What Is Sintered Stone

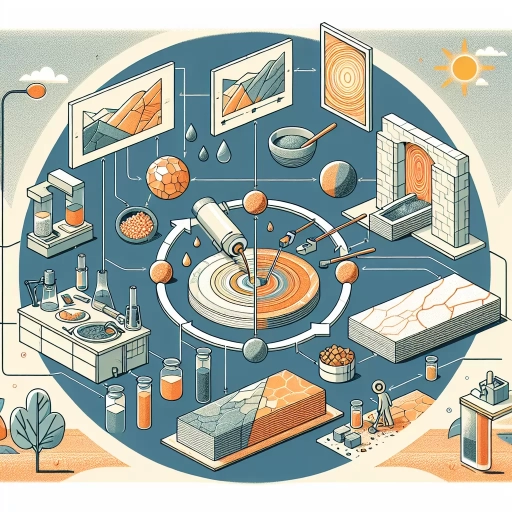
Introduction to Sintered Stone
Sintered stone, a material that has revolutionized the world of architecture and design, offers a unique blend of durability, aesthetic appeal, and versatility. This high-quality material has become a staple in modern construction and interior design due to its exceptional properties. To fully appreciate the significance of sintered stone, it is essential to delve into its definition and origin, understand its historical development, and explore current market trends. **Definition and Origin** will provide a foundational understanding of what sintered stone is and how it is produced. This section will explain the technological process behind its creation, highlighting the combination of natural minerals and advanced manufacturing techniques that result in a product superior to traditional stones. **Historical Development** will trace the evolution of sintered stone from its inception to its current status as a preferred material in various industries. This historical context will reveal how innovations in technology have shaped the production process and expanded its applications. **Current Market Trends** will discuss the contemporary landscape of sintered stone, including its widespread adoption in residential and commercial projects, emerging applications, and the factors driving its popularity. By examining these trends, readers will gain insight into why sintered stone continues to be a material of choice for architects, designers, and homeowners alike. Transitioning to **Definition and Origin**, we will begin by exploring the fundamental characteristics that define sintered stone and uncover its roots in modern manufacturing.
Definition and Origin
**Definition and Origin** Sintered stone, a cutting-edge material in the realm of architecture and design, is defined as a type of engineered stone produced through a sophisticated process known as sintering. This method involves compacting and fusing together particles of natural stone, such as quartz, granite, or marble, under high pressure and temperature without the use of resins or binders. The result is a dense, non-porous, and highly durable material that combines the aesthetic appeal of natural stone with enhanced performance characteristics. The origin of sintered stone can be traced back to the early 20th century when scientists began exploring ways to create synthetic materials that could mimic the properties of natural stones. However, it wasn't until the late 1990s that significant advancements in technology allowed for the commercial production of sintered stone. Companies like Neolith and Dekton pioneered this field by developing proprietary processes that could consistently produce high-quality sintered stone products. These innovations have since revolutionized the construction and interior design industries by offering a versatile material that is resistant to scratches, stains, and heat, making it ideal for applications ranging from kitchen countertops to architectural facades. The term "sintering" itself comes from the German word "sintern," meaning "to compact without melting." This process leverages the principles of powder metallurgy, where powdered materials are compressed and then subjected to high temperatures to form a solid mass. In the context of sintered stone, this technique ensures that the final product retains the natural beauty of its constituent materials while gaining superior mechanical strength and durability. Today, sintered stone is recognized globally for its sustainability, as it often utilizes recycled materials and can be produced with minimal environmental impact compared to traditional quarrying methods. Its versatility in design also makes it a favorite among architects and designers who seek to create visually striking yet functional spaces. Whether used in residential or commercial settings, sintered stone stands as a testament to human ingenuity in transforming raw materials into something extraordinary through advanced technology and innovative manufacturing processes.
Historical Development
The historical development of sintered stone is a narrative that intertwines technological innovation, material science, and industrial evolution. The concept of sintering itself dates back to ancient times, where early civilizations discovered that heating and compressing powders could create durable, cohesive materials. However, the modern iteration of sintered stone as we know it today began to take shape in the mid-20th century. During the post-war period, advancements in ceramic engineering and the development of new manufacturing technologies paved the way for the creation of advanced materials. Researchers and manufacturers began experimenting with various types of powders, including those derived from natural minerals, to produce high-performance surfaces. The breakthrough came with the introduction of advanced presses and kilns that could apply immense pressure and precise temperature control, allowing for the uniform sintering of these powders into solid, non-porous slabs. In the 1990s, Italian companies such as Breton and System Group were at the forefront of this innovation, developing proprietary technologies that enabled mass production of these sintered surfaces. These early products were marketed under various brand names and quickly gained popularity due to their exceptional durability, resistance to scratches and stains, and aesthetic appeal. The term "sintered stone" emerged as a generic descriptor for these materials, distinguishing them from traditional natural stones like marble and granite. As the industry grew, so did the range of applications for sintered stone. Initially used primarily for countertops and flooring, it soon found its way into architectural facades, wall cladding, and even furniture design. The versatility of sintered stone was further enhanced by advancements in digital printing technology, allowing for intricate designs and patterns to be embedded directly into the material during the manufacturing process. Today, sintered stone is a staple in both residential and commercial construction projects worldwide. Its popularity can be attributed not only to its technical attributes but also to its sustainability profile; sintered stone is often made from recycled materials and can be produced with lower environmental impact compared to quarrying natural stone. As technology continues to evolve, we can expect even more innovative applications of sintered stone, further solidifying its place as a premier material choice for architects, designers, and homeowners alike. In summary, the historical development of sintered stone reflects a convergence of technological advancements, industrial innovation, and market demand. From its ancient roots in basic sintering techniques to its modern-day applications in high-performance surfaces, sintered stone has come a long way and continues to shape the future of building materials.
Current Market Trends
In the current market landscape, several trends are shaping the demand and perception of building materials, particularly in the realm of sintered stone. One of the most significant trends is the increasing emphasis on sustainability and eco-friendliness. Consumers and architects alike are seeking materials that not only offer durability and aesthetic appeal but also contribute to a reduced environmental footprint. Sintered stone, with its composition of natural minerals and recycled materials, aligns perfectly with this trend. It is manufactured using advanced technology that minimizes waste and energy consumption, making it an attractive choice for those prioritizing green building practices. Another trend influencing the market is the growing preference for low-maintenance and high-performance materials. Homeowners and commercial property managers are looking for surfaces that can withstand heavy use without requiring frequent upkeep. Sintered stone excels in this regard, offering exceptional resistance to scratches, stains, and heat, thereby reducing the need for constant cleaning and maintenance. This attribute is particularly appealing in high-traffic areas such as kitchens, bathrooms, and public spaces. The rise of smart homes and smart buildings has also led to an increased focus on materials that integrate seamlessly with modern technology. Sintered stone, with its versatility and adaptability, can be easily incorporated into smart design concepts. Its uniformity and consistency make it an ideal surface for various applications, from countertops and flooring to wall cladding and facades, allowing for a cohesive and futuristic aesthetic. Furthermore, the market is witnessing a shift towards personalized and bespoke design solutions. Consumers are no longer content with generic, mass-produced products; instead, they seek unique and customized options that reflect their individual style. Sintered stone manufacturers have responded to this demand by offering a wide range of colors, textures, and patterns, allowing designers to create tailored solutions that meet specific client needs. Lastly, the global construction industry is experiencing a surge in urbanization and infrastructure development, driving up demand for durable and long-lasting materials. Sintered stone's inherent strength and resilience make it an excellent choice for both residential and commercial projects, ensuring that structures can withstand the test of time while maintaining their aesthetic appeal. In summary, the current market trends—sustainability, low maintenance, technological integration, customization, and urbanization—are all favorably aligned with the characteristics of sintered stone. As consumers become more discerning about the materials used in their homes and public spaces, sintered stone stands out as a superior option that meets multiple criteria, making it an increasingly popular choice in the world of architecture and design.
Manufacturing Process of Sintered Stone
The manufacturing process of sintered stone is a complex and highly specialized field that involves several critical stages to produce a high-quality, durable, and aesthetically pleasing product. At the heart of this process are the careful selection and combination of raw materials, which form the foundation of the final product's properties. The composition of these materials is meticulously engineered to ensure optimal performance and appearance. Additionally, technological advancements have significantly enhanced the production process, allowing for greater precision, efficiency, and innovation. These advancements include state-of-the-art machinery and sophisticated manufacturing techniques that contribute to the superior quality of sintered stone. Furthermore, stringent quality control measures are implemented throughout the entire production cycle to guarantee that every product meets the highest standards. By understanding these key aspects—raw materials and composition, technological advancements, and quality control measures—we can appreciate the meticulous craftsmanship and scientific rigor that go into creating sintered stone. Let us begin by examining the raw materials and composition that underpin this entire process.
Raw Materials and Composition
In the manufacturing process of sintered stone, the selection and composition of raw materials play a crucial role in determining the final product's quality, durability, and aesthetic appeal. Sintered stone, also known as engineered stone or porcelain slabs, is primarily composed of natural minerals such as quartz, feldspar, and silica. These minerals are combined with other inorganic materials like metal oxides and ceramic powders to enhance the stone's color, strength, and resistance to wear and tear. The raw materials are carefully sourced to ensure they meet stringent quality standards; for instance, quartz is often chosen for its hardness and stability, while feldspar contributes to the stone's translucency and durability. The composition of sintered stone typically includes a high percentage of quartz (often around 90-95%), which provides the necessary hardness and resistance to scratches and abrasions. Other components may include feldspar (5-10%), silica, and metal oxides that act as pigments to achieve various colors and patterns. Additionally, small amounts of ceramic powders and other additives are incorporated to improve the stone's mechanical properties and facilitate the sintering process. The precise ratio of these components can vary depending on the desired characteristics of the final product, such as its color, texture, and performance attributes. The raw materials undergo rigorous processing before they are ready for sintering. This involves grinding the minerals into fine powders, which are then mixed with other ingredients in a controlled environment to ensure uniformity. The mixture is then pressed into large slabs using advanced machinery that applies high pressure to compact the material. This stage is critical as it determines the density and homogeneity of the sintered stone. During the sintering process, these compacted slabs are subjected to extremely high temperatures (typically between 1200°C to 1400°C) in a controlled atmosphere. This heat treatment causes the particles to fuse together, resulting in a dense and non-porous material that is highly resistant to stains, chemicals, and heat. The sintering process also allows for the creation of complex patterns and designs by manipulating the raw material composition and the conditions under which it is fired. The careful selection and precise composition of raw materials in sintered stone manufacturing ensure that the final product exhibits superior performance characteristics compared to natural stones. These include enhanced durability, low maintenance requirements, and a wide range of design possibilities. Furthermore, the use of advanced technology in processing and sintering allows manufacturers to produce consistent high-quality products that meet or exceed industry standards. Overall, the meticulous attention to raw material composition is a cornerstone of producing high-quality sintered stone that is both functional and aesthetically pleasing.
Technological Advancements in Production
Technological advancements have revolutionized the production of sintered stone, transforming it into a highly efficient and precise manufacturing process. At the heart of these advancements are cutting-edge technologies such as digital printing, robotic automation, and advanced material science. Digital printing allows for the precise application of pigments and patterns onto the raw material, enabling the creation of intricate designs and uniform color distribution. This technology not only enhances aesthetic appeal but also reduces waste and increases production speed. Robotic automation plays a crucial role in ensuring consistency and quality throughout the manufacturing process. Automated systems handle tasks such as material mixing, pressing, and handling with precision, minimizing human error and optimizing workflow. These robots are equipped with advanced sensors that monitor and adjust parameters in real-time, ensuring that each slab meets stringent quality standards. Advanced material science has led to the development of new raw materials and binders that enhance the physical properties of sintered stone. High-performance binders improve durability and resistance to wear and tear, while innovative raw materials expand the range of available colors and textures. Additionally, research into sustainable materials has introduced eco-friendly alternatives that reduce environmental impact without compromising on performance. The integration of Industry 4.0 technologies, such as IoT (Internet of Things) and AI (Artificial Intelligence), further optimizes production processes. Real-time data analytics enable manufacturers to monitor production lines remotely, predict maintenance needs, and make data-driven decisions to improve efficiency. AI algorithms can analyze production data to identify patterns and anomalies, allowing for continuous improvement in product quality. Moreover, 3D scanning and modeling technologies facilitate the creation of complex shapes and custom designs, catering to the growing demand for bespoke architectural features. These technologies allow architects and designers to visualize their designs accurately before production begins, ensuring that the final product meets their exact specifications. In summary, technological advancements have significantly enhanced the manufacturing process of sintered stone by improving precision, efficiency, and quality. From digital printing to robotic automation and advanced material science, these innovations have positioned sintered stone as a premier choice for architects and designers seeking high-performance materials with unparalleled aesthetic appeal. As technology continues to evolve, it is likely that the production of sintered stone will become even more sophisticated, driving further innovation in the field of construction materials.
Quality Control Measures
Quality control measures are paramount in the manufacturing process of sintered stone, ensuring that the final product meets stringent standards of durability, aesthetics, and performance. From raw material selection to the final inspection, a robust quality control framework is essential. The journey begins with the careful selection of raw materials, typically a blend of natural minerals and recycled materials, which are thoroughly tested for purity and consistency. These materials are then subjected to rigorous mixing and homogenization processes to ensure uniformity in composition. The mixture is subsequently pressed into slabs using high-pressure presses, a step where precise control over pressure and temperature is crucial to achieve the desired density and texture. During the sintering process, where the slabs are heated to extremely high temperatures in a controlled environment, continuous monitoring of temperature and time ensures that the material undergoes optimal transformation without defects. Post-sintering, the slabs undergo various treatments such as polishing and finishing, where quality inspectors scrutinize each slab for any imperfections or deviations from specifications. Advanced technologies like automated inspection systems and computer-aided quality control tools are often employed to enhance the accuracy and efficiency of this process. Furthermore, sintered stone manufacturers adhere to international standards and certifications such as ISO 9001 for quality management and ISO 14001 for environmental management. Regular audits and compliance checks ensure that all production processes align with these standards. Additionally, manufacturers often conduct in-house testing for mechanical properties like flexural strength, impact resistance, and chemical resistance to guarantee that the sintered stone can withstand various environmental conditions. Customer feedback and market research also play a significant role in refining quality control measures. Manufacturers continuously gather data on product performance in real-world applications and incorporate this feedback into their quality improvement cycles. This iterative approach ensures that the sintered stone not only meets current standards but also evolves to meet emerging demands and trends. In summary, quality control in the manufacturing of sintered stone is a multifaceted process that involves meticulous attention to detail at every stage, from raw material selection to final product inspection. By leveraging advanced technologies, adhering to international standards, and integrating customer feedback, manufacturers can produce high-quality sintered stone that excels in both form and function. This commitment to quality is what distinguishes superior sintered stone products from their competitors, making them a preferred choice for architects, designers, and homeowners seeking durable and aesthetically pleasing surfaces.
Applications and Benefits of Sintered Stone
Sintered stone, a cutting-edge material engineered through advanced technological processes, offers a myriad of applications and benefits that make it an ideal choice for various industries. This versatile material is not only aesthetically pleasing but also boasts exceptional performance characteristics and durability, making it a preferred option for architects and designers. In architectural and design contexts, sintered stone is celebrated for its ability to enhance the visual appeal of spaces while providing functional advantages. Its performance characteristics, such as resistance to scratches, heat, and stains, ensure that it remains in pristine condition over time. Additionally, sintered stone is environmentally friendly and poses minimal health risks, aligning with modern sustainability and wellness standards. As we delve into the specifics of sintered stone, we will first explore its architectural and design uses, highlighting how this material can transform spaces with its unique blend of form and function.
Architectural and Design Uses
Sintered stone, with its unique blend of durability, versatility, and aesthetic appeal, has revolutionized various aspects of architectural and design applications. This engineered material, crafted through a high-pressure and high-temperature process, offers a robust alternative to natural stone while maintaining the elegance and sophistication that architects and designers seek. In architectural contexts, sintered stone is frequently used for exterior cladding due to its resistance to weathering, UV light, and extreme temperatures. Its non-porous nature makes it ideal for facades, ensuring minimal maintenance and a consistent appearance over time. Additionally, sintered stone's ability to mimic the look of natural materials such as marble, granite, and slate allows architects to achieve desired visual effects without the inherent drawbacks of natural stone. In interior design, sintered stone is a go-to choice for countertops, flooring, and wall coverings. Its high density and lack of porosity make it resistant to stains and scratches, making it perfect for high-traffic areas like kitchens and bathrooms. The material's hygienic properties also make it an excellent option for healthcare facilities and commercial spaces where cleanliness is paramount. Designers appreciate the wide range of colors and patterns available in sintered stone, allowing for endless creative possibilities that can seamlessly integrate with various design styles. Furthermore, its lightweight yet robust construction simplifies installation processes, reducing both time and cost. The versatility of sintered stone extends beyond residential and commercial spaces; it is also gaining traction in public architecture. For instance, it is often used in public buildings such as museums, libraries, and government offices where durability and low maintenance are crucial. The material's ability to withstand heavy foot traffic without compromising on aesthetics makes it an ideal choice for these environments. Moreover, sintered stone can be fabricated into complex shapes and designs, enabling architects to create intricate architectural features that would be challenging or impractical with traditional materials. From a sustainability perspective, sintered stone offers several advantages. It is made from a combination of natural minerals and recycled materials, reducing the environmental impact associated with quarrying natural stone. Additionally, its long lifespan means fewer replacements are needed over time, contributing to a more sustainable built environment. This eco-friendly aspect aligns well with contemporary architectural trends that prioritize green building practices. In summary, sintered stone's unique properties make it an indispensable tool in modern architecture and design. Its durability, aesthetic versatility, and sustainable credentials have positioned it as a preferred choice across various applications—from exterior cladding to interior finishes—and continue to inspire innovative uses in both public and private spaces. As technology continues to evolve, the potential for sintered stone in shaping future architectural landscapes looks promising indeed.
Performance Characteristics and Durability
Sintered stone, a cutting-edge material in the realm of construction and design, boasts an array of performance characteristics and durability traits that make it an ideal choice for various applications. One of its most compelling attributes is its exceptional hardness, often surpassing that of natural stone. This inherent hardness not only enhances its resistance to scratches and abrasions but also ensures that it maintains its aesthetic appeal over time, even in high-traffic areas. Additionally, sintered stone exhibits superior density, which significantly reduces its porosity compared to traditional materials like granite or marble. This reduced porosity translates into enhanced stain resistance and a lower risk of bacterial growth, making it particularly suitable for environments where hygiene is paramount, such as kitchens and bathrooms. Another critical performance characteristic of sintered stone is its thermal resistance. Unlike many other materials that can crack or discolor when exposed to extreme temperatures, sintered stone remains stable and intact. This thermal stability is crucial in settings where heat sources are common, such as near stovetops or fireplaces. Furthermore, sintered stone is highly resistant to chemical damage, standing up well against acidic substances and cleaning products that might compromise other materials. This chemical resilience adds to its durability and longevity, ensuring that it retains its original appearance despite exposure to various substances. In terms of mechanical strength, sintered stone outperforms many natural stones due to its uniform composition and manufacturing process. The sintering process involves subjecting raw materials to high temperatures and pressures, resulting in a homogeneous structure that lacks the natural flaws found in quarried stones. This uniformity contributes to its enhanced mechanical properties, including tensile strength and flexural strength, making it more resistant to cracking and breaking under load. The durability of sintered stone is also underscored by its low maintenance requirements. Unlike natural stones that often need periodic sealing to protect against stains and wear, sintered stone is inherently non-porous and does not require such treatments. This ease of maintenance makes it a practical choice for busy households and commercial spaces where upkeep needs to be minimal yet effective. Moreover, sintered stone's environmental sustainability is another significant aspect of its durability profile. Made from a combination of natural minerals and recycled materials, it offers an eco-friendly alternative to traditional stone products. The manufacturing process itself is designed to minimize waste and energy consumption, aligning with contemporary demands for sustainable building materials. In summary, the performance characteristics and durability of sintered stone make it an exemplary material for a wide range of applications. Its hardness, density, thermal resistance, chemical resilience, mechanical strength, low maintenance needs, and environmental sustainability collectively contribute to its long-lasting performance and aesthetic appeal. Whether used in residential or commercial settings, sintered stone stands as a testament to innovative engineering and material science, offering unparalleled benefits that enhance both functionality and design.
Environmental and Health Considerations
When considering the applications and benefits of sintered stone, it is crucial to delve into the environmental and health implications associated with this material. Sintered stone, a type of engineered stone produced through a process of high-pressure compaction and heat treatment, offers several advantages that align with contemporary environmental and health standards. From an environmental perspective, sintered stone is often made from recycled materials such as ceramic waste, glass, and natural minerals, reducing the need for raw material extraction and minimizing waste disposal issues. This sustainable approach not only conserves natural resources but also decreases the carbon footprint associated with traditional stone quarrying and processing methods. Additionally, sintered stone is highly durable and resistant to wear and tear, which means it requires less maintenance and replacement over time, further reducing its lifecycle impact on the environment. In terms of health considerations, sintered stone stands out for its non-porous nature, which makes it resistant to bacterial growth and moisture absorption. This characteristic is particularly beneficial in kitchens and bathrooms where hygiene is paramount. Unlike natural stones like marble or granite that can harbor bacteria and require frequent sealing, sintered stone maintains its integrity without the need for chemical treatments. Moreover, sintered stone is free from volatile organic compounds (VOCs) and other harmful chemicals that can off-gas and compromise indoor air quality. This makes it an ideal choice for residential and commercial spaces where occupant health is a priority. The absence of VOCs also aligns with green building standards and certifications such as LEED (Leadership in Energy and Environmental Design), making sintered stone a preferred material for architects and builders committed to sustainable design. Furthermore, the manufacturing process of sintered stone involves advanced technologies that ensure consistent quality and minimal waste generation. The use of advanced machinery and automation reduces human error and enhances the overall efficiency of production, leading to a more controlled and environmentally friendly manufacturing environment. This level of precision also translates into a product that is consistent in appearance and performance, which is essential for maintaining high standards in both residential and commercial settings. In conclusion, the environmental and health benefits of sintered stone are significant and multifaceted. By leveraging recycled materials, reducing lifecycle impacts, and offering a non-porous surface that promotes hygiene and indoor air quality, sintered stone emerges as a superior choice for those seeking sustainable yet high-performance building materials. As awareness about environmental sustainability and health continues to grow, the advantages of sintered stone will only become more pronounced, making it an increasingly popular option for architects, builders, and homeowners alike.