What Is Epdm

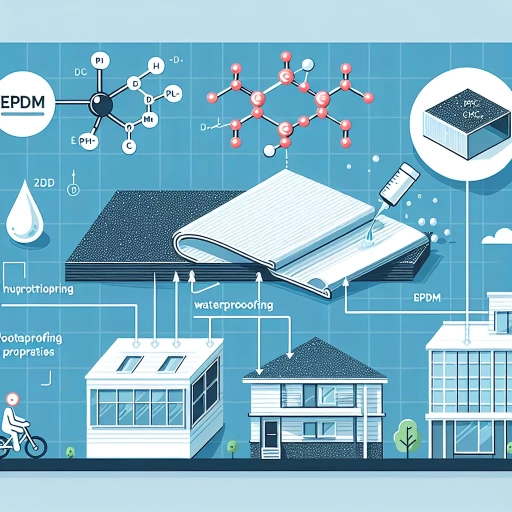
Ethylene Propylene Diene Monomer (EPDM) is a versatile and widely used synthetic rubber known for its exceptional durability and resistance to various environmental factors. This high-quality material has garnered significant attention across multiple industries due to its unique properties and diverse applications. In this article, we will delve into the world of EPDM, starting with an **Introduction to EPDM**, where we will explore its origins, composition, and manufacturing process. We will then examine the **Properties and Characteristics of EPDM**, highlighting its chemical resistance, flexibility, and thermal stability. Finally, we will discuss the **Uses and Benefits of EPDM**, covering its applications in automotive parts, construction materials, and other critical sectors. By understanding these aspects, readers will gain a comprehensive insight into why EPDM remains a cornerstone in modern manufacturing and engineering. Let us begin by diving into the **Introduction to EPDM**.
Introduction to EPDM
Ethylene Propylene Diene Monomer (EPDM) is a versatile and widely used synthetic rubber that has become a cornerstone in various industries due to its exceptional durability and resistance to environmental factors. This article provides a comprehensive introduction to EPDM, delving into its definition and acronym, historical context and development, and common applications. Understanding the definition and acronym of EPDM is crucial as it sets the foundation for grasping its chemical composition and properties. Historically, EPDM has evolved significantly since its inception, with advancements in technology contributing to its widespread adoption. Today, EPDM is utilized in numerous applications, ranging from automotive parts and construction materials to electrical insulation and medical devices. By exploring these aspects, readers will gain a thorough understanding of what EPDM is, how it came to be, and why it remains an essential material in modern industries. Let's begin by examining the definition and acronym of EPDM to establish a clear understanding of this vital material.
Definition and Acronym
**Definition and Acronym** EPDM, an acronym for Ethylene Propylene Diene Monomer, is a synthetic rubber elastomer that has gained widespread recognition for its exceptional durability and versatility. This versatile material is defined by its unique molecular structure, which combines ethylene, propylene, and diene monomers. The ethylene and propylene components provide the backbone of the polymer, while the diene monomer introduces unsaturated bonds that allow for cross-linking during the vulcanization process. This cross-linking enhances the material's mechanical properties, making EPDM highly resistant to heat, ozone, and chemicals. As a result, EPDM is extensively used in various applications such as automotive seals, roofing membranes, and industrial hoses. Its ability to withstand extreme temperatures and harsh environmental conditions makes it an indispensable material in modern engineering and construction. Understanding the definition and acronym of EPDM is crucial for appreciating its role in diverse industries and its contribution to the development of resilient and long-lasting products. In the context of this article, "Introduction to EPDM," grasping the fundamental nature of this material sets the stage for exploring its applications, benefits, and manufacturing processes in greater detail.
Historical Context and Development
**Historical Context and Development** Ethylene Propylene Diene Monomer (EPDM) rubber has a rich historical context that underscores its development and widespread adoption. The journey of EPDM began in the mid-20th century, a period marked by significant advancements in synthetic rubber technology. Following World War II, there was a pressing need for durable, versatile, and weather-resistant materials that could replace natural rubber, which was in short supply due to wartime disruptions. In the 1960s, chemists at the Royal Dutch Shell company successfully synthesized EPDM through the copolymerization of ethylene, propylene, and a diene monomer. This breakthrough led to the commercial production of EPDM, which quickly gained popularity due to its superior properties. Unlike other synthetic rubbers, EPDM exhibited exceptional resistance to heat, ozone, and chemicals, making it an ideal material for various industrial applications. The development of EPDM was further accelerated by advancements in polymer chemistry and manufacturing processes. The introduction of new catalysts and polymerization techniques allowed for the production of EPDM with tailored properties, enhancing its performance in specific uses such as automotive seals, roofing materials, and electrical insulation. By the 1970s and 1980s, EPDM had become a staple in many industries, including construction, automotive, and electrical engineering. Throughout its development, EPDM has continued to evolve with technological innovations. Modern manufacturing processes have improved the consistency and quality of EPDM products, while ongoing research has expanded its range of applications. Today, EPDM is recognized for its sustainability and environmental benefits, as it can be formulated to be recyclable and durable enough to extend the lifespan of products, thereby reducing waste. The historical context of EPDM highlights a narrative of scientific innovation driven by practical needs. From its inception as a response to wartime shortages to its current status as a versatile material in modern industries, EPDM's development reflects human ingenuity in creating solutions that meet evolving demands. This legacy sets the stage for understanding the multifaceted role of EPDM in contemporary applications, as detailed in the subsequent sections of this article.
Common Applications
EPDM (Ethylene Propylene Diene Monomer) rubber is a versatile and widely used synthetic rubber known for its excellent durability, resistance to weathering, and broad range of applications. One of the key reasons EPDM has become a staple in various industries is its ability to withstand harsh environmental conditions, including extreme temperatures, UV radiation, and ozone exposure. This makes it an ideal material for outdoor uses such as roofing membranes, where it provides long-lasting protection against weather elements. In the automotive sector, EPDM is commonly used in seals, gaskets, and hoses due to its resistance to heat, oil, and chemicals. Additionally, its flexibility and resistance to abrasion make it suitable for applications in the construction industry, such as window seals and door gaskets. EPDM's chemical inertness also makes it a preferred choice for water treatment systems and other industrial processes where contamination must be minimized. Furthermore, its electrical insulation properties are beneficial in electrical wiring and cable applications. The versatility of EPDM is further highlighted by its use in consumer products like garden hoses and refrigerator seals, demonstrating its widespread utility across diverse sectors. Overall, the common applications of EPDM underscore its importance as a reliable and adaptable material that meets the demands of various industries and everyday life.
Properties and Characteristics of EPDM
Ethylene Propylene Diene Monomer (EPDM) is a versatile and widely used synthetic rubber known for its exceptional properties and characteristics. This article delves into the key aspects that make EPDM a preferred material in various industries. We will explore its chemical composition and structure, which form the foundation of its unique properties. Additionally, we will examine its physical properties, focusing on durability and flexibility, which are crucial for its applications in sealing, insulation, and other demanding environments. Finally, we will discuss its thermal and electrical properties, highlighting how these attributes contribute to its performance in diverse settings. Understanding these facets is essential for appreciating the full potential of EPDM. To begin, let's first look at the chemical composition and structure of EPDM, which underpins all its other characteristics.
Chemical Composition and Structure
EPDM (Ethylene Propylene Diene Monomer) rubber is a synthetic elastomer known for its exceptional durability and resistance to various environmental factors. The chemical composition and structure of EPDM are crucial in determining its properties and characteristics. EPDM is composed of three primary monomers: ethylene, propylene, and a diene (typically ethylidene norbornene or dicyclopentadiene). The ethylene and propylene units form the backbone of the polymer, while the diene component introduces unsaturation, which is essential for cross-linking during the vulcanization process. This cross-linking enhances the rubber's mechanical strength and elasticity. The molecular structure of EPDM typically consists of a random copolymer arrangement of ethylene and propylene units with the diene monomer dispersed throughout. The ratio of ethylene to propylene can vary, but it is generally around 40-70% ethylene content. This variability allows for the tailoring of specific properties such as flexibility, hardness, and resistance to chemicals and heat. The presence of the diene monomer ensures that EPDM can be vulcanized using sulfur or peroxide curing systems, which are critical for achieving the desired physical properties. The chemical structure also influences EPDM's resistance to ozone, UV light, and extreme temperatures. The absence of double bonds in the main chain (except for those introduced by the diene monomer) reduces the susceptibility to ozone cracking and UV degradation, making EPDM an ideal material for outdoor applications. Additionally, the polymer's low unsaturation level contributes to its excellent resistance to heat and chemicals, including acids, bases, and oils. In summary, the chemical composition and structure of EPDM are fundamental to its robust set of properties and characteristics. The specific arrangement of ethylene, propylene, and diene monomers allows for a versatile material that can withstand harsh conditions while maintaining its integrity and performance over time. This makes EPDM a preferred choice in various industries such as automotive, construction, and industrial manufacturing where durability and reliability are paramount.
Physical Properties: Durability and Flexibility
**Physical Properties: Durability and Flexibility** Ethylene Propylene Diene Monomer (EPDM) is renowned for its exceptional physical properties, particularly its durability and flexibility. These attributes make EPDM a versatile material suitable for a wide range of applications. **Durability** is a key characteristic of EPDM, as it exhibits high resistance to abrasion, weathering, and chemical degradation. This resilience is due to its molecular structure, which includes a high degree of cross-linking that enhances its strength and stability. As a result, EPDM products can withstand harsh environmental conditions such as extreme temperatures, UV radiation, and exposure to ozone without significant deterioration. This durability ensures that EPDM components maintain their performance over extended periods, reducing the need for frequent replacements and thereby saving costs. **Flexibility** is another critical physical property of EPDM. It possesses a high degree of elasticity, allowing it to deform under stress and then return to its original shape once the stress is removed. This flexibility makes EPDM ideal for applications where movement and vibration are present, such as in automotive seals, gaskets, and roofing materials. The material's ability to absorb shock and vibrations without losing its integrity extends its lifespan and enhances its overall performance. Additionally, EPDM's flexibility allows it to be easily molded into various shapes and forms, making it a preferred choice for complex designs and custom applications. The combination of durability and flexibility in EPDM ensures that it remains a reliable and efficient material across diverse industries, from construction to automotive manufacturing. These physical properties collectively contribute to the widespread adoption of EPDM in demanding environments where reliability and longevity are paramount.
Thermal and Electrical Properties
Thermal and electrical properties are crucial aspects of Ethylene Propylene Diene Monomer (EPDM) rubber, influencing its performance in various applications. **Thermal Properties:** EPDM exhibits excellent resistance to heat, with a typical operating temperature range of -40°C to 150°C. This makes it ideal for use in automotive parts, such as engine mounts and seals, as well as in construction materials like roofing and insulation. The material's thermal stability ensures minimal degradation over time, maintaining its elasticity and durability even under extreme temperatures. Additionally, EPDM has a low thermal conductivity, which helps in reducing heat transfer and energy losses in applications like gaskets and seals. **Electrical Properties:** EPDM is known for its excellent electrical insulation properties. It has a high dielectric strength and low dielectric constant, making it suitable for electrical applications such as cable insulation, connectors, and other electrical components. The material's resistance to electrical discharge and its ability to withstand high voltages without significant degradation make it a preferred choice in the electrical industry. Furthermore, EPDM's low moisture absorption rate enhances its electrical performance by reducing the risk of short circuits and electrical failures. This combination of thermal and electrical properties makes EPDM a versatile material that can be reliably used across a wide range of industrial and consumer applications. In summary, the thermal and electrical properties of EPDM rubber are key factors that contribute to its widespread use. Its heat resistance, thermal stability, and excellent electrical insulation capabilities make it an indispensable material in various sectors, ensuring reliable performance and longevity in diverse environments.
Uses and Benefits of EPDM
Ethylene Propylene Diene Monomer (EPDM) is a versatile rubber material that offers a wide range of benefits and applications across various industries. Its unique properties, such as resistance to extreme temperatures, ozone, and chemicals, make it an ideal choice for diverse uses. In the automotive industry, EPDM is crucial for manufacturing seals, gaskets, and other components that require durability and reliability. Additionally, in construction and building materials, EPDM is used in roofing membranes and seals due to its weather-resistant qualities. Furthermore, industrial and consumer products also leverage EPDM for its flexibility and resistance to degradation. This article will delve into these applications, starting with the significant role EPDM plays in the automotive industry. By exploring how EPDM enhances vehicle performance and longevity, we can better understand its broader impact across different sectors. Let's begin by examining the critical applications of EPDM in the automotive industry.
Automotive Industry Applications
The automotive industry heavily relies on Ethylene Propylene Diene Monomer (EPDM) due to its unique properties and versatility. EPDM is widely used in various automotive applications, including seals, gaskets, hoses, and belts. Its excellent resistance to heat, ozone, and chemicals makes it an ideal material for engine components such as radiator hoses, fuel lines, and engine mounts. EPDM's flexibility and durability ensure that these parts can withstand the harsh conditions inside an engine compartment, contributing to the overall reliability and performance of the vehicle. In addition to engine components, EPDM is also used in door seals, window seals, and trunk seals due to its ability to maintain its elasticity over a wide range of temperatures. This ensures that the vehicle remains weather-tight and reduces noise levels by providing a tight seal against air leaks. The material's resistance to UV light and ozone further extends the lifespan of these seals, reducing maintenance costs over time. EPDM's application extends beyond just seals and hoses; it is also used in sound insulation materials within vehicles. By reducing noise levels inside the cabin, EPDM helps create a more comfortable driving environment. Moreover, its use in vibration dampening components like bushings and mounts helps in improving ride quality by absorbing vibrations from the road. The benefits of using EPDM in automotive applications are multifaceted. It enhances vehicle performance by ensuring that critical engine components function optimally under various operating conditions. The material's resistance to degradation from heat and chemicals reduces the need for frequent replacements, thereby lowering maintenance costs and extending the lifespan of vehicle parts. Additionally, EPDM's ability to provide effective seals contributes to better fuel efficiency by minimizing air leaks that could otherwise affect engine performance. Overall, EPDM plays a crucial role in the automotive industry by providing durable, reliable, and high-performance solutions for various applications. Its unique combination of properties makes it an indispensable material for manufacturers seeking to improve vehicle reliability, efficiency, and comfort. As technology continues to evolve, the demand for EPDM is likely to grow further as it remains a key component in modern vehicle design and engineering.
Construction and Building Materials
In the realm of construction and building materials, the selection of appropriate materials is crucial for ensuring durability, sustainability, and performance. Among the diverse array of materials available, Ethylene Propylene Diene Monomer (EPDM) stands out for its versatility and numerous benefits. EPDM, a synthetic rubber, is widely used in various construction applications due to its exceptional properties. One of its primary uses is in roofing, where EPDM membranes provide a waterproof barrier that resists UV rays, ozone, and extreme temperatures. This makes them ideal for flat roofs and other areas where water pooling is a concern. Additionally, EPDM is employed in insulation, sealing, and weatherproofing due to its excellent elasticity and resistance to chemicals and abrasion. In plumbing and HVAC systems, EPDM gaskets and seals ensure tight connections that prevent leaks and maintain system integrity. The material's flexibility also makes it suitable for use in expansion joints and other dynamic applications where movement is anticipated. Furthermore, EPDM's resistance to aging and its ability to withstand harsh environmental conditions make it a preferred choice for outdoor applications such as window seals and door gaskets. From a sustainability perspective, EPDM is valued for its long lifespan, which reduces the need for frequent replacements and thereby minimizes waste. Its recyclability further enhances its environmental credentials. Overall, the use of EPDM in construction offers a blend of performance, durability, and sustainability that makes it an indispensable material in modern building practices.
Industrial and Consumer Products
Industrial and consumer products rely heavily on Ethylene Propylene Diene Monomer (EPDM) due to its unique properties and versatility. EPDM is a synthetic rubber that offers exceptional resistance to heat, ozone, and chemicals, making it an ideal material for various applications. In industrial settings, EPDM is widely used in seals, gaskets, and hoses because of its ability to maintain elasticity and integrity under extreme temperatures and exposure to harsh chemicals. This ensures reliable performance in critical systems such as HVAC, automotive, and construction equipment. In consumer products, EPDM's durability and resistance to weathering make it a preferred choice for outdoor applications. For instance, it is commonly used in roofing materials like rubber shingles and membranes due to its ability to withstand UV radiation and severe weather conditions. Additionally, EPDM is found in automotive parts such as door seals and window gaskets, providing a tight seal that prevents water and air leaks. Its flexibility also makes it suitable for use in vibration dampening components, reducing noise and improving overall vehicle comfort. Moreover, EPDM's chemical resistance extends its utility into household items like dishwashing gloves and other kitchen utensils that need to withstand exposure to detergents and oils. The material's non-toxic nature further enhances its appeal for use in food processing equipment and medical devices where safety is paramount. Overall, the combination of EPDM's physical properties with its cost-effectiveness makes it a valuable component across a broad spectrum of industrial and consumer products, enhancing performance, longevity, and user satisfaction.