What Is Pex

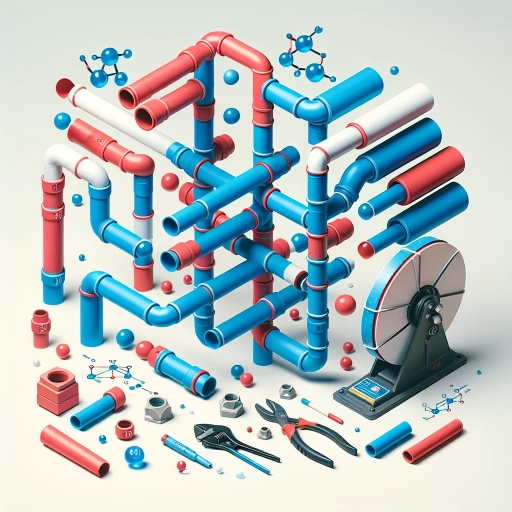
Introduction to PEX
In the realm of modern plumbing and piping systems, PEX (Cross-Linked Polyethylene) has emerged as a versatile and highly efficient material. This introduction to PEX aims to delve into its multifaceted nature, exploring its historical development, widespread applications, and the significant advantages it offers over traditional materials. First, we will examine the **Definition and History of PEX**, tracing its evolution from its inception to its current status as a preferred choice in various industries. This foundational understanding will set the stage for a deeper exploration of **Common Applications of PEX**, highlighting its use in residential, commercial, and industrial settings. Finally, we will discuss the **Key Benefits Over Traditional Materials**, such as its flexibility, resistance to corrosion, and ease of installation. By understanding these aspects, readers will gain a comprehensive insight into why PEX has become a staple in contemporary plumbing solutions. Let us begin by uncovering the origins and definition of PEX, which will provide a solid foundation for our exploration of its applications and benefits.
Definition and History of PEX
**Definition and History of PEX** Polyethylene cross-linked (PEX) tubing is a versatile and widely used material in modern plumbing, hydronic heating, and cooling systems. The term "cross-linked" refers to the chemical process that transforms polyethylene into a more durable and flexible product. This transformation involves creating molecular bonds between polyethylene chains, enhancing the material's resistance to high temperatures, chemicals, and pressure. The history of PEX dates back to the 1960s when it was first developed in Europe. Initially, PEX was used primarily for hydronic heating systems due to its ability to withstand freezing temperatures and its flexibility, which allowed for easier installation around obstacles. Over the decades, advancements in manufacturing processes have improved the quality and reliability of PEX tubing. By the 1980s, PEX began to gain popularity in North America as a viable alternative to traditional copper and PVC piping due to its numerous advantages. One of the key factors contributing to the widespread adoption of PEX is its ease of installation. Unlike rigid copper or PVC pipes, PEX tubing can be bent around corners without the need for fittings, reducing labor costs and installation time. Additionally, PEX is less prone to leaks and corrosion compared to other materials, making it a reliable choice for long-term use. Its resistance to scaling and freezing also makes it an ideal solution for areas with harsh weather conditions. The manufacturing process of PEX involves several methods, including peroxide cross-linking (PE-Xa), silane cross-linking (PE-Xb), and electron beam cross-linking (PE-Xc). Each method has its own set of benefits and is suited for different applications. For instance, PE-Xa is known for its high thermal stability and is often used in high-temperature applications. In recent years, PEX has become a standard material in many residential and commercial plumbing systems. Its adaptability to various environments and its eco-friendly properties have further solidified its position in the market. As technology continues to evolve, new generations of PEX tubing are being developed with enhanced performance characteristics, ensuring that this versatile material remains a cornerstone of modern plumbing and heating systems. Understanding the definition and history of PEX provides a solid foundation for appreciating its role in contemporary construction and infrastructure projects. From its origins in Europe to its widespread use today, PEX has proven itself as a reliable, efficient, and innovative solution for a variety of applications. Its continued development underscores its importance as a key component in modern building practices.
Common Applications of PEX
**Common Applications of PEX** PEX (Cross-Linked Polyethylene) tubing has revolutionized the plumbing and piping industry with its versatility, durability, and ease of installation. Its widespread adoption can be attributed to several key applications that highlight its unique advantages. In residential plumbing, PEX is often used for water supply lines due to its resistance to freezing and scaling, which significantly reduces the risk of pipe bursts and mineral buildup. Its flexibility allows for easier navigation through tight spaces and around corners, making it ideal for retrofitting older homes without major renovations. Additionally, PEX tubing is quieter than traditional copper or PVC pipes, as it absorbs the noise of water flow, providing a more peaceful living environment. In commercial settings, PEX is favored for its ability to withstand high temperatures and pressures, making it suitable for hydronic heating systems. These systems involve circulating hot water through pipes to warm buildings, and PEX's resistance to corrosion and scaling ensures long-term reliability. The tubing's flexibility also simplifies the installation process in complex commercial layouts. Furthermore, PEX is used in radiant floor heating systems where it is embedded in concrete or placed under flooring to distribute heat evenly throughout a space. This application not only provides efficient heating but also reduces energy costs by leveraging the thermal mass of the building materials. Beyond plumbing and heating, PEX finds applications in various industrial sectors. In medical facilities, PEX tubing is used for medical gas distribution systems due to its purity and resistance to contamination. It is also employed in chemical processing plants where its chemical resistance and durability are crucial for handling corrosive substances. In agricultural settings, PEX is used for irrigation systems because it can withstand exposure to sunlight and extreme temperatures without degrading. Another significant application of PEX is in the automotive industry. Here, it is used for fuel lines and cooling systems due to its resistance to chemicals and high temperatures. This ensures the reliability and safety of vehicle operations. Moreover, PEX tubing is utilized in marine environments for potable water systems on boats and ships because it resists corrosion from seawater and other marine contaminants. In summary, the common applications of PEX tubing span across residential, commercial, industrial, and automotive sectors. Its unique properties such as flexibility, resistance to freezing and scaling, chemical inertness, and durability make it an indispensable material in modern piping solutions. Whether it's for water supply lines, hydronic heating systems, medical gas distribution, or automotive fuel lines, PEX continues to prove itself as a versatile and reliable choice for a wide range of applications.
Key Benefits Over Traditional Materials
When comparing PEX (Cross-Linked Polyethylene) tubing to traditional materials like copper, PVC, and galvanized steel, several key benefits emerge that make PEX a superior choice for plumbing and heating applications. **Flexibility** is one of the most significant advantages of PEX. Unlike rigid materials, PEX tubing can be bent and shaped to navigate around obstacles, reducing the need for fittings and connections. This flexibility not only simplifies installation but also minimizes potential leak points, thereby enhancing system reliability. Additionally, PEX is **resistant to corrosion**, a common issue with traditional materials that can lead to costly repairs and replacements. The non-reactive nature of PEX ensures it does not corrode or scale over time, maintaining water quality and system performance. Another critical benefit is **freeze resistance**. PEX tubing can expand to accommodate frozen water, reducing the risk of bursting pipes during cold weather. This feature is particularly valuable in regions prone to freezing temperatures, as it helps prevent the extensive damage often associated with frozen pipes. Furthermore, PEX is **quieter** than traditional materials due to its ability to absorb water hammer noise, providing a more peaceful living environment. The **ease of installation** is another significant advantage; PEX can be installed using push-fit fittings or crimp rings, which are simpler and faster to use compared to soldering or gluing required for other materials. From an **energy efficiency** perspective, PEX offers better insulation properties than many traditional materials. Its inherent flexibility allows it to be used in continuous runs without the need for multiple joints, which can act as thermal bridges and reduce overall system efficiency. Moreover, PEX is **environmentally friendly**; it requires less energy to produce than many other plumbing materials and can be recycled at the end of its life cycle. This eco-friendly aspect aligns well with modern sustainability goals. In terms of **cost-effectiveness**, while the initial cost of PEX might be higher than some traditional materials, its long-term benefits often outweigh these costs. The reduced need for fittings and connections, combined with lower labor costs due to easier installation, can result in significant savings over time. Additionally, the durability and resistance to corrosion mean that PEX systems typically have a longer lifespan than those made from traditional materials, further enhancing their cost-effectiveness. Lastly, **compatibility** with various water treatment systems and chemicals is another key benefit of PEX. It is resistant to chlorine and other disinfectants commonly used in water treatment processes, ensuring that it remains intact and functional even in environments where other materials might degrade. This compatibility makes PEX an ideal choice for both residential and commercial applications where water quality is paramount. In summary, PEX offers a compelling array of benefits over traditional plumbing materials, including flexibility, corrosion resistance, freeze resistance, ease of installation, energy efficiency, environmental friendliness, cost-effectiveness, and compatibility with various water treatment systems. These advantages collectively make PEX a preferred option for modern plumbing and heating solutions.
Technical Aspects of PEX
The technical aspects of PEX (Cross-Linked Polyethylene) tubing are multifaceted and crucial for understanding its widespread adoption in plumbing and heating systems. This article delves into three key areas that highlight the robustness and versatility of PEX: the manufacturing process and materials, the different types of PEX tubing (PEX-A, PEX-B, PEX-C), and its physical properties and durability. Each of these aspects contributes to the overall performance and reliability of PEX tubing, making it a preferred choice for various applications. The manufacturing process, which involves cross-linking polyethylene molecules, is a critical factor in determining the strength and flexibility of the tubing. Understanding the different types of PEX tubing is essential for selecting the right product for specific needs, as each type has unique characteristics. Additionally, examining the physical properties and durability of PEX provides insights into its resistance to corrosion, scaling, and environmental stressors. By exploring these technical aspects, we can appreciate the engineering and science behind PEX tubing and its role in modern infrastructure. Let's begin by examining the manufacturing process and materials that form the foundation of PEX tubing's excellence.
Manufacturing Process and Materials
The manufacturing process of PEX (Cross-Linked Polyethylene) tubing is a complex and highly controlled sequence that ensures the production of a durable, flexible, and resistant material. The journey begins with the selection of high-quality raw materials, primarily ethylene, which is polymerized to form polyethylene. This base material is then subjected to a cross-linking process, where molecular bonds are formed between the polymer chains. There are three primary methods for cross-linking: peroxide (PEX-a), silane (PEX-b), and electron beam (PEX-c). Each method has its own advantages and is chosen based on the desired properties of the final product. In the peroxide method, a peroxide initiator is added to the polyethylene, which decomposes during extrusion, forming free radicals that cross-link the polymer chains. This method is known for its high degree of cross-linking and is often used in applications requiring high temperature resistance. The silane method involves grafting silane groups onto the polyethylene backbone, followed by a hydrolysis reaction that forms the cross-links. This process is more environmentally friendly and results in a material with excellent flexibility and resistance to chemicals. The electron beam method uses high-energy electron beams to break the polymer chains, allowing them to recombine in a cross-linked structure. This technique offers precise control over the degree of cross-linking and is favored for its ability to produce tubing with consistent properties. Once the cross-linking process is complete, the PEX tubing is extruded through a die to achieve the desired diameter and wall thickness. The tubing is then cooled, cut to length, and subjected to various tests to ensure it meets industry standards for strength, flexibility, and resistance to chemicals and temperature fluctuations. The choice of materials in PEX manufacturing is crucial for its performance. Polyethylene itself is a versatile polymer that can be formulated to have a wide range of properties. Additives such as antioxidants, UV stabilizers, and colorants may be included to enhance the tubing's durability and appearance. For instance, antioxidants prevent degradation from oxidative reactions, while UV stabilizers protect the material from ultraviolet light damage. The finished PEX tubing exhibits several key characteristics that make it an ideal choice for various applications, including plumbing, heating systems, and industrial processes. Its flexibility allows for easier installation and reduces the need for fittings, while its resistance to scaling and corrosion extends its lifespan. Additionally, PEX tubing can withstand freezing temperatures without bursting, making it a reliable option for cold climates. In summary, the manufacturing process of PEX involves careful selection of raw materials, precise control over the cross-linking process, and rigorous testing to ensure the production of high-quality tubing. The choice of cross-linking method and additives significantly influences the final product's properties, making PEX a versatile material suitable for a wide range of technical applications. Understanding these technical aspects is essential for appreciating the reliability and performance of PEX in various industrial and residential settings.
Types of PEX Tubing (PEX-A, PEX-B, PEX-C)
When delving into the technical aspects of PEX (Cross-Linked Polyethylene) tubing, it is crucial to understand the different types that exist, each with its own unique characteristics and applications. PEX tubing is categorized into three main types: PEX-A, PEX-B, and PEX-C, each distinguished by the method used to cross-link the polyethylene molecules. **PEX-A** tubing is produced using the peroxide method, where peroxide is added to the polyethylene material during the extrusion process. This method results in a more flexible and kink-resistant tubing compared to other types. PEX-A tubing is known for its excellent resistance to scaling and corrosion, making it ideal for use in plumbing systems where water quality can be variable. Additionally, PEX-A is easier to shape and bend, reducing the need for fittings and making it a favorite among plumbers for its ease of installation. **PEX-B** tubing, on the other hand, is manufactured using the silane method, where silane molecules are grafted onto the polyethylene backbone during the extrusion process. This type of tubing offers a balance between flexibility and durability. While not as flexible as PEX-A, PEX-B is still relatively easy to work with and provides good resistance to scaling and corrosion. It is widely used in residential plumbing due to its cost-effectiveness and reliable performance. **PEX-C** tubing employs an electron beam irradiation method to cross-link the polyethylene molecules. This process involves exposing the tubing to electron beams after extrusion, which creates cross-links within the material. PEX-C tubing is known for its high resistance to chemicals and abrasion but is generally less flexible than both PEX-A and PEX-B. It is often used in commercial applications where higher durability is required. Understanding these differences is essential for selecting the appropriate type of PEX tubing for specific projects. For instance, in areas where water pressure is high or where tubing needs to be bent around tight corners, PEX-A might be the best choice. In contrast, for projects requiring a balance between cost and performance, PEX-B could be more suitable. For applications demanding high chemical resistance and durability, PEX-C would be the preferred option. In summary, the choice between PEX-A, PEX-B, and PEX-C depends on the specific requirements of the project, including factors such as flexibility, durability, resistance to scaling and corrosion, and cost considerations. Each type of PEX tubing has its own set of advantages and is designed to meet different technical specifications, ensuring that there is a suitable option available for a wide range of plumbing and heating applications.
Physical Properties and Durability
**Physical Properties and Durability** When it comes to the technical aspects of PEX (Cross-Linked Polyethylene), its physical properties and durability are paramount. PEX tubing is renowned for its exceptional flexibility, which significantly simplifies installation processes. Unlike rigid pipes, PEX can be bent and shaped to navigate through tight spaces without the need for elbows or fittings, reducing the risk of leaks and making it ideal for complex plumbing systems. This flexibility also enhances its resistance to freezing temperatures; when water inside the pipe freezes, PEX can expand to accommodate the ice without bursting, a common issue with traditional piping materials. Another critical physical property of PEX is its resistance to corrosion and scaling. Unlike metal pipes that can corrode over time due to exposure to water and minerals, PEX is inert and does not react with water or other substances. This characteristic ensures that the water quality remains unaffected by the piping material, making it a healthier choice for potable water systems. Additionally, PEX is resistant to scaling, which means it does not accumulate mineral deposits that can reduce water flow over time. The durability of PEX is also a key factor in its popularity. With a lifespan of up to 50 years or more under normal conditions, PEX outperforms many other piping materials in terms of longevity. Its cross-linked molecular structure provides superior strength and resistance to abrasion and impact. Furthermore, PEX tubing is less prone to damage from external factors such as soil settlement or minor excavations, which can cause cracks in more brittle materials like PVC or ABS. In terms of thermal properties, PEX has a high thermal resistance, meaning it can withstand a wide range of temperatures without losing its integrity. This makes it suitable for both hot and cold water applications, including radiant floor heating systems where it is often used due to its ability to maintain flexibility even at elevated temperatures. The chemical resistance of PEX is another significant advantage. It is resistant to a broad spectrum of chemicals, including those commonly found in household cleaning products and industrial environments. This resistance ensures that the piping system remains intact and functional even when exposed to potentially corrosive substances. Overall, the combination of flexibility, corrosion resistance, durability, and thermal stability makes PEX an excellent choice for various plumbing and heating applications. Its physical properties not only simplify installation but also ensure long-term performance and reliability, making it a preferred material among builders and homeowners alike. As part of the broader discussion on the technical aspects of PEX, understanding these physical properties and durability factors is crucial for appreciating the full value and versatility of this versatile piping material.
Installation and Maintenance of PEX Systems
The installation and maintenance of PEX (Cross-Linked Polyethylene) systems are crucial for ensuring the longevity and efficiency of plumbing infrastructure. PEX systems, known for their flexibility and resistance to corrosion, offer a versatile solution for modern plumbing needs. However, their successful implementation hinges on several key factors. First, understanding the **Tools and Techniques for Installing PEX** is essential to avoid common mistakes and ensure a seamless installation process. This includes selecting the right tubing sizes, using appropriate fittings, and mastering the art of bending and connecting PEX pipes. Additionally, **Best Practices for PEX System Design** must be adhered to, focusing on proper layout, pressure testing, and insulation to optimize performance and prevent potential issues. Lastly, being equipped with knowledge on **Troubleshooting Common Issues with PEX Systems** helps in identifying and resolving problems promptly, thereby minimizing downtime and maintaining system integrity. By delving into these critical aspects, one can ensure that a PEX system operates at its best. To begin, let's explore the **Tools and Techniques for Installing PEX**, which form the foundation of a well-executed PEX installation.
Tools and Techniques for Installing PEX
Installing PEX (Cross-Linked Polyethylene) tubing requires a combination of the right tools and techniques to ensure a reliable, efficient, and durable plumbing system. Here are the key tools and methods you should employ: **Tools:** 1. **PEX Tubing Cutter:** A dedicated cutter is essential for making clean, precise cuts in the tubing. This tool helps prevent damage to the inner walls of the PEX. 2. **PEX Ring Removal Tool:** This tool is used to remove the copper rings from fittings after they have been crimped onto the tubing. 3. **PEX Crimp Tool:** This tool secures fittings onto the PEX tubing by crimping copper rings around them. 4. **PEX Go/No-Go Gauge:** This gauge ensures that the copper ring has been properly crimped onto the fitting. 5. **PEX Pipe Bender:** For bending PEX tubing without kinking or damaging it, a pipe bender is indispensable. 6. **Tubing Reamer:** Used to deburr the cut ends of PEX tubing, ensuring smooth connections. **Techniques:** 1. **Cutting:** Always use a PEX tubing cutter to avoid damaging the inner walls of the tubing. Cut the tubing squarely and deburr the ends with a tubing reamer. 2. **Bending:** Use a PEX pipe bender to create smooth bends without kinking or restricting flow within the tubing. 3. **Connecting Fittings:** Insert the fitting into the PEX tubing, ensuring it is seated properly. Then, place a copper ring over the fitting and use a crimp tool to secure it in place. Verify with a go/no-go gauge that the crimp is correct. 4. **Securing Tubing:** Use PEX clips or clamps to secure the tubing to walls, floors, or ceilings, keeping it organized and preventing damage from movement or pressure. 5. **Testing:** After installation, perform a pressure test to ensure there are no leaks in the system. This involves pressurizing the system with air or water and checking for any drops in pressure over time. **Best Practices:** - **Plan Ahead:** Map out your PEX system before starting installation to minimize waste and ensure efficient routing. - **Follow Manufacturer Guidelines:** Adhere strictly to manufacturer recommendations for tools, fittings, and installation procedures. - **Inspect Regularly:** Regularly inspect your PEX system for signs of wear, damage, or leaks to maintain its integrity. By utilizing these tools and techniques, you can ensure a well-installed PEX system that is durable, efficient, and free from common issues such as leaks or kinks. Proper installation not only extends the lifespan of your plumbing but also enhances overall performance and reliability.
Best Practices for PEX System Design
When designing a PEX (Cross-Linked Polyethylene) system, adhering to best practices is crucial for ensuring the longevity, efficiency, and safety of the installation. **Proper Planning** is the foundation of any successful PEX system design. This involves conducting thorough site assessments to identify potential challenges such as water quality, temperature fluctuations, and space constraints. It is essential to select the appropriate PEX tubing size based on the specific application and flow requirements to avoid under-sizing or over-sizing, which can lead to reduced system performance or increased energy consumption. **Material Selection** is another critical aspect. Choose PEX tubing that meets or exceeds local building codes and standards, such as those set by ASTM (American Society for Testing and Materials) or NSF International. Ensure that all components, including fittings, valves, and manifolds, are compatible with the chosen PEX tubing type to prevent leaks and other issues. **Layout and Routing** should be carefully considered to minimize the risk of damage and ensure easy access for future maintenance. Avoid routing PEX tubing near heat sources, electrical components, or areas where it may be subject to physical stress. Use protective sleeves or shields where necessary to safeguard the tubing from potential hazards. **Support and Securing** of the PEX tubing is vital to prevent sagging and damage. Use clips or hangers specifically designed for PEX systems, spaced at intervals recommended by the manufacturer, to keep the tubing secure and organized. This also helps in maintaining a neat and professional appearance. **Connection Techniques** must be executed with precision. Use the correct tools for making connections, such as press-fit tools or crimp rings, and follow the manufacturer's instructions to ensure secure and leak-free joints. It is advisable to perform pressure tests on the system before finalizing the installation to detect any potential leaks early. **Thermal Expansion** considerations are important, especially in systems that will be exposed to significant temperature changes. Allow for expansion loops or use expansion fittings to accommodate thermal movement without causing undue stress on the system. **Documentation and Training** are often overlooked but are essential for long-term success. Maintain detailed records of the system design, installation, and maintenance activities. Provide training to maintenance personnel on the specific requirements and best practices for the installed PEX system to ensure that any future work is done correctly. By following these best practices, you can ensure that your PEX system operates efficiently, safely, and reliably over its lifespan, minimizing the need for costly repairs and replacements while maximizing overall performance. This meticulous approach not only enhances the functionality of the system but also contributes to a safer and more sustainable plumbing infrastructure.
Troubleshooting Common Issues with PEX Systems
Troubleshooting common issues with PEX (Cross-Linked Polyethylene) systems is crucial for maintaining the integrity and performance of these versatile plumbing networks. Despite their durability and flexibility, PEX systems can encounter various problems that necessitate prompt and effective troubleshooting. One of the most common issues is **leaks**, which can arise from improper connections, damaged tubing, or excessive pressure. To address leaks, inspect the system thoroughly for signs of moisture or water damage. Check all fittings and connections for tightness and ensure that they are not over-tightened, as this can also cause damage. If a leak is found, replace the affected section of tubing or fitting promptly. Another frequent issue is **freezing**, particularly in colder climates. PEX tubing is resistant to freezing but not immune; prolonged exposure to sub-zero temperatures can still cause damage. Insulate exposed sections of PEX tubing in unheated areas like basements or crawlspaces to prevent freezing. Additionally, consider installing freeze-resistant PEX tubing in these areas. **Kinking** and **bending** are also common problems that can restrict water flow. Kinks occur when the tubing is bent too sharply, while bending can happen during installation if the tubing is not properly supported. To resolve kinking, carefully straighten the affected section without causing further damage. For bending issues, ensure that the tubing is supported with clips or hangers at regular intervals to maintain its shape. **Corrosion** at fittings and connections can be another challenge, especially if incompatible materials are used. Use only compatible fittings and ensure they are free from debris before installation. Regularly inspect these areas for signs of corrosion and replace any affected components immediately. **Water quality** issues can also impact PEX systems. Hard water or water with high levels of chlorine can degrade the tubing over time. Consider installing a water filter or softener to mitigate these effects. In cases where **low water pressure** is observed, it may be due to blockages within the system or improper sizing of the tubing. Check for any blockages such as mineral buildup or debris accumulation by flushing the system. If necessary, consult with a professional to ensure that the tubing sizes are appropriate for your specific needs. Finally, **rodent damage** can be a significant issue in some regions. Rodents may chew through PEX tubing if it is exposed in crawlspaces or attics. Protecting these areas with rodent-resistant materials or ensuring that all tubing is well-insulated can help prevent such damage. By understanding these common issues and taking proactive steps to address them, homeowners and installers can ensure that their PEX systems operate efficiently and reliably over their lifespan. Regular maintenance checks and prompt troubleshooting are key to extending the life of these systems and preventing costly repairs down the line.