What Is Creep

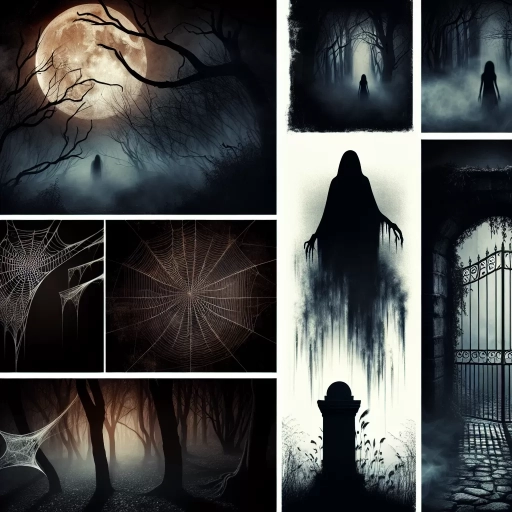
Creep, a phenomenon often overlooked but crucial in various engineering and materials science contexts, refers to the gradual deformation of materials under constant stress over time. This subtle yet significant process can have profound implications on the structural integrity and lifespan of materials, particularly in high-temperature environments. Understanding creep is essential for engineers and researchers as it directly influences the design and performance of critical infrastructure, machinery, and components. In this article, we will delve into the multifaceted nature of creep, starting with its fundamental definition and basic principles. We will then explore the intricate mechanisms and processes that drive creep, highlighting the complex interactions between material properties and environmental conditions. Finally, we will examine the practical applications and implications of creep in engineering, where accurate predictions and mitigations are vital for ensuring safety and efficiency. By grasping these aspects, we can better appreciate the importance of creep and its role in shaping our technological advancements. Let us begin by **Understanding Creep: Definition and Basics**.
Understanding Creep: Definition and Basics
Understanding creep is a fundamental aspect of materials science, particularly in engineering and manufacturing. Creep refers to the gradual deformation of materials under constant stress over time, which can significantly impact the structural integrity and lifespan of components. To fully grasp this phenomenon, it is essential to delve into several key areas. First, **Creep as a Material Property** highlights how different materials exhibit varying degrees of creep resistance, influenced by their intrinsic properties such as grain size, crystal structure, and alloy composition. This understanding is crucial for selecting appropriate materials for high-stress applications. Additionally, **Historical Context of Creep Studies** provides insight into how our knowledge of creep has evolved over time, from early observations to modern experimental techniques and theoretical models. Lastly, **Key Factors Influencing Creep Behavior** explores the external conditions like temperature, stress levels, and environmental factors that can accelerate or mitigate creep. By examining these aspects, engineers can better predict and manage creep in various engineering contexts. Transitioning to the specifics of **Creep as a Material Property**, we will explore how material characteristics play a pivotal role in determining creep behavior, setting the stage for more detailed analysis.
Creep as a Material Property
**Creep as a Material Property** Creep is a fundamental material property that describes the gradual deformation of materials under constant stress over time, often at elevated temperatures. This phenomenon is crucial in understanding the long-term behavior of materials, particularly in engineering applications where structural integrity and durability are paramount. Unlike elastic deformation, which is immediate and reversible, creep occurs slowly and can lead to permanent changes in the material's shape and structure. The rate of creep depends on several factors including the type of material, the magnitude of the applied stress, temperature, and the presence of any environmental factors such as corrosion or radiation. In metals and alloys, creep typically involves the movement of dislocations within the crystal lattice. At high temperatures, thermal energy provides the necessary activation energy for dislocations to move more freely, leading to plastic deformation. This process can be exacerbated by grain boundary sliding and diffusion mechanisms, which further contribute to the material's deformation. For polymers and ceramics, creep mechanisms can be more complex due to their unique microstructures. In polymers, molecular chains can slide past each other under stress, while in ceramics, grain boundary diffusion and dislocation movement play significant roles. Understanding creep is essential for designing and maintaining structures that operate under harsh conditions, such as power plants, aerospace components, and high-temperature industrial equipment. Engineers must consider the creep behavior of materials when selecting them for specific applications to ensure that they can withstand the stresses and temperatures involved without failing prematurely. For instance, in the design of turbine blades in jet engines or steam turbines, materials with low creep rates are chosen to prevent excessive deformation that could lead to reduced efficiency or catastrophic failure. The study of creep also involves various testing methods to quantify a material's creep resistance. These tests typically involve subjecting specimens to constant stress at elevated temperatures and measuring the resulting deformation over time. The data obtained from these tests are often plotted as creep curves, which provide valuable insights into the material's behavior under different conditions. By analyzing these curves, engineers can determine key parameters such as the primary creep stage (initial rapid deformation), secondary creep stage (steady-state deformation), and tertiary creep stage (accelerated deformation leading to failure). In addition to its practical implications, the study of creep has also contributed significantly to our understanding of material science and the underlying mechanisms that govern material behavior. Research into creep has led to the development of new materials with improved high-temperature properties, such as advanced alloys and composites. These advancements have enabled the creation of more efficient and reliable systems across various industries, from energy production to transportation. In summary, creep is a critical material property that influences the long-term performance and reliability of structures under stress and elevated temperatures. Its understanding is vital for engineering design, material selection, and ensuring the safety and efficiency of critical systems. By recognizing the factors that influence creep and employing appropriate testing and analysis techniques, engineers can develop materials and structures that meet stringent performance requirements over extended periods.
Historical Context of Creep Studies
The historical context of creep studies is deeply intertwined with the evolution of materials science and engineering, particularly in the late 19th and early 20th centuries. Creep, the gradual deformation of materials under constant stress over time, became a critical area of study as industrialization demanded more durable and reliable materials for machinery and infrastructure. The earliest systematic investigations into creep were driven by the need to understand the behavior of metals under high temperatures and stresses, especially in steam engines and other machinery used in the Industrial Revolution. One of the pioneers in this field was French engineer and physicist Henri Étienne Sainte-Claire Deville, who in the mid-19th century conducted experiments on the properties of metals at high temperatures. However, it was not until the early 20th century that creep began to receive more focused attention. The work of scientists like Andrade and Orowan laid foundational theories on the mechanisms of creep deformation. Andrade's 1910 paper on the creep of metals introduced the concept of "transient" and "steady-state" creep, which remains fundamental to understanding creep behavior today. The advent of World War II accelerated research in this area due to the urgent need for materials that could withstand extreme conditions. The development of jet engines, for instance, required alloys that could maintain their structural integrity at very high temperatures. This period saw significant contributions from researchers such as Norton and Bailey, who developed empirical laws to describe creep behavior. Norton's power-law relationship between stress and steady-state creep rate is still widely used. Post-war advancements in nuclear energy further propelled creep studies as nuclear reactors demanded materials capable of withstanding prolonged exposure to high temperatures and radiation. This led to a deeper understanding of the microstructural changes that occur during creep and the development of new materials with improved creep resistance. In recent decades, advancements in computational methods and experimental techniques have allowed for more precise modeling and prediction of creep behavior. Modern studies incorporate sophisticated tools such as finite element analysis and electron microscopy to elucidate the complex mechanisms underlying creep deformation at various scales. Throughout its history, the study of creep has been driven by practical engineering needs but has also contributed significantly to our fundamental understanding of material behavior under stress. Today, understanding creep is crucial not only for traditional industries like aerospace and power generation but also for emerging fields such as biomedical engineering and nanotechnology. The historical context of creep studies highlights how scientific inquiry often evolves in response to technological challenges, leading to broader insights that benefit multiple disciplines.
Key Factors Influencing Creep Behavior
Creep behavior, a critical aspect of material science, is influenced by several key factors that determine how materials deform over time under constant stress. **Temperature** is one of the most significant factors; as temperature increases, the rate of creep accelerates. This is because higher temperatures provide more thermal energy, allowing atoms to move more freely and facilitating the processes of dislocation glide and grain boundary sliding. **Stress level** also plays a crucial role; higher stresses generally lead to faster creep rates. The relationship between stress and creep rate can be described by various empirical models, such as the power-law creep model, which highlights the exponential increase in creep rate with increasing stress. **Material composition** is another vital factor. Different materials exhibit varying levels of resistance to creep due to their unique microstructural characteristics. For instance, materials with a high melting point and strong interatomic bonds, such as refractory metals and ceramics, tend to have better creep resistance compared to those with lower melting points and weaker bonds. **Grain size** and **grain boundary characteristics** are also important; finer grain sizes typically result in higher creep rates due to the increased grain boundary area, which can act as a pathway for dislocation movement and diffusion. **Microstructural changes**, including precipitation hardening and solid solution strengthening, can significantly impact creep behavior. These mechanisms can either enhance or degrade the material's resistance to creep depending on how they affect the material's microstructure over time. **Environmental conditions**, such as the presence of corrosive substances or radiation, can also influence creep behavior by altering the material's microstructure or introducing additional stress mechanisms. **Time** itself is a critical factor; creep is a time-dependent phenomenon, and the longer a material is subjected to stress, the more pronounced the creep deformation will be. Understanding the time-dependent nature of creep is essential for predicting long-term material performance in various engineering applications. Finally, **processing history** of the material, including factors like cold working and heat treatment, can influence its initial microstructure and thus its subsequent creep behavior. In summary, the interplay of these factors—temperature, stress level, material composition, grain size, microstructural changes, environmental conditions, time, and processing history—determines the creep behavior of a material. Understanding these influences is crucial for designing and selecting materials for high-temperature and high-stress applications where creep resistance is paramount. By carefully considering these factors, engineers can predict and mitigate creep-related failures, ensuring the reliability and longevity of critical components in industries such as aerospace, power generation, and chemical processing.
Mechanisms and Processes of Creep
Creep, a phenomenon where materials deform over time under constant stress, is a complex process influenced by several key mechanisms. Understanding these mechanisms is crucial for predicting material behavior in various engineering applications. This article delves into the primary processes driving creep deformation, focusing on three critical aspects: Dislocation Movement and Grain Boundary Sliding, Diffusion Mechanisms in Creep Deformation, and the Role of Temperature and Stress in Creep Processes. Dislocation Movement and Grain Boundary Sliding are fundamental to the initial stages of creep, where dislocations within the material's crystal structure move and grain boundaries slide, leading to plastic deformation. This movement is often the first step in the creep process, setting the stage for further deformation mechanisms. In addition to dislocation movement, diffusion mechanisms play a significant role in creep deformation. At elevated temperatures, atoms within the material can diffuse more freely, contributing to the material's deformation through vacancy diffusion and grain boundary diffusion. Temperature and stress are also pivotal factors in creep processes. Higher temperatures increase atomic mobility, while stress levels determine the rate at which creep occurs. These factors interact with dislocation movement and diffusion mechanisms to dictate the overall creep behavior of a material. By examining these interrelated mechanisms, we can gain a comprehensive understanding of how materials creep and how this knowledge can be applied to enhance material performance and longevity. Transitioning to the first supporting paragraph, we will explore in detail the role of Dislocation Movement and Grain Boundary Sliding in initiating and sustaining creep deformation.
Dislocation Movement and Grain Boundary Sliding
Dislocation movement and grain boundary sliding are two critical mechanisms that contribute to the complex phenomenon of creep, a gradual deformation of materials under constant stress over time. **Dislocation movement** involves the migration of line defects within the crystal lattice of a material. These dislocations can move through the lattice by gliding or climbing, processes that are facilitated by thermal energy. At elevated temperatures, dislocations can overcome obstacles such as other dislocations, impurities, or grain boundaries, leading to plastic deformation. This movement is particularly significant in metals and alloys where dislocation dynamics play a pivotal role in determining the material's strength and ductility. The rate at which dislocations move is influenced by factors such as temperature, stress level, and the presence of impurities or alloying elements. **Grain boundary sliding**, on the other hand, occurs at the interfaces between crystalline grains within a polycrystalline material. As grains deform under stress, their boundaries can slide past each other, contributing to overall material deformation. This process is more pronounced at high temperatures where grain boundary diffusion is enhanced, allowing atoms to move more freely along grain boundaries. Grain boundary sliding is particularly important in fine-grained materials where the proportion of grain boundary area is higher compared to coarse-grained materials. It often results in cavitation and crack formation at grain boundaries, which can lead to material failure if not managed properly. The interplay between dislocation movement and grain boundary sliding is crucial for understanding creep behavior, as these mechanisms can either reinforce or mitigate each other depending on the specific material and environmental conditions. In the context of creep mechanisms, both dislocation movement and grain boundary sliding are influenced by similar factors such as temperature, stress level, and material microstructure. However, their relative contributions can vary significantly depending on the specific material and the operating conditions. For instance, in some metals and alloys, dislocation movement may dominate at lower temperatures and higher stress levels, while grain boundary sliding becomes more prevalent at higher temperatures where diffusion processes are more active. Understanding these mechanisms is essential for designing materials and structures that must withstand prolonged exposure to stress at elevated temperatures, such as in power generation equipment or aerospace components. Moreover, the interaction between dislocations and grain boundaries can lead to complex microstructural changes during creep. For example, dislocations can pile up at grain boundaries, creating stress concentrations that facilitate grain boundary sliding. Conversely, grain boundary sliding can create new dislocations as grains move past each other. This dynamic interplay underscores the necessity of considering both mechanisms when predicting creep behavior and designing strategies to mitigate it. In summary, dislocation movement and grain boundary sliding are fundamental processes that drive creep deformation in materials. By understanding how these mechanisms interact and influence each other under various conditions, engineers can develop more robust materials and structures capable of withstanding the rigors of high-temperature service environments. This knowledge is critical for ensuring the reliability and longevity of components in industries where creep resistance is paramount.
Diffusion Mechanisms in Creep Deformation
Creep deformation, a critical aspect of material science, is significantly influenced by diffusion mechanisms. These mechanisms play a pivotal role in understanding how materials deform under constant stress over time. At the heart of creep deformation are the processes by which atoms or vacancies within the material lattice migrate, leading to gradual plastic deformation. One primary diffusion mechanism is **lattice diffusion**, where atoms move through the crystal lattice via vacancies. This process is temperature-dependent and becomes more pronounced at higher temperatures, where thermal energy facilitates the movement of atoms. As atoms diffuse, they can relocate to grain boundaries or other defects, contributing to the overall deformation of the material. Another key mechanism is **grain boundary diffusion**, which occurs along the boundaries between grains in polycrystalline materials. This type of diffusion is particularly significant because grain boundaries offer a pathway for faster atomic movement compared to lattice diffusion. The Coble creep mechanism, for instance, relies heavily on grain boundary diffusion and is often observed in fine-grained materials where grain boundary sliding and diffusion are dominant. **Dislocation climb** is another crucial diffusion-controlled process in creep deformation. Dislocations, which are line defects within the crystal structure, can move through the lattice by climbing over obstacles via vacancy diffusion. This climb allows dislocations to bypass barriers and continue their movement, contributing to the accumulation of plastic strain over time. Additionally, **pipe diffusion** can occur along dislocation lines themselves, providing an even faster pathway for atomic movement compared to lattice or grain boundary diffusion. This mechanism is particularly important in materials with high dislocation densities. The interplay between these diffusion mechanisms and other factors such as temperature, stress level, and material microstructure determines the overall creep behavior of a material. For example, at lower temperatures and stresses, lattice diffusion may dominate, while at higher temperatures and stresses, grain boundary diffusion and dislocation climb become more significant. Understanding these diffusion mechanisms is essential for predicting and mitigating creep deformation in engineering applications. By tailoring material microstructures and controlling environmental conditions such as temperature and stress levels, engineers can design materials that resist creep more effectively. This knowledge is critical in industries such as aerospace, power generation, and chemical processing where components are subjected to prolonged exposure to high temperatures and stresses. In summary, diffusion mechanisms are fundamental to understanding creep deformation. By elucidating how atoms and vacancies move within the material lattice and along defects like grain boundaries and dislocations, researchers can develop strategies to enhance material performance under conditions that would otherwise lead to significant creep-induced deformation. This insight not only aids in material selection but also guides the development of new materials with improved resistance to creep, thereby ensuring the reliability and longevity of critical components in various industrial applications.
Role of Temperature and Stress in Creep Processes
Temperature and stress are pivotal factors in the creep processes that materials undergo, particularly under prolonged exposure to high temperatures and constant loads. Creep, a gradual deformation over time, is significantly influenced by these two variables. **Temperature** plays a crucial role because it affects the material's microstructure and the mobility of dislocations within the material. At elevated temperatures, atoms gain kinetic energy, enhancing diffusion rates and dislocation movement. This increased atomic mobility facilitates grain boundary sliding and dislocation climb, which are key mechanisms in creep deformation. For instance, in metals like aluminum and steel, a small increase in temperature can exponentially increase the creep rate due to the enhanced diffusion processes. **Stress**, on the other hand, drives the deformation process by providing the necessary force for dislocations to move and for grain boundaries to slide. The magnitude of stress determines the rate at which creep occurs; higher stresses generally lead to faster creep rates. However, the relationship between stress and creep rate is not always linear. Below a certain threshold stress, known as the "creep threshold," minimal or no creep occurs. Above this threshold, even small increases in stress can lead to substantial increases in creep rate. This non-linear relationship is often described by power-law or exponential models, which help predict the creep behavior of materials under various stress conditions. The interplay between temperature and stress is complex and synergistic. For example, at lower temperatures, materials may exhibit a higher resistance to creep due to reduced atomic mobility, but if the applied stress is sufficiently high, it can still induce significant deformation over time. Conversely, at high temperatures, even moderate stresses can lead to rapid creep due to the enhanced diffusion and dislocation movement. Understanding this interplay is crucial for designing and selecting materials for high-temperature applications, such as in power plants, aerospace engineering, and advanced manufacturing processes. In addition to these primary factors, other secondary influences such as material composition, grain size, and environmental conditions (like oxidation or corrosion) also impact creep behavior. For instance, alloying elements can form precipitates that pin dislocations, thereby reducing creep rates. Similarly, fine-grained materials often exhibit better creep resistance compared to coarse-grained ones due to the increased grain boundary area that acts as a barrier to dislocation movement. In summary, the role of temperature and stress in creep processes is fundamental. Temperature enhances atomic mobility and diffusion rates, while stress provides the driving force for deformation. The intricate balance between these two factors, along with other material properties and environmental conditions, determines the overall creep behavior of a material. This understanding is essential for predicting material performance in high-temperature and high-stress environments, ensuring the reliability and longevity of critical components in various industrial applications.
Applications and Implications of Creep in Engineering
Creep, the gradual deformation of materials under constant stress over time, is a critical consideration in various engineering fields. Understanding its applications and implications is essential for ensuring the longevity and safety of structures and components. This article delves into the multifaceted aspects of creep, beginning with its significant role in high-temperature engineering applications. Here, we explore how materials behave under prolonged exposure to elevated temperatures, a scenario common in power plants, aerospace, and chemical processing. Additionally, we discuss design considerations that engineers must take into account to mitigate the effects of creep, including material selection, stress analysis, and innovative design strategies. Real-world case studies of creep failure are also examined, highlighting the consequences of neglecting creep in engineering design and the importance of proactive measures. By understanding these facets, engineers can better design and maintain systems that withstand the challenges posed by creep, particularly in high-temperature environments. This comprehensive approach sets the stage for our first focus: Creep in High-Temperature Engineering Applications.
Creep in High-Temperature Engineering Applications
In high-temperature engineering applications, creep is a critical phenomenon that significantly impacts the design, performance, and longevity of materials and structures. Creep refers to the gradual deformation of materials under constant stress over time, particularly at elevated temperatures where thermal energy enhances atomic mobility. This deformation can lead to structural failure if not properly managed. In industries such as power generation, aerospace, and chemical processing, where components are frequently exposed to high temperatures, understanding and mitigating creep is essential. For instance, in power plants, turbine blades and heat exchangers are subjected to continuous high-temperature conditions. Here, creep can cause these components to elongate or change shape, potentially leading to reduced efficiency or catastrophic failure. Engineers must select materials with high creep resistance, such as nickel-based superalloys or ceramic composites, and design components with safety factors that account for expected creep deformation over their service life. In aerospace engineering, components like jet engine parts and rocket nozzles face extreme thermal stresses during operation. Creep can compromise the structural integrity of these parts, affecting the overall safety and reliability of the aircraft or spacecraft. Advanced materials like single-crystal alloys and advanced ceramics are often used due to their superior high-temperature properties and resistance to creep. The implications of creep extend beyond material selection; they also influence the operational protocols and maintenance schedules of high-temperature systems. Regular inspections and monitoring for signs of creep deformation are crucial to prevent unexpected failures. Additionally, engineers may employ techniques such as stress relief treatments or periodic replacement of critical components to manage creep effects. Furthermore, research into creep mechanisms continues to drive innovation in material science. Understanding the microstructural changes that occur during creep allows for the development of new materials with enhanced properties. For example, grain boundary engineering and the introduction of nanoparticles can significantly improve a material's resistance to creep. In summary, creep in high-temperature engineering applications is a multifaceted challenge that requires careful material selection, sophisticated design strategies, and ongoing monitoring and maintenance. By addressing these challenges effectively, engineers can ensure the reliability and efficiency of critical systems across various industries, ultimately enhancing safety and performance under extreme conditions.
Design Considerations to Mitigate Creep Effects
When designing structures and components that are subject to prolonged exposure to high temperatures and stresses, mitigating creep effects is crucial to ensure long-term integrity and performance. Creep, the gradual deformation of materials over time under constant stress, can lead to premature failure if not adequately addressed. Several key design considerations must be taken into account to minimize creep effects. Firstly, **material selection** plays a critical role. Engineers should choose materials with high creep resistance, such as certain alloys and composites that exhibit superior strength and stability at elevated temperatures. For instance, nickel-based superalloys are often used in high-temperature applications like gas turbines due to their excellent creep properties. Secondly, **stress reduction** is essential. Designing components to operate within lower stress ranges can significantly reduce the likelihood of creep. This can be achieved through careful load distribution, optimizing component geometry, and employing stress-reducing features such as fillets and radii. Additionally, using techniques like finite element analysis (FEA) helps in identifying and mitigating high-stress areas. Thirdly, **temperature control** is vital. Since creep rates increase exponentially with temperature, maintaining components within a safe thermal range is critical. This involves designing effective cooling systems, using thermal barriers or coatings, and ensuring that heat sources are managed efficiently. Furthermore, **component geometry** and **structural design** must be optimized. Components should be designed with minimal surface area exposed to high temperatures and stresses. Structural elements like beams and columns should be configured to distribute loads evenly, reducing localized stress concentrations that can accelerate creep. Another important consideration is **surface treatment**. Applying surface treatments such as shot peening or nitriding can enhance the surface properties of materials, improving their resistance to creep by introducing compressive residual stresses that counteract tensile stresses. Regular **inspection and maintenance** are also crucial for mitigating creep effects. Implementing periodic inspections allows for early detection of any signs of creep deformation, enabling timely interventions such as component replacement or repair before catastrophic failure occurs. Lastly, **design for redundancy** is a prudent approach. Incorporating redundant systems or backup components ensures that even if one part fails due to creep, the overall system remains operational until repairs can be made. By integrating these design considerations into the engineering process, engineers can effectively mitigate the adverse effects of creep, ensuring the longevity and reliability of structures and components in demanding environments. This holistic approach not only enhances safety but also optimizes performance and reduces maintenance costs over the lifecycle of the system.
Case Studies: Real-World Examples of Creep Failure
**Case Studies: Real-World Examples of Creep Failure** Creep failure, a phenomenon where materials deform over time under constant stress, has significant implications in various engineering fields. Several real-world case studies illustrate the critical importance of understanding and mitigating creep to ensure the safety and longevity of structures and components. One notable example is the failure of the Liberty Ships during World War II. These ships, constructed using welded joints rather than rivets to expedite production, experienced catastrophic failures due to creep in the welds. The high-stress conditions and cyclic loading from wave action led to brittle fractures, resulting in the loss of several ships. This incident highlighted the need for rigorous material testing and design considerations to account for creep under operational conditions. Another compelling case is the failure of the Tacoma Narrows Bridge in 1940. Although primarily attributed to aerodynamic instability, subsequent analyses revealed that creep in the bridge's structural components contributed to the disaster. The continuous stress from wind and traffic loads caused gradual deformation, weakening the structure's integrity. This example underscores the importance of considering long-term material behavior in structural design, especially for critical infrastructure. In the realm of power generation, creep failure has been a recurring issue in steam turbines and boiler components. For instance, the failure of turbine blades in a nuclear power plant due to high-temperature creep led to significant downtime and costly repairs. The blades, subjected to constant thermal stress, underwent gradual deformation and eventual cracking. This incident emphasizes the necessity of selecting materials with high creep resistance and implementing regular maintenance schedules to monitor for early signs of creep damage. Aerospace engineering also provides stark examples of creep's impact. The Space Shuttle Columbia disaster in 2003 was partly attributed to the failure of reinforced carbon-carbon (RCC) panels due to thermal creep during re-entry. The panels, designed to withstand extreme temperatures, experienced material degradation over multiple missions, leading to a critical failure that compromised the shuttle's integrity. This tragedy underscores the critical need for advanced materials and rigorous testing protocols to ensure component reliability under extreme conditions. Lastly, in the oil and gas industry, creep failure has been observed in pipelines and drilling equipment. For example, the failure of a high-pressure pipeline due to creep in the welds resulted in a major environmental spill. The constant stress from internal pressure and external environmental factors caused gradual deformation and eventual rupture. This incident highlights the importance of regular inspections and material selection based on long-term performance criteria. These case studies collectively demonstrate that understanding and managing creep is crucial across various engineering disciplines. By integrating comprehensive material testing, advanced design methodologies, and stringent maintenance practices, engineers can mitigate the risks associated with creep failure, ensuring the reliability and safety of critical infrastructure and equipment.