What Is A Millright

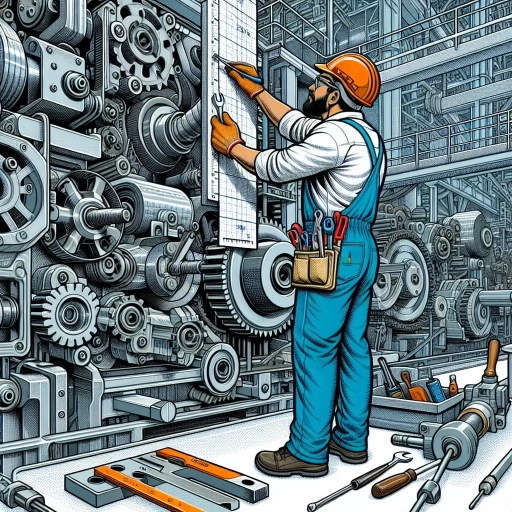
A millwright is a skilled tradesperson who plays a crucial role in the installation, maintenance, and repair of machinery and equipment in various industries. This profession requires a blend of mechanical aptitude, problem-solving skills, and physical stamina. In this article, we will delve into the multifaceted world of millwrights, starting with an in-depth look at **Understanding the Role of a Millwright**, where we explore the core responsibilities and qualifications necessary for this position. We will then examine **The Daily Life and Tasks of a Millwright**, shedding light on the day-to-day activities and challenges faced by these professionals. Finally, we will discuss **The Future and Importance of Millwrights in Industry**, highlighting their significance in modern manufacturing and the evolving landscape of industrial maintenance. By understanding these aspects, readers will gain a comprehensive insight into the vital contributions millwrights make to keeping industries running smoothly. Let's begin by **Understanding the Role of a Millwright**.
Understanding the Role of a Millwright
Understanding the role of a millwright is crucial for appreciating the intricate mechanics and historical significance behind industrial machinery. This profession, which dates back to the early days of industrialization, has evolved significantly over time. To grasp the full scope of a millwright's responsibilities, it is essential to delve into three key areas: the historical context and evolution of the profession, the key responsibilities and duties that millwrights undertake, and the specialized skills and training required for this role. Historically, millwrights were pivotal in constructing and maintaining the machinery that drove the Industrial Revolution. Today, their duties encompass a wide range of tasks from installation and maintenance to troubleshooting complex mechanical systems. The specialized skills they possess are honed through rigorous training programs that equip them with the knowledge to handle advanced technologies. By exploring these aspects, we can gain a comprehensive understanding of the vital role millwrights play in modern industry. Let us begin by examining the historical context and evolution of this esteemed profession.
Historical Context and Evolution
The historical context and evolution of the millwright profession are deeply intertwined with the development of machinery and industrialization. The term "millwright" originates from the Middle Ages, where these skilled craftsmen were responsible for constructing and maintaining mills, which were crucial for grinding grain and other tasks. As technology advanced, millwrights adapted their skills to accommodate new machinery, becoming adept at installing, repairing, and maintaining complex mechanical systems. During the Industrial Revolution, the role of millwrights expanded significantly. They played a pivotal role in setting up and maintaining the machinery in factories, textile mills, and other industrial facilities. Their expertise in mechanical engineering and problem-solving was essential for ensuring that production lines ran smoothly and efficiently. As industries grew and diversified, so did the scope of a millwright's work, encompassing a wide range of machinery from pumps and conveyor systems to turbines and generators. In the 20th century, advancements in technology led to further specialization within the trade. Millwrights began to work with more sophisticated equipment, including precision instruments and automated systems. This necessitated a higher level of technical knowledge and training, leading to formal apprenticeships and certification programs. Today, millwrights are integral to various sectors such as manufacturing, energy production, and construction, where they ensure that machinery operates safely and efficiently. The evolution of the millwright profession has also been influenced by changes in workplace safety regulations and environmental standards. Modern millwrights must adhere to stringent safety protocols and environmental guidelines, which has added another layer of complexity to their role. Despite these challenges, the core skills of a millwright—mechanical aptitude, problem-solving abilities, and attention to detail—remain as relevant as ever. Understanding the historical context and evolution of the millwright profession provides valuable insight into the multifaceted nature of this trade. It highlights how millwrights have consistently adapted to technological advancements while maintaining their core competencies. This adaptability underscores the importance of continuous learning and professional development within the field, ensuring that millwrights remain indispensable in modern industrial settings. By grasping this historical perspective, one can better appreciate the critical role that millwrights play in maintaining and advancing industrial operations today.
Key Responsibilities and Duties
**Key Responsibilities and Duties** A millwright's role is multifaceted and demanding, requiring a blend of technical expertise, physical stamina, and problem-solving skills. Here are the key responsibilities and duties that define this critical profession: 1. **Installation and Maintenance**: Millwrights are responsible for the installation, maintenance, and repair of machinery and equipment in various industrial settings such as factories, power plants, and construction sites. This includes aligning, leveling, and anchoring machinery to ensure optimal performance. 2. **Troubleshooting**: They diagnose and troubleshoot issues with machinery to identify problems and implement corrective actions. This involves using diagnostic tools and techniques to pinpoint mechanical failures or inefficiencies. 3. **Blueprint Interpretation**: Millwrights must interpret blueprints, diagrams, and other technical documents to understand the layout and specifications of machinery. This skill is crucial for accurate installation and maintenance. 4. **Safety Compliance**: Ensuring compliance with safety regulations is paramount. Millwrights conduct risk assessments, follow safety protocols, and use personal protective equipment to prevent injuries and accidents. 5. **Collaboration**: They often work in teams with other tradespeople such as electricians, plumbers, and carpenters. Effective communication and collaboration are essential for completing projects efficiently. 6. **Tool Proficiency**: Millwrights must be proficient in using a variety of tools including hand tools, power tools, and specialized equipment like hoists and cranes. 7. **Quality Control**: They perform quality control checks to ensure that machinery is functioning correctly and meets industry standards. This includes conducting regular inspections and performing routine maintenance tasks. 8. **Documentation**: Keeping detailed records of maintenance activities, repairs, and inspections is another key responsibility. This documentation helps in tracking the history of machinery and planning future maintenance. 9. **Training and Development**: Staying updated with new technologies and techniques is vital in this field. Millwrights may participate in training programs or workshops to enhance their skills and adapt to evolving industry requirements. 10. **Emergency Response**: In cases of machinery breakdowns or emergencies, millwrights are often called upon to respond quickly and effectively to minimize downtime and ensure continuous operation. By understanding these responsibilities and duties, one can appreciate the complexity and importance of the millwright's role in maintaining the operational integrity of industrial machinery and equipment.
Specialized Skills and Training
To fully understand the role of a millwright, it is crucial to delve into the specialized skills and training required for this profession. Millwrights are highly skilled craftsmen who install, maintain, and repair machinery and equipment in various industries, including manufacturing, construction, and power generation. Their work demands a unique blend of mechanical aptitude, problem-solving skills, and physical stamina. **Specialized Skills:** 1. **Mechanical Knowledge:** Millwrights must have a deep understanding of mechanical principles, including kinematics, dynamics, and thermodynamics. This knowledge allows them to diagnose and repair complex machinery. 2. **Blueprint Reading:** The ability to interpret blueprints and technical drawings is essential for millwrights to understand the layout and specifications of machinery. 3. **Precision Measurement:** Millwrights use precision instruments to ensure that machinery is properly aligned and installed. 4. **Troubleshooting:** They must be adept at identifying and resolving mechanical issues quickly to minimize downtime. 5. **Safety Protocols:** Adherence to safety standards is paramount; millwrights must be well-versed in safety procedures to protect themselves and others on the job site. **Training:** 1. **Apprenticeships:** Many millwrights start their careers through apprenticeship programs, which combine on-the-job training with classroom instruction. 2. **Formal Education:** Some may pursue post-secondary education in fields like mechanical technology or industrial maintenance. 3. **Certifications:** Obtaining certifications from organizations such as the United Brotherhood of Carpenters and Joiners of America (UBC) can enhance job prospects and demonstrate expertise. 4. **Continuous Learning:** The field of machinery maintenance is constantly evolving; therefore, ongoing training and professional development are necessary to stay updated with new technologies and techniques. 5. **Hands-On Experience:** Practical experience is invaluable; millwrights often gain this through internships or entry-level positions under the supervision of experienced professionals. In summary, the role of a millwright is multifaceted and requires a robust set of specialized skills and rigorous training. By combining theoretical knowledge with practical experience, millwrights are equipped to handle the complex tasks associated with machinery installation, maintenance, and repair, ensuring that industrial operations run smoothly and efficiently.
The Daily Life and Tasks of a Millwright
The daily life and tasks of a millwright are multifaceted and demanding, requiring a blend of technical expertise, problem-solving skills, and collaborative abilities. Millwrights are essential in various industries, including manufacturing, construction, and energy production, where they play a crucial role in ensuring the smooth operation of machinery. Their primary responsibilities include the installation and maintenance of machinery, which involves precise alignment, leveling, and anchoring of equipment to ensure optimal performance. Additionally, millwrights must employ advanced troubleshooting and repair techniques to diagnose and fix mechanical issues promptly. This often requires a deep understanding of mechanical systems and the ability to interpret technical manuals and blueprints. Furthermore, millwrights frequently collaborate with other tradespeople such as electricians, plumbers, and welders to complete complex projects efficiently. By mastering these diverse tasks, millwrights contribute significantly to the productivity and safety of industrial operations. Let's delve into the specifics of their role, starting with the critical aspect of installation and maintenance of machinery.
Installation and Maintenance of Machinery
The installation and maintenance of machinery are critical components of a millwright's daily life and tasks. Millwrights are skilled tradespeople responsible for ensuring that machinery operates efficiently and safely. When installing new equipment, millwrights meticulously follow manufacturer instructions and blueprints to ensure accurate placement and alignment. They use precision tools such as levels, micrometers, and laser alignment devices to guarantee that the machinery is properly positioned and calibrated. This process often involves dismantling existing equipment, preparing the site, and assembling the new machinery, which requires a deep understanding of mechanical systems and spatial reasoning. Maintenance is equally important, as it extends the lifespan of the machinery and prevents unexpected downtime. Millwrights perform routine inspections to identify potential issues before they become major problems. This includes checking for wear on moving parts, lubricating components, and ensuring that all safety features are functioning correctly. They also conduct scheduled maintenance tasks such as replacing worn-out parts, cleaning filters, and performing alignments to keep the machinery running smoothly. In addition to these tasks, millwrights must be adept at troubleshooting. When machinery malfunctions, they use diagnostic skills to identify the root cause of the problem. This may involve analyzing data from sensors or control systems, inspecting the machinery visually, or using specialized tools to test various components. Once the issue is identified, millwrights repair or replace the faulty parts, ensuring that the machinery is restored to optimal working condition. Safety is paramount in the installation and maintenance of machinery. Millwrights must adhere to strict safety protocols to protect themselves and others from potential hazards. This includes wearing personal protective equipment (PPE), following lockout/tagout procedures to prevent accidental start-ups, and ensuring that all work areas are clear of obstacles. The role of a millwright in installation and maintenance is not only technical but also collaborative. They often work with other tradespeople such as electricians, plumbers, and engineers to ensure that all aspects of the machinery are properly integrated and functioning as intended. Effective communication is key; millwrights must clearly explain their findings and recommendations to supervisors and other team members to ensure that any necessary repairs or adjustments are made promptly. In summary, the installation and maintenance of machinery are fundamental aspects of a millwright's job. These tasks require a blend of technical expertise, attention to detail, and strong problem-solving skills. By ensuring that machinery is installed correctly and maintained regularly, millwrights play a crucial role in maintaining operational efficiency and safety in various industrial settings.
Troubleshooting and Repair Techniques
Troubleshooting and repair techniques are integral components of a millwright's daily life and tasks. Millwrights, skilled tradespeople responsible for installing, maintaining, and repairing machinery and equipment in various industries, must possess a keen ability to diagnose issues quickly and efficiently. Here are some key troubleshooting and repair techniques they employ: 1. **Observation and Inspection**: Millwrights begin by observing the machinery in operation to identify any unusual sounds, vibrations, or visual signs of malfunction. They conduct thorough inspections to pinpoint the source of the problem, often using specialized tools such as infrared thermometers and vibration analyzers. 2. **Review of Maintenance Records**: Reviewing maintenance logs and historical data helps millwrights understand the machine's past performance and any recurring issues. This information can provide valuable insights into potential causes of current problems. 3. **Isolation of Faults**: By systematically isolating different components or systems within the machinery, millwrights can narrow down the possible causes of a malfunction. This methodical approach ensures that they address the root cause rather than just treating symptoms. 4. **Use of Diagnostic Tools**: Advanced diagnostic tools like oscilloscopes, multimeters, and software-based diagnostic systems are essential for identifying electrical or mechanical faults. These tools help millwrights gather precise data that aids in accurate diagnosis. 5. **Consultation with Manuals and Documentation**: Referencing manufacturer manuals, technical specifications, and industry standards ensures that millwrights adhere to best practices and follow recommended procedures for troubleshooting and repair. 6. **Collaboration with Other Technicians**: In complex cases, millwrights may collaborate with other technicians or engineers to leverage their expertise and gain a broader perspective on the issue at hand. 7. **Safety Protocols**: Safety is paramount in any repair operation. Millwrights must adhere to strict safety protocols, including lockout/tagout procedures, to prevent injuries and ensure a safe working environment. 8. **Repair Strategies**: Once the issue is identified, millwrights implement appropriate repair strategies. This may involve replacing worn-out parts, adjusting misaligned components, or performing more extensive overhauls. They also ensure that all repairs are done to meet or exceed industry standards. 9. **Testing and Validation**: After completing repairs, millwrights conduct thorough tests to validate that the machinery is functioning correctly and safely. This step is crucial for ensuring that the repair is effective and that the equipment will operate reliably over time. 10. **Documentation and Reporting**: Finally, millwrights document all troubleshooting steps, repairs made, and test results. This documentation helps in maintaining accurate records and facilitates future maintenance activities by providing a clear history of the equipment's performance and any issues encountered. By employing these techniques, millwrights can efficiently troubleshoot and repair complex machinery, ensuring optimal performance and minimizing downtime in industrial settings. Their ability to diagnose and fix problems quickly is essential for maintaining productivity and safety across various industries.
Collaboration with Other Tradespeople
Collaboration with other tradespeople is a crucial aspect of a millwright's daily life and tasks. Millwrights often work in tandem with various skilled professionals to ensure the efficient installation, maintenance, and repair of machinery and equipment. For instance, they frequently collaborate with electricians to connect electrical systems to machinery, ensuring that all components are properly wired and functioning safely. Additionally, millwrights work closely with welders to fabricate or repair metal parts, leveraging their expertise to create or mend critical components. They also coordinate with plumbers when dealing with hydraulic or pneumatic systems, ensuring that fluid dynamics are correctly managed. Furthermore, millwrights interact with carpenters and riggers during the construction phase of projects, where precise alignment and structural integrity are paramount. In many cases, they also consult with engineers to interpret blueprints and specifications accurately, ensuring that installations meet design standards. This interdisciplinary collaboration not only enhances the quality of work but also fosters a safer working environment by pooling diverse skill sets and knowledge. By working together seamlessly, millwrights and other tradespeople can complete complex projects efficiently and effectively, contributing to the overall success of industrial operations. This collaborative approach underscores the importance of teamwork in the field of millwrighting, where no single trade can accomplish the task alone.
The Future and Importance of Millwrights in Industry
The future of millwrights in industry is poised for significant growth and transformation, driven by several key factors. As technology continues to advance, millwrights will need to adapt to new tools and methodologies, ensuring they remain at the forefront of industrial maintenance and installation. This adaptability will be crucial in leveraging technological advancements and innovations. Additionally, the job outlook for millwrights is highly favorable, with increasing demand for skilled professionals who can manage complex machinery and equipment. The impact on industrial efficiency and safety will also be substantial, as millwrights play a critical role in maintaining and optimizing equipment, thereby reducing downtime and enhancing overall safety standards. As we delve into the specifics, it becomes clear that technological advancements and adaptations will be a cornerstone of the millwright's evolving role, setting the stage for a future where their skills are more valuable than ever. Transitioning to the first supporting paragraph, we will explore how **Technological Advancements and Adaptations** are reshaping the landscape for millwrights.
Technological Advancements and Adaptations
Technological advancements and adaptations are revolutionizing the role of millwrights in industry, enhancing their efficiency, safety, and overall impact. With the advent of advanced machinery and automation, millwrights are now equipped to handle more complex tasks with greater precision. For instance, the integration of robotics and artificial intelligence (AI) allows for predictive maintenance, reducing downtime and increasing productivity. Millwrights can leverage these technologies to perform routine inspections and repairs more effectively, ensuring that equipment operates at optimal levels. The use of augmented reality (AR) and virtual reality (VR) tools is also transforming the training and execution processes for millwrights. These technologies enable immersive learning experiences, allowing new millwrights to gain hands-on experience in a simulated environment before working on actual machinery. This not only improves their skills but also enhances safety by reducing the risk of accidents during training. Furthermore, advancements in data analytics and the Internet of Things (IoT) enable real-time monitoring of equipment performance. Millwrights can access detailed data on machine health, energy consumption, and operational efficiency, facilitating proactive maintenance and minimizing the likelihood of unexpected failures. This data-driven approach also helps in optimizing resource allocation and scheduling maintenance activities more effectively. In addition, the adoption of 3D printing and additive manufacturing is changing how millwrights approach repairs and replacements. Custom parts can be fabricated quickly and accurately, reducing lead times and costs associated with traditional manufacturing methods. This capability is particularly valuable in industries where downtime can be costly, such as in power generation or chemical processing. Moreover, advancements in communication technologies like 5G networks and cloud computing are improving collaboration among millwrights and other stakeholders. Real-time communication and data sharing facilitate better coordination during maintenance activities, ensuring that all team members are aligned and working efficiently towards common goals. Overall, these technological advancements and adaptations are not only enhancing the capabilities of millwrights but also underscoring their importance in maintaining and optimizing industrial operations. As industries continue to evolve, the role of millwrights will remain critical in ensuring that machinery operates safely and efficiently, driving productivity and innovation forward.
Job Outlook and Career Opportunities
The job outlook and career opportunities for millwrights are highly promising, driven by the increasing demand for skilled tradespeople in various industries. As a critical component of industrial maintenance and construction, millwrights play a pivotal role in ensuring the smooth operation of machinery and equipment. According to labor market projections, the demand for millwrights is expected to grow at a rate that is faster than the average for all occupations, primarily due to the need for skilled workers to install, maintain, and repair complex machinery in sectors such as manufacturing, power generation, and construction. Millwrights have diverse career opportunities across different industries. In manufacturing, they are essential for setting up and maintaining production lines, ensuring that machinery operates efficiently and safely. In the energy sector, millwrights are crucial for the installation and maintenance of turbines, generators, and other equipment necessary for power generation. Additionally, in construction, millwrights work on building and installing heavy machinery and equipment, contributing to the completion of large-scale projects. The versatility of millwrights also opens up opportunities for advancement. With experience, millwrights can move into supervisory roles or become specialized in specific types of machinery or industries. Some may choose to start their own contracting businesses, while others may pursue roles in training and education, teaching the next generation of millwrights. Furthermore, the increasing focus on renewable energy and sustainable practices is likely to create new niches for millwrights skilled in installing and maintaining green technologies such as wind turbines and solar panels. In terms of compensation, millwrights are generally well-paid due to their specialized skills and the critical nature of their work. Median salaries for millwrights are typically higher than those for many other trades, reflecting the value placed on their expertise. Moreover, many millwrights belong to unions or collective bargaining agreements, which often provide additional benefits such as health insurance, retirement plans, and apprenticeship programs. Overall, the future for millwrights looks bright, with a strong job outlook and numerous career opportunities available. As industries continue to evolve and rely more heavily on complex machinery, the demand for skilled millwrights will only continue to grow, making this trade an attractive and rewarding career choice for those interested in hands-on work and problem-solving.
Impact on Industrial Efficiency and Safety
The impact of millwrights on industrial efficiency and safety is multifaceted and profound. Millwrights, skilled tradespeople specializing in the installation, maintenance, and repair of machinery and equipment, play a crucial role in ensuring that industrial operations run smoothly and safely. Their expertise in precision alignment, troubleshooting, and preventive maintenance significantly enhances the overall efficiency of industrial processes. By ensuring that machinery is properly installed and maintained, millwrights reduce downtime, extend the lifespan of equipment, and optimize production output. This not only boosts productivity but also helps in controlling operational costs by minimizing the need for frequent repairs and replacements. Moreover, millwrights are instrumental in maintaining a safe working environment. They adhere to stringent safety protocols and regulations, ensuring that all machinery is installed and operated in compliance with industry standards. This includes conducting regular inspections to identify potential hazards and implementing corrective measures to prevent accidents. Their attention to detail and adherence to safety guidelines help in reducing workplace injuries and fatalities, thereby fostering a safer and healthier work environment. Additionally, millwrights often collaborate with other professionals such as engineers and safety specialists to develop and implement comprehensive safety plans, further enhancing the safety culture within industrial settings. The future importance of millwrights in industry is underscored by the increasing complexity of modern machinery and the growing emphasis on automation and technology. As industries continue to adopt advanced technologies like robotics and artificial intelligence, the demand for skilled millwrights who can install, maintain, and troubleshoot these sophisticated systems will only rise. Furthermore, the need for sustainable practices and energy efficiency will require millwrights to be adept at integrating green technologies into existing infrastructure, making them indispensable for future industrial development. In summary, the role of millwrights in enhancing industrial efficiency and safety is vital, and their importance will continue to grow as industries evolve and become more technologically advanced.