What Is Shear Stress

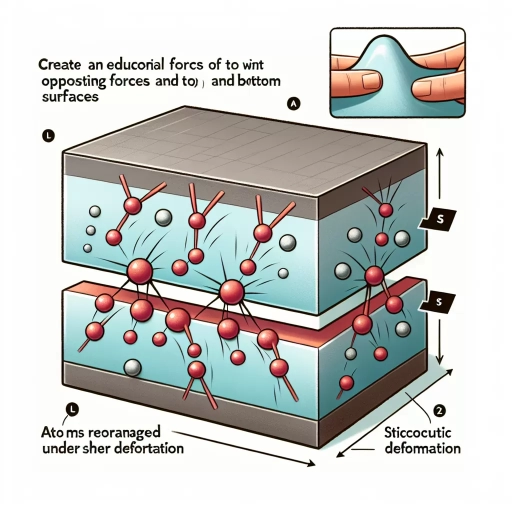
Shear stress is a fundamental concept in mechanics and engineering, playing a crucial role in understanding the behavior of materials under various types of loading. It is the force that causes a material to deform by sliding along a plane parallel to the direction of the force. This phenomenon is essential in numerous fields, including civil engineering, mechanical engineering, and materials science. In this article, we will delve into the intricacies of shear stress, starting with **Understanding Shear Stress Fundamentals**, where we will explore the basic principles and definitions that underpin this concept. We will then examine **Applications and Examples of Shear Stress**, highlighting how it manifests in real-world scenarios such as bridge construction, pipeline design, and soil mechanics. Finally, we will discuss **Calculating and Analyzing Shear Stress**, providing insights into the mathematical models and techniques used to predict and analyze shear stress in different contexts. By grasping these aspects, readers will gain a comprehensive understanding of shear stress and its significance in engineering practices. Let us begin by laying the groundwork with **Understanding Shear Stress Fundamentals**.
Understanding Shear Stress Fundamentals
Understanding shear stress is crucial for engineers, researchers, and anyone involved in the design and analysis of structures and materials. Shear stress, a fundamental concept in mechanics, arises when forces act parallel to a surface, causing deformation. To grasp this complex phenomenon, it is essential to delve into its definition and basic concepts, explore the various types of shear stress, and consider the key factors that influence its magnitude. In this article, we will first define shear stress and discuss its basic concepts, laying the groundwork for a deeper understanding. We will then examine the different types of shear stress, including pure shear, simple shear, and torsional shear, each with its unique characteristics and applications. Finally, we will analyze the key factors influencing shear stress, such as material properties, geometric configurations, and loading conditions. By understanding these aspects, readers will gain a comprehensive insight into how shear stress affects various systems and structures. Let us begin by exploring the definition and basic concepts of shear stress, which form the foundation of this critical mechanical principle.
Definition and Basic Concepts
Shear stress, a fundamental concept in mechanics and engineering, is the force that causes a material to deform by sliding along a plane parallel to the direction of the force. This type of stress is distinct from other forms of stress such as tensile and compressive stress, which act perpendicular to the surface of the material. To understand shear stress, it is crucial to grasp its definition and basic concepts. **Definition and Basic Concepts:** Shear stress (\(\tau\)) is defined as the ratio of the shear force (\(F\)) to the area (\(A\)) over which it is applied. Mathematically, this can be expressed as \(\tau = \frac{F}{A}\). The unit of shear stress is typically measured in pascals (Pa) or pounds per square inch (psi). When a material is subjected to shear stress, it undergoes shear strain, which is the resulting deformation. The relationship between shear stress and shear strain is often described by the shear modulus (\(G\)), a material property that quantifies the material's resistance to shear deformation. In practical terms, imagine a deck of cards being pushed sideways; each card slides over the one below it due to the applied force. This sliding action is analogous to how materials behave under shear stress. The magnitude of shear stress depends on both the force applied and the area over which it acts. For instance, if you apply a constant force but increase the area, the shear stress decreases, and vice versa. Understanding shear stress is critical in various engineering disciplines, including civil engineering, mechanical engineering, and materials science. In civil engineering, for example, shear stress plays a key role in designing beams and bridges where loads can cause significant shear forces. In mechanical engineering, it is essential for analyzing the performance of gears, shafts, and other components that are subject to rotational forces. Moreover, the behavior of materials under shear stress can vary significantly depending on their properties. Some materials like metals exhibit elastic behavior up to a certain limit before deforming plastically or failing. Others, such as polymers or composites, may exhibit more complex behaviors due to their internal structure and bonding mechanisms. In summary, shear stress is a critical force that causes materials to deform through sliding actions. Its understanding is rooted in its definition as the ratio of shear force to area and its relationship with material properties like shear modulus. Recognizing how different materials respond to shear stress is vital for designing safe and efficient structures across various engineering fields. By grasping these fundamentals, engineers can better predict material behavior under different loading conditions, ensuring the integrity and longevity of their designs.
Types of Shear Stress
Shear stress, a fundamental concept in mechanics and engineering, is the force that causes a material to deform by sliding along a plane parallel to the direction of the force. Understanding the various types of shear stress is crucial for designing and analyzing structures, materials, and systems. There are several key types of shear stress that engineers and scientists encounter. **1. Pure Shear Stress:** This occurs when equal and opposite forces are applied tangentially to opposite faces of a material, causing it to deform without any normal stress. Pure shear is often seen in torsion tests where a cylindrical specimen is twisted. **2. Simple Shear Stress:** This type involves a single set of parallel forces acting on opposite faces of a material, resulting in a deformation where one face slides over the other. Simple shear is commonly observed in beam bending and in the deformation of rectangular blocks under lateral loads. **3. Torsional Shear Stress:** Torsional shear occurs when a twisting force (torque) is applied to an object, such as a rod or shaft, causing it to rotate around its longitudinal axis. This type of stress is critical in the design of axles, drive shafts, and other rotating components. **4. Bending Shear Stress:** In bending scenarios, shear stress arises due to the variation in normal stress across the cross-section of a beam. The maximum shear stress in bending typically occurs at the neutral axis where the normal stress is zero. This is particularly important for beams subjected to transverse loads. **5. Compressive Shear Stress:** Although compression primarily involves normal forces, certain conditions can induce shear stresses within compressed materials. For instance, in rock mechanics, compressive forces can lead to shear failure along planes of weakness within the rock. **6. Impact Shear Stress:** This type occurs during sudden impacts or dynamic loading conditions where high forces are applied over very short durations. Impact shear can lead to rapid material failure and is a concern in crash testing and impact-resistant design. Understanding these different types of shear stress allows engineers to predict material behavior under various loading conditions, ensuring the structural integrity and safety of their designs. By recognizing how different types of shear stress interact with materials, engineers can optimize their designs for strength, durability, and performance. This knowledge is essential across a wide range of fields including civil engineering, mechanical engineering, aerospace engineering, and materials science. In summary, recognizing and analyzing the various types of shear stress is fundamental to understanding how materials respond to different loading scenarios. Each type has its unique characteristics and implications for design and analysis, making it imperative for engineers to be well-versed in these concepts to ensure the reliability and efficiency of their work.
Key Factors Influencing Shear Stress
Shear stress, a critical component in understanding the behavior of materials under various loads, is influenced by several key factors that collectively determine its magnitude and impact. **Material Properties** are paramount; the inherent characteristics such as elasticity, viscosity, and shear modulus of a material dictate how it responds to shear forces. For instance, materials with high shear modulus resist deformation more effectively than those with lower values. **Geometry** also plays a significant role; the shape and dimensions of an object can significantly affect the distribution of shear stress. In beams, for example, the cross-sectional area and the distance from the neutral axis influence the shear stress experienced by different parts of the beam. **Loading Conditions** are another crucial factor. The type, magnitude, and direction of applied loads can vary widely, leading to different shear stress profiles. Torsional loads, bending loads, and direct shear loads each produce distinct patterns of shear stress within a material. Additionally, **Boundary Conditions** must be considered; how a material is constrained or supported can alter the distribution of shear stress. For example, a beam fixed at both ends will experience different shear stresses compared to one that is simply supported. **Temperature** can also influence shear stress by altering material properties. Many materials exhibit changes in their mechanical properties with temperature variations, which in turn affect their resistance to shear. Furthermore, **Rate of Loading** is important; dynamic loading conditions can lead to different shear stress responses compared to static loading due to the material's viscoelastic behavior. In engineering applications, understanding these factors is essential for designing structures that can withstand various types of loading without failure. For instance, in civil engineering, bridges must be designed to handle both static loads from the structure itself and dynamic loads from traffic, ensuring that the shear stresses do not exceed the material's capacity. Similarly, in mechanical engineering, gears and shafts are designed with careful consideration of torsional shear stresses to prevent failure under operational conditions. In summary, shear stress is a multifaceted phenomenon influenced by a combination of material properties, geometry, loading conditions, boundary conditions, temperature, and rate of loading. Understanding these key factors is fundamental to predicting and managing shear stress in various engineering contexts, ensuring the safety and reliability of structures and components. By analyzing these influences comprehensively, engineers can design more resilient and efficient systems that meet the demands of real-world applications.
Applications and Examples of Shear Stress
Shear stress, a fundamental concept in physics and engineering, plays a crucial role in various fields, each with its unique applications and examples. This article delves into the multifaceted nature of shear stress, exploring its significance in engineering and structural analysis, fluid dynamics and flow, and biomechanics and medical applications. In engineering and structural analysis, shear stress is essential for designing buildings, bridges, and other infrastructure to ensure they can withstand external forces without failing. It helps engineers determine the strength and stability of materials under different loads. In fluid dynamics and flow, shear stress influences the behavior of fluids in motion, affecting viscosity, turbulence, and boundary layers. This understanding is vital for designing efficient pipelines, turbines, and other fluid-handling systems. Lastly, in biomechanics and medical applications, shear stress impacts the health of tissues and cells, particularly in blood flow and joint mechanics. By understanding these different facets of shear stress, we can develop more robust structures, optimize fluid systems, and improve medical treatments. This article will first examine the critical role of shear stress in engineering and structural analysis, highlighting its importance in ensuring the integrity of our built environment.
Engineering and Structural Analysis
Engineering and structural analysis are pivotal disciplines that underpin the design, construction, and maintenance of various structures, from bridges and skyscrapers to aircraft and medical devices. At the heart of these disciplines lies the understanding of shear stress, a critical force that can lead to deformation or failure if not properly managed. Shear stress occurs when forces act parallel to each other but in opposite directions, causing a material to deform by sliding along a plane. In engineering, this concept is crucial for ensuring the integrity and safety of structures. For instance, in civil engineering, shear stress is a key factor in designing beams and columns. Engineers must calculate the shear forces that these structural elements will encounter due to loads such as weight, wind, or seismic activity. This involves analyzing the cross-sectional area of the beam, the material's shear strength, and the distribution of loads to ensure that the structure can withstand these forces without failing. In bridge construction, for example, engineers use shear stress analysis to determine the optimal dimensions and materials for piers and abutments, ensuring that they can resist the lateral forces imposed by traffic and environmental conditions. In mechanical engineering, shear stress plays a vital role in the design of gears, shafts, and other rotating components. Here, engineers need to consider both static and dynamic shear stresses to prevent wear and tear or catastrophic failure. For example, in gear design, shear stress analysis helps in determining the tooth geometry and material selection to handle the high shear forces generated during gear engagement. Similarly, in aerospace engineering, understanding shear stress is essential for designing aircraft wings and fuselage components that must withstand extreme aerodynamic forces. Structural analysis also extends to biomedical engineering where shear stress affects the design of medical implants such as hip replacements and dental implants. Here, engineers must consider how shear forces will impact the interface between the implant and surrounding bone tissue to ensure proper integration and longevity of the implant. Additionally, in fluid dynamics within biomedical contexts, shear stress is critical in understanding blood flow through arteries and veins, helping researchers develop better models for cardiovascular diseases. In materials science, understanding shear stress is fundamental for developing new materials with enhanced properties. Researchers use shear stress tests to evaluate the mechanical behavior of materials under various loading conditions. This information is crucial for selecting appropriate materials for specific applications where high shear resistance is required. Moreover, computational tools such as finite element analysis (FEA) have revolutionized the field of structural analysis by allowing engineers to simulate complex loading scenarios and predict how structures will behave under different conditions. These simulations enable detailed examination of shear stresses across entire structures, facilitating more accurate designs and reducing the risk of failure. In conclusion, engineering and structural analysis are deeply intertwined with the concept of shear stress. By comprehensively understanding and applying principles related to shear stress, engineers can create safer, more efficient, and durable structures across a wide range of industries. Whether it's designing critical infrastructure or developing life-saving medical devices, the meticulous analysis of shear stress remains an indispensable tool in modern engineering practices.
Fluid Dynamics and Flow
Fluid dynamics, the study of the behavior of fluids under various forces and conditions, is a fundamental discipline that underpins many engineering and scientific applications. At its core, fluid dynamics involves understanding how fluids (liquids and gases) flow, interact with surfaces, and respond to external forces. One critical aspect of fluid dynamics is the concept of shear stress, which arises from the frictional forces within a fluid or between a fluid and a solid boundary. Shear stress plays a pivotal role in determining the flow characteristics of fluids and has numerous practical applications across various fields. In engineering, shear stress is crucial for designing pipelines, pumps, and turbines. For instance, in pipeline design, engineers must consider the shear stress exerted by flowing fluids to ensure that the pipe material can withstand the forces without failing. Similarly, in the design of turbines and pumps, understanding shear stress helps in optimizing blade shapes and angles to maximize efficiency and minimize wear. In civil engineering, shear stress is essential for river dynamics and coastal engineering; it helps predict erosion patterns, sediment transport, and the stability of riverbanks and coastal structures. In biomedical engineering, shear stress is vital for understanding blood flow dynamics. The endothelial cells lining blood vessels respond to shear stress by regulating vascular tone and influencing atherosclerosis development. This knowledge is critical for developing medical devices such as stents and vascular grafts that must withstand the shear forces exerted by blood flow. Additionally, in pharmaceutical applications, shear stress affects the mixing and blending processes in reactors, impacting the quality and consistency of pharmaceutical products. Aerodynamics, a subset of fluid dynamics focused on air and gas flows, heavily relies on shear stress analysis. In aircraft design, understanding shear stress helps engineers optimize wing shapes to reduce drag while maintaining lift. The boundary layer theory, which describes how air flows over surfaces, is fundamentally based on shear stress principles. This theory is indispensable for designing more efficient aircraft and wind turbines. Environmental science also benefits significantly from fluid dynamics and shear stress analysis. For example, ocean currents and tidal flows are influenced by shear stresses that arise from wind friction, gravitational forces, and bottom topography. Understanding these dynamics is crucial for predicting ocean circulation patterns, which in turn affect climate models, marine ecosystems, and coastal management strategies. In industrial processes, fluid dynamics and shear stress are key factors in mixing operations. Chemical reactors rely on efficient mixing to ensure uniform reaction conditions, and shear stress plays a critical role in achieving this uniformity. Similarly, in food processing, understanding shear stress helps in designing equipment that can handle viscous fluids without causing damage or altering their properties. In conclusion, fluid dynamics and the associated concept of shear stress are foundational to a wide range of applications across engineering, biomedical sciences, environmental studies, and industrial processes. By understanding how fluids flow and interact with surfaces under various conditions, scientists and engineers can develop more efficient systems, predict natural phenomena accurately, and improve product quality. The study of fluid dynamics continues to evolve with advancements in computational methods and experimental techniques, further expanding its impact on modern technology and society.
Biomechanics and Medical Applications
Biomechanics, the intersection of biology and mechanics, plays a crucial role in understanding the mechanical properties and behaviors of living tissues and systems. This field has profound implications for medical applications, where the analysis of shear stress is particularly significant. Shear stress, a force that causes deformation by sliding along a plane parallel to the direction of the force, is pivotal in various medical contexts. In orthopedics, for instance, shear stress is a critical factor in understanding bone fractures and the stability of implants. When bones are subjected to shear forces, they can fracture or become unstable, leading to conditions such as osteoporotic fractures or implant loosening. Biomechanical studies help in designing more robust implants and surgical techniques that minimize shear stress on bones, thereby enhancing patient outcomes. For example, hip replacement surgeries involve careful consideration of shear stress to ensure the longevity and stability of the prosthetic joint. In cardiovascular medicine, shear stress is essential for understanding blood flow dynamics and vascular health. The endothelial cells lining blood vessels respond to shear stress by regulating vascular tone and remodeling the vessel wall. Abnormal shear stress patterns can lead to atherosclerosis, a condition where plaque builds up in arteries, increasing the risk of heart attacks and strokes. Biomechanical models help in predicting these patterns and guiding interventions such as stenting or bypass surgeries to restore normal blood flow. In soft tissue engineering, shear stress influences the behavior of cells and tissues in tissue-engineered scaffolds. Researchers use biomechanical principles to design scaffolds that mimic the natural mechanical environment of tissues, promoting cell growth and differentiation. For instance, in the development of artificial skin or muscle tissue, controlled application of shear stress can enhance tissue regeneration and functional integration. Moreover, in sports medicine and rehabilitation, understanding shear stress is crucial for preventing injuries and optimizing recovery. Athletes often experience high levels of shear stress during activities like running or jumping, which can lead to injuries such as ligament sprains or muscle strains. Biomechanical analysis helps in developing training programs and protective gear that reduce the impact of shear forces on joints and muscles. Finally, in neurosurgery, shear stress is relevant in the context of brain injuries and neurodegenerative diseases. Traumatic brain injuries often involve significant shear forces that can cause damage to brain tissue. Biomechanical models are used to simulate these injuries, helping researchers understand the mechanisms of injury and develop more effective treatments. Additionally, conditions like Alzheimer's disease have been linked to abnormal mechanical stresses within the brain, highlighting the need for further biomechanical research. In summary, the application of biomechanics to understand and manage shear stress is vital across a wide range of medical fields. By leveraging insights from biomechanical studies, healthcare professionals can develop more effective treatments, improve patient outcomes, and advance our understanding of human physiology and pathology. Whether it's designing better implants, predicting vascular disease, or optimizing tissue regeneration, the role of shear stress in biomechanics underscores its importance in modern medicine.
Calculating and Analyzing Shear Stress
Calculating and analyzing shear stress is a critical aspect of engineering and materials science, as it directly impacts the structural integrity and performance of various components. To comprehensively understand shear stress, it is essential to delve into three key areas: mathematical formulas and equations, experimental methods for measurement, and software tools for simulation and analysis. Mathematical formulas and equations provide the foundational framework for calculating shear stress, allowing engineers to predict how materials will behave under different loads. These equations, such as the formula for shear stress in beams and the Mohr's circle method, are fundamental in designing safe and efficient structures. Experimental methods for measurement are crucial for validating theoretical calculations and understanding real-world behavior. Techniques like strain gauge measurements and torsion tests provide empirical data that can be compared against theoretical models. Software tools for simulation and analysis offer powerful capabilities to model complex scenarios and predict material behavior under various conditions. These tools enable detailed simulations that can help in optimizing designs and reducing the risk of failure. By combining these approaches, engineers can gain a thorough understanding of shear stress and its implications. Starting with the mathematical formulas and equations, we can establish a solid theoretical basis for our analysis. This foundation is essential for accurately calculating and predicting shear stress in various engineering applications.
Mathematical Formulas and Equations
When delving into the realm of shear stress, a fundamental understanding of mathematical formulas and equations is indispensable. Shear stress, a measure of the force that causes a material to deform by sliding along a plane parallel to the direction of the force, is quantitatively analyzed using several key mathematical constructs. The most basic yet crucial formula for calculating shear stress is \(\tau = \frac{F}{A}\), where \(\tau\) represents the shear stress, \(F\) is the applied force, and \(A\) is the cross-sectional area of the material perpendicular to the force. This formula encapsulates the essence of shear stress as a force per unit area, highlighting its dependence on both the magnitude of the applied force and the geometry of the material. Beyond this foundational equation, more complex scenarios often require the application of Hooke's Law for shear, which states that shear stress (\(\tau\)) is directly proportional to shear strain (\(\gamma\)) within the elastic limit of a material. Mathematically, this relationship is expressed as \(\tau = G \gamma\), where \(G\) is the shear modulus of the material—a measure of its rigidity. This equation underscores the importance of material properties in determining how a substance responds to shear forces. In engineering and structural analysis, the calculation of shear stress often involves more sophisticated formulas that account for various loading conditions and geometric configurations. For instance, in beams subjected to transverse loads, the shear stress distribution can be determined using the formula \(\tau = \frac{V Q}{I b}\), where \(V\) is the shear force, \(Q\) is the first moment of area, \(I\) is the moment of inertia, and \(b\) is the width of the beam. This equation illustrates how shear stress varies across different sections of a beam, emphasizing the need for precise calculations to ensure structural integrity. Furthermore, in materials science and mechanics of materials, understanding the relationship between shear stress and other mechanical properties such as tensile strength and Young's modulus is critical. The Mohr's circle of stress, for example, provides a graphical method to analyze the state of stress at a point within a material, allowing engineers to determine principal stresses and maximum shear stresses. This tool is invaluable in predicting material failure under complex loading conditions. In summary, mathematical formulas and equations form the backbone of shear stress analysis. From simple force-area relationships to more intricate beam theories and material property considerations, these equations enable engineers and scientists to predict and analyze the behavior of materials under various shear loading conditions. By mastering these mathematical tools, professionals can design safer structures, optimize material usage, and ensure the reliability of mechanical systems. Thus, a deep understanding of these formulas is essential for anyone working in fields where shear stress plays a critical role.
Experimental Methods for Measurement
When calculating and analyzing shear stress, experimental methods play a crucial role in obtaining accurate and reliable data. These methods involve the use of various techniques and instruments to measure the shear stress experienced by materials under different conditions. One of the most common experimental methods is the torsion test, where a specimen is subjected to a twisting force, and the resulting deformation is measured. This test is particularly useful for determining the shear modulus and yield strength of materials. Another method is the shear test, which involves applying a force parallel to the surface of the specimen, allowing researchers to directly measure shear stress and strain. For more complex scenarios, such as those involving composite materials or dynamic loading conditions, advanced techniques like digital image correlation (DIC) and strain gauges are employed. DIC uses high-resolution cameras to capture images of the specimen's surface before and after deformation, enabling precise measurement of strain fields. Strain gauges, on the other hand, are attached directly to the specimen and provide real-time data on strain changes as the material undergoes loading. In addition to these direct measurement techniques, indirect methods such as finite element analysis (FEA) can be used in conjunction with experimental data to validate numerical models. FEA involves simulating the behavior of materials under various loads using computational models, which can then be compared with experimental results to ensure accuracy. Furthermore, experimental setups often include sophisticated instrumentation such as load cells and displacement transducers to ensure accurate force and displacement measurements. These instruments are crucial for maintaining the integrity of the data collected during experiments. The choice of experimental method depends on the specific requirements of the study, including the type of material being tested, the nature of the loading conditions, and the desired level of precision. By combining multiple experimental techniques with advanced analytical tools, researchers can gain a comprehensive understanding of shear stress behavior in various materials, which is essential for engineering applications ranging from structural design to material selection. In summary, experimental methods for measuring shear stress are diverse and highly specialized, each offering unique advantages depending on the context of the study. By leveraging these techniques effectively, scientists and engineers can derive valuable insights into material behavior under shear loading, thereby enhancing our ability to design safer and more efficient structures.
Software Tools for Simulation and Analysis
When it comes to calculating and analyzing shear stress, the use of advanced software tools is indispensable. These tools not only streamline the process but also provide precise and reliable results, which are crucial in various engineering disciplines such as mechanical, civil, and aerospace engineering. One of the most widely used software tools for simulation and analysis is Finite Element Analysis (FEA) software. Programs like ANSYS, ABAQUS, and NASTRAN allow engineers to model complex structures and simulate various loading conditions to determine the distribution of shear stress across different components. These simulations can be performed in both static and dynamic conditions, enabling a comprehensive understanding of how materials behave under different types of loads. Another critical tool is Computational Fluid Dynamics (CFD) software, which is particularly useful for analyzing shear stress in fluid dynamics. Tools like OpenFOAM, Fluent, and COMSOL Multiphysics enable the simulation of fluid flow and the calculation of shear stress at the boundary layers, which is essential for designing efficient pipelines, turbines, and other fluid-handling systems. These simulations help engineers optimize designs to minimize shear stress-induced failures and improve overall system performance. In addition to FEA and CFD, specialized software for structural analysis such as ETABS, SAP2000, and STAAD.Pro are also highly effective. These programs allow for detailed modeling of buildings, bridges, and other structures to analyze how shear stress affects their stability and integrity. They often include features for seismic analysis, wind load analysis, and other dynamic loading conditions that can significantly impact shear stress distribution. Moreover, data analysis and visualization tools like MATLAB, Python libraries such as NumPy and SciPy, and graphical interfaces such as Plotly or Matplotlib are essential for interpreting the vast amounts of data generated by these simulations. These tools help engineers to visualize stress distributions, identify critical areas of high shear stress, and make informed decisions based on the analysis. The integration of these software tools into the design process has revolutionized the field of engineering by allowing for more accurate predictions and better design optimization. For instance, in the aerospace industry, these tools are used to simulate the behavior of aircraft components under various flight conditions, ensuring that they can withstand the stresses imposed without failing. Similarly, in civil engineering, they help in designing safer and more durable structures that can resist natural disasters like earthquakes and hurricanes. In conclusion, software tools for simulation and analysis are pivotal in calculating and analyzing shear stress. They offer a robust framework for engineers to model real-world scenarios accurately, predict potential failures, and optimize designs to enhance safety and efficiency. By leveraging these advanced tools, engineers can ensure that their designs meet stringent safety standards while also achieving optimal performance characteristics. This integration of technology with engineering practice has significantly advanced our ability to understand and manage shear stress in various applications.