What Does A Thermocouple Do

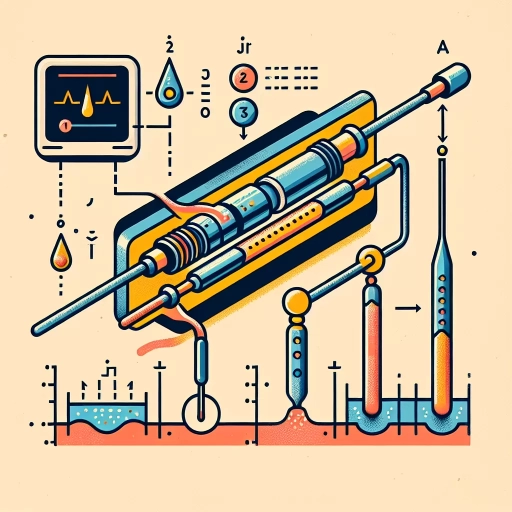
Thermocouples are versatile and essential devices in various industrial, scientific, and everyday applications, playing a crucial role in measuring temperature with high accuracy and reliability. These devices convert thermal energy into electrical signals, allowing for precise temperature monitoring in diverse environments. To fully appreciate the functionality and importance of thermocouples, it is necessary to delve into their fundamental principles, explore their wide range of applications, and understand their advantages, limitations, and maintenance requirements. This article will provide a comprehensive overview, starting with **Understanding the Basics of Thermocouples**, where we will examine the underlying mechanisms and types of thermocouples. We will then discuss **Applications and Uses of Thermocouples**, highlighting their role in industries such as aerospace, automotive, and manufacturing. Finally, we will analyze **Advantages, Limitations, and Maintenance of Thermocouples**, offering insights into their performance, potential drawbacks, and best practices for upkeep. By understanding these aspects, readers will gain a thorough appreciation for how thermocouples operate and their significance in modern technology. Let us begin by **Understanding the Basics of Thermocouples**.
Understanding the Basics of Thermocouples
Understanding the basics of thermocouples is crucial for anyone involved in temperature measurement and control across various industries. Thermocouples are versatile and reliable devices that convert thermal energy into electrical signals, making them indispensable tools in fields such as engineering, manufacturing, and research. To grasp the full potential of thermocouples, it is essential to delve into three key aspects: their definition and principle of operation, the different types available, and their key components and construction. Firstly, understanding the definition and principle of operation provides a foundational knowledge of how thermocouples work. This involves learning about the Seebeck effect, which is the fundamental phenomenon behind thermocouple functionality. By exploring this concept, one can appreciate the intrinsic mechanisms that allow thermocouples to generate voltage in response to temperature differences. Secondly, familiarizing oneself with the various types of thermocouples is vital for selecting the appropriate device for specific applications. Different types, such as K, J, T, and E thermocouples, each have unique characteristics and suitability for different temperature ranges and environments. Lastly, knowing the key components and construction of thermocouples helps in understanding their durability, accuracy, and maintenance requirements. This includes the materials used for the thermoelectric junctions, insulation, and protective casings. By starting with a clear understanding of the definition and principle of operation, one can build a solid foundation for further exploration into the diverse world of thermocouples. Let's begin by examining the definition and principle of operation in more detail.
Definition and Principle of Operation
**Definition and Principle of Operation** A thermocouple is a fundamental device in temperature measurement, leveraging the Seebeck effect to convert thermal energy into electrical signals. Essentially, a thermocouple consists of two dissimilar metals joined at one end, known as the hot junction, while the other ends are connected to a measuring device. The principle of operation hinges on the thermoelectric effect, where the difference in temperature between the hot junction and the cold junction (the point where the wires are connected to the measuring device) generates a small voltage. This voltage is directly proportional to the temperature difference, allowing for precise temperature measurement. When the hot junction is exposed to a higher temperature than the cold junction, electrons flow from the metal with the lower electron density to the metal with the higher electron density, creating an electric potential difference. This potential difference is measured by a voltmeter or other electrical measuring device, which can then be calibrated to indicate the temperature at the hot junction. The choice of metals for the thermocouple is critical, as different combinations yield different voltage outputs and temperature ranges. Common types include Type K (chromel-alumel), Type J (iron-constantan), and Type T (copper-constantan), each suited for specific applications based on their sensitivity, accuracy, and durability. The simplicity and robustness of thermocouples make them versatile tools in various industries, including aerospace, automotive, and industrial processes. They can withstand harsh environments and are often used in high-temperature applications where other temperature sensors might fail. However, it is crucial to consider factors such as oxidation, contamination, and electromagnetic interference when deploying thermocouples to ensure accurate readings. By understanding the fundamental principles behind thermocouples—namely the Seebeck effect and the specific characteristics of different metal combinations—users can effectively utilize these devices to monitor and control temperatures with high precision. This foundational knowledge is essential for optimizing thermocouple performance and ensuring reliable temperature measurements across diverse applications.
Types of Thermocouples
Thermocouples are versatile temperature-measuring devices that come in various types, each designed to cater to specific applications and environments. The primary classification of thermocouples is based on the materials used for their construction, which determines their temperature range, accuracy, and durability. **Type K (Chromel-Alumel):** One of the most commonly used thermocouples, Type K is known for its wide temperature range (-200°C to 1260°C) and good stability. It is widely applied in industrial processes, heating and cooling systems, and automotive applications. **Type J (Iron-Constantan):** Type J thermocouples are less expensive than Type K but have a narrower temperature range (-40°C to 760°C). They are often used in lower-temperature applications such as in HVAC systems and food processing. **Type T (Copper-Constantan):** With a temperature range of -200°C to 370°C, Type T thermocouples are particularly useful in cryogenic and low-temperature applications. They are also commonly used in laboratory settings due to their high accuracy. **Type E (Chromel-Constantan):** Known for its high sensitivity and wide temperature range (-200°C to 316°C), Type E thermocouples are ideal for precision measurements in scientific research and calibration purposes. **Type N (Nicrosil-Nisil):** Introduced as an alternative to Type K, Type N thermocouples offer better stability at high temperatures (up to 1300°C) and are less prone to degradation over time. They are often used in high-temperature industrial processes. **Type S (Platinum-Rhodium):** Type S thermocouples are made from noble metals, making them highly resistant to oxidation and corrosion. They have a wide temperature range (0°C to 1480°C) and are typically used in high-precision applications such as in the aerospace industry. **Type R (Platinum-Rhodium):** Similar to Type S but with a slightly different composition, Type R thermocouples also offer high accuracy and stability up to 1480°C. They are commonly used in laboratory furnaces and other high-temperature environments. **Type B (Platinum-Rhodium):** With an operating range of 0°C to 1820°C, Type B thermocouples are among the highest-temperature thermocouples available. However, they have lower sensitivity compared to other types and are typically used in very high-temperature industrial processes. Each type of thermocouple has its unique characteristics, advantages, and limitations, making it crucial to select the appropriate type based on the specific requirements of the application. Understanding these differences is essential for ensuring accurate temperature measurements and optimal performance in various industrial, scientific, and everyday applications. By choosing the right thermocouple type, users can ensure reliable and precise temperature monitoring, which is critical in maintaining process control, safety, and efficiency.
Key Components and Construction
When delving into the intricacies of thermocouples, it is crucial to understand their key components and construction. At its core, a thermocouple is a temperature-measuring device that relies on the principle of thermoelectricity, where two dissimilar metals are joined together to produce a small voltage proportional to the temperature difference between their junctions. The primary components include the sensing junction, the extension wires, and the insulation. The **sensing junction** is where the magic happens; it is the point where the two different metals meet. This junction can be configured in various ways, such as butt-welded, twisted, or soldered, depending on the application. The choice of metals is critical because different metal combinations yield different thermoelectric properties, leading to various types of thermocouples like Type K (chromel-alumel), Type J (iron-constantan), and Type T (copper-constantan), each suited for specific temperature ranges and environments. **Extension wires** are used to connect the sensing junction to the measuring instrument. These wires are typically made from the same materials as the thermocouple itself to ensure that no additional thermoelectric effects are introduced, which could skew the readings. However, in some cases, compensating cables may be used if the extension wires cannot be made from the same materials; these cables are designed to mimic the thermoelectric properties of the thermocouple. **Insulation** plays a vital role in maintaining the integrity of the thermocouple's readings. It protects the wires from environmental factors such as moisture, chemicals, and physical damage. Common insulating materials include ceramic, glass, or mineral-insulated metal sheaths. The choice of insulation depends on the operating conditions; for instance, high-temperature applications might require refractory insulation like ceramic or quartz. The **construction** of a thermocouple can vary significantly based on its intended use. For example, **grounded thermocouples** have the sensing junction in direct contact with the protective sheath, which can provide faster response times but may introduce electrical noise. **Ungrounded thermocouples**, on the other hand, have an insulating layer between the junction and the sheath, offering better electrical isolation but potentially slower response times. In addition to these core components, other factors such as **protection tubes** and **connectors** are also important. Protection tubes shield the thermocouple from harsh environments like high pressures or corrosive substances, while connectors ensure secure and reliable connections to measuring instruments. Understanding these key components and their construction is essential for selecting and using thermocouples effectively. By knowing how each part contributes to the overall performance of the device, users can optimize their temperature measurement setups for accuracy, reliability, and longevity. Whether in industrial processes, scientific research, or everyday applications, the meticulous design and construction of thermocouples make them indispensable tools for precise temperature measurement.
Applications and Uses of Thermocouples
Thermocouples are versatile and essential tools in various industries due to their ability to accurately measure temperature across a wide range of conditions. Their applications span multiple sectors, each leveraging their unique characteristics to achieve specific goals. In industrial settings, thermocouples play a crucial role in temperature measurement, ensuring the optimal operation of machinery and processes. Beyond this, they are integral in aerospace and automotive applications, where precise temperature monitoring is vital for safety and performance. Additionally, thermocouples find significant use in medical and scientific research, enabling precise temperature control and measurement in critical experiments and treatments. This article will delve into these diverse applications, starting with the critical role of thermocouples in industrial temperature measurement, where their reliability and durability are paramount for maintaining operational efficiency and safety standards.
Industrial Temperature Measurement
Industrial temperature measurement is a critical component in various sectors, including manufacturing, chemical processing, power generation, and aerospace. The accuracy and reliability of temperature measurements directly impact the efficiency, safety, and quality of industrial processes. Thermocouples, due to their robustness, wide temperature range, and rapid response time, are among the most widely used temperature measurement devices in industrial settings. In manufacturing, thermocouples are employed to monitor and control temperatures in furnaces, heat exchangers, and other process equipment. For instance, in steel production, thermocouples ensure that the molten metal reaches the precise temperature required for casting or rolling. Similarly, in the chemical industry, thermocouples are used to monitor reaction temperatures in reactors and distillation columns, helping to optimize chemical reactions and prevent overheating or underheating that could lead to unsafe conditions or product degradation. In power generation, particularly in nuclear and fossil fuel plants, thermocouples play a vital role in monitoring temperatures of critical components such as turbines, generators, and heat exchangers. This ensures that these components operate within safe limits, preventing overheating which could lead to equipment failure or even catastrophic events. Additionally, thermocouples are used in the aerospace industry for monitoring engine temperatures during flight and ground testing, providing essential data for engine performance optimization and safety. The versatility of thermocouples also extends to food processing and pharmaceutical industries where precise temperature control is essential for product quality and safety. In these sectors, thermocouples are used in ovens, pasteurizers, and sterilizers to ensure that products are heated or cooled to the required temperatures without compromising their integrity. Moreover, the rugged design of thermocouples makes them suitable for harsh environments where other temperature measurement devices might fail. They can withstand high temperatures, corrosive atmospheres, and mechanical stress, making them ideal for use in extreme conditions such as those found in oil refineries or chemical plants. The ease of installation and maintenance of thermocouples further enhances their appeal in industrial applications. They can be easily integrated into existing systems and require minimal calibration compared to other temperature measurement devices. This convenience, combined with their reliability and accuracy over a wide range of temperatures, makes thermocouples an indispensable tool for ensuring the smooth operation of industrial processes. In summary, industrial temperature measurement is a crucial aspect of modern industry, and thermocouples are at the forefront of this field due to their reliability, versatility, and robustness. Their widespread use across various industries underscores their importance in maintaining process efficiency, ensuring product quality, and enhancing overall safety standards. Whether it's monitoring furnace temperatures in steel production or engine temperatures in aerospace applications, thermocouples provide the accurate and reliable data needed to optimize industrial operations effectively.
Aerospace and Automotive Applications
In the realms of aerospace and automotive engineering, thermocouples play a pivotal role in ensuring the safety, efficiency, and performance of vehicles and aircraft. These temperature-sensing devices are crucial for monitoring and controlling various critical systems. In aerospace applications, thermocouples are used to measure the high temperatures generated by jet engines, rocket nozzles, and heat shields during flight. This real-time data is essential for engine performance optimization, fuel efficiency, and preventing overheating which could lead to catastrophic failures. For instance, in jet engines, thermocouples monitor the turbine inlet temperature to ensure that the engine operates within safe limits, thereby extending its lifespan and enhancing overall aircraft reliability. In the automotive sector, thermocouples are integral to modern vehicle design. They are employed in exhaust gas recirculation (EGR) systems to monitor the temperature of exhaust gases, helping to reduce emissions by optimizing combustion processes. Additionally, thermocouples are used in catalytic converters to ensure that the catalyst operates at the optimal temperature range for efficient pollutant reduction. This not only helps in complying with stringent emission regulations but also improves fuel economy and reduces harmful emissions. Furthermore, thermocouples are utilized in advanced driver-assistance systems (ADAS) such as autonomous driving technologies where precise temperature monitoring of critical components like batteries and electronic control units is necessary for reliable operation. The durability and accuracy of thermocouples make them ideal for these demanding environments where extreme temperatures and harsh conditions are common. Their ability to withstand high temperatures and provide rapid response times allows for real-time feedback, enabling immediate adjustments to be made to maintain optimal performance. Moreover, the compact size and versatility of thermocouples enable their integration into various subsystems without compromising the overall design or functionality of the vehicle or aircraft. In summary, thermocouples are indispensable tools in aerospace and automotive applications due to their reliability, precision, and robustness. By accurately measuring temperatures across a wide range of conditions, they contribute significantly to enhancing safety standards, improving efficiency, and reducing environmental impact. As technology continues to evolve, the role of thermocouples will remain vital in these industries, driving innovation and ensuring that vehicles and aircraft operate at peak performance while adhering to stringent safety and environmental regulations.
Medical and Scientific Uses
Thermocouples play a pivotal role in various medical and scientific applications, leveraging their ability to accurately measure temperature across a wide range of conditions. In the medical field, thermocouples are used in procedures that require precise temperature control, such as in cryosurgery and hyperthermia treatments. Cryosurgery, for instance, involves freezing tissues to destroy abnormal cells, and thermocouples help monitor the temperature to ensure that the target area is cooled to the optimal level without causing unnecessary damage to surrounding healthy tissues. Conversely, hyperthermia treatments involve heating tissues to enhance the effectiveness of chemotherapy or radiation therapy; here, thermocouples ensure that the tissues are heated to the precise temperature required for therapeutic efficacy. In scientific research, thermocouples are indispensable tools for conducting experiments that involve temperature measurements. For example, in materials science, thermocouples are used to study the thermal properties of materials under different conditions. This includes measuring the melting points of substances, monitoring temperature changes during chemical reactions, and assessing the thermal conductivity of various materials. In environmental science, thermocouples help in monitoring soil and water temperatures, which is crucial for understanding ecological processes and predicting climate changes. Additionally, thermocouples are integral in the development and testing of medical devices. They are used to calibrate and validate the performance of medical equipment such as incubators, autoclaves, and dialysis machines, ensuring that these devices operate within safe and effective temperature ranges. In pharmaceutical research, thermocouples monitor the temperature during drug synthesis and storage, which is critical for maintaining the stability and potency of medications. In the realm of aerospace and space exploration, thermocouples are employed to measure extreme temperatures encountered during rocket launches and space missions. These measurements are vital for understanding the thermal stresses on spacecraft components and ensuring their durability under harsh conditions. Similarly, in industrial settings like power plants and chemical processing facilities, thermocouples monitor temperatures in high-temperature environments such as furnaces and reactors, helping to optimize process efficiency and safety. The versatility of thermocouples also extends to their use in food processing and safety. They are used to monitor cooking temperatures in commercial kitchens to prevent foodborne illnesses by ensuring that food is cooked to a safe internal temperature. In laboratories, thermocouples are used in various analytical techniques such as gas chromatography and mass spectrometry, where precise temperature control is essential for accurate results. Overall, the reliability and accuracy of thermocouples make them an essential component across diverse medical and scientific applications. Their ability to withstand extreme temperatures and provide real-time data makes them invaluable for both routine monitoring and complex research endeavors. As technology continues to evolve, the role of thermocouples is likely to expand further, enabling more precise measurements and enhancing the efficiency of various scientific and medical processes.
Advantages, Limitations, and Maintenance of Thermocouples
Thermocouples are versatile temperature measurement devices widely used across various industries due to their robust design, broad temperature range, and rapid response times. Understanding the advantages, limitations, and maintenance requirements of thermocouples is crucial for their effective deployment. This article delves into the benefits and advantages of thermocouples in different settings, highlighting their utility in harsh environments and their ability to provide accurate readings over a wide temperature spectrum. It also explores the potential limitations and challenges associated with thermocouples, such as accuracy drift and susceptibility to electromagnetic interference. Additionally, the article outlines best practices for maintenance and calibration, ensuring that these devices continue to operate reliably over their lifespan. By examining these key aspects, users can maximize the performance of thermocouples and make informed decisions about their application. Let's begin by exploring the benefits and advantages of thermocouples in various settings, where their unique characteristics make them an indispensable tool.
Benefits and Advantages in Various Settings
Thermocouples offer a multitude of benefits and advantages across various settings, making them a versatile and indispensable tool in numerous industries. In industrial processes, thermocouples provide accurate and reliable temperature measurements, which are crucial for maintaining optimal operating conditions. For instance, in chemical plants, thermocouples help monitor temperatures in reactors and pipelines, ensuring that reactions occur within safe and efficient parameters. Similarly, in power generation, thermocouples are used to measure temperatures in turbines and boilers, enhancing overall plant efficiency and safety. In the automotive sector, thermocouples are integral to engine management systems. They monitor exhaust gas temperatures, helping to optimize fuel efficiency and reduce emissions. This not only improves vehicle performance but also contributes to environmental sustainability by minimizing harmful pollutants. Additionally, thermocouples are used in aerospace applications where precise temperature control is vital for the safe operation of aircraft engines and other critical systems. In medical settings, thermocouples play a significant role in patient care. They are used in medical devices such as thermometers and temperature probes, providing quick and accurate readings that are essential for diagnosing and treating various health conditions. Their small size and durability make them ideal for use in surgical procedures and patient monitoring. Furthermore, thermocouples are widely employed in research and development. Scientists rely on them to measure temperatures in extreme environments, such as high-temperature furnaces or cryogenic chambers. This allows for the study of material properties under diverse conditions, driving innovation in fields like materials science and physics. The advantages of thermocouples extend beyond their technical capabilities; they are also cost-effective and easy to maintain. Unlike other temperature measurement devices, thermocouples do not require an external power source, making them self-sufficient and reducing operational costs. Their rugged construction ensures longevity, even in harsh environments, which minimizes the need for frequent replacements or repairs. In summary, the benefits and advantages of thermocouples are far-reaching and multifaceted. From industrial processes to medical applications, these devices provide accurate temperature measurements that are critical for efficiency, safety, and innovation. Their durability, cost-effectiveness, and ease of use make them an indispensable tool across various settings, underscoring their importance in modern technology and industry.
Potential Limitations and Challenges
While thermocouples offer numerous advantages, such as high temperature range, durability, and simplicity, they are not without their limitations and challenges. One of the primary limitations is the inherent inaccuracy and non-linearity of thermocouple readings. Unlike other temperature measurement devices, thermocouples do not provide a direct linear output; instead, their voltage output is non-linear and requires calibration to accurately determine the temperature. This complexity can lead to errors if not properly addressed. Additionally, thermocouples are susceptible to electromagnetic interference (EMI) and radio-frequency interference (RFI), which can distort the signal and affect accuracy. This issue is particularly significant in industrial environments where various electrical devices are present. Another challenge is the potential for degradation over time due to exposure to high temperatures, corrosive environments, or mechanical stress. The materials used in thermocouples can oxidize or degrade, leading to a reduction in their lifespan and accuracy. For instance, type K thermocouples, which are commonly used due to their wide temperature range, can suffer from oxidation at high temperatures, affecting their performance. Furthermore, the junction of the thermocouple itself can be a point of failure if not properly protected or if it becomes contaminated. Maintenance is also a critical aspect to consider when using thermocouples. Regular calibration checks are essential to ensure that the thermocouple is providing accurate readings. This involves comparing the thermocouple's output against a known temperature standard and adjusting as necessary. Moreover, the physical integrity of the thermocouple must be maintained; this includes ensuring that the insulation is intact and that there is no damage to the wires or junction. In some applications, the response time of thermocouples can be a limitation. While they generally respond quickly to changes in temperature, certain types may have slower response times compared to other temperature measurement devices like thermistors or RTDs (Resistance Temperature Detectors). This slower response can be problematic in processes that require rapid temperature adjustments or monitoring. Lastly, environmental factors such as humidity and exposure to certain chemicals can also impact thermocouple performance. For example, in highly humid environments, moisture can seep into the thermocouple assembly and cause electrical shorts or corrosion, leading to inaccurate readings or complete failure. In summary, while thermocouples are versatile and widely used temperature measurement tools, they come with several potential limitations and challenges that must be carefully considered and managed. By understanding these limitations and implementing appropriate maintenance and calibration practices, users can ensure that thermocouples continue to provide reliable and accurate temperature measurements over their lifespan.
Maintenance and Calibration Best Practices
**Maintenance and Calibration Best Practices** To ensure the optimal performance and longevity of thermocouples, adhering to rigorous maintenance and calibration best practices is crucial. Regular inspections are essential; visually examine the thermocouple for signs of wear, corrosion, or physical damage. Check for any insulation breaches or exposed wires, as these can compromise accuracy and safety. Cleaning the thermocouple tip and surrounding area is also vital to prevent contamination that could affect readings. Calibration is another critical aspect of thermocouple maintenance. It involves comparing the thermocouple's output against a known standard to verify its accuracy. This process should be performed periodically, especially after exposure to extreme conditions or when there are noticeable deviations in readings. Use high-quality calibration equipment and follow established protocols to ensure reliable results. For instance, using a calibration furnace or ice bath can provide precise temperature references. Proper installation techniques are also integral to maintaining thermocouple integrity. Ensure that the thermocouple is securely fastened and protected from mechanical stress, which can lead to wire fatigue or breakage. The use of appropriate connectors and extension wires that match the thermocouple type is important to avoid signal degradation. Documentation of maintenance activities is indispensable for tracking the history of each thermocouple. Keeping detailed records of inspections, calibrations, and any repairs helps in identifying trends and potential issues before they become critical. This documentation also aids in compliance with regulatory standards and quality control requirements. Additionally, training personnel on proper handling and maintenance procedures is essential. Incorrect handling can lead to damage or contamination, so educating users on best practices ensures that the thermocouples are treated with care. Regular training sessions can also update staff on new technologies or methodologies that may enhance maintenance efficiency. Incorporating these best practices into a routine maintenance schedule not only extends the lifespan of thermocouples but also ensures their reliability and accuracy over time. By combining regular inspections, thorough calibrations, proper installations, meticulous documentation, and comprehensive training, users can maximize the performance of their thermocouples while minimizing downtime and errors. This holistic approach to maintenance underscores the importance of proactive care in maintaining these critical temperature-measuring devices.