What Is Hydraulic Cement

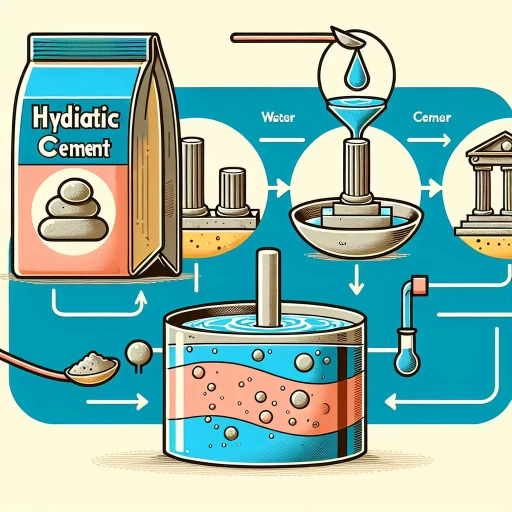
Hydraulic cement is a versatile and essential material in modern construction, known for its unique properties that allow it to harden when exposed to water. This article delves into the intricacies of hydraulic cement, starting with its definition and composition, which are crucial for understanding its fundamental nature. We will explore the properties and characteristics that make hydraulic cement so valuable in various applications, including its strength, durability, and resistance to environmental factors. Additionally, we will examine the diverse applications and uses of hydraulic cement, from building foundations and bridges to repairing infrastructure. By understanding these aspects, readers will gain a comprehensive insight into why hydraulic cement remains a cornerstone in the construction industry. To begin, let's first define and break down the composition of hydraulic cement, which sets the stage for its remarkable properties and widespread uses.
Definition and Composition of Hydraulic Cement
Hydraulic cement, a cornerstone in modern construction, is defined by its ability to harden when exposed to water and form a durable, water-resistant bond. This unique property makes it indispensable for various applications, from building foundations to repairing infrastructure. To fully understand hydraulic cement, it is crucial to delve into its chemical composition, explore the different types available, and appreciate its historical development. The chemical composition of hydraulic cement is a complex blend of minerals and compounds, primarily calcium silicates, aluminates, and ferrites, which react with water to form the binding paste. This intricate chemistry is what sets hydraulic cement apart from other types of cement. Understanding the various types of hydraulic cements, such as Portland cement, blended cements, and specialized cements like sulfate-resistant and white cement, provides insight into their specific uses and advantages. Each type has been developed to meet different performance criteria, ensuring that the right cement is used for the right job. Historically, the development of hydraulic cement has been a gradual process, with significant milestones marking improvements in its formulation and application. From ancient Roman concrete to modern-day high-performance cements, this evolution has been driven by technological advancements and changing construction needs. By examining the chemical composition of hydraulic cement, we can gain a deeper understanding of its fundamental properties and how these contribute to its versatility and strength. This foundational knowledge is essential for appreciating the broader context of hydraulic cement's role in construction and engineering. Therefore, let us begin by exploring the chemical composition of hydraulic cement in more detail.
Chemical Composition
Hydraulic cement, a cornerstone in modern construction, owes its remarkable properties to its intricate chemical composition. At its core, hydraulic cement is primarily composed of limestone, clay, and other minerals. The limestone provides calcium oxide (CaO), while the clay contributes silica (SiO₂) and alumina (Al₂O₃). These components undergo a high-temperature calcination process in a kiln, resulting in the formation of clinker, which is then ground into a fine powder known as Portland cement. The chemical composition of hydraulic cement can be broken down into several key compounds. Calcium silicates, particularly tricalcium silicate (C₃S) and dicalcium silicate (C₂S), are the primary constituents, responsible for the early and late strength development of the cement, respectively. Tricalcium aluminate (C₃A) and tetracalcium aluminoferrite (C₄AF) are other significant components that influence the setting time and durability of the cement. Additionally, small amounts of gypsum (CaSO₄·2H₂O) are added to control the setting rate by retarding the hydration of C₃A. The hydration process, where water reacts with these compounds, is crucial for the development of cement's binding properties. When water is added to hydraulic cement, it triggers a series of chemical reactions that form a hardened paste. The hydration of C₃S and C₂S produces calcium silicate hydrate (CSH) gel, which provides the bulk of the cement's strength. The reaction also releases calcium hydroxide (Ca(OH)₂), contributing to the alkalinity of the concrete environment. Understanding the chemical composition of hydraulic cement is essential for optimizing its performance in various applications. For instance, adjusting the ratio of C₃S to C₂S can tailor the cement's strength development to suit different construction needs. Similarly, controlling the amount of C₃A helps in mitigating potential issues related to sulfate attack, which can degrade the concrete over time. In summary, the chemical composition of hydraulic cement is a complex interplay of calcium, silica, alumina, and other minerals that undergo specific reactions to form a robust and durable binding agent. This intricate chemistry underpins the versatility and reliability of hydraulic cement in modern construction, making it an indispensable material for building structures that stand the test of time.
Types of Hydraulic Cements
Hydraulic cements, a crucial component in modern construction, are categorized into several types based on their composition, properties, and applications. **Ordinary Portland Cement (OPC)** is the most widely used type, known for its versatility and cost-effectiveness. It is composed primarily of limestone, clay, and other minerals, which are ground into a fine powder and then mixed with water to form a paste that hardens over time. **Blended Hydraulic Cements**, such as Portland Pozzolana Cement (PPC) and Portland Slag Cement (PSC), incorporate supplementary cementitious materials like fly ash or slag to enhance durability and reduce environmental impact. These blends offer improved resistance to sulfate attack and lower heat of hydration, making them suitable for large-scale concrete structures. **White Portland Cement** is another variant, distinguished by its white color due to the absence of iron oxide. It is often used in architectural applications where aesthetics are paramount, such as in decorative concrete and precast elements. **Sulfate-Resistant Cement** is formulated to withstand aggressive environments where high sulfate concentrations are present, making it ideal for construction near seawater or in areas with high soil salinity. **Rapid Hardening Cement** accelerates the setting process, allowing for quicker construction timelines and early strength gain, which is beneficial in cold weather conditions or when rapid formwork removal is necessary. **Low Heat Cement** is designed to produce lower heat during hydration, reducing thermal cracking in large concrete pours and ensuring structural integrity over time. This type is commonly used in massive structures like dams and nuclear power plants. **High Alumina Cement**, also known as calcium aluminate cement, has a different chemical composition that provides high early strength and resistance to high temperatures, making it suitable for refractory applications and emergency repairs. **Expansive Cements**, including types like K and M, are specialized to counteract shrinkage in concrete by expanding during the setting process. These cements are used in grouting and sealing applications where tight seals are required. **Colored Cements** incorporate pigments to achieve specific hues, enhancing the visual appeal of concrete surfaces without compromising on performance. Each type of hydraulic cement is engineered to meet specific needs in construction, ensuring that the right material is chosen for the job to guarantee durability, performance, and aesthetic satisfaction. Understanding these variations is essential for selecting the appropriate cement for various engineering projects, thereby ensuring optimal results and longevity of the structures built.
Historical Development
The historical development of hydraulic cement is a fascinating narrative that spans centuries, reflecting human ingenuity and the relentless pursuit of durable construction materials. The earliest known forms of hydraulic cement date back to ancient civilizations, with the Egyptians and Greeks using lime-based mortars around 2000 BCE. However, it was the Romans who made significant strides in this field. They developed a sophisticated form of hydraulic cement known as Opus caementicium, which combined lime with volcanic ash and water to create a strong, durable binding agent. This innovation allowed for the construction of monumental structures like the Pantheon and Colosseum, which still stand today. The Middle Ages saw a decline in the use of hydraulic cements as Roman techniques were largely forgotten. However, during the Renaissance, there was a renewed interest in classical knowledge, leading to a revival in the use of lime-based mortars. The 18th century marked a significant turning point with the discovery of natural cements by British engineer John Smeaton in 1756. Smeaton identified that certain types of limestone, when burned and mixed with water, produced a hydraulic lime that could set underwater. The modern era of hydraulic cement began in the early 19th century with the invention of Portland cement by Joseph Aspdin in 1824. Aspdin, an English bricklayer and builder, patented a method for making a superior form of hydraulic cement by heating a mixture of limestone and clay to high temperatures. This process produced a more consistent and stronger product than its predecessors, revolutionizing the construction industry. Since Aspdin's invention, there have been numerous advancements in the composition and production of hydraulic cements. The late 19th and early 20th centuries saw improvements in manufacturing processes, including the introduction of rotary kilns that allowed for mass production. Modern hydraulic cements are tailored for specific applications, with various additives and admixtures enhancing their performance characteristics such as strength, durability, and sustainability. Today, hydraulic cements are a cornerstone of modern construction, enabling the creation of complex infrastructure projects like high-rise buildings, bridges, and dams. The ongoing research into new materials and technologies continues to evolve the definition and composition of hydraulic cement, ensuring it remains a vital component in meeting the demands of an ever-changing built environment. This historical trajectory underscores how human innovation has transformed raw materials into a fundamental tool for building our world.
Properties and Characteristics of Hydraulic Cement
Hydraulic cement, a cornerstone in modern construction, boasts a myriad of properties and characteristics that make it an indispensable material. Its versatility and performance are underscored by three key aspects: setting time and strength, workability and flowability, and durability and resistance. Understanding these attributes is crucial for engineers and builders to ensure the structural integrity and longevity of their projects. The setting time and strength of hydraulic cement determine how quickly it hardens and its ultimate load-bearing capacity, which are critical for scheduling construction activities and ensuring the structural soundness of buildings. Additionally, the workability and flowability of the cement influence its ease of use and ability to fill complex forms without compromising its quality. Lastly, the durability and resistance of hydraulic cement against environmental factors such as water, chemicals, and extreme temperatures are vital for maintaining the integrity of structures over time. By delving into these characteristics, we can appreciate the complexity and importance of hydraulic cement in construction. Let's begin by examining the setting time and strength of hydraulic cement, which form the foundation of its utility in building projects.
Setting Time and Strength
**Setting Time and Strength** The setting time and strength of hydraulic cement are crucial properties that determine its suitability for various construction applications. The setting time refers to the period it takes for the cement paste to harden and become rigid after mixing with water. This process is divided into two stages: initial set and final set. The initial set, typically occurring within 30 minutes to an hour, marks the beginning of the hardening process where the cement starts to lose its plasticity. The final set, usually achieved within 2-4 hours, signifies the point at which the cement has reached a significant portion of its ultimate strength and is no longer susceptible to deformation. The strength of hydraulic cement is another vital characteristic, measured in terms of compressive strength, tensile strength, and flexural strength. Compressive strength, which is the most commonly evaluated, indicates the ability of the cement to withstand forces pushing inward from all sides. This is typically measured at specific intervals such as 1 day, 3 days, 7 days, and 28 days after mixing. The 28-day compressive strength is often considered the standard benchmark for evaluating the long-term performance of hydraulic cement. Factors influencing both setting time and strength include the chemical composition of the cement, ambient temperature, humidity, and the presence of admixtures. For instance, higher temperatures generally accelerate the setting process but may also affect long-term strength if excessive. Conversely, lower temperatures slow down the hydration reaction, leading to delayed setting but potentially higher ultimate strengths. In practical applications, understanding these properties is essential for ensuring that concrete structures meet design specifications and perform as intended over their lifespan. For example, in cold weather concreting, special cements with faster setting times or chemical admixtures that accelerate hydration may be used to mitigate delays. Similarly, in high-strength concrete applications such as skyscrapers or bridges, cements with higher early-age strengths are preferred to support rapid construction schedules. Overall, the setting time and strength of hydraulic cement are interrelated yet distinct properties that must be carefully managed to achieve optimal performance in various construction scenarios. By selecting the appropriate type of hydraulic cement and controlling environmental conditions during placement and curing, engineers can ensure that concrete structures exhibit the desired durability and structural integrity.
Workability and Flowability
Workability and flowability are crucial properties of hydraulic cement, significantly influencing the ease and quality of concrete placement and finishing. **Workability** refers to the ability of freshly mixed concrete to be placed, consolidated, and finished without excessive effort. It encompasses factors such as slump, flow, and cohesion, which determine how easily the concrete can be poured, spread, and smoothed. High workability is desirable as it allows for better placement around reinforcing bars, easier finishing operations, and reduced labor costs. However, excessive workability can lead to segregation and reduced strength. **Flowability**, on the other hand, is a measure of how easily the concrete can flow under its own weight or with minimal external force. This property is particularly important for self-consolidating concrete (SCC) and other specialized mixes where high flowability is required to fill complex forms without vibration. Flowability is often assessed using tests like the slump flow test or the L-box test. In hydraulic cement, flowability is influenced by the cement's particle size distribution, surface area, and the presence of admixtures such as superplasticizers. These admixtures can enhance flowability by reducing the water-cement ratio while maintaining or improving workability. The balance between workability and flowability is critical because it directly affects the constructability and final quality of the concrete structure. For instance, in high-performance concrete applications, achieving optimal workability and flowability ensures that the concrete can be placed efficiently while maintaining its structural integrity. This balance also impacts the durability of the concrete, as proper placement and finishing reduce the risk of defects and improve resistance to environmental factors. In practice, engineers and contractors often use a combination of cement type, admixtures, and mixing techniques to achieve the desired levels of workability and flowability. The choice of hydraulic cement itself plays a significant role; different types of hydraulic cements have varying properties that can affect these characteristics. For example, Type III hydraulic cement, known for its high early strength, may require adjustments in mixing water content or admixture dosage to maintain adequate workability. Overall, understanding and managing workability and flowability are essential for ensuring that hydraulic cement-based concrete meets the required standards for placement, finishing, and long-term performance. By optimizing these properties through careful selection of materials and mixing practices, construction projects can benefit from improved efficiency, reduced costs, and enhanced structural quality.
Durability and Resistance
Durability and resistance are paramount properties of hydraulic cement, ensuring the long-term integrity and performance of structures. Hydraulic cement, unlike non-hydraulic types, hardens when exposed to water and continues to set even underwater, making it highly durable in various environmental conditions. This durability is attributed to its ability to form a dense, impermeable paste that resists chemical attacks and physical wear. The hydration process of hydraulic cement involves the formation of calcium silicate hydrate (CSH) and calcium hydroxide, which contribute to its strength and resistance against degradation. In terms of resistance, hydraulic cement exhibits superior performance against several factors. It is highly resistant to chemical attacks from substances like sulfates, chlorides, and acids, which are common in soil and water environments. This resistance is crucial for structures exposed to aggressive environments, such as marine or industrial settings. Additionally, hydraulic cement offers excellent mechanical resistance, with high compressive strength that can withstand significant loads without compromising the structure's integrity. Its resistance to freeze-thaw cycles is also noteworthy, as it can endure repeated exposure to freezing temperatures and subsequent thawing without suffering significant damage. The durability of hydraulic cement is further enhanced by its low permeability, which reduces the penetration of harmful substances like water and ions that could otherwise cause deterioration. This property is particularly important for structures that are exposed to moisture or submerged in water, such as dams, bridges, and offshore platforms. Moreover, the low shrinkage of hydraulic cement minimizes the risk of cracking, which can compromise the structure's overall durability and resistance. In practical applications, the durability and resistance of hydraulic cement are evident in its widespread use in critical infrastructure projects. For instance, in the construction of high-rise buildings, hydraulic cement ensures that the concrete maintains its structural integrity over decades despite exposure to various environmental stresses. Similarly, in road construction, it provides a durable surface that can withstand heavy traffic and harsh weather conditions without significant degradation. Overall, the combination of durability and resistance makes hydraulic cement an indispensable material in modern construction. Its ability to perform well under diverse conditions ensures that structures built with this material can endure for extended periods, reducing maintenance costs and enhancing safety. As a result, hydraulic cement remains a cornerstone in the development of resilient and long-lasting infrastructure.
Applications and Uses of Hydraulic Cement
Hydraulic cement, known for its rapid setting and high strength, is a versatile material with a wide range of applications across various industries. Its unique properties make it an essential component in construction and building projects, where it is used to create durable and long-lasting structures. Beyond its use in building foundations, walls, and floors, hydraulic cement also plays a crucial role in infrastructure projects such as bridges, roads, and tunnels, ensuring the structural integrity and longevity of these critical public works. Additionally, its specialized industrial uses extend to applications in marine environments, nuclear facilities, and other high-performance settings where extreme conditions demand superior material performance. This article will delve into these three key areas—construction and building, infrastructure projects, and specialized industrial uses—to highlight the diverse and essential roles of hydraulic cement. We begin by examining its critical role in construction and building.
Construction and Building
In the realm of construction and building, hydraulic cement plays a pivotal role due to its unique properties and versatility. Hydraulic cement, unlike non-hydraulic cement, hardens when exposed to water and can set underwater, making it an indispensable material for various applications. One of the primary uses of hydraulic cement is in the construction of structures that are exposed to water or moisture, such as dams, bridges, and marine foundations. Its ability to set and harden in wet conditions ensures the durability and stability of these structures, even in harsh environments. In building construction, hydraulic cement is widely used in concrete mixes for foundations, walls, and floors. It provides high compressive strength and resistance to chemical attacks, which are crucial for ensuring the longevity of buildings. For instance, in areas prone to high humidity or where structures are exposed to seawater or acidic soils, hydraulic cement-based concrete offers superior protection against degradation. Additionally, its rapid setting time allows for faster construction schedules, which is particularly beneficial in urban development projects where time is of the essence. Hydraulic cement also finds extensive use in repair and restoration works. Its compatibility with existing concrete structures makes it ideal for patching and repairing damaged areas. This is especially important for maintaining the integrity of older buildings and infrastructure, where the original materials may have deteriorated over time. Furthermore, hydraulic cement can be used to create specialized mortars and grouts that are designed to fill gaps and voids in masonry structures, enhancing their structural integrity. Another significant application of hydraulic cement is in the production of precast concrete products such as pipes, manholes, and other prefabricated components. These products are manufactured in controlled environments and then transported to construction sites, where they are assembled to form larger structures. The use of hydraulic cement in these products ensures they can withstand various environmental conditions without compromising their structural integrity. Moreover, hydraulic cement is essential in geotechnical engineering projects such as tunnel linings and shafts. Here, its ability to set quickly and provide high early strength is critical for maintaining the stability of excavations and ensuring safe working conditions. In addition, hydraulic cement-based grouts are used for anchoring and stabilizing rock formations, which is vital for preventing rockfalls and ensuring the safety of both workers and the general public. In summary, hydraulic cement's unique properties make it a cornerstone material in modern construction and building practices. Its ability to set underwater, provide high strength, and resist chemical attacks makes it an invaluable resource for a wide range of applications, from marine structures to building repairs and geotechnical projects. As a result, hydraulic cement continues to play a central role in shaping the built environment and ensuring the durability and safety of our infrastructure.
Infrastructure Projects
Infrastructure projects are the backbone of modern society, providing essential services and facilitating economic growth. These projects rely heavily on high-quality materials, with hydraulic cement being a cornerstone due to its unique properties. Hydraulic cement, unlike non-hydraulic cement, hardens when exposed to water and can set underwater, making it ideal for a wide range of infrastructure applications. In the construction of bridges, hydraulic cement is crucial for creating durable and resilient structures that can withstand harsh environmental conditions. It is used in the production of concrete for bridge foundations, piers, and decks, ensuring stability and longevity. For instance, in the construction of the iconic Golden Gate Bridge in San Francisco, hydraulic cement played a pivotal role in its foundation and structural integrity. Roads and highways also benefit significantly from hydraulic cement. It is used to create high-strength concrete pavements that can handle heavy traffic loads and adverse weather conditions. The durability of hydraulic cement-based concrete reduces maintenance needs and extends the lifespan of road infrastructure, making it a cost-effective solution in the long term. Water management systems, including dams, canals, and water treatment plants, are another critical area where hydraulic cement is indispensable. Its ability to set underwater makes it perfect for constructing dams that control water flow and prevent flooding. For example, the Hoover Dam, one of the world's largest dams, was built using hydraulic cement to ensure its structural integrity and water resistance. In addition to these large-scale projects, hydraulic cement is also essential for urban infrastructure such as buildings, tunnels, and subway systems. It provides the necessary strength and durability for high-rise buildings and underground structures that are subject to various stresses and environmental factors. Furthermore, hydraulic cement is used in the repair and rehabilitation of existing infrastructure. Its fast-setting properties make it ideal for emergency repairs on roads and bridges, minimizing downtime and ensuring public safety. This versatility underscores its importance in maintaining and upgrading infrastructure to meet growing demands. In summary, hydraulic cement's unique properties make it a vital component in various infrastructure projects. Its ability to set underwater, combined with its strength and durability, ensures that critical infrastructure can withstand the test of time and environmental challenges. As societies continue to grow and urbanize, the role of hydraulic cement in building and maintaining robust infrastructure will remain paramount.
Specialized Industrial Uses
Hydraulic cement, known for its ability to set and harden when exposed to water, finds specialized industrial uses across various sectors due to its unique properties. In the construction industry, hydraulic cement is crucial for underwater construction projects such as building dams, bridges, and marine structures. Its capacity to set in wet conditions makes it ideal for these applications, ensuring structural integrity and durability even in submerged environments. Additionally, hydraulic cement is used in the repair of concrete structures that are exposed to water or high humidity, such as seawalls, canals, and water treatment plants. Its rapid setting time and high early strength are particularly beneficial in emergency repairs where quick action is necessary. In the oil and gas sector, hydraulic cement plays a vital role in well drilling operations. It is used to seal the annular space between the casing pipe and the borehole wall, preventing fluid migration and ensuring the stability of the well. This application requires cements that can withstand high temperatures and pressures, making hydraulic cement a preferred choice. Furthermore, in the nuclear industry, hydraulic cement is utilized for the containment of radioactive materials due to its ability to form a strong, impermeable barrier that can resist chemical attack and radiation exposure. In mining operations, hydraulic cement is used to stabilize rock formations and prevent collapse. It helps in backfilling mined-out areas with a mixture of cement, aggregate, and water, which hardens to provide structural support. This technique enhances mine safety and extends the lifespan of mining tunnels. Moreover, in environmental engineering, hydraulic cement is employed in the remediation of contaminated soil and groundwater. It can be used to create impermeable barriers that prevent the spread of pollutants, thereby protecting groundwater sources. The versatility of hydraulic cement also extends to its use in specialized flooring applications. For instance, it is used in the creation of high-strength, abrasion-resistant floors in industrial facilities such as warehouses, factories, and airports. These floors must withstand heavy traffic and mechanical loads, making hydraulic cement an ideal choice due to its high compressive strength and resistance to wear. In summary, the specialized industrial uses of hydraulic cement are diverse and critical across various sectors. Its unique ability to set in wet conditions, combined with its high strength and durability, makes it an indispensable material for underwater construction, well drilling, nuclear containment, mining stabilization, environmental remediation, and specialized flooring applications. These uses highlight the importance of hydraulic cement in ensuring the safety, efficiency, and longevity of industrial operations.