What Happens To Metal Pipe When Heated With 100c Liquid

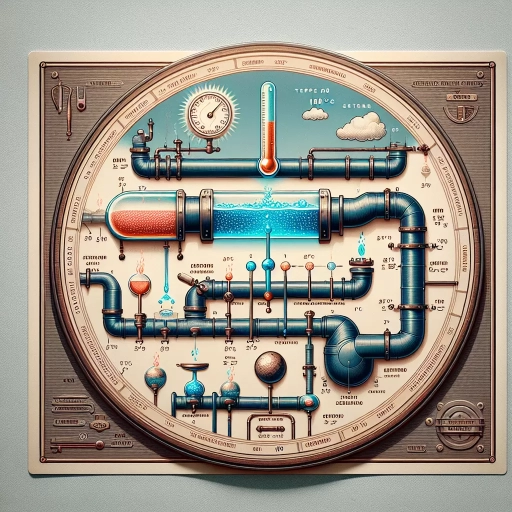
When a metal pipe is exposed to a 100°C liquid, several critical processes occur that can significantly impact its structure, functionality, and safety. Understanding these phenomena is crucial for engineers, technicians, and anyone working with metal pipes in various industrial settings. This article delves into the comprehensive effects of heating metal pipes, focusing on three key aspects: Thermal Expansion and Deformation, Material Properties and Heat Transfer, and Safety Considerations and Practical Implications. As we explore these topics, it becomes evident that the initial and most immediate effect is the thermal expansion of the metal. This expansion can lead to deformation, altering the pipe's dimensions and potentially compromising its integrity. By examining how heat influences the physical properties of metal and the mechanisms of heat transfer, we can better predict and manage these changes. Additionally, considering the safety implications and practical applications of these principles is essential for ensuring safe and efficient operations. Let us begin by examining the fundamental concept of Thermal Expansion and Deformation, which sets the stage for understanding the broader impacts of heating metal pipes.
Thermal Expansion and Deformation
Thermal expansion and deformation are fundamental concepts in physics and engineering, highlighting the critical impact of temperature changes on materials. When materials are subjected to varying temperatures, they undergo significant changes in their dimensions and structure. This article delves into three key aspects of thermal expansion and deformation: the linear expansion of metals, radial expansion and its effects on pipe diameters, and the potential for structural deformation. Understanding these phenomena is crucial for designing and maintaining infrastructure, machinery, and other systems that operate under diverse thermal conditions. The linear expansion of metals, for instance, is a direct consequence of increased atomic spacing as temperatures rise, leading to predictable length changes. Radial expansion, on the other hand, affects the diameter of pipes and cylinders, which can have profound implications for fluid dynamics and structural integrity. Furthermore, the potential for structural deformation due to thermal stress can compromise the safety and functionality of entire systems. Each of these aspects underscores the importance of considering thermal effects in engineering and construction. By grasping these principles, engineers can mitigate risks associated with thermal changes, ensuring that structures and systems perform optimally across a range of temperatures. Let us begin by examining the linear expansion of metals, a foundational concept that sets the stage for understanding more complex thermal phenomena.
Linear Expansion of Metal
When a metal pipe is exposed to a 100°C liquid, it undergoes a phenomenon known as linear expansion, which is a fundamental aspect of thermal expansion and deformation. Linear expansion refers to the increase in length of a material when its temperature rises. This occurs because the atoms or molecules in the metal gain kinetic energy and start vibrating more vigorously, causing them to move further apart. As a result, the interatomic distances increase, leading to an overall elongation of the material. In metals, this expansion is typically uniform and predictable, following the principle that the change in length (\(\Delta L\)) is directly proportional to the original length (\(L\)), the change in temperature (\(\Delta T\)), and the coefficient of linear thermal expansion (\(\alpha\)). The coefficient of thermal expansion is a material property that quantifies how much a material expands per degree of temperature increase. For example, if a metal pipe has a length of 1 meter and a coefficient of thermal expansion of \(10^{-5}\) per degree Celsius, then heating it from room temperature (20°C) to 100°C would result in an increase in length of approximately 0.8 millimeters. The linear expansion of metal pipes can have significant practical implications. In engineering and construction, it is crucial to account for thermal expansion to avoid structural failures or damage. For instance, in piping systems, expansion joints or flexible connections are often used to accommodate the increased length of pipes when they are heated. Failure to do so could lead to excessive stress, leakage, or even rupture of the pipe. Moreover, understanding linear expansion is essential for designing and maintaining various industrial equipment and infrastructure. For example, in power plants, where high-temperature fluids are common, accurate calculations of thermal expansion are necessary to ensure the integrity of pipes and other components. Similarly, in automotive engineering, the thermal expansion of engine components must be considered to prevent overheating and potential failure. In addition to practical applications, the study of linear expansion also provides insights into the fundamental properties of materials. By measuring how different metals expand under various temperature conditions, researchers can gain a deeper understanding of their atomic structures and bonding mechanisms. This knowledge can be used to develop new materials with tailored thermal properties, which is particularly important in fields such as aerospace and electronics where temperature stability is critical. In conclusion, the linear expansion of metal pipes when heated with a 100°C liquid is a critical aspect of thermal expansion and deformation. It is governed by well-defined physical principles and has significant implications for engineering design, material science, and industrial operations. By understanding and accurately predicting this phenomenon, engineers and scientists can ensure the reliability and safety of various systems and structures that involve metal components subjected to temperature changes.
Radial Expansion and Pipe Diameter Changes
When a metal pipe is subjected to heating, such as being exposed to a 100°C liquid, it undergoes significant changes due to thermal expansion and deformation. One critical aspect of this phenomenon is radial expansion, which refers to the outward movement of the pipe's diameter as it heats up. This expansion occurs because the atoms within the metal gain kinetic energy and start vibrating more vigorously, causing them to move further apart. As a result, the overall dimensions of the pipe increase. The magnitude of radial expansion depends on several factors, including the type of metal, its initial temperature, and the temperature change it experiences. For instance, materials with higher coefficients of thermal expansion (CTE) will exhibit more pronounced radial expansion compared to those with lower CTE values. Common metals used in piping, such as copper and steel, have different CTEs; copper expands more than steel for the same temperature increase. Pipe diameter changes due to radial expansion can have practical implications in various engineering applications. In plumbing systems, for example, this expansion must be accounted for to prevent damage or leakage. Engineers often use expansion joints or flexible connections to accommodate these changes, ensuring that the system remains intact and functional even under varying thermal conditions. Moreover, understanding radial expansion is crucial in designing and maintaining industrial processes where high temperatures are involved. In chemical plants or power generation facilities, pipes may be exposed to fluids at elevated temperatures, leading to significant radial expansion. If not properly managed, this could result in structural instability or even catastrophic failures. In addition to practical considerations, the study of radial expansion and pipe diameter changes contributes to our broader understanding of material science and thermodynamics. By analyzing how different materials respond to temperature changes, researchers can develop new materials with tailored properties for specific applications. This knowledge also aids in optimizing manufacturing processes and improving the durability of engineered systems. In conclusion, radial expansion and the resulting changes in pipe diameter are fundamental aspects of thermal expansion and deformation. These phenomena are not merely theoretical concepts but have direct implications for engineering design, safety, and efficiency. As technology advances and more complex systems are developed, understanding and managing thermal effects will remain a critical component of ensuring the reliability and longevity of metal pipes under various thermal conditions.
Potential for Structural Deformation
When a metal pipe is subjected to heating with a 100°C liquid, the potential for structural deformation becomes a critical concern. Thermal expansion, the tendency of materials to expand when heated, is a fundamental principle that governs this scenario. As the metal pipe absorbs heat from the liquid, its atoms gain kinetic energy and start vibrating more vigorously. This increased atomic motion leads to an expansion of the material's lattice structure, causing the pipe to elongate and possibly change its shape. The extent of this deformation depends on several factors, including the type of metal, its initial dimensions, and the rate at which it is heated. For instance, metals with higher coefficients of thermal expansion (CTE) such as aluminum or copper will deform more significantly than those with lower CTEs like stainless steel or titanium. Additionally, if the heating process is rapid, it can create thermal gradients within the pipe where some sections expand more than others, leading to uneven deformation and potential stress concentrations. Structural deformation can manifest in various ways. Uniform heating might result in a straightforward elongation of the pipe, but non-uniform heating can cause bending or warping. In extreme cases, if the pipe is constrained at both ends and unable to expand freely, it may experience compressive stresses that could lead to buckling or even failure. Furthermore, repeated cycles of heating and cooling can induce fatigue in the material, weakening its structural integrity over time. Understanding these dynamics is crucial for designing and operating systems that involve heated metal pipes. Engineers must consider thermal expansion when specifying pipe materials and dimensions to ensure that any deformation does not compromise the system's functionality or safety. This includes selecting materials with appropriate thermal properties, designing expansion joints or flexible connections to accommodate movement, and implementing control measures to maintain uniform heating rates. In practical applications such as industrial piping systems or heat exchangers, managing thermal expansion is essential for maintaining operational efficiency and preventing costly failures. For example, in power plants where high-temperature fluids are used, careful consideration of pipe materials and their thermal expansion characteristics helps prevent catastrophic failures that could lead to downtime and significant economic losses. In conclusion, the potential for structural deformation in metal pipes heated with a 100°C liquid is a complex issue influenced by material properties, heating rates, and system design. By understanding these factors and implementing appropriate engineering solutions, it is possible to mitigate risks associated with thermal expansion and ensure reliable performance of critical infrastructure. This knowledge underscores the importance of integrating thermal analysis into the design process for any system involving heated metal components.
Material Properties and Heat Transfer
Understanding material properties is crucial for optimizing heat transfer in various engineering and scientific applications. The behavior of materials under thermal conditions can significantly impact the efficiency and safety of systems ranging from electronic devices to industrial processes. This article delves into three key aspects of material properties that influence heat transfer: conductivity and heat absorption rates, specific heat capacity and energy absorption, and thermal diffusivity and temperature distribution. Each of these properties plays a distinct role in how materials interact with heat. Conductivity and heat absorption rates determine how quickly heat is transferred through a material, which is vital for applications such as cooling systems and thermal insulation. Specific heat capacity and energy absorption reveal how much energy a material can absorb without a significant change in temperature, making it essential for understanding thermal energy storage and release. Thermal diffusivity and temperature distribution explain how heat spreads within a material over time, affecting the uniformity of temperature across different parts of the system. By examining these properties, engineers and scientists can design more efficient, reliable, and safe systems that manage heat effectively. Let's begin by exploring the first critical aspect: conductivity and heat absorption rates, which form the foundation of understanding how materials facilitate or hinder the flow of thermal energy.
Conductivity and Heat Absorption Rates
When considering the behavior of a metal pipe subjected to heating with a 100°C liquid, it is crucial to understand the material properties that govern heat transfer, particularly conductivity and heat absorption rates. Conductivity, or thermal conductivity, is a measure of how efficiently a material can transfer heat through itself. Metals generally have high thermal conductivity compared to other materials, meaning they can effectively distribute heat across their structure. For instance, metals like copper and aluminum are renowned for their excellent thermal conductivity, making them ideal for applications such as heat exchangers and cookware. Heat absorption rate, on the other hand, is influenced by the specific heat capacity of the material. Specific heat capacity is the amount of heat energy required to raise the temperature of a unit mass of a substance by one degree Celsius. Metals typically have lower specific heat capacities compared to liquids or gases, which means they absorb and release heat more quickly. When a metal pipe is heated with a 100°C liquid, the high thermal conductivity of the metal allows it to rapidly absorb and distribute the heat along its length. This efficient heat transfer minimizes temperature gradients within the pipe, ensuring that the entire structure heats up uniformly. The interplay between conductivity and heat absorption rates is critical in determining how quickly and evenly a metal pipe will heat up. For example, if you were to immerse a copper pipe in boiling water (100°C), the copper would rapidly absorb the heat due to its high thermal conductivity and relatively low specific heat capacity. This would result in a quick rise in temperature throughout the pipe, with minimal lag or hotspots. Conversely, materials with lower thermal conductivity and higher specific heat capacities would heat more slowly and potentially develop significant temperature gradients. Understanding these material properties is essential for designing and operating systems that involve heat transfer, such as plumbing, HVAC systems, and industrial processes. In practical applications, selecting materials with appropriate thermal properties can significantly impact efficiency, safety, and overall performance. For instance, in plumbing systems where hot water is transported over long distances, using pipes made from materials with high thermal conductivity can reduce energy losses and ensure consistent water temperatures at the point of use. In summary, the conductivity and heat absorption rates of metals play pivotal roles in determining how a metal pipe responds when heated with a 100°C liquid. High thermal conductivity ensures rapid and uniform heat distribution, while specific heat capacity influences how quickly the material absorbs and releases heat. These properties are fundamental to optimizing heat transfer in various engineering applications, making them crucial considerations in material selection and system design.
Specific Heat Capacity and Energy Absorption
When considering the behavior of a metal pipe exposed to a 100°C liquid, understanding the concept of specific heat capacity and its role in energy absorption is crucial. Specific heat capacity, denoted by the symbol \(c\), is a material property that quantifies the amount of heat energy required to raise the temperature of a unit mass of a substance by one degree Celsius (or Kelvin). This property varies significantly among different materials, influencing how they absorb and distribute thermal energy. For metals, specific heat capacity is generally lower compared to other materials like water or certain polymers. For instance, the specific heat capacity of copper is approximately 0.385 J/g°C, while that of aluminum is about 0.903 J/g°C. When a metal pipe is heated with a 100°C liquid, the pipe's material will absorb heat energy based on its specific heat capacity. The lower the specific heat capacity, the less energy is needed to raise the temperature of the metal by one degree. The process involves several key steps: first, the liquid transfers heat to the surface of the metal pipe through convection. This heat then penetrates into the metal through conduction, where it is absorbed by the atoms or molecules of the metal, causing them to vibrate more vigorously and thus increasing their kinetic energy. The amount of heat absorbed is directly proportional to the mass of the metal, its specific heat capacity, and the change in temperature. In practical terms, if you have two metal pipes made from different materials but identical in size and shape—one made from copper and one from aluminum—and you expose them both to the same 100°C liquid, they will heat up at different rates due to their differing specific heat capacities. The aluminum pipe, with its higher specific heat capacity, will require more energy to reach the same temperature as the copper pipe. Understanding these principles is essential for various engineering applications, such as designing heat exchangers, thermal insulation systems, and even safety protocols for handling hot materials. For example, in industrial processes where metals are heated or cooled rapidly, knowing their specific heat capacities helps engineers predict thermal stresses and potential deformation or damage to the material. In summary, specific heat capacity plays a pivotal role in determining how efficiently a metal pipe absorbs energy when exposed to a hot liquid. This material property not only affects the rate at which the pipe heats up but also influences its overall thermal behavior and stability under varying temperature conditions. By grasping these fundamental concepts, engineers can better design and manage systems involving heat transfer and material interactions, ensuring optimal performance and safety in diverse industrial and technological applications.
Thermal Diffusivity and Temperature Distribution
Thermal diffusivity is a critical material property that influences the temperature distribution within a metal pipe when it is heated, such as with a 100°C liquid. This property quantifies how quickly heat spreads through a material, essentially measuring the rate at which temperature changes propagate. In the context of a metal pipe, thermal diffusivity determines how rapidly the heat from the 100°C liquid penetrates and distributes throughout the pipe's cross-section. When a metal pipe is exposed to a heated liquid, the initial contact between the liquid and the pipe's surface causes an immediate rise in temperature at that interface. The thermal diffusivity of the metal dictates how swiftly this heat is conducted away from the surface and into the bulk of the material. For metals with high thermal diffusivity, such as copper or aluminum, heat is transferred rapidly, leading to a more uniform temperature distribution across the pipe's thickness relatively quickly. Conversely, metals with lower thermal diffusivity, like stainless steel or cast iron, exhibit slower heat transfer rates, resulting in a more pronounced temperature gradient within the pipe. The temperature distribution within the pipe is further influenced by factors such as the pipe's geometry, the initial temperature of the metal, and any boundary conditions imposed by external environments. For instance, if one end of the pipe is insulated while the other is exposed to ambient air, there will be a significant difference in how heat is dissipated along its length. Understanding these dynamics is crucial for predicting and managing thermal stresses that can arise due to non-uniform heating, which can lead to material deformation or even failure. In practical applications, knowing the thermal diffusivity of a metal pipe allows engineers to design systems that optimize heat transfer efficiency while minimizing potential risks associated with thermal gradients. For example, in heat exchangers or piping systems used in chemical processing plants, selecting materials with appropriate thermal diffusivity ensures that fluids are heated uniformly without causing undue stress on the pipes. Additionally, this knowledge aids in the selection of materials for specific applications where uniform temperature distribution is critical, such as in aerospace engineering where materials must withstand extreme thermal conditions. In summary, thermal diffusivity plays a pivotal role in determining the temperature distribution within a metal pipe when it is heated by a 100°C liquid. By understanding this material property and its implications on heat transfer, engineers can better design and manage systems involving heated metals, ensuring both efficiency and safety in various industrial and engineering contexts. This understanding is integral to the broader topic of material properties and heat transfer, highlighting the importance of considering thermal diffusivity in any scenario where metals are subjected to temperature changes.
Safety Considerations and Practical Implications
When discussing safety considerations and practical implications in various industrial and engineering contexts, it is crucial to address several key aspects that can significantly impact the integrity and operational safety of systems. This article delves into three critical areas: the risk of thermal shock and material failure, the impact on pipe integrity and leak potential, and operational safety precautions and guidelines. Understanding these elements is essential for preventing catastrophic failures and ensuring continuous, safe operation. Thermal shock, for instance, can lead to sudden and unexpected material failures, which can have devastating consequences. Similarly, the integrity of pipes is paramount as any compromise can result in leaks that pose significant environmental and health risks. Finally, adhering to operational safety precautions and guidelines is vital for mitigating these risks and maintaining a safe working environment. By examining these factors, we can better prepare for and respond to potential hazards. Let us begin by exploring the risk of thermal shock and material failure, a critical consideration that underscores the importance of careful design and maintenance practices.
Risk of Thermal Shock and Material Failure
When a metal pipe is subjected to heating with a 100°C liquid, the risk of thermal shock and material failure becomes a critical safety consideration. Thermal shock occurs when a material undergoes rapid temperature changes, causing significant stress due to the differential expansion and contraction of its components. For metal pipes, this can lead to catastrophic failure if not managed properly. The primary concern is the sudden and extreme temperature gradient that develops across the pipe wall. Metals have different coefficients of thermal expansion, meaning they expand and contract at varying rates with temperature changes. When one side of the pipe is rapidly heated while the other side remains cooler, it creates uneven stresses that can exceed the material's yield strength. This can result in cracking, warping, or even complete rupture of the pipe. Moreover, the type of metal used in the pipe plays a crucial role in determining its susceptibility to thermal shock. For instance, materials like stainless steel and titanium have higher thermal shock resistance compared to carbon steel or aluminum due to their lower coefficients of thermal expansion and higher thermal conductivity. However, even these more resilient materials can fail if exposed to extreme and rapid temperature fluctuations. Practical implications of thermal shock include the need for careful design and operation of piping systems. Engineers must consider the thermal gradients that may arise during normal operation and take steps to mitigate them. This could involve using insulation to reduce heat transfer rates, selecting materials with appropriate thermal properties, or implementing gradual heating and cooling procedures to avoid sudden temperature changes. Additionally, regular maintenance and inspection are essential to identify any signs of thermal stress or material degradation before they lead to failure. Techniques such as non-destructive testing (NDT) can help detect cracks or other defects that may have developed due to thermal shock. In summary, the risk of thermal shock and material failure when heating a metal pipe with a 100°C liquid is significant and must be addressed through careful material selection, system design, and operational practices. By understanding these risks and implementing appropriate safety measures, industries can prevent costly failures and ensure the safe operation of their piping systems.
Impact on Pipe Integrity and Leak Potential
When metal pipes are exposed to liquids heated to 100°C, several critical factors come into play that significantly impact pipe integrity and leak potential. The primary concern is thermal expansion, where the metal material expands as it absorbs heat. This expansion can lead to increased stress on the pipe, particularly if it is constrained by fittings or supports that restrict its movement. Over time, repeated cycles of heating and cooling can cause fatigue, weakening the pipe's structural integrity and increasing the likelihood of cracks or fractures. Another significant issue is the potential for corrosion acceleration. Many metals, especially those commonly used in piping such as carbon steel and stainless steel, are more susceptible to corrosion at elevated temperatures. The presence of hot liquid can accelerate chemical reactions that degrade the pipe material, leading to pitting, scaling, or other forms of corrosion that compromise the pipe's wall thickness and strength. Additionally, if the liquid contains corrosive substances or contaminants, this effect can be exacerbated. The thermal gradient across the pipe wall also plays a crucial role. When a hot liquid flows through a pipe, it creates a temperature difference between the inner and outer surfaces of the pipe. This gradient can cause uneven expansion and contraction, leading to residual stresses that may result in warping or distortion of the pipe. Such deformations can disrupt the sealing integrity of connections and joints, increasing the risk of leaks. Furthermore, high-temperature liquids can affect the properties of any coatings or linings applied to the pipe. These protective layers are designed to prevent corrosion and ensure smooth flow but may degrade or flake off when exposed to elevated temperatures, exposing the underlying metal to corrosive environments. From a practical standpoint, these factors necessitate careful consideration in the design and operation of piping systems. Engineers must select materials that are suitable for the expected temperature range and ensure that pipes are adequately supported to accommodate thermal expansion. Regular inspections and maintenance are crucial to detect early signs of corrosion or damage before they lead to catastrophic failures. In terms of safety considerations, the potential for leaks due to compromised pipe integrity poses significant risks. Leaks involving hot liquids can lead to severe burns and injuries, while leaks of hazardous substances can result in environmental contamination and health hazards. Therefore, it is imperative to implement robust safety protocols, including emergency shutdown procedures and leak detection systems, to mitigate these risks effectively. In conclusion, heating metal pipes with 100°C liquid introduces a range of challenges that must be addressed to maintain pipe integrity and prevent leaks. By understanding these thermal, corrosive, and mechanical impacts, engineers and operators can take proactive steps to ensure the safe and reliable operation of piping systems. This includes selecting appropriate materials, designing for thermal expansion, conducting regular inspections, and implementing robust safety measures to protect against potential failures.
Operational Safety Precautions and Guidelines
When dealing with the heating of metal pipes, particularly those exposed to 100°C liquids, operational safety precautions and guidelines are paramount to prevent accidents and ensure a safe working environment. The primary concern is thermal expansion, as metals expand when heated, which can lead to increased pressure within the pipe system. To mitigate this risk, it is crucial to implement proper thermal expansion compensation mechanisms such as expansion joints or flexible connections. These components allow for the safe absorption of thermal expansion without causing undue stress on the piping system. Additionally, the material selection of the pipe itself is critical. Different metals have varying thermal properties; for instance, stainless steel and certain alloys are more resistant to high temperatures compared to carbon steel. Ensuring that the pipe material is compatible with the operating temperature can prevent catastrophic failures such as bursting or cracking. Regular maintenance and inspection are also essential. Before exposing pipes to high-temperature liquids, a thorough inspection should be conducted to identify any potential weaknesses or defects. This includes checking for signs of corrosion, wear, and tear, as well as ensuring all connections and fittings are secure. Operational guidelines should include strict protocols for temperature control. Monitoring the temperature of both the liquid and the pipe is vital to avoid overheating. Automated temperature control systems can be implemented to maintain a safe operating range and alert personnel if temperatures exceed safe limits. Furthermore, personnel training is indispensable. Workers handling heated pipes must be educated on the hazards associated with thermal expansion and how to respond in case of an emergency. This includes knowing how to safely handle hot equipment, understanding emergency shutdown procedures, and being aware of personal protective equipment (PPE) requirements. In terms of practical implications, adhering to these safety precautions can significantly reduce downtime due to equipment failure and minimize the risk of workplace injuries. Compliance with industry standards such as those set by ASME (American Society of Mechanical Engineers) or API (American Petroleum Institute) ensures that operations are conducted within established safety parameters. Moreover, environmental considerations should not be overlooked. Leaks or ruptures in heated pipes can result in the release of hazardous materials into the environment. Therefore, having contingency plans in place for spill response and containment is essential. In conclusion, operational safety precautions and guidelines are critical when heating metal pipes with 100°C liquids. By focusing on material selection, thermal expansion compensation, regular maintenance, strict temperature control, personnel training, compliance with industry standards, and environmental considerations, organizations can ensure a safe and efficient operation while minimizing risks associated with high-temperature processes. These measures not only protect personnel but also contribute to the overall reliability and sustainability of industrial operations.