What Is Lead Time

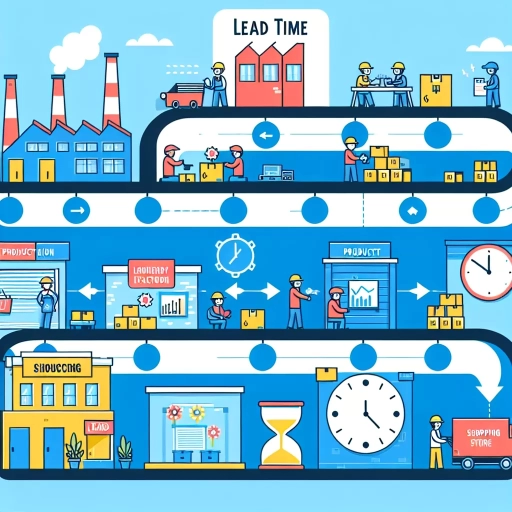
In the fast-paced world of business and manufacturing, understanding and managing lead time is crucial for maintaining efficiency, reducing costs, and enhancing customer satisfaction. Lead time, the period between the initiation of a process and its completion, plays a pivotal role in supply chain management, production planning, and overall operational performance. This article delves into the multifaceted concept of lead time, starting with a foundational understanding of its definition and basics. We will explore the components and factors that influence lead time, including material sourcing, production processes, and logistical considerations. Additionally, we will discuss strategies to optimize and reduce lead time, such as streamlining workflows, leveraging technology, and implementing lean manufacturing practices. By grasping these elements, businesses can better navigate the complexities of lead time and make informed decisions to improve their operational agility. Let's begin by **Understanding Lead Time: Definition and Basics**.
Understanding Lead Time: Definition and Basics
In the fast-paced world of business operations, understanding key metrics is crucial for optimizing efficiency and ensuring smooth workflow. One such critical metric is lead time, which plays a pivotal role in managing production cycles, supply chains, and customer satisfaction. This article delves into the concept of lead time, providing a comprehensive overview that will help you grasp its fundamentals. We begin by defining what lead time is, breaking down its core components to ensure a clear understanding. Next, we explore the various types of lead time, highlighting their distinct characteristics and applications. Finally, we discuss the importance of lead time in business operations, illustrating how it impacts decision-making, resource allocation, and overall performance. By the end of this article, you will have a solid foundation in understanding lead time: its definition and basics.
1. Definition of Lead Time
**Understanding Lead Time: Definition and Basics** **Definition of Lead Time** Lead time is a critical metric in various industries, particularly in manufacturing, logistics, and supply chain management. It is defined as the total time required to complete a process or fulfill an order from the initial request to the final delivery. This period encompasses several key stages: the time it takes to receive raw materials or components, the production or manufacturing time, and the shipping or delivery time. Essentially, lead time measures how long it takes for a product to move through each phase of its lifecycle, from procurement of inputs to the point where it reaches the end customer. In practical terms, lead time can be broken down into several components. For instance, in a manufacturing context, it includes the procurement lead time (the time taken to receive raw materials), production lead time (the time spent on producing the product), and shipping lead time (the time taken for the product to reach the customer). Each of these components can significantly impact the overall efficiency and responsiveness of a business. A shorter lead time generally indicates better operational efficiency and faster response to market demands, while a longer lead time can lead to delays, increased inventory costs, and potential loss of customer satisfaction. Understanding lead time is crucial for businesses as it helps in planning production schedules, managing inventory levels, and setting realistic delivery expectations with customers. By analyzing and optimizing lead times, companies can streamline their operations, reduce bottlenecks, and enhance their competitive edge. For example, companies like Amazon have significantly reduced their lead times through advanced logistics and supply chain management strategies, enabling them to offer same-day or next-day delivery options that drive customer loyalty and growth. Moreover, lead time is not just a metric but also a strategic tool. It influences pricing strategies, inventory management policies, and even marketing campaigns. Businesses that can consistently deliver products quickly are often able to charge premium prices due to the value they offer in terms of speed and reliability. Conversely, prolonged lead times can result in lost sales and damaged brand reputation. In summary, lead time is a multifaceted concept that reflects the efficiency and agility of a company's operations. By defining and understanding lead time accurately, businesses can identify areas for improvement, optimize their processes, and ultimately deliver better value to their customers. This foundational understanding is essential for any organization aiming to enhance its operational performance and stay competitive in today's fast-paced market environment.
2. Types of Lead Time
Understanding lead time is crucial for effective supply chain management, and it encompasses various types that help businesses optimize their operations. There are two primary types of lead time: **Manufacturing Lead Time** and **Supplier Lead Time**. **Manufacturing Lead Time** refers to the duration required to produce a product from raw materials to finished goods. This includes the time spent on processing, assembly, quality control, and packaging. It is essential for manufacturers to accurately calculate this lead time to ensure they can meet demand without overstocking or understocking. Factors influencing manufacturing lead time include production capacity, labor availability, and the complexity of the manufacturing process. For instance, a company producing custom furniture might have a longer manufacturing lead time due to the need for precise craftsmanship and quality checks compared to a mass-produced item like a smartphone. On the other hand, **Supplier Lead Time** is the period between placing an order with a supplier and receiving the goods. This type of lead time is critical for businesses that rely on external suppliers for raw materials or components. It includes the time taken for order processing, shipping, and delivery. Supplier lead times can vary significantly depending on factors such as the supplier's location, shipping methods, and their own production schedules. For example, a company sourcing components from overseas may experience longer supplier lead times due to international shipping delays compared to sourcing locally. Both types of lead times are interdependent and must be carefully managed to maintain a smooth supply chain. Misjudging either can lead to stockouts, overstocking, or delayed product launches, which can have significant financial and reputational consequences. By understanding and optimizing both manufacturing and supplier lead times, businesses can improve their operational efficiency, reduce costs, and enhance customer satisfaction. Effective communication with suppliers and internal teams is key to ensuring that these lead times are accurately estimated and managed. Additionally, leveraging technology such as ERP systems and supply chain analytics can provide real-time insights into lead times, enabling more precise forecasting and better decision-making. In summary, recognizing the distinction between manufacturing and supplier lead times is vital for any business aiming to streamline its supply chain operations. By meticulously managing these two types of lead times, companies can ensure timely production and delivery of products, ultimately driving business success and customer loyalty.
3. Importance in Business Operations
In the realm of business operations, understanding and managing lead time is crucial for maintaining efficiency, reducing costs, and enhancing customer satisfaction. Lead time, the period between the initiation of a process and its completion, directly impacts various facets of business operations. Firstly, it influences **inventory management**. Knowing the lead time for procurement allows businesses to optimize their inventory levels, avoiding both stockouts and overstocking. This balance is essential for minimizing holding costs and ensuring that products are available when needed, thereby improving supply chain reliability. Secondly, lead time plays a significant role in **production planning**. By accurately estimating the time required for each stage of production, businesses can better allocate resources, manage workflows, and meet production targets. This foresight enables companies to adjust their production schedules according to demand fluctuations and avoid bottlenecks that could lead to delays or inefficiencies. Thirdly, lead time has a direct impact on **customer service**. Faster lead times can significantly improve customer satisfaction by ensuring timely delivery of products. In today's competitive market, where consumers expect quick turnaround times, businesses that can deliver products swiftly gain a competitive edge. Conversely, prolonged lead times can lead to customer dissatisfaction and potential loss of business. Moreover, understanding lead time helps in **risk management**. By identifying potential bottlenecks or delays in the supply chain, businesses can develop contingency plans to mitigate risks such as supplier failures or transportation disruptions. This proactive approach ensures continuity of operations even in the face of unforeseen challenges. Finally, lead time is integral to **cost optimization**. Reducing lead times often results in lower costs associated with inventory holding, transportation, and labor. Streamlined processes and efficient supply chains not only save money but also enhance the overall profitability of the business. In summary, the importance of lead time in business operations cannot be overstated. It is a critical metric that influences inventory levels, production planning, customer service, risk management, and cost optimization. By meticulously monitoring and managing lead times, businesses can achieve greater operational efficiency, enhance customer satisfaction, and ultimately drive growth and profitability.
Components and Factors Influencing Lead Time
In the realm of manufacturing and supply chain management, lead time is a critical metric that determines the efficiency and effectiveness of operations. Lead time, essentially the duration between the initiation of a process and its completion, is influenced by a myriad of components and factors. This article delves into the intricate dynamics that shape lead time, focusing on three pivotal areas: **Production Lead Time**, which examines the internal processes and manufacturing stages that contribute to overall lead times; **Supply Chain and Logistics Factors**, highlighting the role of procurement, transportation, and inventory management in lead time optimization; and **External Factors Affecting Lead Time**, which explores how external elements such as market demand, regulatory changes, and geopolitical events impact lead times. By understanding these components and their interplay, businesses can better manage their operations to reduce lead times, enhance productivity, and improve customer satisfaction. This comprehensive analysis builds upon the foundational knowledge of **Understanding Lead Time: Definition and Basics**, providing a detailed roadmap for optimizing lead times in various industrial contexts.
1. Production Lead Time
**Production Lead Time** is a critical component in the broader context of lead time, significantly influencing the efficiency and competitiveness of any manufacturing or production process. It refers to the duration between the start of production and the completion of a product, encompassing all stages from raw material procurement to final assembly and quality control. This period is pivotal because it directly affects the time-to-market, inventory levels, and overall operational costs. Several factors contribute to production lead time, each with its own set of challenges and opportunities for optimization. **Material Sourcing** is one such factor; delays in receiving raw materials or components can significantly extend the production cycle. Companies often mitigate this by implementing just-in-time (JIT) inventory systems or maintaining strong supplier relationships to ensure timely deliveries. **Manufacturing Complexity** is another key influencer; products with intricate designs or those requiring specialized labor may have longer production lead times compared to simpler items. Here, process improvements such as lean manufacturing techniques can help streamline operations and reduce unnecessary steps. **Capacity Utilization** also plays a crucial role; if production lines are operating at or near full capacity, any unexpected disruptions can lead to bottlenecks and increased lead times. Effective capacity planning and flexible production scheduling can help manage these risks. Additionally, **Quality Control** processes are essential but can add to the overall lead time if not optimized. Implementing robust quality assurance protocols early in the production process can prevent costly rework later on, thereby reducing the total lead time. Technological advancements have also become integral in managing production lead times. **Automation** and **Industry 4.0 technologies**, such as robotics and advanced manufacturing execution systems (MES), enable real-time monitoring and optimization of production workflows. These tools help in identifying inefficiencies, predicting potential delays, and making data-driven decisions to improve throughput. Furthermore, **Supply Chain Integration** is vital for minimizing production lead times. Seamless communication between different departments within an organization and with external partners ensures that all stakeholders are aligned, reducing misunderstandings that could cause delays. This integration can be facilitated through enterprise resource planning (ERP) systems that provide a unified platform for managing all aspects of production. In summary, production lead time is a multifaceted metric influenced by various components including material sourcing, manufacturing complexity, capacity utilization, quality control processes, technological advancements, and supply chain integration. By understanding these factors and implementing strategies to optimize each stage of the production process, businesses can significantly reduce their production lead times, enhancing their ability to respond quickly to market demands and maintain a competitive edge.
2. Supply Chain and Logistics Factors
Supply chain and logistics factors play a pivotal role in determining lead time, as they directly influence the efficiency and speed at which goods move from the supplier to the end consumer. One of the key factors is **transportation**, which can significantly impact lead time. The choice of transportation mode—whether by air, land, or sea—determines the speed of delivery. For instance, air freight is generally faster but more expensive, while sea freight is slower but often more cost-effective. Additionally, the reliability and frequency of transportation services can affect lead times; consistent and frequent shipments can reduce wait times and ensure smoother operations. Another critical factor is **inventory management**. Effective inventory control ensures that products are available when needed, reducing the time spent waiting for restocking. Just-in-Time (JIT) inventory systems, for example, aim to maintain minimal inventory levels while ensuring that products are delivered just in time to meet demand, thereby minimizing lead times. However, this approach requires precise forecasting and reliable suppliers to avoid stockouts and delays. **Warehouse and distribution center operations** also contribute to lead time. The efficiency of these facilities in receiving, storing, and dispatching goods can either expedite or delay the supply chain process. Modern warehouse management systems (WMS) and automation technologies can streamline these processes, reducing handling times and improving accuracy. Moreover, strategic location of distribution centers can cut down on transportation times, further reducing overall lead times. **Supplier performance** is another crucial element. The reliability and responsiveness of suppliers directly affect the lead time. Suppliers who consistently meet delivery schedules and maintain high-quality standards help in maintaining a smooth supply chain. Conversely, suppliers with poor performance can introduce variability and delays into the system. Lastly, **technology integration** within the supply chain can significantly reduce lead times. Advanced technologies such as blockchain, IoT sensors, and AI-driven analytics provide real-time visibility into the supply chain, enabling better tracking and faster decision-making. These technologies help in identifying bottlenecks and optimizing processes, thereby reducing lead times. In summary, supply chain and logistics factors are integral to managing lead times effectively. By optimizing transportation methods, improving inventory management practices, enhancing warehouse operations, ensuring reliable supplier performance, and leveraging advanced technologies, businesses can significantly reduce their lead times and improve overall supply chain efficiency. These strategies not only enhance operational speed but also contribute to better customer satisfaction and competitive advantage in the market.
3. External Factors Affecting Lead Time
External factors significantly influence lead time, impacting the efficiency and reliability of supply chains. One crucial external factor is **supplier performance**. The reliability and responsiveness of suppliers can drastically affect lead times. If suppliers are inconsistent in their delivery schedules or have poor quality control, it can lead to delays and increased lead times. For instance, if a supplier experiences production issues or inventory shortages, it can cause a ripple effect throughout the supply chain, resulting in longer wait times for downstream operations. Another external factor is **transportation and logistics**. The efficiency of transportation networks, including road, air, sea, and rail systems, plays a critical role in determining lead times. Factors such as traffic congestion, weather conditions, customs clearance delays, and geopolitical instability can all contribute to longer transit times. For example, natural disasters like hurricanes or floods can disrupt transportation routes, while political tensions may lead to trade restrictions that slow down the movement of goods. **Market demand and seasonality** also exert significant influence on lead times. During peak demand periods or seasonal fluctuations, suppliers may face increased orders, leading to backlogs and extended lead times. For instance, retailers preparing for holiday seasons often experience higher demand for certain products, which can strain supply chains and result in longer lead times. Additionally, economic conditions such as inflation or recession can alter consumer behavior and purchasing patterns, affecting the speed at which goods move through the supply chain. Lastly, **regulatory and compliance issues** can impact lead times. Changes in regulations or compliance requirements can necessitate additional steps in the production and delivery process, adding time to the overall lead time. For example, new safety standards or environmental regulations might require suppliers to implement new testing procedures or certification processes, which can slow down production and shipment. Understanding these external factors is essential for businesses aiming to optimize their supply chains and reduce lead times. By monitoring supplier performance, investing in efficient logistics solutions, anticipating market demand fluctuations, and staying compliant with regulatory changes, companies can better manage external influences on lead time and improve their overall operational efficiency. This proactive approach not only enhances customer satisfaction but also provides a competitive edge in today's fast-paced global market.
Strategies to Optimize and Reduce Lead Time
In today's fast-paced business environment, optimizing and reducing lead time is crucial for maintaining a competitive edge. Lead time, the duration between the initiation of a process and its completion, directly impacts efficiency, customer satisfaction, and overall profitability. To achieve significant reductions in lead time, businesses must employ a multifaceted approach. This article delves into three key strategies: **Process Streamlining and Efficiency**, which involves identifying and eliminating bottlenecks to enhance workflow; **Inventory Management Techniques**, which focus on optimizing stock levels and supply chain dynamics; and **Technology and Automation Solutions**, leveraging advanced tools to streamline operations and reduce manual errors. By understanding and implementing these strategies, organizations can significantly shorten their lead times, thereby improving productivity and customer responsiveness. For those new to the concept, it is essential to first grasp the fundamentals outlined in **Understanding Lead Time: Definition and Basics**, which provides a comprehensive overview of what lead time entails and its importance in operational management. This foundational knowledge will serve as a robust backdrop for exploring the advanced strategies discussed here.
1. Process Streamlining and Efficiency
**Process Streamlining and Efficiency** In the quest to optimize and reduce lead time, process streamlining and efficiency play pivotal roles. Streamlining involves identifying and eliminating unnecessary steps, bottlenecks, and inefficiencies within the workflow. This can be achieved through a thorough analysis of the current processes, often using tools like value stream mapping or process flowcharts. By visualizing each stage of the process, organizations can pinpoint areas where time is being wasted and implement changes to streamline operations. For instance, automating repetitive tasks or integrating different departments' workflows can significantly reduce manual errors and waiting times. Efficiency gains are further amplified by adopting lean principles, which focus on minimizing waste and maximizing value-added activities. This includes reducing inventory levels, implementing just-in-time production, and enhancing employee skills to handle multiple tasks effectively. Technology also plays a crucial role in this context; leveraging advanced software solutions such as workflow management systems, project management tools, and data analytics platforms helps in real-time monitoring and optimization of processes. These tools enable organizations to track performance metrics, identify trends, and make data-driven decisions to continuously improve their processes. Moreover, fostering a culture of continuous improvement is essential for sustained efficiency. Encouraging employees to suggest improvements and empowering them to take ownership of their tasks can lead to innovative solutions that might not have been apparent otherwise. Regular training and development programs ensure that the workforce remains adept at handling new technologies and methodologies, thereby maintaining high levels of productivity. Additionally, outsourcing non-core activities or partnering with specialized service providers can help in focusing on core competencies while ensuring that other critical functions are handled efficiently. This strategic outsourcing not only reduces the workload but also brings in expertise that might be lacking internally. In summary, process streamlining and efficiency are cornerstone strategies for reducing lead time. By systematically analyzing and optimizing workflows, leveraging technology, fostering a culture of continuous improvement, and strategically outsourcing non-core activities, organizations can significantly cut down on unnecessary delays and enhance overall productivity. These measures collectively contribute to a more agile and responsive operation, ultimately leading to shorter lead times and improved customer satisfaction.
2. Inventory Management Techniques
Effective inventory management is a crucial component in strategies to optimize and reduce lead time. Two key techniques that stand out in this context are **Just-in-Time (JIT) Inventory Management** and **Vendor-Managed Inventory (VMI)**. **Just-in-Time (JIT) Inventory Management** is a method where inventory is received just in time to meet customer demand, thereby minimizing storage costs and reducing the risk of inventory obsolescence. This technique requires precise forecasting and tight coordination with suppliers to ensure that materials arrive exactly when needed. By maintaining low inventory levels, JIT helps in reducing lead times significantly because it eliminates the need for lengthy storage periods. Additionally, JIT encourages continuous improvement in production processes, leading to higher efficiency and reduced waste. On the other hand, **Vendor-Managed Inventory (VMI)** involves the supplier managing the buyer's inventory levels on their behalf. In VMI, the supplier has access to the buyer's inventory data and is responsible for replenishing stock as needed. This approach can significantly reduce lead times by ensuring that inventory levels are always optimal and that replenishment occurs in real-time. VMI also fosters stronger relationships between buyers and suppliers, leading to better communication and more reliable supply chains. By outsourcing inventory management to suppliers who have a deeper understanding of their own production cycles, businesses can focus on other critical areas while ensuring that their inventory needs are met promptly. Both JIT and VMI techniques are highly effective in optimizing inventory management processes, which in turn helps in reducing overall lead times. By streamlining inventory replenishment and minimizing unnecessary stockpiling, these methods ensure that products move through the supply chain more efficiently. Moreover, they promote a culture of continuous improvement and collaboration, which are essential for maintaining competitive edge in today's fast-paced business environment. Implementing these techniques can lead to significant reductions in lead times, enabling businesses to respond more quickly to market demands and ultimately enhancing customer satisfaction.
3. Technology and Automation Solutions
In the quest to optimize and reduce lead time, technology and automation solutions play a pivotal role. By leveraging cutting-edge technologies, businesses can significantly streamline their processes, enhance efficiency, and minimize delays. One of the most impactful solutions is the implementation of Enterprise Resource Planning (ERP) systems. ERP integrates various business functions such as production planning, inventory management, and supply chain operations into a single platform, providing real-time visibility and enabling better decision-making. This holistic approach allows for the synchronization of different departments, reducing bottlenecks and ensuring that all components of the production cycle are aligned. Another key technology is the Internet of Things (IoT). IoT devices can monitor and control machinery in real-time, detecting potential issues before they become major problems. This predictive maintenance capability helps in preventing downtime, thereby reducing lead times. Additionally, IoT can optimize production workflows by automating tasks that were previously manual, such as quality control checks and inventory tracking. Automation in manufacturing is also crucial for lead time reduction. Robotic Process Automation (RPA) and Industrial Automation technologies can automate repetitive tasks with high precision and speed, freeing up human resources for more strategic activities. For instance, automated assembly lines can work around the clock without breaks, significantly increasing throughput while maintaining quality standards. Furthermore, advanced analytics and machine learning algorithms can analyze production data to identify inefficiencies and suggest improvements, allowing businesses to continuously refine their processes. Moreover, digital twin technology is gaining traction as it allows companies to create virtual replicas of their physical systems. This enables simulation-based testing and optimization of production processes before actual implementation, reducing the risk of errors and delays. By simulating different scenarios, businesses can identify the most efficient workflows and make data-driven decisions to optimize their operations. In summary, technology and automation solutions are indispensable tools for optimizing and reducing lead times. From ERP systems that integrate business functions to IoT devices that enable predictive maintenance, and from RPA that automates repetitive tasks to digital twins that simulate production processes, these technologies collectively contribute to a more efficient, agile, and responsive supply chain. By embracing these innovations, businesses can significantly cut down their lead times, enhance customer satisfaction, and gain a competitive edge in the market.