What Is Ppr

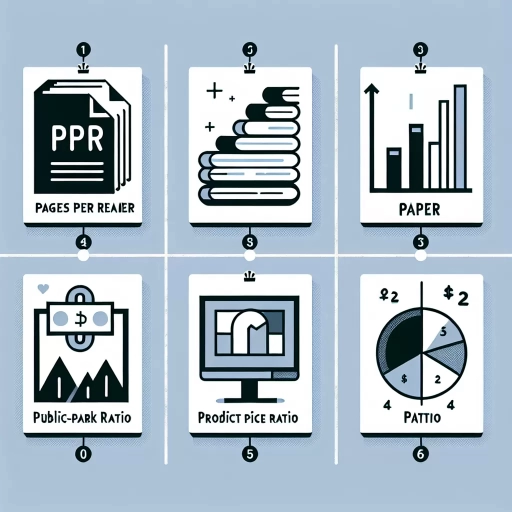
Polypropylene Random (PPR) is a versatile and widely used thermoplastic material that has revolutionized various industries, including plumbing, heating, and industrial piping. Known for its durability, resistance to chemicals, and ease of installation, PPR has become a preferred choice for many applications. This article delves into the world of PPR, providing a comprehensive overview of its technical specifications and properties, its numerous advantages and uses, as well as essential safety considerations. By understanding the technical aspects of PPR, such as its molecular structure and mechanical properties, we can appreciate its robust performance in diverse environments. Additionally, exploring the advantages and uses of PPR will highlight why it is a go-to material for modern infrastructure projects. Finally, addressing safety considerations ensures that users can harness the full potential of PPR while minimizing risks. To begin, let's introduce the fundamental aspects of PPR and explore what makes it such a valuable material in today's engineering landscape. **Introduction to PPR**
Introduction to PPR
In the realm of modern engineering and construction, Polypropylene Random Copolymer (PPR) has emerged as a versatile and highly sought-after material. This introduction to PPR aims to delve into the multifaceted aspects of this polymer, providing a comprehensive overview that spans its definition and acronym, historical context and development, and common applications. Understanding the acronym PPR is crucial as it stands for Polypropylene Random Copolymer, a specific type of polypropylene that offers enhanced properties. The historical context of PPR reveals its evolution from earlier polypropylene variants, highlighting key milestones in its development that have made it a preferred choice today. Furthermore, exploring the common applications of PPR will illustrate its widespread use in plumbing, heating, and industrial systems, showcasing its durability, resistance to chemicals, and ease of installation. By examining these facets, this article will provide a thorough introduction to PPR, equipping readers with a solid foundation in this essential material. Transitioning seamlessly into the detailed sections that follow, this introduction sets the stage for a deeper exploration of what PPR is, how it came to be, and where it is most effectively utilized.
Definition and Acronym
In the context of "Introduction to PPR," understanding the definitions and acronyms associated with this term is crucial for a comprehensive grasp of the subject. **PPR** stands for **Polypropylene Random Copolymer**, a type of thermoplastic material widely used in various industrial and consumer applications. This acronym encapsulates the chemical composition and structural characteristics of the material, which is a random copolymer of propylene and ethylene. Polypropylene Random Copolymer is distinguished by its unique properties, such as high impact resistance, flexibility, and resistance to chemicals and abrasion. These attributes make PPR an ideal choice for manufacturing pipes, fittings, and other components in plumbing, heating, and cooling systems. The term "random copolymer" indicates that the molecular structure of PPR involves a random arrangement of propylene and ethylene monomers, which enhances its mechanical strength and durability compared to other types of polypropylene. The definition of PPR extends beyond its chemical structure to include its practical applications. In construction and engineering, PPR pipes are favored due to their ease of installation, resistance to corrosion, and ability to withstand high temperatures. Additionally, PPR is used in medical devices, automotive parts, and consumer goods where its versatility and performance are advantageous. Understanding the acronym and definition of PPR is essential for professionals and consumers alike who need to specify materials for projects or evaluate product performance. It highlights the importance of precision in technical communication, ensuring that stakeholders are aware of the specific characteristics and benefits that PPR offers. By delving into the meaning behind this acronym, one can appreciate the technological advancements and innovations that have made PPR a cornerstone in modern material science. This foundational knowledge sets the stage for a deeper exploration into the applications, advantages, and future developments of PPR in various industries.
Historical Context and Development
The historical context and development of Polypropylene (PPR) piping systems are deeply intertwined with advancements in polymer technology and the evolving needs of modern infrastructure. The journey of PPR began in the mid-20th century, when scientists first synthesized polypropylene, a thermoplastic polymer known for its durability, resistance to chemicals, and versatility. Initially used in various industrial applications, polypropylene's potential for piping was recognized due to its superior properties compared to traditional materials like copper, PVC, and galvanized steel. In the 1970s and 1980s, the development of PPR piping gained momentum as manufacturers began to tailor polypropylene for specific plumbing needs. This involved creating formulations that could withstand high temperatures and pressures, making it suitable for both hot and cold water distribution systems. The introduction of fusion welding techniques further enhanced the reliability and integrity of PPR connections, significantly reducing the risk of leaks and failures. The 1990s saw a significant surge in the adoption of PPR piping globally, driven by its cost-effectiveness, ease of installation, and environmental benefits. Unlike traditional materials that required soldering or threading, PPR pipes could be quickly fused together using specialized tools, reducing labor costs and installation time. Additionally, PPR's resistance to corrosion and scaling made it an attractive option for regions with hard water or aggressive soil conditions. Over the past few decades, continuous innovation has led to the development of advanced PPR formulations with enhanced performance characteristics. Modern PPR pipes are designed to meet stringent international standards, ensuring they can handle a wide range of temperatures and pressures while maintaining their structural integrity. The integration of additives such as antioxidants and UV stabilizers has also improved the long-term durability of PPR systems, making them a preferred choice for residential, commercial, and industrial applications. Today, PPR piping systems are recognized for their sustainability and eco-friendliness. Unlike metal pipes that can leach chemicals into water or contribute to environmental pollution during manufacturing, PPR pipes are non-toxic and recyclable. This aligns with global trends towards green infrastructure and sustainable development. As technology continues to evolve, it is expected that PPR will remain a cornerstone in modern plumbing solutions, offering a balance of performance, cost-efficiency, and environmental responsibility. Understanding the historical context and development of PPR is crucial for appreciating its current role and future potential in shaping the landscape of modern infrastructure.
Common Applications
In the realm of modern plumbing and piping systems, Polypropylene Random Copolymer (PPR) has emerged as a versatile and highly sought-after material due to its myriad applications. PPR pipes and fittings are widely used across various industries, including residential, commercial, and industrial sectors, owing to their unique properties such as high resistance to corrosion, excellent durability, and ease of installation. One of the most common applications of PPR is in plumbing systems for hot and cold water distribution. Its ability to withstand high temperatures without compromising on structural integrity makes it an ideal choice for both domestic and commercial water supply lines. Additionally, PPR's resistance to scaling and corrosion ensures that the water quality remains unaffected, reducing the risk of contamination and extending the lifespan of the piping system. In the industrial sector, PPR is utilized for transporting chemicals and other corrosive substances due to its chemical inertness. This property allows it to maintain its integrity even when exposed to harsh environments, making it a reliable option for chemical processing plants and other industrial facilities. Furthermore, PPR's low thermal conductivity reduces heat loss during the transportation of fluids, thereby enhancing energy efficiency. The construction industry also benefits significantly from PPR's versatility. It is often used in radiant floor heating systems where its flexibility and resistance to freezing temperatures are particularly advantageous. Moreover, PPR's lightweight nature simplifies transportation and installation processes, contributing to cost savings and faster project completion times. Another significant application of PPR is in agricultural irrigation systems. Here, its resistance to UV rays and ability to withstand outdoor conditions make it an excellent choice for distributing water across vast agricultural lands. The ease with which PPR pipes can be connected using fusion welding techniques also ensures leak-free joints, minimizing water loss and optimizing irrigation efficiency. In summary, the diverse applications of PPR underscore its importance in modern infrastructure development. From residential plumbing to industrial chemical transport and from construction projects to agricultural irrigation systems, PPR's unique combination of durability, corrosion resistance, and ease of installation makes it an indispensable material across a wide range of sectors. As technology continues to evolve, the role of PPR in meeting the demands of various industries is likely to expand further, solidifying its position as a cornerstone material in contemporary engineering practices.
Technical Specifications and Properties
In the realm of engineering and construction, understanding technical specifications and properties is paramount for ensuring the integrity, safety, and performance of materials. This article delves into the critical aspects that define a material's suitability for various applications, focusing on three key areas: Material Composition, Physical and Chemical Properties, and Manufacturing Process. The Material Composition section will explore the elemental makeup of materials, highlighting how different constituents influence overall performance. The Physical and Chemical Properties segment will examine the intrinsic characteristics that determine a material's behavior under different conditions, such as strength, durability, and resistance to environmental factors. Finally, the Manufacturing Process section will discuss how production methods impact the final product's quality and functionality. By grasping these fundamental concepts, engineers and practitioners can make informed decisions that align with project requirements. This comprehensive overview sets the stage for a deeper exploration of specific materials, leading us to an Introduction to PPR (Polypropylene Random Copolymer), a versatile and widely used material in modern engineering.
Material Composition
Material composition is a critical aspect of understanding the properties and performance of Polypropylene Random Copolymer (PPR), a widely used thermoplastic material in various applications, particularly in plumbing and piping systems. PPR is a type of polypropylene that combines the benefits of both homopolymer and block copolymer polypropylenes. The material's composition primarily consists of propylene monomers, with a random incorporation of ethylene monomers. This random copolymerization process introduces short ethylene sequences into the polypropylene chain, which significantly enhances the material's impact resistance, flexibility, and weldability compared to homopolymer polypropylene. The precise composition of PPR typically includes around 80-90% propylene and 10-20% ethylene by weight. This balanced mix allows PPR to retain the excellent chemical resistance, low density, and high melting point characteristic of polypropylene while gaining improved toughness and resistance to stress cracking. The presence of ethylene also facilitates better fusion welding properties, making PPR pipes and fittings easier to join securely without compromising their integrity. In terms of technical specifications, the material composition directly influences key properties such as tensile strength, elongation at break, and thermal stability. For instance, PPR pipes are known for their ability to withstand pressures up to 25 bar at 20°C and temperatures ranging from -20°C to 95°C, making them suitable for both hot and cold water distribution systems. Additionally, the material's low thermal conductivity reduces heat loss in heating systems and minimizes the risk of freezing in cold water lines. The chemical structure of PPR also contributes to its resistance against various corrosive substances, including acids, bases, and salts, which is crucial for applications in industrial and municipal water supply networks. Furthermore, the non-toxic nature of PPR ensures compliance with health and safety standards for potable water distribution. In summary, the material composition of PPR is meticulously engineered to balance mechanical strength, thermal stability, and chemical resistance. This careful blend of propylene and ethylene monomers enables PPR to meet stringent technical specifications and properties required for diverse applications, solidifying its position as a preferred material in modern plumbing and piping solutions.
Physical and Chemical Properties
When discussing the technical specifications and properties of Polypropylene Random (PPR) pipes, it is crucial to delve into their physical and chemical properties, which are pivotal in determining their performance and suitability for various applications. **Physical Properties:** PPR pipes exhibit a range of beneficial physical attributes. They are lightweight, making them easier to transport and install compared to traditional materials like metal or PVC. This lightness also reduces labor costs and enhances overall efficiency in construction projects. Additionally, PPR pipes are highly flexible, allowing for easier bending and maneuverability around corners and obstacles, which simplifies the installation process. Their smooth inner surface minimizes friction, ensuring higher flow rates and reduced pressure drops, thereby optimizing water distribution systems. Furthermore, PPR pipes have excellent thermal insulation properties, reducing heat loss and maintaining consistent water temperatures over long distances. **Chemical Properties:** The chemical properties of PPR pipes are equally impressive. They are resistant to a wide range of chemicals, including acids, bases, and salts, making them ideal for use in industrial applications where corrosive substances are present. This resistance also extends to chlorine and other disinfectants commonly used in water treatment processes, ensuring the longevity of the pipes without degradation. PPR pipes are non-toxic and comply with international standards for potable water supply systems, guaranteeing safe drinking water distribution. Moreover, they are resistant to scaling and fouling, which reduces maintenance needs and extends their service life. The material's inherent resistance to UV light prevents degradation from sunlight exposure, allowing for outdoor use without additional protective measures. In summary, the physical and chemical properties of PPR pipes make them a superior choice for various applications, from residential plumbing to industrial piping systems. Their lightweight nature, flexibility, and smooth inner surface contribute to ease of installation and optimal performance. The chemical resistance and non-toxicity ensure durability and safety, while their thermal insulation and UV resistance add to their versatility. These attributes collectively underscore why PPR pipes are increasingly preferred over traditional materials in modern construction and infrastructure projects.
Manufacturing Process
The manufacturing process of Polypropylene Random (PPR) pipes is a meticulous and highly controlled sequence of steps, ensuring the production of high-quality, durable, and reliable piping systems. It begins with the selection of raw materials, primarily polypropylene resin, which is carefully sourced to meet stringent quality standards. The resin is then compounded with additives such as stabilizers, pigments, and impact modifiers to enhance the pipe's performance characteristics. Next, the compounded material undergoes extrusion, where it is melted and formed into a long, continuous tube. This process involves feeding the material through an extruder, which heats and mixes it uniformly before forcing it through a die to achieve the desired pipe diameter and wall thickness. The extruded pipe is then cooled and sized using a calibration sleeve to maintain precise dimensions. Following extrusion, the pipe undergoes various quality control checks to ensure it meets technical specifications. These checks include visual inspections for defects, dimensional verification, and testing for mechanical properties such as tensile strength and impact resistance. Additionally, the pipes may undergo further processing steps like printing or marking with relevant information such as pressure ratings and manufacturer details. To enhance durability and resistance to environmental stress cracking, PPR pipes often undergo a process called "fusing" or "welding," where fittings such as elbows, tees, and couplers are joined to the pipe using heat fusion techniques. This method creates a strong, leak-proof bond that is integral to the overall integrity of the piping system. Finally, the finished pipes are packaged and prepared for distribution. They are typically coiled or cut into specific lengths depending on customer requirements and are accompanied by detailed technical specifications outlining their properties and applications. These specifications include information on pressure ratings, temperature resistance, chemical compatibility, and compliance with relevant industry standards. Throughout this manufacturing process, adherence to strict quality control measures ensures that PPR pipes consistently meet or exceed industry benchmarks for performance and reliability. This attention to detail is crucial in applications ranging from residential plumbing to industrial processes, where the integrity of the piping system can have significant implications for safety and operational efficiency. By understanding the meticulous steps involved in manufacturing PPR pipes, users can better appreciate their robustness and versatility in various environments.
Advantages, Uses, and Safety Considerations
In the realm of modern construction and plumbing, Polypropylene Random Copolymer (PPR) has emerged as a versatile and highly sought-after material. Known for its durability, resistance to corrosion, and ease of installation, PPR pipes have become a staple in both industrial and residential settings. This article delves into the multifaceted advantages of PPR, exploring its benefits over other materials, its diverse applications in various industries, and the crucial safety considerations that must be adhered to during its handling and use. By understanding the unique benefits that set PPR apart from other materials, readers will gain insight into why it is preferred for numerous applications. Additionally, we will examine the widespread industrial and residential uses of PPR, highlighting its adaptability and performance in different environments. Finally, we will discuss the essential safety precautions and handling guidelines that are vital for ensuring safe and effective use of PPR. Transitioning seamlessly from these key points, this introduction sets the stage for a comprehensive exploration of PPR, leading you to an in-depth **Introduction to PPR**.
Benefits Over Other Materials
When comparing PPR (Polypropylene Random) pipes to other materials, several key benefits emerge that make PPR a preferred choice in various applications. **Durability** is one of the standout advantages; PPR pipes are highly resistant to corrosion and chemical damage, which extends their lifespan significantly compared to traditional materials like copper or galvanized steel. This resistance also means they require less maintenance over time, reducing the need for frequent repairs and replacements. Another significant benefit of PPR pipes is their **flexibility**. Unlike rigid materials such as PVC or ABS, PPR can absorb impacts without cracking, making it ideal for installations where vibrations or movements are anticipated. This flexibility also simplifies the installation process, as fewer fittings are required due to the ability of PPR pipes to bend around corners and obstacles. **Thermal Insulation** is another area where PPR excels. These pipes have a lower thermal conductivity compared to metal pipes, which helps in reducing heat loss during hot water distribution and minimizing the risk of freezing in cold water lines. This property not only enhances energy efficiency but also contributes to a more consistent water temperature. In terms of **safety**, PPR pipes are non-toxic and do not leach harmful chemicals into the water supply, ensuring safe drinking water for consumers. Additionally, they are resistant to scaling and do not support the growth of bacteria or algae, further enhancing water quality. From an **environmental perspective**, PPR pipes are more eco-friendly than many other materials. They are made from recyclable materials and can be reused at the end of their service life, reducing waste and the environmental impact associated with production and disposal. Lastly, **cost-effectiveness** plays a crucial role in the selection of piping materials. While the initial cost of PPR pipes might be higher than some alternatives, their long-term benefits—such as reduced maintenance needs, extended lifespan, and lower risk of leaks—make them a more economical choice in the long run. Overall, the combination of durability, flexibility, thermal insulation properties, safety features, environmental benefits, and cost-effectiveness makes PPR pipes a superior option over many other materials for various applications ranging from plumbing systems to industrial processes.
Industrial and Residential Uses
Industrial and residential uses of PPR (Polypropylene Random Copolymer) pipes are diverse and highly beneficial, leveraging the material's unique properties to enhance efficiency, safety, and durability. In industrial settings, PPR pipes are widely adopted due to their resistance to chemicals, high temperature tolerance, and excellent mechanical strength. These pipes are ideal for transporting hot and cold water, as well as various chemicals and gases, making them a staple in manufacturing facilities, chemical plants, and HVAC systems. Their resistance to scaling and corrosion ensures a longer lifespan compared to traditional metal pipes, reducing maintenance costs and downtime. Additionally, PPR pipes are lightweight and easy to install, which simplifies the process of setting up complex piping systems. In residential applications, PPR pipes offer numerous advantages that make them a preferred choice for plumbing systems. They are non-toxic and do not leach chemicals into the water supply, ensuring safe drinking water for households. The flexibility of PPR pipes allows for easier installation around corners and through tight spaces, reducing the need for multiple fittings and joints. This flexibility also helps in absorbing vibrations and shocks, minimizing the risk of pipe damage. Furthermore, PPR pipes are resistant to freezing temperatures and can withstand the pressure fluctuations common in residential plumbing systems. Their smooth inner surface reduces friction, which helps in maintaining consistent water pressure throughout the house. The aesthetic appeal of PPR pipes is another advantage; they come in various colors and can be used for both visible and hidden installations, enhancing the overall appearance of a home. From a safety perspective, PPR pipes are designed with multiple layers that provide additional protection against external damage. The outer layer is typically made of a material that offers UV resistance, while the middle layer provides insulation against temperature extremes. This layered structure ensures that the pipes remain intact even under harsh conditions. Moreover, PPR pipes are certified to meet various international standards for safety and quality, such as ISO and ASTM certifications, which guarantee their performance and reliability. Overall, the versatility, durability, and safety features of PPR pipes make them an indispensable component in both industrial and residential environments, offering a reliable solution for a wide range of piping needs.
Safety Precautions and Handling Guidelines
When handling PPR (Polypropylene Random) pipes and fittings, it is crucial to adhere to strict safety precautions and handling guidelines to ensure both personal safety and the integrity of the materials. First, always wear appropriate personal protective equipment (PPE) such as gloves, safety glasses, and a dust mask to protect against potential hazards like sharp edges, chemical exposure, and airborne particles. Ensure the workspace is well-ventilated to prevent inhalation of any fumes that may be emitted during cutting or welding processes. Proper handling techniques are essential to avoid damage to the PPR components. Lift pipes and fittings carefully to prevent bending or kinking, which can compromise their structural integrity. Use suitable lifting equipment when dealing with heavy loads to avoid straining muscles. When transporting PPR materials, secure them properly to prevent shifting during transit, which could lead to damage or injury. During installation, follow the manufacturer's instructions meticulously. Ensure all tools and equipment are in good working condition and suitable for the task at hand. For instance, use a high-quality pipe cutter or saw to avoid rough edges that could lead to leaks or other issues. When welding PPR pipes, maintain a clean and dry environment to ensure strong, reliable joints. Always follow the recommended welding parameters to avoid overheating or underheating the material. Storage of PPR materials also requires careful consideration. Store pipes and fittings in a dry, well-ventilated area away from direct sunlight and extreme temperatures. Avoid stacking materials too high, as this can cause bending or crushing. Label and organize the storage area clearly to facilitate easy access and minimize the risk of accidents. Regular inspection of PPR systems is vital for maintaining safety and performance. Check for signs of wear, damage, or leaks regularly, especially in high-pressure applications. Address any issues promptly to prevent more severe problems from developing. By adhering to these safety precautions and handling guidelines, users can maximize the benefits of PPR pipes and fittings while minimizing risks. This includes ensuring the longevity of the system, preventing accidents, and maintaining compliance with industry standards and regulations. Proper handling and safety measures are integral components of any successful PPR installation project, contributing significantly to its overall success and reliability.