What Is Mro

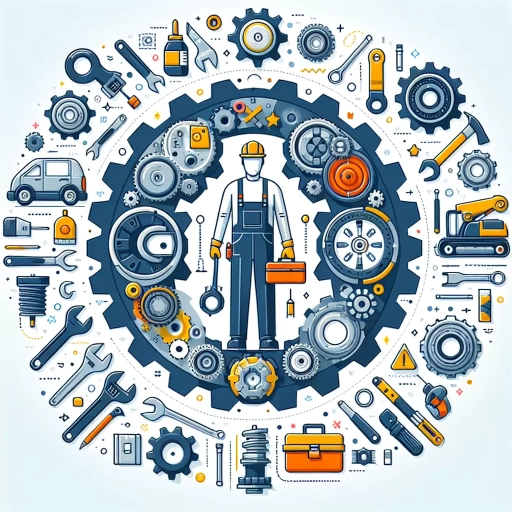
In the realm of industrial operations, Maintenance, Repair, and Operations (MRO) plays a pivotal role in ensuring the smooth functioning and efficiency of equipment, facilities, and overall production processes. MRO encompasses a broad spectrum of activities that are crucial for maintaining asset reliability, reducing downtime, and optimizing resource utilization. This article delves into the multifaceted world of MRO, beginning with **Understanding the Basics of MRO**, where we explore the fundamental principles and components that define this critical function. We then examine **The Role of MRO in Industrial Operations**, highlighting its impact on productivity, safety, and cost management. Finally, we discuss **Best Practices and Future Trends in MRO**, shedding light on innovative strategies and technological advancements that are shaping the future of maintenance and operations. By grasping these key aspects, readers will gain a comprehensive understanding of how MRO contributes to the success of industrial enterprises. Let's start by **Understanding the Basics of MRO**.
Understanding the Basics of MRO
Understanding the basics of Maintenance, Repair, and Operations (MRO) is crucial for any organization aiming to optimize its operational efficiency and reduce downtime. This comprehensive overview will delve into three key aspects: the definition and scope of MRO, its historical context and evolution, and the key components and processes involved. Firstly, grasping the definition and scope of MRO is essential as it sets the foundation for understanding how these activities integrate into an organization's overall strategy. This includes identifying what constitutes MRO, the various types of maintenance (preventive, corrective, predictive), and how these activities impact different departments within an organization. Secondly, exploring the historical context and evolution of MRO provides valuable insights into how these practices have developed over time. From traditional reactive maintenance to modern predictive and proactive approaches, this historical perspective helps in understanding the current best practices and future trends. Lastly, examining the key components and processes involved in MRO highlights the practical aspects of implementation. This includes inventory management, procurement strategies, and the use of technology such as CMMS (Computerized Maintenance Management Systems) to streamline operations. By starting with a clear understanding of the definition and scope of MRO, we can better appreciate its significance and how it fits into the broader operational landscape. Let's begin by defining what MRO entails and its scope within an organizational framework.
Definition and Scope of MRO
**Definition and Scope of MRO** Maintenance, Repair, and Operations (MRO) is a critical component of any organization's operational framework, particularly in industries that rely heavily on equipment and machinery. At its core, MRO encompasses all activities related to the upkeep, maintenance, and repair of physical assets to ensure they remain in optimal working condition. This includes routine maintenance tasks such as inspections, replacements, and repairs, as well as the procurement of spare parts and consumables necessary for these activities. The scope of MRO is broad and multifaceted. It involves not only the technical aspects of maintaining equipment but also the logistical and administrative processes that support these activities. For instance, MRO includes inventory management to ensure that the right parts are available when needed, supply chain management to source materials efficiently, and quality control measures to guarantee that repairs meet standards. Additionally, it involves scheduling maintenance activities to minimize downtime and maximize productivity, often leveraging advanced technologies like predictive maintenance and condition monitoring. In modern industrial settings, the scope of MRO extends beyond traditional maintenance practices. It incorporates advanced technologies such as IoT (Internet of Things) sensors, AI (Artificial Intelligence), and data analytics to predict potential failures before they occur. This proactive approach allows organizations to adopt a more preventive maintenance strategy, reducing unplanned downtime and improving overall operational efficiency. Moreover, effective MRO involves a strong focus on safety and compliance. This includes adhering to regulatory standards, ensuring that all maintenance activities are performed by trained personnel, and maintaining detailed records of all work done. The integration of safety protocols into MRO processes helps in mitigating risks and ensuring a safe working environment. From a financial perspective, MRO plays a crucial role in cost management. By optimizing maintenance schedules and reducing the need for emergency repairs, organizations can significantly lower their operational costs. Furthermore, well-managed MRO processes can extend the lifespan of equipment, delaying the need for capital expenditures on new machinery. In summary, the definition and scope of MRO are comprehensive and integral to the smooth operation of any asset-intensive business. It encompasses a wide range of activities from routine maintenance and repair to advanced predictive maintenance strategies, all aimed at ensuring that equipment operates efficiently and safely. Understanding these basics is essential for organizations looking to optimize their operations and achieve higher levels of productivity and cost-effectiveness.
Historical Context and Evolution
Understanding the historical context and evolution of Maintenance, Repair, and Operations (MRO) is crucial for grasping its significance and impact on modern industrial practices. The concept of MRO has its roots in the early days of industrialization, where maintaining machinery and equipment was essential for continuous production. In the 19th century, as factories began to dominate manufacturing, the need for systematic maintenance became apparent. Initially, maintenance was reactive; repairs were made only after equipment failed, leading to costly downtime and reduced productivity. As industries evolved, so did the approach to maintenance. The early 20th century saw the introduction of preventive maintenance strategies, where regular checks and scheduled repairs were implemented to minimize failures. This shift was largely driven by the advent of World War II, where efficient use of resources and machinery became critical for war efforts. Post-war, the development of new technologies and materials further enhanced MRO practices. The 1960s and 1970s witnessed the rise of predictive maintenance, leveraging emerging technologies like condition monitoring and vibration analysis to anticipate potential failures before they occurred. The 1980s marked a significant turning point with the introduction of computerized maintenance management systems (CMMS). These systems allowed for better tracking, scheduling, and analysis of maintenance activities, leading to improved efficiency and reduced costs. The advent of the internet and digital technologies in the late 20th century further transformed MRO by enabling real-time data collection, remote monitoring, and advanced analytics. Today, MRO incorporates cutting-edge technologies such as artificial intelligence (AI), Internet of Things (IoT), and machine learning to optimize maintenance schedules, predict failures accurately, and enhance overall asset reliability. The evolution of MRO has also been influenced by changing regulatory environments and safety standards. Stricter regulations have necessitated more rigorous maintenance practices to ensure compliance and prevent accidents. Additionally, environmental concerns have led to the development of sustainable MRO strategies that focus on reducing waste and energy consumption. In contemporary times, MRO is no longer just about fixing broken equipment but about optimizing asset performance throughout its lifecycle. This holistic approach involves integrating maintenance with other business functions like procurement, supply chain management, and quality control. The integration of digital twins—virtual replicas of physical assets—allows for simulated testing and predictive analytics, further enhancing the precision and effectiveness of MRO activities. In summary, the historical context and evolution of MRO reflect a journey from reactive to proactive and now predictive strategies. This transformation has been driven by technological advancements, changing regulatory landscapes, and an increasing focus on efficiency and sustainability. Understanding this evolution is essential for appreciating the complexities and opportunities within modern MRO practices, ultimately contributing to improved operational reliability and business success.
Key Components and Processes
Understanding the basics of Maintenance, Repair, and Operations (MRO) involves grasping its key components and processes, which are essential for ensuring the smooth operation of any organization. At its core, MRO encompasses all activities related to maintaining and repairing physical assets, such as machinery, equipment, and facilities. **Inventory Management** is a critical component, as it involves tracking and managing spare parts, tools, and other supplies necessary for maintenance tasks. Effective inventory management ensures that the right materials are available when needed, reducing downtime and increasing efficiency. **Work Order Management** is another vital process within MRO. This involves generating, assigning, and tracking work orders to ensure that maintenance tasks are completed systematically. Work orders help in scheduling preventive maintenance, addressing breakdowns promptly, and documenting all maintenance activities for future reference. **Preventive Maintenance (PM)** is a proactive approach aimed at preventing equipment failures through regular inspections and scheduled maintenance. PM schedules are typically based on the manufacturer's recommendations or historical data on equipment performance. **Condition-Based Maintenance (CBM)** is an advanced approach that uses real-time data from sensors and monitoring systems to predict when maintenance is required. This method optimizes maintenance activities by performing them only when necessary, thereby reducing unnecessary interventions and extending the lifespan of equipment. **Root Cause Analysis (RCA)** is a problem-solving method used to identify the underlying causes of equipment failures. By understanding the root cause, organizations can implement corrective actions to prevent future occurrences. **Supplier Management** plays a crucial role in MRO as it involves selecting reliable suppliers for spare parts and services. Building strong relationships with suppliers ensures timely delivery of high-quality materials, which is critical for maintaining operational continuity. **Training and Development** of maintenance personnel is also essential. Well-trained technicians can perform tasks more efficiently and effectively, leading to better overall performance and safety. **Technology Integration**, such as the use of Enterprise Asset Management (EAM) software or Computerized Maintenance Management Systems (CMMS), enhances the efficiency of MRO processes. These systems provide real-time data analytics, automate workflows, and offer insights into asset performance, enabling data-driven decision-making. By integrating these key components and processes into their operations, organizations can optimize their MRO activities, reduce costs, improve asset reliability, and ultimately enhance their overall productivity and competitiveness. Understanding these elements is fundamental to mastering the basics of MRO and leveraging its full potential to drive operational excellence.
The Role of MRO in Industrial Operations
In the realm of industrial operations, Maintenance, Repair, and Operations (MRO) plays a pivotal role in ensuring the smooth and efficient functioning of equipment and facilities. MRO encompasses a wide range of activities that are crucial for maintaining the reliability and uptime of machinery, managing costs effectively, and enhancing safety and compliance standards. By focusing on these key areas, industrial operations can significantly improve their overall performance and productivity. The impact of MRO on equipment reliability and uptime is particularly significant, as it directly affects the operational efficiency and output of any industrial facility. Effective MRO strategies not only reduce downtime but also extend the lifespan of equipment, thereby ensuring continuous production without interruptions. Additionally, MRO practices contribute to cost savings and budget management by optimizing resource allocation and reducing unnecessary expenditures. Furthermore, adhering to MRO protocols enhances safety and compliance by ensuring that all equipment meets regulatory standards, thereby protecting both personnel and the environment. Understanding the role of MRO in these aspects is essential for any industrial operation aiming to achieve peak performance. Let's delve deeper into the impact of MRO on equipment reliability and uptime, a critical factor that underpins the success of industrial operations.
Impact on Equipment Reliability and Uptime
The impact of Maintenance, Repair, and Operations (MRO) on equipment reliability and uptime is pivotal in industrial operations. Effective MRO practices ensure that machinery and equipment perform at optimal levels, minimizing downtime and maximizing productivity. By implementing a robust maintenance schedule, industries can prevent unexpected failures, reduce the need for costly repairs, and extend the lifespan of their assets. Regular inspections and predictive maintenance techniques, such as condition monitoring and vibration analysis, help in identifying potential issues before they escalate into major problems. This proactive approach not only enhances equipment reliability but also allows for planned maintenance windows, thereby reducing the likelihood of unplanned shutdowns that can disrupt production cycles. Moreover, a well-managed MRO strategy involves the efficient management of spare parts inventory. Having the right parts available at the right time can significantly reduce repair times, ensuring that equipment is back in operation quickly. This inventory management also helps in optimizing stock levels, avoiding overstocking or understocking scenarios that can lead to unnecessary costs or delays. Additionally, leveraging technology such as Computerized Maintenance Management Systems (CMMS) and Enterprise Asset Management (EAM) software can streamline MRO processes by automating work orders, tracking maintenance history, and providing real-time data analytics to improve decision-making. The role of skilled technicians is another critical factor in maintaining high equipment reliability and uptime. Continuous training and development programs ensure that maintenance personnel are equipped with the latest techniques and technologies, enabling them to perform tasks efficiently and effectively. Furthermore, fostering a culture of continuous improvement within the organization encourages feedback loops where insights from maintenance activities are used to refine processes and improve overall operational efficiency. In summary, the impact of MRO on equipment reliability and uptime is multifaceted and far-reaching. By combining proactive maintenance strategies, efficient inventory management, technological advancements, and skilled workforce development, industries can significantly enhance their operational performance. This not only leads to increased productivity but also reduces operational costs associated with downtime and repairs, ultimately contributing to the overall success and competitiveness of the organization. As such, MRO stands as a cornerstone in industrial operations, underpinning the reliability and uptime of critical equipment that drives business continuity and growth.
Cost Savings and Budget Management
In the realm of industrial operations, cost savings and budget management are pivotal components that significantly impact the overall efficiency and profitability of an organization. Maintenance, Repair, and Operations (MRO) play a crucial role in this context by ensuring that equipment and facilities are maintained at optimal levels, thereby reducing downtime and extending the lifespan of assets. Effective MRO practices involve meticulous planning, execution, and monitoring of maintenance schedules, which help in preventing unexpected breakdowns and reducing the need for costly repairs. By implementing predictive maintenance strategies, industries can anticipate potential issues before they arise, allowing for proactive measures that save both time and money. Budget management within MRO involves allocating resources efficiently to meet maintenance needs without overextending financial limits. This includes optimizing inventory levels of spare parts, negotiating favorable contracts with suppliers, and leveraging technology such as enterprise asset management (EAM) systems to streamline processes. EAM systems provide real-time data on asset performance, enabling better decision-making regarding maintenance priorities and resource allocation. Additionally, adopting a total cost of ownership (TCO) approach helps in evaluating the long-term costs associated with different maintenance strategies, ensuring that decisions are made with a holistic view of expenses. Another key aspect of cost savings through MRO is the reduction of energy consumption and waste. Regular maintenance of machinery ensures that it operates at peak efficiency, minimizing energy usage and reducing the environmental footprint of the operation. Furthermore, well-maintained equipment tends to produce fewer defects and less waste, contributing to both cost savings and sustainability goals. Training personnel in best practices for maintenance also enhances the effectiveness of MRO activities, as skilled workers can identify potential issues early on and perform tasks more efficiently. Incorporating data analytics into MRO processes further enhances budget management by providing insights into historical trends and patterns in equipment performance. This data can be used to forecast future maintenance needs accurately, allowing for better budget planning and resource allocation. Moreover, leveraging automation technologies such as IoT sensors can provide real-time monitoring of equipment health, enabling swift responses to emerging issues before they escalate into major problems. Ultimately, the integration of robust MRO practices into industrial operations not only leads to significant cost savings but also improves overall operational reliability and productivity. By focusing on preventive maintenance, optimizing resource allocation, and leveraging advanced technologies, industries can achieve substantial reductions in operational expenses while maintaining high levels of performance and efficiency. This holistic approach to MRO underscores its critical role in driving cost-effective and sustainable industrial operations.
Enhancing Safety and Compliance
Enhancing safety and compliance is a critical aspect of industrial operations, and Maintenance, Repair, and Operations (MRO) plays a pivotal role in achieving these objectives. Effective MRO practices ensure that equipment and facilities are maintained in optimal condition, reducing the risk of accidents and ensuring adherence to regulatory standards. By implementing robust maintenance schedules, industries can prevent equipment failures that could lead to hazardous situations. Regular inspections and predictive maintenance technologies, such as condition monitoring and vibration analysis, help identify potential issues before they escalate into major problems. This proactive approach not only enhances safety but also minimizes downtime, thereby improving overall operational efficiency. Compliance with industry regulations is another key area where MRO excels. Industries must adhere to stringent safety and environmental standards set by governing bodies. MRO ensures that all equipment and processes are compliant with these regulations through meticulous record-keeping and adherence to maintenance protocols. For instance, in industries like oil and gas or chemical processing, MRO teams must ensure that critical safety systems are functioning correctly and that regular audits are conducted to verify compliance. This not only avoids legal penalties but also fosters a culture of safety within the organization. Moreover, MRO contributes significantly to environmental compliance by ensuring that industrial operations do not harm the environment. Proper maintenance of pollution control equipment and waste management systems is crucial for preventing environmental hazards. By keeping these systems in good working order, industries can avoid costly fines and reputational damage associated with environmental violations. In addition to these benefits, advanced MRO strategies leverage technology to enhance safety and compliance further. The use of digital twins, IoT sensors, and data analytics allows for real-time monitoring of equipment health and performance. These tools provide insights that help in making informed decisions about maintenance schedules, thereby optimizing resource allocation and reducing the likelihood of unexpected failures. Training and continuous education are also integral components of an effective MRO strategy aimed at enhancing safety and compliance. Well-trained personnel are better equipped to handle complex maintenance tasks safely and efficiently. Regular training programs ensure that employees are updated on the latest technologies and regulatory requirements, which is essential for maintaining a safe and compliant work environment. In conclusion, MRO is indispensable for enhancing safety and compliance in industrial operations. Through proactive maintenance practices, adherence to regulatory standards, environmental stewardship, technological innovation, and continuous training, MRO ensures that industries operate safely while minimizing risks and legal liabilities. By integrating these elements into their operational framework, industries can achieve higher levels of efficiency, reliability, and sustainability.
Best Practices and Future Trends in MRO
In the rapidly evolving landscape of Maintenance, Repair, and Operations (MRO), several key best practices and future trends are shaping the industry. To remain competitive and efficient, organizations must adopt a multifaceted approach that integrates cutting-edge technologies, strategic sourcing, and continuous improvement. The adoption of digital technologies is a cornerstone of modern MRO, enabling real-time monitoring, predictive maintenance, and data-driven decision-making. Strategic sourcing and supply chain management are also crucial, as they help in optimizing resource allocation and ensuring the availability of critical components. Additionally, continuous improvement and training programs are essential for maintaining a skilled workforce and driving innovation. By focusing on these areas, MRO operations can enhance operational efficiency, reduce downtime, and improve overall performance. As we delve into the specifics of these strategies, it becomes clear that the adoption of digital technologies is a foundational element that sets the stage for transformative change in MRO practices. Transitioning to the first key area, the adoption of digital technologies is revolutionizing how MRO is conducted, offering unprecedented levels of precision and efficiency. --- **Adoption of Digital Technologies** The integration of digital technologies such as IoT sensors, AI algorithms, and cloud-based platforms is revolutionizing MRO by enabling proactive maintenance strategies. These technologies allow for real-time monitoring of equipment health, predictive analytics to forecast potential failures, and automated workflows that streamline maintenance processes. For instance, IoT sensors can detect anomalies in machinery performance, triggering alerts for maintenance personnel to intervene before a failure occurs. This proactive approach not only reduces unplanned downtime but also extends the lifespan of equipment, leading to significant cost savings and improved operational reliability. As digital technologies continue to advance, they will play an increasingly vital role in optimizing MRO operations. --- **Strategic Sourcing and Supply Chain Management** Effective strategic sourcing and supply chain management are critical components of successful MRO operations. By leveraging data analytics and market intelligence, organizations can optimize their procurement processes to ensure the timely availability of necessary parts and materials. This involves building strong relationships with suppliers, implementing just-in-time inventory systems, and utilizing digital platforms for procurement and logistics management. Strategic sourcing also involves diversifying supply chains to mitigate risks associated with single-source dependencies. By doing so, organizations can minimize lead times, reduce inventory costs, and enhance their overall supply chain resilience. --- **Continuous Improvement and Training** Continuous improvement and training are essential for maintaining a competitive edge in MRO. Regular training programs ensure that maintenance personnel are equipped with the latest skills and knowledge to handle advanced technologies and complex equipment. This includes training in areas such as data analysis, robotics, and cybersecurity. Additionally, fostering a culture of continuous improvement encourages employees to identify and implement process improvements, leading to enhanced efficiency and reduced errors. Organizations can also benefit from adopting methodologies like Lean and Six Sigma to eliminate waste and optimize workflows. By investing in their workforce and promoting a culture of continuous improvement, organizations can drive innovation and achieve sustained excellence in MRO operations.
Adoption of Digital Technologies
The adoption of digital technologies is revolutionizing the Maintenance, Repair, and Operations (MRO) sector, transforming traditional practices into highly efficient and data-driven processes. At the heart of this transformation are advanced technologies such as Artificial Intelligence (AI), Internet of Things (IoT), and Big Data analytics. These innovations enable real-time monitoring and predictive maintenance, allowing organizations to anticipate equipment failures before they occur. For instance, IoT sensors can be embedded in machinery to continuously monitor performance metrics, sending alerts when anomalies are detected. This proactive approach not only reduces downtime but also optimizes resource allocation and extends the lifespan of equipment. AI algorithms further enhance MRO operations by analyzing vast amounts of data to identify patterns and trends that human analysts might miss. Machine learning models can predict maintenance needs based on historical data, environmental conditions, and usage patterns, ensuring that maintenance is performed exactly when needed. Additionally, digital twin technology creates virtual replicas of physical assets, allowing for simulated testing and optimization without the risk of disrupting actual operations. Another significant impact of digital technologies in MRO is the integration of augmented reality (AR) and virtual reality (VR). These tools enhance training programs by providing immersive experiences that simulate real-world scenarios, improving the skills and confidence of maintenance personnel. AR can also guide technicians through complex repair procedures in real-time, reducing errors and speeding up the repair process. Moreover, cloud-based platforms and mobile applications are streamlining communication and collaboration within MRO teams. These platforms provide centralized access to maintenance records, schedules, and inventory levels, ensuring that all stakeholders have the information they need at their fingertips. Automated workflows and notifications help in managing work orders efficiently, reducing administrative burdens and improving overall productivity. In terms of future trends, the integration of blockchain technology is expected to play a crucial role in ensuring transparency and security in MRO supply chains. Blockchain can track the origin and movement of spare parts, preventing counterfeiting and ensuring compliance with regulatory standards. Furthermore, the increasing use of 5G networks will enable faster data transfer rates and lower latency, making remote monitoring and control even more effective. As organizations continue to adopt these digital technologies, best practices will include investing in robust cybersecurity measures to protect sensitive data, fostering a culture of continuous learning to keep up with technological advancements, and implementing phased rollouts to minimize disruption to existing operations. By embracing these trends and best practices, MRO professionals can leverage digital technologies to drive efficiency, reduce costs, and enhance overall operational reliability. This holistic approach will not only meet current demands but also position organizations for long-term success in an increasingly complex and interconnected world.
Strategic Sourcing and Supply Chain Management
Strategic sourcing and supply chain management are pivotal components in the realm of Maintenance, Repair, and Operations (MRO), ensuring that organizations optimize their procurement processes and maintain operational efficiency. At its core, strategic sourcing involves a systematic approach to identifying, evaluating, and engaging suppliers that can provide the best value for the organization. This goes beyond mere cost-cutting; it encompasses a holistic view of supplier performance, quality, reliability, and innovation. By leveraging advanced analytics and market intelligence, companies can make informed decisions that align with their long-term goals. In the context of MRO, strategic sourcing is particularly crucial because it directly impacts the availability and quality of spare parts, tools, and services necessary for maintaining equipment and facilities. Effective strategic sourcing in MRO involves developing robust supplier relationships, implementing just-in-time inventory systems, and ensuring compliance with regulatory standards. This not only reduces downtime but also enhances overall plant reliability and safety. Supply chain management complements strategic sourcing by focusing on the end-to-end flow of goods, services, and information from raw materials to end customers. In MRO, this includes managing the logistics of spare parts delivery, coordinating with multiple stakeholders, and optimizing inventory levels to meet demand without overstocking. Advanced technologies such as IoT sensors, predictive analytics, and blockchain are transforming supply chain management by providing real-time visibility into inventory levels, predicting maintenance needs, and ensuring transparency across the supply chain. Best practices in strategic sourcing and supply chain management for MRO include adopting a category management approach where procurement is segmented into distinct categories to maximize leverage and expertise. Another key practice is implementing a total cost of ownership (TCO) analysis to evaluate suppliers based on their overall impact on the organization rather than just initial purchase price. Additionally, fostering collaborative relationships with suppliers through joint innovation initiatives can lead to mutual benefits such as improved product design and reduced lead times. Looking ahead, future trends in strategic sourcing and supply chain management for MRO are likely to be driven by digital transformation. The integration of artificial intelligence (AI) and machine learning (ML) will enable more accurate demand forecasting, automated procurement processes, and enhanced supplier performance monitoring. The rise of Industry 4.0 technologies will also see increased adoption of smart warehouses and autonomous logistics systems, further streamlining the supply chain. Moreover, sustainability will become a critical factor as organizations seek to reduce their environmental footprint through green procurement practices and sustainable supply chains. In conclusion, strategic sourcing and supply chain management are essential for optimizing MRO operations. By adopting best practices such as category management, TCO analysis, and collaborative supplier relationships, organizations can enhance their operational efficiency and reduce costs. As technology continues to evolve, embracing digital transformation will be key to staying competitive in the future landscape of MRO.
Continuous Improvement and Training
Continuous Improvement and Training are cornerstone elements in the realm of Maintenance, Repair, and Operations (MRO), driving best practices and future trends. In an ever-evolving industrial landscape, organizations must adopt a culture of continuous improvement to stay competitive. This involves a systematic approach to identifying areas for enhancement, implementing changes, and measuring the impact of these changes. Training plays a pivotal role in this process, as it equips personnel with the necessary skills and knowledge to execute new methodologies effectively. Effective continuous improvement begins with a robust feedback loop, where data from various sources—such as maintenance logs, customer feedback, and performance metrics—are analyzed to pinpoint inefficiencies. This data-driven approach allows for targeted interventions that can significantly reduce downtime, improve asset reliability, and enhance overall operational efficiency. For instance, adopting lean principles can help streamline processes by eliminating waste and optimizing workflows. Training is integral to the success of continuous improvement initiatives. It ensures that employees are not only aware of new procedures but also have the competencies to implement them seamlessly. Modern training methods include on-the-job training, simulation-based learning, and digital platforms that offer real-time access to instructional content. These methods cater to diverse learning styles and can be tailored to address specific skill gaps within the workforce. Moreover, continuous improvement fosters a culture of innovation within organizations. By encouraging employees to suggest improvements and rewarding innovative ideas, companies can leverage collective intelligence to drive progress. This collaborative approach not only boosts morale but also ensures that solutions are practical and feasible from an operational standpoint. Looking ahead, future trends in MRO will increasingly focus on leveraging technology to enhance continuous improvement and training. The integration of Industry 4.0 technologies such as IoT sensors, AI, and machine learning will provide real-time insights into asset performance, enabling predictive maintenance strategies that minimize unexpected failures. Virtual and augmented reality will revolutionize training by offering immersive experiences that simulate real-world scenarios without the risks associated with actual equipment operation. Additionally, the adoption of digital twin technology will allow for the creation of virtual replicas of physical assets, facilitating detailed analysis and simulation of maintenance scenarios. This will enable more precise planning and execution of maintenance activities, further optimizing resource allocation and reducing costs. In conclusion, continuous improvement and training are essential components of best practices in MRO. By fostering a culture of ongoing enhancement and equipping personnel with the latest skills and knowledge, organizations can achieve higher levels of efficiency, reliability, and innovation. As technology continues to advance, embracing these trends will be crucial for staying ahead in the competitive landscape of MRO.