What Is Cnc Play

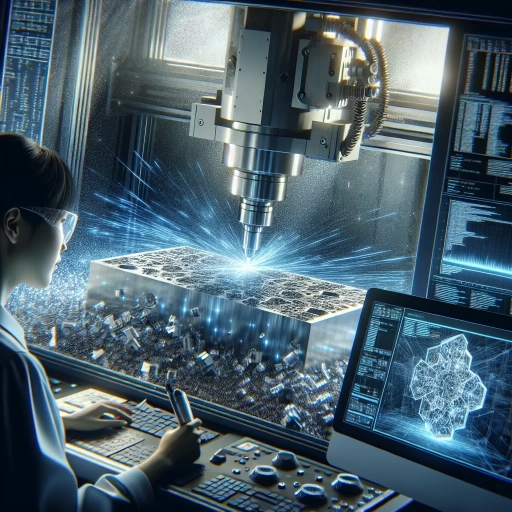
In the modern era of precision manufacturing, Computer Numerical Control (CNC) technology has revolutionized the way industries produce goods. CNC machining, often referred to as CNC play, involves the use of computer-controlled machines to perform a variety of tasks with unparalleled accuracy and speed. This innovative technology has transformed traditional manufacturing processes, enabling the creation of complex parts and products that were previously impossible to produce. The article delves into the multifaceted world of CNC, starting with an in-depth look at **Understanding CNC Technology**, where we explore the fundamental principles and mechanisms behind this advanced manufacturing method. We then examine **Applications and Uses of CNC**, highlighting how this technology is employed across various sectors, from aerospace to automotive and beyond. Finally, we discuss **Benefits and Future of CNC**, outlining the advantages it offers and its potential impact on future industrial landscapes. By understanding the core of CNC technology, we can better appreciate its widespread applications and the significant benefits it brings to modern manufacturing. Let's begin by diving into the intricacies of **Understanding CNC Technology**.
Understanding CNC Technology
In the modern manufacturing landscape, Computer Numerical Control (CNC) technology stands as a cornerstone of precision and efficiency. This advanced technology has revolutionized the way industries produce complex parts and components, ensuring high accuracy and repeatability. To fully grasp the significance of CNC technology, it is essential to delve into its fundamental aspects. This article will explore the **Definition and Basics of CNC**, providing a clear understanding of how these systems operate and their core principles. We will also trace the **History and Evolution of CNC**, highlighting key milestones that have shaped this technology into what it is today. Additionally, we will examine the **Key Components of CNC Systems**, detailing the critical elements that make these machines so effective. By understanding these foundational elements, readers will gain a comprehensive insight into the world of CNC technology, enabling them to appreciate its capabilities and applications in various industries. This journey through the basics, history, and components will ultimately lead to a deeper **Understanding of CNC Technology**.
Definition and Basics of CNC
**Definition and Basics of CNC** Computer Numerical Control (CNC) technology is a cornerstone of modern manufacturing, revolutionizing the way parts and products are designed, prototyped, and produced. At its core, CNC involves the use of computer systems to control machine tools and related machinery. This integration of computers with mechanical devices enables precise and repetitive tasks to be performed with minimal human intervention, significantly enhancing accuracy, efficiency, and productivity. The basic components of a CNC system include the machine tool itself (such as milling machines, lathes, or grinders), a controller or computer that interprets and executes the instructions, and software that generates the necessary code. The process begins with Computer-Aided Design (CAD) software, where designers create detailed digital models of the parts to be manufactured. These designs are then translated into Computer-Aided Manufacturing (CAM) software, which generates the specific instructions or G-code that the CNC machine will follow. Once the G-code is loaded into the CNC controller, the machine executes the commands with precision, moving cutting tools or other components according to the programmed sequence. This automation allows for complex geometries and intricate designs to be produced consistently and accurately, making CNC indispensable in industries ranging from aerospace and automotive to medical devices and consumer electronics. Key benefits of CNC technology include reduced setup times, improved part quality, and increased throughput. By minimizing manual labor, CNC machines also reduce the risk of human error, ensuring that each part meets stringent quality standards. Additionally, CNC systems can operate around the clock without breaks, further boosting production capacity. In summary, CNC technology represents a symbiotic relationship between advanced computing and traditional machining techniques. By leveraging computer-controlled precision and automation, manufacturers can achieve higher levels of efficiency, accuracy, and innovation in their production processes. Understanding the basics of CNC is essential for anyone looking to grasp the full potential of modern manufacturing and its role in shaping the future of industry.
History and Evolution of CNC
The history and evolution of Computer Numerical Control (CNC) technology is a fascinating narrative that spans several decades, marked by significant advancements in precision, efficiency, and automation. The journey began in the 1940s when the U.S. Air Force commissioned a project to develop automated machining tools for the production of complex aircraft parts. This initiative led to the creation of the first Numerical Control (NC) machines by John T. Parsons and Frank L. Stulen, who used punched cards to control machine tools. These early NC machines were cumbersome and prone to errors but laid the groundwork for future innovations. In the 1950s and 1960s, NC technology evolved with the introduction of magnetic tapes and then digital computers, which significantly improved accuracy and reliability. The term "Computer Numerical Control" emerged as computers became integral to the control process. This period saw the development of the first CNC machines by companies like General Electric and IBM, which integrated computer systems directly into machine tools. The 1970s and 1980s witnessed a revolution in CNC technology with the advent of microprocessors and personal computers. These advancements enabled more sophisticated control systems, better user interfaces, and greater flexibility in programming. The introduction of CAD/CAM (Computer-Aided Design/Computer-Aided Manufacturing) software further streamlined the design-to-manufacturing process, allowing for seamless integration between design stages and production. In the 1990s and 2000s, CNC technology continued to advance with improvements in hardware and software. High-speed machining capabilities, advanced servo motors, and better cooling systems enhanced performance and precision. The widespread adoption of Ethernet and other networking technologies enabled real-time monitoring and remote control of CNC machines, fostering greater efficiency and productivity. Today, CNC technology is at the forefront of Industry 4.0, with advancements in artificial intelligence, machine learning, and the Internet of Things (IoT). Modern CNC machines are equipped with sophisticated sensors, predictive maintenance capabilities, and advanced analytics tools that optimize production processes. The integration of robotics and automation has also expanded CNC's role beyond traditional machining to include tasks such as assembly, inspection, and material handling. Throughout its evolution, CNC technology has transformed manufacturing by offering unparalleled precision, speed, and flexibility. From its humble beginnings with punched cards to the current era of smart factories and Industry 4.0, CNC has played a pivotal role in shaping modern manufacturing practices. Understanding this history provides a deeper appreciation for the capabilities and potential of CNC technology in contemporary industrial settings.
Key Components of CNC Systems
**Key Components of CNC Systems** At the heart of Computer Numerical Control (CNC) technology lies a sophisticated interplay of several key components, each playing a crucial role in transforming digital instructions into precise physical actions. The core of any CNC system is the **Control Unit**, which serves as the brain of the operation. This unit interprets and executes the programmed instructions, often in the form of G-code or M-code, to guide the machine's movements. The control unit is typically a computer or specialized controller that manages data input, processing, and output. **Sensors and Feedback Systems** are another vital component, providing real-time data on the machine's status and performance. These sensors monitor parameters such as position, speed, and temperature, ensuring that the machine operates within specified tolerances and maintains optimal conditions. This feedback loop allows for continuous adjustments and corrections, enhancing accuracy and reliability. The **Drive System**, comprising motors and drives, converts the digital commands from the control unit into mechanical movements. This includes servo motors, stepper motors, and spindle motors that power the machine's axes (X, Y, Z, etc.) and other functional components like tool changers and coolant systems. The drive system's precision and power directly influence the machine's ability to execute complex tasks with high accuracy. **Machine Axes** are the physical components that move according to the instructions from the control unit. These axes can be linear (moving in straight lines) or rotary (moving in circular motions), enabling a wide range of motions necessary for various machining operations such as cutting, drilling, and milling. The number and configuration of these axes determine the machine's versatility and capability. **Human-Machine Interface (HMI)** is essential for user interaction with the CNC system. This interface allows operators to input programs, monitor operations, and adjust parameters in real-time. Modern HMIs often feature intuitive touchscreens or graphical displays that simplify the operation process and reduce the learning curve for new users. **Software** plays a pivotal role in CNC systems, encompassing both the operating system of the control unit and specialized CAD/CAM software used for designing and programming parts. This software enables users to create complex designs, simulate machining processes, and generate optimized G-code for efficient production. Finally, **Safety Features** are integrated into CNC systems to protect both the machine and the operator. These include features like emergency stops, interlocks, and protective enclosures that prevent accidents and ensure a safe working environment. Together, these components form a cohesive system that leverages advanced technology to achieve unparalleled precision and efficiency in manufacturing processes. Understanding these key components is crucial for appreciating the full potential of CNC technology and its transformative impact on modern industry.
Applications and Uses of CNC
In the realm of modern manufacturing and creative endeavors, Computer Numerical Control (CNC) technology has emerged as a transformative force, revolutionizing how we design, produce, and innovate. CNC machines, with their precision and versatility, have become indispensable tools across various sectors. This article delves into the multifaceted applications and uses of CNC technology, exploring its significant impact on manufacturing and industrial processes, its creative and hobbyist uses, and its role in driving advancements in modern industries. From enhancing efficiency and accuracy in large-scale production to enabling intricate craftsmanship in hobbyist projects, CNC technology has redefined the boundaries of what is possible. By understanding the diverse applications of CNC, we can better appreciate its potential to shape the future of manufacturing, creativity, and innovation. As we delve into these topics, we will transition seamlessly into a deeper understanding of CNC technology itself, uncovering its underlying principles and capabilities that make it such a powerful tool in today's world.
Manufacturing and Industrial Applications
In the realm of manufacturing and industrial applications, Computer Numerical Control (CNC) technology plays a pivotal role in enhancing precision, efficiency, and productivity. CNC machines, which operate under computer control, are integral to various sectors including aerospace, automotive, medical devices, and consumer goods. These machines enable the precise cutting, drilling, and shaping of materials such as metals, plastics, and composites with unparalleled accuracy and speed. One of the most significant advantages of CNC in manufacturing is its ability to automate complex processes. This automation reduces human error and allows for continuous operation without breaks, significantly increasing production rates. For instance, in the automotive industry, CNC machines are used to manufacture engine components, gearboxes, and other critical parts with high precision. Similarly, in aerospace engineering, CNC machining is essential for producing intricate components such as aircraft parts and satellite components that require stringent tolerances. CNC technology also supports the production of custom and complex designs that would be challenging or impossible to achieve with traditional machining methods. This capability is particularly valuable in industries like medical devices where custom implants and surgical instruments are often required. Additionally, CNC machines can handle a wide range of materials, from soft plastics to hard metals, making them versatile tools across different manufacturing environments. The integration of CNC with other technologies such as 3D printing and robotics further amplifies its impact. For example, combining CNC machining with additive manufacturing allows for the creation of hybrid parts that leverage the strengths of both processes—complex geometries from 3D printing and precise finishing from CNC machining. This synergy opens up new possibilities for innovative product design and development. Moreover, advancements in CNC software have made these systems more user-friendly and accessible. Modern CNC systems often come with intuitive interfaces that simplify programming and operation, reducing the learning curve for operators. This ease of use has democratized access to CNC technology, enabling smaller manufacturers and startups to adopt these systems and compete effectively in the global market. In summary, CNC technology is a cornerstone of modern manufacturing and industrial applications. Its ability to automate complex processes, achieve high precision, and support custom designs makes it indispensable across various industries. As technology continues to evolve, the role of CNC in driving innovation and efficiency will only continue to grow.
Creative and Hobbyist Uses
**Creative and Hobbyist Uses** Beyond its industrial applications, CNC technology has revolutionized the creative and hobbyist communities, offering unparalleled precision and versatility. For artists, designers, and makers, CNC machines serve as powerful tools that bridge the gap between imagination and reality. Woodworkers can craft intricate furniture pieces with flawless accuracy, while metalworkers can fabricate complex components with ease. The ability to work with a wide range of materials—from wood and metal to plastic and even stone—opens up endless possibilities for creative expression. In the realm of 3D carving, CNC routers allow hobbyists to transform raw materials into detailed sculptures, custom signs, and decorative items. This technology is particularly popular among woodturners who can create intricate designs on wooden objects such as bowls, pens, and other decorative items. Additionally, CNC laser cutters enable precise cutting of materials like paper, fabric, and acrylics, making them ideal for crafting custom jewelry, model kits, and other delicate projects. For DIY enthusiasts and makerspaces, CNC machines offer a platform for prototyping and innovation. They can be used to fabricate custom parts for robotics projects or to create prototypes for new product ideas. The precision of CNC machining also makes it an essential tool in model making and miniature crafting communities where small details are crucial. Moreover, educational institutions are increasingly incorporating CNC technology into their curricula to teach students about design, engineering, and manufacturing processes. This hands-on learning experience not only enhances technical skills but also fosters creativity and problem-solving abilities. The accessibility of CNC technology has been further enhanced by the development of affordable hobbyist-grade machines and user-friendly software. Platforms like Fusion 360 and SketchUp provide intuitive interfaces that allow beginners to design complex projects without extensive prior knowledge. Online communities and forums dedicated to CNC enthusiasts offer valuable resources, tutorials, and project ideas that help newcomers get started. In summary, the creative and hobbyist uses of CNC technology are as diverse as they are innovative. By providing precision, flexibility, and accessibility, these machines have democratized advanced manufacturing techniques, empowering individuals to bring their most imaginative projects to life with unprecedented ease and accuracy. Whether you're an artist looking to push the boundaries of your craft or a DIY enthusiast seeking new challenges, CNC technology offers a world of creative possibilities waiting to be explored.
Advancements in Modern Industries
Advancements in modern industries have been significantly driven by the integration of Computer Numerical Control (CNC) technology, transforming the manufacturing landscape with unprecedented precision, efficiency, and versatility. CNC machines, which operate under computer control, have revolutionized various sectors by enabling the production of complex parts with high accuracy and minimal human intervention. In the aerospace industry, for instance, CNC machining allows for the creation of intricate components such as engine parts and aircraft structures that require strict tolerances and precision. Similarly, in the automotive sector, CNC technology is crucial for producing high-performance engine components, gearboxes, and other critical parts that demand exacting standards. The medical industry also benefits greatly from CNC advancements. Custom implants, surgical instruments, and medical devices are fabricated with precision using CNC machines, ensuring patient safety and efficacy. Additionally, the electronics industry relies on CNC for the production of intricate circuit boards and components, facilitating the development of compact and sophisticated electronic devices. The use of CNC in these industries not only enhances product quality but also reduces production time and costs, making it a cornerstone of modern manufacturing. Moreover, advancements in CNC have led to the development of advanced materials processing techniques. For example, CNC laser cutting and milling enable the precise shaping of metals, plastics, and composites, which is essential for industries such as aerospace and automotive where lightweight yet strong materials are critical. The integration of artificial intelligence (AI) and machine learning (ML) with CNC systems further enhances their capabilities by optimizing production processes, predicting maintenance needs, and improving overall system reliability. In the realm of additive manufacturing, CNC technology plays a pivotal role in 3D printing processes. By combining traditional CNC machining with additive techniques, manufacturers can create complex geometries that were previously impossible to produce. This hybrid approach allows for the rapid prototyping and production of customized parts, significantly shortening the product development cycle. Overall, the advancements in CNC technology have been instrumental in driving innovation across various modern industries. By offering unparalleled precision, speed, and adaptability, CNC machines continue to redefine manufacturing processes, enabling the creation of sophisticated products that meet stringent quality standards. As technology continues to evolve, the role of CNC in shaping the future of industry will only become more pronounced, underscoring its importance as a foundational element of modern manufacturing.
Benefits and Future of CNC
The advent of Computer Numerical Control (CNC) technology has revolutionized the manufacturing industry, offering unparalleled precision, efficiency, and sustainability. At the heart of modern production, CNC machines have transformed the way goods are designed, produced, and delivered. This article delves into the multifaceted benefits and future prospects of CNC technology, exploring three key areas: **Increased Precision and Efficiency**, **Economic and Environmental Impact**, and **Future Trends and Innovations**. By understanding how CNC enhances production processes, reduces costs, and minimizes environmental footprint, we can appreciate its transformative role in industry. Moreover, examining the cutting-edge developments and emerging trends in CNC technology provides a glimpse into a future where manufacturing becomes even more streamlined, sustainable, and innovative. As we navigate the complexities of modern production, it is crucial to grasp the fundamentals of CNC technology to fully leverage its potential. Therefore, this article aims to guide readers through the intricacies of CNC, transitioning seamlessly into a deeper **Understanding of CNC Technology**.
Increased Precision and Efficiency
The integration of Computer Numerical Control (CNC) technology has revolutionized manufacturing by significantly enhancing precision and efficiency. At the heart of CNC systems lies sophisticated software and hardware that enable machines to execute complex tasks with unparalleled accuracy. Unlike traditional manual methods, CNC machines operate based on precise digital instructions, eliminating human error and ensuring consistent results. This heightened precision is particularly crucial in industries such as aerospace, automotive, and medical device manufacturing, where even the slightest deviation can have critical consequences. Efficiency is another key benefit of CNC technology. These machines can operate continuously without breaks, reducing downtime and increasing overall productivity. Automated processes allow for faster production cycles, enabling businesses to meet high demand without compromising on quality. Additionally, CNC machines can perform multiple operations simultaneously, such as cutting, drilling, and milling, further streamlining the manufacturing process. This multifunctionality not only saves time but also reduces the need for multiple specialized machines, thereby optimizing factory space and resource allocation. Moreover, CNC technology facilitates rapid prototyping and design changes. With the ability to easily modify digital designs and upload new instructions to the machine, manufacturers can quickly adapt to changing market demands or design improvements. This agility is invaluable in today's fast-paced industrial landscape where innovation and adaptability are key to staying competitive. In terms of future advancements, the integration of artificial intelligence (AI) and machine learning (ML) with CNC systems promises even greater precision and efficiency. AI can analyze production data to predict maintenance needs, optimize cutting paths for reduced material waste, and improve overall system performance. Furthermore, advancements in robotics and IoT (Internet of Things) will enable more seamless communication between different components of the manufacturing process, creating a more interconnected and efficient production environment. As industries continue to evolve, the role of CNC technology will become increasingly pivotal. Its ability to deliver high-precision products at accelerated speeds will be essential for meeting the demands of a rapidly changing world. Whether it's producing intricate components for cutting-edge electronics or fabricating large-scale structures for infrastructure projects, CNC machines will remain at the forefront of manufacturing innovation, driving progress and efficiency in every sector they touch.
Economic and Environmental Impact
The integration of Computer Numerical Control (CNC) technology into various industries has profound economic and environmental impacts, underscoring its pivotal role in the future of manufacturing. Economically, CNC machines enhance productivity by automating complex processes, reducing labor costs, and increasing precision. This automation leads to higher quality products with minimal human error, thereby boosting customer satisfaction and loyalty. Additionally, the efficiency of CNC systems allows for faster production cycles, enabling businesses to meet demand more effectively and expand their market reach. This scalability can drive economic growth by creating new job opportunities in fields such as CNC programming, maintenance, and operation. From an environmental perspective, CNC technology contributes significantly to sustainability. By optimizing material usage through precise cutting and shaping, CNC machines minimize waste generation. This reduction in waste not only conserves raw materials but also decreases the environmental footprint associated with material extraction and processing. Furthermore, the precision of CNC operations reduces the need for rework and scrap, which in turn lowers energy consumption and greenhouse gas emissions. The use of advanced materials and coatings in CNC manufacturing also enhances product durability, extending product lifetimes and reducing the frequency of replacements—another key factor in reducing overall environmental impact. Moreover, the data-driven nature of CNC systems allows for real-time monitoring and optimization of energy consumption. Modern CNC machines are designed with energy efficiency in mind, incorporating features such as power-saving modes during idle times and optimized tool paths that minimize energy expenditure. This focus on energy efficiency aligns with global efforts to reduce carbon emissions and transition towards more sustainable industrial practices. In the future, the economic and environmental benefits of CNC technology are expected to expand further. Advances in artificial intelligence (AI) and machine learning (ML) will enable even greater automation and optimization of manufacturing processes. Predictive maintenance capabilities will reduce downtime, ensuring that machines operate at peak efficiency while minimizing the environmental impact of repairs and replacements. As industries continue to adopt more sustainable practices, the role of CNC technology in driving both economic prosperity and environmental stewardship will become increasingly critical. In summary, the economic and environmental impacts of CNC technology are multifaceted and far-reaching. By enhancing productivity, reducing waste, optimizing energy use, and supporting sustainable practices, CNC machines play a crucial role in shaping a more efficient and environmentally conscious future for manufacturing. As technology continues to evolve, the benefits of CNC will only become more pronounced, making it an indispensable tool for industries aiming to balance economic growth with environmental responsibility.
Future Trends and Innovations
As we delve into the future trends and innovations in CNC (Computer Numerical Control) technology, it becomes clear that this field is on the cusp of a transformative era. One of the most significant trends is the integration of Industry 4.0 principles, which involves leveraging advanced technologies such as artificial intelligence (AI), machine learning (ML), and the Internet of Things (IoT). These technologies enable real-time monitoring, predictive maintenance, and autonomous decision-making, thereby enhancing efficiency and reducing downtime. For instance, AI-powered algorithms can analyze data from sensors to predict when a machine might fail, allowing for proactive maintenance and minimizing production interruptions. Another key innovation is the adoption of cloud-based CNC systems. Cloud computing allows for greater flexibility and scalability, enabling manufacturers to access and control their CNC machines remotely. This not only facilitates global collaboration but also provides real-time updates and analytics, which can be crucial for optimizing production processes. Additionally, cloud-based systems can integrate with other smart factory technologies, creating a seamless and highly efficient manufacturing environment. The rise of additive manufacturing (3D printing) is also set to revolutionize the CNC landscape. By combining traditional CNC machining with additive techniques, manufacturers can produce complex geometries and hybrid parts that were previously impossible to create. This fusion of technologies opens up new possibilities for industries such as aerospace, automotive, and healthcare, where customized and intricate components are increasingly in demand. Furthermore, advancements in robotics and automation are expected to play a pivotal role in future CNC trends. Collaborative robots (cobots) are being integrated into CNC workflows to handle tasks that require precision and dexterity, such as assembly and inspection. These cobots can work alongside human operators, enhancing productivity while ensuring safety and accuracy. Sustainability is another critical area where CNC technology is evolving. With growing environmental concerns, manufacturers are turning to CNC solutions that offer energy efficiency and reduced material waste. For example, advanced CNC software can optimize cutting paths to minimize material usage, while energy-efficient motors and drives reduce the overall carbon footprint of manufacturing operations. In conclusion, the future of CNC technology is marked by a convergence of cutting-edge innovations that promise to transform the manufacturing sector. From AI-driven predictive maintenance to cloud-based control systems, additive manufacturing, robotic integration, and sustainable practices, these trends collectively point towards a more efficient, adaptable, and environmentally conscious industrial landscape. As these technologies continue to evolve, they will undoubtedly drive significant benefits for industries relying on CNC machinery, ensuring higher productivity, better product quality, and a competitive edge in the global market.