What Is Dekton

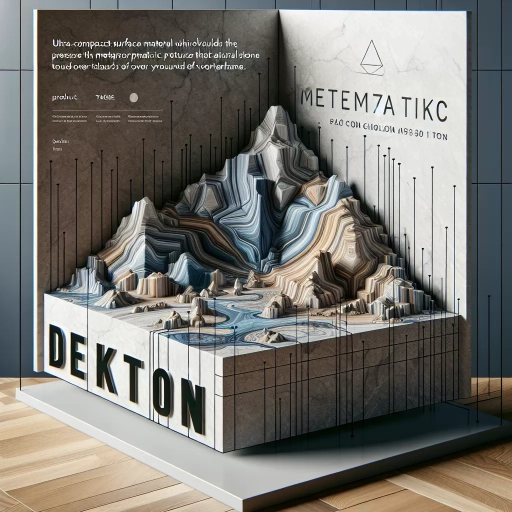
In the realm of modern construction and design, innovative materials are continually reshaping the landscape. Among these, Dekton stands out as a cutting-edge surface material that has garnered significant attention for its durability, versatility, and aesthetic appeal. This article delves into the world of Dekton, exploring its fundamental characteristics, the intricate manufacturing process that sets it apart, and the diverse applications where it excels. We will begin by introducing Dekton, uncovering its unique properties and how it compares to other surface materials. Next, we will delve into the manufacturing process of Dekton, highlighting the advanced technologies and techniques that contribute to its exceptional quality. Finally, we will examine the various applications and benefits of Dekton, from residential kitchens to commercial spaces, showcasing why it has become a preferred choice for architects, designers, and homeowners alike. Let's start our journey into the world of Dekton by first understanding what it is and what makes it so distinctive. **Introduction to Dekton**.
Introduction to Dekton
In the realm of modern construction and design, few materials have garnered as much attention and acclaim as Dekton. This high-performance surface material has revolutionized the way architects, designers, and homeowners approach projects, offering a blend of durability, aesthetics, and versatility. To fully appreciate Dekton's impact, it is essential to delve into its definition and origin, understanding how it came to be and what sets it apart from other materials. Additionally, exploring its key characteristics will reveal why Dekton has become a preferred choice for various applications, from countertops to facades. Finally, examining the historical context in which Dekton was developed provides insight into the technological advancements and market demands that led to its creation. By understanding these facets, we can gain a comprehensive view of what makes Dekton such a valuable asset in contemporary design. Let us begin by defining what Dekton is and tracing its origins.
Definition and Origin
**Definition and Origin** Dekton, a revolutionary material in the world of architecture and design, is defined as a high-performance, ultra-compact surface engineered by the Spanish company Cosentino. This innovative product combines the best qualities of natural stone, such as durability and aesthetic appeal, with the technological advancements of modern manufacturing. Dekton's origin dates back to 2013 when Cosentino, known for its pioneering work in quartz surfaces with Silestone, embarked on a mission to create a material that could withstand the demands of both residential and commercial environments. Through extensive research and development, Cosentino's scientists and engineers perfected a unique blend of raw materials—quartz, porcelain, and glass—using an advanced technological process called TSP (Technology of Sintered Particles). This proprietary method involves subjecting the raw materials to extremely high pressure and temperature conditions, resulting in a dense and non-porous surface that is resistant to scratches, heat, and stains. The birth of Dekton marked a significant milestone in the industry, offering architects, designers, and homeowners a versatile and reliable material for various applications, from countertops and flooring to facades and furniture. With its inception, Dekton has set new standards for performance and design flexibility, making it an indispensable choice for those seeking both functionality and elegance in their projects.
Key Characteristics
Dekton, a cutting-edge material developed by Cosentino, boasts several key characteristics that set it apart from other surfaces in the market. **Durability** is one of its most compelling attributes; Dekton is highly resistant to scratches, heat, and stains, making it an ideal choice for both residential and commercial applications. This resilience is due to its unique composition, which includes a blend of quartz, porcelain, and glass, combined with advanced manufacturing techniques. Another significant characteristic of Dekton is its **versatility**. Available in a wide range of colors and patterns, Dekton can be tailored to fit any design aesthetic. Whether you're looking for a sleek, modern look or a more traditional appearance, Dekton offers the flexibility to match your vision. Additionally, its large format slabs (up to 320 cm x 144 cm) allow for seamless installations with minimal joints, enhancing the visual appeal of any space. **Low Maintenance** is another hallmark of Dekton. Unlike natural stone surfaces that require periodic sealing, Dekton is non-porous and does not need any special care or maintenance. This makes it perfect for busy households and commercial environments where ease of upkeep is crucial. Furthermore, its non-porous nature also makes it highly resistant to bacteria and other microorganisms, contributing to a cleaner and healthier environment. Dekton also stands out for its **UV Resistance**. Unlike some other materials that may fade or discolor over time when exposed to sunlight, Dekton retains its color and appearance even in outdoor settings. This stability ensures that your surfaces look as good as new for years to come, regardless of the environmental conditions. Moreover, Dekton is **Eco-Friendly**. Made from a combination of natural materials and advanced technology, Dekton is produced using sustainable practices that minimize environmental impact. The manufacturing process involves recycling waste materials and using energy-efficient methods, aligning with the growing demand for green building solutions. In terms of **Thermal Shock Resistance**, Dekton excels by withstanding extreme temperature changes without compromising its integrity. This means you can place hot pans directly on the surface without worrying about damage—a feature that is particularly beneficial in kitchen settings. Lastly, Dekton's **Hygiene** benefits are noteworthy. Its non-porous surface prevents the absorption of liquids and substances, reducing the risk of contamination and making it easier to clean. This characteristic is especially important in areas where hygiene is paramount, such as healthcare facilities and food preparation spaces. Overall, Dekton's unique blend of durability, versatility, low maintenance requirements, UV resistance, eco-friendliness, thermal shock resistance, and hygiene benefits make it an exceptional material for various applications. Whether you're designing a kitchen countertop, bathroom vanity, or outdoor patio area, Dekton offers unparalleled performance and aesthetic appeal that can enhance any space.
Historical Context
**Historical Context** To fully appreciate the innovative material known as Dekton, it is essential to delve into its historical context. Dekton, a high-performance surface material, was first introduced by Cosentino Group in 2013. However, its development is rooted in decades of technological advancements and market demands. The journey begins with the early 20th century when natural stone and ceramics were the primary materials for countertops and surfaces. These materials, while aesthetically pleasing, had significant limitations such as fragility, porosity, and maintenance requirements. The mid-20th century saw the rise of engineered quartz surfaces, which offered improved durability and low maintenance compared to natural stone. Companies like Caesarstone and Silestone pioneered this market segment, providing consumers with a more practical alternative. However, these materials still had their drawbacks, including heat sensitivity and potential for scratches. In the early 2000s, there was a growing demand for surfaces that combined the aesthetic appeal of natural stone with the durability of engineered materials. This demand was driven by both residential and commercial sectors seeking high-performance solutions that could withstand heavy use without compromising on design. Cosentino Group, a Spanish company with a long history in the stone industry dating back to 1979, recognized this gap in the market. Leveraging their extensive experience in natural stone and quartz surfaces, they embarked on a research and development project aimed at creating a revolutionary new material. After years of intensive research and collaboration with leading scientists and engineers, Dekton was born. Dekton's unique composition involves a combination of inorganic materials such as quartz, feldspar, and porcelain, which are subjected to an advanced technological process known as Particle Sintering Technology (PST). This process involves subjecting the raw materials to extremely high pressure and temperature conditions, resulting in a compact and homogeneous surface that is highly resistant to scratches, heat, stains, and UV light. The launch of Dekton marked a significant milestone in the evolution of surface materials. It not only addressed the limitations of previous materials but also set new standards for performance and sustainability. Dekton's versatility has made it a favorite among architects, designers, and homeowners alike, suitable for various applications ranging from kitchen countertops to exterior facades. Understanding the historical context behind Dekton's development highlights the continuous quest for innovation within the industry. It underscores how technological advancements are driven by consumer needs and market demands. As we explore what Dekton is and its myriad applications, it becomes clear that this material represents a culmination of decades-long efforts to create surfaces that are both beautiful and functional.
Manufacturing Process of Dekton
The manufacturing process of Dekton, a cutting-edge surface material, is a testament to modern industrial innovation. This process is underpinned by three critical components: the selection and use of high-quality raw materials, the integration of advanced technological innovations, and stringent quality control measures. At the heart of Dekton's production lies the careful selection of raw materials, which includes a blend of quartz, feldspar, and other minerals. These materials are chosen for their durability and aesthetic appeal, ensuring that the final product meets the highest standards of performance and design. The technological innovations employed in the manufacturing process further enhance the material's properties, making it resistant to scratches, heat, and stains. Additionally, rigorous quality control measures are implemented at every stage to guarantee consistency and excellence in each slab produced. By understanding these key elements, we can appreciate the meticulous craftsmanship and scientific precision that go into creating Dekton. Let us begin by examining the raw materials used in this sophisticated process.
Raw Materials Used
The manufacturing process of Dekton, a cutting-edge surfacing material, relies heavily on the selection and integration of high-quality raw materials. Dekton is produced by Cosentino, a leading company in the field of surface design, using a proprietary technology known as Particle Sintering Technology (PST). This innovative process involves the combination of inorganic raw materials such as quartz, feldspar, and porcelain, along with other minerals and recycled materials. These components are meticulously chosen for their durability, resistance to heat and scratches, and aesthetic appeal. Quartz, one of the primary raw materials, contributes significantly to Dekton's hardness and stability. Feldspar, another key component, enhances the material's resistance to thermal shock and chemical attacks. Porcelain adds a layer of sophistication and elegance to the final product while ensuring it remains non-porous and easy to clean. Additionally, Dekton incorporates recycled materials as part of its commitment to sustainability, making it an environmentally friendly choice for architects and designers. The PST process involves subjecting these raw materials to extremely high temperatures and pressures in a controlled environment. This sintering process compacts the particles into a dense, homogeneous mass without the need for resins or other binders, resulting in a material that is both durable and versatile. The absence of resins also means that Dekton is free from volatile organic compounds (VOCs), making it a healthier option for indoor environments. The careful selection and precise blending of these raw materials ensure that Dekton exhibits exceptional performance characteristics. It is highly resistant to scratches, heat, and stains, making it ideal for use in various applications including kitchen countertops, flooring, and cladding. Moreover, Dekton's non-porous nature prevents the absorption of liquids, reducing the risk of bacterial growth and simplifying maintenance. In summary, the raw materials used in the production of Dekton are crucial to its superior quality and functionality. By combining quartz, feldspar, porcelain, and recycled materials through the advanced PST process, Cosentino creates a material that not only meets but exceeds industry standards for durability and aesthetics. This meticulous attention to detail in raw material selection underscores why Dekton has become a preferred choice among professionals in the design and construction sectors.
Technological Innovations
Technological innovations have revolutionized the manufacturing process of Dekton, a high-performance, ultra-compact surface material. At the heart of Dekton's production lies advanced technology that ensures precision, efficiency, and sustainability. The manufacturing process begins with a sophisticated blend of raw materials such as quartz, porcelain, and glass, which are carefully selected for their durability and aesthetic appeal. These materials are then subjected to a proprietary process known as TSP (Technology of Sintered Particles), developed by Cosentino, the creators of Dekton. This cutting-edge technology involves subjecting the raw materials to extremely high temperatures and pressures, mimicking the natural processes that create stone over millions of years but in a fraction of the time. The TSP process is facilitated by state-of-the-art machinery that ensures uniformity and consistency across each slab. Advanced computer-controlled systems monitor every stage of production, from material mixing to final curing, ensuring that each Dekton slab meets stringent quality standards. Additionally, robotic arms and automated handling systems streamline the manufacturing process, reducing human error and increasing productivity. Sustainability is another key area where technological innovations play a crucial role in Dekton's production. The use of recycled materials and eco-friendly practices minimizes environmental impact. For instance, Dekton incorporates recycled glass and porcelain, reducing waste and conserving natural resources. Furthermore, the energy-efficient machinery and optimized production lines help in lowering carbon emissions. Innovative technologies also enhance the aesthetic and functional qualities of Dekton. Advanced digital printing techniques allow for intricate designs and patterns to be applied directly onto the surface, offering a wide range of styles and finishes that cater to diverse architectural and design needs. Moreover, the material's resistance to heat, scratches, and stains is significantly improved through nanotechnology treatments that create a durable, non-porous surface. The integration of Industry 4.0 principles further elevates Dekton's manufacturing process. Real-time data analytics and IoT sensors enable real-time monitoring and optimization of production parameters, ensuring continuous improvement in quality and efficiency. This data-driven approach also facilitates predictive maintenance, reducing downtime and enhancing overall plant reliability. In conclusion, technological innovations are the backbone of Dekton's manufacturing process, driving excellence in every aspect from raw material selection to final product quality. By leveraging advanced technologies such as TSP, automation, sustainability practices, digital printing, nanotechnology treatments, and Industry 4.0 principles, Cosentino has set a new benchmark for ultra-compact surfaces that combine unparalleled performance with stunning aesthetics. This synergy of technology and craftsmanship positions Dekton as a leader in the world of architectural surfaces.
Quality Control Measures
In the manufacturing process of Dekton, a cutting-edge surfacing material known for its durability and aesthetic appeal, quality control measures play a pivotal role in ensuring the final product meets the highest standards. Dekton, produced by Cosentino, is a hybrid surface that combines the benefits of natural stone, quartz, and ceramic materials. To maintain its reputation for excellence, Cosentino implements rigorous quality control protocols at every stage of production. From raw material selection to the final product inspection, each step is meticulously monitored. The process begins with the careful selection of raw materials—quartz, feldspar, and porcelain—which are sourced from trusted suppliers to ensure consistency and purity. These materials are then subjected to thorough testing for chemical composition and physical properties to guarantee they meet the specified criteria. Once the raw materials are verified, they are mixed and processed using advanced technology. The proprietary TSP (Technology of Sinterized Particles) process involves subjecting the mixture to extremely high temperatures and pressures, resulting in a compact and durable material. During this phase, continuous monitoring ensures that the conditions are precisely controlled to achieve uniformity and consistency across each slab. After sintering, the slabs undergo various treatments such as polishing and finishing. Here again, quality control is paramount; each slab is inspected for any defects or imperfections using advanced optical and tactile inspection systems. Any slabs that do not meet the stringent quality standards are removed from the production line. Furthermore, Dekton's performance characteristics such as resistance to scratches, stains, and heat are tested in accordance with international standards. These tests simulate real-world conditions to ensure that Dekton can withstand the demands of daily use in residential and commercial settings. In addition to these technical checks, Cosentino also conducts regular audits and certifications by third-party organizations to validate their quality control processes. This includes compliance with ISO 9001 for quality management systems and other industry-specific certifications that underscore their commitment to excellence. The final step involves packaging and shipping, where each slab is carefully handled and protected to prevent damage during transit. Before dispatching the products to distributors and retailers, a final quality check is performed to ensure that every slab meets the expected standards. In summary, the manufacturing process of Dekton is characterized by an unwavering focus on quality control. From raw material selection through to the final inspection, every stage is meticulously managed to produce a product that is not only visually stunning but also exceptionally durable and reliable. This rigorous approach to quality control is what sets Dekton apart in the market and makes it a preferred choice for architects, designers, and homeowners alike.
Applications and Benefits of Dekton
Dekton, a cutting-edge surfacing material, has revolutionized various aspects of construction and design. Its versatility and superior qualities make it an ideal choice for architects, designers, and homeowners alike. This article delves into the multifaceted applications and benefits of Dekton, exploring three key areas: Architectural and Design Uses, Performance and Durability, and Environmental Impact. In terms of Architectural and Design Uses, Dekton offers unparalleled flexibility and aesthetic appeal. Its wide range of colors and textures allows for seamless integration into any design scheme, from modern to traditional. Whether used for countertops, flooring, or exterior cladding, Dekton's unique properties enhance the visual and functional aspects of any space. Moving forward, we will first examine how Dekton's architectural and design capabilities are transforming the way we build and design spaces, providing endless possibilities for creative expression and functional efficiency.
Architectural and Design Uses
Dekton, a cutting-edge ultracompact surface material, has revolutionized the architectural and design landscape with its versatility, durability, and aesthetic appeal. In the realm of architectural applications, Dekton is a go-to choice for both interior and exterior projects due to its exceptional resistance to heat, scratches, and stains. Architects leverage Dekton for cladding facades, creating visually striking exteriors that are not only beautiful but also resilient against harsh weather conditions. Its UV resistance ensures that the material retains its color and integrity over time, making it an ideal option for outdoor applications such as patios, walkways, and pool decks. In interior design, Dekton's adaptability shines through its use in various elements like countertops, flooring, and wall coverings. Its non-porous nature makes it a hygienic choice for kitchens and bathrooms, where cleanliness is paramount. Designers appreciate the wide range of colors and textures available in Dekton, allowing them to create cohesive and stylish spaces that reflect their clients' unique tastes. The material's ability to mimic natural stone without the maintenance hassles has made it a favorite among homeowners and commercial property owners alike. Moreover, Dekton's sustainability credentials are a significant draw for architects and designers committed to green building practices. Made from a combination of quartz, porcelain, and glass, Dekton is an eco-friendly alternative to traditional materials. Its production process involves recycling waste materials, reducing environmental impact while ensuring high-quality performance. This aligns perfectly with modern design principles that prioritize both aesthetics and sustainability. From a functional standpoint, Dekton's durability and low maintenance requirements make it an excellent choice for high-traffic areas such as commercial spaces, restaurants, and public buildings. Its resistance to chemicals and heavy use means that it can withstand the demands of busy environments without compromising on appearance or performance. Additionally, Dekton's ease of installation and repair further enhances its appeal; it can be easily integrated into existing designs or used as part of new construction projects. The aesthetic versatility of Dekton is another key factor in its widespread adoption within architectural and design communities. Available in a diverse palette of colors and patterns inspired by nature—such as marble, granite, and wood—Dekton allows designers to achieve sophisticated looks that are both timeless and contemporary. This flexibility enables architects to create cohesive designs that blend seamlessly with other materials while adding a touch of elegance to any space. In summary, Dekton's architectural and design uses are multifaceted and far-reaching. Its unique blend of durability, sustainability, and aesthetic appeal makes it an indispensable tool for architects and designers seeking to create functional yet beautiful spaces. Whether used in exterior cladding or interior design elements, Dekton consistently delivers high-quality results that meet the demands of modern building practices while enhancing the visual appeal of any project.
Performance and Durability
**Performance and Durability** Dekton, a cutting-edge surfacing material, stands out for its exceptional performance and durability, making it an ideal choice for various applications. Engineered by Cosentino, Dekton combines the best qualities of natural stone, glass, and porcelain to create a product that is both aesthetically pleasing and highly resilient. One of its key strengths is its resistance to scratches and abrasions. Unlike many other materials, Dekton does not require sealing due to its non-porous nature, which significantly reduces maintenance needs. This characteristic also makes it highly resistant to stains, ensuring that it retains its appearance over time without the need for frequent cleaning or protective treatments. In terms of thermal resistance, Dekton excels by withstanding extreme temperatures without compromising its integrity. It can handle direct heat from appliances like stovetops and ovens without sustaining damage, making it perfect for kitchen countertops. Additionally, its UV resistance ensures that the material does not fade or discolor when exposed to sunlight, maintaining its vibrant colors and patterns even in outdoor settings. Dekton's durability is further enhanced by its high density and hardness. It is resistant to impact and can withstand heavy use without showing signs of wear and tear. This makes it an excellent option for high-traffic areas such as commercial spaces, public buildings, and busy households. The material's dimensional stability means that it does not expand or contract significantly with temperature changes, reducing the likelihood of cracks or breaks. Another significant advantage of Dekton is its chemical resistance. It is impervious to acidic substances and other chemicals that could potentially damage other materials. This property makes it suitable for use in laboratories, hospitals, and other environments where exposure to harsh chemicals is common. The combination of these performance attributes—scratch resistance, thermal stability, UV resistance, high density, and chemical resistance—positions Dekton as a superior choice for various applications. Whether used in residential kitchens and bathrooms or in commercial settings such as restaurants and healthcare facilities, Dekton delivers unparalleled durability and reliability. Its ability to withstand the rigors of daily use while maintaining its appearance ensures that it remains a valuable investment for years to come. By integrating Dekton into your design, you can enjoy the benefits of a high-performance material that enhances both functionality and aesthetics.
Environmental Impact
When considering the applications and benefits of Dekton, a crucial aspect to highlight is its significant environmental impact. Dekton, a high-performance surface material developed by Cosentino, stands out not only for its aesthetic appeal and durability but also for its commitment to sustainability. Unlike natural stone, which often involves extensive quarrying and transportation processes that can harm ecosystems, Dekton is manufactured using a combination of natural minerals and advanced technology. This production process minimizes the extraction of raw materials from the earth, reducing the carbon footprint associated with traditional stone quarrying. Moreover, Dekton's manufacturing process incorporates recycled materials, further enhancing its eco-friendly credentials. The use of recycled content in Dekton reduces waste and conserves natural resources, aligning with global efforts to promote circular economy practices. Additionally, Dekton's long lifespan and resistance to wear and tear mean that it requires less frequent replacement compared to other surface materials. This longevity reduces the need for repeated production cycles, thereby lowering overall energy consumption and environmental degradation. Another key environmental benefit of Dekton is its non-toxic and non-reactive nature. Unlike some other materials that may leach chemicals into the environment over time, Dekton maintains its integrity without posing any health risks or contributing to pollution. This makes it an ideal choice for both residential and commercial applications where indoor air quality is a priority. In terms of end-of-life management, Dekton's recyclable composition ensures that it can be reused or repurposed at the end of its service life, minimizing landfill waste. This forward-thinking approach to material lifecycle management underscores Cosentino's dedication to responsible manufacturing practices. Furthermore, Dekton's versatility allows it to be used in various applications such as countertops, flooring, and cladding, which can help in reducing the overall material usage in construction projects. By offering a single material that can serve multiple purposes, Dekton helps in streamlining construction processes and minimizing waste generation. In conclusion, the environmental impact of Dekton is a compelling reason to consider this material for various applications. Its sustainable production process, recyclable content, long lifespan, non-toxic properties, and end-of-life recyclability make it an exemplary choice for those seeking to balance aesthetic appeal with environmental responsibility. As consumers become increasingly conscious of their ecological footprint, materials like Dekton are poised to play a significant role in shaping a more sustainable future for construction and design.