What Causes Low Oil Pressure

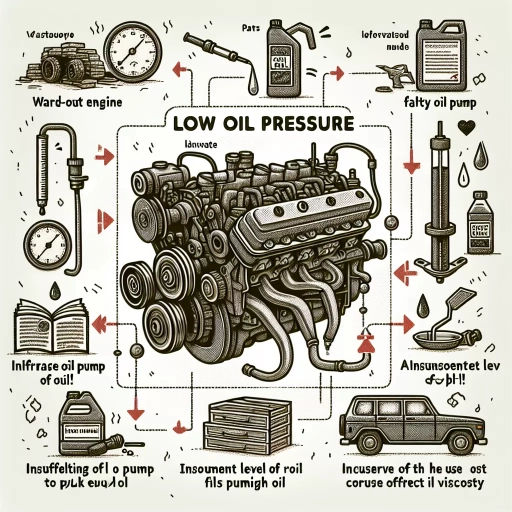
Low oil pressure is a critical issue that can significantly impact the performance and longevity of an engine. It is often a symptom of underlying problems that, if left unaddressed, can lead to severe engine damage. There are several key factors that contribute to low oil pressure, each requiring careful consideration to diagnose and rectify the issue effectively. Engine wear and tear, which includes the degradation of moving parts over time, is a primary cause. Additionally, issues within the oil system itself, such as clogged oil filters or faulty oil pumps, can also lead to low oil pressure. External factors and maintenance practices, including the type of oil used and the frequency of oil changes, also play crucial roles. Understanding these causes is essential for maintaining optimal engine health. In this article, we will delve into these factors, starting with the impact of engine wear and tear on oil pressure.
Engine Wear and Tear
Engine wear and tear is a critical aspect of vehicle maintenance, as it directly impacts the performance, efficiency, and longevity of an engine. This degradation can manifest in various forms, each with its own set of consequences. One of the primary concerns is the wear on engine bearings, which can lead to increased friction and eventual engine failure. Another significant issue is piston ring wear, which compromises the engine's ability to seal combustion chambers effectively, resulting in reduced power output and increased fuel consumption. Additionally, cylinder wall degradation can cause significant damage by allowing combustion gases to escape, leading to a drop in engine performance and potentially catastrophic failures. Understanding these specific types of wear is essential for diagnosing and addressing engine problems promptly. Let's delve into the first of these critical areas: **Worn Engine Bearings**.
Worn Engine Bearings
Worn engine bearings are a significant contributor to engine wear and tear, which can lead to low oil pressure. Engine bearings, typically made of metal or ceramic materials, play a crucial role in supporting the crankshaft and camshaft, allowing them to rotate smoothly while minimizing friction. Over time, these bearings can wear down due to various factors such as high mileage, inadequate lubrication, overheating, and contamination by debris or dirt. When bearings wear out, they lose their precision fit and smooth surface finish, leading to increased clearance between the bearing and the shaft. This increased clearance results in reduced oil pressure because the engine's oil pump must work harder to maintain adequate lubrication across the larger gaps. Consequently, the engine's oil pressure gauge may show lower readings, indicating potential issues that need immediate attention. Furthermore, worn bearings can cause the engine to vibrate excessively, produce unusual noises, and generate excessive heat—all of which are indicative of impending engine failure if not addressed promptly. Regular maintenance, including oil changes and inspections, is crucial for identifying and replacing worn bearings before they cause irreparable damage to the engine. By addressing worn engine bearings early on, vehicle owners can prevent more severe problems that could lead to costly repairs or even complete engine failure. Therefore, monitoring and maintaining engine bearings is essential for ensuring optimal engine performance and longevity.
Piston Ring Wear
Piston ring wear is a critical factor in engine wear and tear, directly impacting the overall performance and longevity of an engine. Piston rings are thin, circular bands that fit into grooves on the piston and play a crucial role in sealing the combustion chamber, transferring heat from the piston to the cylinder wall, and controlling oil consumption. Over time, these rings can wear out due to various factors such as high mileage, poor engine maintenance, inadequate lubrication, and excessive engine load. When piston rings wear down, they lose their ability to seal the combustion chamber effectively. This leads to a decrease in compression pressure, which can result in reduced engine power and efficiency. Additionally, worn piston rings allow combustion gases to escape into the crankcase, causing oil contamination and potentially leading to low oil pressure. The escaped gases can also increase the pressure inside the crankcase, forcing oil out through seals and gaskets, further exacerbating the issue of low oil pressure. Moreover, worn piston rings can cause excessive oil consumption as they fail to scrape off excess oil from the cylinder walls efficiently. This not only increases the cost of frequent oil top-ups but also leads to premature wear on other engine components due to inadequate lubrication. The increased friction between moving parts without sufficient lubrication accelerates wear on bearings, camshafts, and other critical components, contributing to overall engine deterioration. Regular maintenance is key to preventing or mitigating piston ring wear. Ensuring proper oil levels and using high-quality engine oil can help maintain the health of piston rings. Regular oil changes and filter replacements also help in keeping the engine clean and free from contaminants that could accelerate wear. Furthermore, addressing issues such as overheating or excessive engine load promptly can help extend the life of piston rings and other engine components. In summary, piston ring wear is a significant contributor to engine wear and tear, leading to issues like low oil pressure, reduced engine performance, and increased maintenance costs. By understanding the causes and consequences of piston ring wear and adhering to a rigorous maintenance schedule, engine longevity can be significantly improved, ensuring optimal performance and minimizing the risk of costly repairs.
Cylinder Wall Degradation
Cylinder wall degradation is a critical factor contributing to engine wear and tear, which can ultimately lead to low oil pressure. This degradation occurs when the cylinder walls, which are the inner surfaces of the engine's cylinders where the pistons move up and down, begin to wear down over time. Several key factors contribute to this degradation. Firstly, friction between the piston rings and the cylinder walls can cause micro-scratches and wear, especially if the engine is not properly lubricated. Secondly, combustion byproducts such as soot and carbon deposits can accumulate on the walls, reducing their smoothness and increasing friction. Additionally, overheating can cause thermal stress that weakens the material of the cylinder walls, making them more susceptible to damage. The presence of contaminants like dirt, dust, or metal shavings can also accelerate wear by acting as abrasive particles that scrape against the walls during engine operation. Furthermore, poor fuel quality or incorrect fuel type can lead to incomplete combustion, resulting in harmful residues that adhere to and degrade the cylinder walls. Engine knock or pinging, which occurs when fuel ignites prematurely in the combustion chamber, can also cause significant stress on these walls. As cylinder wall degradation progresses, it compromises the engine's ability to maintain proper compression and oil pressure. The increased clearance between the piston rings and the worn-down walls allows more oil to seep into the combustion chamber, where it is burned off rather than being circulated back into the engine's lubrication system. This not only reduces oil pressure but also increases emissions and decreases fuel efficiency. Moreover, the increased friction from worn-down surfaces generates more heat, which can further exacerbate engine wear and potentially lead to catastrophic failures if left unchecked. Regular maintenance practices such as oil changes with high-quality lubricants, filter replacements, and ensuring proper cooling system function are essential in mitigating cylinder wall degradation. Additionally, using fuel additives that help clean the engine and maintain cylinder wall health can be beneficial. Early detection through monitoring engine performance and addressing any issues promptly can prevent severe damage and maintain optimal engine operation. In summary, understanding and addressing cylinder wall degradation is crucial for maintaining engine health and preventing low oil pressure, thereby extending the lifespan of your vehicle's engine.
Oil System Issues
When it comes to maintaining the health and performance of your vehicle, the oil system is a critical component that cannot be overlooked. Issues within this system can lead to severe engine damage and even complete failure if not addressed promptly. This article delves into three key areas where problems often arise: low oil levels, clogged oil filters, and oil pump failure. Each of these issues can have devastating consequences if left unchecked. A low oil level can cause friction between moving parts, leading to overheating and potential engine seizure. A clogged oil filter restricts the flow of clean oil, allowing contaminants to circulate and cause wear on vital components. Lastly, an oil pump failure halts the circulation of oil altogether, resulting in catastrophic engine failure. Understanding these potential pitfalls is crucial for any vehicle owner seeking to ensure their car runs smoothly and efficiently. Let's start by examining the dangers of a low oil level and how it can impact your vehicle's performance.
Low Oil Level
A low oil level is a critical issue that can lead to severe engine damage and potentially catastrophic consequences. When the oil level in your vehicle's engine drops below the recommended minimum, it compromises the lubrication system, which is essential for maintaining engine health. Here are the key points to understand about low oil levels: 1. **Insufficient Lubrication**: Engine components such as pistons, rings, and cylinders rely on oil to reduce friction and prevent overheating. With a low oil level, these parts may not receive adequate lubrication, leading to increased wear and tear. 2. **Increased Engine Temperature**: Without sufficient oil, the engine's cooling mechanism is impaired. This can cause the engine temperature to rise, potentially leading to overheating and damage to critical components like the head gasket or engine block. 3. **Noise and Vibration**: Low oil levels can result in unusual noises such as knocking or clunking sounds from the engine due to metal-on-metal contact. This is often accompanied by increased vibration, indicating that the engine is not functioning smoothly. 4. **Reduced Fuel Efficiency**: An engine operating with insufficient oil may experience decreased performance and reduced fuel efficiency. This is because the engine has to work harder to compensate for the lack of lubrication, which can lead to increased fuel consumption. 5. **Potential for Seizure**: If the oil level remains low for an extended period, it can cause the engine to seize. This occurs when moving parts lock up due to excessive heat and friction, requiring costly repairs or even replacement of the engine. 6. **Causes of Low Oil Levels**: Common causes include leaks from gaskets or seals, excessive oil consumption by the engine (often due to worn piston rings or valve stem seals), and neglecting regular oil checks and top-offs. 7. **Preventive Measures**: Regularly checking the oil level using the dipstick and ensuring it is within the recommended range can help prevent these issues. Additionally, scheduling routine oil changes as per the manufacturer's guidelines helps maintain optimal engine performance. 8. **Symptoms to Watch For**: Keep an eye out for warning signs such as the oil light on your dashboard, unusual engine noises, increased temperature readings, and decreased performance. Addressing these symptoms promptly can help avoid more serious problems. In summary, a low oil level is a serious issue that demands immediate attention to prevent irreversible damage to your vehicle's engine. Regular maintenance and vigilance are key to ensuring your engine operates smoothly and efficiently.
Clogged Oil Filter
A clogged oil filter is a significant contributor to low oil pressure in an engine, posing serious risks to the overall health and longevity of the vehicle. When an oil filter becomes clogged, it restricts the flow of engine oil, which is essential for lubricating moving parts and cooling the engine. This restriction increases the pressure drop across the filter, leading to a decrease in oil pressure throughout the system. As a result, critical components such as piston rings, cylinder walls, and bearings may not receive adequate lubrication, causing friction to increase and potentially leading to overheating and premature wear. The primary causes of a clogged oil filter include excessive contaminants in the oil, such as dirt, debris, or metal shavings, which can accumulate over time. Poor maintenance practices, like using low-quality oil filters or failing to replace them at recommended intervals, also contribute to clogging. Additionally, driving conditions that expose the engine to extreme temperatures or dusty environments can accelerate filter clogging. Symptoms of a clogged oil filter include a drop in oil pressure readings on the dashboard gauge, increased engine noise due to friction between moving parts, and elevated engine temperatures. In severe cases, this can lead to engine stalling or failure if not addressed promptly. To prevent these issues, regular maintenance is crucial. This includes checking and replacing the oil filter according to the manufacturer's schedule and ensuring that high-quality filters are used. It is also important to monitor oil pressure regularly and address any signs of low pressure immediately to avoid potential damage. In summary, a clogged oil filter is a common cause of low oil pressure that can have detrimental effects on engine performance and longevity. By understanding the causes and symptoms of a clogged filter and adhering to proper maintenance practices, vehicle owners can mitigate these risks and ensure their engines run smoothly and efficiently.
Oil Pump Failure
Oil pump failure is a critical issue that can lead to severe engine damage and potentially result in costly repairs or even engine replacement. The oil pump is responsible for circulating engine oil throughout the engine, ensuring that all moving parts are adequately lubricated to prevent friction and wear. When the oil pump fails, it disrupts this essential lubrication process, leading to increased friction between moving components such as pistons, rings, and cylinder walls. This heightened friction generates excessive heat, which can cause metal surfaces to warp or seize, resulting in catastrophic engine failure. Several factors can contribute to oil pump failure. One common cause is low oil viscosity or using the wrong type of oil for the vehicle. If the oil is too thin, it may not provide sufficient pressure to keep the pump operating efficiently. Conversely, if the oil is too thick, it can put excessive strain on the pump, leading to premature wear. Another significant factor is contamination within the oil system. Debris, dirt, or metal shavings can clog the pump's internal passages or damage its components, causing it to malfunction. Additionally, wear and tear over time can lead to mechanical failure of the pump itself or its drive mechanism. Regular maintenance is crucial in preventing oil pump failure. This includes changing the engine oil at recommended intervals and using high-quality oil filters to keep contaminants out of the system. It is also important to monitor oil pressure regularly; a sudden drop in pressure could indicate impending pump failure. In some cases, symptoms such as unusual noises from the engine area or increased engine temperature may precede a complete failure. If an oil pump does fail, immediate action is necessary to prevent further damage. Continuing to operate the vehicle with a failed oil pump can result in irreversible damage within minutes. The engine should be shut off immediately, and a professional mechanic should be consulted for repair or replacement of the oil pump. In some instances, additional repairs may be required due to secondary damage caused by lack of lubrication. In summary, oil pump failure is a serious issue that can have devastating consequences for an engine if not addressed promptly. Understanding the causes and taking preventive measures through regular maintenance are key steps in avoiding this problem. Early detection and swift action upon noticing symptoms are critical in minimizing potential damage and ensuring the longevity of the engine.
External Factors and Maintenance
When it comes to maintaining the health and longevity of your vehicle, external factors play a crucial role. These factors can significantly impact the performance and lifespan of your car, and understanding them is essential for optimal maintenance. Three key external factors that deserve attention are incorrect oil viscosity, infrequent oil changes, and blockages in oil passages. Incorrect oil viscosity can lead to inadequate lubrication, causing wear and tear on engine components. Infrequent oil changes allow contaminants to build up, compromising engine efficiency and potentially leading to serious damage. Blockages in oil passages restrict the flow of lubricant, which can result in overheating and engine failure. By addressing these issues, you can ensure your vehicle runs smoothly and efficiently. Let's start by examining the critical importance of using the correct oil viscosity for your vehicle.
Incorrect Oil Viscosity
Incorrect oil viscosity is a critical external factor that can significantly impact engine performance and contribute to low oil pressure. Viscosity refers to the oil's thickness and flowability, which varies with temperature. Using the wrong viscosity can lead to several issues. If the oil is too thin (low viscosity), it may not provide adequate lubrication, especially at higher temperatures, causing increased wear on moving parts and potentially leading to overheating. Conversely, if the oil is too thick (high viscosity), it may not flow easily enough at lower temperatures, resulting in poor engine performance and decreased fuel efficiency. When an engine operates with incorrect oil viscosity, it can experience increased friction between moving parts, which in turn increases the load on the oil pump. This heightened demand can lead to a drop in oil pressure because the pump may struggle to maintain the required flow rate. Additionally, incorrect viscosity can affect the engine's ability to dissipate heat efficiently, as the right viscosity helps in cooling the engine components. Over time, this can result in premature wear on critical components such as piston rings, cylinder walls, and bearings. Moreover, using the wrong oil viscosity can void the manufacturer's warranty and lead to costly repairs down the line. It is essential to consult the vehicle's owner's manual or speak with a mechanic to determine the correct viscosity for your specific vehicle and operating conditions. Seasonal changes also play a role; for instance, thinner oils are often recommended for colder climates to ensure proper engine start-up and performance, while thicker oils are better suited for warmer climates to maintain adequate lubrication. In summary, incorrect oil viscosity is a significant external factor that can cause low oil pressure by increasing friction, affecting lubrication, and straining the oil pump. Ensuring the correct viscosity is crucial for maintaining optimal engine performance, preventing premature wear, and avoiding potential damage that could lead to costly repairs. Regular maintenance checks should include verifying that the correct oil viscosity is being used to safeguard the longevity and health of your vehicle's engine.
Infrequent Oil Changes
Infrequent oil changes are a significant external factor that can lead to low oil pressure in vehicles. Engine oil plays a crucial role in lubricating the engine's moving parts, cooling the engine, and cleaning the engine by carrying away contaminants. When oil is not changed regularly, it becomes degraded and loses its effectiveness. Over time, the oil's viscosity decreases, making it less capable of maintaining the necessary pressure to lubricate the engine properly. This degradation can cause increased wear on engine components such as piston rings, cylinder walls, and bearings, which in turn can lead to a drop in oil pressure. Moreover, dirty oil can clog the oil filter and oil passages within the engine, further reducing oil flow and pressure. The buildup of sludge and varnish from old oil can also restrict the movement of critical engine parts, exacerbating the problem. Additionally, infrequent oil changes can allow contaminants like metal shavings and combustion byproducts to accumulate in the oil, which can damage the oil pump and other components responsible for maintaining oil pressure. Regular oil changes are essential to ensure that the engine operates within optimal parameters. Fresh oil maintains its lubricating properties, keeps the engine clean, and helps in dissipating heat more efficiently. It also ensures that the oil pump operates effectively, maintaining the required pressure to keep all engine components well-lubricated. Neglecting this maintenance task can result in premature wear on the engine, leading to costly repairs or even engine failure. Therefore, adhering to the recommended oil change interval specified by the vehicle manufacturer is crucial for maintaining healthy oil pressure and overall engine health.
Blockages in Oil Passages
Blockages in oil passages are a significant external factor that can lead to low oil pressure in engines. These blockages can occur due to various reasons, including debris accumulation, sludge formation, and contamination. When debris such as metal shavings, dirt, or other particulate matter enters the oil system, it can clog the narrow passages and restrict oil flow. Similarly, sludge formation often results from the breakdown of engine oil over time, which can solidify and block critical oil pathways. Contamination from water or fuel can also contribute to blockages by causing the oil to thicken and lose its lubricating properties. Regular maintenance is crucial in preventing these blockages. Changing the engine oil at recommended intervals helps remove contaminants and prevents sludge buildup. Using high-quality oil filters can trap debris before it enters the engine's oil passages. Additionally, ensuring that the engine is properly sealed to prevent external contaminants from entering the system is vital. Regular inspections of the oil system for signs of wear or damage can also help identify potential blockages early on. In some cases, blockages may require more invasive maintenance such as cleaning or replacing affected components. For instance, if sludge has formed in critical areas like the oil pump or main bearings, these parts may need to be cleaned or replaced to restore proper oil flow. In severe cases where blockages have caused significant damage, a full engine overhaul might be necessary. Preventive measures such as using synthetic oils that are less prone to sludge formation and maintaining a clean engine environment can also mitigate the risk of blockages. Furthermore, monitoring oil pressure regularly through the use of pressure gauges or dashboard indicators can help detect any issues early, allowing for prompt action to be taken before serious damage occurs. In summary, blockages in oil passages are a critical external factor that can lead to low oil pressure, emphasizing the importance of regular maintenance and preventive measures to ensure optimal engine performance and longevity. By understanding the causes of these blockages and taking proactive steps to prevent them, vehicle owners can significantly reduce the risk of engine damage and maintain healthy oil pressure levels.