What Is Resin Made Of

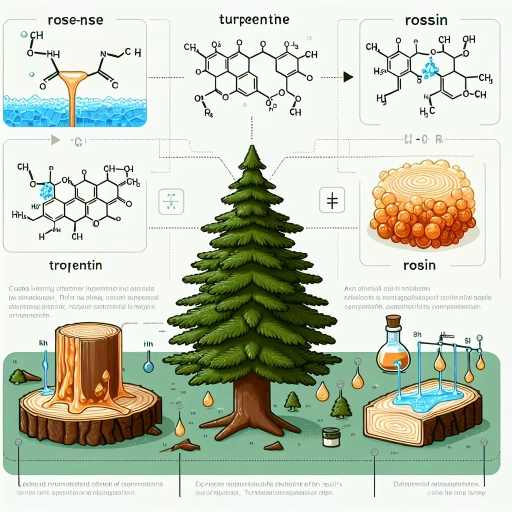
Resin, a versatile and widely used material, has become an integral part of various industries ranging from construction and automotive to art and crafts. Its diverse applications are rooted in its unique properties, which are determined by its chemical composition and the raw materials used in its production. Understanding what resin is made of is crucial for appreciating its versatility and functionality. This article delves into the intricacies of resin, starting with its chemical composition, which forms the foundation of its characteristics. We will explore the specific compounds that constitute resin, followed by an examination of the raw materials that are typically used in its production. Finally, we will discuss the applications and properties of different types of resins, highlighting their distinct uses and benefits. By grasping these fundamental aspects, readers will gain a comprehensive understanding of resin's multifaceted nature. Let us begin by dissecting the chemical composition of resin, the cornerstone of its identity and functionality.
Chemical Composition of Resin
Resin, a versatile and widely used material, is fundamentally composed of complex chemical structures that determine its properties and applications. Understanding the chemical composition of resin is crucial for both industrial and scientific purposes. This article delves into the core components and processes that define resin's chemical makeup. We begin by exploring the building blocks of resin: **Monomers and Polymers**, which are the foundational units that combine to form the resin's structure. Next, we examine **Types of Chemical Bonds**, which play a pivotal role in stabilizing and shaping the resin's molecular framework. Additionally, we discuss the **Role of Catalysts and Initiators**, essential agents that facilitate the polymerization process, transforming monomers into a cohesive polymer network. By grasping these key aspects, we can better comprehend the intricate **Chemical Composition of Resin**, enabling us to harness its full potential across various industries. This comprehensive overview will provide a detailed insight into the chemical intricacies of resin, enhancing our understanding of its composition and functionality.
Monomers and Polymers
Monomers and polymers are fundamental components in the chemical composition of resin, playing a crucial role in its structure and properties. **Monomers** are small, simple molecules that serve as the building blocks of polymers. These molecules typically contain reactive functional groups that allow them to bond with other monomers during a process known as polymerization. Common types of monomers include ethylene, propylene, and styrene, each with distinct chemical properties that influence the final polymer's characteristics. **Polymers**, on the other hand, are large molecules formed by the chemical bonding of numerous monomer units. This polymerization process can occur through various mechanisms such as addition polymerization or condensation polymerization, depending on the type of monomers involved. The resulting polymer can exhibit a wide range of physical and chemical properties, including strength, flexibility, and resistance to heat or chemicals. For instance, polyethylene is a versatile polymer derived from ethylene monomers and is widely used in packaging materials due to its durability and resistance to moisture. In the context of resin, the specific combination and arrangement of monomers determine its chemical composition and subsequent performance. For example, epoxy resins are formed from the polymerization of epoxide monomers with hardeners, resulting in a strong and adhesive material commonly used in industrial applications. Similarly, polyurethane resins are synthesized from isocyanate and polyol monomers, offering excellent flexibility and resistance to abrasion. The versatility of monomers and polymers allows for the creation of resins with tailored properties, making them indispensable in various industries such as construction, automotive, and electronics. Understanding the chemistry behind monomer-polymer interactions is essential for developing new resin formulations that meet specific requirements. Moreover, advancements in polymer science continue to expand the range of available resins, enabling innovative solutions across diverse fields. In summary, monomers and polymers are the foundational elements that define the chemical composition of resin. Their unique properties and interactions during polymerization dictate the final characteristics of the resin, making them crucial for a wide array of applications. As research and technology evolve, the potential for creating new and improved resin materials remains vast, underscoring the importance of understanding these fundamental components.
Types of Chemical Bonds
Chemical bonds are the fundamental forces that hold atoms together to form molecules, and understanding these bonds is crucial for grasping the chemical composition of resin. There are several types of chemical bonds, each with distinct characteristics that influence the properties and behavior of the resulting compounds. **1. Covalent Bonds:** Covalent bonds are formed when two or more atoms share one or more pairs of electrons to achieve a stable electronic configuration. This type of bonding is prevalent in organic compounds, including many types of resins. For instance, in epoxy resins, covalent bonds between carbon, oxygen, and hydrogen atoms create a robust and durable polymer network. The strength and flexibility of these bonds contribute significantly to the mechanical properties of the resin. **2. Ionic Bonds:** Ionic bonds result from the transfer of electrons between atoms, leading to the formation of ions with opposite charges that attract each other. While less common in organic resins, ionic bonds can be present in certain inorganic components or additives that may be included in resin formulations. These bonds can enhance thermal stability and resistance to chemicals. **3. Hydrogen Bonds:** Hydrogen bonds are relatively weak electrostatic attractions between a hydrogen atom bonded to a highly electronegative atom (such as oxygen, nitrogen, or fluorine) and another electronegative atom. In resins, hydrogen bonds can play a role in secondary interactions that influence the material's viscosity, solubility, and overall performance. For example, in polyurethane resins, hydrogen bonding between urethane linkages can affect the polymer's flexibility and toughness. **4. Van der Waals Bonds:** Van der Waals bonds are the weakest type of intermolecular forces but are essential for understanding the physical properties of resins. These bonds arise from temporary dipoles formed due to electron cloud fluctuations in non-polar molecules. In resins like polyethylene or polypropylene, van der Waals interactions contribute to the material's melting point, crystallinity, and impact resistance. **5. Pi Bonds:** Pi bonds are a type of covalent bond that involves the sideways overlap of p-orbitals. These bonds are particularly relevant in unsaturated polymers such as acrylic resins, where double or triple bonds between carbon atoms provide sites for cross-linking reactions during curing processes. The presence of pi bonds can significantly impact the resin's reactivity and final mechanical properties. Understanding these different types of chemical bonds is essential for comprehending the chemical composition and behavior of various resins. Each bond type contributes uniquely to the overall structure and performance characteristics of the resin, making it possible to tailor resin formulations for specific applications by manipulating these bonding interactions. Whether it's enhancing strength through covalent networks or improving thermal stability with ionic components, the nature of chemical bonding in resins underpins their versatility and utility across diverse industries.
Role of Catalysts and Initiators
In the intricate process of resin formation, catalysts and initiators play pivotal roles that are both crucial and complementary. These chemical agents are essential for initiating and sustaining the polymerization reaction, which transforms monomers into the complex polymer network that constitutes resin. **Catalysts**, often metal-based compounds, accelerate chemical reactions without being consumed in the process. They lower the activation energy required for the reaction to proceed, thereby increasing the reaction rate and efficiency. For instance, in the production of epoxy resins, catalysts such as amines or imidazoles facilitate the curing process by speeding up the cross-linking reactions between epoxy groups and hardeners. This ensures that the resin achieves its desired mechanical properties and stability within a shorter timeframe. **Initiators**, on the other hand, are substances that start the polymerization reaction by generating free radicals or ions. These reactive species then propagate through the monomer units, leading to chain growth and eventually forming the polymer chain. In the context of acrylic resins, photoinitiators like benzophenone or camphorquinone are commonly used. When exposed to light of a specific wavelength, these initiators decompose to produce free radicals that trigger the polymerization of acrylic monomers. The choice of initiator is critical as it influences the rate of polymerization, the molecular weight of the polymer, and ultimately the physical properties of the resin. The synergy between catalysts and initiators is key to achieving optimal resin performance. For example, in the synthesis of polyurethane resins, a combination of catalysts (such as tin or bismuth compounds) and initiators (like isocyanates) ensures that the reaction proceeds smoothly and efficiently. The catalysts enhance the reactivity of the isocyanate groups with polyols, while the initiators ensure that the polymerization starts promptly and proceeds uniformly. This balanced interplay allows for precise control over the chemical composition and structure of the resulting resin, enabling it to meet specific application requirements such as strength, flexibility, or thermal stability. In summary, catalysts and initiators are indispensable components in the chemical composition of resin, each contributing uniquely to the polymerization process. By understanding their roles and interactions, manufacturers can tailor resin formulations to achieve desired properties, making these materials versatile and indispensable across various industries from automotive to biomedical applications. The precise selection and optimization of these agents are critical steps in ensuring that resins exhibit the required performance characteristics, underscoring their central role in the broader context of resin chemistry.
Raw Materials Used in Resin Production
Resin production is a multifaceted process that relies on a diverse array of raw materials, each contributing unique properties and benefits to the final product. At the heart of resin manufacturing are three primary categories of raw materials: petroleum-based derivatives, natural sources and biopolymers, and recycled materials. Petroleum-based derivatives, such as styrene and polyethylene, provide the foundational building blocks for many resin types, offering durability and versatility. In contrast, natural sources and biopolymers, including plant-based oils and cellulose, offer sustainable alternatives that are increasingly important in today's eco-conscious market. Additionally, the integration of recycled materials into resin production not only reduces waste but also enhances the environmental sustainability of the manufacturing process. Understanding these raw materials is crucial as it directly influences the chemical composition of resin, which in turn determines its performance, application, and overall quality. This article delves into these three key areas, providing a comprehensive overview of how different raw materials shape the chemical composition of resin.
Petroleum-Based Derivatives
Petroleum-based derivatives play a pivotal role in the production of resins, serving as fundamental raw materials that underpin the manufacturing process. These derivatives are obtained from crude oil through various refining processes, including cracking, reforming, and distillation. The most common petroleum-based derivatives used in resin production include ethylene, propylene, butadiene, and styrene. Ethylene, for instance, is a key precursor for polyethylene and polyvinyl chloride (PVC) resins, which are widely used in packaging materials, pipes, and vinyl records. Propylene is another crucial derivative that is converted into polypropylene resin, known for its durability and resistance to chemicals; it is often used in automotive parts, medical devices, and consumer goods. Butadiene, derived from the cracking of naphtha or other petroleum fractions, is essential for producing styrene-butadiene rubber (SBR) and styrene-butadiene styrene (SBS) block copolymers. These materials are integral to the tire industry and also find applications in adhesives and sealants. Styrene, which can be produced from ethylene and benzene, is a critical component in the synthesis of polystyrene resins. Polystyrene is versatile and used in foam cups, insulation materials, and electronic components. The versatility of petroleum-based derivatives stems from their ability to be chemically modified and combined in various ways to produce resins with specific properties. For example, the addition of additives such as plasticizers, fillers, and stabilizers can enhance the performance characteristics of these resins. This adaptability makes them indispensable in a broad spectrum of industries ranging from construction to electronics. However, it is important to note that the reliance on petroleum-based derivatives also comes with environmental and sustainability concerns. The extraction and processing of crude oil are energy-intensive processes that contribute to greenhouse gas emissions. Additionally, the non-renewable nature of petroleum resources underscores the need for ongoing research into alternative raw materials and more sustainable production methods. Despite these challenges, advancements in technology have led to more efficient refining processes and the development of greener alternatives such as bio-based resins derived from renewable resources like plant oils and biomass. These innovations aim to reduce the environmental footprint of resin production while maintaining the high performance standards demanded by various industries. In summary, petroleum-based derivatives remain a cornerstone in resin production due to their availability, versatility, and cost-effectiveness. However, as the world moves towards a more sustainable future, it is crucial to balance these benefits with the development of eco-friendly alternatives that can meet the growing demand for resins without compromising environmental integrity.
Natural Sources and Biopolymers
Natural sources and biopolymers play a pivotal role in the production of resins, offering sustainable alternatives to traditional petroleum-based materials. These biopolymers are derived from renewable resources such as plants, algae, and microorganisms, which can be replenished quickly compared to fossil fuels. One of the most significant natural sources is cellulose, a primary component of plant cell walls. Cellulose can be extracted from wood pulp or plant fibers and converted into cellulose acetate, a versatile biopolymer used in various resin formulations. Another key source is starch, found abundantly in crops like corn, potatoes, and tapioca. Starch-based biopolymers can be modified to enhance their mechanical properties and thermal stability, making them suitable for a wide range of applications. Lignin, a byproduct of the paper and pulp industry, is another promising natural source. It can be chemically modified to produce lignin-based resins that exhibit excellent thermal resistance and mechanical strength. Additionally, proteins such as soy protein, wheat gluten, and casein are being explored for their potential in biopolymer production. These proteins can be cross-linked to form robust networks that mimic the properties of synthetic resins. Microorganisms also contribute significantly to biopolymer production through fermentation processes. For instance, polyhydroxyalkanoates (PHA) are biodegradable polymers produced by bacterial fermentation of sugars or lipids. PHA resins offer excellent biocompatibility and can be tailored for specific applications in medical devices, packaging materials, and even 3D printing. Algae are another emerging source for biopolymer production. Algal biomass can be converted into various biopolymers, including polyesters and polyamides, which have potential uses in resin formulations for coatings, adhesives, and composites. The use of algae reduces the competition with food crops for land and resources, making it a highly sustainable option. The integration of these natural sources and biopolymers into resin production not only reduces dependence on non-renewable resources but also mitigates environmental impacts associated with traditional resin manufacturing. Biodegradability and compostability of these materials further enhance their appeal by reducing waste accumulation and promoting a circular economy. As technology continues to advance, the versatility and performance of biopolymer-based resins are expected to improve, making them increasingly competitive with their synthetic counterparts. This shift towards sustainable raw materials is crucial for the future of resin production, aligning with global efforts to achieve environmental sustainability and reduce carbon footprints.
Recycled Materials and Sustainability
In the quest for sustainability, the integration of recycled materials into various production processes has become a cornerstone of environmental stewardship. This is particularly evident in the realm of resin production, where the use of recycled materials not only reduces the demand on virgin raw materials but also significantly diminishes the ecological footprint associated with traditional manufacturing methods. Recycled materials, such as post-consumer plastics and industrial waste, can be transformed into high-quality resin through advanced recycling technologies. For instance, polyethylene terephthalate (PET) from discarded plastic bottles can be recycled and converted into polyester resin, which is widely used in applications ranging from automotive parts to consumer goods. Similarly, polypropylene (PP) and polyvinyl chloride (PVC) from various waste streams can be recycled and incorporated into resin formulations, enhancing their durability and performance while minimizing waste disposal issues. The adoption of recycled materials in resin production also fosters a circular economy by closing the loop on material usage, thereby reducing landfill waste and conserving natural resources. Moreover, this approach aligns with global sustainability goals by decreasing greenhouse gas emissions and energy consumption associated with extracting, processing, and transporting raw materials. As consumers increasingly demand eco-friendly products, manufacturers are incentivized to innovate and expand their use of recycled materials, driving a market shift towards more sustainable practices. By leveraging recycled materials in resin production, industries can achieve a dual benefit: enhancing their environmental credentials while maintaining the quality and functionality of their products. This synergy between sustainability and performance underscores the critical role that recycled materials play in shaping a more environmentally conscious future for resin production and beyond.
Applications and Properties of Different Resins
Resins, versatile and widely used materials, play a crucial role in various industries due to their unique properties and applications. This article delves into the characteristics, uses, and industrial significance of three prominent types of resins: epoxy, polyester, and acrylic. Epoxy resins, known for their exceptional strength and durability, are often employed in structural adhesives, coatings, and composite materials. Polyester resins, with their excellent resistance to chemicals and UV light, are commonly used in fiberglass production, marine applications, and automotive parts. Acrylic resins, characterized by their transparency and flexibility, find extensive use in coatings, adhesives, and medical devices. Understanding the distinct properties and applications of these resins is essential for selecting the right material for specific tasks. As we explore the diverse uses of epoxy, polyester, and acrylic resins, it becomes clear that their effectiveness is deeply rooted in their chemical composition. This article will transition seamlessly into a detailed examination of the chemical composition of resins, providing a comprehensive understanding of what makes each type so valuable in its respective field.
Epoxy Resin Characteristics and Uses
Epoxy resin stands out as a versatile and highly sought-after material due to its unique characteristics and diverse applications. At its core, epoxy resin is a two-part system consisting of an epoxide and a hardener, which when mixed together, undergo a chemical reaction known as curing. This process transforms the liquid components into a solid, rigid, and durable material. One of the key characteristics of epoxy resin is its exceptional mechanical strength and resistance to impact, making it ideal for structural applications. Additionally, epoxy exhibits excellent adhesion to various substrates such as metals, glass, and other plastics, which enhances its utility in bonding and coating processes. The chemical stability of epoxy resin is another significant attribute; it offers resistance to chemicals, heat, and moisture, making it suitable for use in harsh environments. This property is particularly beneficial in industrial settings where exposure to corrosive substances or extreme temperatures is common. Furthermore, epoxy resin can be formulated to have specific properties such as flexibility or rigidity, transparency or coloration, and even electrical conductivity, allowing it to cater to a wide range of needs. In terms of applications, epoxy resin is ubiquitous across various industries. In construction, it is used as an adhesive for bonding concrete and steel in structural repairs and as a coating to protect surfaces from corrosion. In electronics, epoxy is employed as an encapsulant for protecting sensitive components from environmental stressors. The automotive sector also leverages epoxy for its high-performance adhesives and coatings that enhance vehicle durability and aesthetics. Artists and hobbyists appreciate epoxy resin for its versatility in crafting decorative items such as jewelry, furniture, and sculptures. Its ability to be colored and mixed with pigments or fillers allows for the creation of intricate designs and patterns. Moreover, epoxy's transparency makes it an excellent choice for casting clear objects like river tables or artistic pieces that require depth and clarity. In medical fields, epoxy resins are used in dental applications due to their biocompatibility and ability to form strong bonds with tooth structures. They are also utilized in the manufacture of medical devices where sterilization and chemical resistance are crucial. Overall, the combination of mechanical strength, chemical resistance, and versatility in formulation makes epoxy resin an indispensable material across multiple disciplines. Its wide array of applications underscores its importance as a modern engineering material capable of meeting diverse performance requirements. Whether in industrial manufacturing, artistic expression, or medical technology, epoxy resin continues to play a vital role due to its unique characteristics and adaptability.
Polyester Resin Properties and Applications
Polyester resin, a versatile and widely used thermosetting polymer, boasts a range of properties that make it an ideal material for various applications. **Mechanical Properties:** Polyester resin is known for its high tensile strength, impact resistance, and durability, making it suitable for structural components and composite materials. Its ability to withstand harsh environmental conditions, such as exposure to chemicals and UV light, further enhances its utility. **Thermal Properties:** The resin exhibits good thermal stability, allowing it to maintain its integrity over a broad temperature range. This characteristic is crucial in applications where the material may be subjected to heat fluctuations. **Chemical Resistance:** Polyester resin offers excellent resistance to many chemicals, including acids, bases, and solvents, which is particularly beneficial in industrial settings where exposure to corrosive substances is common. **Applications:** The diverse properties of polyester resin have led to its widespread adoption across multiple industries. **Composite Materials:** It is frequently used in the production of fiberglass-reinforced plastics (FRP), which are employed in boat hulls, car bodies, and other structural components due to their lightweight yet robust nature. **Construction:** Polyester resin is utilized in the manufacture of roofing materials, flooring systems, and other building elements because of its durability and resistance to weathering. **Industrial Coatings:** Its chemical resistance makes it an excellent choice for protective coatings on metal surfaces, tanks, and pipes. **Art and Craft:** In the realm of art and craft, polyester resin is popular for creating sculptures, jewelry, and other decorative items due to its ease of use and ability to achieve high-gloss finishes. **Specialized Applications:** Beyond these general uses, polyester resin finds niche applications in fields such as **Medical Devices:** Here, it is valued for its biocompatibility and ability to be sterilized, making it suitable for medical implants and equipment. **Electrical Insulation:** The resin's electrical insulating properties make it a material of choice for encapsulating electrical components and ensuring safe operation. **Automotive:** In the automotive sector, polyester resin is used in body panels and other components where weight reduction without compromising strength is critical. In summary, the unique combination of mechanical, thermal, and chemical properties of polyester resin makes it a versatile material with a broad spectrum of applications. From industrial and construction uses to artistic endeavors and specialized fields like medicine and electronics, polyester resin continues to be a cornerstone in modern manufacturing due to its reliability, performance, and adaptability.
Acrylic Resin Features and Industrial Uses
Acrylic resin stands out as a versatile and highly sought-after material in various industrial applications, thanks to its unique combination of properties. One of the key features of acrylic resin is its exceptional clarity and transparency, making it an ideal choice for applications where optical clarity is crucial. This characteristic is particularly beneficial in the production of lenses, light guides, and other optical components. Additionally, acrylic resin exhibits excellent impact resistance and durability, which makes it suitable for use in demanding environments such as automotive parts, signage, and construction materials. Another significant advantage of acrylic resin is its ease of fabrication. It can be molded, cast, or extruded into complex shapes with high precision, allowing for a wide range of design possibilities. This versatility is further enhanced by its compatibility with various pigments and additives, enabling the creation of products with specific colors and properties. For instance, UV stabilizers can be added to improve the resin's resistance to ultraviolet light degradation, extending its lifespan in outdoor applications. In terms of industrial uses, acrylic resin plays a critical role in several sectors. In the automotive industry, it is used to manufacture components such as dashboards, trim parts, and even body panels due to its lightweight yet robust nature. The aerospace industry also leverages acrylic resin for producing transparent canopies and windows due to its high strength-to-weight ratio and resistance to weathering. The construction industry benefits from acrylic resin's ability to form durable and weather-resistant coatings for floors and walls. These coatings offer excellent chemical resistance and are easy to clean, making them ideal for high-traffic areas and industrial settings. Furthermore, acrylic resin is widely used in medical devices due to its biocompatibility and sterilizability. It is often employed in the manufacture of medical instruments, implants, and diagnostic equipment. In addition to these applications, acrylic resin is also a popular choice in the arts and crafts sector. Its ability to be molded into intricate shapes and its compatibility with various dyes make it a favorite among artists and hobbyists. The resin's fast curing time and low odor also contribute to its appeal in these creative fields. Overall, the unique blend of transparency, impact resistance, ease of fabrication, and versatility in terms of additives makes acrylic resin an indispensable material across multiple industries. Its diverse applications underscore its importance as a modern engineering material capable of meeting a wide range of performance requirements. Whether in automotive parts, medical devices, or artistic creations, acrylic resin continues to play a vital role in driving innovation and efficiency.