What Is Po Number

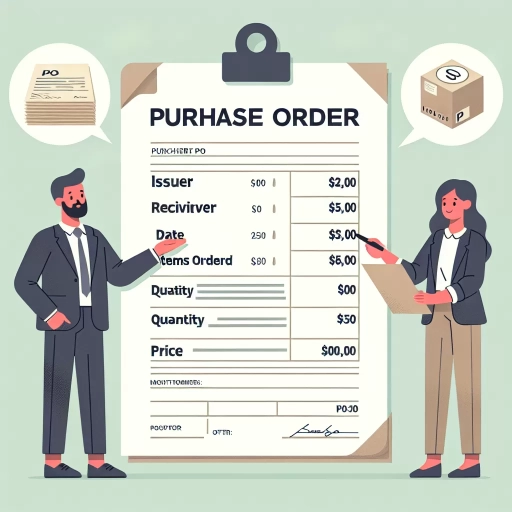
In the intricate world of business operations, a purchase order (PO) number serves as a crucial identifier that streamlines transactions and ensures clarity in procurement processes. This article delves into the multifaceted role of PO numbers, providing a comprehensive overview that is both informative and engaging. We will begin by **Understanding the Basics of a Purchase Order Number**, exploring what constitutes a PO number, its significance, and how it is generated. This foundational knowledge will set the stage for a deeper examination of **How Purchase Order Numbers Are Used in Business Operations**, where we will discuss their role in managing inventory, tracking orders, and facilitating communication between buyers and suppliers. Finally, we will outline **Best Practices for Creating and Managing Purchase Order Numbers**, offering practical advice on how to optimize their use for enhanced efficiency and accuracy. By the end of this article, readers will have a thorough understanding of the importance and application of PO numbers, starting with the fundamental principles that underpin their use. Let's begin by **Understanding the Basics of a Purchase Order Number**.
Understanding the Basics of a Purchase Order Number
Understanding the basics of a purchase order (PO) number is crucial for any business looking to streamline its procurement processes and maintain accurate financial records. A PO number serves as a unique identifier for each purchase order, facilitating efficient tracking and management of transactions. This article will delve into three key aspects of PO numbers: their definition and purpose, the key components that make up a PO number, and their importance in business transactions. First, we will explore the **Definition and Purpose** of a PO number, clarifying its role in initiating and documenting purchases. This foundational understanding is essential for grasping how PO numbers integrate into broader business operations. Next, we will dissect the **Key Components of a PO Number**, highlighting the elements that ensure each number is distinct and informative. This breakdown will help readers appreciate the structured approach behind creating these identifiers. Finally, we will discuss the **Importance in Business Transactions**, illustrating how PO numbers enhance transparency, accountability, and efficiency in procurement processes. By understanding these facets, businesses can better leverage PO numbers to optimize their operations. To begin, let's start with the **Definition and Purpose** of a PO number, which sets the stage for comprehending its significance and application in business contexts.
Definition and Purpose
A Purchase Order (PO) number is a unique identifier assigned to a purchase order, serving as a critical component in the procurement process. **Definition and Purpose** of a PO number are intertwined, as it not only defines the transaction but also facilitates efficient tracking and management. A PO number is essentially a serial number or code that distinguishes one purchase order from another within an organization's system. This identifier is typically generated by the purchasing department or procurement software and is included on the purchase order document. The purpose of a PO number is multifaceted: it ensures clarity and precision in communication between the buyer and the seller, helps in organizing and tracking orders, and simplifies the process of reconciling invoices with corresponding orders. From a practical standpoint, the PO number acts as a reference point for all parties involved in the transaction. For instance, when a supplier receives an order, they can quickly identify the specific purchase order being referenced by the PO number, ensuring that they fulfill the correct order details. Similarly, when the buyer receives goods or services, they can match the PO number on the delivery documents with their internal records to verify that the correct items have been received. Moreover, PO numbers play a crucial role in financial management. They help in maintaining accurate records of expenditures, which is essential for budgeting and auditing purposes. By using a unique PO number for each transaction, organizations can easily trace back any discrepancies or issues related to the order, thereby enhancing accountability and transparency. In addition to these functional benefits, PO numbers also streamline the workflow within an organization. They enable automated processing of orders through enterprise resource planning (ERP) systems or other procurement software, reducing manual errors and increasing efficiency. This automation allows for quicker approval processes, faster order fulfillment, and improved overall productivity. In summary, the definition and purpose of a PO number are deeply rooted in its role as a unique identifier that enhances clarity, efficiency, and accountability in the procurement process. By assigning a distinct PO number to each purchase order, organizations can better manage their transactions, ensure accurate record-keeping, and improve their overall operational performance. This foundational element of procurement is essential for maintaining smooth and reliable business operations.
Key Components of a PO Number
### Key Components of a PO Number A Purchase Order (PO) number is a critical element in the procurement process, serving as a unique identifier for each purchase order. Understanding its key components is essential for efficient and accurate transaction management. Here are the primary elements that make up a PO number: 1. **Prefix**: Often used to indicate the type of purchase order or the department issuing it, the prefix helps in categorizing and tracking orders based on specific criteria. 2. **Sequential Number**: This is a unique numerical identifier that distinguishes one purchase order from another. It ensures that each PO is distinct and can be easily referenced. 3. **Date Code**: Incorporating a date code within the PO number helps in tracking when the order was placed. This can be particularly useful for auditing and compliance purposes. 4. **Vendor Code**: Including a vendor code allows for quick identification of the supplier involved in the transaction, facilitating better vendor management and relationship tracking. 5. **Department Code**: This component identifies which department within the organization is responsible for the purchase, aiding in internal budgeting and accountability. 6. **Project Code**: For organizations that manage multiple projects, a project code ensures that purchases are correctly allocated to the relevant project, enhancing financial transparency and project tracking. 7. **Revision Number**: If changes are made to an existing purchase order, a revision number helps in tracking these amendments, ensuring that all stakeholders are aware of the latest version. 8. **Check Digit**: Some PO numbers include a check digit to verify the integrity of the number, preventing errors during data entry or transmission. Each of these components plays a vital role in ensuring that purchase orders are processed efficiently, accurately, and transparently. By including these elements, organizations can streamline their procurement processes, reduce errors, and improve overall operational efficiency. For instance, having a clear vendor code can expedite payment processing and improve supplier relationships, while a department code can help in budgetary control and resource allocation. The inclusion of a date code and revision number enhances audit trails and compliance with regulatory requirements. In summary, understanding and effectively utilizing these key components of a PO number is crucial for maintaining robust procurement practices within any organization.
Importance in Business Transactions
In the realm of business transactions, understanding the importance of a Purchase Order (PO) number is crucial for maintaining efficiency, transparency, and accountability. A PO number serves as a unique identifier for each purchase order, allowing both buyers and sellers to track and manage transactions seamlessly. This identifier is essential for several reasons. Firstly, it helps in organizing and categorizing orders within a company's system, making it easier to locate specific orders and their associated details. This organization is vital for inventory management, as it ensures that goods are received, stored, and dispatched correctly. Secondly, a PO number enhances communication between the buyer and the seller. It acts as a reference point in all correspondence related to the order, reducing misunderstandings and errors. For instance, if there are discrepancies in the shipment or billing, the PO number can be used to quickly identify the issue and resolve it promptly. This clarity in communication also fosters trust and reliability between business partners. Thirdly, from an accounting perspective, PO numbers are indispensable for accurate financial recording. They help in matching invoices with corresponding orders, ensuring that payments are made correctly and on time. This process aids in maintaining accurate financial records and simplifies the auditing process by providing a clear audit trail. Moreover, PO numbers play a significant role in compliance and regulatory adherence. In industries subject to strict regulations, such as healthcare or defense, PO numbers can be used to track and verify compliance with legal requirements. This ensures that all transactions are conducted in accordance with industry standards and laws. Additionally, PO numbers contribute to improved customer service. By having a unique identifier for each order, businesses can provide better support to their customers. For example, if a customer queries about the status of their order, the PO number can be used to quickly retrieve the relevant information and provide an update. In summary, the importance of a PO number in business transactions cannot be overstated. It streamlines operations, enhances communication, ensures financial accuracy, supports regulatory compliance, and improves customer service. As a fundamental component of purchase orders, understanding and utilizing PO numbers effectively is essential for any business looking to optimize its procurement processes and maintain strong relationships with suppliers and customers. By integrating PO numbers into their transactional framework, businesses can achieve greater efficiency, transparency, and reliability in their operations.
How Purchase Order Numbers Are Used in Business Operations
In the intricate landscape of business operations, purchase order numbers play a pivotal role in ensuring efficiency, transparency, and accuracy across various departments. These unique identifiers are more than just numerical codes; they serve as the backbone of several critical processes. First, they facilitate **Order Placement and Tracking**, enabling businesses to monitor the status of their orders from inception to delivery. This not only streamlines communication between buyers and suppliers but also helps in managing expectations and resolving any discrepancies promptly. Additionally, purchase order numbers are essential for **Inventory Management and Control**, as they help in tracking the receipt and storage of goods, thereby maintaining accurate inventory levels. Lastly, they are crucial in **Financial Accounting and Auditing**, providing a clear audit trail that aids in reconciling invoices, managing budgets, and ensuring compliance with financial regulations. By integrating these functions seamlessly, purchase order numbers enhance overall operational efficiency. Let's delve deeper into how these numbers are used in **Order Placement and Tracking** to understand their impact on the initial stages of procurement.
Order Placement and Tracking
Order placement and tracking are pivotal components in the efficient execution of business operations, particularly when it comes to managing purchase orders. The process begins with the creation of a purchase order (PO), which is a formal document issued by a buyer to a seller, detailing the items, quantities, and agreed-upon prices for goods or services. Once the PO is generated and sent to the supplier, it serves as a legally binding contract that outlines the terms of the transaction. The PO number, a unique identifier assigned to each purchase order, plays a crucial role in this process. It facilitates easy tracking and referencing of the order throughout its lifecycle. When an order is placed, the PO number is used to communicate with the supplier, ensuring that both parties are on the same page regarding the specifics of the order. This clarity helps in avoiding misunderstandings and delays. As the order progresses from placement to delivery, the PO number becomes an essential tool for tracking purposes. It allows procurement teams to monitor the status of their orders in real-time, whether it is in production, shipping, or awaiting receipt. This transparency enables better inventory management and helps in planning for future needs. For instance, if an order is delayed, the PO number can be used to quickly identify the issue and communicate with the supplier to resolve it promptly. Moreover, the PO number is integral to financial management within an organization. It helps in matching invoices received from suppliers with the corresponding purchase orders, ensuring that payments are accurate and timely. This process, known as "three-way matching," involves verifying that the invoice details match both the PO and the goods received, thereby reducing the risk of errors or fraudulent activities. In addition to these operational benefits, the PO number also enhances accountability and compliance within an organization. It provides a clear audit trail that can be used to trace back any discrepancies or issues related to the order. This is particularly important for regulatory compliance and internal audits, where detailed records of transactions are often required. Technological advancements have further streamlined the order placement and tracking process. Many businesses now use enterprise resource planning (ERP) systems or procurement software that automate much of the PO management process. These systems generate PO numbers automatically, send notifications at various stages of the order lifecycle, and provide real-time updates on order status. This automation not only increases efficiency but also reduces manual errors, making the entire process more reliable and efficient. In conclusion, the PO number is a cornerstone of effective order placement and tracking in business operations. It ensures clarity, transparency, and accountability throughout the procurement process, from initial order placement to final delivery and payment. By leveraging this unique identifier, businesses can optimize their supply chain management, improve financial accuracy, and maintain regulatory compliance, ultimately contributing to smoother and more efficient business operations.
Inventory Management and Control
Inventory management and control are pivotal components of efficient business operations, particularly when integrated with the use of purchase order numbers. Effective inventory management involves the systematic tracking, monitoring, and optimization of stock levels to ensure that the right products are available in the right quantities at the right time. This process is crucial for maintaining smooth supply chain operations, reducing costs, and enhancing customer satisfaction. Incorporating purchase order numbers into inventory management adds a layer of precision and accountability. A purchase order (PO) number serves as a unique identifier for each order, allowing businesses to track the status of their purchases from initiation to delivery. This helps in maintaining accurate records of ordered items, expected delivery dates, and costs associated with each purchase. By linking PO numbers to inventory records, businesses can better manage stock levels by knowing exactly what has been ordered, when it is expected to arrive, and how much of it is already in stock. Moreover, PO numbers facilitate better communication between departments within an organization and with external suppliers. For instance, if there are discrepancies or delays in shipments, the PO number can be used to quickly identify the specific order in question and resolve issues promptly. This transparency also aids in financial management by ensuring that invoices are matched correctly with corresponding POs, thereby preventing errors in accounting and payment processing. From an operational standpoint, integrating PO numbers into inventory control systems enables real-time tracking and analysis. Advanced inventory management software often includes features that allow businesses to generate reports based on PO numbers, providing insights into purchasing trends, supplier performance, and inventory turnover rates. These analytics can inform strategic decisions such as optimizing reorder points, negotiating better terms with suppliers, and improving overall supply chain efficiency. Additionally, the use of PO numbers in inventory management helps in maintaining compliance with regulatory requirements and internal policies. For example, in industries subject to strict auditing standards like healthcare or aerospace, having a detailed record of all purchases linked to specific PO numbers ensures that all transactions are traceable and auditable. This level of documentation also supports internal audits and helps in identifying any irregularities or discrepancies early on. In summary, the integration of purchase order numbers into inventory management and control processes is essential for modern businesses seeking to optimize their operations. By providing a clear and traceable record of all purchases, PO numbers enhance transparency, accountability, and efficiency across various aspects of business operations—from procurement and logistics to finance and compliance. This holistic approach ensures that businesses can maintain optimal stock levels while minimizing errors and maximizing customer satisfaction.
Financial Accounting and Auditing
In the realm of business operations, financial accounting and auditing play crucial roles in ensuring the integrity and transparency of financial transactions. When it comes to purchase order numbers, these disciplines are particularly relevant. Financial accounting involves the systematic recording, reporting, and analysis of financial transactions, including those related to purchases. A purchase order (PO) number is a unique identifier assigned to each purchase order, which serves as a reference point for tracking and verifying transactions. This number is essential for maintaining accurate financial records, as it helps in matching invoices with corresponding purchase orders, thereby preventing discrepancies and fraud. Auditing, on the other hand, involves an independent examination of financial records to ensure their accuracy and compliance with established standards. In the context of purchase orders, auditors use PO numbers to verify that all transactions are properly authorized, recorded, and accounted for. For instance, auditors can trace a PO number through various stages of the procurement process—from the initial request to the final payment—to ensure that each step aligns with company policies and regulatory requirements. This meticulous scrutiny helps in identifying any irregularities or potential misappropriations of funds. The integration of PO numbers into financial accounting and auditing processes enhances the overall efficiency and reliability of business operations. It facilitates better budgeting and forecasting by providing clear insights into expenditure patterns. Moreover, it aids in compliance with financial regulations such as the Sarbanes-Oxley Act, which mandates robust internal controls over financial reporting. By leveraging PO numbers effectively, businesses can streamline their procurement processes, reduce errors, and build trust with stakeholders through transparent financial practices. In summary, the use of purchase order numbers is a cornerstone of sound financial management within business operations. It not only aids in accurate financial recording but also supports rigorous auditing practices that uphold the integrity of financial transactions. As such, PO numbers are indispensable tools for ensuring that businesses operate with transparency, accountability, and compliance with regulatory standards.
Best Practices for Creating and Managing Purchase Order Numbers
When it comes to creating and managing purchase order numbers, several best practices are crucial for ensuring efficiency, accuracy, and compliance. At the heart of effective purchase order management lies the importance of **Standardization and Consistency**, which helps in maintaining a uniform format that can be easily understood and tracked across the organization. However, this is just one piece of the puzzle. **Automation and Integration with Systems** also play a vital role by streamlining processes, reducing manual errors, and enhancing overall productivity. Additionally, **Security and Compliance Considerations** must be taken into account to protect sensitive information and adhere to regulatory requirements. By implementing these best practices, businesses can significantly improve their procurement processes. Let's start by exploring the foundational aspect of **Standardization and Consistency**, which sets the stage for a well-organized and reliable purchase order system.
Standardization and Consistency
Standardization and consistency are cornerstone principles in the effective creation and management of purchase order numbers. These elements ensure that every transaction is uniquely identifiable, traceable, and compliant with organizational and regulatory standards. By standardizing the format and structure of purchase order numbers, businesses can avoid confusion and errors that might arise from inconsistent or ambiguous numbering systems. For instance, a standardized format could include a combination of letters and numbers that denote specific details such as the date of issuance, vendor code, or departmental identifier. This not only enhances clarity but also facilitates quick retrieval and analysis of purchase order data. Consistency in generating purchase order numbers also aids in maintaining a seamless audit trail. When each purchase order number follows a predictable pattern, it becomes easier to track the history of transactions, identify trends, and detect any discrepancies or anomalies. This is particularly crucial for compliance purposes, as it allows organizations to demonstrate transparency and adherence to internal controls and external regulations. Moreover, standardized purchase order numbers streamline communication between departments and with external stakeholders like vendors and auditors. It ensures that all parties involved in the procurement process are on the same page, reducing misunderstandings and improving overall efficiency. In addition to these operational benefits, standardization and consistency contribute significantly to data integrity. By using a uniform system for generating purchase order numbers, organizations can minimize the risk of duplicate or missing numbers, which could lead to financial discrepancies or legal issues. Automated systems that generate these numbers based on predefined rules further enhance accuracy and reduce human error. This systematic approach also supports scalability; as the organization grows, the standardized system remains robust and adaptable, ensuring that the integrity of purchase order data is maintained across all transactions. Ultimately, the integration of standardization and consistency into the creation and management of purchase order numbers is a best practice that underpins effective procurement processes. It fosters a culture of precision, transparency, and reliability within an organization, ultimately contributing to better decision-making and improved financial management. By adhering to these principles, businesses can ensure that their purchase order systems are robust, efficient, and compliant with both internal policies and external regulations. This foundational aspect of procurement management sets the stage for streamlined operations, enhanced accountability, and sustained business success.
Automation and Integration with Systems
Automation and integration with systems are crucial components in the efficient creation and management of purchase order numbers. By automating the process, businesses can significantly reduce manual errors, streamline workflows, and enhance overall productivity. For instance, automated systems can generate unique purchase order numbers sequentially, ensuring consistency and avoiding duplicates. This not only simplifies the tracking and auditing of orders but also minimizes the risk of human error. Integration with existing systems such as Enterprise Resource Planning (ERP), Customer Relationship Management (CRM), and Supply Chain Management (SCM) further amplifies these benefits. When purchase order numbers are seamlessly integrated into these systems, real-time updates and synchronization become possible. This allows for better visibility across departments, enabling procurement teams to monitor order status, track inventory levels, and manage supplier relationships more effectively. Moreover, integrated systems can automate approval workflows, ensuring that purchase orders are reviewed and approved in a timely manner. Automated notifications can be set up to alert stakeholders at various stages of the process, reducing delays and improving communication. Additionally, advanced analytics and reporting capabilities provided by integrated systems help in identifying trends, optimizing purchasing decisions, and improving supplier performance metrics. From a compliance perspective, automation and integration also play a vital role. Automated systems can enforce company policies and regulatory requirements consistently, reducing the risk of non-compliance. For example, they can ensure that all purchase orders adhere to specific formatting standards or include necessary documentation such as tax IDs or vendor information. In summary, integrating automation into the creation and management of purchase order numbers is a best practice that enhances operational efficiency, reduces errors, and improves compliance. By leveraging advanced technologies and integrating them with existing business systems, organizations can achieve greater transparency, better decision-making capabilities, and ultimately drive more effective procurement processes. This strategic approach not only supports the smooth operation of daily activities but also positions businesses for long-term success in an increasingly complex and competitive market environment.
Security and Compliance Considerations
When it comes to creating and managing purchase order numbers, security and compliance considerations are paramount to ensure the integrity and reliability of your procurement processes. Here, it is crucial to implement robust security measures to protect sensitive information and adhere to regulatory standards. Firstly, **data encryption** should be a cornerstone of your security strategy. Encrypting purchase order data both in transit and at rest safeguards against unauthorized access and potential breaches. This is particularly important if you are using digital platforms or cloud services for managing POs. Additionally, **access controls** must be stringent, with role-based permissions that limit who can create, edit, or view purchase orders. This helps prevent unauthorized modifications and ensures that only authorized personnel have access to sensitive financial information. **Compliance** is another critical aspect. Depending on your industry, there may be specific regulations you need to adhere to, such as the General Data Protection Regulation (GDPR) in Europe or the Sarbanes-Oxley Act (SOX) in the United States. Ensuring that your PO management system is compliant with these regulations can help avoid legal repercussions and maintain trust with stakeholders. For instance, GDPR mandates that personal data be processed securely and transparently, which includes any personal information included in purchase orders. **Audit trails** are essential for maintaining transparency and accountability. Implementing a system that logs all changes to purchase orders provides a clear record of who made what changes and when. This not only helps in tracking down any discrepancies but also serves as a deterrent against fraudulent activities. Moreover, regular **security audits** should be conducted to identify vulnerabilities and update your security protocols accordingly. **Vendor vetting** is also a key consideration. Before issuing a purchase order, it is vital to ensure that the vendor is reputable and compliant with your organization's standards. This includes verifying their credentials, checking for any past compliance issues, and ensuring they have adequate security measures in place to protect your data. Incorporating **two-factor authentication** for users accessing the PO system adds an extra layer of security, making it more difficult for unauthorized individuals to gain access. Furthermore, **training programs** for employees involved in the procurement process can help them understand the importance of security and compliance, reducing the risk of human error. Finally, having a **disaster recovery plan** in place ensures that your purchase order data remains accessible even in the event of a system failure or natural disaster. This plan should include regular backups and a clear protocol for restoring data quickly. By prioritizing these security and compliance considerations, you can ensure that your purchase order management process is not only efficient but also secure and compliant with relevant regulations, thereby protecting your organization's financial integrity and reputation.