What Is A Solenoid Valve

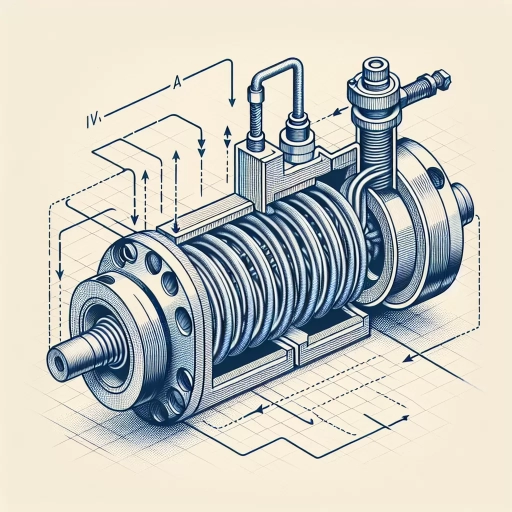
In the realm of fluid control and automation, solenoid valves stand as a cornerstone of modern engineering, offering precise and reliable operation in a wide range of applications. These versatile devices are integral to various industries, including manufacturing, healthcare, and aerospace, due to their ability to regulate the flow of fluids with high accuracy. But what exactly is a solenoid valve? This article delves into the fundamental aspects of solenoid valves, starting with an **Introduction to Solenoid Valves**, where we explore their definition, types, and historical development. We will then examine **How Solenoid Valves Work**, detailing the mechanical and electrical principles that govern their operation. Finally, we will discuss **Advantages, Disadvantages, and Maintenance**, highlighting the benefits and drawbacks of using solenoid valves and providing insights into their upkeep and longevity. By understanding these key aspects, readers will gain a comprehensive overview of solenoid valves and their critical role in contemporary technology. Let us begin by diving into the **Introduction to Solenoid Valves**.
Introduction to Solenoid Valves
Solenoid valves are a cornerstone of modern industrial and technological systems, playing a crucial role in controlling fluid flow across various sectors. These devices have evolved significantly over the years, transforming from simple mechanical components to sophisticated, electronically controlled units. To fully appreciate the significance of solenoid valves, it is essential to delve into their definition and basic function, which form the foundation of their operation. Historically, solenoid valves have undergone substantial development, from their early inception to the advanced designs seen today. This evolution has been driven by technological advancements and the increasing demand for precision and reliability in industrial processes. Understanding this historical context provides valuable insights into how these valves have adapted to meet diverse needs. In contemporary times, solenoid valves find applications across a wide range of industries, including automotive, aerospace, medical devices, and water treatment. Their versatility and reliability make them indispensable in these fields, where precise control over fluid flow is critical. By examining these common applications, we can better understand the widespread impact of solenoid valves. To begin our exploration, let us first define what solenoid valves are and how they function at a basic level. This foundational knowledge will serve as a springboard for understanding their historical development and their myriad applications in various industries.
Definition and Basic Function
A solenoid valve is a crucial component in various industrial and commercial applications, serving as an electromechanical device that controls the flow of fluid. At its core, the **definition** of a solenoid valve revolves around its ability to regulate the passage of liquids, gases, or other fluids through an electrically operated solenoid. This device is essentially a valve that is actuated by an electric current, allowing for precise control over fluid flow. The **basic function** of a solenoid valve is to open or close a valve in response to an electrical signal. When an electric current is applied to the solenoid coil, it generates a magnetic field that moves a metal piston or plunger, which in turn opens or closes the valve. This action either allows fluid to flow through the valve or blocks it, depending on the design and intended use. Solenoid valves can be configured in different ways, such as normally open (NO) or normally closed (NC), where the valve remains open or closed respectively when no electrical current is applied. In practical terms, solenoid valves are integral in systems requiring automated fluid control. For instance, in hydraulic systems, they help manage pressure and flow rates efficiently. In pneumatic systems, they control air flow to actuators like cylinders and motors. Additionally, solenoid valves are used in water treatment plants to manage water flow and in medical devices to regulate gas flow. Their versatility and reliability make them indispensable in numerous industries including manufacturing, automotive, aerospace, and more. The operational simplicity and reliability of solenoid valves contribute significantly to their widespread adoption. They offer quick response times and can be easily integrated into complex systems using control circuits and sensors. Moreover, solenoid valves are designed to operate under various conditions and can handle different types of fluids, making them adaptable to diverse applications. In summary, the definition and basic function of a solenoid valve underscore its role as a vital component in fluid control systems. By leveraging electrical signals to manage fluid flow, these valves provide precise control and reliability, making them essential in a broad range of industrial and commercial settings. Understanding the fundamental principles of solenoid valves is crucial for optimizing their performance and ensuring efficient operation in various applications.
Historical Development and Evolution
The historical development and evolution of solenoid valves are deeply intertwined with advancements in electrical engineering, fluid mechanics, and industrial automation. The concept of using electromagnetic forces to control fluid flow dates back to the early 19th century, but it wasn't until the late 1800s that the first practical solenoid valves began to emerge. These early devices were rudimentary, often consisting of simple electromagnetic coils that actuated mechanical valves. However, they laid the groundwork for more sophisticated designs. In the early 20th century, significant improvements were made with the introduction of more reliable materials and manufacturing techniques. The development of stainless steel and other corrosion-resistant materials allowed solenoid valves to be used in a wider range of applications, including those involving harsh chemicals and high pressures. This period also saw the integration of solenoid valves into larger control systems, marking the beginning of their role in industrial automation. The post-World War II era witnessed a surge in technological innovation, driven by the need for more efficient and reliable industrial processes. Solenoid valves became more compact, efficient, and versatile, with advancements in coil design and valve construction. The introduction of direct-acting and pilot-operated solenoid valves expanded their applicability across various industries, from water treatment and chemical processing to medical devices and aerospace. The advent of electronic control systems in the latter half of the 20th century further transformed the landscape. Solenoid valves began to be integrated with electronic controllers, enabling precise control over fluid flow rates, pressures, and temperatures. This integration also facilitated remote operation and monitoring, enhancing safety and efficiency in industrial settings. In recent decades, advancements in materials science and digital technologies have continued to drive the evolution of solenoid valves. Modern solenoid valves are designed with advanced materials such as ceramic and polymer-coated components, which offer improved durability and resistance to corrosion. Additionally, the integration of microcontrollers and IoT technologies has enabled real-time monitoring, predictive maintenance, and smart control strategies. Today, solenoid valves are a cornerstone of modern industrial processes, found in everything from HVAC systems to medical equipment. Their ability to provide fast, reliable, and precise control over fluid flow has made them indispensable in a wide array of applications. As technology continues to advance, it is likely that solenoid valves will become even more sophisticated, incorporating emerging technologies such as artificial intelligence and nanotechnology to meet the evolving needs of various industries. This ongoing evolution underscores the critical role that solenoid valves play in shaping the future of industrial automation and control systems.
Common Applications Across Industries
Solenoid valves are versatile components that find widespread application across various industries due to their reliability, efficiency, and precision in controlling fluid flow. In the **automotive industry**, solenoid valves play a crucial role in fuel injection systems, ensuring accurate fuel delivery to engines. They are also integral in anti-lock braking systems (ABS), where they rapidly open and close to modulate brake pressure, enhancing vehicle safety. In **industrial automation**, solenoid valves are essential for controlling pneumatic and hydraulic systems. They are used in manufacturing processes to regulate air and fluid flow, enabling precise control over machinery and equipment. This is particularly evident in applications such as conveyor systems, where solenoid valves help manage the movement of materials with high accuracy. The **medical sector** also relies heavily on solenoid valves for critical applications. In medical devices like ventilators and dialysis machines, these valves ensure precise control over gas and fluid flow, which is vital for patient care. Additionally, in laboratory settings, solenoid valves are used in analytical instruments to manage sample flow and reagent delivery. In **agriculture**, solenoid valves are used in irrigation systems to control water distribution efficiently. They help in automating the irrigation process, ensuring that crops receive the right amount of water at the right time, thereby optimizing crop yield and conserving water resources. The **HVAC (Heating, Ventilation, and Air Conditioning) industry** also benefits from the use of solenoid valves. These valves are used in heating and cooling systems to control the flow of refrigerants and water, ensuring optimal system performance and energy efficiency. Furthermore, **chemical processing** and **petrochemical industries** utilize solenoid valves to manage the flow of hazardous chemicals safely. Their ability to operate under high pressure and in corrosive environments makes them ideal for these applications. In **water treatment plants**, solenoid valves help in controlling the flow of water and chemicals during the treatment process. They ensure that the right amount of disinfectants and other chemicals are added to the water supply, maintaining water quality and safety standards. Lastly, **aerospace engineering** employs solenoid valves in various aircraft systems, including fuel management and hydraulic control systems. Their reliability and precision are critical in these high-stakes environments where safety is paramount. In summary, the versatility and reliability of solenoid valves make them indispensable across a wide range of industries. Their ability to precisely control fluid flow under various conditions has made them a cornerstone in modern industrial processes, ensuring efficiency, safety, and optimal performance. Understanding the applications of solenoid valves is crucial for appreciating their significance in different sectors and their role in driving technological advancements.
How Solenoid Valves Work
Solenoid valves are crucial components in various industrial and domestic applications, ensuring precise control over fluid flow. Understanding how these valves operate is essential for optimizing their performance and selecting the right type for specific needs. This article delves into the intricate workings of solenoid valves, focusing on three key aspects: the electromagnetic principle that drives their operation, the mechanical components that facilitate their function, and the diverse types of solenoid valves available, such as 2-way and 3-way configurations. By grasping these fundamental concepts, users can better appreciate the versatility and reliability of solenoid valves. At the heart of a solenoid valve's operation lies the electromagnetic principle, which converts electrical energy into mechanical motion. This principle is the foundation upon which the entire mechanism is built, making it a critical starting point for understanding how solenoid valves work. Let's begin by exploring this electromagnetic principle in detail.
Electromagnetic Principle
**Electromagnetic Principle** The operation of solenoid valves is fundamentally based on the electromagnetic principle, which involves the interaction between electric currents and magnetic fields. This principle is a cornerstone of electromagnetism, a branch of physics that describes the relationship between electrically charged particles and the electromagnetic forces acting between them. When an electric current flows through a conductor, such as a coil of wire, it generates a magnetic field around the conductor. This phenomenon is known as the Ampère's law, which states that the magnetic field produced by an electric current is directly proportional to the current and inversely proportional to the distance from the conductor. In the context of solenoid valves, this electromagnetic principle is harnessed to control fluid flow. A solenoid valve typically consists of a coil, a plunger or piston, and a valve body. When an electric current is applied to the coil, it creates a magnetic field that attracts the plunger or piston, causing it to move. This movement either opens or closes the valve, allowing or blocking the flow of fluid through the valve body. The precise control over this movement is what makes solenoid valves highly reliable and efficient in various applications, including industrial processes, medical devices, and automotive systems. The efficiency and reliability of solenoid valves are also enhanced by the quick response time to changes in the electric current. As soon as the current is turned on or off, the magnetic field changes almost instantaneously, allowing for rapid actuation of the valve. This rapid response is crucial in many applications where precise timing and control are essential. Additionally, solenoid valves can be designed to operate in different modes, such as normally closed (NC) or normally open (NO), depending on whether the valve is closed or open when no current is applied. The electromagnetic principle underlying solenoid valves also allows for their integration with other control systems. For instance, they can be controlled by programmable logic controllers (PLCs), timers, or sensors, enabling complex automation scenarios. This versatility makes solenoid valves indispensable in modern industrial automation, where precise control over fluid flow is critical for maintaining process integrity and efficiency. In summary, the electromagnetic principle is the foundational mechanism that enables solenoid valves to function effectively. By leveraging the interaction between electric currents and magnetic fields, these valves provide reliable and efficient control over fluid flow, making them a vital component in a wide range of applications. Understanding this principle is essential for appreciating how solenoid valves work and their significance in various technological and industrial contexts.
Mechanical Components and Operation
Mechanical components are the backbone of any mechanical system, including solenoid valves, which rely on these components to operate efficiently. At the heart of a solenoid valve lies a complex interplay of mechanical parts that work in harmony to control fluid flow. The primary mechanical components include the solenoid coil, plunger, spring, and valve body. The solenoid coil, when energized by an electric current, generates a magnetic field that attracts the plunger. This movement of the plunger is crucial as it either opens or closes the valve, depending on the design. In normally closed (NC) valves, the plunger is held in place by a spring when the coil is de-energized, blocking fluid flow. When the coil is energized, the magnetic force overcomes the spring's resistance, lifting the plunger and allowing fluid to pass through. The valve body houses these components and provides the structural integrity necessary for withstanding various pressures and fluid types. It typically includes inlet and outlet ports where the fluid enters and exits, respectively. The seat and orifice within the valve body are critical for sealing and directing fluid flow. When the plunger moves, it either seals against or moves away from these seats, thereby controlling the flow path. The precision engineering of these mechanical components ensures reliable operation under diverse conditions, making solenoid valves indispensable in industries ranging from automotive to medical devices. In addition to these core components, other mechanical elements such as seals, gaskets, and O-rings play vital roles in maintaining system integrity by preventing leaks and ensuring tight seals. These seals must be durable enough to withstand repeated cycles of opening and closing without compromising performance. Furthermore, materials used in constructing these components must be compatible with the fluid being controlled to prevent corrosion or contamination. The operational dynamics of these mechanical components are finely tuned to respond quickly and accurately to electrical signals. For instance, in applications requiring rapid actuation, solenoid valves can open or close in milliseconds due to the swift movement of the plunger driven by the magnetic field. This speed and reliability make solenoid valves ideal for applications where precise control over fluid flow is essential, such as in hydraulic systems, pneumatic systems, and process control environments. In summary, the intricate operation of solenoid valves hinges on the precise interaction of their mechanical components. Understanding how these parts work together is key to appreciating the versatility and reliability of solenoid valves in various industrial settings. By leveraging advanced materials and design principles, engineers can optimize these components for specific applications, ensuring that solenoid valves continue to play a critical role in modern technology.
Types of Solenoid Valves (2-way, 3-way, etc.)
Solenoid valves are versatile control devices used in a wide range of applications, including industrial processes, medical equipment, and consumer products. These valves are categorized based on their functionality and the number of ports they have, which determines how they manage fluid flow. The primary types include 2-way, 3-way, and 4-way solenoid valves. **2-Way Solenoid Valves** are the simplest and most common type. They have two ports: one inlet and one outlet. These valves can either allow or block the flow of fluid between these ports, making them ideal for on/off control applications. When the solenoid coil is energized, the valve opens or closes, depending on its design (normally open or normally closed). This type is frequently used in systems where a simple on/off function is required, such as in irrigation systems or HVAC units. **3-Way Solenoid Valves** have three ports: two inlets/outlets and one exhaust port. These valves can divert fluid flow between two different paths or mix fluids from two sources. There are several configurations for 3-way valves, including normally closed, normally open, and universal (which can be used as either normally open or normally closed). They are commonly used in applications like pneumatic systems, where air needs to be directed to different parts of a machine, or in hydraulic systems where fluid needs to be redirected. **4-Way Solenoid Valves** are more complex and have four ports: two inlets and two outlets. These valves are typically used in applications requiring more sophisticated control over fluid flow, such as in hydraulic systems for heavy machinery or in complex pneumatic circuits. They can control the direction of fluid flow in multiple paths simultaneously, making them essential for systems that require precise control over multiple actuators. In addition to these primary types, there are also **Proportional Solenoid Valves** which allow for variable control over fluid flow rather than just on/off operation. These valves use a proportional solenoid coil that can be energized to different levels, enabling precise regulation of flow rates. This makes them suitable for applications requiring fine-tuned control, such as in chemical processing or medical devices. Understanding the different types of solenoid valves is crucial for selecting the right valve for a specific application. Each type offers unique advantages and is designed to meet specific operational requirements. By knowing how each type functions and how they can be integrated into a system, engineers and technicians can optimize performance, efficiency, and safety in various industrial and commercial settings. Whether it's a simple 2-way valve for basic control or a more complex 4-way valve for intricate fluid management, solenoid valves play a vital role in modern automation and process control systems.
Advantages, Disadvantages, and Maintenance
When evaluating the effectiveness of any system, whether it be technological, mechanical, or organizational, it is crucial to consider both the advantages and disadvantages as well as the maintenance requirements. Understanding these aspects can help in making informed decisions and optimizing performance. This article delves into the multifaceted nature of systems by exploring their benefits and advantages in various contexts, highlighting potential drawbacks and limitations, and providing essential maintenance tips and best practices. By examining the benefits, we can identify how different systems enhance efficiency, productivity, and overall quality. However, it is equally important to acknowledge the potential drawbacks that may arise, such as cost, complexity, or environmental impact. Finally, maintaining these systems is vital for sustained performance, which involves regular checks, updates, and adherence to best practices. In this comprehensive analysis, we will first explore the benefits and advantages in various systems, shedding light on how they can be leveraged to achieve superior outcomes.
Benefits and Advantages in Various Systems
In the realm of fluid control and automation, solenoid valves stand out for their numerous benefits and advantages across various systems. One of the primary advantages is their **high precision and reliability**. Solenoid valves are designed to operate with minimal human intervention, ensuring consistent performance and reducing the likelihood of errors. This reliability is particularly crucial in industrial settings where downtime can be costly. Additionally, these valves offer **rapid actuation times**, allowing for quick responses to changes in system conditions, which is vital in applications requiring precise timing, such as in chemical processing or medical devices. Another significant benefit is their **energy efficiency**. Solenoid valves typically consume power only when switching states, making them more energy-efficient compared to other types of valves that may require continuous power to maintain their position. This efficiency not only reduces operational costs but also contributes to a more sustainable operation. Furthermore, solenoid valves are **compact and lightweight**, making them ideal for installations where space is limited. This compact design also simplifies the integration of these valves into complex systems, enhancing overall system flexibility. The **low maintenance requirements** of solenoid valves are another key advantage. Unlike mechanical valves that may require frequent adjustments or replacements, solenoid valves have fewer moving parts and are less prone to wear and tear. This reduces the need for regular maintenance, thereby lowering operational costs and extending the lifespan of the valve. Moreover, solenoid valves can be easily integrated with control systems and automation technologies, facilitating **advanced control capabilities**. This integration enables real-time monitoring and remote control, enhancing system performance and allowing for more precise control over fluid flow. In terms of **safety**, solenoid valves offer several advantages. They can be designed with fail-safe mechanisms that ensure the valve returns to a safe position in case of power failure or system malfunction. This feature is particularly important in hazardous environments where safety is paramount. Additionally, solenoid valves can be used to isolate sections of a system for maintenance or repair, reducing the risk of accidents and improving overall system safety. From a **cost perspective**, while the initial investment in solenoid valves may be higher than some other types of valves, their long-term benefits often outweigh these costs. The combination of energy efficiency, low maintenance needs, and high reliability translates into significant cost savings over time. Moreover, the versatility of solenoid valves allows them to be used in a wide range of applications, from simple on/off control to more complex proportional control scenarios, making them a valuable asset in diverse industrial and commercial settings. In conclusion, the benefits and advantages of solenoid valves make them an indispensable component in various systems. Their precision, reliability, energy efficiency, compact design, low maintenance requirements, advanced control capabilities, safety features, and cost-effectiveness collectively contribute to their widespread adoption across different industries. Whether in industrial automation, medical devices, or other fluid control applications, solenoid valves offer a robust solution that enhances system performance and reliability.
Potential Drawbacks and Limitations
While solenoid valves offer numerous advantages, they are not without their potential drawbacks and limitations. One significant limitation is their susceptibility to contamination and debris. If the fluid or gas flowing through the valve contains particulate matter, it can lead to clogging or sticking of the valve's moving parts, which may result in malfunction or complete failure. This issue is particularly pertinent in applications where cleanliness is crucial, such as in medical devices or food processing equipment. Another drawback is the reliance on an electrical power source. Solenoid valves require a consistent and reliable electrical supply to operate, which can be a disadvantage in environments where power outages are frequent or where battery life is a concern. Additionally, the electrical components can be vulnerable to electromagnetic interference (EMI) and radio-frequency interference (RFI), potentially disrupting valve operation. The mechanical components of solenoid valves also have a finite lifespan and may require periodic maintenance to ensure optimal performance. Wear and tear on the solenoid coil, piston seals, and other moving parts can lead to reduced efficiency over time. Furthermore, certain types of solenoid valves may not be suitable for high-pressure or high-temperature applications due to material limitations and design constraints. In terms of operational limitations, solenoid valves can exhibit hysteresis—the difference between the opening and closing pressures—which can affect precision control in some applications. This hysteresis can lead to inconsistent performance and may necessitate additional calibration or compensation mechanisms. Moreover, the choice of material for the valve body and internal components is critical but also restrictive. For instance, certain materials may not be compatible with specific fluids or gases, limiting the versatility of the valve in diverse industrial settings. Corrosion resistance is another factor; if the valve is exposed to corrosive substances, it could degrade faster than expected. Lastly, while solenoid valves are generally compact and efficient, they may not always be the best choice for large-scale fluid control due to flow rate limitations. In applications requiring high flow rates, other types of valves such as ball valves or gate valves might be more appropriate. In summary, while solenoid valves are highly versatile and widely used across various industries due to their reliability and precision control capabilities, they do come with several potential drawbacks and limitations that must be carefully considered during selection and implementation. Understanding these limitations is crucial for ensuring optimal performance and longevity of the valve in any given application.
Maintenance Tips and Best Practices
**Maintenance Tips and Best Practices** To ensure the optimal performance and longevity of solenoid valves, regular maintenance is crucial. Here are some key tips and best practices to follow: 1. **Regular Inspection**: Periodically inspect the solenoid valve for signs of wear, corrosion, or damage. Check for any leaks, rust, or mineral buildup which can affect its operation. 2. **Cleaning**: Clean the valve regularly to prevent debris accumulation. Use a soft brush or cloth to wipe down the exterior and ensure all ports are free from obstructions. 3. **Lubrication**: If your solenoid valve requires lubrication, use the recommended type and amount specified by the manufacturer. Over-lubrication can lead to clogging, while under-lubrication may cause friction issues. 4. **Filtering**: Install filters upstream of the solenoid valve to protect it from contaminants such as dirt, dust, and other particles that could interfere with its operation. 5. **Power Management**: Ensure that the power supply to the solenoid valve is stable and within the recommended voltage range. Voltage fluctuations can damage the coil or affect performance. 6. **Actuator Maintenance**: For pneumatic or hydraulic solenoid valves, maintain the actuators according to manufacturer guidelines. This includes checking for proper air pressure or hydraulic fluid levels. 7. **Replacement of Parts**: Replace worn-out parts promptly to avoid complete system failure. Keep spare parts on hand for critical components like O-rings, seals, and coils. 8. **Documentation**: Keep detailed records of maintenance activities including dates of inspections, cleaning schedules, and any repairs or replacements made. This helps in tracking the valve's history and planning future maintenance. 9. **Training**: Ensure that personnel responsible for maintaining solenoid valves are adequately trained on proper procedures to avoid human error which could lead to malfunctions or safety hazards. 10. **Manufacturer Guidelines**: Always refer to the manufacturer’s manual for specific maintenance recommendations tailored to your particular model of solenoid valve. By adhering to these maintenance tips and best practices, you can significantly extend the lifespan of your solenoid valves, reduce downtime due to failures, and maintain overall system efficiency and reliability. Regular maintenance not only saves time but also reduces costs associated with premature replacements and repairs while ensuring safe operation across various applications.