What Is A Stepper Motor

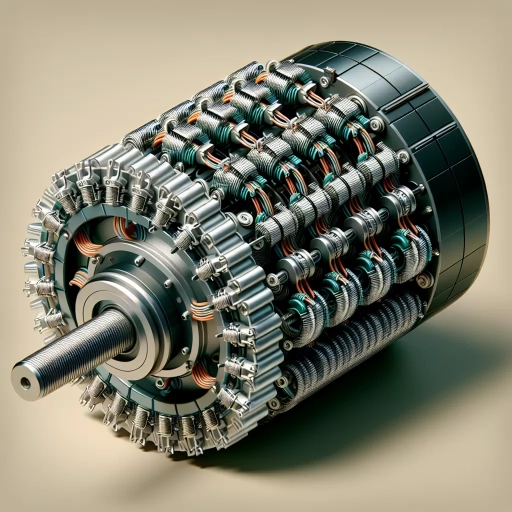
A stepper motor is a type of electric motor that converts digital pulses into discrete mechanical movements, making it a crucial component in various precision applications. Unlike traditional motors, stepper motors move in precise steps, allowing for accurate positioning and control. This article delves into the world of stepper motors, starting with an **Introduction to Stepper Motors**, where we explore their history, significance, and common uses. We then examine **How Stepper Motors Work**, detailing the internal mechanisms and principles that enable their unique functionality. Finally, we discuss **Types and Characteristics of Stepper Motors**, highlighting the different types available and their specific attributes. By understanding these aspects, readers will gain a comprehensive insight into the operation and versatility of stepper motors. Let's begin by diving into the **Introduction to Stepper Motors**.
Introduction to Stepper Motors
Stepper motors are a crucial component in modern technology, offering precise control and reliability in various applications. To understand their significance, it is essential to delve into their definition and basic principles, historical development and evolution, and common applications across different industries. Starting with the fundamentals, **Definition and Basic Principles** will explore how stepper motors operate by converting electrical pulses into discrete mechanical movements. This section will explain the key components, such as the stator and rotor, and how they interact to produce rotational motion. The **Historical Development and Evolution** of stepper motors will highlight their origins and advancements over time. From their early use in the 1920s to the sophisticated designs of today, this section will trace the technological milestones that have made stepper motors more efficient and versatile. Finally, **Common Applications and Industries** will illustrate the widespread use of stepper motors in fields such as robotics, medical devices, 3D printing, and automotive systems. Understanding these applications will provide insight into why stepper motors are a preferred choice for precision and reliability. By grasping these aspects, readers will gain a comprehensive understanding of stepper motors, beginning with their core principles. Let's start by examining the **Definition and Basic Principles** of stepper motors to lay the groundwork for this in-depth exploration.
Definition and Basic Principles
A stepper motor is a type of electric motor that converts digital pulses into discrete mechanical movements. The definition of a stepper motor hinges on its ability to rotate in precise, incremental steps, allowing for accurate positioning and control. At its core, a stepper motor operates on the principle of electromagnetic attraction and repulsion between its stator and rotor components. Here are the basic principles: 1. **Construction**: A stepper motor consists of a stator (the stationary part) and a rotor (the moving part). The stator has multiple windings, while the rotor can be either a permanent magnet or an electromagnet. 2. **Magnetic Fields**: When an electrical current flows through the stator windings, magnetic fields are generated. These fields interact with the rotor's magnetic field, causing it to rotate. 3. **Step-by-Step Movement**: The motor moves in discrete steps due to the sequential energization of the stator windings. Each step corresponds to a specific angular displacement, typically measured in degrees. 4. **Control Mechanism**: Stepper motors are controlled by a driver that receives digital signals from a controller or microcontroller. These signals determine the sequence and timing of the current flow through the stator windings. 5. **Types of Stepper Motors**: There are several types, including unipolar, bipolar, and hybrid stepper motors. Unipolar motors use a single power supply and are simpler but less efficient, while bipolar motors use two power supplies and offer higher torque. Hybrid motors combine elements of both for improved performance. 6. **Advantages**: Stepper motors offer high precision, reliability, and low maintenance. They are widely used in applications requiring precise positioning, such as 3D printers, CNC machines, and medical devices. 7. **Applications**: Due to their precise control over movement, stepper motors are integral in various industries including robotics, automotive systems, and consumer electronics like hard disk drives and DVD players. Understanding these basic principles is crucial for effectively utilizing stepper motors in various applications, as it allows engineers and technicians to design and implement systems that leverage the unique advantages of these motors. By grasping how stepper motors function at a fundamental level, one can better appreciate their role in modern technology and their potential for future innovations.
Historical Development and Evolution
The historical development and evolution of stepper motors are deeply intertwined with advancements in technology and the need for precise control in various applications. The concept of stepper motors dates back to the early 20th century, but it wasn't until the 1950s that they began to take shape as a viable technology. One of the earliest forms of stepper motors was the variable reluctance (VR) stepper motor, which was developed in the 1950s. These motors relied on the principle of magnetic reluctance to rotate the rotor in discrete steps. In the 1960s, the introduction of permanent magnet (PM) stepper motors marked a significant milestone. PM steppers used permanent magnets instead of electromagnets, enhancing efficiency and reliability. This period also saw the development of hybrid stepper motors, which combined elements of both VR and PM designs, offering improved performance characteristics such as higher torque and better positional accuracy. The advent of microprocessors and digital control systems in the 1970s revolutionized the field by enabling sophisticated control algorithms and precise step-by-step movement. This era witnessed a surge in the use of stepper motors in industrial automation, robotics, and medical devices where precise positioning was crucial. The 1980s brought about significant advancements in materials science and manufacturing techniques, leading to more compact and efficient stepper motor designs. The introduction of bipolar and unipolar configurations expanded the versatility of stepper motors, allowing them to be used in a wider range of applications. In recent decades, advancements in electronics and software have continued to drive innovation. Modern stepper motors are often integrated with advanced control systems that include microcontrollers, drivers, and feedback mechanisms like encoders. These enhancements have improved speed, accuracy, and overall performance, making stepper motors indispensable in modern technologies such as 3D printing, CNC machines, and precision medical equipment. Throughout their evolution, stepper motors have been shaped by technological innovations and the demands of various industries. From their humble beginnings as simple variable reluctance motors to their current sophisticated forms, stepper motors have become a cornerstone of precision engineering and automation. Their ability to provide precise control over rotational movement has made them an essential component in many modern applications, underscoring their importance in the broader landscape of technological progress.
Common Applications and Industries
Stepper motors are versatile and widely used in various applications across multiple industries due to their precision, reliability, and ease of control. In the **medical field**, stepper motors are integral in medical imaging devices such as MRI and CT scanners, where precise movement is crucial for accurate imaging. They are also used in surgical robots and automated laboratory equipment, ensuring precise and repeatable movements. In **industrial automation**, stepper motors drive conveyor belts, pick-and-place machines, and CNC machines, enabling precise positioning and control. Their ability to maintain position without power makes them ideal for applications requiring high accuracy and reliability. **3D printing** also heavily relies on stepper motors to move the print head with precision, allowing for detailed and intricate designs. The **aerospace industry** utilizes stepper motors in navigation systems, satellite positioning, and other critical control systems where accuracy and reliability are paramount. In **consumer electronics**, stepper motors are found in printers, scanners, and DVD drives, providing smooth and precise movement. In **automotive systems**, stepper motors control fuel injection systems, anti-lock braking systems (ABS), and other critical components that require precise control. The **robotics sector** also benefits from stepper motors, enabling robots to perform tasks with high precision and repeatability. Additionally, **scientific instruments** such as telescopes and microscopes use stepper motors for precise positioning and movement. Their use extends to **home appliances** like washing machines and air conditioners, where they control various functions with accuracy. Overall, the broad applicability of stepper motors stems from their ability to provide precise control over movement, making them a cornerstone in many modern technologies across diverse industries.
How Stepper Motors Work
Stepper motors are a crucial component in modern technology, offering precise control and reliability in a wide range of applications, from 3D printers to medical devices. To understand how these motors work, it is essential to delve into three key aspects: their electromagnetic operation, the step-by-step movement mechanism, and the control systems and drivers that govern their behavior. At the heart of a stepper motor lies its electromagnetic operation, which involves the interaction between magnetic fields and electrical currents to produce rotational motion. This fundamental principle is what allows stepper motors to achieve such high precision and control. By examining the electromagnetic operation, we can gain insight into how these motors generate torque and move in discrete steps. This understanding sets the stage for exploring the step-by-step movement mechanism and the sophisticated control systems and drivers that ensure these motors operate efficiently and accurately. Let's begin by diving into the electromagnetic operation, the foundation upon which the entire functionality of stepper motors is built.
Electromagnetic Operation
Electromagnetic operation is the fundamental principle behind the functioning of stepper motors. In essence, a stepper motor converts electrical energy into mechanical energy through a series of precise, controlled movements. Here’s how it works: A stepper motor consists of two main components: the stator and the rotor. The stator is the stationary part, typically made up of multiple coils of wire (phases) that are energized in sequence to create magnetic fields. The rotor, on the other hand, is the moving part and can be either a permanent magnet or an electromagnet. When an electrical current flows through the coils in the stator, it generates a magnetic field that interacts with the rotor's magnetic field. The sequence in which these coils are energized determines the direction and speed of the rotor's rotation. By carefully controlling the timing and order of coil activation, the motor can achieve precise angular movements, known as steps. Each step corresponds to a specific angular displacement, allowing for highly accurate positioning and control. The process begins with the controller sending a pulse signal to the driver, which then energizes the appropriate coils in the stator. This creates a magnetic field that attracts or repels the rotor, causing it to rotate by one step. As each coil is energized in sequence, the rotor continues to move in discrete steps, resulting in smooth and continuous motion when viewed at higher speeds. There are several types of stepper motors, including bipolar and unipolar configurations, each with its own method for energizing the coils. Bipolar motors require more complex drivers but offer higher torque and efficiency, while unipolar motors are simpler to drive but may have lower performance. In addition to their precision and control, stepper motors are also known for their ability to hold position without continuous power input due to their inherent holding torque. This makes them ideal for applications requiring precise positioning and holding capabilities, such as in 3D printers, CNC machines, and medical devices. Overall, the electromagnetic operation of stepper motors enables them to provide reliable, accurate, and repeatable motion control, making them a crucial component in many modern technological systems.
Step-by-Step Movement Mechanism
In the context of stepper motors, the step-by-step movement mechanism is the core principle that allows these motors to achieve precise and controlled motion. Here’s a detailed breakdown of how this mechanism operates: 1. **Magnetic Field Interaction**: Stepper motors rely on the interaction between magnetic fields generated by the motor's stator (stationary part) and rotor (rotating part). The stator consists of multiple windings, each of which can be energized to create a magnetic field. 2. **Step Angle**: The motor is designed to rotate in discrete steps, with each step corresponding to a specific angle. This angle is determined by the number of poles and phases in the motor. For example, a common stepper motor might have a step angle of 1.8 degrees, meaning it rotates 1.8 degrees per step. 3. **Phase Sequencing**: To achieve movement, the windings in the stator are energized in a specific sequence. This sequencing is controlled by a driver circuit that applies current to the windings in a predetermined order. Each phase energizes a different set of windings, creating a magnetic field that attracts the rotor to align with it. 4. **Rotor Alignment**: As each phase is energized, the rotor aligns itself with the magnetic field generated by that phase. This alignment causes the rotor to rotate by one step angle. By sequencing through multiple phases, the rotor can be made to rotate continuously in small, precise steps. 5. **Direction Control**: The direction of rotation is controlled by reversing the sequence of phase energization. If the sequence is reversed, the rotor will rotate in the opposite direction. 6. **Microstepping**: For even finer control, some stepper motors and drivers use microstepping. In microstepping, the current to each winding is varied to create intermediate positions between full steps, effectively increasing the resolution of the motor's movement. 7. **Holding Torque**: When a stepper motor is not moving but is still energized, it maintains a holding torque that keeps the rotor in its current position. This ensures that the motor remains stable and does not drift from its set position. 8. **Open-Loop Operation**: Unlike servo motors, stepper motors typically operate in an open-loop system, meaning they do not require feedback to maintain position. However, this also means they can lose synchronization if overloaded or if the load exceeds the motor's capabilities. Understanding these steps provides a clear insight into how stepper motors achieve their characteristic precise and controlled movement, making them invaluable in applications such as 3D printing, CNC machining, and robotics.
Control Systems and Drivers
Control systems and drivers are crucial components in the operation of stepper motors, ensuring precise and efficient movement. A control system for a stepper motor typically includes a microcontroller or dedicated IC that generates the necessary step sequence. This sequence is based on the motor's step angle and the desired speed and direction of rotation. The control system interprets commands from higher-level systems, such as computers or PLCs, and translates them into step pulses that drive the motor. The driver, often an integrated circuit (IC) or a dedicated module, acts as an intermediary between the control system and the stepper motor. Its primary function is to amplify the low-current signals from the control system to high-current signals required by the motor. Drivers also manage current limiting, which prevents overheating and damage to the motor. Some advanced drivers include features like microstepping, which allows for finer resolution by dividing each full step into smaller increments, thereby increasing precision and reducing vibration. In addition to amplification and current management, drivers often include feedback mechanisms such as current sensing and temperature monitoring. These features help maintain optimal performance and prevent overheating or overcurrent conditions that could damage the motor or driver. Modern drivers may also support various control modes such as full-step, half-step, and microstep modes, allowing for flexibility in application design. The integration of control systems and drivers with stepper motors enables applications requiring high precision and reliability, such as 3D printers, CNC machines, and medical devices. For instance, in 3D printing, precise control over stepper motors ensures accurate layer deposition and smooth movement of the print head. Similarly, in CNC machining, precise control allows for intricate cuts and shapes with minimal error. In summary, control systems and drivers are essential for the proper functioning of stepper motors. They provide the necessary signals, amplification, and protection to ensure that the motor operates efficiently and accurately. By understanding how these components work together, engineers can design systems that leverage the unique advantages of stepper motors in a wide range of applications.
Types and Characteristics of Stepper Motors
Stepper motors are a crucial component in modern machinery, offering precise control over rotational movement. Understanding the various types and characteristics of these motors is essential for selecting the right one for specific applications. This article delves into three key aspects: the comparison between Permanent Magnet and Variable Reluctance motors, the advantages and disadvantages of Hybrid Stepper Motors, and the benefits of Microstepping and High-Resolution Motors. Each type has unique features that make them suitable for different tasks. For instance, Permanent Magnet motors are known for their simplicity and reliability, while Variable Reluctance motors offer higher torque at lower speeds. Hybrid Stepper Motors combine the best of both worlds but come with their own set of trade-offs. Additionally, Microstepping and High-Resolution Motors provide finer control over movement, enhancing precision in applications requiring detailed positioning. By exploring these differences, engineers and technicians can make informed decisions about which stepper motor to use in their designs. First, let's examine the fundamental differences between Permanent Magnet and Variable Reluctance motors.
Permanent Magnet vs. Variable Reluctance Motors
When comparing Permanent Magnet (PM) and Variable Reluctance (VR) stepper motors, several key differences emerge that are crucial for understanding their applications and performance characteristics. **Permanent Magnet Stepper Motors** utilize permanent magnets as the rotor, which interacts with the electromagnetic fields generated by the stator coils. This design provides a high torque-to-current ratio, making PM motors efficient and capable of delivering significant torque at low speeds. However, they can suffer from detent torque, which is the residual magnetic field that causes the rotor to align with the stator's magnetic poles even when no current is applied. This can lead to slight positional errors and vibrations. **Variable Reluctance Stepper Motors**, on the other hand, do not use permanent magnets; instead, they rely on the principle of magnetic reluctance to operate. The rotor is made of ferromagnetic material and aligns itself with the magnetic fields produced by the stator coils due to the tendency of magnetic flux to follow paths of least reluctance. VR motors are known for their high step accuracy and low detent torque, making them ideal for applications requiring precise positioning and smooth operation. However, they generally produce lower torque compared to PM motors and may require higher current levels to achieve similar performance. In terms of **applications**, PM stepper motors are often used in systems where high torque at low speeds is necessary, such as in robotics, CNC machines, and medical devices. Their efficiency and robustness make them suitable for a wide range of industrial and commercial uses. VR stepper motors, with their high precision and low detent torque, are preferred in applications requiring precise positioning and smooth operation, such as in 3D printers, laser engravers, and other precision machinery. **Control and Drive Requirements** also differ between these two types. PM motors typically require simpler drive circuits due to their inherent magnetic field, which helps in maintaining rotor position. VR motors, lacking a permanent magnetic field, often require more sophisticated drive systems to ensure accurate step-by-step movement. In summary, while both PM and VR stepper motors have their unique advantages and disadvantages, understanding these differences is essential for selecting the appropriate motor type based on specific application requirements. PM motors excel in high-torque applications with simpler drive needs, whereas VR motors offer superior precision and smooth operation but may demand more complex drive systems. This distinction highlights the importance of considering motor characteristics when designing or selecting stepper motor systems.
Hybrid Stepper Motors: Advantages and Disadvantages
Hybrid stepper motors, a blend of the features of both permanent magnet and variable reluctance stepper motors, offer a unique set of advantages and disadvantages. **Advantages** include higher torque output compared to other types of stepper motors, making them suitable for applications requiring significant rotational force. They also exhibit improved step resolution, typically ranging from 200 to 400 steps per revolution, which enhances precision and accuracy in positioning. Additionally, hybrid stepper motors are known for their robustness and reliability, making them a preferred choice in industrial environments where durability is crucial. Their ability to operate at higher speeds without losing step accuracy further expands their applicability in high-performance applications such as CNC machines and robotics. However, **disadvantages** must also be considered. One significant drawback is the higher cost associated with hybrid stepper motors due to their complex design and manufacturing process. This can be a barrier for budget-conscious projects or applications where cost is a primary factor. Furthermore, these motors often require more sophisticated control systems to fully utilize their capabilities, which can add complexity and cost to the overall system design. The higher power consumption of hybrid stepper motors compared to other types can also be a concern, particularly in energy-sensitive applications. Lastly, the increased complexity of these motors can make them more challenging to maintain and repair compared to simpler motor designs. Despite these trade-offs, hybrid stepper motors remain a popular choice for many applications due to their balanced performance characteristics and versatility. Understanding both the advantages and disadvantages is essential for selecting the right type of stepper motor for specific needs, ensuring optimal performance and efficiency in various industrial and technological contexts.
Microstepping and High-Resolution Motors
Microstepping and high-resolution motors are advanced technologies that enhance the performance and precision of stepper motors. **Microstepping** involves dividing the full step of a stepper motor into smaller, more precise steps. Instead of moving in full steps, the motor moves in fractions of a step, typically 1/4, 1/8, or even 1/16 of a step. This technique reduces vibration and noise, improves positional accuracy, and allows for smoother motion. By increasing the number of steps per revolution, microstepping enables finer control over motor movement, making it ideal for applications requiring high precision and low noise levels, such as in 3D printing, CNC machines, and medical devices. **High-resolution motors**, on the other hand, are designed to inherently provide a higher number of steps per revolution compared to standard stepper motors. These motors typically have more poles or phases, which allow for more precise control over the rotor's position. High-resolution motors can achieve higher step counts without the need for microstepping, offering superior accuracy and stability. They are often used in applications where precise positioning is critical, such as in robotics, precision machinery, and optical instruments. The combination of microstepping and high-resolution motors can significantly improve the overall performance of stepper motor systems, offering enhanced precision, reduced noise, and smoother operation. This makes them highly suitable for demanding applications where accuracy and reliability are paramount. By understanding these technologies, users can select the most appropriate stepper motor configuration to meet their specific needs for precision and performance.