What Is A Foundry

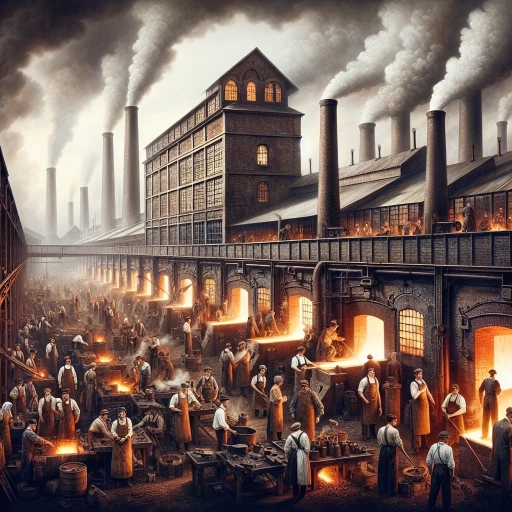
A foundry is a pivotal industrial facility where raw materials are transformed into intricate and precise metal components, playing a crucial role in various sectors such as automotive, aerospace, and construction. The process of creating these components involves several complex steps, from designing and molding to casting and finishing. In this article, we will delve into the world of foundries, starting with an **Introduction to Foundries**, where we explore the history, types, and significance of these industrial hubs. We will then examine **The Foundry Process**, detailing the meticulous stages involved in producing high-quality metal products. Finally, we will discuss **Applications and Innovations in Foundries**, highlighting how advancements in technology are expanding the capabilities and efficiency of modern foundries. By understanding these aspects, readers will gain a comprehensive insight into the vital role that foundries play in modern manufacturing. Let us begin by exploring the foundational aspects of these industrial powerhouses in our **Introduction to Foundries**.
Introduction to Foundries
Foundries, the heart of metal manufacturing, have been pivotal in shaping human civilization from ancient times to the present day. These facilities, where molten metal is cast into various shapes and forms, have evolved significantly over the centuries. To fully appreciate the role of foundries, it is essential to delve into their historical context and understand how they have adapted to technological advancements. This article will provide a comprehensive introduction to foundries, starting with a **Definition and Historical Context** that explores their origins and development. We will then examine the **Types of Foundries**, highlighting the diverse range of casting processes and specialized foundries that cater to different industries. Finally, we will discuss the **Importance in Modern Industry**, revealing how foundries continue to play a crucial role in manufacturing sectors such as automotive, aerospace, and construction. By understanding these aspects, readers will gain a deeper insight into the significance and functionality of foundries, setting the stage for a thorough exploration of this vital industrial sector in our article: **Introduction to Foundries**.
Definition and Historical Context
A foundry, by definition, is a factory where metal casting takes place. This process involves melting metal and pouring it into molds to create specific shapes and designs. The historical context of foundries is rich and spans thousands of years, reflecting the evolution of human technology and industry. The earliest evidence of metal casting dates back to around 3000 BCE, during the Bronze Age, where copper and tin were alloyed to produce bronze. Ancient civilizations such as the Egyptians, Greeks, and Romans extensively used foundries to create tools, weapons, and decorative items. These early foundries were often simple pits or shallow trenches where molten metal was poured into clay or stone molds. As civilizations advanced, so did the techniques and materials used in foundries. The Industrial Revolution marked a significant turning point with the introduction of iron and steel casting. New technologies like the blast furnace and the development of more sophisticated molding techniques enabled mass production and higher precision in metal casting. This period saw the establishment of large-scale foundries that became integral to the manufacturing of machinery, engines, and other industrial equipment. In the 20th century, advancements in materials science and engineering led to the development of new casting processes such as die casting, investment casting, and sand casting. These methods allowed for greater versatility and precision, enabling the production of complex components for various industries including automotive, aerospace, and healthcare. Today, foundries continue to play a crucial role in modern manufacturing. They utilize advanced technologies like 3D printing for mold creation and computer-aided design (CAD) for precision engineering. Modern foundries also focus on sustainability and environmental responsibility, adopting practices that minimize waste and reduce energy consumption. Understanding the historical context of foundries provides a deeper appreciation for their significance in shaping human history and their ongoing importance in contemporary industry. From ancient bronze artifacts to modern-day precision components, the evolution of foundries reflects human ingenuity and the relentless pursuit of technological advancement. This historical backdrop sets the stage for exploring the current state and future directions of foundries in the modern world.
Types of Foundries
Foundries, the heart of metal manufacturing, come in various types, each specializing in different materials and production processes. **Iron Foundries** are among the most common, focusing on casting iron alloys such as gray iron, ductile iron, and malleable iron. These foundries are crucial for producing components like engine blocks, gearboxes, and pipes due to iron's durability and cost-effectiveness. **Steel Foundries** specialize in casting steel alloys, which are known for their high strength and resistance to wear. These foundries cater to industries requiring precision and high-performance parts, such as aerospace and automotive. **Aluminum Foundries** are another significant category, leveraging aluminum's lightweight yet strong properties. These foundries produce a wide range of products from automotive parts to consumer goods like cookware and furniture. **Copper and Brass Foundries** focus on casting non-ferrous metals, which are valued for their excellent electrical conductivity and corrosion resistance. These materials are often used in electrical components, plumbing fixtures, and architectural hardware. **Die Casting Foundries** employ a unique process where molten metal is injected into a die under high pressure. This method allows for the production of intricate shapes with precise dimensions, making it ideal for manufacturing components like car parts, electronic casings, and household appliances. **Investment Casting Foundries**, also known as lost-wax casting, use a wax pattern coated with a refractory material to create highly detailed and complex shapes. This technique is favored in the aerospace and medical industries where precision is paramount. **Sand Casting Foundries** are the oldest and most versatile type, using sand molds to cast a variety of metals including iron, steel, aluminum, and copper. This method is widely used due to its flexibility and cost-effectiveness. **Permanent Mold Casting Foundries** use metal molds instead of sand, allowing for higher production rates and better surface finish. This technique is commonly used for casting aluminum and magnesium alloys. Each type of foundry has its own set of advantages and applications, making them indispensable in various industrial sectors. Understanding these different types is crucial for selecting the appropriate foundry for specific manufacturing needs, ensuring the production of high-quality components that meet industry standards. Whether it's the robustness of iron, the lightness of aluminum, or the precision of investment casting, each foundry type plays a vital role in shaping modern manufacturing processes.
Importance in Modern Industry
In the modern industrial landscape, foundries play a pivotal role that cannot be overstated. These facilities are the backbone of various sectors, including automotive, aerospace, construction, and consumer goods, by providing the critical components necessary for the production of complex machinery and infrastructure. The importance of foundries lies in their ability to cast metals into precise shapes and forms, a process that is essential for manufacturing high-performance parts such as engine blocks, gearboxes, and aircraft components. The precision and versatility offered by foundries enable industries to achieve stringent quality standards and meet demanding specifications. For instance, in the automotive sector, foundries produce cast iron and aluminum parts that are crucial for engine efficiency and vehicle safety. Similarly, in aerospace, the intricate casting of alloys is vital for creating lightweight yet incredibly strong components that withstand extreme conditions. Moreover, advancements in foundry technology have significantly enhanced productivity and efficiency. Modern foundries leverage cutting-edge techniques such as 3D printing, robotic automation, and advanced material science to improve casting accuracy and reduce waste. These innovations not only streamline production processes but also contribute to environmental sustainability by minimizing energy consumption and reducing emissions. Additionally, foundries are integral to the development of new technologies and materials. Research and development within these facilities drive the creation of novel alloys and casting methods that cater to emerging industries like renewable energy and electric vehicles. For example, the production of wind turbine components and electric motor parts relies heavily on specialized casting techniques developed in foundries. The economic impact of foundries is also substantial. They provide employment opportunities across various skill levels, from skilled craftsmen to engineers and technicians. Furthermore, the output from foundries supports a wide range of downstream industries, contributing significantly to GDP and economic growth. In summary, the importance of foundries in modern industry cannot be overstated. They are indispensable for producing high-quality metal components that underpin critical sectors, drive technological innovation, and support economic stability. As industries continue to evolve with new demands for precision, sustainability, and performance, the role of foundries will only become more vital.
The Foundry Process
The foundry process is a complex and multifaceted industry that transforms raw materials into intricate, high-quality products. At its core, this process involves several critical stages that ensure the production of precise and durable components. First, **Pattern Making and Tooling** sets the foundation by creating the molds and tools necessary for casting. This stage requires meticulous attention to detail to ensure that the final product meets exact specifications. Next, **Melting and Casting Techniques** involve the transformation of raw materials into molten form and their careful pouring into the prepared molds. This step demands a deep understanding of metallurgy and casting methods to achieve the desired properties. Finally, **Post-Casting Operations and Finishing** refine the cast product through various treatments and processes, enhancing its strength, appearance, and functionality. Understanding these stages is essential for appreciating the sophistication and importance of the foundry process. In this article, we will delve into each of these critical components, providing a comprehensive overview that transitions seamlessly into an **Introduction to Foundries**.
Pattern Making and Tooling
Pattern making and tooling are crucial components of the foundry process, serving as the foundation for the creation of precise and high-quality castings. In essence, pattern making involves designing and constructing a model or template, known as a pattern, which is an exact replica of the desired final product but slightly larger to account for shrinkage during the casting process. These patterns can be made from various materials such as wood, plastic, or metal, each chosen based on the complexity of the design and the number of castings required. The tooling aspect involves creating molds or dies that will shape the molten metal into the desired form. This can include sand molds, investment molds, or permanent molds like metal dies. The precision and quality of these tools directly influence the final product's accuracy and surface finish. For instance, in sand casting, a sand mold is created around the pattern, while in investment casting, a wax pattern is encased in a refractory material that is then melted out to create a cavity for the molten metal. Advanced technologies such as 3D printing have revolutionized pattern making by allowing for rapid prototyping and complex geometries that would be difficult or impossible to achieve with traditional methods. This not only accelerates the development process but also enables the production of intricate designs with high accuracy. Effective pattern making and tooling require a deep understanding of materials science, mechanical engineering, and manufacturing processes. Engineers must consider factors such as thermal expansion, material properties, and dimensional tolerances to ensure that the final casting meets specifications. Additionally, the durability and longevity of the tools are critical; well-designed and well-maintained tools can significantly reduce production costs and improve overall efficiency. In summary, pattern making and tooling are indispensable steps in the foundry process that demand meticulous attention to detail and a blend of traditional craftsmanship with modern technological advancements. By leveraging these techniques effectively, foundries can produce castings with exceptional precision and quality, meeting the stringent demands of various industries ranging from automotive to aerospace. The synergy between pattern making and tooling ensures that each casting is a faithful representation of its intended design, underscoring their pivotal role in the broader context of the foundry process.
Melting and Casting Techniques
In the intricate world of foundry processes, melting and casting techniques are pivotal steps that transform raw materials into precise, functional components. These techniques are the backbone of the foundry process, ensuring that the final product meets stringent quality standards. Melting involves heating metal alloys to their melting points, typically in furnaces such as electric arc furnaces, induction furnaces, or crucible furnaces. The choice of furnace depends on the type of metal being melted and the desired level of control over the process. For instance, induction furnaces are often used for melting ferrous metals due to their high efficiency and ability to maintain consistent temperatures. Once the metal is molten, it is transferred to a ladle where it may undergo further refining processes such as degassing or alloying to achieve the desired chemical composition. This step is crucial as it ensures that the final product has the required mechanical properties and durability. The molten metal is then poured into a mold, which has been carefully prepared to capture the exact shape and details of the intended part. Casting techniques can vary widely depending on the complexity of the part and the material being used. Sand casting, for example, involves pouring molten metal into sand molds and is commonly used for producing large, complex parts like engine blocks and cylinder heads. Die casting, on the other hand, uses permanent molds made from steel or other durable materials and is ideal for producing high-volume parts with precise dimensions. Gravity casting and investment casting are other techniques that offer unique advantages. Gravity casting relies on gravity to fill the mold, making it suitable for parts that require minimal complexity but high accuracy. Investment casting, also known as lost-wax casting, involves creating a wax model of the part which is then encased in a refractory material before being melted out and replaced with molten metal. This method is particularly useful for producing intricate parts with fine details such as aerospace components or medical devices. The precision and quality of the final product are heavily dependent on these melting and casting techniques. Factors such as temperature control, mold design, and material selection play critical roles in determining the success of the casting process. Modern foundries often employ advanced technologies like computer-aided design (CAD) and simulation software to optimize these processes, ensuring that each part meets or exceeds industry standards. By mastering these techniques, foundries can produce a wide range of products from simple hardware components to complex machinery parts, underscoring their importance in various industries including automotive, aerospace, and healthcare. Ultimately, the art of melting and casting is a blend of traditional craftsmanship and cutting-edge technology that forms the heart of the foundry process.
Post-Casting Operations and Finishing
**Post-Casting Operations and Finishing** Following the casting process, several critical steps are undertaken to transform the raw casting into a finished product, a phase known as post-casting operations and finishing. This stage is integral to the overall foundry process, ensuring that the final product meets the required specifications and quality standards. First, **de-gating** involves removing the gating system, which includes the sprue, runners, and risers, from the casting. This is typically done using saws, grinders, or other mechanical tools to separate these unwanted parts from the main casting. Next, **cleaning** is performed to remove any residual sand, debris, or other contaminants that may have adhered to the casting during the molding process. Techniques such as sand blasting, wire brushing, or chemical cleaning are employed depending on the material and desired finish. **Heat treatment** is another crucial step where the casting is subjected to controlled heating and cooling cycles to achieve specific mechanical properties such as hardness, ductility, or strength. Common heat treatments include annealing, normalizing, quenching, and tempering. These processes can significantly enhance the performance characteristics of the casting. **Machining** often follows heat treatment to refine dimensions and achieve precise tolerances. This involves various machining operations like turning, milling, drilling, and grinding using CNC machines or conventional equipment. Machining ensures that the final product fits perfectly into its intended application. Additionally, **surface finishing** techniques are applied to improve the appearance and functionality of the casting. Methods such as polishing, plating (e.g., chrome or nickel), painting, or applying a protective coating are used to enhance corrosion resistance and aesthetic appeal. **Inspection and testing** are also vital components of post-casting operations. Castings undergo various tests including dimensional checks, visual inspections for defects like porosity or cracks, and non-destructive testing (NDT) such as radiography or ultrasonic testing to ensure they meet quality standards. Finally, **packaging and shipping** prepare the finished products for distribution. Proper packaging protects the castings from damage during transit while ensuring they are delivered in pristine condition to customers. In summary, post-casting operations and finishing are essential phases in the foundry process that transform raw castings into high-quality finished products ready for use in diverse industries ranging from automotive to aerospace. Each step in this process contributes significantly to achieving the desired properties and functionalities of the final product.
Applications and Innovations in Foundries
In the heart of modern manufacturing, foundries play a pivotal role in shaping the future of various industries. These facilities, where molten metal is cast into precise forms, are not just relics of the past but vibrant hubs of innovation and technological advancement. The applications of foundries extend far beyond traditional metal casting, influencing sectors such as automotive and aerospace, where precision and durability are paramount. Technological innovations, including 3D printing and automation, have revolutionized the foundry industry, enabling faster production, higher accuracy, and reduced costs. Additionally, the increasing focus on sustainability and environmental considerations has led to significant improvements in foundry practices, ensuring a greener and more responsible approach to metal casting. As we delve into the world of foundries, it becomes clear that these advancements are not merely incremental but transformative. In this article, we will explore the industrial uses, technological advancements, and sustainability efforts that define the modern foundry landscape, ultimately leading us to a deeper understanding of the critical role these facilities play in our industrial ecosystem. **Introduction to Foundries**.
Industrial Uses: Automotive, Aerospace, and More
Foundries play a pivotal role in various industrial sectors, particularly in automotive, aerospace, and other critical industries. In the automotive sector, foundries are essential for producing high-performance engine components such as cylinder blocks, crankshafts, and gearboxes. These parts require precise casting to ensure durability and efficiency, making foundries indispensable for meeting the stringent quality standards of modern vehicles. For instance, aluminum alloy castings are widely used in vehicle chassis and engine components due to their lightweight yet robust properties, contributing significantly to fuel efficiency and overall vehicle performance. In the aerospace industry, foundries are crucial for manufacturing complex components that must withstand extreme conditions such as high temperatures and stresses. Titanium and nickel-based alloys are commonly cast in foundries for aerospace applications due to their exceptional strength-to-weight ratio and resistance to corrosion. These materials are used in aircraft engines, turbine blades, and other structural components where reliability and safety are paramount. The precision and quality control in foundry processes ensure that these critical parts meet the rigorous standards required for flight safety. Beyond automotive and aerospace, foundries contribute to a wide range of other industries. In the energy sector, foundries produce castings for wind turbines, nuclear reactors, and oil drilling equipment. These castings often involve specialized materials like stainless steel and high-chromium alloys that offer resistance to corrosion and wear under harsh operating conditions. Additionally, foundries supply critical components to the construction industry, including heavy machinery parts such as excavator tracks and hydraulic cylinders. The versatility of foundry processes allows for the production of customized parts tailored to specific industrial needs. Innovations in foundry technology have further enhanced the capabilities of these industries. Advances in 3D printing and simulation software have improved the accuracy and efficiency of casting processes, enabling the creation of complex geometries that were previously impossible to achieve. Moreover, sustainable practices such as recycling metal scrap and using energy-efficient furnaces are becoming more prevalent in modern foundries, reducing environmental impact while maintaining high-quality output. Overall, the role of foundries in supporting key industrial sectors is multifaceted and vital. By providing high-quality castings with precise specifications, foundries enable industries to innovate and produce reliable, efficient products that meet demanding performance criteria. As technology continues to evolve, the importance of foundries will only grow, driving further advancements in materials science and manufacturing processes.
Technological Advancements: 3D Printing and Automation
In the realm of foundries, technological advancements such as 3D printing and automation have revolutionized the industry, transforming traditional manufacturing processes into highly efficient and innovative operations. **3D Printing**, also known as additive manufacturing, allows for the creation of complex geometries and customized parts with unprecedented precision. This technology enables foundries to produce prototypes and final products with reduced material waste and faster turnaround times. For instance, 3D printing can be used to create intricate molds and cores that would be impossible or economically unfeasible to produce using conventional methods. This not only enhances the quality of castings but also opens up new possibilities for design and innovation, allowing foundries to cater to a wider range of industries including aerospace, automotive, and healthcare. **Automation** is another critical technological advancement that has significantly impacted foundry operations. By integrating automated systems, foundries can achieve higher levels of consistency and accuracy in their production processes. Automated machinery can handle tasks such as sand preparation, mold making, and casting with greater precision and speed than manual labor. Additionally, automation reduces the risk of human error, leading to improved product quality and reliability. Advanced robotics and machine learning algorithms further enhance these capabilities by optimizing production workflows, predicting maintenance needs, and ensuring continuous operation with minimal downtime. This integration of automation also allows for real-time monitoring and data analytics, providing valuable insights that can be used to optimize production processes and improve overall efficiency. The combination of 3D printing and automation in foundries has led to a new era of innovation and competitiveness. These technologies enable foundries to adapt quickly to changing market demands and customer requirements, making them more agile and responsive. Moreover, they facilitate the development of new materials and alloys that can be tailored for specific applications, further expanding the capabilities of foundry operations. As these technologies continue to evolve, they are likely to play an even more pivotal role in shaping the future of foundries, driving advancements in both process efficiency and product innovation. By embracing these cutting-edge technologies, foundries can maintain their competitive edge while contributing to broader industrial advancements across various sectors.
Sustainability and Environmental Considerations
In the context of foundries, sustainability and environmental considerations are paramount, as these facilities have historically been significant contributors to industrial pollution. Modern foundries are increasingly adopting innovative practices to mitigate their environmental footprint, aligning with global efforts to achieve sustainable development. One key area of focus is energy efficiency; advanced technologies such as electric induction furnaces and heat recovery systems are being integrated to reduce energy consumption and lower greenhouse gas emissions. Additionally, foundries are transitioning towards cleaner energy sources like solar and wind power, further diminishing their reliance on fossil fuels. Water conservation is another critical aspect, with many foundries implementing water recycling and treatment systems to minimize wastewater discharge. This not only conserves this precious resource but also reduces the amount of pollutants released into waterways. Furthermore, foundries are adopting best practices in waste management, including recycling metal scrap and reusing sand from casting processes. This circular economy approach significantly reduces the need for virgin materials and decreases landfill waste. Innovative casting techniques and materials are also playing a crucial role in enhancing sustainability. For instance, the use of 3D printing in foundries allows for more precise casting, reducing material waste and energy consumption associated with traditional methods. Moreover, research into new materials like biodegradable binders and sustainable alloys is gaining traction, offering alternatives that are less harmful to the environment. Regulatory compliance and stakeholder engagement are also driving sustainability initiatives in foundries. Many countries have implemented stringent environmental regulations that foundries must adhere to, prompting the adoption of cleaner technologies and processes. Moreover, consumer demand for eco-friendly products is influencing the industry, with companies recognizing the value of sustainability in maintaining a positive brand image and ensuring long-term viability. Ultimately, the integration of sustainability and environmental considerations into foundry operations is not just a moral imperative but also a strategic necessity. By embracing these principles, foundries can reduce operational costs, enhance their reputation, and contribute to a more sustainable future. As the industry continues to evolve, it is clear that innovative applications and technologies will be essential in balancing economic growth with environmental stewardship.