What Is A Dynamic Load

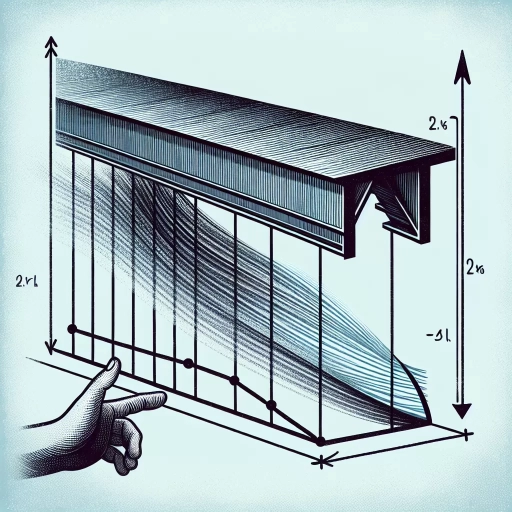
In the realm of engineering and structural analysis, understanding the concept of dynamic load is crucial for ensuring the safety and durability of various systems and structures. A dynamic load, unlike its static counterpart, is a force that varies over time, often due to external factors such as vibrations, impacts, or cyclic stresses. This type of loading can significantly affect the performance and lifespan of mechanical components, buildings, and other engineered structures. To grasp the full implications of dynamic loads, it is essential to delve into three key areas: **Understanding the Concept of Dynamic Load**, which explores the fundamental principles and characteristics of these forces; **Factors Influencing Dynamic Load**, which examines the various elements that contribute to their magnitude and frequency; and **Calculating and Managing Dynamic Load**, which discusses the methods and strategies for accurately predicting and mitigating their effects. By understanding these aspects, engineers and designers can better design and optimize systems to withstand the challenges posed by dynamic loads. Let's begin by **Understanding the Concept of Dynamic Load** to lay the groundwork for a comprehensive exploration of this critical topic.
Understanding the Concept of Dynamic Load
Understanding the concept of dynamic load is crucial in various engineering and scientific disciplines, as it directly impacts the design, safety, and efficiency of structures and systems. Dynamic loads, unlike static loads, are time-varying forces that can significantly alter the behavior of materials and structures. To grasp this complex concept, it is essential to delve into three key areas: the definition and basic principles of dynamic loads, the various types of dynamic loads, and their real-world applications. First, understanding the definition and basic principles of dynamic loads provides a foundational knowledge of how these forces interact with different materials and structures. This includes recognizing the differences between static and dynamic loads, as well as the mathematical models used to predict and analyze dynamic load behavior. Next, exploring the types of dynamic loads helps in identifying specific scenarios where these forces are encountered. This could range from impact loads to cyclic loads, each with its unique characteristics and effects on structures. Finally, examining real-world applications of dynamic load analysis highlights its practical importance in fields such as civil engineering, mechanical engineering, and aerospace engineering. By understanding how dynamic loads are managed in real-world scenarios, engineers can design safer, more resilient structures. Transitioning to the definition and basic principles of dynamic loads, it becomes clear that a thorough understanding of these fundamentals is the cornerstone for any further exploration into this critical area.
Definition and Basic Principles
Understanding the concept of dynamic load begins with a clear definition and an exploration of its basic principles. Dynamic load refers to the forces that act on a structure or system over time, varying in magnitude and direction. Unlike static loads, which remain constant, dynamic loads are characterized by their fluctuating nature, often resulting from external factors such as wind, seismic activity, or the movement of vehicles on a bridge. The basic principles underlying dynamic loads involve several key concepts: 1. **Frequency and Amplitude**: Dynamic loads are described in terms of their frequency (the number of cycles per second) and amplitude (the maximum displacement from the equilibrium position). These parameters are crucial for determining the stress and strain on a structure. 2. **Resonance**: When the frequency of the dynamic load matches the natural frequency of the structure, resonance occurs. This can lead to amplified stresses and potentially catastrophic failures if not properly managed through design and engineering. 3. **Damping**: Damping refers to the energy dissipation mechanisms within a system that reduce the amplitude of oscillations over time. Proper damping is essential for stabilizing structures under dynamic loading conditions. 4. **Inertia and Elasticity**: The response of a structure to dynamic loads depends on its inertia (resistance to changes in motion) and elasticity (ability to deform under stress and return to its original shape). These properties influence how forces are distributed and absorbed within the structure. 5. **Time-Dependent Behavior**: Unlike static loads, dynamic loads require an understanding of how structures behave over time. This involves analyzing the transient response (the initial reaction) and the steady-state response (the long-term behavior) of the system. 6. **Material Properties**: The material properties of a structure, such as its stiffness, strength, and ductility, play a critical role in its ability to withstand dynamic loads. Engineers must select materials that can absorb and distribute these forces effectively. 7. **Design Considerations**: Designing for dynamic loads involves sophisticated analysis techniques, including finite element methods and modal analysis. These tools help engineers predict how structures will respond to various loading scenarios, ensuring safety and durability. In summary, understanding dynamic loads is pivotal for the safe and efficient design of structures that must endure varying forces over time. By grasping the fundamental principles of frequency, amplitude, resonance, damping, inertia, elasticity, time-dependent behavior, and material properties, engineers can create resilient structures capable of withstanding the dynamic stresses imposed by real-world conditions. This knowledge is essential for ensuring that buildings, bridges, and other critical infrastructure can perform reliably under a wide range of dynamic loading conditions.
Types of Dynamic Loads
Dynamic loads, which are forces that vary over time, play a crucial role in the design and analysis of structures, machinery, and other engineering systems. Understanding the different types of dynamic loads is essential for ensuring the safety, durability, and performance of these systems. There are several key types of dynamic loads that engineers must consider. **Impact Loads** are sudden and brief forces that occur when two objects collide or when a structure is subjected to a sudden drop or fall. These loads can be particularly damaging because they concentrate a large amount of energy into a very short time period, often exceeding the static strength of materials. For instance, in automotive engineering, impact loads are critical in crash testing to ensure vehicle safety. **Vibration Loads** arise from repetitive motion and can be either forced or self-excited. Forced vibrations occur when an external force causes the system to oscillate at a specific frequency, while self-excited vibrations are generated internally by the system itself. Vibration loads are significant in mechanical engineering as they can lead to fatigue failure over time if not properly managed. **Cyclic Loads** involve repeated application and removal of forces over multiple cycles. These loads are common in machinery and structural components that undergo repetitive stress, such as bridges under traffic or aircraft wings during flight. Cyclic loading can lead to fatigue failure if the material's endurance limit is exceeded. **Random Loads** are unpredictable and vary in both magnitude and frequency over time. These loads are often encountered in natural phenomena like wind, waves, or seismic activity. Random loads pose significant challenges in design because their variability makes it difficult to predict peak values accurately. **Shock Loads** are similar to impact loads but typically involve a more gradual application of force over a slightly longer period. These loads can still cause significant stress on structures and are often seen in scenarios where sudden deceleration occurs, such as during landing of aircraft or braking of vehicles. **Seismic Loads** result from earthquakes and involve complex motions that include horizontal and vertical components. These loads are critical in civil engineering for designing buildings and bridges that can withstand seismic activity without collapsing. Each type of dynamic load requires specific analytical techniques and design considerations to ensure that structures and systems can withstand them without failure. By understanding these different types of dynamic loads, engineers can develop more robust designs that enhance safety, efficiency, and longevity across various fields of engineering. This comprehensive understanding is pivotal in mitigating risks associated with dynamic loading conditions and ensuring optimal performance under real-world operating conditions.
Real-World Applications
Understanding the concept of dynamic load is crucial for various real-world applications, where the ability to manage and predict changing forces is paramount. In the field of **civil engineering**, dynamic loads play a significant role in designing structures such as bridges, skyscrapers, and dams. These structures must withstand not only static loads like the weight of the building itself but also dynamic loads from wind, seismic activity, and traffic. For instance, bridge designers use advanced computational models to simulate how different types of dynamic loads—such as those from high-speed vehicles or extreme weather conditions—will affect the structure's integrity and stability. In **aerospace engineering**, dynamic loads are critical in the design and operation of aircraft and spacecraft. These vehicles are subjected to a wide range of dynamic forces during flight, including turbulence, gusts, and the stresses of takeoff and landing. Engineers must meticulously analyze these loads to ensure that the aircraft's materials and structural components can endure them without compromising safety or performance. Similarly, in **automotive engineering**, understanding dynamic loads helps in designing safer and more efficient vehicles. Car manufacturers use simulations to test how vehicles respond to various road conditions and impacts, which aids in optimizing suspension systems and enhancing overall vehicle stability. The **energy sector** also relies heavily on understanding dynamic loads. In power generation, particularly in renewable energy sources like wind turbines and hydroelectric dams, dynamic loads are essential for optimizing performance and ensuring reliability. Wind turbines, for example, must be designed to handle fluctuating wind speeds and directions without suffering mechanical failure. In hydroelectric systems, dynamic loads from water flow variations need careful management to maintain efficient power generation while preventing damage to turbines. In **medical devices**, dynamic loads are significant in the development of prosthetics and orthotics. These devices must be able to withstand the dynamic forces generated by human movement, ensuring both comfort and functionality for users. Advanced materials and designs are used to mimic natural joints' ability to absorb and distribute dynamic loads, thereby enhancing patient mobility and reducing the risk of injury. Furthermore, **industrial machinery** benefits from an understanding of dynamic loads. Manufacturing equipment such as conveyor belts, pumps, and gears are subjected to continuous dynamic forces that can lead to wear and tear if not properly managed. By analyzing these loads, engineers can optimize machine design for increased durability and efficiency, reducing downtime and maintenance costs. Lastly, **sports equipment** manufacturers also leverage knowledge of dynamic loads to create better products. For instance, bicycle frames are designed using finite element analysis to withstand the dynamic stresses imposed by riders' movements and road conditions. Similarly, golf clubs are engineered with materials that can handle the high-speed impacts involved in golf swings without compromising performance or safety. In summary, understanding dynamic loads is essential across a wide spectrum of industries where managing changing forces is critical for safety, efficiency, and performance. By applying this knowledge through advanced simulations and material science, engineers can create more resilient structures, safer vehicles, more efficient machinery, and better-performing sports equipment—ultimately enhancing our daily lives in numerous ways.
Factors Influencing Dynamic Load
Dynamic loads, which are forces that change over time, are influenced by a variety of critical factors that must be understood to ensure the stability and performance of structures and machinery. Three key elements play a significant role in determining these loads: speed and acceleration, mass and inertia, and environmental conditions. Speed and acceleration are fundamental because they directly impact the magnitude and direction of dynamic forces. For instance, high-speed operations or rapid changes in velocity can generate significant inertial forces that must be accounted for in design and operation. Mass and inertia are equally important as they determine how an object resists changes in its motion. The greater the mass, the greater the inertia, and thus the more force is required to alter its state of motion, which in turn affects the dynamic load experienced. Environmental conditions such as temperature, humidity, and external forces like wind or seismic activity also significantly influence dynamic loads. These conditions can alter material properties and introduce additional stresses that need to be considered. Understanding these factors is crucial for designing and maintaining systems that can withstand dynamic loads effectively. By examining each of these elements, engineers can better predict and manage the stresses imposed on structures and machinery, ensuring safety and efficiency. Let's delve deeper into the first of these critical factors: **Speed and Acceleration**.
Speed and Acceleration
Speed and acceleration are fundamental concepts in understanding dynamic loads, as they directly influence the forces exerted on structures and mechanisms. **Speed**, the rate of change of an object's position with respect to time, is a scalar quantity that provides insight into how fast an object is moving. However, it does not account for changes in direction. On the other hand, **acceleration**, a vector quantity, measures the rate of change of velocity and includes both the magnitude and direction of this change. This distinction is crucial because acceleration, not just speed, determines the dynamic loads experienced by a system. When an object accelerates, it experiences inertial forces due to its resistance to changes in motion. According to Newton's second law of motion, force (F) is equal to mass (m) times acceleration (a): F = ma. This means that even if an object is moving at a constant speed, any change in direction (which involves acceleration) will generate forces that contribute to dynamic loads. For instance, in a vehicle turning a corner, the tires and suspension system experience significant dynamic loads due to the lateral acceleration, even if the vehicle's speed remains constant. In engineering and design, understanding these principles is essential for ensuring structural integrity and safety. For example, in bridge design, engineers must consider the dynamic loads imposed by vehicles accelerating or decelerating as they cross the bridge. Similarly, in aerospace engineering, the high accelerations experienced during launch and re-entry phases necessitate careful consideration of dynamic loads to prevent structural failure. Moreover, the relationship between speed and acceleration affects how materials respond under different loading conditions. High-speed impacts can result in severe dynamic loads due to the rapid acceleration involved. This is why crash testing in automotive engineering involves simulating various impact scenarios to evaluate how vehicles withstand sudden decelerations and the resulting dynamic forces. In addition to these direct effects, speed and acceleration also influence other factors that contribute to dynamic loads. For example, vibrations and oscillations can arise from uneven surfaces or imbalances in rotating parts, leading to additional dynamic forces. These vibrations are more pronounced at higher speeds and accelerations, further complicating the analysis of dynamic loads. In conclusion, speed and acceleration are interlinked yet distinct factors that significantly influence dynamic loads. While speed provides a baseline understanding of an object's motion, acceleration is the key determinant of the inertial forces and resulting dynamic loads. By comprehending these principles, engineers can design more resilient structures and mechanisms capable of withstanding the stresses imposed by various motion scenarios. This understanding is pivotal in ensuring safety, efficiency, and reliability across a wide range of applications from transportation to aerospace engineering.
Mass and Inertia
**Mass and Inertia: Cornerstones of Dynamic Load** Mass and inertia are fundamental concepts that underpin the understanding of dynamic loads, which are forces that vary over time and can significantly impact the behavior of mechanical systems. Mass, a measure of the amount of matter in an object, is a key determinant of an object's resistance to changes in its motion. This resistance is known as inertia, a property described by Newton's First Law of Motion, which states that an object at rest will remain at rest, and an object in motion will continue to move with a constant velocity, unless acted upon by an external force. The relationship between mass and inertia is crucial because it directly influences how an object responds to dynamic loads. For instance, in a system subjected to varying forces, such as a vehicle navigating uneven terrain or a machine experiencing cyclic loading, the mass of the components plays a critical role in determining the magnitude of the inertial forces that arise. These inertial forces can lead to significant stresses and strains on the system, potentially causing wear, fatigue, or even failure if not properly managed. In engineering applications, understanding the interplay between mass and inertia is essential for designing robust and reliable systems. For example, in the design of bridges, engineers must consider the inertial effects of moving vehicles to ensure that the structure can withstand dynamic loads without compromising safety. Similarly, in aerospace engineering, the mass distribution of aircraft components is meticulously optimized to minimize inertial forces during flight maneuvers, thereby enhancing stability and performance. Moreover, the concept of mass and inertia extends beyond mechanical systems to include considerations of material properties. Different materials have varying densities, which affect their mass per unit volume. This variability can significantly impact the inertial behavior of components made from these materials. For instance, lightweight materials like aluminum or carbon fiber may offer advantages in terms of reduced mass and lower inertial forces but must be carefully selected to ensure they meet the required strength and durability standards. In summary, mass and inertia are integral factors influencing dynamic loads. By understanding how these properties interact within a system, engineers can design more resilient structures and machines that are better equipped to handle the stresses imposed by varying forces over time. This knowledge is pivotal in ensuring the safety, efficiency, and longevity of mechanical systems across diverse fields of engineering. As such, it forms a critical component of the broader discussion on dynamic loads and their impact on system performance.
Environmental Conditions
Environmental conditions play a crucial role in influencing dynamic loads, which are forces that vary over time and can significantly impact the structural integrity and performance of various systems. These conditions encompass a wide range of factors including temperature, humidity, wind, seismic activity, and weather patterns. Temperature fluctuations, for instance, can cause materials to expand and contract, leading to changes in stress levels within structures. In extreme cases, such as during heatwaves or cold snaps, these thermal stresses can become critical, potentially leading to material failure or reduced lifespan. Humidity also affects dynamic loads by altering the physical properties of materials; for example, high humidity can lead to corrosion in metals or degradation in composites, while low humidity can cause brittleness in certain materials. Wind is another significant environmental factor that influences dynamic loads. Wind-induced forces can cause vibrations and oscillations in structures like bridges, tall buildings, and wind turbines. These forces are particularly pertinent in coastal areas or regions prone to storms, where gusts can be intense and unpredictable. Seismic activity is another critical environmental condition that impacts dynamic loads. Earthquakes generate powerful ground motions that subject structures to sudden and intense forces, testing their resilience and ability to withstand such stresses without collapse. Weather patterns such as hurricanes, tornadoes, and typhoons also impose significant dynamic loads on structures. These storms bring high winds, heavy rainfall, and sometimes hail or lightning strikes, all of which can exert extraordinary forces on buildings and infrastructure. The unpredictability of these events necessitates robust design standards that account for worst-case scenarios to ensure public safety. In addition to these direct forces, environmental conditions can indirectly affect dynamic loads through their impact on soil and foundation stability. For example, heavy rainfall can lead to soil liquefaction during earthquakes or cause settlement issues due to water infiltration into the ground. Similarly, drought conditions can lead to soil shrinkage, affecting the foundation stability of structures. Understanding these environmental conditions is essential for engineers and architects who design structures intended to withstand various dynamic loads. By integrating data from meteorological studies, geotechnical analyses, and material science research into their designs, professionals can create more resilient and sustainable infrastructure that minimizes risks associated with environmental factors. In summary, environmental conditions are a critical component in assessing and mitigating dynamic loads. By considering temperature, humidity, wind patterns, seismic activity, weather events, and their effects on soil stability, engineers can develop structures that are better equipped to handle the stresses imposed by these varying environmental factors. This holistic approach ensures that infrastructure remains safe and functional under a wide range of conditions, ultimately enhancing public safety and reducing maintenance costs over time.
Calculating and Managing Dynamic Load
Calculating and managing dynamic loads is a critical aspect of various engineering disciplines, including civil, mechanical, and aerospace engineering. The accuracy and efficiency of load management directly impact the safety, performance, and longevity of structures and systems. To achieve this, engineers rely on a multifaceted approach that integrates mathematical models and formulas, advanced engineering techniques, and cutting-edge technological tools. Mathematical models and formulas provide the foundational framework for understanding and predicting load behaviors under different conditions. These models help in quantifying the stresses and strains on structures, enabling precise calculations that are essential for design and optimization. Engineering techniques for load management involve practical strategies and methodologies that translate theoretical models into real-world applications. These techniques ensure that the calculated loads are managed effectively to prevent failures and optimize performance. Technological tools for load analysis leverage advanced software and hardware to simulate, monitor, and analyze dynamic loads in real-time. These tools enhance the accuracy of load calculations and provide continuous feedback, allowing for timely adjustments and improvements. By combining these three elements—mathematical models and formulas, engineering techniques, and technological tools—engineers can comprehensively calculate and manage dynamic loads, ensuring robust and reliable systems. Let's delve deeper into the mathematical models and formulas that underpin this process.
Mathematical Models and Formulas
Mathematical models and formulas are indispensable tools in calculating and managing dynamic loads, which are forces that vary over time and can significantly impact the structural integrity and performance of systems. These models allow engineers to predict, analyze, and mitigate the effects of dynamic loads, ensuring the safety and efficiency of various engineering applications. At the heart of these models are fundamental principles from mechanics and mathematics, such as Newton's laws of motion, Hooke's law for elastic materials, and Fourier analysis for decomposing complex signals into simpler components. One of the key mathematical frameworks used is the finite element method (FEM), which discretizes a continuous system into smaller elements to solve partial differential equations that describe the behavior under dynamic loads. This method is particularly useful for complex geometries and non-linear material behaviors. Another crucial tool is the use of differential equations, such as those derived from Lagrange's equations or Hamilton's principle, which describe the motion of systems under various types of dynamic loading. For instance, in structural engineering, the dynamic load can be modeled using the equation of motion for a single-degree-of-freedom system: \(m \ddot{x} + c \dot{x} + kx = F(t)\), where \(m\) is mass, \(c\) is damping coefficient, \(k\) is stiffness, \(x\) is displacement, and \(F(t)\) represents the time-varying force. This equation helps in understanding how structures respond to seismic activity, wind loads, or other transient forces. In mechanical engineering, mathematical models often incorporate concepts from vibration analysis. The natural frequency of a system (\(\omega_n = \sqrt{\frac{k}{m}}\)) and its damping ratio (\(\zeta = \frac{c}{2 \sqrt{mk}}\)) are critical parameters that determine how a system will respond to dynamic loads. These parameters can be used to design systems that either amplify or dampen vibrations, depending on the application. Furthermore, statistical methods such as Monte Carlo simulations and reliability-based design optimization (RBDO) are employed to account for uncertainties in material properties and loading conditions. These techniques enable engineers to quantify the risk associated with dynamic loads and ensure that designs meet safety standards with a high degree of confidence. In addition to these analytical tools, computational software like MATLAB, ANSYS, and ABAQUS play a vital role in solving complex mathematical models numerically. These software packages allow for detailed simulations that can predict the behavior of systems under various dynamic loading scenarios, facilitating the optimization of designs before physical prototypes are built. In summary, mathematical models and formulas are essential for calculating and managing dynamic loads across various engineering disciplines. By leveraging these tools, engineers can predict and mitigate the effects of time-varying forces, ensuring the reliability, efficiency, and safety of engineered systems. Whether it's through analytical solutions or numerical simulations, these mathematical frameworks provide a robust foundation for addressing the challenges posed by dynamic loads.
Engineering Techniques for Load Management
Engineering techniques for load management are crucial in ensuring the efficient and reliable operation of various systems, particularly those subject to dynamic loads. Dynamic loads, which vary in magnitude and direction over time, pose significant challenges due to their unpredictable nature. To manage these loads effectively, engineers employ several advanced techniques. **1. Structural Analysis and Design:** Engineers use sophisticated structural analysis tools such as Finite Element Analysis (FEA) and Computational Fluid Dynamics (CFD) to simulate the behavior of structures under dynamic loads. These simulations help in optimizing the design of structures to withstand fluctuating forces, ensuring stability and minimizing the risk of failure. **2. Material Selection:** The choice of materials is critical in load management. Engineers select materials with properties that can absorb and distribute dynamic loads efficiently. For instance, composite materials like carbon fiber reinforced polymers (CFRP) are often used in aerospace and automotive applications due to their high strength-to-weight ratio and ability to handle dynamic stresses. **3. Damping Systems:** Damping systems are designed to reduce the amplitude of vibrations caused by dynamic loads. These systems can be passive (e.g., shock absorbers) or active (e.g., using actuators and sensors). Active damping systems, in particular, offer real-time adjustment capabilities, allowing for more precise control over load mitigation. **4. Load Balancing:** Load balancing techniques distribute the dynamic load across multiple components or systems to prevent any single point from experiencing excessive stress. This is commonly seen in power transmission systems where load-sharing mechanisms ensure that no single gear or bearing bears the entire load. **5. Real-Time Monitoring:** Advanced sensors and monitoring systems provide real-time data on the state of the system under dynamic loads. This data is used in predictive maintenance and condition-based monitoring, enabling proactive measures to prevent failures and optimize performance. **6. Control Systems:** Control systems, including feedback control and model predictive control, play a vital role in managing dynamic loads. These systems adjust parameters in real-time to maintain stability and performance. For example, in wind turbines, control systems adjust blade angles to optimize energy production while managing the dynamic loads imposed by wind gusts. **7. Energy Harvesting:** In some cases, engineers design systems to harness energy from dynamic loads rather than merely mitigating them. For instance, piezoelectric materials can convert mechanical stress into electrical energy, providing a sustainable solution for powering small devices. By integrating these engineering techniques, engineers can effectively calculate and manage dynamic loads, ensuring the reliability, efficiency, and safety of various systems across different industries. These methods not only enhance performance but also extend the lifespan of equipment, reducing maintenance costs and downtime. As technology continues to evolve, the development of more sophisticated load management techniques will remain a key focus area for engineers seeking to optimize system performance under dynamic conditions.
Technological Tools for Load Analysis
When it comes to calculating and managing dynamic loads, the integration of advanced technological tools is paramount. These tools not only enhance the accuracy and efficiency of load analysis but also provide real-time data and predictive insights, enabling better decision-making. One of the key technological tools in this domain is **Finite Element Analysis (FEA) software**. FEA allows engineers to simulate various loading conditions on structures, predicting stress distributions, deformations, and potential failure points with high precision. This method is particularly useful for complex systems where traditional analytical methods may fall short. Another crucial tool is **Sensors and IoT Devices**. These devices can be embedded within structures to monitor real-time load conditions, providing continuous data on stress, strain, and other critical parameters. This real-time monitoring enables immediate response to changes in load conditions, reducing the risk of structural failure. For instance, in bridges and buildings, sensors can detect subtle changes in structural integrity due to dynamic loads such as wind or traffic, allowing for proactive maintenance. **Machine Learning and Artificial Intelligence (AI)** also play a significant role in dynamic load analysis. AI algorithms can analyze vast amounts of data from sensors and other sources to predict future load patterns and potential risks. These predictive models help in optimizing structural design and maintenance schedules, ensuring that structures are resilient against dynamic loads. Additionally, AI-driven tools can automate the process of data analysis, freeing up engineers to focus on higher-level tasks such as design optimization and risk assessment. **Computational Fluid Dynamics (CFD)** is another powerful tool for analyzing dynamic loads, especially in scenarios involving fluid flow like wind or water. CFD simulations help engineers understand how fluids interact with structures, predicting pressure distributions and flow patterns that can induce dynamic loads. This is particularly important for designing structures like wind turbines, offshore platforms, and high-rise buildings that are susceptible to wind-induced loads. **Big Data Analytics** complements these tools by providing a comprehensive framework for managing and interpreting the vast amounts of data generated during load analysis. By leveraging big data analytics, engineers can identify trends, patterns, and anomalies in load data that might not be apparent through traditional methods. This holistic approach ensures that all aspects of dynamic load are considered, leading to more robust and reliable structural designs. In summary, the combination of FEA, sensors and IoT devices, machine learning and AI, CFD, and big data analytics forms a robust toolkit for calculating and managing dynamic loads. These technological tools not only enhance the precision of load analysis but also provide real-time monitoring and predictive capabilities, ensuring that structures can withstand the complexities of dynamic loading conditions. By integrating these technologies into their workflow, engineers can design safer, more efficient, and resilient structures that meet the demands of modern engineering challenges.