What Is A Taper

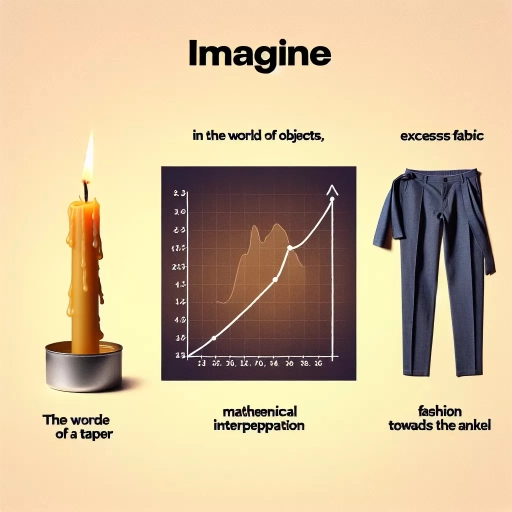
In the realm of precision and craftsmanship, the concept of a taper plays a crucial role, particularly in fields such as engineering, manufacturing, and even everyday DIY projects. A taper is essentially a gradual reduction in diameter or thickness, often used to create smooth transitions between different sizes or shapes. This article delves into the multifaceted world of tapers, exploring their fundamental principles, diverse types, and practical applications. We begin by **Understanding the Concept of a Taper**, where we dissect the core definition and significance of tapers. Next, we examine **Types and Variations of Tapers**, highlighting the various forms they can take and their specific uses. Finally, we discuss **Practical Uses and Benefits of Tapers**, illustrating how these precision elements enhance performance and efficiency across different industries. By grasping these key aspects, readers will gain a comprehensive understanding of tapers and their indispensable role in modern technology and craftsmanship. Let's start by **Understanding the Concept of a Taper**.
Understanding the Concept of a Taper
In the realm of engineering, design, and manufacturing, the concept of a taper is a fundamental principle that underpins various applications across diverse industries. A taper, essentially, is a gradual reduction in diameter or thickness of an object, which can significantly impact its functionality and performance. To fully grasp the importance and versatility of tapers, it is crucial to delve into their definition and basic principles, understanding how they are defined and how they operate. Additionally, exploring the historical context and evolution of tapers provides valuable insights into their development and adaptation over time. Finally, examining common applications across industries such as aerospace, automotive, and construction highlights the widespread utility and critical role tapers play in modern engineering. By understanding these facets, we can appreciate the intricate details and broad implications of tapers, ultimately enhancing our comprehension of this essential concept. This article aims to provide a comprehensive overview, transitioning seamlessly into the core aspects of **Understanding the Concept of a Taper**.
Definition and Basic Principles
Understanding the concept of a taper begins with grasping its definition and basic principles. A taper, in various contexts such as engineering, manufacturing, and even sports, refers to a gradual reduction in size or thickness over a specific length or distance. This concept is crucial for ensuring smooth transitions, optimal performance, and safety in different applications. In engineering and manufacturing, a taper is often used to connect two components of different diameters or to facilitate the assembly and disassembly of parts. For instance, in mechanical engineering, tapered shafts and holes allow for precise fitting without the need for additional fasteners, enhancing the structural integrity and reducing wear and tear. The basic principle here involves creating a conical shape where the diameter decreases uniformly along the length of the component. This uniform reduction ensures that the transition from one diameter to another is seamless, minimizing stress concentrations that could lead to failure. In sports, particularly in running and cycling, a taper refers to the period of reduced training intensity and volume before a major competition. This principle is based on the physiological need for athletes to allow their bodies to recover from intense training, thereby optimizing performance on race day. The taper period typically involves a gradual decrease in training load over several weeks, allowing muscles to repair and adapt while maintaining peak fitness levels. The underlying principle across these contexts is the importance of gradual change. Whether it's a physical component or an athlete's training regimen, abrupt changes can lead to inefficiencies or even failures. A well-designed taper ensures that transitions are smooth and effective, whether it's facilitating mechanical connections or enhancing athletic performance. Moreover, understanding the concept of a taper involves recognizing its application in various fields beyond engineering and sports. In finance, for example, a taper can refer to the gradual reduction of monetary policy interventions by central banks. Here, the principle involves slowly withdrawing stimulus measures to avoid economic shocks and ensure a stable transition to normal market conditions. In summary, the definition and basic principles of a taper revolve around the concept of gradual reduction or transition. This principle is essential for achieving optimal outcomes in diverse fields by ensuring smooth transitions, enhancing performance, and minimizing risks associated with abrupt changes. By understanding how tapers work and their applications, individuals can better appreciate the intricacies involved in design, manufacturing, athletic training, and even economic policy-making.
Historical Context and Evolution
The concept of a taper, though often associated with modern manufacturing and engineering, has a rich historical context that spans centuries. The evolution of tapering techniques is deeply intertwined with advancements in toolmaking, precision engineering, and the needs of various industries. In ancient civilizations, such as Egypt and Greece, craftsmen used rudimentary methods to create tapered shapes for architectural elements, tools, and weapons. These early techniques involved manual labor and basic tools like chisels and files. As civilizations progressed, so did the sophistication of tapering methods. During the Industrial Revolution, the introduction of machine tools revolutionized the process. Lathes and milling machines enabled mass production of tapered parts with greater precision and consistency. This period also saw the development of standardized taper systems, such as the Morse taper and the Jarno taper, which became essential in woodworking and metalworking industries. In the 20th century, advancements in materials science and computer-aided design (CAD) further refined tapering techniques. The advent of CNC (Computer Numerical Control) machining allowed for intricate and precise tapers to be produced with ease, catering to the demands of aerospace, automotive, and medical industries. Modern manufacturing also incorporates advanced materials like composites and alloys, which require specialized tapering methods to ensure optimal performance. The evolution of tapering is not just about technological advancements but also about understanding the underlying principles of mechanics and physics. The concept of a taper involves a gradual reduction in diameter or thickness, which affects stress distribution, structural integrity, and functional efficiency. This understanding has been crucial in designing everything from drill bits to aircraft components. Today, the concept of a taper is integral to various fields, including engineering, architecture, and even art. In engineering, precise tapers are critical for ensuring smooth operation and longevity of machinery. In architecture, tapered columns and beams provide both aesthetic appeal and structural support. Even in artistic endeavors like woodworking and sculpture, tapered shapes can add elegance and functionality to creations. Understanding the historical context and evolution of tapers provides a deeper appreciation for the complexity and importance of this seemingly simple concept. From ancient hand tools to modern CNC machines, the journey of tapering reflects human ingenuity and the relentless pursuit of precision and innovation. This historical backdrop underscores why tapers remain a fundamental aspect of modern design and manufacturing, highlighting their significance in achieving optimal performance across diverse applications.
Common Applications Across Industries
In the realm of precision engineering and manufacturing, the concept of a taper is universally applicable across various industries, each leveraging its unique benefits to enhance performance, efficiency, and safety. In **aerospace engineering**, tapers are crucial for the design of aircraft components such as engine nozzles and propeller shafts, where precise angular dimensions ensure optimal airflow and structural integrity. Similarly, in **automotive manufacturing**, tapered parts are used in engine blocks, gearboxes, and axles to facilitate smooth power transmission and reduce wear on moving parts. In **medical devices**, tapers play a vital role in the design of surgical instruments and implants. For instance, tapered needles and cannulas are designed to minimize tissue damage during insertion, while tapered bone screws provide secure fixation with minimal bone disruption. The **oil and gas industry** also relies heavily on tapered components, particularly in drilling operations where tapered drill bits and casings are essential for maintaining stability and preventing collapse in deep wells. **Construction and architecture** benefit from tapered elements in building design, such as tapered columns that distribute loads more efficiently, enhancing structural stability and aesthetic appeal. In **electronics**, tapered connectors and sockets ensure secure connections with minimal signal loss, critical for high-frequency applications. Even in **agriculture**, tapered tools like plow blades and drill bits are optimized for soil penetration and seed placement, improving crop yields and reducing soil erosion. The versatility of tapers extends to **sports equipment** as well; for example, golf clubs feature tapered shafts that balance flexibility with strength, enhancing swing dynamics. In **industrial machinery**, tapered bearings and bushings reduce friction and increase the lifespan of moving parts, contributing to overall plant efficiency. Across these diverse sectors, the precision and functionality offered by tapers underscore their importance as a fundamental design element, highlighting their role in achieving optimal performance and reliability. Understanding the concept of a taper is thus essential for engineers and manufacturers seeking to innovate and improve their products and processes.
Types and Variations of Tapers
In the realm of precision engineering and manufacturing, tapers play a crucial role in ensuring the accurate fit and function of various components. A taper, by definition, is a gradual reduction in diameter or thickness over a specific length, which can be tailored to meet diverse industrial needs. This article delves into the multifaceted world of tapers, exploring their types and variations that cater to different applications. We will examine **Standard Taper Dimensions and Specifications**, which outline the common measurements and guidelines that govern the production of tapers. Additionally, we will discuss **Specialized Tapers for Specific Uses**, highlighting how these are designed to address unique requirements in fields such as aerospace, automotive, and medical devices. Finally, we will touch on **Custom and Precision Tapers**, which are crafted to meet the exacting demands of specialized industries where off-the-shelf solutions are insufficient. By understanding these different types and variations, readers will gain a comprehensive insight into the concept of a taper, enabling them to make informed decisions in their respective fields. Transitioning seamlessly into **Understanding the Concept of a Taper**, this introduction sets the stage for a detailed exploration of what tapers are, how they are used, and why they are indispensable in modern engineering.
Standard Taper Dimensions and Specifications
Standard taper dimensions and specifications are crucial in ensuring the precise fit and functionality of tapered components across various industries. A taper is a conical or pyramidal shape that narrows down from a larger base to a smaller apex, and its dimensions are defined by specific standards to maintain consistency and interoperability. The most common standard for taper dimensions is the American National Standards Institute (ANSI) and the International Organization for Standardization (ISO), which provide detailed guidelines for different types of tapers. For instance, the Morse taper, widely used in machine tools and woodworking equipment, follows strict ANSI standards. These standards dictate the angle of the taper, typically ranging from 1:48 to 1:3.5, and the dimensions of the major and minor diameters at specific lengths. The Brown & Sharpe taper, another common type, also adheres to ANSI specifications with precise measurements for its angle and diameters to ensure seamless integration with other components. In medical and dental applications, the ISO 5832 standard governs the dimensions of surgical tapers used in implants and instruments. This standard ensures that all components fit together accurately, which is critical for patient safety and the success of surgical procedures. Similarly, in the automotive industry, tapers used in steering columns and other mechanical assemblies must comply with SAE (Society of Automotive Engineers) standards to guarantee reliability and performance. The importance of adhering to these standards cannot be overstated. Non-compliance can lead to misfits, reduced performance, and even safety hazards. For example, a mismatched Morse taper in a lathe could result in poor tool alignment, affecting the quality of the workpiece and potentially causing equipment failure. In medical contexts, incorrect taper dimensions could compromise the structural integrity of implants, posing serious health risks. Moreover, standard taper dimensions facilitate easier maintenance and replacement of parts. When all components adhere to the same specifications, technicians can interchange parts from different manufacturers without worrying about compatibility issues. This interoperability not only streamlines production processes but also reduces costs associated with custom fabrication and troubleshooting. In conclusion, standard taper dimensions and specifications are essential for ensuring the reliability, safety, and efficiency of tapered components across diverse industries. By adhering to established standards like ANSI and ISO, manufacturers can guarantee that their products meet the required levels of precision and compatibility, ultimately enhancing overall performance and user satisfaction. This emphasis on standardization underscores the critical role that precise taper dimensions play in maintaining the integrity and functionality of complex systems.
Specialized Tapers for Specific Uses
Specialized tapers are designed to cater to specific needs and applications, showcasing the versatility and precision that tapers can offer. In the realm of woodworking, for instance, **tapered shank bits** are crucial for creating precise holes in various materials. These bits have a tapered shank that fits into a corresponding tapered socket in the drill press or hand drill, ensuring a secure and balanced operation. This design minimizes wobbling and enhances accuracy, making them ideal for intricate woodworking projects. In the automotive industry, **tapered roller bearings** play a vital role in supporting heavy loads and withstanding high stresses. These bearings feature tapered rollers that allow for better load distribution and improved stability, especially in applications where both radial and axial loads are present. This specialized design ensures smoother operation and extended lifespan of the bearings, which is critical for the performance and safety of vehicles. For medical procedures, **tapered needles** are essential for various surgical and diagnostic applications. These needles have a gradually narrowing tip that facilitates easier insertion into tissues with minimal trauma. The tapered shape helps in reducing tissue resistance, making the procedure less invasive and more comfortable for patients. Additionally, tapered needles are often used in dental procedures to ensure precise injections and minimize discomfort. In construction and engineering, **tapered rebar** is used to enhance the structural integrity of concrete structures. Tapered rebar allows for easier bending and shaping, which is particularly useful in complex architectural designs or when working with confined spaces. The tapered ends also facilitate better anchorage within the concrete, improving the overall strength and durability of the structure. Lastly, in the realm of sports equipment, **tapered shafts** in golf clubs and hockey sticks provide a balance between flexibility and rigidity. The tapered design allows for optimal weight distribution and improved swing dynamics, enhancing the performance of athletes. For golf clubs, the taper helps in achieving a consistent swing speed and better ball control, while for hockey sticks, it enhances stickhandling and shooting accuracy. These examples illustrate how specialized tapers are engineered to meet the unique demands of various industries and applications. By leveraging the advantages of tapered designs, professionals can achieve higher precision, improved performance, and enhanced safety across different fields. Whether it's woodworking, automotive engineering, medical procedures, construction, or sports equipment, the right taper can make a significant difference in the outcome of a project or activity.
Custom and Precision Tapers
Custom and precision tapers are specialized tools designed to meet specific requirements in various industries, including manufacturing, aerospace, and healthcare. Unlike standard tapers, which are mass-produced to fit general applications, custom tapers are tailored to precise specifications to ensure optimal performance and accuracy. These tapers can be made from a wide range of materials, such as stainless steel, titanium, or advanced polymers, each chosen for its unique properties that align with the intended use. One of the key advantages of custom tapers is their ability to fit into unique or irregularly shaped spaces where standard tapers would not suffice. For instance, in the aerospace industry, custom tapers might be used in the assembly of complex components where precise alignment and fit are critical. Similarly, in medical devices, precision tapers can be designed to interface with specific anatomical features or to accommodate specialized surgical instruments. The process of creating custom tapers involves meticulous engineering and manufacturing techniques. It begins with detailed design specifications provided by the client, which are then translated into CAD models. Advanced machining technologies such as CNC milling or 3D printing may be employed to produce these tapers with high precision and accuracy. Quality control measures are stringent, ensuring that each taper meets the required tolerances and performance standards. Variations in custom tapers can include different shapes, sizes, and surface finishes. For example, some applications may require a taper with a specific thread pattern or a unique angle of tapering. Others might necessitate specialized coatings or treatments to enhance durability or reduce friction. The flexibility in design allows for innovative solutions that can significantly improve operational efficiency and product reliability. In addition to their technical benefits, custom and precision tapers also offer economic advantages. While the initial cost of a custom taper might be higher than that of a standard one, the long-term savings can be substantial. Custom tapers can reduce downtime by fitting perfectly into their intended spaces, minimizing the need for adjustments or replacements. They also contribute to overall system reliability, which can lead to lower maintenance costs over time. In summary, custom and precision tapers represent a pinnacle of engineering excellence, offering unparalleled fit, function, and performance tailored to specific needs. Their versatility in design and material selection makes them indispensable in industries where precision is paramount. As technology continues to evolve, the capabilities of custom tapers will only expand further, enabling even more sophisticated applications across various sectors.
Practical Uses and Benefits of Tapers
In the realm of engineering and construction, precision and efficiency are paramount, and one often overlooked yet crucial element that contributes significantly to these goals is the taper. A taper, by definition, is a gradual reduction in diameter or thickness of an object, typically used in various mechanical and structural applications. This simple yet effective design feature offers a multitude of practical uses and benefits that span across different fields. For instance, in construction, tapers play a vital role in enhancing structural integrity by providing smooth transitions and reducing stress concentrations. In mechanical systems, tapers improve performance by facilitating easier assembly and disassembly, as well as optimizing the distribution of forces. Additionally, in various engineering fields, tapers optimize design by allowing for more versatile and adaptable solutions. Understanding these applications is essential to appreciating the full potential of tapers. As we delve into the practical uses and benefits of tapers, it becomes clear that their significance extends far beyond their simple geometric form. To fully grasp these advantages, it is first important to understand the concept of a taper.
Enhancing Structural Integrity in Construction
Enhancing structural integrity in construction is a critical aspect that directly impacts the safety, durability, and overall performance of buildings and infrastructure. One of the practical tools that contribute significantly to achieving this goal is the use of tapers. Tapers, which are precision-cut pieces designed to fit snugly into specific spaces, play a pivotal role in ensuring that structures maintain their intended form and function over time. In the context of construction, tapers are often used to create smooth transitions between different materials or components, such as between concrete slabs and steel beams. This seamless integration helps in distributing loads evenly, thereby reducing stress concentrations that could lead to cracks or failures. For instance, in high-rise buildings, tapers can be used to align and secure the connections between floor slabs and vertical columns, enhancing the structural stability and resistance to seismic forces. Moreover, tapers facilitate precise alignment during assembly, which is crucial for maintaining the structural integrity of complex systems like bridges or large industrial facilities. By ensuring that all components are perfectly aligned, tapers help in preventing misfits that could compromise the structure's ability to withstand various environmental and operational stresses. This precision also aids in minimizing the risk of material fatigue and wear over time, extending the lifespan of the structure. Another significant benefit of using tapers is their ability to enhance the aesthetic appeal of a structure while maintaining its functional integrity. In architectural designs where smooth transitions are essential for visual coherence, tapers can be customized to fit specific dimensions and shapes, ensuring that the final product meets both engineering and design standards. This dual benefit makes tapers an indispensable tool for architects and engineers who seek to balance form and function effectively. From a practical standpoint, the use of tapers simplifies the construction process by reducing the need for extensive manual adjustments or additional materials. This not only saves time but also lowers construction costs, making projects more economically viable without compromising on quality. Additionally, tapers can be fabricated from a variety of materials, including metals, plastics, and composites, allowing for flexibility in different construction scenarios. In summary, tapers are a versatile and essential component in enhancing structural integrity in construction. By ensuring precise alignment, smooth transitions, and even load distribution, tapers contribute significantly to the safety, durability, and aesthetic appeal of buildings and infrastructure. Their practical uses span across various aspects of construction, from high-rise buildings to complex industrial facilities, making them an invaluable tool for architects, engineers, and builders alike.
Improving Performance in Mechanical Systems
Improving performance in mechanical systems often hinges on the strategic use of precision components, and one such critical element is the taper. Tapers, by definition, are conical or tapered shapes that gradually decrease in diameter from one end to the other. In mechanical systems, these components play a pivotal role in enhancing efficiency, reliability, and overall performance. One of the primary benefits of tapers is their ability to provide secure and precise connections between different parts of a mechanical system. For instance, tapered shafts and bearings ensure a snug fit that minimizes play and vibration, thereby reducing wear and tear on moving parts. This tight fit also improves the transmission of torque and rotational forces, leading to smoother operation and increased durability. Additionally, tapers facilitate easy assembly and disassembly, which is crucial for maintenance and repair operations. The precision fit offered by tapers allows for the accurate alignment of components, which is essential for maintaining optimal performance and preventing premature failure. Moreover, tapers can significantly enhance the structural integrity of mechanical systems. In applications such as tooling and machinery, tapered shanks provide a robust connection that can withstand high forces and stresses without compromising the stability of the system. This is particularly important in industries like manufacturing and construction where heavy-duty machinery is used extensively. The use of tapers also allows for better load distribution, which helps in preventing localized stress concentrations that could lead to component failure. From a design perspective, tapers offer considerable flexibility and versatility. They can be customized to fit specific requirements, making them adaptable to a wide range of applications. For example, in aerospace engineering, tapered components are used to optimize weight while maintaining structural strength, which is critical for achieving high performance and efficiency in aircraft and spacecraft. Similarly, in automotive engineering, tapered bearings are used to improve the performance of suspension systems, enhancing vehicle stability and handling. In summary, the practical use of tapers in mechanical systems is multifaceted and highly beneficial. By providing secure connections, enhancing structural integrity, facilitating easy assembly and disassembly, and offering design flexibility, tapers contribute significantly to improving the performance of mechanical systems. Whether it's in heavy industry, precision engineering, or high-performance applications, the incorporation of tapers can lead to enhanced efficiency, reliability, and overall system longevity. As such, understanding the role and benefits of tapers is essential for engineers and technicians seeking to optimize mechanical system performance.
Optimizing Design in Various Engineering Fields
Optimizing design in various engineering fields is a critical aspect that significantly impacts the performance, efficiency, and durability of engineered systems. Across disciplines such as mechanical, aerospace, civil, and biomedical engineering, the strategic use of tapers can be a game-changer. In mechanical engineering, tapers are often employed to reduce stress concentrations and improve the structural integrity of components. For instance, tapered shafts and axles distribute loads more evenly, enhancing their resistance to bending and torsional forces. This optimization is particularly crucial in high-performance applications like aircraft engines and industrial machinery. In aerospace engineering, the aerodynamic benefits of tapers are paramount. Tapered wings and fuselage designs help reduce drag by smoothing airflow over the surface of aircraft, thereby increasing fuel efficiency and maneuverability. Similarly, in civil engineering, tapered columns and beams are used to minimize material usage while maintaining structural strength. This approach not only reduces construction costs but also enhances the aesthetic appeal of buildings and bridges. Biomedical engineers also leverage tapers to design more effective medical devices. Tapered needles and catheters facilitate smoother insertion into tissues, reducing patient discomfort and the risk of complications. Additionally, tapered implants such as hip replacements and dental implants promote better osseointegration, leading to longer-lasting and more stable outcomes. The practical uses and benefits of tapers extend beyond these specific examples. They offer a versatile solution for optimizing weight, reducing material costs, and enhancing overall system performance. By carefully designing tapers, engineers can mitigate potential failure points, improve safety, and extend the lifespan of engineered components. Furthermore, the use of tapers can simplify manufacturing processes by reducing the complexity of part geometries and enabling more efficient assembly techniques. In summary, optimizing design with tapers is a multifaceted strategy that enhances the functionality and reliability of engineered systems across various fields. By understanding and applying the principles of taper design, engineers can create more efficient, durable, and cost-effective solutions that meet the demanding requirements of modern engineering challenges. Whether it's improving aerodynamics, reducing material usage, or enhancing patient outcomes, the strategic use of tapers stands as a testament to the power of thoughtful design in engineering.