprehensively, one can ensure a safe and efficient electrical system that meets all necessary standards and requirements. This meticulous approach not only prevents potential hazards but also optimizes system performance and longevity.
Consequences of Incorrect Wire Sizing
Incorrect wire sizing can have severe and far-reaching consequences, making it crucial to understand the basics of wire sizing, especially for high-current applications like 50 amps. When wires are undersized, they cannot handle the electrical load efficiently, leading to overheating. This excessive heat can cause insulation to melt or degrade, potentially resulting in short circuits or even fires. Moreover, undersized wires increase the resistance in the circuit, which not only reduces the overall efficiency of the electrical system but also increases energy losses due to heat dissipation. This inefficiency can lead to higher electricity bills and reduced lifespan of electrical components. On the other hand, oversized wires may seem like a safe choice but come with their own set of drawbacks. While they do not pose the same risk of overheating or fire hazards, they are more expensive and may require larger conduits or more extensive infrastructure. This can significantly increase the overall cost of the electrical installation. Additionally, oversized wires can make connections more difficult due to their larger diameter, complicating the installation process and potentially leading to errors. From a safety perspective, incorrect wire sizing is a serious concern. Undersized wires can lead to electrical shocks or electrocution if they fail under load. Furthermore, improperly sized wires can violate local electrical codes and standards, such as those set by the National Electric Code (NEC), which could result in failed inspections and legal issues. In commercial settings, this non-compliance can lead to costly rework and downtime. In terms of reliability and performance, incorrect wire sizing affects the overall stability of the electrical system. For instance, in industrial environments where machinery relies on consistent power supply, undersized wires can cause frequent shutdowns or malfunctions due to voltage drops. This not only disrupts operations but also impacts productivity and profitability. Lastly, environmental considerations should not be overlooked. Inefficient electrical systems resulting from incorrect wire sizing contribute to higher energy consumption and increased greenhouse gas emissions. As global efforts focus on sustainability and reducing carbon footprints, ensuring proper wire sizing becomes an essential part of responsible electrical design. In conclusion, understanding the basics of wire sizing is paramount to avoid these consequences. For a 50-amp circuit, selecting the right gauge wire based on factors such as distance, load type, and ambient temperature ensures safe, efficient, and compliant electrical installations. By adhering to established guidelines and best practices in wire sizing, individuals can prevent potential hazards, optimize system performance, and contribute to a more sustainable future.
Calculating the Right Wire Size for 50 Amps
When it comes to ensuring the safe and efficient operation of electrical systems, calculating the right wire size for a 50-amp circuit is crucial. This task involves several key considerations to avoid overheating, voltage drops, and potential safety hazards. First, it is essential to use the National Electric Code (NEC) Wire Sizing Chart, which provides a standardized guide for selecting the appropriate wire gauge based on the current load and conductor type. However, this is just the starting point. Additionally, one must consider the distance between the power source and the load, as longer distances can lead to significant voltage drops that affect system performance. Lastly, accounting for ambient temperature is vital, as high temperatures can reduce the ampacity of wires, necessitating larger gauges to maintain safety and efficiency. By carefully evaluating these factors—using the NEC Wire Sizing Chart, considering distance and voltage drop, and accounting for ambient temperature—you can ensure that your electrical system operates reliably and safely. Let's begin by delving into the specifics of using the NEC Wire Sizing Chart.
Using the NEC Wire Sizing Chart
When calculating the right wire size for a 50-amp circuit, one of the most reliable tools at your disposal is the NEC (National Electric Code) wire sizing chart. This chart is a cornerstone of electrical planning, ensuring that your wiring system is both safe and efficient. To use the NEC wire sizing chart effectively, start by identifying the key parameters of your circuit: the current (in this case, 50 amps), the voltage (usually 120 or 240 volts for residential applications), and the type of wire insulation and conductor material you are using. First, locate the section of the chart that corresponds to your specific voltage and conductor type. The NEC chart typically categorizes wires based on their insulation type (such as THHN, THWN, or UF) and whether they are copper or aluminum. For most residential applications, you will likely be using copper conductors with THHN or THWN insulation. Next, find the row that corresponds to your circuit's current rating—50 amps in this scenario. The columns will list various wire gauges (AWG) along with their corresponding ampacity ratings. Ampacity refers to the maximum current a wire can safely carry without overheating. For a 50-amp circuit at 120 volts, you would typically need a wire gauge that can handle at least 55 amps to account for any potential overloads or inefficiencies. According to the NEC chart, a #6 AWG copper wire with THHN insulation is generally recommended for such applications. However, it's crucial to consider other factors such as ambient temperature, the number of conductors in a conduit, and any derating factors that might apply. Always refer to the latest edition of the NEC for the most current guidelines and ensure compliance with local electrical codes and regulations. Additionally, consulting with a licensed electrician can provide further assurance that your wiring meets all safety standards and is appropriately sized for your specific needs. By meticulously using the NEC wire sizing chart, you can ensure that your electrical system operates safely and efficiently, minimizing risks associated with overheating or electrical fires. This approach not only adheres to regulatory requirements but also safeguards against potential hazards, making it an indispensable step in any electrical installation or upgrade project.
Considering Distance and Voltage Drop
When calculating the right wire size for a 50-amp electrical circuit, it is crucial to consider two key factors: distance and voltage drop. The distance between the power source and the load significantly impacts the wire size required, as longer distances result in greater resistance and potential voltage drops. Voltage drop, which is the reduction in voltage that occurs as electricity travels through a wire, must be kept within acceptable limits to ensure efficient and safe operation of electrical systems. For instance, if you are installing a 50-amp circuit over a long distance, you will need to use a larger gauge wire to minimize voltage drop. The American Wire Gauge (AWG) system is commonly used to determine wire sizes, with lower AWG numbers indicating larger wires. According to the National Electric Code (NEC), for a 50-amp circuit at 120/240 volts, a minimum of 6 AWG wire is typically recommended for shorter distances. However, if the circuit spans longer than 100 feet, you may need to upgrade to 4 AWG or even 2 AWG wire to maintain an acceptable voltage drop. The NEC provides tables and charts that help in determining the appropriate wire size based on current, voltage, and distance. These resources are invaluable for ensuring compliance with safety standards and preventing overheating or underperformance of electrical systems. Additionally, using specialized calculators or consulting with electrical engineers can provide more precise calculations tailored to specific scenarios. In practical terms, failing to account for distance and voltage drop can lead to serious consequences such as reduced system efficiency, overheated wires, and even fire hazards. Therefore, it is essential to meticulously plan and calculate the wire size requirements before initiating any electrical installation project. Moreover, environmental factors such as ambient temperature and the presence of other heat sources can also influence the choice of wire size. For example, in high-temperature environments or when multiple circuits are bundled together, larger wires may be necessary to compensate for increased resistance. In summary, considering distance and voltage drop is paramount when determining the right wire size for a 50-amp circuit. By adhering to NEC guidelines and taking into account specific installation conditions, you can ensure that your electrical system operates safely and efficiently. This careful planning not only prevents potential hazards but also guarantees optimal performance over the lifespan of the electrical system.
Accounting for Ambient Temperature
When calculating the right wire size for a 50-amp electrical circuit, one crucial factor to consider is the ambient temperature of the environment in which the wiring will be installed. Ambient temperature refers to the average temperature of the surrounding air, and it significantly impacts the performance and safety of electrical wiring. High ambient temperatures can reduce the current-carrying capacity of wires, as excessive heat can cause insulation degradation and increase the risk of electrical fires. For instance, if you are installing wiring in an attic or outdoor environment where temperatures can soar during summer months, you need to account for these higher temperatures when selecting wire sizes. The National Electric Code (NEC) provides tables and guidelines that adjust wire ampacity based on ambient temperatures. For example, if the ambient temperature is expected to be around 86°F (30°C), which is a common assumption for many indoor installations, you might use one set of ampacity ratings. However, if the wiring will be exposed to temperatures above this threshold, such as in an attic where temperatures can reach up to 104°F (40°C) or more, you must derate the wire's ampacity accordingly. Derating involves reducing the maximum allowable current through the wire to prevent overheating. This means that for a 50-amp circuit in a hot environment, you may need to use a larger wire size than you would in a cooler environment to ensure safe operation. For example, while a #6 AWG copper wire might be sufficient for a 50-amp circuit at room temperature, you might need to upgrade to a #4 AWG or even larger wire if the ambient temperature is significantly higher. Additionally, it's important to consider other factors that can affect wire temperature, such as the number of wires bundled together (since bundling can increase heat retention) and any local regulations or standards that may specify different derating factors. By accurately accounting for ambient temperature and other environmental conditions, you can ensure that your electrical wiring system operates safely and efficiently, minimizing the risk of overheating and potential electrical hazards. In summary, when determining the appropriate wire size for a 50-amp circuit, it is essential to take into account the ambient temperature of the installation environment. This involves consulting relevant NEC tables and guidelines to derate wire ampacity appropriately based on expected temperatures. Proper consideration of ambient temperature ensures that your electrical system remains safe and reliable under various environmental conditions.
Practical Applications and Safety Considerations
When it comes to electrical installations, the practical applications and safety considerations are paramount. Ensuring that all aspects of the process are meticulously managed is crucial for both efficiency and safety. This involves several key steps, starting with choosing the right material for the job. The debate between copper and aluminum wiring is a significant one, each having its own set of advantages and disadvantages that must be carefully weighed. Additionally, compliance with local electrical codes is essential to avoid legal issues and ensure that the installation meets all necessary standards. Finally, adhering to best practices for installation and maintenance is vital to prevent accidents and extend the lifespan of the electrical system. By focusing on these critical areas, individuals can guarantee a safe, efficient, and compliant electrical setup. Let's begin by examining the first of these considerations: choosing the right material, specifically the comparison between copper and aluminum.
Choosing the Right Material (Copper vs. Aluminum)
When it comes to selecting the right material for electrical wiring, particularly for applications requiring a 50-amp current, the choice between copper and aluminum is crucial. Both materials have their own set of advantages and disadvantages, which must be carefully considered to ensure optimal performance and safety. Copper is widely regarded as the gold standard for electrical wiring due to its superior conductivity. It offers higher current-carrying capacity, meaning it can handle more power with less resistance, resulting in less heat generation and reduced risk of overheating. This makes copper an excellent choice for high-amperage applications like 50 amps. Additionally, copper is more durable and resistant to corrosion, especially when properly insulated, which extends its lifespan and reliability. However, copper wiring is generally more expensive than aluminum, which can be a significant factor in budget-conscious projects. On the other hand, aluminum wiring has seen increased use in recent decades due to its lower cost and lighter weight compared to copper. While it is still a good conductor, aluminum has about 60% of the conductivity of copper, necessitating larger wire sizes to achieve the same current-carrying capacity. This can lead to increased material costs and more complex installations. Furthermore, aluminum is more prone to oxidation and corrosion, which can compromise its conductivity over time if not properly maintained. Despite these challenges, advancements in technology have led to the development of improved aluminum alloys that mitigate some of these issues. From a practical application standpoint, copper remains the preferred choice for high-amperage wiring due to its reliability and performance. For instance, in residential electrical systems where 50-amp circuits are common (e.g., for electric ranges or HVAC units), copper wiring ensures consistent power delivery without significant voltage drops or heat buildup. However, in larger commercial or industrial settings where cost is a critical factor and the infrastructure can support larger wire sizes, aluminum might be a viable option. Safety considerations also play a pivotal role in this decision. Copper's superior conductivity reduces the risk of overheating and potential fires, making it a safer choice for high-amperage applications. Aluminum wiring, if not installed correctly or maintained properly, can lead to loose connections and arcing due to its tendency to expand and contract with temperature changes. This underscores the importance of adhering strictly to installation guidelines and regular maintenance schedules when using aluminum. In conclusion, while both copper and aluminum have their merits and drawbacks, copper stands out as the better material for high-amperage wiring due to its superior conductivity, durability, and safety profile. For applications requiring 50 amps or more, investing in copper wiring may be more cost-effective in the long run despite its higher initial cost. This ensures reliable performance and minimizes potential safety hazards associated with electrical wiring.
Ensuring Compliance with Local Electrical Codes
Ensuring compliance with local electrical codes is a critical aspect of any electrical installation, particularly when determining the appropriate wire size for a 50-amp circuit. Local electrical codes, often based on the National Electric Code (NEC) but with specific regional amendments, provide guidelines to ensure safety and efficiency in electrical systems. These codes dictate various aspects such as wire sizing, insulation requirements, and installation practices to prevent electrical hazards like overheating, short circuits, and fires. For a 50-amp circuit, the NEC typically requires a minimum wire size of 6 AWG (American Wire Gauge) for copper conductors and 4 AWG for aluminum conductors. However, local codes may specify different requirements based on factors such as ambient temperature, conductor insulation type, and the presence of other heat sources. For instance, in areas with high ambient temperatures or where conductors are exposed to direct sunlight, larger wire sizes might be mandated to compensate for increased heat loads. Compliance also involves adhering to specific installation practices. This includes proper grounding techniques to ensure that all metal parts of the electrical system are safely connected to earth, reducing the risk of electrical shock. Additionally, local codes often specify the types of materials and equipment that can be used in various environments—such as wet locations or hazardous areas—which further enhance safety. Regular inspections by certified electricians are essential to ensure that installations meet local code standards. These inspections verify that all components are correctly sized and installed according to code requirements. Non-compliance can lead to serious safety risks and may result in fines or even legal action. Moreover, staying updated with the latest code revisions is crucial. Electrical codes are periodically updated to reflect new technologies and safety standards. For example, recent updates may include requirements for arc fault circuit interrupters (AFCIs) or ground fault circuit interrupters (GFCIs) in certain applications to mitigate specific hazards. In summary, ensuring compliance with local electrical codes when determining wire size for a 50-amp circuit involves understanding and adhering to specific guidelines related to conductor sizing, installation practices, and material specifications. This not only ensures the safety of individuals but also prevents potential legal and financial repercussions associated with non-compliance. By following these codes diligently, electrical installations can be both efficient and safe, aligning with the broader goal of practical applications and safety considerations in electrical work.
Best Practices for Installation and Maintenance
When it comes to the installation and maintenance of electrical systems, adhering to best practices is crucial for ensuring safety, efficiency, and longevity. For a 50-amp circuit, which is commonly used in residential settings for heavy-duty appliances like electric dryers or HVAC units, the correct wire size is paramount. Here are some key best practices to consider: **Wire Size Selection**: The American National Standards Institute (ANSI) and the National Electric Code (NEC) provide guidelines for wire sizing based on the current load and distance from the power source. For a 50-amp circuit, a minimum wire size of 6 AWG (American Wire Gauge) is typically recommended for copper wires, assuming a voltage drop of 3% or less over the length of the run. However, this can vary depending on factors such as insulation type, ambient temperature, and specific local codes. **Installation Techniques**: Proper installation involves careful planning and execution. Ensure that all connections are secure and made with compatible materials to prevent overheating or arcing. Use appropriate connectors and lugs that match the wire size and type. When running wires through conduits or raceways, avoid overfilling to prevent damage during installation or future maintenance. **Safety Considerations**: Safety should always be the top priority. Ensure that all work is performed by qualified electricians who follow local electrical codes and safety standards. Use personal protective equipment (PPE) such as gloves, safety glasses, and non-contact voltage testers to prevent electrical shock. Always de-energize circuits before performing any maintenance or repairs. **Regular Maintenance**: Regular maintenance is essential to extend the life of your electrical system and prevent potential hazards. Schedule periodic inspections to check for signs of wear, overheating, or corrosion on wires and connections. Clean dust from electrical panels and replace any damaged components promptly. **Documentation and Compliance**: Maintain detailed records of your electrical system's design, installation, and maintenance history. Ensure compliance with local building codes and regulations by obtaining necessary permits before starting any work. This documentation will be invaluable during future inspections or when troubleshooting issues. By adhering to these best practices for installation and maintenance, you can ensure a safe, efficient, and reliable electrical system that meets your needs while minimizing risks associated with electrical malfunctions. Whether you're installing a new circuit for a heavy-duty appliance or performing routine maintenance on an existing system, attention to detail and adherence to industry standards are key components of a successful outcome.