What Was The Primary Reason That Whmis Was Introduced In Canada In 1988?

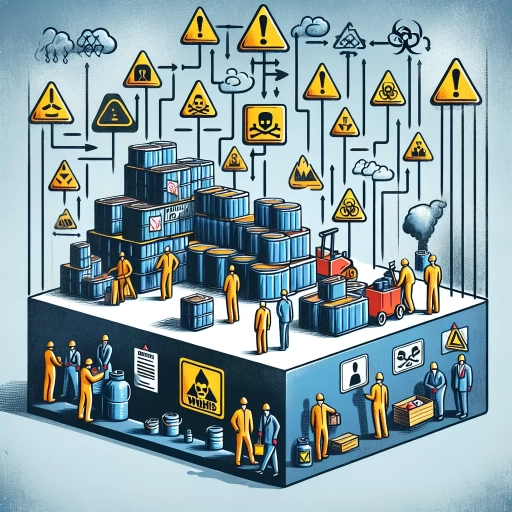
In 1988, Canada introduced the Workplace Hazardous Materials Information System (WHMIS) to address a critical gap in workplace safety and health. This initiative was not merely a regulatory tweak but a comprehensive response to the growing concerns about chemical hazards in the workplace. The primary reason for WHMIS's introduction was to ensure that workers were adequately informed about the dangers of hazardous materials they handled daily. This article delves into the historical context and regulatory environment that necessitated WHMIS, the key objectives and goals that drove its implementation, and the impact it has had on workplace safety. By understanding these facets, we can appreciate the significance of WHMIS in protecting Canadian workers. Let us begin by examining the historical context and regulatory environment that laid the groundwork for this pivotal legislation.
Historical Context and Regulatory Environment
The historical context and regulatory environment surrounding chemical safety in Canada are multifaceted and influenced by various factors. Understanding these elements is crucial for grasping the evolution of safety standards and their impact on public and workplace safety. This article delves into three key areas: Pre-WHIMS Chemical Safety Standards, International Influences on Canadian Policy, and Public and Workplace Safety Concerns. Each of these aspects plays a significant role in shaping the current regulatory landscape. The pre-WHIMS era, for instance, highlights the early attempts at regulating chemical safety, laying the groundwork for more comprehensive standards. International influences have also been pivotal, as global best practices and agreements have shaped Canadian policy. Additionally, public and workplace safety concerns have driven the need for stringent regulations to protect individuals from hazardous substances. By examining these historical and regulatory dimensions, we can better appreciate the development of robust safety protocols. This exploration begins with a closer look at the Pre-WHIMS Chemical Safety Standards, which set the stage for the more sophisticated regulations that followed.
Pre-WHIMS Chemical Safety Standards
The introduction of the Workplace Hazardous Materials Information System (WHMIS) in Canada in 1988 was a pivotal moment in the country's chemical safety standards, driven primarily by the need to protect workers from the hazards associated with handling and using hazardous materials. Prior to WHMIS, Canada's regulatory environment was fragmented and lacked a comprehensive system for managing workplace chemical safety. The pre-WHMIS era saw various provincial and federal regulations, but these were often inconsistent and inadequate, leading to significant gaps in worker protection. Historically, the early 20th century saw a rapid expansion of industrial activities, which led to an increase in the use of hazardous chemicals in workplaces. However, this growth was not matched by corresponding improvements in safety standards. By the 1970s and 1980s, public and worker concerns about chemical hazards had reached a critical point. The lack of standardized labeling, material safety data sheets (MSDS), and training programs meant that many workers were exposed to dangerous substances without proper knowledge or protection. The primary reason for the introduction of WHMIS was to address these deficiencies by creating a harmonized national system that would ensure consistent and reliable information about hazardous materials. WHMIS was designed to provide workers with the right to know about the chemicals they were working with, through standardized labeling and MSDS. This system mandated that suppliers of hazardous materials classify these substances based on their physical and health hazards, label them appropriately, and provide detailed safety information. The regulatory environment leading up to WHMIS involved significant collaboration between federal, provincial, and territorial governments. The Canadian government recognized the need for a unified approach to chemical safety and worked closely with labor unions, industry stakeholders, and health organizations to develop WHMIS. This collaborative effort ensured that the new standards would be both effective and feasible to implement across different sectors and regions. The introduction of WHMIS in 1988 marked a significant shift towards a more proactive and preventive approach to chemical safety in Canadian workplaces. By providing workers with essential information about the hazards they faced, WHMIS empowered them to take necessary precautions and contributed to a safer working environment. This initiative also set a precedent for future regulatory improvements, demonstrating the importance of coordinated national standards in protecting worker health and safety. Overall, the primary reason for introducing WHMIS was to fill the critical gaps in pre-existing safety standards, thereby enhancing worker protection and fostering a safer workplace culture across Canada.
International Influences on Canadian Policy
The introduction of the Workplace Hazardous Materials Information System (WHMIS) in Canada in 1988 was significantly influenced by international policy and regulatory standards. At the core of this initiative was the need to align Canadian workplace safety regulations with emerging global best practices, particularly those set forth by the United Nations and other developed nations. The primary reason for WHMIS's introduction was to harmonize Canada's hazardous materials management with the United Nations' Recommendations on the Transport of Dangerous Goods, which had been gaining international acceptance since the 1950s. These recommendations emphasized standardized labeling, classification, and information dissemination to ensure worker safety and environmental protection. Canada's decision to adopt WHMIS was also driven by economic considerations. As a trading nation, Canada sought to facilitate smoother cross-border transactions by aligning its regulations with those of its major trading partners, particularly the United States. The U.S. Occupational Safety and Health Administration (OSHA) had already implemented similar regulations under the Hazard Communication Standard (HCS) in 1983, which mandated that employers provide workers with information about hazardous chemicals in the workplace. By adopting WHMIS, Canada ensured that its industries could comply with both domestic and international standards, thereby enhancing trade efficiency and competitiveness. Moreover, the international community's growing awareness of occupational health and safety issues played a crucial role in shaping Canadian policy. The International Labour Organization (ILO), a specialized agency of the United Nations, had long advocated for improved workplace safety standards. Canada's participation in ILO and its commitment to upholding international labor standards further underscored the necessity of implementing robust hazardous materials management protocols. In addition to these external influences, domestic factors such as public concern over workplace safety and environmental protection also contributed to the introduction of WHMIS. The Canadian government recognized that a comprehensive system for managing hazardous materials was essential not only for protecting workers but also for safeguarding public health and the environment. By integrating international best practices into its regulatory framework, Canada aimed to create a safer and more sustainable working environment. In summary, the primary reason for introducing WHMIS in Canada in 1988 was to align the country's regulatory environment with international standards and best practices, thereby enhancing workplace safety, facilitating trade, and reflecting Canada's commitment to global labor and environmental standards. This move underscored Canada's proactive approach to addressing occupational health and safety issues while ensuring economic competitiveness in a rapidly globalizing world.
Public and Workplace Safety Concerns
The introduction of the Workplace Hazardous Materials Information System (WHMIS) in Canada in 1988 was a pivotal moment in the country's history of public and workplace safety. This regulatory framework was primarily introduced to address the significant gaps in workplace safety standards and to protect workers from the hazards associated with handling and using hazardous materials. Prior to WHMIS, there was a lack of standardized information and training for workers regarding the safe handling of chemicals, leading to numerous workplace injuries and illnesses. The historical context reveals that the 1970s and 1980s saw a growing awareness of occupational health and safety issues, with mounting evidence of chemical-related health problems among workers. In response to these concerns, the Canadian government collaborated with labor unions, industry stakeholders, and health organizations to develop WHMIS. This system mandated that suppliers of hazardous materials provide safety data sheets (SDSs) and labels to inform workers about the risks associated with these substances. Employers were also required to train workers on how to safely handle these materials, ensuring that they understood the hazards and knew how to mitigate them. The regulatory environment at the time was characterized by a shift towards more stringent safety standards, reflecting a broader societal recognition of the importance of protecting worker health. WHMIS aligned with international standards, particularly those set by the United Nations, and has since been updated to include the Globally Harmonized System of Classification and Labelling of Chemicals (GHS). This alignment ensures that Canadian workplaces adhere to global best practices in chemical safety. The introduction of WHMIS marked a significant step forward in Canada's commitment to workplace safety, demonstrating a proactive approach to preventing injuries and illnesses caused by hazardous materials. By providing clear guidelines and mandatory training, WHMIS has contributed substantially to reducing workplace accidents and enhancing overall public health and safety. Today, WHMIS remains a cornerstone of Canada's occupational health and safety regulations, underscoring the country's ongoing commitment to protecting its workforce from chemical hazards.
Key Objectives and Goals of WHIMS
The Workplace Hazardous Materials Information System (WHIMS) is a comprehensive framework designed to ensure the safe handling, use, and disposal of hazardous materials in the workplace. At its core, WHIMS has three key objectives that underpin its effectiveness: Enhancing Workplace Safety and Health, Standardizing Hazard Communication, and Compliance with International Standards. By focusing on these objectives, WHIMS aims to create a safer and more informed work environment. Enhancing Workplace Safety and Health is a primary goal, as it involves providing workers with the necessary information and training to handle hazardous materials safely. This is complemented by Standardizing Hazard Communication, which ensures that all stakeholders have access to consistent and reliable information about the hazards associated with various materials. Additionally, Compliance with International Standards ensures that WHIMS aligns with global best practices, fostering a culture of safety that is recognized and respected internationally. By achieving these objectives, WHIMS plays a crucial role in protecting workers and promoting a healthier workplace environment, making Enhancing Workplace Safety and Health a foundational aspect of its overall mission.
Enhancing Workplace Safety and Health
The primary reason WHMIS (Workplace Hazardous Materials Information System) was introduced in Canada in 1988 was to enhance workplace safety and health by providing workers with the necessary information to handle hazardous materials safely. This initiative was a response to the growing concern over the risks associated with exposure to hazardous substances in the workplace. Prior to WHMIS, there was a lack of standardized protocols for identifying, labeling, and communicating the dangers of these materials, leading to numerous workplace injuries and illnesses. By mandating the use of standardized labels, safety data sheets (SDS), and worker training programs, WHMIS aimed to bridge this knowledge gap and ensure that workers were adequately informed about the hazards they faced. WHMIS aligns with key objectives and goals such as reducing occupational illnesses and injuries, promoting a culture of safety, and fostering compliance with health and safety regulations. The system ensures that all hazardous products are properly labeled with clear hazard statements, precautionary statements, and pictograms, making it easier for workers to understand potential risks. Additionally, SDSs provide detailed information on safe handling practices, emergency procedures, and first aid measures. This comprehensive approach not only protects workers but also contributes to a safer work environment overall. The introduction of WHMIS has had a significant impact on workplace safety in Canada. It has led to increased awareness among workers about the hazards they encounter daily, enabling them to take preventive measures and respond effectively in emergency situations. Employers have also benefited from reduced liability and lower costs associated with workplace accidents and illnesses. Furthermore, WHMIS has set a precedent for other countries to adopt similar systems, highlighting Canada's commitment to occupational health and safety standards. In summary, the introduction of WHMIS in 1988 was a pivotal step towards enhancing workplace safety and health in Canada by providing a structured framework for managing hazardous materials. This initiative has been instrumental in reducing workplace hazards, promoting worker safety, and aligning with broader objectives of creating a safer and healthier work environment. As part of the key objectives and goals of WHMIS, this system continues to play a crucial role in safeguarding the well-being of Canadian workers.
Standardizing Hazard Communication
The primary reason for the introduction of the Workplace Hazardous Materials Information System (WHMIS) in Canada in 1988 was to standardize hazard communication, ensuring that workers, employers, and the public are adequately informed about the dangers associated with hazardous materials. This initiative was a response to the growing concern over workplace safety and the need for a unified system to manage chemical hazards. Prior to WHMIS, there was a lack of consistency in how hazardous materials were labeled, classified, and communicated, leading to confusion and increased risk of accidents. WHMIS aimed to bridge this gap by establishing a comprehensive framework that mandates the classification of hazardous products, the labeling of containers, and the provision of safety data sheets (SDSs). This standardized approach ensures that all stakeholders have access to clear, consistent, and reliable information about the hazards posed by chemicals. For instance, WHMIS requires that all hazardous products be classified based on their physical and health hazards, which helps in identifying potential risks and taking appropriate preventive measures. The key objectives and goals of WHMIS include ensuring that workers are trained to handle hazardous materials safely, reducing the incidence of workplace injuries and illnesses, and promoting a culture of safety within organizations. By standardizing hazard communication, WHMIS facilitates better decision-making at all levels, from procurement to disposal of hazardous substances. Employers are required to provide their employees with necessary training on WHMIS, which includes understanding labels, reading SDSs, and knowing how to handle emergencies involving hazardous materials. Moreover, WHMIS aligns Canada with international standards, particularly those set by the United Nations' Globally Harmonized System of Classification and Labelling of Chemicals (GHS). This alignment enhances trade and communication across borders, making it easier for Canadian businesses to comply with global regulations while maintaining high safety standards. In practice, WHMIS has significantly improved workplace safety by ensuring that workers are well-informed about the chemicals they work with. The system has also led to better compliance with safety regulations, reduced chemical-related accidents, and enhanced overall occupational health. As a result, WHMIS has become an integral part of Canada's occupational health and safety framework, reflecting the country's commitment to protecting its workforce and promoting a safer working environment. In summary, the introduction of WHMIS in 1988 was a critical step towards standardizing hazard communication in Canada. By providing a unified system for classifying, labeling, and communicating hazards associated with chemical substances, WHMIS has significantly enhanced workplace safety and compliance with international standards. Its key objectives and goals continue to drive improvements in occupational health and safety, making it an essential component of Canada's regulatory landscape.
Compliance with International Standards
The introduction of the Workplace Hazardous Materials Information System (WHMIS) in Canada in 1988 was primarily driven by the need to enhance workplace safety and compliance with international standards. At the time, there was a significant gap in the regulation and communication of hazardous material risks, leading to numerous workplace injuries and fatalities. WHMIS was designed to address this issue by mandating a standardized system for classifying, labeling, and providing safety data sheets (SDS) for hazardous materials. This initiative aligned Canada with international best practices, particularly those set forth by the United Nations' Globally Harmonized System of Classification and Labelling of Chemicals (GHS), which aims to ensure consistent communication of chemical hazards worldwide. Compliance with international standards was a key objective of WHMIS. By adopting a harmonized approach, Canada ensured that its regulations were consistent with those of other countries, facilitating trade and reducing confusion among workers who might be exposed to similar hazards in different jurisdictions. This harmonization also helped Canadian businesses to compete more effectively in the global market, as they could adhere to a single set of standards rather than navigating multiple regulatory frameworks. Moreover, WHMIS compliance has been instrumental in improving workplace safety. The system requires employers to provide comprehensive training to employees on the safe handling of hazardous materials, which has led to a reduction in workplace accidents and illnesses. The standardized labeling and SDS requirements ensure that workers have access to critical information about the hazards they are exposed to, enabling them to take appropriate precautions. In addition, WHMIS has fostered a culture of safety awareness and responsibility among employers and employees alike. By making hazard information readily available and understandable, WHMIS encourages proactive measures to mitigate risks. This proactive approach not only protects workers but also contributes to a more efficient and productive work environment. The alignment of WHMIS with international standards has also facilitated continuous improvement. As global best practices evolve, WHMIS regulations can be updated to reflect these changes, ensuring that Canada remains at the forefront of workplace safety. This dynamic approach ensures that Canadian workplaces remain safe and compliant, supporting the broader goals of protecting public health and the environment. In summary, the primary reason for introducing WHMIS in Canada in 1988 was to enhance workplace safety through compliance with international standards. By adopting a harmonized system for classifying and communicating hazardous material risks, WHMIS has significantly improved safety outcomes, facilitated global trade, and fostered a culture of safety awareness and responsibility. This alignment with international standards continues to be a cornerstone of WHMIS, ensuring that Canadian workplaces remain safe, compliant, and competitive on the global stage.
Implementation and Impact of WHIMS
The implementation and impact of the Workplace Hazardous Materials Information System (WHMIS) have been pivotal in enhancing workplace safety across various industries. This comprehensive system has multifaceted benefits, which can be understood through three key aspects: Training and Education Programs, Regulatory Enforcement and Compliance, and Long-term Effects on Workplace Safety Culture. Firstly, WHMIS mandates rigorous Training and Education Programs to ensure that workers are well-informed about the hazards associated with the materials they handle. This educational component is crucial as it equips employees with the knowledge necessary to handle hazardous materials safely, thereby reducing the risk of accidents and injuries. Secondly, Regulatory Enforcement and Compliance play a significant role in ensuring that workplaces adhere to WHMIS standards. Strict regulations and regular inspections help maintain a safe working environment by enforcing the proper labeling, storage, and handling of hazardous substances. Lastly, the Long-term Effects on Workplace Safety Culture are profound. By integrating WHMIS into daily operations, organizations foster a culture of safety awareness and responsibility among employees, leading to sustained improvements in workplace safety over time. Understanding these elements begins with a strong foundation in Training and Education Programs, which are essential for the effective implementation of WHMIS. By focusing on these educational initiatives, we can ensure that workers are equipped with the necessary skills and knowledge to handle hazardous materials safely.
Training and Education Programs
The primary reason WHMIS (Workplace Hazardous Materials Information System) was introduced in Canada in 1988 was to ensure the safe handling, use, and disposal of hazardous materials in the workplace. This initiative was driven by the need to protect workers from the risks associated with chemical substances. Prior to WHMIS, there was a significant gap in the regulation and communication of hazardous material information, leading to numerous workplace injuries and illnesses. WHMIS aimed to bridge this gap by mandating comprehensive training and education programs for employees who work with or around hazardous materials. These training and education programs are a cornerstone of WHMIS implementation. They are designed to equip workers with the knowledge and skills necessary to identify, handle, and respond to hazardous substances safely. The programs typically cover several key areas: understanding the WHMIS system itself, recognizing the hazards associated with specific chemicals, interpreting safety data sheets (SDSs), and understanding the proper use of labels and personal protective equipment (PPE). By ensuring that all employees are well-trained, employers can significantly reduce the risk of accidents and ensure compliance with regulatory standards. The impact of these training programs is multifaceted. Firstly, they enhance workplace safety by reducing the incidence of chemical-related injuries and illnesses. This not only protects the health and well-being of workers but also minimizes downtime and associated costs for employers. Secondly, these programs foster a culture of safety within organizations, encouraging employees to take an active role in maintaining a safe working environment. Thirdly, they contribute to environmental protection by promoting responsible handling and disposal practices for hazardous materials. Moreover, the effectiveness of WHMIS training is reinforced through regular updates and refreshers. As new substances are introduced into the workplace or as regulations evolve, ongoing education ensures that workers remain informed and compliant. This continuous learning approach helps in adapting to changing workplace conditions and technological advancements, thereby sustaining a high level of safety awareness. In addition to the direct benefits for workers and employers, WHMIS training has broader societal implications. By reducing occupational health risks, it contributes to overall public health and reduces the burden on healthcare systems. Furthermore, it aligns Canada with international standards for chemical safety, enhancing the country's reputation as a leader in occupational health and safety. In conclusion, the introduction of WHMIS in 1988 marked a significant milestone in Canada's commitment to workplace safety. The robust training and education programs mandated by WHMIS have been instrumental in creating safer workplaces, reducing chemical-related hazards, and promoting a culture of safety among Canadian workers. As these programs continue to evolve and improve, they remain a vital component of ensuring that workers are equipped with the knowledge and skills necessary to handle hazardous materials safely and responsibly.
Regulatory Enforcement and Compliance
The introduction of the Workplace Hazardous Materials Information System (WHMIS) in Canada in 1988 was primarily driven by the need to enhance workplace safety and protect workers from the hazards associated with chemical substances. Regulatory enforcement and compliance played a crucial role in this initiative. Prior to WHMIS, there was a significant gap in the regulation of hazardous materials, leading to numerous workplace injuries and illnesses due to inadequate information about the dangers of chemicals. The Canadian government recognized that a standardized system was necessary to ensure that workers had access to critical information about the chemicals they handled, thereby enabling them to take appropriate precautions. WHMIS was designed to provide a comprehensive framework for classifying, labeling, and communicating the hazards of controlled products. This included the development of safety data sheets (SDSs) and standardized labels that provided essential information on the safe handling, use, storage, and disposal of hazardous substances. The regulatory enforcement aspect ensured that manufacturers, suppliers, and employers were held accountable for adhering to these standards. Compliance was mandated through legislation, with penalties for non-compliance aimed at ensuring that all stakeholders took the necessary steps to protect workers. The implementation of WHMIS involved a multi-faceted approach. Regulatory bodies such as Health Canada and the Canadian Centre for Occupational Health and Safety (CCOHS) played key roles in developing and enforcing the regulations. Employers were required to train their employees on WHMIS standards, ensuring that workers understood how to read labels and SDSs, and how to handle hazardous materials safely. This training component was critical in fostering a culture of safety within workplaces. The impact of WHMIS has been significant. By providing workers with accurate and consistent information about chemical hazards, WHMIS has contributed to a reduction in workplace injuries and illnesses related to hazardous materials. The standardized system has also facilitated better compliance with health and safety regulations, as employers are more likely to adhere to guidelines when they are clear and consistent. Additionally, WHMIS has promoted a proactive approach to workplace safety, encouraging employers to implement preventive measures rather than merely reacting to incidents. In terms of regulatory enforcement, WHMIS has empowered regulatory bodies to conduct inspections and audits to ensure compliance. Non-compliance can result in fines, penalties, and even legal action, which serves as a strong deterrent against neglecting safety protocols. This robust enforcement mechanism has helped maintain high standards of safety across various industries. Overall, the introduction of WHMIS in 1988 marked a significant milestone in Canada's commitment to workplace safety. By mandating comprehensive regulatory enforcement and compliance measures, WHMIS has created a safer work environment for millions of Canadians, underscoring the importance of informed and proactive safety practices in the handling of hazardous materials.
Long-term Effects on Workplace Safety Culture
The introduction of the Workplace Hazardous Materials Information System (WHMIS) in Canada in 1988 was primarily driven by the need to enhance workplace safety and protect workers from the hazards associated with chemical substances. Prior to WHMIS, there was a significant gap in the regulation and communication of chemical hazards, leading to numerous workplace injuries and illnesses. WHMIS was designed to ensure that workers have access to critical information about the chemicals they handle, thereby enabling them to take necessary precautions and mitigate risks. This system mandated the labeling of hazardous materials, the provision of safety data sheets (SDS), and the training of employees on how to safely handle these substances. By standardizing this information, WHMIS aimed to foster a culture of safety within workplaces, where employees are empowered with knowledge and equipped with the tools to manage chemical hazards effectively. The long-term effects of WHMIS on workplace safety culture have been profound. Over the years, it has contributed significantly to reducing the incidence of chemical-related accidents and illnesses. By ensuring that workers are well-informed about the hazards they face, WHMIS has promoted a proactive approach to safety, encouraging employees to take personal responsibility for their own safety and that of their colleagues. This has led to a shift in workplace culture, where safety is no longer seen as an afterthought but as an integral part of daily operations. Employers have also benefited from WHMIS, as it has helped them comply with regulatory requirements and reduce the financial burdens associated with workplace injuries and illnesses. Moreover, the standardized approach to hazard communication has facilitated better coordination and cooperation among different stakeholders, including manufacturers, distributors, and end-users of hazardous materials. The impact of WHMIS extends beyond the immediate workplace environment; it has also influenced broader societal attitudes towards occupational health and safety. By raising awareness about chemical hazards and the importance of proper handling and use, WHMIS has contributed to a broader cultural shift towards prioritizing safety in all aspects of life. This has led to increased public demand for safer products and practices, driving innovation in safety technologies and practices. Furthermore, WHMIS has served as a model for other countries and regions, influencing international standards and best practices in chemical hazard communication. In conclusion, the introduction of WHMIS in 1988 marked a significant milestone in the evolution of workplace safety culture in Canada. By providing a comprehensive framework for hazard communication, WHMIS has not only improved workplace safety but also fostered a culture of responsibility and vigilance. As workplaces continue to evolve and new challenges emerge, the principles and practices established by WHMIS remain essential for ensuring that workers are protected and empowered to maintain a safe working environment.