What Is A Mechanical Mixture

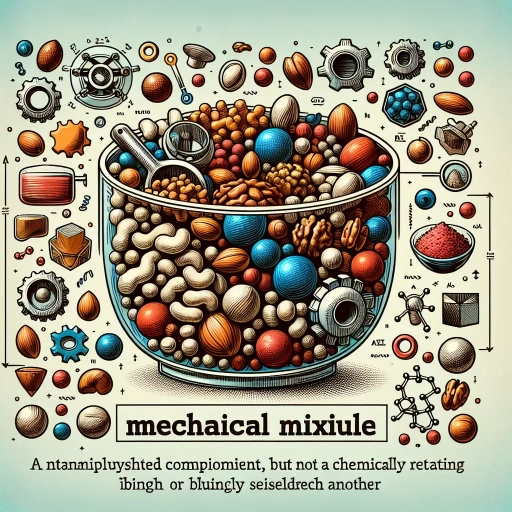
In the realm of materials science and engineering, understanding the nature of mixtures is crucial for various applications, from pharmaceuticals to construction materials. A mechanical mixture, also known as a physical mixture, is a blend of two or more substances that retain their chemical identities. Unlike chemical mixtures, where compounds react to form new substances, mechanical mixtures involve the simple physical blending of components. This article delves into the intricacies of mechanical mixtures, starting with a detailed **Definition and Concept of Mechanical Mixtures**, where we explore the fundamental principles and characteristics that define these blends. We will then examine **Types and Examples of Mechanical Mixtures**, highlighting diverse applications across different industries. Finally, we will discuss **Properties and Behavior of Mechanical Mixtures**, shedding light on how the physical properties of individual components influence the overall performance of the mixture. By grasping these concepts, readers will gain a comprehensive understanding of mechanical mixtures and their significance in various fields. Let us begin by defining what constitutes a mechanical mixture and its underlying concept.
Definition and Concept of Mechanical Mixtures
Mechanical mixtures, a fundamental concept in materials science and chemistry, represent a blend of two or more substances that retain their chemical identities. This concept is pivotal in understanding various industrial and natural processes. To delve into the intricacies of mechanical mixtures, it is essential to explore their historical context and development, which have shaped our current understanding. Additionally, examining the key characteristics and distinctions of mechanical mixtures helps in distinguishing them from other types of mixtures, such as solutions and alloys. Finally, grasping the scientific terminology and nomenclature associated with these mixtures is crucial for accurate communication and analysis. By understanding these aspects, we can appreciate the complexity and significance of mechanical mixtures in both historical and contemporary contexts. Let us begin by tracing the historical context and development of mechanical mixtures, which have evolved significantly over time, influencing numerous scientific and technological advancements.
Historical Context and Development
The concept of mechanical mixtures has a rich historical context that spans centuries, evolving from simple observations to sophisticated scientific understanding. The earliest recorded understanding of mixtures dates back to ancient civilizations, where alchemists and philosophers like Aristotle and Epicurus discussed the nature of matter and its combinations. However, it wasn't until the 17th and 18th centuries that the scientific method began to shape our understanding of mixtures. Chemists such as Antoine Lavoisier and Joseph Proust laid foundational principles by identifying elements and compounds, distinguishing between chemical and physical changes. In the 19th century, the work of scientists like John Dalton and Amedeo Avogadro further refined these concepts. Dalton's atomic theory posited that elements are composed of small, indivisible particles called atoms, which could combine in whole number ratios to form compounds. This theory provided a framework for understanding how different substances could be mixed without undergoing chemical reactions, thus forming mechanical mixtures. The term "mechanical mixture" itself became more defined as scientists began to differentiate between homogeneous mixtures (solutions) and heterogeneous mixtures (suspensions and colloids). The late 19th and early 20th centuries saw significant advancements in physical chemistry, particularly with the development of phase theory by Willard Gibbs. Gibbs' work on thermodynamics and phase equilibria provided a rigorous mathematical framework for understanding how different components in a mixture interact and coexist. This theoretical groundwork was crucial for the development of modern materials science, where mechanical mixtures play a pivotal role in creating composite materials with tailored properties. In the 20th century, technological advancements allowed for the precise control and analysis of mixtures at the molecular level. Techniques such as chromatography, spectroscopy, and electron microscopy enabled scientists to study the composition and structure of mixtures in unprecedented detail. These tools have been instrumental in developing new materials with unique properties, such as nanocomposites and smart materials, which rely on the principles of mechanical mixtures. Today, the concept of mechanical mixtures is integral to various fields including materials science, pharmaceuticals, and environmental engineering. In materials science, researchers create advanced composites by combining different materials to achieve specific mechanical, thermal, or electrical properties. In pharmaceuticals, understanding mechanical mixtures is crucial for formulating drugs with optimal delivery characteristics. In environmental engineering, knowledge of mechanical mixtures helps in designing systems for pollution control and waste management. The historical development of the concept of mechanical mixtures reflects a gradual shift from empirical observations to a deep scientific understanding grounded in theoretical frameworks and supported by advanced technological tools. This evolution has not only expanded our knowledge but also enabled the creation of innovative materials and technologies that are essential to modern society. As research continues to advance, the concept of mechanical mixtures remains a cornerstone in various scientific disciplines, driving innovation and solving complex problems across multiple fields.
Key Characteristics and Distinctions
When delving into the concept of mechanical mixtures, it is crucial to understand their key characteristics and distinctions. A mechanical mixture, also known as a physical mixture, is a blend of two or more substances that retain their chemical identities and properties. Unlike chemical mixtures, where components react to form new compounds, mechanical mixtures involve the simple physical blending of different materials. One of the primary characteristics of mechanical mixtures is the presence of distinct phases or components that can be visually identified or separated through physical means such as filtration, sedimentation, or magnetic separation. For instance, a mixture of sand and iron filings is a mechanical mixture because the sand and iron filings maintain their individual properties and can be separated using a magnet. Another significant distinction lies in the uniformity of the mixture. Mechanical mixtures can be either homogeneous or heterogeneous. Homogeneous mixtures, like solutions where one substance is dissolved in another (e.g., sugar in water), appear uniform throughout, while heterogeneous mixtures (e.g., a suspension of solid particles in a liquid) exhibit visible differences in composition. The method of preparation also plays a critical role; mechanical mixtures are typically prepared by mechanical processes such as grinding, stirring, or shaking, rather than through chemical reactions. The physical properties of the components in a mechanical mixture are preserved, which is a key distinguishing feature from chemical mixtures. For example, in a mixture of salt and pepper, both retain their taste and texture despite being mixed together. This preservation of properties allows for easy identification and separation of the components based on their physical attributes. Furthermore, the stability of mechanical mixtures varies widely depending on the nature of the components involved. Some mechanical mixtures may settle over time due to differences in density (e.g., oil and water), while others remain stable indefinitely (e.g., a well-mixed suspension). Understanding these characteristics is essential for applications across various fields such as pharmaceuticals, where precise control over the composition and stability of mixtures is critical for drug efficacy and safety. In summary, the key characteristics and distinctions of mechanical mixtures revolve around their physical blending without chemical alteration, retention of component properties, potential for homogeneity or heterogeneity, and variable stability. These features underscore the importance of recognizing mechanical mixtures as distinct entities within the broader context of mixtures and solutions. By grasping these nuances, one can better appreciate the role and significance of mechanical mixtures in both everyday life and specialized scientific contexts.
Scientific Terminology and Nomenclature
Scientific terminology and nomenclature are the backbone of precise communication in the scientific community, particularly when discussing complex concepts such as mechanical mixtures. The use of standardized terms ensures clarity and consistency, allowing researchers and scientists to convey ideas accurately and avoid misunderstandings. In the context of mechanical mixtures, understanding the specific vocabulary is crucial for defining and conceptualizing these mixtures. Mechanical mixtures, also known as physical mixtures or blends, are composed of two or more substances that are not chemically combined but are instead physically combined. The key terms here include "mechanical," indicating the physical nature of the combination, and "mixture," signifying the blending of different components. Each component retains its chemical identity and properties, unlike in chemical mixtures where compounds are formed through chemical reactions. The nomenclature for mechanical mixtures involves describing the composition and structure of the blend. For instance, terms like "suspension," "colloid," and "solution" are used to describe different types of mechanical mixtures based on the size of the dispersed particles and the nature of the dispersion medium. A suspension contains larger particles that settle over time, while a colloid has particles that remain suspended due to their smaller size and interactions with the medium. Solutions, on the other hand, involve particles at the molecular or ionic level, fully dissolved in the solvent. Understanding these terms is essential for accurately describing and analyzing mechanical mixtures. For example, in pharmaceuticals, knowing whether a drug is delivered as a suspension or solution can affect its efficacy and stability. Similarly, in materials science, distinguishing between different types of mechanical mixtures helps in designing materials with specific properties. The International Union of Pure and Applied Chemistry (IUPAC) plays a significant role in standardizing scientific terminology, including that related to mechanical mixtures. IUPAC guidelines ensure that scientists worldwide use consistent language, facilitating international collaboration and communication. This standardization also aids in education by providing clear definitions that students can rely on as they learn about various scientific concepts. In summary, scientific terminology and nomenclature are vital tools for defining and understanding mechanical mixtures. By using precise terms such as "suspension," "colloid," and "solution," scientists can accurately describe these mixtures and their properties. This clarity is crucial for advancing research, ensuring effective communication among scientists, and applying knowledge in practical fields such as medicine and materials science. The adherence to standardized terminology not only enhances the rigor of scientific discourse but also fosters a global community of researchers who can collaborate seamlessly across linguistic and cultural boundaries.
Types and Examples of Mechanical Mixtures
Mechanical mixtures, also known as physical mixtures, are combinations of two or more substances that retain their chemical identities. These mixtures are crucial in various aspects of our lives, from everyday applications to industrial processes. Understanding the different types of mechanical mixtures is essential for appreciating their diverse roles. This article delves into the distinctions between homogeneous and heterogeneous mixtures, highlighting their unique characteristics and examples. It also explores common examples of mechanical mixtures in everyday life, such as the air we breathe and the soil we walk on. Additionally, we examine the significant industrial applications and uses of these mixtures, including their role in manufacturing and engineering. By grasping these concepts, we can better appreciate the complexity and utility of mechanical mixtures. To begin, let's first differentiate between homogeneous and heterogeneous mixtures, as this fundamental distinction underpins the broader understanding of mechanical mixtures.
Homogeneous vs. Heterogeneous Mixtures
In the realm of mechanical mixtures, understanding the distinction between homogeneous and heterogeneous mixtures is crucial for grasping their properties and applications. A **homogeneous mixture** is characterized by its uniform composition throughout, meaning that the components are evenly distributed at a molecular or atomic level. This uniformity ensures that any sample taken from the mixture will have the same properties as the whole. A classic example of a homogeneous mixture is air, which is a blend of gases such as nitrogen, oxygen, and trace amounts of other gases. Another example is sugar dissolved in water, where the sugar molecules are dispersed evenly throughout the solution. Homogeneous mixtures can be further divided into solutions and colloids; solutions involve the dissolution of one substance in another (like sugar in water), while colloids consist of particles that are larger than molecules but smaller than what can be seen with the naked eye (such as milk). On the other hand, **heterogeneous mixtures** exhibit non-uniform composition, with distinct phases or components that can be visually distinguished. These mixtures do not have a uniform distribution of their constituents, and samples taken from different parts may have different properties. A quintessential example of a heterogeneous mixture is sand in water. Here, the sand particles settle at the bottom of the container and do not dissolve in the water, creating distinct layers. Another common example is fruit salad, where different fruits retain their individual identities and textures within the mixture. Heterogeneous mixtures can also include suspensions (like mud in water) and emulsions (such as mayonnaise), where one liquid is dispersed in another but remains distinct. The differences between these two types of mixtures are not just theoretical; they have practical implications in various fields. For instance, in chemistry and pharmaceuticals, homogeneous mixtures are often preferred because their uniformity ensures consistent properties and reactions. In contrast, heterogeneous mixtures are commonly used in construction (e.g., concrete) and food processing (e.g., salad dressings), where the distinct phases provide specific textures and functionalities. Understanding these distinctions is essential for predicting the behavior and potential uses of mechanical mixtures. Whether it's the uniformity of a homogeneous mixture or the distinct phases of a heterogeneous one, recognizing these characteristics allows scientists and engineers to tailor their applications to meet specific needs and achieve desired outcomes. This knowledge also underscores the versatility of mechanical mixtures, highlighting how different combinations of substances can yield a wide range of materials with unique properties and applications.
Common Examples in Everyday Life
In everyday life, mechanical mixtures are ubiquitous and play a crucial role in various aspects of our daily routines. One of the most common examples is the air we breathe, which is a mixture of gases such as nitrogen, oxygen, carbon dioxide, and trace amounts of other gases. This mechanical mixture is essential for human respiration and supports life on Earth. Another example is soil, which is a complex mixture of minerals, organic matter, water, and air. Soil's composition varies widely depending on its location and is crucial for plant growth and agricultural productivity. Food items also frequently involve mechanical mixtures. For instance, trail mix is a blend of nuts, seeds, dried fruits, and sometimes chocolate or other sweet ingredients. Each component retains its individual properties but together forms a tasty and nutritious snack. Similarly, granola is a mixture of rolled oats, nuts, seeds, and sometimes dried fruits or chocolate chips, baked together to create a crunchy breakfast or snack option. In the realm of construction and engineering, concrete is a prime example of a mechanical mixture. It consists of cement, water, aggregate (such as gravel or sand), and sometimes admixtures like fly ash or silica fume. Each component maintains its distinct characteristics but combines to form a strong and durable building material. Even personal care products often involve mechanical mixtures. Cosmetics like face powder or foundation are blends of various powders and pigments mixed with binders and other additives to achieve the desired texture and color. These mixtures allow for a wide range of shades and finishes to suit different skin types and preferences. Furthermore, pharmaceuticals frequently rely on mechanical mixtures to deliver medications effectively. For example, some tablets or capsules contain a mixture of active ingredients along with excipients such as fillers, binders, and lubricants. These excipients help in the manufacturing process and ensure the medication is released properly in the body. Lastly, household cleaning products often consist of mechanical mixtures designed to tackle specific cleaning tasks. Laundry detergents, for instance, are blends of surfactants, builders, enzymes, and other additives that work together to remove stains and clean fabrics without damaging them. These examples illustrate how mechanical mixtures are integral to various aspects of our daily lives—from the air we breathe to the food we eat and the products we use. Each component within these mixtures retains its unique properties while contributing to the overall functionality and effectiveness of the final product. Understanding these mixtures can provide insights into their applications and importance in our everyday world.
Industrial Applications and Uses
Industrial applications and uses of mechanical mixtures are diverse and critical across various sectors, highlighting their versatility and importance. In the construction industry, mechanical mixtures such as concrete and asphalt are fundamental. Concrete, a mixture of cement, water, aggregate (sand or gravel), and sometimes admixtures, is used in building foundations, walls, and infrastructure projects due to its strength and durability. Asphalt, a blend of bitumen, aggregate, and sand, is widely used for road surfaces and parking lots because of its flexibility and resistance to weather conditions. In the pharmaceutical industry, mechanical mixtures are essential for producing uniform drug formulations. For instance, tablets and capsules often contain a mixture of active pharmaceutical ingredients (APIs) and excipients like fillers, binders, and lubricants. These mixtures ensure consistent dosage and bioavailability of the medication. Similarly, in the food industry, mechanical mixtures are used to create uniform blends of ingredients in products such as cereals, snack foods, and baking powders. This ensures consistent taste, texture, and nutritional content. The aerospace and automotive sectors also rely heavily on mechanical mixtures. Composite materials like carbon fiber reinforced polymers (CFRP) are mechanical mixtures of carbon fibers and polymer resin, offering high strength-to-weight ratios that are crucial for lightweight yet robust components in aircraft and vehicles. Additionally, brake pads and linings are mechanical mixtures of various materials including metals, ceramics, and polymers, designed to provide optimal friction and wear resistance. In the agricultural sector, fertilizers and pesticides often come in the form of mechanical mixtures. These blends ensure that the active ingredients are evenly distributed, enhancing their effectiveness and reducing environmental impact. Furthermore, in the cosmetics industry, products such as face powders and eyeshadows are mechanical mixtures of pigments, binders, and fillers that provide consistent color and texture. The manufacturing of paints and coatings also involves mechanical mixtures. Paints are typically blends of pigments, binders, solvents, and additives that must be mixed precisely to achieve the desired color, finish, and durability. Similarly, in the electronics industry, solder pastes used for surface mount technology (SMT) are mechanical mixtures of solder particles, fluxes, and other additives that facilitate reliable connections between components. In summary, mechanical mixtures play a vital role in numerous industrial applications by providing consistent properties and performance. Their use spans from construction materials to pharmaceuticals, food products, aerospace components, agricultural chemicals, cosmetics, paints, and electronic materials. The ability to tailor these mixtures to specific requirements makes them indispensable in modern manufacturing processes.
Properties and Behavior of Mechanical Mixtures
Mechanical mixtures, composed of two or more distinct phases, exhibit a complex interplay of properties and behaviors that are crucial for understanding their performance and applications. These mixtures can be analyzed through several key lenses: their physical properties and phase separation, chemical stability and reactivity, and thermodynamic principles and equilibrium. The physical properties of mechanical mixtures, such as density, viscosity, and surface area, are significantly influenced by the characteristics of each component and their interactions. Phase separation, a common phenomenon in these mixtures, can lead to variations in these physical properties over time. Additionally, the chemical stability and reactivity of the components play a vital role in determining the long-term viability and potential transformations within the mixture. Finally, thermodynamic principles govern the equilibrium states of these mixtures, dictating how they will behave under different conditions. By examining these aspects, we can gain a comprehensive understanding of mechanical mixtures. Let us first delve into the physical properties and phase separation, which form the foundational basis for understanding these complex systems.
Physical Properties and Phase Separation
In the context of mechanical mixtures, understanding physical properties and phase separation is crucial for predicting and controlling the behavior of these composite materials. Physical properties such as density, viscosity, and thermal conductivity are often determined by the individual components and their proportions within the mixture. For instance, in a mixture of sand and water, the overall density will be influenced by the relative amounts of each component. However, when these components have significantly different physical properties, phase separation can occur, leading to distinct phases within the mixture. Phase separation arises due to differences in intermolecular forces between the components, causing them to segregate into separate phases. This phenomenon is commonly observed in liquid-liquid mixtures where two immiscible liquids, such as oil and water, separate into distinct layers. Similarly, in solid-solid mixtures like sand and gravel, particles may settle or segregate based on size and density differences. The process of phase separation can be influenced by various factors including temperature, pressure, and the presence of surfactants or other additives that alter interfacial tensions. The behavior of mechanical mixtures during phase separation is also influenced by kinetic factors such as diffusion rates and gravitational forces. For example, in a suspension of particles in a fluid (like mud), particles may settle over time due to gravity if the fluid's viscosity is low enough to allow for sedimentation. Conversely, if the fluid's viscosity is high or if there are stabilizing agents present (such as polymers), particles may remain dispersed. Understanding these principles is essential for various industrial applications. In pharmaceuticals, ensuring uniform distribution of active ingredients in a mixture is critical for efficacy and safety; phase separation could lead to inconsistent dosing. In construction materials like concrete, controlling the phase separation of cement paste from aggregate particles is vital for achieving desired strength and durability. Additionally, in environmental engineering, managing phase separation in wastewater treatment helps in efficient removal of contaminants. From a theoretical perspective, models such as the Gibbs free energy model can be used to predict the likelihood and extent of phase separation based on thermodynamic principles. These models help in designing mixtures with specific properties by selecting components that minimize or maximize phase separation depending on the application. In conclusion, physical properties and phase separation are fundamental aspects that govern the behavior of mechanical mixtures. By understanding these phenomena and their influencing factors, engineers and scientists can design and optimize composite materials for a wide range of applications, ensuring desired performance characteristics while mitigating potential issues related to phase instability. This knowledge not only enhances the functionality of mechanical mixtures but also contributes to advancements in various fields where these materials are crucial.
Chemical Stability and Reactivity
Chemical stability and reactivity are crucial factors in understanding the properties and behavior of mechanical mixtures. A mechanical mixture, also known as a physical mixture, is a blend of two or more substances that retain their chemical identities and do not undergo any chemical reaction to form a new compound. The stability and reactivity of these components can significantly influence the overall characteristics and performance of the mixture. Chemical stability refers to the resistance of a substance to undergo chemical changes under given conditions. In a mechanical mixture, each component maintains its inherent stability unless external factors such as temperature, pressure, or the presence of catalysts induce a reaction. For instance, mixing sulfur and carbon black to create a mechanical mixture for use in rubber production does not alter their individual stabilities; however, when heated during the vulcanization process, these components can react with other additives to form cross-links that enhance the rubber's durability. Reactivity, on the other hand, pertains to the tendency of substances to participate in chemical reactions. In mechanical mixtures, reactivity can be both beneficial and detrimental. For example, in pharmaceutical formulations, certain excipients may be chosen for their inertness to ensure that they do not react with the active ingredients, thereby maintaining the efficacy and stability of the drug. Conversely, in some industrial applications like explosives or propellants, high reactivity is desired; here, mechanical mixtures are designed to maximize the interaction between components upon ignition or detonation. The interplay between stability and reactivity is particularly important when considering the long-term storage and handling of mechanical mixtures. Substances with high reactivity may require special storage conditions to prevent unintended reactions that could lead to degradation or even safety hazards. For instance, mixing oxidizers with fuels in certain proportions can create highly reactive mixtures that are prone to ignition; thus, such mixtures must be stored in controlled environments to mitigate risks. Understanding the chemical stability and reactivity of components in mechanical mixtures also aids in predicting their behavior under various environmental conditions. This knowledge is essential for optimizing the performance of products such as paints, adhesives, and composite materials where the interaction between different phases can affect properties like strength, durability, and color retention. In summary, the chemical stability and reactivity of components within mechanical mixtures play pivotal roles in determining their overall properties and behavior. By carefully selecting and managing these factors, manufacturers can create products with desired attributes while ensuring safety and reliability. This nuanced understanding is critical for advancing various technologies that rely on the precise control of material interactions at a molecular level.
Thermodynamic Principles and Equilibrium
Thermodynamic principles play a crucial role in understanding the properties and behavior of mechanical mixtures. At the heart of these principles lies the concept of equilibrium, which is essential for predicting the stability and interactions within a mixture. Thermodynamics, the study of heat, work, and energy, provides a framework to analyze how components in a mechanical mixture interact and reach a state of balance. When considering a mechanical mixture, it is important to distinguish between the thermodynamic equilibrium of the individual components and the overall mixture. Thermodynamic equilibrium occurs when the system's properties no longer change with time, indicating that the rates of forward and reverse processes are equal. For a mechanical mixture, this means that each component must be in its own thermodynamic equilibrium state, but the mixture as a whole may not necessarily be in chemical equilibrium since it does not involve chemical reactions. The Gibbs Free Energy (ΔG) is a key thermodynamic parameter that determines the spontaneity of processes and the stability of phases within a mixture. A negative ΔG indicates a spontaneous process, while a positive ΔG suggests non-spontaneity. In the context of mechanical mixtures, ΔG helps predict whether components will separate or remain mixed under given conditions. For instance, if ΔG is negative for the mixing process, it implies that mixing is thermodynamically favorable. Another critical aspect is the concept of entropy (S), which measures disorder or randomness. According to the second law of thermodynamics, entropy tends to increase over time in an isolated system. In mechanical mixtures, entropy changes can influence phase separation or mixing behavior. For example, if mixing increases entropy significantly due to increased disorder among molecules, it can drive the formation of a stable mixture. Phase diagrams are also invaluable tools for understanding equilibrium in mechanical mixtures. These diagrams graphically represent the equilibrium states of different phases (solid, liquid, gas) as functions of temperature and composition. By analyzing phase diagrams, one can determine under what conditions a mechanical mixture will form distinct phases or remain homogeneous. Furthermore, thermodynamic principles guide our understanding of interfacial phenomena in mechanical mixtures. Interfaces between different components can significantly affect the overall behavior of the mixture due to interfacial tension and adsorption phenomena. These interfacial interactions can be quantified using thermodynamic models such as the Gibbs adsorption isotherm, which relates surface tension changes to adsorption at interfaces. In summary, thermodynamic principles provide a robust framework for understanding how mechanical mixtures behave and reach equilibrium states. By considering Gibbs Free Energy, entropy changes, phase diagrams, and interfacial phenomena, one can predict whether components will mix or separate under various conditions. This knowledge is crucial for designing and optimizing mechanical mixtures in various industrial applications such as materials science, pharmaceuticals, and food technology. Understanding these thermodynamic principles ensures that the resulting mixtures exhibit desired properties and stability over time.