What Are The Two Types Of Whmis Training

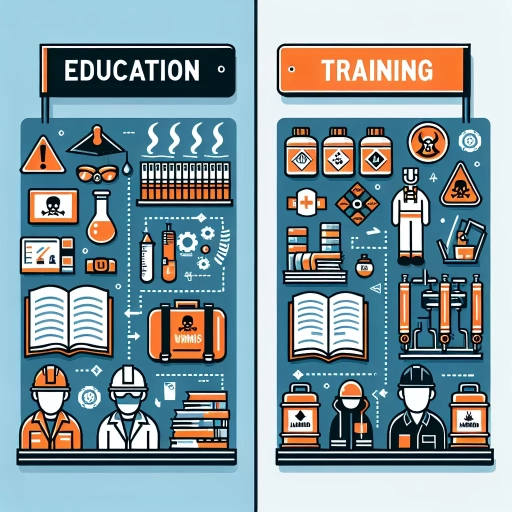
In the realm of workplace safety, the Workplace Hazardous Materials Information System (WHMIS) plays a crucial role in ensuring that employees are well-equipped to handle hazardous materials safely. WHMIS training is not a one-size-fits-all solution; it is tailored to meet specific needs through two distinct types: General WHMIS Training and Site-Specific WHMIS Training. Understanding these types is essential for effective implementation. This article will delve into the basics of WHMIS training, explore the differences between General and Site-Specific training, and discuss best practices for implementing these programs. By grasping these fundamental concepts, employers and employees can better navigate the complexities of hazardous material handling. To begin, it is vital to **Understand the Basics of WHMIS Training**, which sets the foundation for a comprehensive approach to workplace safety.
Understanding the Basics of WHMIS Training
Understanding the basics of WHMIS (Workplace Hazardous Materials Information System) training is crucial for ensuring a safe and compliant work environment. This comprehensive system is designed to protect workers from the dangers associated with hazardous materials. To grasp the full scope of WHMIS, it is essential to delve into three key areas: the definition and purpose of WHMIS, the legal requirements for WHMIS training, and the key components of WHMIS legislation. Firstly, understanding the definition and purpose of WHMIS sets the foundation for all subsequent knowledge. This involves recognizing how WHMIS classifies, labels, and communicates the hazards of chemical products in the workplace. Secondly, familiarizing oneself with the legal requirements for WHMIS training is vital to ensure compliance with regulatory standards. This includes knowing the mandatory training requirements and the frequency at which they must be updated. Lastly, exploring the key components of WHMIS legislation provides insight into the specific rules and guidelines that govern its implementation. By starting with a clear understanding of the definition and purpose of WHMIS, individuals can better appreciate its role in workplace safety and compliance. This foundational knowledge will serve as a stepping stone to understanding the broader legal and legislative aspects of WHMIS training. Therefore, let us begin by examining the definition and purpose of WHMIS in detail.
Definition and Purpose of WHMIS
**Understanding the Basics of WHMIS Training: Definition and Purpose of WHMIS** The Workplace Hazardous Materials Information System (WHMIS) is a comprehensive Canadian regulatory framework designed to ensure the safe handling, use, and disposal of hazardous materials in the workplace. Established under the Hazardous Products Act and the Controlled Products Regulations, WHMIS serves as a critical component of occupational health and safety policies. The primary purpose of WHMIS is to provide workers with essential information about the hazards associated with the chemicals they use, thereby enabling them to take necessary precautions to protect themselves and their colleagues. WHMIS achieves this through several key components: classification of hazardous products, labeling of containers, provision of safety data sheets (SDSs), and worker education and training. The classification system categorizes hazardous materials based on their physical and health hazards, ensuring that workers are aware of the specific risks involved. Labels on containers provide immediate visual warnings and instructions, while SDSs offer detailed information on safe handling practices, emergency procedures, and first aid measures. Worker training is central to WHMIS, as it equips employees with the knowledge and skills necessary to handle hazardous materials safely and respond effectively in case of emergencies. By mandating these measures, WHMIS aims to reduce workplace injuries and illnesses caused by exposure to hazardous substances. It also fosters a culture of safety awareness among workers, employers, and suppliers, promoting a collaborative approach to managing chemical hazards. Overall, WHMIS plays a vital role in safeguarding the health and well-being of Canadian workers by ensuring they have access to accurate and comprehensive information about the hazardous materials they encounter on the job. This foundational understanding is crucial for effective WHMIS training, which is divided into two main types: general WHMIS training and site-specific training. General training covers the basics of WHMIS, including hazard classification, labeling, and SDSs, while site-specific training focuses on the specific hazards and procedures relevant to an individual workplace. Both types of training are essential for ensuring that workers are adequately prepared to handle hazardous materials safely and responsibly.
Legal Requirements for WHMIS Training
**Legal Requirements for WHMIS Training** In Canada, the legal requirements for Workplace Hazardous Materials Information System (WHMIS) training are stringent and governed by federal and provincial regulations. The Hazardous Products Act and the Controlled Products Regulations, enforced by Health Canada, mandate that all employers ensure their workers are properly trained on WHMIS. Specifically, employers must provide training that covers the three main components of WHMIS: hazard classification, safety data sheets (SDSs), and labels. This training is crucial for ensuring that workers can safely handle hazardous materials and respond to emergencies. Under the law, employers are required to provide WHMIS training to all employees who work with or may be exposed to hazardous products. This includes not only those directly handling the materials but also those who may be in proximity to them. The training must be specific to the workplace and the types of hazardous products used there. Employers must also ensure that the training is updated whenever there are changes in the workplace or new hazardous products are introduced. Provincial and territorial occupational health and safety regulations also play a significant role in enforcing WHMIS training requirements. For example, provinces like Ontario and Alberta have their own legislation that complements federal laws, requiring employers to maintain records of employee training and ensure that workers understand the hazards associated with the products they use. Additionally, employers are responsible for ensuring that workers understand how to read and interpret SDSs and labels, which provide critical information about the safe handling, use, storage, and disposal of hazardous materials. This includes understanding the Globally Harmonized System of Classification and Labelling of Chemicals (GHS), which is now integrated into WHMIS 2015. Non-compliance with these legal requirements can result in significant fines and penalties. Therefore, it is imperative for employers to take WHMIS training seriously and ensure that all necessary steps are taken to protect their workers from the risks associated with hazardous materials. By adhering to these legal requirements, employers not only comply with the law but also contribute to a safer and healthier work environment.
Key Components of WHMIS Legislation
The Key Components of WHMIS (Workplace Hazardous Materials Information System) Legislation are crucial for ensuring the safe handling, use, and disposal of hazardous materials in Canadian workplaces. At its core, WHMIS is designed to protect workers from the dangers associated with hazardous chemicals. Here are the primary components: 1. **Classification**: This involves categorizing hazardous products based on their physical and health hazards. Products are classified into two main categories: physical hazards (e.g., flammable gases, oxidizing solids) and health hazards (e.g., toxic substances, carcinogens). 2. **Labels**: Hazardous products must be labeled with specific information to alert workers about the risks. Labels include the product identifier, hazard statements, precautionary statements, pictograms (symbols representing hazards), and supplier identifier. 3. **Safety Data Sheets (SDSs)**: These detailed documents provide comprehensive information about a hazardous product, including its composition, first aid measures, fire-fighting measures, accidental release measures, handling and storage, exposure controls/personal protection, physical and chemical properties, stability and reactivity, toxicological information, ecological information, disposal considerations, transport information, regulatory information, and other relevant data. 4. **Training**: Employers are required to provide education and training to workers on the safe handling of hazardous materials. This includes general WHMIS training as well as site-specific training tailored to the workplace. 5. **Program Implementation**: Employers must implement a WHMIS program that includes procedures for receiving, storing, handling, using, and disposing of hazardous products. This program must also ensure that all hazardous products are properly labeled and that SDSs are readily available. 6. **Compliance and Enforcement**: The legislation is enforced by Health Canada and provincial/territorial authorities. Employers who fail to comply with WHMIS requirements can face penalties and fines. Understanding these components is essential for effective WHMIS training, which is divided into two types: general WHMIS training that covers the basics of the legislation and site-specific training that addresses the specific hazards and procedures relevant to a particular workplace. By adhering to these key components, workplaces can significantly reduce the risks associated with hazardous materials and ensure a safer environment for all employees.
Types of WHMIS Training: General vs. Site-Specific
In the realm of workplace safety, understanding the different types of WHMIS (Workplace Hazardous Materials Information System) training is crucial for ensuring compliance and protecting employees. This article delves into the distinctions between General WHMIS Training and Site-Specific WHMIS Training, providing a comprehensive overview of each. We will first explore the General WHMIS Training Overview, which covers the foundational knowledge necessary for all workers handling hazardous materials. Next, we will examine the Site-Specific WHMIS Training Requirements, highlighting the unique needs and protocols that vary by workplace. Finally, we will discuss the Differences Between General and Site-Specific Training, clarifying how these two types of training complement each other to create a robust safety framework. By understanding these aspects, employers and employees can better navigate the complexities of WHMIS training, ensuring a safer and more informed work environment. Let's begin with a detailed look at General WHMIS Training Overview.
General WHMIS Training Overview
General WHMIS (Workplace Hazardous Materials Information System) training is a foundational component of workplace safety in Canada, designed to educate workers on the safe handling, use, and disposal of hazardous materials. This training is mandatory for all employees who work with or around hazardous products, ensuring they understand the risks associated with these substances and how to mitigate them. The core elements of General WHMIS training include understanding the WHMIS classification system, which categorizes hazardous products into six classes based on their physical and health hazards. Workers learn to identify and interpret the labels and Safety Data Sheets (SDSs) associated with these products, which provide critical information about safe handling practices, emergency procedures, and personal protective equipment requirements. Additionally, General WHMIS training covers the principles of safe work practices, such as proper storage, transportation, and disposal of hazardous materials. It also emphasizes the importance of reporting incidents and spills promptly to prevent further risks. By providing a comprehensive overview of WHMIS standards and best practices, General WHMIS training equips employees with the knowledge necessary to protect themselves and their colleagues from potential hazards in the workplace. This foundational training serves as a precursor to site-specific training, which tailors the information to the specific hazards and procedures relevant to each workplace environment. Overall, General WHMIS training is essential for maintaining a safe and compliant work environment where hazardous materials are present.
Site-Specific WHMIS Training Requirements
Site-Specific WHMIS Training is a tailored approach that focuses on the unique hazards and conditions present in a specific workplace. Unlike General WHMIS Training, which provides a broad overview of the Workplace Hazardous Materials Information System, Site-Specific Training delves into the specifics of how hazardous materials are handled, stored, and used within the particular workplace. This type of training is crucial because it addresses the unique risks associated with the specific chemicals and substances used on-site, ensuring that employees are fully aware of the potential dangers and know how to mitigate them effectively. For instance, in a manufacturing plant where various chemicals are used in different processes, Site-Specific WHMIS Training would cover the specific safety protocols for each chemical, including proper handling techniques, emergency response procedures, and the use of personal protective equipment (PPE). It would also include information on the location of safety data sheets (SDSs) and how to read and interpret them in the context of the workplace. This targeted approach ensures that employees are equipped with the knowledge and skills necessary to handle hazardous materials safely and efficiently in their specific work environment. Moreover, Site-Specific WHMIS Training often involves hands-on training and simulations to prepare employees for real-world scenarios. For example, in a laboratory setting, employees might participate in mock spill responses or practice using fire extinguishers on chemical fires. This practical training enhances their ability to respond correctly in emergency situations, thereby reducing the risk of accidents and injuries. Additionally, Site-Specific Training must be updated regularly to reflect any changes in the workplace, such as new chemicals being introduced or changes in processes. This ensures that the training remains relevant and effective over time. Employers are responsible for ensuring that all employees receive this type of training and that it is documented properly to comply with regulatory requirements. In summary, Site-Specific WHMIS Training is essential for ensuring workplace safety by providing employees with detailed knowledge and practical skills tailored to their specific work environment. It complements General WHMIS Training by addressing the unique hazards and procedures of the workplace, thereby enhancing overall safety and compliance.
Differences Between General and Site-Specific Training
When it comes to Workplace Hazardous Materials Information System (WHMIS) training, there are two distinct types: General and Site-Specific. Understanding the differences between these two is crucial for ensuring that workers are adequately prepared to handle hazardous materials safely. **General WHMIS Training** focuses on providing a broad foundation of knowledge about WHMIS. This type of training covers the basics of the WHMIS system, including the classification of hazardous products, the use and interpretation of safety data sheets (SDSs), and the understanding of labels on hazardous products. General training is typically standardized and can be applied across various workplaces because it does not address specific workplace conditions or procedures. It is essential for all workers who handle or may be exposed to hazardous materials, regardless of their job role or location. **Site-Specific WHMIS Training**, on the other hand, is tailored to the specific hazards and conditions present in a particular workplace. This type of training goes beyond the general knowledge by incorporating details about the specific hazardous materials used in that workplace, the unique risks associated with them, and the specific safety protocols and emergency procedures in place. Site-Specific training ensures that workers are aware of how to handle and respond to hazards in their immediate work environment. For example, it might include information on where to find SDSs, how to use personal protective equipment (PPE) specific to the site, and what steps to take in case of a spill or exposure. In summary, while General WHMIS Training provides a foundational understanding of hazardous materials and their handling, Site-Specific Training delves into the nuances of the specific workplace environment. Both types are complementary and necessary; General Training lays the groundwork, while Site-Specific Training ensures that workers are fully equipped to manage hazards effectively in their particular setting. Employers must ensure that their employees receive both types of training to maintain a safe and compliant work environment.
Implementation and Best Practices for WHMIS Training
Implementing effective WHMIS (Workplace Hazardous Materials Information System) training is crucial for ensuring the safety and well-being of employees in workplaces where hazardous materials are present. A comprehensive approach to WHMIS training involves several key components. First, **Developing a Comprehensive Training Program** is essential to cover all necessary aspects of WHMIS, including hazard identification, safety data sheets, and label requirements. This foundational step sets the stage for a robust training framework. Additionally, **Effective Delivery Methods for WHMIS Training** must be employed to engage learners and ensure knowledge retention. This includes leveraging various teaching techniques such as interactive sessions, simulations, and hands-on training. Finally, **Ensuring Compliance and Continuous Improvement** is vital to maintain the effectiveness of the training program over time, involving regular updates and audits to align with evolving regulations and best practices. By focusing on these areas, organizations can create a WHMIS training program that is both informative and engaging. Let's start by examining the critical steps involved in **Developing a Comprehensive Training Program**.
Developing a Comprehensive Training Program
Developing a comprehensive training program for WHMIS (Workplace Hazardous Materials Information System) is crucial for ensuring the safety and compliance of employees in workplaces where hazardous materials are present. This program should be structured to cover both theoretical knowledge and practical skills, addressing the two primary types of WHMIS training: General WHMIS Training and Workplace-Specific Training. **General WHMIS Training** focuses on providing a foundational understanding of WHMIS principles, including the classification of hazardous products, the use and interpretation of Safety Data Sheets (SDSs), and the identification and understanding of labels. This training ensures that all employees have a uniform baseline of knowledge regarding hazardous materials, regardless of their specific job roles. It typically includes modules on the WHMIS 2015 system, hazard classification, and the Globally Harmonized System of Classification and Labelling of Chemicals (GHS). **Workplace-Specific Training**, on the other hand, is tailored to the specific hazards and procedures relevant to each workplace. This type of training delves into the handling, storage, and emergency procedures for the particular hazardous materials used in that workplace. It involves practical demonstrations and hands-on training to ensure employees can safely manage and respond to potential hazards in their immediate work environment. This training also covers site-specific policies, procedures, and equipment usage. To implement these training programs effectively, several best practices should be followed: 1. **Needs Assessment**: Conduct a thorough needs assessment to identify the specific training requirements for different job roles within the organization. 2. **Clear Objectives**: Define clear learning objectives for both general and workplace-specific training to ensure that all necessary topics are covered. 3. **Engaging Content**: Use a variety of training methods such as videos, interactive modules, and hands-on exercises to keep the content engaging and retain employee interest. 4. **Regular Updates**: Regularly update the training content to reflect changes in regulations, new products, or updated procedures. 5. **Evaluation and Feedback**: Include evaluation mechanisms to assess employee understanding and gather feedback for continuous improvement of the training program. 6. **Record Keeping**: Maintain detailed records of employee training to ensure compliance with regulatory requirements and for future reference. By integrating these elements into a comprehensive training program, organizations can ensure that their employees are well-equipped to handle hazardous materials safely and effectively, thereby reducing workplace risks and enhancing overall safety culture.
Effective Delivery Methods for WHMIS Training
Effective delivery methods for WHMIS (Workplace Hazardous Materials Information System) training are crucial to ensure that employees understand and apply the necessary safety protocols when handling hazardous materials. Here are some high-impact methods: 1. **Interactive Online Modules**: Utilize interactive online training platforms that include quizzes, simulations, and gamification to engage learners. These modules can be accessed at any time, allowing employees to learn at their own pace and revisit material as needed. 2. **In-Person Training Sessions**: Conduct in-person training sessions where instructors can provide hands-on demonstrations and address questions directly. This method fosters a more personal connection and immediate feedback. 3. **Video-Based Training**: Employ video tutorials that visually demonstrate safe handling practices, emergency procedures, and the use of personal protective equipment (PPE). Videos can be particularly effective for visual learners. 4. **Workplace Simulations**: Organize workplace simulations where employees practice responding to scenarios involving hazardous materials. This experiential learning helps reinforce theoretical knowledge with practical application. 5. **Mobile Learning Apps**: Develop mobile learning apps that provide bite-sized training sessions, allowing employees to learn during breaks or downtime. These apps can also include push notifications for updates and reminders. 6. **Peer-to-Peer Training**: Encourage experienced employees to train their peers. This method leverages internal expertise and fosters a sense of community and shared responsibility for safety. 7. **Blended Learning**: Combine different delivery methods (e.g., online modules followed by in-person sessions) to cater to various learning styles and ensure comprehensive understanding. 8. **Regular Refresher Courses**: Schedule regular refresher courses to update employees on new regulations, products, or procedures. This ensures that knowledge remains current and relevant. 9. **Multilingual Support**: Provide training materials in multiple languages to accommodate diverse workforces, ensuring that all employees can understand and comply with WHMIS requirements. 10. **Feedback Mechanisms**: Implement feedback mechanisms such as surveys or quizzes to gauge the effectiveness of the training and identify areas for improvement. By incorporating these methods into your WHMIS training program, you can enhance employee engagement, retention of information, and overall workplace safety. Each method has its strengths, and a combination of several can create a robust and effective training strategy.
Ensuring Compliance and Continuous Improvement
Ensuring compliance and continuous improvement are crucial components of effective WHMIS (Workplace Hazardous Materials Information System) training. To maintain compliance, organizations must regularly review and update their training programs to align with the latest regulations and standards. This involves conducting periodic audits to ensure all employees have received the necessary training and that records are accurately maintained. Additionally, employers should establish clear policies and procedures for handling hazardous materials, which should be communicated clearly to all staff members. Continuous improvement is equally important and can be achieved through feedback mechanisms. Employers should solicit feedback from employees who have undergone WHMIS training to identify areas for enhancement. This feedback can help in refining the training content, delivery methods, and overall effectiveness of the program. Moreover, incorporating new technologies and best practices into the training can enhance engagement and retention rates among employees. For instance, using interactive modules, simulations, and real-world scenarios can make the training more engaging and relevant. Regular refresher training sessions are also essential to reinforce knowledge and address any new hazards or changes in workplace procedures. These sessions can be tailored to specific job roles or departments to ensure that the information remains relevant and applicable. Furthermore, involving subject matter experts in the development and delivery of WHMIS training can add credibility and depth to the program. Incorporating continuous improvement into WHMIS training also involves monitoring workplace incidents and near-misses related to hazardous materials. Analyzing these incidents can provide valuable insights into gaps in current training practices, allowing for targeted improvements. By fostering a culture of safety and continuous learning, organizations can not only ensure compliance but also reduce risks associated with hazardous materials, ultimately creating a safer and more efficient work environment. This holistic approach to WHMIS training ensures that employees are well-equipped to handle hazardous materials safely and responsibly, contributing to a safer workplace for everyone.