What Does Exception Mean Dhl

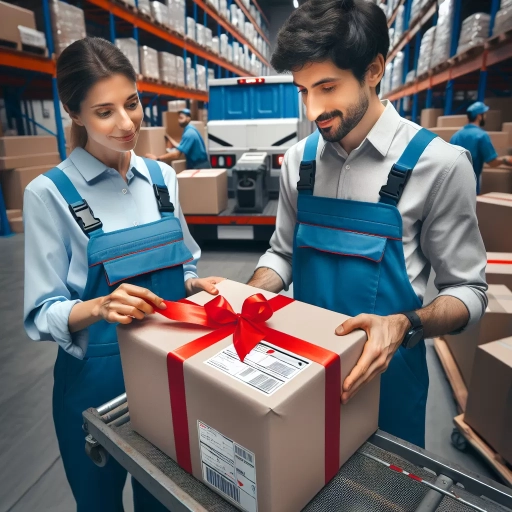
In the logistics industry, particularly within DHL, the term "exception" refers to any deviation from the standard or expected process in the delivery of packages. These exceptions can significantly impact the efficiency and reliability of logistics operations. Understanding what constitutes an exception is crucial for maintaining high service standards. This article delves into the concept of exceptions in DHL, exploring their causes and triggers, and how they are managed and resolved. By examining the underlying reasons behind exceptions, such as operational errors or external factors, we can better comprehend the complexities involved. Additionally, we will discuss the strategies and protocols DHL employs to manage and resolve these exceptions effectively. To begin, it is essential to grasp the fundamental concept of exceptions in DHL operations, which will be the focus of our first section: **Understanding the Concept of Exceptions in DHL**.
Understanding the Concept of Exceptions in DHL
Understanding the concept of exceptions in DHL is crucial for optimizing logistics operations and ensuring smooth delivery processes. This article delves into three key aspects: the definition and context of exceptions, the various types of exceptions that can occur, and the importance of managing these exceptions in logistics. By grasping these elements, logistics professionals can better anticipate, mitigate, and resolve issues that might disrupt the supply chain. The definition and context of exceptions set the foundation for understanding how and why they arise, providing a clear framework for identifying potential problems. Knowing the different types of exceptions helps in developing targeted strategies to address each scenario effectively. Finally, recognizing the importance of exceptions in logistics underscores their impact on operational efficiency, customer satisfaction, and overall business performance. This comprehensive approach ensures that logistics teams are well-equipped to handle any deviations from the norm, thereby enhancing the reliability and effectiveness of DHL's services. Let's begin by exploring the definition and context of exceptions in more detail.
Definition and Context
In the context of logistics and supply chain management, particularly within DHL, the term "exception" refers to any deviation from the planned or expected course of events during the shipment process. This can include a wide range of scenarios such as delays, misrouting, damage to goods, customs clearance issues, or any other unforeseen circumstances that disrupt the normal flow of operations. Understanding exceptions is crucial for maintaining efficiency, ensuring customer satisfaction, and mitigating potential losses. Exceptions can arise due to various factors including weather conditions, traffic congestion, mechanical failures, human error, or regulatory changes. For instance, a shipment might be delayed because of a natural disaster affecting transportation routes or due to incorrect labeling leading to misrouting. Each exception requires prompt attention and resolution to minimize its impact on the overall delivery timeline and quality of service. DHL, as a global logistics provider, has developed sophisticated systems and protocols to identify, manage, and resolve exceptions efficiently. This includes advanced tracking technologies that monitor shipments in real-time, enabling swift detection of any anomalies. Additionally, DHL employs a team of experts who are trained to handle exceptions proactively by communicating with stakeholders, rerouting shipments when necessary, and providing alternative solutions to ensure timely delivery. The context in which exceptions occur is also significant. For example, in peak seasons or during global events that increase demand for logistics services, the likelihood of exceptions may rise due to increased volume and pressure on resources. Similarly, shipments involving perishable goods or high-value items may require more stringent exception management to prevent losses. Effective exception management involves not only resolving immediate issues but also analyzing root causes to prevent future occurrences. This includes reviewing operational processes, enhancing employee training, and investing in technology upgrades. By doing so, DHL can improve its service reliability and maintain its reputation as a dependable logistics partner. In summary, exceptions in DHL are critical events that necessitate immediate attention to ensure smooth operations and customer satisfaction. Understanding these exceptions involves recognizing their causes, implementing effective management strategies, and continuously improving processes to minimize their occurrence. This proactive approach is essential for maintaining high standards in logistics services and upholding DHL's commitment to excellence in delivery.
Types of Exceptions
In the context of DHL and logistics, exceptions refer to any deviation from the standard or expected process in the delivery or handling of shipments. Understanding the types of exceptions is crucial for managing and resolving issues efficiently. Here are the key types: 1. **Address Exceptions**: These occur when there is an issue with the delivery address, such as an incorrect or incomplete address, which can delay or prevent delivery. 2. **Customs Exceptions**: These arise when shipments encounter problems during customs clearance, including missing or incorrect documentation, duties and taxes issues, or prohibited items. 3. **Weather Exceptions**: Inclement weather conditions like storms, floods, or extreme temperatures can disrupt transportation networks and cause delays. 4. **Traffic and Road Conditions Exceptions**: Congestion, road closures, or construction can impede the movement of vehicles carrying shipments. 5. **Operational Exceptions**: These include internal operational issues such as system failures, staffing shortages, or facility closures that affect the handling and delivery of shipments. 6. **Customer-Related Exceptions**: These involve issues with the recipient, such as unavailability to receive the shipment, incorrect contact information, or refusal to accept the package. 7. **Regulatory Exceptions**: Compliance with local regulations and laws can sometimes cause exceptions if shipments do not meet specific requirements or if there are changes in regulations that affect delivery processes. 8. **Mechanical and Equipment Failures**: Breakdowns of vehicles, machinery, or other equipment necessary for transportation and handling can lead to delays and disruptions. 9. **Security Exceptions**: Issues related to security checks, such as suspicious packages or security breaches at facilities, can also cause exceptions. 10. **Natural Disaster Exceptions**: Major events like earthquakes, hurricanes, or wildfires can severely impact logistics operations and cause significant delays. Understanding these types of exceptions allows DHL and other logistics providers to anticipate potential problems, implement proactive measures to mitigate them, and develop effective strategies for resolving issues quickly when they arise. This not only enhances customer satisfaction but also improves operational efficiency and reliability in the delivery process. By categorizing and addressing these exceptions systematically, logistics companies can better manage risks and ensure smoother operations despite unforeseen challenges.
Importance in Logistics
Logistics plays a pivotal role in the modern supply chain, serving as the backbone that ensures the efficient and timely movement of goods from manufacturers to consumers. The importance of logistics cannot be overstated, as it directly impacts the overall performance and profitability of businesses. Here are several key reasons why logistics is crucial: 1. **Supply Chain Efficiency**: Logistics optimizes the flow of goods, services, and information from raw materials to end customers. Efficient logistics streamline operations, reduce lead times, and enhance the reliability of deliveries, which in turn improve customer satisfaction. 2. **Cost Management**: Effective logistics management helps in controlling costs associated with transportation, warehousing, and inventory management. By optimizing routes, reducing transit times, and leveraging economies of scale, businesses can significantly lower their operational expenses. 3. **Risk Mitigation**: Logistics involves managing risks such as delays, damage to goods, and compliance issues. A well-planned logistics strategy can mitigate these risks through contingency planning, insurance coverage, and adherence to regulatory standards. 4. **Customer Satisfaction**: Timely and accurate delivery of products is critical for maintaining customer trust and loyalty. Logistics ensures that products reach customers in the right condition and at the right time, thereby enhancing customer satisfaction and driving repeat business. 5. **Competitive Advantage**: In today’s competitive market, companies that excel in logistics can gain a significant edge over their competitors. By offering faster delivery times, flexible shipping options, and reliable service, businesses can differentiate themselves and attract more customers. 6. **Data-Driven Decision Making**: Modern logistics relies heavily on data analytics to optimize operations. By analyzing data on shipment patterns, traffic conditions, and inventory levels, businesses can make informed decisions that improve their supply chain resilience and agility. 7. **Global Reach**: With the rise of international trade, logistics has become essential for connecting businesses across different regions. It facilitates the movement of goods across borders while ensuring compliance with various regulations and customs requirements. 8. **Innovation and Technology**: The integration of technology such as AI, IoT, and blockchain into logistics has revolutionized the industry. These technologies enhance visibility, improve tracking capabilities, and automate processes, leading to greater efficiency and accuracy. In the context of understanding exceptions in DHL or any other logistics provider, recognizing the importance of logistics underscores why exceptions—such as delays or misdeliveries—must be managed proactively. By understanding these exceptions within the broader framework of logistics' critical role in supply chain management, businesses can better address disruptions and maintain high service standards. This holistic approach ensures that any deviations from the norm are quickly identified and resolved to minimize their impact on overall operations.
Causes and Triggers of Exceptions in DHL Operations
In the complex and dynamic environment of DHL operations, exceptions can arise from a multitude of factors, impacting the efficiency and reliability of logistics services. This article delves into the primary causes and triggers of these exceptions, categorizing them into three key areas: Operational Issues, External Factors, and Customer-Related Issues. Operational Issues, such as inadequate staffing, equipment malfunctions, and procedural inefficiencies, can significantly disrupt the smooth flow of operations. External Factors, including weather conditions, geopolitical instability, and regulatory changes, also play a crucial role in causing exceptions. Additionally, Customer-Related Issues, such as incorrect address information or special handling requirements, can complicate the delivery process. Understanding these causes is essential for mitigating risks and enhancing service quality. By examining these factors in detail, we can better address the root causes of exceptions and improve overall operational performance. Let's begin by exploring the Operational Issues that frequently affect DHL operations.
Operational Issues
Operational issues within DHL's logistics network can significantly impact the efficiency and reliability of their services, leading to exceptions that disrupt the smooth flow of operations. One primary operational issue is **inefficient routing and scheduling**, where suboptimal routes or scheduling conflicts can cause delays and increased fuel consumption. This can be exacerbated by **traffic congestion** and **road conditions**, which are often unpredictable and can lead to unforeseen delays. Another critical issue is **inventory management**, where inaccurate stock levels or misplaced items can result in failed deliveries or additional handling costs. **Technological glitches**, such as system downtime or software malfunctions, can also hinder operations by disrupting communication between different departments and stakeholders. Furthermore, **human error** remains a significant factor, with mistakes in data entry, labeling, or handling procedures contributing to exceptions. **Weather conditions** and **natural disasters** are external factors that can severely impact logistics operations, causing delays and damage to shipments. Additionally, **regulatory compliance issues** can arise from changes in customs regulations or local laws, leading to delays at border crossings or other checkpoints. **Supply chain disruptions**, including supplier failures or manufacturing delays, can also cascade into operational issues for DHL. Lastly, **capacity constraints** during peak periods can overwhelm the system, leading to backlogs and increased exception rates. Addressing these operational issues requires a multifaceted approach that includes investing in advanced technology, enhancing employee training, and developing robust contingency plans to mitigate the impact of external factors. By doing so, DHL can minimize exceptions and maintain high service standards despite the complexities inherent in global logistics operations.
External Factors
External factors play a crucial role in the causes and triggers of exceptions in DHL operations. These factors are beyond the control of DHL but significantly impact the efficiency and reliability of their services. One of the primary external factors is **weather conditions**. Inclement weather such as heavy rain, snowstorms, or hurricanes can disrupt transportation networks, causing delays and damage to shipments. For instance, a severe storm might force the closure of airports or highways, leading to missed delivery deadlines and potential damage to cargo. Another significant external factor is **government regulations and policies**. Changes in customs regulations, trade policies, or security protocols can create bottlenecks in the logistics chain. For example, new tariffs imposed by a country can lead to increased costs and delays due to additional paperwork and inspections required for compliance. Similarly, changes in border control policies can slow down cross-border shipments. **Economic conditions** also contribute to exceptions in DHL operations. Economic downturns or recessions can lead to reduced consumer spending, resulting in lower demand for logistics services. Conversely, economic booms can create surges in demand that may strain DHL's capacity, leading to delays and inefficiencies. Additionally, fluctuations in fuel prices can impact operational costs and affect delivery schedules. **Geopolitical instability** is another critical external factor. Conflicts, political unrest, or sanctions in certain regions can make it difficult or impossible to operate in those areas. This instability can lead to rerouting shipments, which increases transit times and costs. For instance, a conflict in a key transit country might necessitate diverting shipments through alternative routes that are longer and more expensive. **Public health crises**, such as pandemics, also have a profound impact on logistics operations. During such crises, governments may impose lockdowns or travel restrictions that limit the movement of goods and personnel. This can result in significant delays and disruptions across the supply chain. For example, during the COVID-19 pandemic, many countries implemented strict lockdowns that severely impacted global logistics operations. Finally, **infrastructure issues** such as road closures, port congestion, or airport capacity constraints can also trigger exceptions. These issues can arise due to natural disasters, construction projects, or simply inadequate infrastructure to handle peak volumes. For example, a major port closure due to a natural disaster can cause a backlog of shipments waiting to be processed, leading to extended delivery times. In summary, external factors such as weather conditions, government regulations, economic conditions, geopolitical instability, public health crises, and infrastructure issues are key contributors to exceptions in DHL operations. Understanding these factors is crucial for mitigating their impact and ensuring smoother logistics operations despite these challenges.
Customer-Related Issues
Customer-related issues are a significant source of exceptions in DHL operations, often stemming from misunderstandings, miscommunications, or unmet expectations. One primary cause is **inaccurate or incomplete shipping information**, where customers provide incorrect addresses, contact details, or package descriptions. This can lead to delays, failed deliveries, and additional costs for redelivery or return shipping. Another common issue is **customer availability**, where recipients are not present to receive packages during scheduled delivery times, necessitating multiple attempts and potential storage fees. **Communication gaps** also play a crucial role. When customers do not receive timely updates on their shipment status or experience difficulties in tracking their packages, it can lead to frustration and mistrust. Moreover, **special handling instructions** that are not clearly communicated can result in mishandling of packages, such as those requiring signature upon delivery or specific handling due to fragile contents. Additionally, **customer expectations** regarding delivery times and service levels can sometimes be unrealistic or not aligned with the service chosen. For instance, choosing a standard shipping option but expecting expedited delivery times can lead to dissatisfaction when the package does not arrive as quickly as anticipated. **Returns and claims** are another area where customer-related issues arise. When customers initiate returns due to dissatisfaction with the product or service, it can trigger a series of logistical challenges for DHL, including reverse logistics and potential disputes over refund policies. Lastly, **cultural and language barriers** can complicate interactions between DHL representatives and international customers. Misunderstandings due to language differences or cultural nuances in communication styles can exacerbate issues and prolong resolution times. Addressing these customer-related issues requires proactive measures such as clear communication channels, robust tracking systems, flexible delivery options, and comprehensive training for customer service representatives to handle diverse customer needs effectively. By mitigating these triggers, DHL can reduce exceptions and enhance overall customer satisfaction.
Managing and Resolving Exceptions in DHL
Managing and resolving exceptions is a critical aspect of logistics operations, particularly for a global leader like DHL. Effective exception management ensures that disruptions are minimized, and service quality is maintained. This article delves into three key strategies that DHL employs to manage and resolve exceptions: proactive measures, reactive strategies, and the utilization of technology and tools. Proactive measures involve anticipating potential issues before they arise, such as conducting thorough risk assessments and implementing preventive maintenance. Reactive strategies focus on swift and effective responses to unexpected disruptions, ensuring minimal impact on operations. Technology and tools play a pivotal role in enhancing both proactive and reactive approaches by providing real-time data, automated alerts, and advanced analytics. By integrating these strategies, DHL can significantly reduce the occurrence and impact of exceptions. Let's start by examining the proactive measures that form the foundation of DHL's exception management framework.
Proactive Measures
In the context of managing and resolving exceptions at DHL, proactive measures are crucial for minimizing disruptions and ensuring smooth operations. These measures involve anticipating potential issues before they arise, thereby reducing the likelihood of exceptions occurring in the first place. One key proactive measure is **predictive analytics**, where data is analyzed to forecast potential bottlenecks or delays in the supply chain. By leveraging advanced algorithms and historical data, DHL can identify high-risk areas and implement preventive strategies such as rerouting shipments or increasing resource allocation. Another vital proactive measure is **regular maintenance** of equipment and vehicles. Scheduled maintenance ensures that machinery and vehicles are in optimal working condition, reducing the risk of mechanical failures that could lead to exceptions. Additionally, **staff training** plays a significant role; well-trained personnel are better equipped to handle unexpected situations efficiently and make informed decisions that mitigate the impact of exceptions. **Real-time monitoring** is also essential for proactive exception management. Utilizing GPS tracking and other monitoring technologies allows DHL to keep a close eye on shipments in transit, enabling swift intervention if any deviations from the planned route or schedule occur. This real-time visibility helps in identifying potential exceptions early, allowing for timely corrective actions. Furthermore, **collaboration with suppliers** is a proactive measure that can significantly reduce exceptions. Building strong relationships with suppliers and ensuring they adhere to strict quality and delivery standards helps in maintaining a reliable supply chain. Regular audits and performance reviews of suppliers also help in identifying and addressing any potential issues before they escalate into exceptions. **Contingency planning** is another critical proactive measure. Developing comprehensive contingency plans for various scenarios such as natural disasters, geopolitical instability, or unexpected demand surges ensures that DHL is prepared to respond effectively when exceptions do occur. These plans outline clear procedures for diverting resources, rerouting shipments, and communicating with stakeholders, thereby minimizing the impact of exceptions on operations. In summary, proactive measures at DHL involve a combination of predictive analytics, regular maintenance, staff training, real-time monitoring, supplier collaboration, and contingency planning. By implementing these strategies, DHL can significantly reduce the occurrence of exceptions and ensure that when exceptions do arise, they are managed efficiently to maintain high service standards and customer satisfaction. These proactive approaches not only enhance operational reliability but also contribute to a more resilient and adaptable logistics network.
Reactive Strategies
In the context of managing and resolving exceptions at DHL, reactive strategies play a crucial role in mitigating the impact of unforeseen disruptions. These strategies are designed to be implemented after an exception has occurred, focusing on swift and effective responses to restore normal operations as quickly as possible. When an exception arises, such as a shipment delay or loss, DHL's reactive strategies kick into action. The first step involves immediate notification to all relevant stakeholders, including customers, to ensure transparency and manage expectations. This proactive communication helps in building trust and reduces the likelihood of further complications. Next, a thorough investigation is conducted to identify the root cause of the exception. This involves analyzing data from various sources, including tracking systems, customer feedback, and internal reports. By understanding what went wrong, DHL can implement corrective actions to prevent similar exceptions in the future. Simultaneously, contingency plans are activated to minimize the impact on the customer. For instance, if a shipment is delayed, DHL might expedite an alternative shipment or provide a temporary replacement solution. These measures ensure that the customer's needs are met despite the initial disruption. Another key aspect of reactive strategies at DHL is the use of advanced technology. Leveraging tools like real-time tracking and predictive analytics helps in identifying potential exceptions before they become critical issues. This allows for more timely interventions and better resource allocation. Additionally, DHL's reactive strategies emphasize continuous improvement. Post-incident reviews are conducted to assess the effectiveness of the response and identify areas for enhancement. This feedback loop ensures that lessons learned from each exception are integrated into future operations, enhancing overall resilience and efficiency. In summary, DHL's reactive strategies for managing exceptions are centered around swift communication, thorough investigation, effective contingency planning, technological leverage, and continuous improvement. By adopting these strategies, DHL can efficiently resolve exceptions, maintain customer satisfaction, and uphold its commitment to reliable logistics services.
Technology and Tools
In the context of managing and resolving exceptions at DHL, technology and tools play a pivotal role in enhancing efficiency, accuracy, and customer satisfaction. Advanced tracking systems, such as GPS and RFID, enable real-time monitoring of shipments, allowing for immediate identification of any deviations from the planned route or schedule. This proactive approach enables DHL to swiftly address potential issues before they escalate into full-blown exceptions. Automated exception management software integrates with these tracking systems to flag anomalies automatically, triggering alerts to relevant teams who can then take corrective action promptly. Additionally, data analytics tools provide insights into recurring patterns of exceptions, helping DHL to identify root causes and implement preventive measures. For instance, predictive analytics can forecast potential delays due to weather conditions or traffic congestion, allowing for proactive rerouting or rescheduling. Furthermore, mobile applications empower field operatives with real-time information and communication tools, facilitating quicker resolution of on-ground issues. Customer-facing platforms also ensure transparency by providing updates on shipment status and any exceptions encountered, fostering trust and reducing inquiries. Overall, leveraging cutting-edge technology and specialized tools not only streamlines exception management but also enhances the overall logistics experience for both DHL and its clients. By integrating these technologies seamlessly into their operations, DHL can minimize the impact of exceptions and maintain a high level of service reliability.