What Is A Bearing

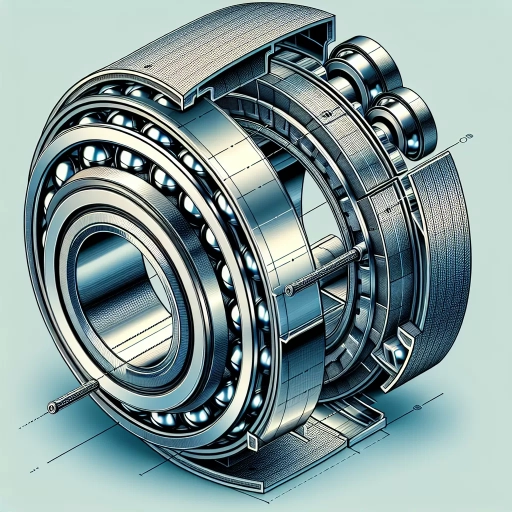
Introduction to Bearings
Bearings, an essential component of modern machinery, have been revolutionizing industries globally with their ability to diminish friction and ensure the smooth functioning of equipment. This article aims to offer an insightful introduction to bearings, delving into the definition and purpose of bearings, their historical development and their quintessential role in contemporary machinery. The initial section will unveil the true definition of bearings and shed light on their primary purpose of handling mechanical loads. Following that, we'll dive into the past ages of early innovation, tracing the historical development of bearings from their inception. In the last part, we will unfold the immense importance of bearings in modern machinery, illustrating the breadth of their utilization across diversified sectors. As we commence this explorative journey into the world of bearings, it is only fitting that we begin by getting to the heart of what bearings truly are, facilitating every reader’s comprehension of their definitions and essential purposes.
Definition and Purpose
Bearings, an integral part of modern machinery, can be defined as highly specialized, precision-made components that facilitate linear or rotational movements, reducing friction between objects and improving performance and efficiency. They are designed to bear the load, providing a smooth surface over which various parts can move freely. Tracing their evolution from simple wooden bearings used in wheel axels during ancient times to sophisticated, advanced materials designed today, bearings have become an indispensable part of our everyday lives. The primary purpose of bearings—to reduce frictional resistance to relative motion— continues to drive innovation and inspire engineering advancements. Bearings come in various types, including ball bearings, roller bearings, thrust bearings, precision bearings, and more, each one designed and purposed for specific applications. Ball bearings, for instance, are commonly used in high-speed applications. Their ability to reduce rotational friction and support radial and axial loads makes them ideal for use in car axles, dental equipment, hard drives, rollerblades, and even machinery used in space exploration! The purpose of a bearing is not solely relegated to reducing friction. Bearings also play a pivotal role in determining the reliability, lifespan, noise, speed, and performance of machinery. From a humble skateboard wheel to a high-speed electric drill to intricate machinery of a jet engine, the operational efficiency largely rests on the bearings used. Their performance and longevity significantly impact the overall reliability and cost-effectiveness of the machines. In industrial applications, for instance, the virtue of bearings cannot be overstated. Their role in reducing friction and associated heat helps to minimize wear and tear, thereby prolonging the life of the machinery. By facilitating the free rotation of gears, axles, and wheels under heavy loads, bearings aid in enhancing the performance efficiency, ensuring that the machinery operates smoothly and without disruption. Moreover, bearings also help in maintaining the alignment of moving parts. In vehicles, they assist in the seamless operation of wheels and axles, ensuring safety and comfort. In precision instruments, like hard drives and medical devices, bearings guarantee high levels of accuracy and control. The contribution of bearings to various sectors—industrial, manufacturing, automotive, aerospace, renewables—is monumental. As technology advances, the purpose of bearings has evolved to meet the wider challenges and demands. With the rise of electric vehicles and renewable energy technologies, bearings are becoming increasingly relevant in these spheres, devised to meet specific environmental and efficiency criteria. In conclusion, bearings—despite their miniature size and simple core functionality—play a vital role in our world, reducing friction and enabling smooth, efficient machine operation. From the perspective of design, cost, energy efficiency, and sustainability, the importance of bearings cannot be overlooked. They exemplify the adage, "small is big," shedding light on how refined design and engineering can make a big difference in achieving efficiency and sustainability in our daily lives. Therefore, understanding the definition and purpose of bearings is not only essential but profoundly enriching for anyone interested in mechanical engineering or related fields.
Historical Development
In the grand timeline of human ingenuity, bearings have professedly carved a prominent niche, serving as the central mechanisms enabling the tangible motion in many machines and devices. From the swift spinning of computer hard drives to the incessant rotation of car wheels, bearings find their application sprawling across various domains. Delving deeper into history to unravel the genesis of bearings, one can trace back to ancient Egyptians who ingeniously employed tree trunks under sleds for the easy transportation of massive rocks and stones. This rudimentary bearing mechanism, albeit crude, was the stepping stone in the evolutionary journey of bearings. The ancient Romans significantly advanced the bearing technology, inventing primitive roller bearings to support Roman Naves - their curvy warships. This marked the inception of bearings playing a crucial role in maritime and naval technology, a relationship that holds strong even today. In the ensuing centuries, the bearing technology witnessed an incessant growth parallel to the scientific and industrial advancements across the globe. In the Renaissance, for instance, Leonardo da Vinci sketched designs for an elementary ball bearing in the 16th century. The pivotal point in the historical development of bearings, however, came in the 19th century during the Industrial Revolution. It was an era that saw a surge in the invention of machines requiring parts with reduced friction for increased efficiency. Thus the modern day radial ball bearings materialized in 1869, patented by a Parisian bicycle mechanic, Jules Suriray. This paved the way for the era of industrial bearings attuned to the growing demands of diverse industries ranging from automotive to aerospace. The 20th century, in particular, experienced an exponential growth in bearing technology. This lead to the development of new types of bearings, including magnetic and fluid bearings. The innovation of bearing technology still continues today as scientists and engineers work fervently to enhance the performance, durability and load capabilities of bearings. Undeniably, the historical development of bearings is intriguing, as it's directly intertwined with the unfurling human civilization and technological evolution over the centuries. It is a testament to human aspiration and the relentless quest for progress and efficiency. It points to how a simple mechanism to ease transportation in ancient times has morphed into a technology integral to many industries and applications in modern society. It also foretells the potential of bearings to transcend further into unprecedented paradigms, shaping not just machinery, but the very contours of the future itself.
Importance in Modern Machinery
In the modern world, the significance of machinery is undeniable and the role of bearings is particularly crucial in facilitating their functionality. Bearings, although small and often overlooked, play a vital role in supporting rotational or linear movement while reducing friction and handling stress, thus enhancing the efficiency and longevity of machinery. They are a fundamental element of any rotating machine and their purpose underlies various applications across diverse industries. In the mechanical realm, a vast range of devices, from the smallest electric motor to the largest industrial machinery, relies on bearings for smooth operations, underscoring the paramount importance of bearings. Without the inclusion of bearings, the performance of machines would be severely hindered, largely owing to increased friction and wear and tear. This could lead to foul operational efficiency and costly repairs, giving bearings a role of significant consequence. Furthermore, the significance of bearings transcends merely improving machine performance. In an age where energy conservation and efficiency are imperative, bearings contribute remarkably to energy saving by reducing friction. This not only makes machinery energy-efficient, but also environmentally friendly, thus easing the pressure on our planet's limited resources. Their potential to decrease energy consumption has profound implications for industries aiming to enhance their sustainability practices. In the automotive industry, for instance, wheel bearings allow for frictionless rotation of the wheels, translating into smoother and more efficient vehicle movement. In heavy machinery, roller bearings support large loads while minimizing friction, thereby improving equipment durability and productivity. In precision tools like hard drives and watches, tiny ball bearings are critical for ensuring accurate and reliable functionality. Thus, the importance of bearings in modern machinery is vast and multifaceted. Moreover, advancements in technology have led to the evolution of bearings with several characteristics like high load capacity, long-lasting life, resistance to harsh conditions, and low maintenance requirements. This makes them an integral component of machinery used in challenging environments, such as aerospace & defense, maximizing operational lifespan while maintaining reliable performance. In conclusion, bearings serve as the linchpins to the uninterrupted and efficient functioning of modern machinery. Their ability to reduce friction and support movement amplifies machine efficiency, curbs energy consumption, and bolsters the durable operation of technological equipment. Despite their small size, bearings are monumental in the world of machinery, proving that intricacy lies in the minutest details.
Types of Bearings
Bearings play a crucial and often underappreciated role in the functioning of our modern, industrial world. The purpose of this meticulously researched article is to illuminate the different types of bearings and their unique uses. We will divide our discussion into three main sections: ball bearings, roller bearings, and specialized bearings such as thrust, needle, and magnetic bearings. To begin with, ball bearings, often seen in automobiles and machinery, use spherical elements to decrease rotational friction and bear radial loads. Moving towards, roller bearings use cylindrical rolling elements and are well-suited to handle heavy loads. Our third section will focus on the more specialized types of bearings, such as thrust bearings designed to handle axial loads, needle bearings for space limitations, and magnetic bearings that leverage magnetic levitation to support high rotating speeds. In this way, the vast, complex world of bearings will be made readily accessible and comprehensible. Now, let's dive deeper into our first topic - ball bearings.
Ball Bearings
Ball bearings are one of the most prevalent types of bearings used around the globe. These bearings are revered for their durability, efficiency, and concentricity, all of which significantly reduce rotational friction. Ball bearings are composed of several key components which include an outer ring, an inner ring, balls that provide the bearing capacity, and a cage that sustains the balls in place. The balls, which are precision-ground to promote smoother operation, work to distribute the load evenly over the bearing while the cage separates the balls to prevent friction and resultant wear. Four main types of ball bearings exist, catering to a diverse array of applications. These include deep groove ball bearings, angular contact ball bearings, self-aligning ball bearings, and thrust ball bearings. Deep groove ball bearings, characterized by deep, uninterrupted raceways, are particularly versatile. They facilitate both radial and axial loads whilst also permitting high speeds. Angular contact ball bearings, with their asymmetrical designs, can handle higher axial loads in either direction. Their distinct contact angle also allows them to support substantial radial loads. Self-aligning ball bearings, a further subtype, can tolerate angular misalignments, making them useful for applications where imprecise alignment may occur. Lastly, thrust ball bearings - constructed solely to cater to axial loads - are paramount in low-speed applications such as bar stools where they can handle excessive thrust loads efficiently. Each variant of the ball bearing serves a unique purpose and possesses distinct attributes aiding in particular applications. For instance, industries like skateboarding, manufacturing, and aerospace rely heavily on these bearings. Ball bearings enable the spinning wheels of a skateboard, allow the smooth operation of conveyor belts, and aid in the launch of space shuttles. However, despite the robustness and versatility of ball bearings, they are not without their limitations. Ball bearings are susceptible to deformation under heavy loads and can falter under varying temperatures. Moreover, they tend to generate high noise levels during operation, which can be disruptive in certain settings. Regardless of their drawbacks, the merits of ball bearings are manifold, making them integral components in countless machines and devices. When carefully chosen and properly maintained, they can significantly enhance the efficacy and longevity of machinery, making them an indispensable solution for many mechanical challenges. From skateboards to spacecraft - ball bearings are hard at work everywhere, proving their worth in countless applications and industries. So, whether you’re an engineer, a hobbyist, or just an everyday user of countless products that incorporate ball bearings, it’s clear to see the importance and impact of this seemingly humble invention.
Roller Bearings
Roller Bearings comprise another pivotal category in the pantheon of bearing types, known for their versatility and efficacy in managing heavy radial loads. Roller bearings, designed with cylindrical rolling elements as the name suggests, are outstandingly adept at handling high-capacity operational loads. The clue to their robustness lies in the large surface area contact between the rollers and the outer ring, which begets superior load distribution. Fundamentally, roller bearings present two key subtypes: Cylindrical Roller Bearings and Tapered Roller Bearings. Cylindrical Roller Bearings, the simpler variant, are designed to handle high radial loads but struggle with significant thrust loads. Owing to the line contact between the cylindrical rollers and races, this type of bearing can accommodate hefty radial loads while minimizing friction, making them an optimal choice in high-speed applications such as electric motors, automotive transmissions, and airplane engines. On the other hand, Tapered Roller Bearings specialize in handling both heavy radial and thrust loads. The converging, tapered rollers – housed in the inner and outer rings of the bearing – are designed to handle substantial radial and axial loads in one direction. The genius design of these bearings lies in their ability to adjust to handling combined loads – a feature exemplified by their extensive use in car hubs, where they successfully withstand extreme radial and thrust loads. Roller bearings, thus, are incredibly efficient, able to endure high-capacity loads and friction while showcasing increased bearing life and reliability. They exhibit a marked resilience to misalignment and shaft deflection, which makes them indispensable across various machinery. However, it is important to consider trade-offs such as higher cost and tricky installation when using roller bearings. Nonetheless, when correctly applied in terms of load, speed, and maintenance requirements, the roller bearing can become an integral component in many complex mechanical systems.
Specialized Bearings (e.g., Thrust, Needle, and Magnetic)
Specialized Bearings, such as Thrust Bearings, Needle Bearings, and Magnetic Bearings account for a significant subset of the broad, complex world of bearings, each offering distinct characteristics and functionalities tailored to specific applications. Thrust Bearings, for instance, are chiefly designed to accommodate axial loads, which are forces exerted parallel to the bearing's axis. This differs fundamentally from the mainstay radial load carried by many bearings, with a force exerted perpendicular to the shaft. Thrust Bearings finds their utility in applications such as automotive transmissions or marine propellers, where precise accommodation of axial load is crucial. On the other hand, Needle Bearings, characterized by their slender, long cylindrical rollers - akin to needles -, perform at an exceptional level when space is confined yet high-load capacity is required. The inherent compactness of Needle Bearings, coupled with their ability to deal with high radial loads, makes them an ideal choice for sectors such as the automotive and manufacturing industries, where instruments often work within severe space constraints. Moreover, these bearings significantly reduce the friction of a rotating surface, increasing the overall performance and efficiency of the equipment. Equally important and equally intriguing is the Magnetic Bearings. Unlike typical bearings that firmly rely on physical contact between components, Magnetic Bearings operate on the principle of magnetic levitation. Magnetic fields suspend the rotating shaft and allow it to pivot, eliminating direct physical contact, thus reducing wear and tear and absolute eradication of friction- a real deal-breaker in settings where minimal friction is intrinsically advantageous. Not surprisingly, Magnetic Bearings find their application in high-speed devices, such as flywheels, where the speed could otherwise result in destructive outcomes due to heat from friction. Furthermore, the lifetime longevity achieved by removing physical contact is a significant factor in the appeal of Magnetic Bearings. All these specialized bearings form the building blocks in countless applications, uncompromisingly improving the efficiency, productivity, and longevity of various mechanisms in numerous fields. To summarize, these Specialized Bearings with their distinct properties elegantly underline the remarkable adaptability and flexibility of engineering solutions to specific engineering problems.
Functionality and Applications
The function and application of different systems are a testament to the brink of human innovation, paving the way to accelerated progress. This article will examine three pivotal aspects of this field: Mechanical Advantage and Load Distribution, Reduction of Friction and Wear, and Industrial and Everyday Applications. Starting with Mechanical Advantage and Load Distribution, we delve into the ingenious mechanisms employed to redistribute stress, facilitating the lifting or moving of substantial loads with minimal effort. Subsequently, we explore the Reduction of Friction and Wear - the various methods applied to conserve machinery and prolong lifespan, minimizing costly and time-consuming maintenance. Finally, we turn our attention to Industrial and Everyday Applications, illuminating the impact of these concepts on a range of sectors and on our day-to-day lives. By delving into these subtopics, we will better understand the functionality and applications of various principles that make modern life not just possible, but also efficient. We initiate this exploration with an in-depth assessment of Mechanical Advantage and Load Distribution, where ratio and equilibrium hold the key.
Mechanical Advantage and Load Distribution
Mechanical advantage and load distribution play a critical role in the function and application of bearings. Bearings, commonly associated with industries such as transportation, manufacturing, and construction, capitalize on the principle of mechanical advantage. This principle essentially translates into the ability of bearings to amplify an input force by altering factors like distance, speed, direction, and more importantly, load bearing capacity. Therefore, a bearing’s functionality is largely rooted in its superior mechanical advantage, which allows a smaller force to transport heavy loads with relative ease, thus contributing to overall operational efficiency and performance. Further investigation into the dynamics of a bearing elucidates the concept of load distribution, which is intrinsically woven into the fabric of its functionality. Load distribution refers to the bearing's ability to evenly distribute the weight of the load, determining the extent to which stress is placed on each part of the bearing. An optimal load distribution is one that mitigates uneven stress and reduces the potential for wear, breakdown, or failure. For the bearing to work effectively, the load must be spread evenly across all parts, from the raceway surfaces to the rolling elements and cages. It is this even distribution of load that brings about longevity and greater efficiency in bearings, minimizing friction and energy consumption while maximizing performance. The impact of mechanical advantage and load distribution becomes particularly apparent in real-world applications such as the automobile industry where tapered roller bearings are used in car suspensions and axles, taking advantage of their high load-bearing capacity and superior ability to handle both radial and thrust loads. Similarly, in wind turbines, spherical roller bearings aid in managing the complex load distribution resulting from wind gusts and turbine operations. In conclusion, the study of mechanical advantage and load distribution is crucial in understanding the functionality and application of bearings, and it is these inherent qualities that make bearings indispensable in multiple sectors. Whether it is in enhancing operational efficiency or increasing longevity by reducing wear and tear, bearings prove their worth by leveraging their mechanical advantage and managing load distribution effectively. Bearings, therefore, embody the harmonious union of science and engineering, furnishing an array of industries with solutions designed for optimal performance.
Reduction of Friction and Wear
The reduction of friction and wear are crucial aspects of the functionality and application of bearings. Bearings are typically used in various mechanical systems such as automobiles, airplanes, and industrial equipment to support both axial and radial loads. However, due to the continuous relative motion between contact surfaces, bearings are prone to considerable friction and wear, which can lead to significant energy losses, part failure, and maintenance costs. To address these challenges, numerous techniques have been developed to reduce friction and wear. For instance, the use of lubricants is a widely adopted method in both rolling and slide bearings. Lubricants create a thin film that separates contact surfaces, reducing friction and preventing direct metal-to-metal contact, hence increasing the life cycle of the bearing. Long-life lubricants, synthetic oils, and greases are utilized to meet a range of operating conditions such as high temperature, extreme pressure, and high speed. Moreover, anti-friction coatings can substantially decrease wear rates by improving surface hardness and offering superior resistance to galling, scuffing, and micropitting. Additionally, advances in material science have resulted in the development of bearings made from materials with excellent anti-friction and wear-resistant properties. For example, ceramic bearings provide a lower coefficient of friction, reduce wear, improve rolling contact fatigue life, and allow for operation under harsh conditions. On the other hand, polymer bearings, thanks to their self-lubricating properties, can prevent friction in environments where traditional lubricants are not suitable. Furthermore, optimization of bearing design is another strategy for reducing friction and wear. For example, some bearing configurations like taper roller bearings and thrust ball bearings, due to their specific design features, are more capable of handling significant axial or radial loads, therefore reducing contact pressure and, accordingly, friction and wear. It's also worth noting that regular maintenance contributes to the decrease of friction and wear in bearings. Techniques such as proper installation, alignment, and balancing, cleaning and inspection, lubricant replenishment and monitoring are crucial in prolonging the bearing performance and lifespan. In recent years, novel technologies such as tribological design, advanced manufacturing methods, and digital tools for predictive maintenance have been increasingly employed to enhance bearing durability by mitigating friction and wear, thus ensuring its optimal performance. These emerging advances not only improve the operational efficiency of mechanical systems but also contribute to sustainability goals by reducing energy consumption and overall environmental footprint. Hence, the reduction of friction and wear plays a key role in the successful application and functionality of bearings.
Industrial and Everyday Applications
Bearing, a machine element, plays a vital role in many industrial applications and everyday customer applications. Bearings, operating on the simple principle of reducing friction and facilitating motion, are the unsung heroes, giving life to numerous machinery and everyday gadgets we use. In an industrial scenario, you can find bearings deployed in a broad spectrum: from massive constructions such as bridges and wind turbines to compact machinery including manufacturing equipment and power tools. Even in complex and high-integrity systems such as airplane and spacecraft engines, bearings are an indelible component. In the automotive industry, bearings are incorporated not only in wheels but also in wipers, transmissions, alternators, and steering systems. For instance, the wheel bearings are instrumental in promoting efficient wheel rotation and play a major role in ensuring safety by contributing to better vehicle control. Similarly, in the renewable energy sector, wind turbines utilize large bearings to ease the rotatory movement of massive blades, contributing to a sustainable future. Turning our lens to everyday applications, the utilization of bearings might surprise many. Any rotating parts in home appliances, like washing machines, microwaves, and fans, make use of bearings to promote smooth movement and efficiencies. Skateboards and fidget spinners, the everyday play utilities, also deploy miniature bearings to provide effortless, flawless spinning. Apart from these, medical devices, including MRI machines and CT scanners, utilize specially designed bearings. The power of a bearing lies in its functionality. Regardless of the application, whether it's industrial or daily use, bearings help in reducing friction, supporting loads, enhancing speed, and ensuring smooth and swift motion. It's an imperative part that improves performance, extends the durability and longevity of machinery, and results in significant savings by reducing maintenance costs, energy consumption, and wastage. In essence, bearings are omnipresent, silently facilitating smoother and efficient operations in both grand industrial machines and small everyday gadgets. They might remain under the radar, yet without them, our world would literally grind to a halt. So, next time when you spin your fidget spinner, just remember – it’s not magic, it’s the bearing!