What Is Whmis Stand For

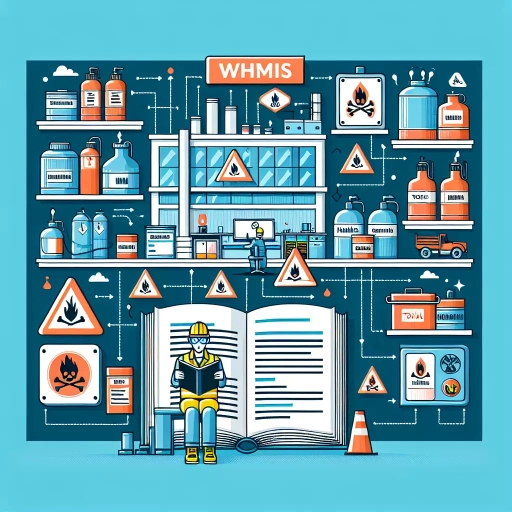
In the realm of workplace safety and chemical management, few acronyms are as pivotal as WHMIS. Standing for Workplace Hazardous Materials Information System, WHMIS is a comprehensive framework designed to protect workers from the dangers associated with hazardous materials. This system is not just a set of regulations; it is a robust mechanism that ensures employers and employees alike are well-informed about the risks and proper handling procedures for hazardous substances. To delve into the intricacies of WHMIS, it is essential to first understand the acronym itself, which sets the stage for exploring its core principles. These principles form the backbone of WHMIS, outlining how to classify, label, and communicate the hazards of various materials. Finally, effective implementation and compliance with WHMIS are crucial for maintaining a safe work environment. By grasping these elements, organizations can ensure that they are not only adhering to legal standards but also fostering a culture of safety and responsibility. Let us begin by understanding the acronym WHMIS, which is the foundation upon which all other aspects of this vital system are built.
Understanding the Acronym WHMIS
In the realm of workplace safety and chemical management, few acronyms are as pivotal as WHMIS. The Workplace Hazardous Materials Information System is a cornerstone of Canadian health and safety regulations, designed to protect workers from the dangers associated with hazardous materials. To fully grasp the significance of WHMIS, it is essential to delve into its definition and origin, understanding how it came to be a standard in occupational safety. Additionally, breaking down the key components and abbreviations within WHMIS provides clarity on its practical application. Historical context is also crucial, as it reveals the evolution of WHMIS over time, highlighting significant changes and updates that have enhanced its effectiveness. By exploring these facets—definition and origin, key components and abbreviation breakdown, and historical context and evolution—we can gain a comprehensive understanding of the acronym WHMIS and its critical role in ensuring a safer work environment. Understanding the Acronym WHMIS is more than just memorizing letters; it is about embracing a system that safeguards lives and promotes a culture of safety in the workplace.
Definition and Origin
**Definition and Origin** WHMIS, or the Workplace Hazardous Materials Information System, is a comprehensive Canadian standard designed to ensure the safe handling, use, storage, and disposal of hazardous materials in the workplace. The acronym WHMIS encapsulates a multifaceted system that integrates hazard classification, labeling, material safety data sheets (MSDS), and worker training to mitigate risks associated with hazardous substances. Originating in the late 1980s, WHMIS was developed through a collaborative effort between the federal, provincial, and territorial governments in Canada. This initiative aimed to harmonize the various regulations and standards across different jurisdictions, creating a unified framework for managing workplace hazards. At its core, WHMIS is built on three key pillars: hazard classification, labeling, and material safety data sheets. Hazard classification involves categorizing substances based on their physical and health hazards, ensuring that workers are aware of the potential dangers they may encounter. Labels on hazardous products provide critical information about the substance's identity, hazards, and safety precautions. Material safety data sheets (MSDS), now known as Safety Data Sheets (SDS), offer detailed information on the safe handling, use, storage, and emergency procedures for each hazardous material. The origins of WHMIS are rooted in the need for a standardized approach to workplace safety. Prior to its implementation, different regions in Canada had varying regulations and standards, which often led to confusion and inconsistencies. The introduction of WHMIS in 1988 marked a significant shift towards a more coordinated and effective system for managing workplace hazards. Over the years, WHMIS has undergone several updates and revisions to align with international standards, such as those set by the United Nations' Globally Harmonized System of Classification and Labelling of Chemicals (GHS). These updates have enhanced the system's effectiveness in protecting workers from chemical hazards. Understanding WHMIS is crucial for employers and employees alike, as it provides a structured framework for identifying and mitigating hazards. By adhering to WHMIS guidelines, workplaces can significantly reduce the risk of accidents, injuries, and illnesses related to hazardous materials. The system's emphasis on worker training ensures that employees are equipped with the knowledge and skills necessary to handle hazardous substances safely. In essence, WHMIS serves as a cornerstone of occupational health and safety in Canada, fostering a safer and healthier work environment through its comprehensive and integrated approach to hazard management.
Key Components and Abbreviation Breakdown
Understanding the acronym WHMIS (Workplace Hazardous Materials Information System) is crucial for ensuring safety in workplaces where hazardous materials are present. At the heart of WHMIS are several key components that work together to provide comprehensive information about the safe handling, use, and disposal of hazardous substances. **Key Components:** 1. **Labels:** These are critical for immediate identification of hazards. WHMIS labels must include a product identifier, hazard pictograms, signal words (such as "Danger" or "Warning"), hazard statements, and precautionary statements. 2. **Safety Data Sheets (SDS):** These detailed documents provide extensive information about the chemical, including its composition, first aid measures, fire-fighting measures, accidental release measures, handling and storage, exposure controls/personal protection, physical and chemical properties, stability and reactivity, toxicological information, ecological information, disposal considerations, transport information, regulatory information, and any other relevant data. 3. **Training:** Employers are required to provide training to workers on the safe handling of hazardous materials. This includes understanding labels and SDSs as well as procedures for handling emergencies. 4. **Classifications:** Hazardous materials are classified based on their physical or health hazards. There are 10 main hazard classes under WHMIS 2015: Explosives; Flammable Gases; Flammable Aerosols; Oxidizing Gases; Gases under Pressure; Flammable Liquids; Flammable Solids; Self-reactive Substances and Mixtures; Pyrophoric Liquids and Solids; Self-heating Substances and Mixtures; Substances and Mixtures which, in contact with water, emit flammable gases; Oxidizing Liquids and Solids; Corrosive to Metals; Toxic (Acute) Effects; Toxic (Chronic) Effects; Aspiration Hazard; Respiratory or Skin Sensitization; Germ Cell Mutagenicity; Carcinogenicity; Reproductive Toxicity; Specific Target Organ Toxicity (Single or Repeated Exposure); and Bioaccumulative Potential. **Abbreviation Breakdown:** - **WHMIS:** Workplace Hazardous Materials Information System - **SDS:** Safety Data Sheets - **GHS:** Globally Harmonized System of Classification and Labelling of Chemicals (the international standard that WHMIS 2015 aligns with) - **HCS:** Hazard Communication Standard (the U.S. equivalent of WHMIS) - **CAS:** Chemical Abstracts Service (a unique identifier for chemicals) - **DSL:** Domestic Substances List (a list of substances that were in commerce in Canada between 1984 and 1986) - **NDSL:** Non-Domestic Substances List (substances not on the DSL but may still be imported or manufactured in Canada) By understanding these components and abbreviations, workers can better navigate the complex world of hazardous materials management, ensuring a safer workplace environment. This knowledge empowers them to handle chemicals responsibly and respond effectively in emergency situations, aligning with the overarching goal of WHMIS: to protect workers' health and safety through accurate information and proper training.
Historical Context and Evolution
The acronym WHMIS, standing for Workplace Hazardous Materials Information System, has its roots deeply embedded in the historical context of occupational health and safety in Canada. The evolution of WHMIS reflects a significant shift in how hazardous materials are managed and communicated within workplaces. In the early 20th century, workplace safety was largely unregulated, leading to numerous accidents and health issues among workers. As industrialization accelerated, so did the awareness of the dangers posed by hazardous substances. By the mid-20th century, there was a growing consensus that comprehensive regulations were necessary to protect workers from chemical hazards. In 1985, the Canadian government introduced WHMIS as a national standard to ensure that workers were informed about the hazards of materials they worked with. This initiative was part of a broader movement towards better occupational health and safety standards, influenced by international best practices and advocacy from labor unions and health organizations. The initial WHMIS regulations mandated that suppliers of hazardous products provide Material Safety Data Sheets (MSDS) and labels to communicate critical safety information. Over the years, WHMIS has undergone significant updates to align with global standards and address emerging challenges. A major revision occurred in 2015 when Canada adopted the Globally Harmonized System of Classification and Labelling of Chemicals (GHS), an international standard developed by the United Nations. This transition from MSDS to Safety Data Sheets (SDS) and new labeling requirements enhanced the clarity and consistency of hazard communication across different countries. Today, WHMIS continues to evolve with technological advancements and changing workplace environments. Digital platforms now facilitate easier access to SDSs, and training programs are more comprehensive, incorporating both theoretical knowledge and practical skills. The integration of WHMIS into broader occupational health and safety frameworks underscores its importance as a cornerstone of workplace safety in Canada. As industries diversify and new chemical substances are introduced, WHMIS remains a dynamic system that adapts to these changes, ensuring that workers are equipped with the information they need to handle hazardous materials safely. This ongoing evolution underscores the commitment to protecting workers' health and safety while fostering a culture of safety awareness in Canadian workplaces.
Core Principles of WHMIS
The Workplace Hazardous Materials Information System (WHMIS) is a critical component of workplace safety in Canada, designed to protect workers from the dangers associated with hazardous materials. At its core, WHMIS operates on three fundamental principles: the classification of hazardous materials, labeling and signage requirements, and the role of Safety Data Sheets (SDS). Understanding these principles is essential for ensuring that workers are aware of the risks they face and know how to handle hazardous substances safely. The classification of hazardous materials helps identify the specific dangers posed by each substance, while labeling and signage requirements provide immediate visual warnings about potential hazards. Safety Data Sheets (SDS) serve as comprehensive resources that detail the safe handling, use, storage, and emergency procedures for each hazardous material. By grasping these key elements, individuals can better navigate the complexities of WHMIS and contribute to a safer work environment. This article will delve into each of these critical areas, providing a thorough understanding of the core principles of WHMIS and ultimately shedding light on what the acronym WHMIS truly represents.
Classification of Hazardous Materials
**Classification of Hazardous Materials** The classification of hazardous materials is a cornerstone of the Workplace Hazardous Materials Information System (WHMIS), a critical framework designed to ensure the safe handling, use, and disposal of hazardous substances in Canadian workplaces. Under WHMIS, hazardous materials are categorized based on their physical and health hazards, as well as their environmental impacts. This systematic approach helps employers, workers, and emergency responders understand the risks associated with these substances and take appropriate measures to mitigate them. Hazardous materials are broadly classified into two main categories: physical hazards and health hazards. Physical hazards include substances that can cause fires, explosions, or other immediate physical harm. These are further subdivided into six classes: Flammable Gases, Flammable Aerosols, Oxidizing Gases, Gases Under Pressure, Flammable Liquids, and Combustible Liquids. Each class has specific criteria and hazard statements that outline the potential risks and necessary precautions. Health hazards, on the other hand, encompass substances that can cause adverse health effects through inhalation, ingestion, or skin contact. These are categorized into nine classes: Toxic, Corrosive, Irritant, Sensitizer, Mutagen, Reproductive Toxicant, Respiratory Sensitizer, Aspiration Hazard, and Biohazardous Infectious Materials. For instance, toxic substances can cause harm through acute or chronic exposure, while corrosive materials can severely damage skin and other tissues upon contact. In addition to these primary classifications, WHMIS also considers environmental hazards. Substances that are harmful to aquatic life or can cause other environmental damage are labeled accordingly. This comprehensive classification system ensures that all stakeholders have a clear understanding of the potential risks posed by each hazardous material. The classification process involves detailed hazard assessments and the assignment of specific hazard statements and precautionary statements. Hazard statements describe the nature of the hazard, while precautionary statements provide advice on how to minimize or prevent adverse effects. This information is communicated through Safety Data Sheets (SDS) and labels on the hazardous materials themselves, ensuring that workers are well-informed and equipped to handle these substances safely. By categorizing hazardous materials in such a structured manner, WHMIS facilitates a culture of safety and compliance in workplaces across Canada. It empowers employers to implement effective safety protocols and training programs, while enabling workers to recognize and respond appropriately to potential hazards. This rigorous classification system is integral to the core principles of WHMIS, ensuring that hazardous materials are managed responsibly and that workplaces remain safe and healthy environments for all.
Labeling and Signage Requirements
Labeling and signage are critical components of the Workplace Hazardous Materials Information System (WHMIS), ensuring that workers are adequately informed about the hazards associated with the chemicals they handle. Under WHMIS, labeling requirements are stringent to guarantee that all hazardous products are clearly identified. Each label must include specific information: the product identifier, hazard statements, precautionary statements, and pictograms. The product identifier links the label to the Safety Data Sheet (SDS), which provides detailed information about the chemical's properties, hazards, and safe handling practices. Hazard statements describe the nature of the hazards posed by the chemical, while precautionary statements offer advice on how to minimize or prevent adverse effects. Pictograms, which are standardized symbols, visually communicate the type of hazard present, making it easier for workers to quickly identify potential dangers. Signage also plays a vital role in WHMIS compliance. Workplace signs must be used to identify areas where hazardous materials are stored or used, alerting workers to potential risks. These signs should be clear, legible, and placed in locations where they are easily visible. The use of standardized symbols and colors helps ensure consistency and clarity, reducing confusion and enhancing safety. For instance, warning signs might include symbols for flammability, toxicity, or corrosiveness, immediately alerting workers to specific hazards. Compliance with labeling and signage requirements is not only a legal mandate but also a cornerstone of workplace safety. Proper labeling and signage help prevent accidents by ensuring that workers are aware of the risks associated with the chemicals they handle. This awareness enables them to take necessary precautions, such as wearing appropriate personal protective equipment (PPE) or following specific handling procedures. Moreover, in the event of an emergency, clear labeling and signage facilitate quick identification of hazards, allowing for more effective response and mitigation strategies. In summary, labeling and signage under WHMIS are essential for maintaining a safe and informed workplace. By adhering to these requirements, employers can ensure that their workers are equipped with the knowledge needed to handle hazardous materials safely, thereby reducing the risk of injuries and illnesses. This aligns with the core principles of WHMIS, which emphasize the importance of providing accurate and accessible information about hazardous materials to protect worker health and safety.
Safety Data Sheets (SDS) and Their Role
Safety Data Sheets (SDS) are a cornerstone of the Workplace Hazardous Materials Information System (WHMIS), playing a crucial role in ensuring the safe handling, use, and disposal of hazardous materials in the workplace. These detailed documents provide essential information about the chemical composition, hazards, safe handling practices, emergency procedures, and regulatory requirements for each hazardous product. Under WHMIS, SDSs are mandated to be readily available to all workers who may be exposed to hazardous substances, thereby empowering them with the knowledge necessary to protect themselves and their colleagues. An SDS typically includes 16 sections, each addressing a specific aspect of the hazardous material. These sections cover everything from the identification of the substance and its manufacturer to first aid measures, fire-fighting procedures, accidental release measures, handling and storage guidelines, exposure controls, physical and chemical properties, stability and reactivity data, toxicological information, ecological information, disposal considerations, transport information, regulatory information, and other relevant details. This comprehensive approach ensures that workers have access to a single, reliable source of information that can guide their actions in both routine and emergency situations. The role of SDSs extends beyond mere compliance; they are integral to fostering a culture of safety within the workplace. By providing clear instructions on how to handle hazardous materials safely, SDSs help prevent accidents and reduce the risk of injuries and illnesses. For instance, knowing the proper personal protective equipment (PPE) to use when handling a particular chemical can significantly reduce exposure risks. Additionally, SDSs facilitate better communication among workers, supervisors, and emergency responders by standardizing the information provided about each hazardous substance. In alignment with the core principles of WHMIS—which include classifying hazardous products, labeling them appropriately, and providing safety data sheets and worker training—SDSs serve as a critical link between these elements. They bridge the gap between classification and labeling by providing detailed explanations of the hazards identified on product labels. Furthermore, SDSs support worker training by serving as a reference point for educational programs aimed at enhancing workplace safety awareness. In summary, Safety Data Sheets are indispensable tools within the WHMIS framework. They not only comply with regulatory requirements but also contribute significantly to creating a safer work environment by equipping workers with vital information about hazardous materials. As such, SDSs are a fundamental component of any effective workplace safety strategy, ensuring that all stakeholders are well-informed and prepared to handle hazardous substances responsibly.
Implementation and Compliance with WHMIS
The Workplace Hazardous Materials Information System (WHMIS) is a critical component of workplace safety in Canada, designed to protect workers from the dangers associated with hazardous materials. Effective implementation and compliance with WHMIS are paramount to ensuring a safe and healthy work environment. This article delves into the key aspects of WHMIS implementation, focusing on three essential areas: **Training and Education for Workers**, which highlights the importance of equipping employees with the knowledge to handle hazardous substances safely; **Workplace Safety Protocols and Procedures**, which outlines the necessary steps and guidelines for managing hazardous materials in the workplace; and **Regulatory Enforcement and Penalties**, which discusses the legal framework and consequences of non-compliance. By understanding these elements, employers and workers alike can better navigate the complexities of WHMIS, ultimately enhancing workplace safety. To fully grasp these concepts, it is crucial to start by **Understanding the Acronym WHMIS**.
Training and Education for Workers
Training and education are pivotal components in the implementation and compliance with the Workplace Hazardous Materials Information System (WHMIS). Effective training ensures that workers are well-equipped to handle hazardous materials safely, understand the risks associated with these substances, and know how to respond in emergency situations. A comprehensive training program should include detailed information about the classification of hazardous products, the interpretation of safety data sheets (SDSs), and the proper use of labels and pictograms. Workers must be taught how to identify and manage hazards, use personal protective equipment (PPE) correctly, and follow established safety protocols. Moreover, ongoing education is essential to keep workers updated on new regulations, emerging hazards, and best practices. This can be achieved through regular refresher courses, workshops, and on-the-job training sessions. Employers should also ensure that training materials are accessible and understandable for all employees, regardless of their language proficiency or literacy level. Interactive training methods such as simulations, role-playing scenarios, and hands-on exercises can enhance engagement and retention of critical safety information. Additionally, training programs should be tailored to the specific needs of different job roles within an organization. For instance, workers who handle hazardous materials directly may require more in-depth training compared to those who are less frequently exposed. Supervisors and managers also need specialized training to ensure they can effectively enforce WHMIS regulations and provide adequate support to their teams. Compliance with WHMIS requires not only initial training but also continuous monitoring and evaluation of worker knowledge. Employers must maintain records of all training activities and conduct regular assessments to identify any gaps in understanding or compliance. This proactive approach helps in maintaining a safe work environment where workers are confident in their ability to manage hazardous materials responsibly. In summary, robust training and education programs are the backbone of successful WHMIS implementation. By investing in comprehensive and ongoing training, employers can ensure that their workforce is well-prepared to handle hazardous materials safely, thereby reducing the risk of accidents and ensuring compliance with regulatory requirements. This commitment to worker safety not only protects employees but also contributes to a more efficient and productive workplace.
Workplace Safety Protocols and Procedures
Implementing and complying with Workplace Hazardous Materials Information System (WHMIS) protocols is crucial for ensuring a safe and healthy work environment. Workplace safety protocols and procedures are the backbone of any effective WHMIS compliance strategy. These protocols involve a comprehensive approach that includes training, labeling, material safety data sheets (MSDS), and personal protective equipment (PPE). Firstly, **training** is a cornerstone of workplace safety. Employees must be educated on the hazards associated with the chemicals they handle, how to read labels and MSDS, and how to use PPE correctly. Regular training sessions and refresher courses help maintain awareness and adherence to safety standards. This ensures that workers can identify potential hazards and take necessary precautions to mitigate risks. **Labeling** is another critical component. Chemicals must be labeled with standardized WHMIS symbols and information to alert workers of potential dangers. These labels provide immediate visual cues about the nature of the hazard, whether it is flammable, toxic, or corrosive, allowing workers to take appropriate precautions. **Material Safety Data Sheets (MSDS)**, now known as Safety Data Sheets (SDS), provide detailed information about each chemical product. These documents outline the chemical's properties, safe handling practices, emergency procedures, and first aid measures. Ensuring that SDS are readily available and easily accessible is essential for compliance and worker safety. **Personal Protective Equipment (PPE)** is vital for protecting workers from chemical hazards. Employers must ensure that appropriate PPE is provided and that employees understand its proper use. This includes gloves, goggles, respirators, and other protective gear tailored to the specific hazards present in the workplace. Additionally, **emergency response plans** must be in place to handle spills, leaks, or other incidents involving hazardous materials. These plans should include procedures for containment, cleanup, and evacuation if necessary. Regular drills and simulations help ensure that all employees are prepared to respond effectively in an emergency situation. Finally, **regular inspections and audits** are necessary to ensure ongoing compliance with WHMIS protocols. These checks help identify any gaps in training or procedures and allow for prompt corrective actions to be taken. By maintaining a culture of safety through continuous monitoring and improvement, organizations can significantly reduce the risk of workplace injuries and illnesses related to hazardous materials. In summary, implementing robust workplace safety protocols and procedures is essential for effective WHMIS compliance. Through comprehensive training, accurate labeling, accessible MSDS/SDS, appropriate PPE use, well-defined emergency response plans, and regular inspections, employers can create a safer work environment that protects both employees and the organization as a whole.
Regulatory Enforcement and Penalties
Regulatory enforcement and penalties are crucial components of ensuring compliance with the Workplace Hazardous Materials Information System (WHMIS). WHMIS, a Canadian standard for managing hazardous materials in the workplace, relies heavily on stringent enforcement mechanisms to protect workers and the environment. The primary regulatory bodies responsible for enforcing WHMIS include Health Canada and provincial/territorial occupational health and safety authorities. These agencies conduct regular inspections and audits to verify that employers are adhering to WHMIS requirements, such as proper labeling, material safety data sheets (MSDS), and employee training. Non-compliance can result in significant penalties. Employers who fail to implement WHMIS correctly may face fines, which can range from several thousand to hundreds of thousands of dollars depending on the severity of the violation. For instance, under the Canada Labour Code, fines for non-compliance can reach up to $1 million for corporations and $250,000 for individuals. Additionally, repeat offenders may face increased penalties, and in severe cases, criminal charges can be laid. These financial deterrents are designed to ensure that employers prioritize worker safety and take proactive steps to maintain a compliant workplace. Moreover, regulatory enforcement extends beyond financial penalties. Employers may also be required to take corrective actions, such as implementing new safety protocols or providing additional training to employees. In some cases, non-compliant workplaces may be subject to temporary or permanent shutdowns until the necessary corrections are made. The transparency and public disclosure of enforcement actions further serve as a deterrent, as companies risk damage to their reputation if found non-compliant. Employee participation is also a key aspect of regulatory enforcement. Workers have the right to report any WHMIS-related concerns or violations to their employers or regulatory authorities. This whistleblower protection ensures that employees feel empowered to speak up without fear of reprisal, thereby enhancing overall workplace safety. In summary, the robust enforcement framework and stringent penalties associated with WHMIS compliance underscore the importance of adhering to these regulations. By combining rigorous inspections, substantial fines, and corrective actions with employee participation, regulatory bodies ensure that workplaces remain safe and compliant with WHMIS standards. This comprehensive approach not only protects workers but also fosters a culture of safety and responsibility within Canadian workplaces.