What Shrinks The More You Use It

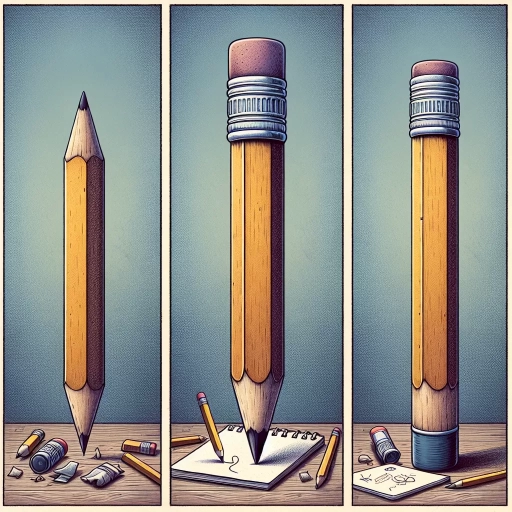
In the realm of materials science, there exists a fascinating phenomenon where certain materials shrink as they are used. This concept is not merely a curiosity but has significant implications across various industries, from textiles and construction to electronics and aerospace. Understanding why and how these materials shrink is crucial for optimizing their performance and longevity. This article delves into the intricacies of shrinking materials, exploring three key aspects: the fundamental concept behind shrinking materials, the types of materials that exhibit this behavior over time, and the factors that influence the rate of shrinkage, including temperature and heat exposure, moisture and humidity levels, and usage patterns and wear and tear. By grasping these elements, we can better appreciate the complexities involved and make informed decisions about material selection and usage. To begin, it is essential to **Understand the Concept of Shrinking Materials**, which forms the foundation for comprehending this intriguing phenomenon.
Understanding the Concept of Shrinking Materials
In the realm of materials science, the concept of shrinking materials is a fascinating and multifaceted topic that has garnered significant attention due to its diverse applications and underlying scientific principles. To fully grasp this phenomenon, it is essential to delve into its definition and examples, which illustrate the various forms and contexts in which shrinking materials occur. Understanding the scientific principles behind these materials is crucial, as it reveals the intricate mechanisms that drive their behavior. Furthermore, exploring the common applications of shrinking materials in everyday life highlights their practical significance and impact on our daily experiences. By examining these aspects, we can gain a comprehensive insight into the concept of shrinking materials, enabling us to appreciate their complexity and utility. This article aims to provide a detailed exploration of these key areas, ultimately leading to a deeper understanding of the concept of shrinking materials.
Definition and Examples
Understanding the concept of shrinking materials involves delving into the definitions and examples that illustrate this phenomenon. **Definition:** Shrinking materials are substances that reduce in size or volume when subjected to specific conditions, such as heat, light, or mechanical stress. This reduction can occur due to various physical or chemical changes within the material's structure. For instance, polymers like polyethylene and polypropylene can shrink when heated due to the relaxation of molecular chains, leading to a more compact arrangement. **Examples:** One of the most common examples is **thermoplastic shrink tubing**, widely used in electrical insulation. When heated, this tubing contracts to fit snugly around wires, providing a secure and protective covering. Another example is **shrink wrap**, a plastic film used to package goods. When exposed to heat, it shrinks tightly around the item it is covering, ensuring a secure and tamper-evident seal. In textiles, fabrics like wool and cotton can shrink when washed in hot water or dried at high temperatures due to the felting process in wool or the relaxation of fibers in cotton. In advanced materials science, **shape-memory alloys** (SMAs) also exhibit shrinking properties. These alloys can change shape in response to temperature changes and return to their original shape upon heating or cooling. For example, nitinol, a nickel-titanium alloy, is used in medical devices such as stents and orthodontic wires because it can be compressed and then expand to its original shape when heated. Additionally, certain types of **ceramics** and **composites** can shrink during the manufacturing process due to the removal of binders or solvents. This shrinkage is critical in achieving precise dimensions and desired properties in the final product. Understanding these examples helps in appreciating how different materials respond to various stimuli and how these properties can be harnessed for practical applications across diverse industries. In summary, the concept of shrinking materials encompasses a broad range of substances that undergo size reduction under specific conditions. By examining the definitions and examples of these materials, we gain insight into their unique properties and potential uses, which are crucial for innovation and problem-solving in fields such as engineering, manufacturing, and consumer goods production. This understanding not only enhances our ability to design and utilize these materials effectively but also opens up new avenues for research and development in material science.
Scientific Principles Behind Shrinking
The scientific principles behind shrinking materials are rooted in the fundamental properties of materials and their interactions with environmental factors. At the core, shrinking occurs due to changes in the material's structure or volume, often triggered by external stimuli such as temperature, humidity, or mechanical stress. For instance, polymers and fabrics can shrink when exposed to heat because the molecules within these materials gain kinetic energy and start vibrating more vigorously. This increased motion causes the polymer chains to contract and tighten, leading to a reduction in size. In the case of textiles, particularly those made from natural fibers like wool or cotton, shrinking is often a result of felting or relaxation of fibers. When these fibers are subjected to heat and moisture, they tend to felt together, causing the fabric to contract and become denser. This process is irreversible because once the fibers have bonded together, they cannot return to their original state without significant chemical or mechanical intervention. Another key principle involves the concept of thermodynamics. Many materials exhibit a phenomenon known as thermal contraction, where they shrink as they cool down. This is because the atoms or molecules in these materials move closer together as their kinetic energy decreases with lower temperatures. Conversely, some materials may expand when heated due to increased molecular motion but can revert to their original size upon cooling if no permanent structural changes occur. Additionally, materials science plays a crucial role in understanding shrinking phenomena. The crystalline structure of metals and alloys can change under different conditions, leading to variations in volume. For example, certain alloys may undergo phase transitions where their crystal structure changes from one form to another, resulting in changes in density and hence volume. Furthermore, the concept of viscoelasticity is important for understanding how some materials shrink over time. Viscoelastic materials exhibit both viscous and elastic characteristics; they can flow like liquids under prolonged stress but also return to their original shape when the stress is removed. However, repeated stress cycles can lead to permanent deformation and shrinkage as the material's internal structure adjusts to accommodate the external forces. In summary, the scientific principles behind shrinking materials encompass a range of physical and chemical processes influenced by factors such as temperature, humidity, mechanical stress, and material structure. Understanding these principles is essential for predicting and controlling the behavior of various materials in different applications, from textiles and polymers to metals and alloys. By grasping these underlying mechanisms, scientists and engineers can develop strategies to mitigate unwanted shrinkage or harness it for innovative purposes.
Common Applications in Everyday Life
The concept of shrinking materials, though seemingly counterintuitive, has numerous practical applications in everyday life. One of the most common examples is found in the realm of textiles. Fabrics like wool and cotton are known to shrink when exposed to heat or repeated washing, a phenomenon that can be both a nuisance and a benefit. For instance, pre-shrinking fabrics before manufacturing garments ensures that the final product will retain its size and shape over time, enhancing durability and fit. This process is particularly important for industries such as fashion and upholstery, where consistency in material dimensions is crucial. In the field of construction, materials like concrete and wood also exhibit shrinking properties as they dry or age. Understanding these changes is vital for architects and engineers who must account for these shrinkages to ensure structural integrity and prevent cracks or other defects. For example, concrete shrinkage can lead to significant issues if not properly managed; hence, techniques such as controlled curing and reinforcement with fibers are employed to mitigate these effects. Another significant application lies in the domain of electronics. Modern electronic devices often use materials that shrink or expand with temperature changes, affecting their performance and lifespan. For instance, thermal interface materials (TIMs) are designed to maintain contact between components despite thermal expansion and contraction, ensuring efficient heat dissipation and preventing damage from thermal stress. In healthcare, shrinking materials play a critical role in medical devices such as stents and implantable devices. These devices are often made from shape-memory alloys that can be compressed to a smaller size for easier insertion into the body and then expand to their original shape once in place. This technology allows for minimally invasive procedures, reducing recovery times and improving patient outcomes. Furthermore, in the automotive industry, materials like rubber and certain plastics exhibit shrinkage properties that must be considered during manufacturing. For example, tires are designed with specific tread patterns that account for the natural shrinkage of rubber over time, ensuring consistent traction and safety on the road. Lastly, even in everyday household items like kitchen utensils and cookware, understanding material shrinkage is important. Non-stick coatings on pans may degrade over time due to heat exposure, leading to a slight shrinkage that affects their non-stick properties. Recognizing these changes helps consumers maintain their cookware effectively. In summary, the concept of shrinking materials is not just a theoretical curiosity but has profound implications across various sectors of our daily lives. From textiles to electronics, construction to healthcare, and automotive to household items, understanding how materials shrink or expand is essential for designing reliable, efficient, and safe products. This knowledge enables us to create better products that meet our needs while minimizing potential drawbacks associated with material changes over time.
Materials That Shrink Over Time
Materials that shrink over time are a fascinating yet often overlooked phenomenon, impacting various industries and everyday life. This article delves into the intriguing world of shrinking materials, exploring three key categories: natural fibers and textiles, plastics and polymers, and metals under specific conditions. Natural fibers and textiles, such as cotton and wool, can shrink due to moisture and heat, affecting the fit and durability of clothing. Plastics and polymers, commonly used in packaging and consumer goods, may shrink as a result of thermal contraction or degradation. Metals, while generally stable, can also exhibit shrinkage under certain conditions like high temperatures or specific chemical treatments. Understanding these different types of shrinking materials is crucial for manufacturers, consumers, and researchers alike. By examining these categories in depth, we can better grasp the underlying mechanisms and practical implications of material shrinkage, ultimately enhancing our ability to predict and manage this phenomenon effectively. This article aims to provide a comprehensive overview, transitioning seamlessly into **Understanding the Concept of Shrinking Materials**.
Natural Fibers and Textiles
Natural fibers and textiles, derived from plants, animals, and minerals, have been integral to human civilization for millennia. These materials, such as cotton, wool, silk, and linen, offer unique properties that make them both versatile and sustainable. Cotton, for instance, is one of the most widely used natural fibers due to its breathability, softness, and durability. However, it is also known to shrink significantly when exposed to heat or repeated washing cycles. This shrinkage can be attributed to the fiber's natural tendency to contract when subjected to high temperatures or aggressive washing methods. Wool, another prominent natural fiber, is renowned for its warmth and insulation properties. Despite its resilience, wool fibers can also experience shrinkage, particularly if they are not treated with care. The felting process, which involves the matting and tangling of wool fibers, can lead to noticeable shrinkage. This phenomenon occurs because the scales on wool fibers interlock and contract when exposed to heat, agitation, or harsh detergents. Silk, a protein fiber produced by silkworms, is celebrated for its luxurious feel and lustrous appearance. While silk is generally more resistant to shrinkage compared to other natural fibers, it can still contract if not handled properly. High temperatures during washing or drying can cause silk fibers to tighten and lose their original dimensions. Linen, derived from the flax plant, is known for its strength and cooling properties. Although linen is less prone to shrinkage than other natural fibers, it can still experience some contraction over time. This is often due to the fiber's natural tendency to relax and settle after repeated use and washing. The inherent characteristics of these natural fibers mean that they can shrink over time with use, making them a prime example of materials that shrink the more you use them. Understanding these properties is crucial for maintaining the quality and longevity of textiles made from these fibers. Proper care, such as using cold water, mild detergents, and avoiding high heat during drying, can help minimize shrinkage and ensure that natural fiber textiles retain their original dimensions and functionality for a longer period. By appreciating the unique attributes of natural fibers and adopting appropriate care practices, consumers can enjoy the benefits of these sustainable materials while preserving their integrity over time.
Plastics and Polymers
Plastics and polymers are ubiquitous materials in modern life, known for their versatility, durability, and wide range of applications. However, one fascinating aspect of these materials is their tendency to shrink over time under certain conditions. This phenomenon is particularly relevant when discussing materials that shrink the more you use them. Polymers, the building blocks of plastics, are long chains of repeating molecular units. When these chains are subjected to stress, heat, or chemical exposure, they can undergo changes that lead to shrinkage. For instance, thermoplastics like polyethylene and polypropylene can shrink when exposed to high temperatures due to the relaxation of polymer chains. This process is often seen in plastic components used in automotive and aerospace industries where thermal cycling can cause dimensional changes. Another factor contributing to the shrinkage of plastics is the loss of volatile compounds such as solvents or plasticizers. These additives are commonly used to enhance the flexibility and processability of polymers but can evaporate over time, leading to a reduction in volume and subsequent shrinkage. This is particularly evident in materials like PVC (polyvinyl chloride), where the loss of plasticizers can result in a more brittle and shrunken product. Mechanical stress also plays a significant role in the shrinkage of plastics. When polymers are subjected to repeated loading and unloading cycles, they can undergo creep—a gradual deformation under constant stress—which may eventually lead to permanent shrinkage. This is a concern in applications such as medical devices and consumer electronics where consistent performance is crucial. Furthermore, environmental factors such as UV radiation and moisture can degrade polymer chains, causing them to break down and contract. This photochemical degradation is common in outdoor applications like plastic fencing or roofing materials, where prolonged exposure to sunlight can lead to significant shrinkage. Understanding the mechanisms behind plastic shrinkage is essential for material selection and design in various industries. By choosing the right type of polymer and considering the potential environmental and operational stresses it will face, engineers can mitigate unwanted shrinkage and ensure the long-term integrity of their products. In conclusion, while plastics and polymers offer numerous benefits due to their adaptability and strength, their propensity to shrink under various conditions must be carefully considered to optimize their performance over time.
Metals Under Specific Conditions
Metals, often perceived as rigid and unyielding, can exhibit surprising behaviors under specific conditions. When discussing materials that shrink over time, it is crucial to consider the unique properties of metals in various environments. For instance, certain metals undergo a phenomenon known as "thermal contraction," where they shrink as their temperature decreases. This is particularly relevant in cryogenic applications where metals like aluminum and titanium contract significantly when exposed to extremely low temperatures. Conversely, some metals expand when heated, but this expansion can be followed by contraction if the metal is then cooled rapidly or subjected to specific thermal cycles. Another condition that affects metal dimensions is mechanical stress. Metals can undergo plastic deformation when subjected to high pressures or stresses, leading to changes in their shape and size. For example, in the process of cold working, metals are deformed at room temperature, causing them to become denser and sometimes shrink in certain dimensions due to the realignment of their crystal structures. Additionally, fatigue and creep can cause metals to deform over time under cyclic loading or constant stress, respectively, leading to dimensional changes that might be interpreted as shrinkage. Chemical conditions also play a significant role in the dimensional stability of metals. Corrosion, for instance, can lead to the loss of material and thus a reduction in size. In marine environments, metals like steel and aluminum can corrode rapidly due to the presence of saltwater and oxygen, resulting in structural weakening and shrinkage. Similarly, in high-temperature environments where oxidation occurs, metals can form oxides that flake off over time, reducing their overall dimensions. Furthermore, the microstructural changes within metals can influence their dimensions. Phase transformations, such as those occurring in shape-memory alloys (SMAs), allow these metals to change shape in response to temperature changes. While SMAs are designed to recover their original shape upon heating or cooling, other metals may undergo irreversible phase transformations that result in permanent dimensional changes. In summary, metals can exhibit shrinkage under various specific conditions including thermal changes, mechanical stresses, chemical reactions, and microstructural transformations. Understanding these behaviors is essential for engineering applications where dimensional stability is critical. By recognizing how metals respond to different environments and treatments, engineers can design structures that account for these changes, ensuring the longevity and performance of materials in diverse settings. This nuanced understanding highlights the complex nature of metals and underscores their dynamic behavior beyond their commonly perceived rigidity.
Factors Influencing the Rate of Shrinkage
Temperature and Heat Exposure
Moisture and Humidity Levels
Usage Patterns and Wear and Tear
Shrinkage, a common phenomenon in various materials, is influenced by a multitude of factors that can significantly impact the durability and performance of products. Understanding these factors is crucial for manufacturers, engineers, and consumers alike. This article delves into three key elements that affect the rate of shrinkage: temperature and heat exposure, moisture and humidity levels, and usage patterns and wear and tear. Temperature and heat exposure can accelerate chemical reactions and alter material structures, leading to rapid shrinkage. Moisture and humidity levels play a critical role, as excessive moisture can cause materials to swell and subsequently shrink as they dry. Additionally, usage patterns and wear and tear contribute to the degradation of materials over time, influencing their shrinkage rates. By examining these factors in depth, we can gain a comprehensive understanding of the complex processes involved in material shrinkage, ultimately enhancing our ability to predict and mitigate its effects. This knowledge is essential for optimizing material performance and extending the lifespan of products, making it a vital aspect of understanding the concept of shrinking materials.
Temperature and Heat Exposure
Moisture and Humidity Levels
Usage Patterns and Wear and Te
The rate of shrinkage in materials, particularly textiles and fabrics, is significantly influenced by several key factors: temperature and heat exposure, moisture and humidity levels, and usage patterns along with wear and tear. **Temperature and Heat Exposure** play a crucial role as high temperatures can cause fibers to contract and lose their elasticity. When fabrics are exposed to heat, whether through washing, drying, or environmental conditions, the molecular structure of the fibers can change, leading to shrinkage. For instance, wool fibers are particularly susceptible to heat-induced shrinkage due to their natural crimp and elasticity. **Moisture and Humidity Levels** also have a profound impact on the shrinkage rate. High humidity can cause fibers to swell, while subsequent drying can lead to contraction and shrinkage. This is especially true for natural fibers like cotton and wool, which absorb moisture readily. In contrast, synthetic fibers may exhibit less shrinkage under similar conditions but can still be affected by extreme moisture fluctuations. **Usage Patterns and Wear and Tear** further exacerbate the shrinkage process. Frequent use of a fabric can lead to mechanical stress on the fibers, causing them to break down over time. Activities such as washing, drying, and ironing can all contribute to wear and tear, with each cycle potentially reducing the fabric's size. Additionally, how a fabric is used—whether it is stretched, pulled, or subjected to friction—can also influence its rate of shrinkage. For example, clothing items that are frequently worn and washed, such as t-shirts and socks, are more likely to shrink than less frequently used items like curtains or upholstery. Understanding these factors is essential for predicting and mitigating shrinkage in various materials. By controlling temperature and moisture levels during manufacturing and use, and by adopting gentle usage patterns, it is possible to minimize the effects of shrinkage. This knowledge is particularly valuable in industries where dimensional stability is critical, such as in textiles, construction materials, and even some types of electronics. Ultimately, recognizing the interplay between these factors allows for better material selection, care practices, and design considerations to ensure that products maintain their integrity over time.
Temperature and Heat Exposure
**Temperature and Heat Exposure** Temperature and heat exposure are critical factors that significantly influence the rate of shrinkage in various materials, particularly textiles and polymers. When materials are subjected to high temperatures, the molecular structure undergoes changes that can lead to shrinkage. For instance, in textiles, heat causes the fibers to contract and tighten, resulting in a reduction in size. This phenomenon is especially pronounced in natural fibers like wool and cotton, which are more susceptible to thermal shrinkage compared to synthetic fibers. The mechanism behind this process involves the breaking and reforming of hydrogen bonds within the fiber molecules. As heat is applied, these bonds break, allowing the fibers to relax and then re-form in a more compact arrangement. This re-arrangement leads to a permanent reduction in the material's dimensions. The extent of shrinkage can vary depending on the intensity and duration of the heat exposure. For example, a brief exposure to moderate heat might cause minimal shrinkage, while prolonged exposure to high temperatures can result in substantial dimensional changes. In addition to the type of fiber, the manufacturing process also plays a role in determining how much a material will shrink when exposed to heat. Pre-treatment processes such as sanforization, which involves shrinking the fabric before it is cut and sewn, can reduce the likelihood of significant shrinkage during subsequent heat exposure. However, materials that have not undergone such treatments are more likely to experience noticeable shrinkage when exposed to heat. Understanding the impact of temperature and heat exposure is crucial for maintaining the integrity and performance of materials over time. This knowledge is particularly important in industries such as textiles, where consistent sizing and fit are essential. By controlling temperature conditions during use and storage, users can mitigate the effects of heat-induced shrinkage, ensuring that materials retain their original dimensions and functionality. In the broader context of factors influencing shrinkage, temperature and heat exposure stand out as key variables that must be carefully managed to prevent unwanted dimensional changes.
Moisture and Humidity Levels
**Moisture and Humidity Levels** Moisture and humidity levels play a crucial role in determining the rate of shrinkage in various materials, particularly those that are sensitive to water content. When materials such as fabrics, wood, and certain plastics are exposed to high humidity or moisture, they tend to absorb water molecules. This absorption can lead to swelling, which may seem counterintuitive to shrinkage. However, once these materials dry out, they often shrink back to their original size or even smaller due to the loss of moisture. For instance, cotton fabrics are notorious for shrinking when washed and dried. This is because cotton fibers expand when wet and contract as they dry, leading to a reduction in fabric size. Similarly, wood products like furniture and flooring can shrink significantly with changes in humidity levels. In humid environments, wood absorbs moisture and swells, while in dry conditions, it releases moisture and shrinks. This shrinkage can cause cracks and gaps in wood surfaces. The impact of moisture and humidity on shrinkage is also evident in construction materials. Concrete, for example, can shrink over time due to the evaporation of water from its mixture. This process, known as drying shrinkage, can lead to cracks and structural issues if not managed properly. In addition, some synthetic materials like polyurethane foams and certain types of plastics are also susceptible to shrinkage when exposed to varying humidity levels. Understanding the relationship between moisture, humidity, and shrinkage is essential for maintaining the integrity and longevity of various products. For consumers, this means being mindful of storage conditions and usage patterns to minimize the effects of shrinkage. Manufacturers, on the other hand, must consider these factors during the design and production phases to ensure that their products remain stable and functional over time. In summary, moisture and humidity levels are key factors influencing the rate of shrinkage in a wide range of materials. By controlling these environmental conditions, we can mitigate the effects of shrinkage and ensure that products retain their intended dimensions and performance characteristics. This knowledge is particularly important for industries where precision and durability are paramount, such as textiles, construction, and manufacturing.