What Is Resin Material

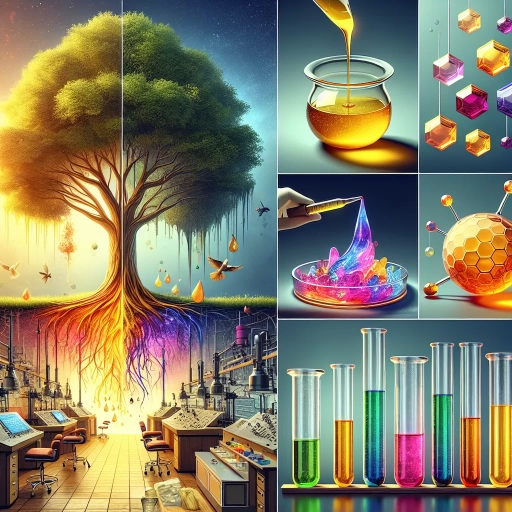
Resin material, a versatile and widely used substance, has become a cornerstone in various industries ranging from construction and automotive to art and crafts. Its unique properties, such as durability, flexibility, and resistance to chemicals, make it an ideal choice for numerous applications. This article delves into the world of resin materials, providing a comprehensive overview of what they are, their different types, and how they are manufactured and processed. We will begin by introducing the fundamental characteristics and uses of resin material, followed by an exploration of the diverse types of resin materials available, each with its own set of advantages and applications. Finally, we will examine the manufacturing and processing techniques that transform raw materials into the finished resin products that are integral to modern manufacturing. By understanding these aspects, readers will gain a deeper appreciation for the significance and versatility of resin materials in today's world. Let us start with an **Introduction to Resin Material** to lay the groundwork for this in-depth exploration.
Introduction to Resin Material
Resin materials have become a cornerstone in various industries due to their versatility, durability, and unique properties. This article provides an in-depth introduction to resin, exploring its definition and basic properties, historical use and development, and common applications across different sectors. Understanding the fundamental characteristics of resin is crucial for appreciating its widespread use. From its early applications in ancient civilizations to its modern-day roles in manufacturing, construction, and art, resin has evolved significantly over time. Today, it is a key component in industries such as automotive, aerospace, and healthcare, among others. By delving into the historical context and industrial applications of resin, we can better grasp its importance and potential. This journey begins with a clear definition and examination of the basic properties that make resin such a valuable material. Transitioning to the next section, we will explore the **Definition and Basic Properties** of resin, laying the groundwork for a deeper understanding of its historical and industrial significance.
Definition and Basic Properties
Resin materials are a class of polymers that are widely used in various industrial, commercial, and artistic applications due to their versatile properties and ease of manipulation. **Definition:** Resin is a type of organic compound that is typically viscous or semi-solid at room temperature but can be melted or dissolved in solvents. It is often derived from plant sources, such as pine sap, but can also be synthesized from petroleum-based materials. **Basic Properties:** 1. **Viscosity:** Resins can range from highly viscous to semi-solid, depending on their composition and temperature. This property makes them suitable for different applications, such as coatings, adhesives, and casting materials. 2. **Thermoplastic vs. Thermoset:** Resins can be categorized into thermoplastic and thermoset types. Thermoplastic resins can be melted and reformed multiple times without undergoing any significant chemical change, while thermoset resins undergo a chemical reaction when heated, resulting in a rigid structure that cannot be melted again. 3. **Chemical Resistance:** Many resin materials exhibit high resistance to chemicals, making them ideal for use in environments where exposure to corrosive substances is a concern. 4. **Mechanical Strength:** Resins can possess varying levels of mechanical strength, from flexible to rigid, depending on their formulation and curing process. 5. **Optical Clarity:** Some resins, particularly epoxy and acrylic resins, offer high optical clarity, making them suitable for applications requiring transparency or translucency. 6. **Adhesion:** Resins often have good adhesive properties, which are enhanced by surface preparation and the use of appropriate primers or additives. 7. **Curing Process:** The curing process for resins can involve heat, light (UV or visible), or chemical catalysts. This process transforms the resin from a liquid or semi-solid state into a solid form with desired properties. 8. **Environmental Impact:** The environmental impact of resins varies; some are biodegradable and derived from renewable sources, while others are petroleum-based and may have more significant environmental footprints. Understanding these basic properties is crucial for selecting the appropriate resin material for specific applications, whether it be in manufacturing, construction, art, or any other field where these versatile materials are utilized.
Historical Use and Development
Resin materials have a rich and diverse history that spans thousands of years, with their development and use evolving significantly over time. The earliest recorded use of resin dates back to ancient civilizations, where natural resins such as pine resin, amber, and plant-based resins were utilized for various purposes. In ancient Egypt, for instance, resin was used in mummification processes to preserve bodies and in the creation of intricate artworks. Similarly, in ancient Greece and Rome, resin was employed in shipbuilding to seal wooden hulls and protect them from water. The industrial revolution marked a significant turning point in the development of resin materials. With the advent of synthetic chemistry in the late 19th and early 20th centuries, scientists began to develop artificial resins. One of the first synthetic resins was Bakelite, invented by Leo Baekeland in 1907. This phenol-formaldehyde resin was groundbreaking because it was the first commercially successful synthetic resin, paving the way for modern plastics. Throughout the 20th century, the development of new resin types accelerated. Epoxy resins, introduced in the 1940s, became widely used in adhesives, coatings, and composite materials due to their exceptional strength and durability. Polyurethane resins emerged in the mid-20th century and are now commonly used in foams, elastomers, and coatings. Acrylic resins also gained prominence for their transparency and versatility in applications ranging from paints to dental materials. In recent decades, advancements in technology have led to the creation of specialized resins tailored for specific industries. For example, high-performance resins like carbon fiber-reinforced polymers (CFRP) are crucial in aerospace and automotive sectors due to their lightweight yet incredibly strong properties. Biodegradable resins have also been developed to address environmental concerns, offering sustainable alternatives for packaging and disposable products. The historical use and development of resin materials highlight a continuous quest for innovation and improvement. From ancient natural resins to modern synthetic polymers, each advancement has expanded the range of applications and improved performance characteristics. Today, resin materials play a vital role in various industries including construction, electronics, healthcare, and more, underscoring their importance as versatile and indispensable materials in modern society.
Common Applications Across Industries
Resin materials are versatile and widely used across various industries due to their unique properties and adaptability. In the **construction industry**, resin is often employed in flooring and coatings for its durability and resistance to wear and tear. It is also used in composite materials for structural components, such as beams and panels, offering lightweight yet strong alternatives to traditional materials. In **automotive manufacturing**, resin-based composites are integral for producing lightweight vehicle parts, including body panels and interior components, which help in reducing fuel consumption and enhancing overall vehicle performance. The **aerospace industry** also leverages resin composites for building aircraft and spacecraft components, where high strength-to-weight ratios are crucial. The **medical field** utilizes resin in medical devices, implants, and diagnostic equipment due to its biocompatibility and resistance to sterilization processes. Dental applications include resin-based composites for fillings and restorations, offering aesthetic and functional benefits. In **electronics**, epoxy resins are commonly used as encapsulants to protect electronic components from environmental factors such as moisture and vibration. The **art and craft sector** also benefits from resin, with artists using it to create intricate sculptures, jewelry, and other decorative items due to its ability to be molded into various shapes and colors. Additionally, **industrial manufacturing** relies on resin for producing molds, tooling, and other machinery parts that require high precision and durability. The **marine industry** uses fiberglass-reinforced resin composites for boat hulls and other marine structures because of their resistance to corrosion and water damage. Overall, the diverse applications of resin materials across these industries highlight their versatility, strength, and adaptability, making them an essential component in modern manufacturing processes.
Types of Resin Materials
Resin materials are versatile and widely used in various industries due to their unique properties and applications. This article delves into three primary types of resin: epoxy, polyurethane, and acrylic. Each type has distinct characteristics that make them suitable for different uses. Epoxy resin, known for its durability and chemical resistance, is often used in construction, automotive, and electronics. Polyurethane resin offers flexibility and impact resistance, making it ideal for applications such as coatings, adhesives, and foams. Acrylic resin, with its transparency and UV stability, is commonly found in industrial coatings, dental materials, and 3D printing. Understanding these types of resin is crucial for selecting the right material for specific projects. In this article, we will explore each type in detail, starting with epoxy resin and its characteristics and uses. --- **Epoxy Resin: Characteristics and Uses**
Epoxy Resin: Characteristics and Uses
Epoxy resin is a versatile and highly sought-after type of resin material, renowned for its exceptional mechanical properties and diverse applications. **Characteristics:** Epoxy resin is a two-part system consisting of an epoxy resin and a hardener, which when mixed together, undergo a chemical reaction known as curing. This process results in a rigid, three-dimensional structure that exhibits excellent strength, durability, and resistance to chemicals, heat, and impact. Epoxy resins are also known for their low shrinkage during curing, which minimizes the risk of cracks and ensures dimensional stability. Additionally, they offer good electrical insulation properties and can be formulated to meet specific requirements such as transparency, flexibility, or high thermal resistance. **Uses:** The broad range of applications for epoxy resin stems from its unique combination of physical and chemical attributes. In **industrial settings**, epoxy resins are widely used as adhesives for bonding metals, plastics, and other materials due to their high bonding strength and resistance to environmental factors. They are also employed in the manufacture of composite materials like carbon fiber reinforced polymers (CFRP) used in aerospace and automotive industries. **Construction** benefits from epoxy resins as they are used in flooring systems, coatings for concrete surfaces, and as a binder in aggregate-based flooring materials due to their durability and resistance to wear. In **electronics**, epoxy resins serve as encapsulants for electronic components, protecting them from moisture, dust, and mechanical stress. They are also used in the production of printed circuit boards (PCBs) where they provide insulation between conductive layers. **Artistic applications** include casting sculptures, jewelry making, and creating decorative items like tabletops and countertops because of their ability to be colored and finished to a high gloss. Furthermore, epoxy resins are used in **marine** environments for boat building and repair due to their water resistance and bonding capabilities with various substrates. In **medical fields**, epoxy resins are utilized in dental restorations and orthopedic implants due to their biocompatibility and mechanical strength. Additionally, they are used in medical device manufacturing where sterilization is required without compromising material integrity. Overall, the versatility of epoxy resin makes it an indispensable material across multiple industries, offering a balance of performance characteristics that meet a wide range of needs.
Polyurethane Resin: Advantages and Applications
Polyurethane resin stands out as a versatile and highly sought-after material due to its numerous advantages and diverse applications. One of the primary benefits of polyurethane resin is its exceptional durability and resistance to wear, tear, and chemical corrosion. This makes it an ideal choice for industrial and commercial uses where longevity is crucial. Additionally, polyurethane resin exhibits excellent mechanical properties, including high tensile strength, elasticity, and impact resistance, which are essential for applications requiring robust performance. In terms of applications, polyurethane resin is widely used in various industries. In the automotive sector, it is utilized for producing flexible foams for car seats and rigid foams for insulation and structural components. The construction industry leverages polyurethane resin for creating durable coatings, adhesives, and sealants that enhance the lifespan of buildings and infrastructure. It is also a key material in the manufacturing of furniture and bedding due to its ability to form flexible foams that provide comfort and support. Furthermore, polyurethane resin plays a significant role in the medical field. It is used in the production of medical devices such as wound dressings, implantable devices, and surgical instruments due to its biocompatibility and resistance to sterilization processes. The electronics industry also benefits from polyurethane resin as it is used for encapsulating electronic components to protect them from environmental factors like moisture and vibration. Moreover, polyurethane resin is a popular choice among artists and hobbyists due to its ease of use and versatility. It can be formulated to have different properties such as transparency, color, and texture, making it suitable for casting, molding, and other creative projects. In the field of renewable energy, polyurethane resin is used in wind turbine blades and solar panels due to its ability to withstand harsh environmental conditions. Another significant advantage of polyurethane resin is its environmental sustainability. Modern formulations of polyurethane resin are designed to be more eco-friendly, with some versions being biodegradable or made from renewable resources. This shift towards sustainability makes polyurethane resin an attractive option for companies looking to reduce their environmental footprint. In summary, polyurethane resin's combination of durability, mechanical strength, and versatility makes it a valuable material across various industries. Its wide range of applications, from industrial manufacturing to artistic endeavors, underscores its importance as a key component in modern technology and everyday life. As part of the broader category of resin materials, polyurethane resin continues to evolve with advancements in technology, ensuring it remains a critical material for future innovations.
Acrylic Resin: Properties and Industrial Uses
Acrylic resin, a versatile and widely used synthetic polymer, is renowned for its exceptional properties and diverse industrial applications. It is derived from acrylic acid or its derivatives, such as acrylates and methacrylates, which are polymerized to form a robust and flexible material. One of the key properties of acrylic resin is its transparency and clarity, making it an ideal choice for applications requiring optical purity. Additionally, it exhibits high impact resistance, chemical stability, and excellent UV resistance, which enhances its durability in various environments. In terms of industrial uses, acrylic resin is a cornerstone in several sectors. In the automotive industry, it is used in the production of automotive coatings and adhesives due to its superior weathering resistance and adhesion properties. The construction industry leverages acrylic resin for sealants, caulks, and concrete repair materials because of its strong bonding capabilities and resistance to environmental degradation. The electronics sector also benefits from acrylic resin, which is used in the manufacture of insulating materials, encapsulants, and adhesives due to its electrical insulation properties and thermal stability. Furthermore, acrylic resin plays a crucial role in the medical field as a component in dental materials, such as dentures and implants, owing to its biocompatibility and mechanical strength. In the realm of art and design, acrylic resin is a favorite among artists and craftsmen for creating sculptures, jewelry, and other decorative items due to its ease of manipulation, color stability, and glossy finish. Moreover, it is used extensively in 3D printing technologies as a resin material for producing detailed models with high precision. The packaging industry utilizes acrylic resin for coating and laminating various substrates to enhance their barrier properties against moisture and gases. Its use in water treatment plants is also significant, where it serves as a flocculant to improve water clarity by aggregating suspended particles. Overall, the unique combination of physical and chemical properties makes acrylic resin an indispensable material across a broad spectrum of industries, from automotive and construction to electronics, medical, art, and packaging. Its versatility, durability, and performance characteristics ensure that it remains a preferred choice for numerous applications where reliability and quality are paramount.
Manufacturing and Processing of Resin
The manufacturing and processing of resin involve a complex series of steps that transform raw materials into versatile, high-quality products. At the heart of this process are three critical phases: the selection and understanding of raw materials and chemical composition, the various manufacturing processes such as casting and molding, and the post-processing techniques including curing, finishing, and quality control. Each phase is integral to producing resins that meet specific industrial standards and applications. Beginning with the raw materials and chemical composition, it is essential to understand the properties and interactions of the components involved. This foundational knowledge sets the stage for effective manufacturing processes, whether through casting, molding, or other methods. Finally, post-processing techniques ensure that the final product meets the required specifications and quality standards. By delving into these three key areas, we can gain a comprehensive understanding of how resin is manufactured and processed. Let's start by examining the raw materials and chemical composition that form the basis of resin production.
Raw Materials and Chemical Composition
Raw materials and chemical composition are crucial elements in the manufacturing and processing of resin. Resin, a versatile material used in various industries, is typically derived from a combination of organic and synthetic components. The primary raw materials include monomers such as styrene, ethylene, propylene, and vinyl chloride, which are often combined with other additives like plasticizers, fillers, and stabilizers to enhance the resin's properties. The chemical composition of resin can vary significantly depending on its intended application. For instance, epoxy resins are formed through the reaction of epoxide groups with hardeners, resulting in a strong and durable material commonly used in adhesives and coatings. Polyethylene and polypropylene resins, on the other hand, are produced through the polymerization of ethylene and propylene monomers, respectively, and are widely used in packaging and consumer goods due to their flexibility and resistance to chemicals. Phenolic resins, another type, are synthesized from phenol and formaldehyde, offering excellent heat resistance and electrical insulation properties, making them ideal for electrical components and automotive parts. The specific chemical composition can be tailored to achieve desired physical and mechanical properties such as tensile strength, impact resistance, and thermal stability. In addition to these primary components, various additives are incorporated to improve the performance of the resin. These include catalysts to speed up polymerization reactions, antioxidants to prevent degradation from oxidation, and pigments or dyes for coloration. The precise formulation of these raw materials and additives is critical as it directly influences the final product's quality and functionality. Understanding the raw materials and chemical composition is essential for manufacturers as it allows them to control the production process effectively. This includes optimizing reaction conditions, selecting appropriate processing techniques such as extrusion or injection molding, and ensuring compliance with safety and environmental regulations. By carefully managing these aspects, manufacturers can produce high-quality resin materials that meet specific industry standards and customer requirements. In summary, the selection and combination of raw materials along with their chemical composition play a pivotal role in determining the characteristics and applications of resin. This knowledge is fundamental for efficient manufacturing and processing, enabling the creation of diverse resin products that cater to various industrial needs.
Manufacturing Processes: Casting, Molding, and More
Manufacturing processes such as casting, molding, and others play a crucial role in the production of resin materials. **Casting** involves pouring liquid resin into a mold, where it hardens to form the desired shape. This method is particularly useful for creating complex geometries and small batches. **Molding**, on the other hand, can be further divided into several techniques. **Injection Molding** is a high-volume process where molten resin is injected into a mold under pressure, ideal for mass-producing parts with precise dimensions. **Compression Molding** involves placing resin between two mold halves and applying pressure to shape it, often used for thermosetting resins. **Transfer Molding** is similar but uses a transfer ram to push the resin into the mold, reducing waste and improving part quality. In addition to these methods, **Extrusion** is another key process where resin is melted and forced through a die to create continuous profiles like pipes, tubes, or sheets. **Blow Molding** is used for producing hollow objects such as bottles and containers by inflating a molten resin tube within a mold. **Rotational Molding** (or rotomolding) involves rotating a mold filled with resin to evenly distribute the material, commonly used for large, hollow items like tanks and playground equipment. **3D Printing** has also become a significant manufacturing process for resin materials, allowing for the creation of highly complex and customized parts layer by layer. This additive manufacturing technique is particularly beneficial for prototyping and small-scale production due to its flexibility and precision. Each of these manufacturing processes offers unique advantages depending on the specific requirements of the product being made. For instance, casting is ideal for intricate designs, while injection molding excels in high-volume production with tight tolerances. Understanding these different techniques is essential for optimizing the manufacturing and processing of resin materials to achieve desired properties and functionalities. By selecting the appropriate method, manufacturers can ensure that their resin products meet the necessary standards of quality, durability, and performance.
Post-Processing Techniques: Curing, Finishing, and Quality Control
Post-processing techniques are crucial steps in the manufacturing and processing of resin materials, ensuring the final product meets desired standards of quality, durability, and aesthetic appeal. **Curing** is a fundamental post-processing technique that involves exposing the resin to specific conditions such as heat, light, or chemicals to initiate a chemical reaction that hardens the material. This process can be achieved through various methods including UV curing, thermal curing, or chemical curing, each tailored to the specific type of resin being used. For instance, UV curing is commonly used for photopolymers where exposure to ultraviolet light triggers polymerization. **Finishing** techniques follow curing and are designed to enhance the surface quality and appearance of the resin product. This may include sanding to smooth out rough edges, polishing to achieve a glossy finish, or applying coatings to protect the surface from environmental factors. Chemical treatments can also be applied to improve adhesion properties or to introduce specific functionalities such as hydrophobicity or conductivity. Additionally, techniques like painting or dyeing can be employed to add color and visual appeal. **Quality Control** is an integral part of post-processing, ensuring that every product meets the required specifications and standards. This involves a series of inspections and tests to verify dimensions, surface finish, mechanical properties, and other critical attributes. Visual inspection under magnification can help identify defects such as bubbles, cracks, or uneven curing. Mechanical testing may include tensile strength, impact resistance, and hardness tests to ensure the product's performance under various conditions. Chemical analysis can also be conducted to verify the material's composition and purity. Incorporating advanced technologies like 3D scanning and computer vision into quality control processes allows for more precise and efficient evaluation of resin products. These tools enable real-time monitoring and detection of defects, facilitating immediate corrective actions during production. Furthermore, data analytics from these inspections can provide valuable insights into process optimization, helping manufacturers refine their techniques to achieve higher consistency and quality in their resin products. Overall, post-processing techniques such as curing, finishing, and quality control are essential for transforming raw resin into a high-quality final product that meets industry standards and customer expectations. By carefully executing these steps, manufacturers can ensure their resin products exhibit superior performance, durability, and aesthetic appeal, making them suitable for a wide range of applications from industrial components to consumer goods.