What Is A Board Foot

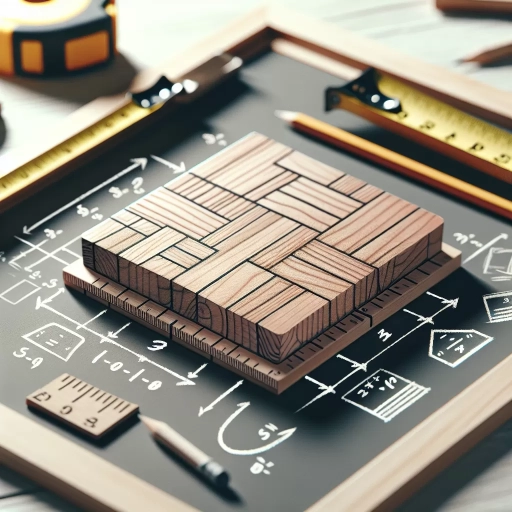
In the realm of woodworking, construction, and forestry, the term "board foot" is a crucial measurement that often sparks curiosity and confusion. A board foot is not just a unit of volume; it is a fundamental concept that underpins various aspects of these industries. To fully grasp its significance, it is essential to delve into the core of what a board foot represents. This article will explore the concept in depth, starting with **Understanding the Concept of a Board Foot**, where we will break down the definition and calculation methods. We will then move on to **Practical Applications of Board Feet**, highlighting how this measurement is used in real-world scenarios. Finally, we will address **Common Misconceptions and Best Practices**, providing clarity on frequent misunderstandings and offering tips for accurate usage. By the end of this journey, you will have a comprehensive understanding of the board foot, beginning with the foundational knowledge that sets the stage for its practical and nuanced applications. Let's start by understanding what a board foot truly is.
Understanding the Concept of a Board Foot
Understanding the concept of a board foot is crucial for anyone involved in woodworking, construction, or forestry. This unit of measurement, though often misunderstood, plays a significant role in quantifying lumber. To delve into its significance, it is essential to explore three key aspects: **Definition and Origin**, **Measurement and Calculation**, and **Historical Context**. By examining the definition and origin of the board foot, we can grasp its fundamental purpose and how it has evolved over time. Understanding how to measure and calculate board feet is vital for accurate estimations and efficient use of materials. Additionally, delving into the historical context provides insight into why this unit has endured despite modern alternatives. By combining these perspectives, we can gain a comprehensive understanding of the board foot, making it easier to navigate projects that require precise measurements and calculations. This article aims to provide a detailed exploration of these facets, ultimately leading to a deeper **Understanding of the Concept of a Board Foot**.
Definition and Origin
To fully grasp the concept of a board foot, it is essential to delve into its definition and origin. A board foot is a unit of measure used primarily in the lumber industry to quantify the volume of wood. It is defined as the volume of a piece of wood that is one foot long, one foot wide, and one inch thick. This standardized measurement allows for consistent and accurate calculations of wood quantities, which is crucial for both suppliers and consumers in the industry. The origin of the board foot dates back to the early days of woodworking and timber trading. Historically, wood was sold by the "board," which referred to a plank or board of wood. Over time, as trade and commerce evolved, there was a need for a more precise method to measure and price wood. The board foot emerged as a practical solution, providing a clear and uniform way to calculate the volume of wood regardless of its shape or size. This measurement system has been refined over centuries to ensure accuracy and fairness in transactions. For instance, if a piece of wood is 6 inches wide, 8 feet long, and 1 inch thick, it would be calculated as 4 board feet (since 6 inches is half of 12 inches, and thus half of a foot). This method simplifies complex calculations and helps in estimating costs, inventory management, and project planning. Understanding the definition and origin of a board foot not only highlights its practical application but also underscores its historical significance. It reflects how human ingenuity has adapted to the needs of trade and industry, creating standardized systems that facilitate efficiency and clarity. In the context of woodworking and construction, knowing what constitutes a board foot is fundamental for making informed decisions about materials, budgets, and project timelines. By appreciating this unit of measurement, individuals can better navigate the complexities of working with wood and ensure that their projects are executed with precision and accuracy.
Measurement and Calculation
Understanding the concept of a board foot is deeply rooted in the principles of measurement and calculation, which are fundamental to various fields such as carpentry, engineering, and architecture. Measurement is the process of determining the size, extent, or degree of something, while calculation involves the use of mathematical operations to derive quantitative results. In the context of lumber and wood products, precise measurements are crucial for accurate calculations, ensuring that materials are used efficiently and projects are completed correctly. When dealing with wood, measurements typically involve dimensions such as length, width, and thickness. These dimensions are often expressed in units like inches or feet. For instance, a piece of lumber might be described as 2 inches by 4 inches by 8 feet long. The calculation of a board foot—a unit of measure equal to a piece of wood that is 12 inches long, 12 inches wide, and 1 inch thick—requires careful consideration of these dimensions. To calculate the number of board feet in a given piece of lumber, one must multiply the length (in feet), width (in inches), and thickness (in inches), then divide by 12. For example, if you have a piece of wood that is 8 feet long, 6 inches wide, and 1 inch thick, you would first convert all dimensions to a consistent unit: 8 feet (length) remains as is; 6 inches (width) is already in inches; and 1 inch (thickness) is also in inches. Then, you multiply these values together: \(8 \times 6 \times 1 = 48\). Finally, you divide this product by 12 to get the total number of board feet: \(48 / 12 = 4\). This means that the piece of wood contains 4 board feet. The accuracy of these measurements and calculations is paramount because it directly affects project planning, material procurement, and cost estimation. Inaccurate measurements can lead to wasted materials or insufficient supplies, both of which can significantly impact project timelines and budgets. Therefore, understanding how to measure and calculate board feet is essential for anyone working with wood products, ensuring that projects are executed efficiently and effectively. In summary, measurement and calculation are integral components of understanding the concept of a board foot. By accurately measuring dimensions and performing precise calculations, individuals can determine the exact quantity of wood needed for any project. This not only aids in efficient resource allocation but also ensures that projects are completed with minimal waste and optimal results.
Historical Context
Understanding the concept of a board foot is deeply rooted in historical context, particularly within the evolution of woodworking and timber trade practices. The term "board foot" emerged as a standard unit of measurement in the early days of American forestry and woodworking, primarily during the 18th and 19th centuries. During this period, the demand for lumber skyrocketed due to rapid urbanization and industrialization. To facilitate efficient trade and ensure consistency, lumber merchants and woodworkers needed a reliable method to quantify wood. The board foot was born out of this necessity. It is defined as a unit of volume equal to a piece of wood that is 12 inches long, 12 inches wide, and one inch thick. This standardization allowed for easier calculation of wood quantities, making transactions more transparent and fair. Historically, the board foot was crucial for assessing the value of timber, determining labor costs, and planning construction projects accurately. In colonial America, the availability of vast forests made wood a primary building material. As settlements expanded, so did the need for standardized measurements to avoid disputes over quantities and quality. The board foot became an essential tool in this context, enabling craftsmen to communicate effectively about their materials and ensuring that builders could estimate their needs precisely. Moreover, the development of the board foot reflects broader economic and technological changes. The Industrial Revolution brought about advancements in sawmilling technology, which increased the efficiency of wood production. This led to a surge in the availability of lumber, further solidifying the board foot as a critical metric in the industry. Today, despite modern advancements in materials science and construction techniques, the board foot remains a fundamental unit in woodworking and forestry, serving as a testament to its enduring utility and historical significance. In summary, the concept of a board foot is not merely a technical term but a reflection of historical necessity and innovation. It has played a pivotal role in shaping the timber trade and continues to be an essential component in understanding wood quantities and values. By grasping this historical context, one can better appreciate the importance of the board foot in both past and present woodworking practices.
Practical Applications of Board Feet
In the realm of woodworking, construction, and the lumber industry, understanding the practical applications of board feet is crucial for efficient and accurate project planning. A board foot, a unit of measure representing a piece of wood that is 12 inches by 12 inches by 1 inch, is more than just a metric; it is a cornerstone for calculating material costs, estimating project requirements, and ensuring precision in various industries. This article delves into the multifaceted uses of board feet across three key sectors: the lumber industry, where it aids in inventory management and sales; construction and building projects, where it helps in budgeting and resource allocation; and woodworking and carpentry, where it enables craftsmen to create intricate designs with precision. By exploring these practical applications, readers will gain a deeper understanding of how board feet are integral to these fields. Ultimately, this knowledge will lead to a comprehensive grasp of the concept of a board foot, empowering professionals and hobbyists alike to make informed decisions in their respective endeavors. Understanding the Concept of a Board Foot is essential for anyone working with wood, and this article provides the foundational knowledge needed to master this critical metric.
Lumber Industry Uses
The lumber industry is a cornerstone of modern construction and manufacturing, leveraging the practical applications of board feet to ensure efficiency and precision. Board feet, a unit of measurement that quantifies the volume of lumber, are crucial for various aspects of the industry. In construction, board feet help builders and architects accurately estimate material costs and requirements for projects. This precision is essential for budgeting and planning, as it allows for the optimal use of resources without unnecessary waste or shortages. For instance, when building a house, knowing the exact amount of lumber needed in board feet enables contractors to order the right quantity, reducing both financial and environmental impacts. In addition to construction, the lumber industry relies on board feet for quality control and grading. Lumber mills use this measurement to categorize wood based on its dimensions and quality, ensuring that each piece meets specific standards. This process is vital for maintaining consistency in products such as flooring, paneling, and framing materials. Manufacturers can then confidently label their products with accurate measurements, which helps consumers make informed decisions about their purchases. The use of board feet also extends into the realm of sustainability and forestry management. By accurately measuring the volume of harvested timber, foresters can better manage forest resources and implement sustainable logging practices. This approach helps in maintaining healthy forests while ensuring a steady supply of lumber for future generations. Furthermore, understanding the volume of wood in board feet aids in the calculation of carbon sequestration and emissions, which is critical for environmental impact assessments. In the manufacturing sector, board feet play a pivotal role in the production of engineered wood products like plywood, oriented strand board (OSB), and glue-laminated timber (Glulam). These products are made from smaller pieces of wood that are pressed together to form larger sheets or beams. Accurate measurements in board feet are necessary to ensure that the raw materials are used efficiently and that the final products meet the required specifications. Moreover, the use of board feet facilitates international trade by providing a standardized unit of measurement that is widely recognized. This standardization simplifies transactions between suppliers and buyers across different regions, reducing misunderstandings and errors. It also enables the comparison of prices and quality across various markets, promoting fair competition and better value for consumers. In summary, the practical applications of board feet are multifaceted and indispensable within the lumber industry. From construction planning and quality control to sustainable forestry practices and international trade, board feet serve as a fundamental metric that ensures efficiency, accuracy, and consistency. As the demand for lumber continues to grow, the importance of understanding and utilizing board feet will only increase, underscoring their critical role in the industry's operations and future development.
Construction and Building Projects
In the realm of construction and building projects, understanding the concept of board feet is crucial for accurate material estimation, budgeting, and project planning. A board foot, defined as a unit of measure equal to a piece of wood that is 12 inches long, 12 inches wide, and 1 inch thick, plays a pivotal role in quantifying lumber needs. For instance, when constructing a house or a commercial building, architects and builders must meticulously calculate the amount of wood required for framing, flooring, and other structural elements. This calculation involves converting dimensions into board feet to ensure that the correct quantity of lumber is ordered and utilized efficiently. Practical applications of board feet are evident in various stages of construction. During the planning phase, architects use board feet to estimate the total cost of materials, helping clients set realistic budgets. For example, if a project requires 1,000 board feet of 2x4 lumber for framing, knowing the cost per board foot allows for precise financial planning. In the execution phase, contractors rely on these measurements to manage inventory and avoid overstocking or understocking materials. This precision also helps in minimizing waste and optimizing resource allocation. Moreover, understanding board feet facilitates better communication among stakeholders involved in the project. Builders can clearly specify their material requirements to suppliers, reducing errors in delivery and ensuring that projects stay on schedule. Additionally, this metric aids in comparing different types of wood based on their volume rather than just their dimensions, which is particularly useful when selecting materials with varying densities or grades. In terms of sustainability, accurate measurement using board feet can help in reducing environmental impact by minimizing excess material usage. By optimizing lumber requirements, builders can contribute to more efficient use of natural resources and lower their carbon footprint. Furthermore, this precision enables better adherence to building codes and regulations, ensuring that structures meet safety standards while also being environmentally responsible. In summary, the practical applications of board feet in construction and building projects are multifaceted and indispensable. From initial planning and budgeting to execution and sustainability considerations, this unit of measurement serves as a cornerstone for efficient and effective project management. By mastering the concept of board feet, professionals in the construction industry can streamline their processes, enhance productivity, and deliver high-quality results while maintaining environmental stewardship.
Woodworking and Carpentry
Woodworking and carpentry are ancient crafts that have evolved over centuries, leveraging the practical applications of board feet to create a wide range of functional and aesthetic pieces. At the heart of these disciplines lies the precise measurement and utilization of wood, with board feet serving as a fundamental unit of measurement. A board foot is a volume measurement equivalent to a piece of wood that is 12 inches long, 12 inches wide, and 1 inch thick. This standardization allows woodworkers and carpenters to accurately calculate the amount of material needed for various projects, ensuring efficiency and minimizing waste. In woodworking, the application of board feet is crucial for planning intricate furniture pieces, cabinetry, and other decorative items. For instance, when crafting a custom dining table, a woodworker must calculate the total board feet required for the tabletop, legs, and any additional features like drawers or shelves. This calculation helps in selecting the right type and quantity of wood, whether it be hardwoods like oak or maple, or softwoods such as pine or fir. The precision in measurement ensures that the final product meets the desired specifications without unnecessary excess material. Carpentry, on the other hand, involves more structural applications where board feet are essential for estimating lumber needs for building frames, walls, floors, and roofs. In residential construction, carpenters use board feet to determine how much lumber is required for framing a house or installing decking. This measurement helps in budgeting and scheduling projects accurately, as it directly influences the cost and availability of materials. For example, when building a deck, knowing the total board feet needed for the joists, beams, and planks ensures that the project stays within budget and timeline. Beyond these practical applications, understanding board feet also enhances creativity in woodworking and carpentry. With a clear grasp of material quantities, artisans can experiment with different designs and techniques without worrying about running out of material mid-project. This freedom allows for innovative approaches to traditional crafts, leading to unique pieces that blend functionality with artistic expression. Moreover, the use of board feet promotes sustainability in woodworking and carpentry by encouraging efficient use of resources. By accurately measuring and planning projects, woodworkers and carpenters can reduce waste significantly. This not only saves money but also contributes to environmental conservation by minimizing the demand on forests and reducing the amount of wood that ends up in landfills. In conclusion, the concept of board feet is a cornerstone in both woodworking and carpentry, enabling practitioners to execute their craft with precision, efficiency, and creativity. Whether it's crafting a piece of furniture or building a house, understanding and applying board feet ensures that projects are completed successfully while respecting the value of this precious resource.
Common Misconceptions and Best Practices
In the realm of measurement and project management, understanding key concepts is crucial for accuracy and efficiency. However, several common misconceptions often hinder effective practice. This article aims to clarify these misunderstandings and provide best practices, focusing on three critical areas: **Common Errors in Measurement**, **Conversion to Other Units**, and **Efficient Use in Projects**. By addressing these topics, we will delve into the nuances that can significantly impact the outcome of any project. Common errors in measurement can lead to costly mistakes, while proper conversion between units is essential for maintaining consistency. Additionally, understanding how to use measurements efficiently can streamline project workflows. These insights are particularly relevant when it comes to **Understanding the Concept of a Board Foot**, a fundamental unit in various industries that requires precise handling to avoid errors and ensure optimal results. By exploring these aspects, this article will equip readers with the knowledge necessary to navigate measurement challenges with confidence and accuracy.
Common Errors in Measurement
When dealing with measurements, particularly in the context of lumber and wood products, common errors can lead to significant discrepancies and misunderstandings. One of the most prevalent mistakes is the confusion between nominal and actual dimensions. For instance, a 2x4 piece of lumber is often assumed to be exactly 2 inches by 4 inches, but in reality, it typically measures 1.5 inches by 3.5 inches due to planing and drying processes. This discrepancy can result in miscalculations when estimating material needs or costs. Another error involves the misuse of units, especially when converting between different systems. For example, mixing up feet with inches or failing to account for the differences between board feet and linear feet can lead to substantial errors in measurement. A board foot is a unit of volume equal to a piece of wood that is 12 inches long, 12 inches wide, and 1 inch thick; however, many individuals mistakenly use it interchangeably with linear feet, which measure length alone. Additionally, neglecting to consider the moisture content of wood can also introduce measurement errors. Wood shrinks and expands based on its moisture content, so measurements taken at different times or under different conditions may not be consistent. This is particularly relevant when working with green lumber versus kiln-dried lumber. Furthermore, human error during the measurement process itself is a common issue. Misreading tape measures, failing to account for fractions or decimals accurately, and not using calibrated tools can all contribute to inaccuracies. It is crucial to double-check measurements and ensure that all tools are properly calibrated to avoid these pitfalls. Best practices to mitigate these errors include using precise terminology and understanding the specific dimensions and units involved. Always verify the actual dimensions of materials rather than relying on nominal sizes. When converting between units, use reliable conversion factors and double-check calculations. Regularly calibrate measuring tools and ensure that all measurements are taken under consistent conditions to minimize variability due to environmental factors. By being aware of these common errors and adhering to best practices, individuals can significantly improve the accuracy of their measurements and avoid costly mistakes in projects involving wood and other materials. This attention to detail not only enhances the quality of work but also fosters a more efficient and cost-effective process overall.
Conversion to Other Units
When discussing the concept of a board foot, it is crucial to address the common misconceptions and best practices surrounding its measurement and conversion. One of the key areas where confusion often arises is in the conversion to other units. A board foot is a unit of volume, specifically 12 inches by 12 inches by 1 inch (or 144 cubic inches), but it can be challenging to translate this into more familiar units such as cubic feet or square feet. To clarify, a board foot does not equate to a square foot; rather, it represents a volume measurement. For instance, if you have a piece of lumber that is 4 feet long, 6 inches wide, and 1 inch thick, calculating its volume in board feet involves multiplying the length by the width (in feet) and then by the thickness (in inches). This example would yield 2 board feet (4 ft * 0.5 ft * 1 in). Converting board feet to cubic feet is straightforward: since there are 12 board feet in a cubic foot (because 12 inches * 12 inches * 1 inch = 144 cubic inches, which is one-twelfth of a cubic foot), you simply divide the number of board feet by 12. For example, 24 board feet would be equivalent to 2 cubic feet. Another common misconception is that converting between different types of lumber measurements requires complex calculations. However, understanding the basic principles can simplify these conversions significantly. For example, if you need to convert from linear feet (the length of the lumber) to board feet, you must know the dimensions of the lumber's cross-section. Best practices include always double-checking your calculations and ensuring that all measurements are in consistent units before performing conversions. Additionally, using conversion charts or calculators can help avoid errors and streamline the process. In summary, converting between units related to board feet requires a clear understanding of volume measurements and consistent application of conversion factors. By recognizing that a board foot is a volume unit distinct from area units like square feet and by following best practices such as double-checking calculations and using conversion tools, you can accurately navigate these conversions and avoid common misconceptions. This precision is essential for accurate planning and execution in woodworking and construction projects where material quantities are critical.
Efficient Use in Projects
Efficient use in projects is a critical aspect that often gets overlooked, leading to common misconceptions about what truly constitutes effective project management. One of the most prevalent misconceptions is the belief that efficiency equates to cutting corners or reducing quality. However, true efficiency involves optimizing resources, streamlining processes, and ensuring that every element of the project contributes to its overall success. In the context of woodworking and carpentry, where the concept of a board foot is central, efficient use can significantly impact both cost and quality. A board foot is a unit of measure equal to a piece of wood that is 12 inches long, 12 inches wide, and one inch thick. Misconceptions arise when project managers fail to accurately calculate the required amount of lumber, leading to either excessive waste or insufficient material. Best practices dictate that precise measurements and detailed planning are essential to avoid such pitfalls. For instance, using software tools to create detailed project plans and 3D models can help identify potential inefficiencies early on. Additionally, adopting a "design for manufacturability" approach ensures that the design is optimized for the materials and tools available, reducing waste and improving overall efficiency. Another key aspect is the selection of materials. Choosing lumber that is sustainably sourced and of appropriate quality can reduce waste and minimize the environmental impact of the project. Furthermore, implementing lean principles such as just-in-time delivery and minimizing inventory can help reduce costs associated with storage and handling. Effective communication among team members is also crucial for efficient project execution. Clear instructions and regular updates can prevent misunderstandings that lead to inefficiencies. Regular audits and feedback loops ensure that any deviations from the plan are quickly identified and addressed. In summary, efficient use in projects involves a holistic approach that includes accurate planning, optimal resource allocation, and continuous improvement. By dispelling common misconceptions and adhering to best practices, project managers can ensure that their projects are completed on time, within budget, and to the desired quality standards. This not only enhances the project's success but also contributes to a more sustainable and responsible use of resources.