What Is Rtv Silicone

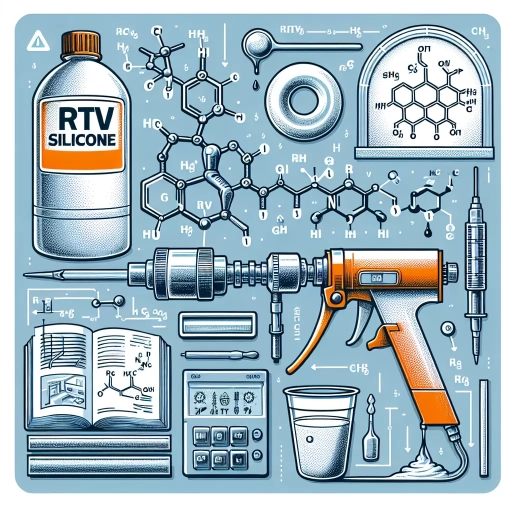
RTV silicone, or room temperature vulcanizing silicone, is a versatile and widely used material that has garnered significant attention across various industries due to its unique properties and diverse applications. This article delves into the essence of RTV silicone, exploring its fundamental characteristics, its distinctive properties, and the practical uses that make it an indispensable component in modern manufacturing and everyday life. We will begin by introducing RTV silicone, explaining what it is and how it is produced. This foundational understanding will then be expanded upon by examining the properties and characteristics that set RTV silicone apart from other materials, including its flexibility, durability, and resistance to extreme temperatures. Finally, we will discuss the practical uses and benefits of RTV silicone, highlighting its role in fields such as electronics, automotive, and construction. By the end of this article, readers will have a comprehensive grasp of RTV silicone's significance and its multifaceted applications. Let us start with an **Introduction to RTV Silicone**, where we uncover the basics of this remarkable material.
Introduction to RTV Silicone
RTV (Room Temperature Vulcanizing) silicone is a versatile and widely used material that has revolutionized various industries with its unique properties and applications. This article provides a comprehensive introduction to RTV silicone, delving into its definition and composition, historical development and evolution, and common applications and uses. To begin, understanding the definition and composition of RTV silicone is crucial. It is a type of silicone rubber that cures at room temperature, typically through a chemical reaction initiated by exposure to air. This process allows for easy handling and application without the need for high-temperature curing ovens, making it highly accessible for both industrial and DIY projects. The historical development and evolution of RTV silicone are also noteworthy. Since its inception, RTV silicone has undergone significant advancements in terms of performance, durability, and versatility. From its early use in sealants and adhesives to its current applications in aerospace, automotive, and medical fields, RTV silicone has continuously adapted to meet the demands of modern technology. In addition to its rich history, RTV silicone finds extensive use across various sectors due to its excellent thermal stability, flexibility, and resistance to chemicals and weathering. Common applications include sealing joints in construction, insulating electrical components, and creating molds for casting. Transitioning to the core of what makes RTV silicone so valuable, we will first explore its **Definition and Composition**, which lays the foundation for understanding its properties and capabilities.
Definition and Composition
**Definition and Composition** RTV (Room Temperature Vulcanization) silicone is a versatile and widely used elastomeric material that undergoes curing at ambient temperatures, typically between 20°C to 30°C. This unique property allows RTV silicone to be applied in various environments without the need for specialized heating equipment, making it highly convenient for both industrial and consumer applications. The term "vulcanization" refers to the chemical process that transforms the liquid silicone into a solid, flexible rubber-like material. This transformation is usually initiated by the presence of a catalyst, which reacts with the silicone polymer to form cross-links between the molecular chains, thereby enhancing the material's mechanical properties. The composition of RTV silicone typically includes a base polymer, a cross-linking agent, and various additives such as catalysts, fillers, and pigments. The base polymer is usually a polydimethylsiloxane (PDMS) or a similar siloxane-based compound, which provides the inherent flexibility and durability of the silicone. Cross-linking agents, such as organotin compounds or platinum-based catalysts, are crucial for initiating the vulcanization process. Fillers like silica or calcium carbonate may be added to improve the mechanical strength and thermal stability of the final product. Pigments can also be included to achieve specific colors for aesthetic purposes. The curing process of RTV silicone can be either condensation-based or addition-based, depending on the type of cross-linking agent used. Condensation-cure RTV silicones release by-products such as acetic acid or ethanol during the curing process, while addition-cure RTV silicones do not release any by-products, making them more suitable for applications where cleanliness is critical. This versatility in curing mechanisms allows RTV silicone to be tailored for a wide range of applications, from sealants and adhesives in construction and automotive industries to encapsulants in electronics and medical devices. In addition to its ease of application and diverse range of formulations, RTV silicone offers several advantageous properties that contribute to its widespread use. These include excellent thermal stability over a broad temperature range, good electrical insulation, and resistance to chemicals and UV light. Furthermore, RTV silicones exhibit low toxicity and are generally considered safe for use in food contact applications and medical devices, subject to regulatory approvals. Overall, the definition and composition of RTV silicone underscore its adaptability and performance across various sectors. Its ability to cure at room temperature, combined with its robust mechanical and chemical properties, makes it an indispensable material in modern manufacturing and engineering practices. Whether used as a sealant, adhesive, or encapsulant, RTV silicone continues to play a vital role in ensuring the reliability and longevity of products in diverse industries.
Historical Development and Evolution
The historical development and evolution of RTV (Room Temperature Vulcanizing) silicone are deeply intertwined with advancements in materials science and the growing demand for versatile, high-performance sealants. The journey began in the early 20th century when silicones were first synthesized by Frederick Kipping in 1901. Initially, these early silicones were not suitable for practical applications due to their instability and limited properties. However, the breakthrough came in the 1940s when Eugene G. Rochow developed a method to synthesize methyl silicones, laying the groundwork for modern silicone technology. In the post-war era, the development of RTV silicones accelerated significantly. By the 1950s, chemists had discovered ways to create silicones that could cure at room temperature, a critical innovation that expanded their utility beyond traditional industrial settings. These early RTV silicones were primarily used in aerospace and automotive industries for sealing and bonding applications due to their excellent thermal stability, flexibility, and resistance to chemicals. The 1960s and 1970s saw further refinement in RTV silicone formulations, leading to improved mechanical properties and broader compatibility with various substrates. This period also witnessed the introduction of different types of RTV silicones, such as one-component (1K) and two-component (2K) systems, each offering distinct advantages depending on the application. One-component RTV silicones, which cure upon exposure to moisture in the air, became popular for their ease of use and convenience. Two-component systems, requiring a catalyst for curing, offered faster curing times and higher strength. The advent of new catalysts and additives in the 1980s and 1990s further enhanced the performance characteristics of RTV silicones. These advancements included improved adhesion promoters, UV stabilizers, and fillers that enhanced durability and reduced costs. This era also saw a significant expansion of RTV silicone applications into consumer goods, construction materials, and medical devices. In recent years, the evolution of RTV silicones has been driven by environmental concerns and regulatory changes. The development of low-VOC (volatile organic compound) and eco-friendly formulations has become a priority, ensuring that these materials meet stringent environmental standards without compromising their performance. Additionally, advancements in nanotechnology have led to the creation of nano-filled RTV silicones with enhanced mechanical properties and thermal conductivity. Today, RTV silicones are ubiquitous across various industries, from electronics and healthcare to automotive and construction. Their versatility, combined with continuous innovation in formulation and application techniques, ensures that they remain a cornerstone in modern engineering and manufacturing. As technology continues to evolve, it is likely that RTV silicones will play an even more critical role in addressing future challenges related to sustainability, durability, and performance. This rich historical development underscores the importance of RTV silicones as a cornerstone material in contemporary engineering and manufacturing practices.
Common Applications and Uses
RTV (Room Temperature Vulcanizing) silicone, a versatile and widely used material, finds its applications across various industries due to its unique properties such as flexibility, durability, and resistance to extreme temperatures. One of the most common applications of RTV silicone is in the realm of sealants and adhesives. It is frequently used in construction to seal joints and gaps in buildings, ensuring weatherproofing and structural integrity. Its ability to maintain elasticity over a wide temperature range makes it an ideal choice for sealing windows, doors, and other exterior components. In the automotive sector, RTV silicone plays a crucial role in gasketing and sealing engine components. It is used to create seals that can withstand the high temperatures and pressures within an engine, thereby preventing leaks and ensuring optimal performance. Additionally, RTV silicone is utilized in the production of various automotive parts such as hoses, belts, and other rubber components due to its excellent thermal stability and resistance to oils and fuels. The electronics industry also benefits significantly from RTV silicone. It is used as a potting compound to encapsulate electronic components, providing them with protection against moisture, dust, and mechanical stress. This ensures the reliability and longevity of electronic devices even in harsh environments. Furthermore, RTV silicone's dielectric properties make it suitable for use in electrical insulation applications. In medical and healthcare settings, RTV silicone is valued for its biocompatibility and non-toxic nature. It is used in the manufacture of medical devices such as implants, catheters, and wound dressings. Its flexibility and softness make it an excellent material for creating prosthetic devices that mimic human tissue. Moreover, RTV silicone has found its way into consumer goods such as kitchen utensils, cookware, and bakeware due to its heat resistance and non-stick properties. It is also used in the production of baby products like pacifiers and bottle nipples because of its safety and durability. In the realm of arts and crafts, RTV silicone is popular among sculptors and model makers. It can be molded into intricate shapes and forms, making it an ideal material for creating prototypes or final products that require detailed precision. Lastly, RTV silicone's environmental benefits should not be overlooked. It is often used in green building projects as a sustainable alternative to traditional sealants and adhesives. Its ability to reduce air leakage and improve energy efficiency contributes significantly to energy conservation efforts. In summary, the versatility of RTV silicone makes it a staple material across diverse industries. From construction and automotive to electronics, healthcare, consumer goods, arts, and sustainable building practices, its unique properties ensure that it remains a highly sought-after material for a wide range of applications.
Properties and Characteristics of RTV Silicone
RTV (Room Temperature Vulcanizing) silicone is a versatile and widely used material, renowned for its unique properties and characteristics that make it indispensable in various industrial and consumer applications. This article delves into the multifaceted nature of RTV silicone, exploring three key aspects that contribute to its popularity: its chemical and physical properties, its thermal and electrical insulation capabilities, and its flexibility and durability. Firstly, the chemical and physical properties of RTV silicone are foundational to its performance. These properties include its molecular structure, viscosity, and curing mechanisms, which determine its strength, adhesion, and resistance to environmental factors. Understanding these properties is crucial for selecting the right type of RTV silicone for specific uses. Secondly, RTV silicone's thermal and electrical insulation capabilities make it an excellent choice for applications requiring protection against heat and electrical currents. Its ability to maintain integrity under varying temperatures and its non-conductive nature ensure safe and efficient operation in diverse settings. Lastly, the flexibility and durability of RTV silicone allow it to withstand mechanical stress and maintain its form over time. This combination of flexibility and durability makes it ideal for sealing, bonding, and coating in both static and dynamic environments. In this article, we will begin by examining the **Chemical and Physical Properties** of RTV silicone, laying the groundwork for a comprehensive understanding of this material's broad range of applications.
Chemical and Physical Properties
Chemical and physical properties are fundamental aspects that define the characteristics and applications of RTV (Room Temperature Vulcanizing) silicone. RTV silicone, a type of elastomer, exhibits a unique combination of properties that make it versatile and widely used in various industries. **Chemically**, RTV silicone is known for its excellent resistance to chemicals, including oils, fuels, and cleaning agents. This is due to its stable molecular structure, which is less reactive and more durable compared to other polymers. Additionally, RTV silicone has a high degree of thermal stability, maintaining its integrity over a wide temperature range from -50°C to 250°C, making it suitable for applications in extreme environments. **Physically**, RTV silicone is characterized by its flexibility and elasticity. It can be formulated to have different hardness levels, typically measured on the Shore A scale, allowing it to be used in applications requiring varying degrees of rigidity. The material also possesses excellent electrical insulation properties, making it a preferred choice for electrical components and sealants. Furthermore, RTV silicone has a low modulus of elasticity, which means it can absorb vibrations and shocks effectively, contributing to its use in damping and cushioning applications. Another significant physical property of RTV silicone is its adhesion to various substrates. It can bond well with metals, plastics, and other materials, enhancing its utility as a sealant and adhesive. The material's low shrinkage during curing ensures that it maintains its shape and integrity over time, which is crucial for maintaining seals and bonds in critical applications. Moreover, RTV silicone is generally non-toxic and hypoallergenic, making it safe for use in medical devices and food contact applications. The curing process of RTV silicone is also noteworthy. Unlike other elastomers that require high temperatures or pressures to cure, RTV silicone cures at room temperature through a condensation or addition reaction. This ease of curing makes it convenient for on-site applications and reduces the need for specialized equipment. The curing process can be accelerated or slowed down depending on the specific formulation and environmental conditions, providing flexibility in manufacturing and application processes. In summary, the chemical and physical properties of RTV silicone—such as its chemical resistance, thermal stability, flexibility, electrical insulation, adhesion capabilities, and ease of curing—make it an indispensable material across diverse industries including construction, automotive, electronics, and healthcare. These properties collectively contribute to the robust performance and reliability of RTV silicone in various applications, solidifying its position as a versatile and reliable material in modern technology.
Thermal and Electrical Insulation Capabilities
Thermal and electrical insulation capabilities are crucial aspects of RTV (Room Temperature Vulcanizing) silicone, making it a versatile material in various industrial and consumer applications. RTV silicone's unique properties allow it to effectively insulate against both thermal and electrical energy, enhancing safety, efficiency, and performance in diverse settings. **Thermal Insulation:** RTV silicone exhibits excellent thermal insulation characteristics due to its low thermal conductivity. This means it can efficiently reduce heat transfer between different components or environments, making it ideal for applications where temperature control is critical. For instance, in electronics, RTV silicone can be used to encapsulate components, protecting them from extreme temperatures and ensuring stable operation. In construction, it can be applied as a sealant around windows and doors to minimize heat loss during winter and heat gain during summer, thereby improving energy efficiency and reducing energy costs. **Electrical Insulation:** The electrical insulation properties of RTV silicone are equally impressive. With a high dielectric strength and low dielectric constant, RTV silicone acts as an effective barrier against electrical currents. This makes it a preferred choice for insulating electrical components such as wires, connectors, and circuit boards. In high-voltage applications, RTV silicone's ability to withstand electrical stress without failing ensures reliable operation and safety. Additionally, its flexibility allows it to conform to complex shapes, providing comprehensive protection against electrical discharges. **Combined Benefits:** The combination of thermal and electrical insulation capabilities in RTV silicone offers significant advantages. For example, in automotive applications, RTV silicone can be used to seal and insulate electrical connectors exposed to harsh environmental conditions, protecting them from both temperature extremes and electrical surges. Similarly, in aerospace engineering, RTV silicone's dual insulation properties are invaluable for ensuring the reliability of critical electronic systems under extreme temperatures and electrical stresses. **Durability and Flexibility:** A key factor contributing to the effectiveness of RTV silicone as an insulator is its durability and flexibility. Unlike rigid insulators that may crack or break under stress, RTV silicone remains flexible even after curing, allowing it to absorb vibrations and movements without compromising its insulation properties. This flexibility also makes it easier to apply and ensures a tight seal around irregularly shaped components. **Chemical Resistance:** Another important aspect of RTV silicone's insulation capabilities is its chemical resistance. It remains stable when exposed to a wide range of chemicals, including fuels, oils, and cleaning agents, which is particularly beneficial in industrial settings where exposure to such substances is common. This resistance helps maintain the integrity of the insulation over time, ensuring consistent performance. In summary, the thermal and electrical insulation capabilities of RTV silicone make it an indispensable material across various industries. Its ability to provide effective insulation against both heat and electricity, combined with its durability, flexibility, and chemical resistance, positions RTV silicone as a go-to solution for enhancing safety, efficiency, and reliability in numerous applications. Whether used in electronics, construction, automotive, or aerospace engineering, RTV silicone's insulation properties play a critical role in ensuring optimal performance and longevity of systems and components.
Flexibility and Durability
Flexibility and durability are two of the most compelling properties of RTV (Room Temperature Vulcanizing) silicone, making it a versatile material for a wide range of applications. RTV silicone's flexibility is rooted in its molecular structure, which allows it to maintain elasticity over a broad temperature range. This inherent flexibility enables RTV silicone to absorb vibrations, withstand mechanical stress, and adapt to changing environmental conditions without losing its integrity. For instance, in automotive applications, RTV silicone seals can flex with the movement of engine components, ensuring a tight seal even under dynamic conditions. Similarly, in construction, RTV silicone sealants can accommodate the expansion and contraction of building materials due to temperature fluctuations, thereby preventing cracks and leaks. Durability is another hallmark of RTV silicone, stemming from its robust chemical composition and cross-linking process. Once cured, RTV silicone forms a strong three-dimensional network that resists degradation from exposure to various chemicals, UV light, and extreme temperatures. This durability ensures that RTV silicone products remain effective over long periods, reducing the need for frequent replacements or repairs. In industrial settings, RTV silicone coatings and sealants protect equipment from corrosive substances and harsh environmental conditions, extending the lifespan of machinery and reducing maintenance costs. Additionally, in medical devices and consumer products, the durability of RTV silicone ensures consistent performance and safety, as it maintains its physical properties even when subjected to repeated use and cleaning. The combination of flexibility and durability makes RTV silicone an ideal choice for applications where both mechanical resilience and long-term reliability are crucial. For example, in electronics, RTV silicone encapsulants protect sensitive components from physical shock and environmental stressors while maintaining their electrical insulation properties. In aerospace, RTV silicone sealants and adhesives are used to bond and seal critical components that must withstand extreme temperatures and mechanical loads. The synergy between flexibility and durability in RTV silicone thus enhances its overall performance, making it a preferred material across diverse industries where reliability and longevity are paramount. Moreover, the flexibility and durability of RTV silicone are often enhanced through the addition of fillers and additives that tailor its properties to specific needs. For instance, incorporating reinforcing fillers can further improve the mechanical strength of RTV silicone, while UV stabilizers can enhance its resistance to ultraviolet light degradation. This ability to customize the material's properties allows engineers and manufacturers to optimize RTV silicone for a variety of demanding applications, from high-performance industrial uses to everyday consumer products. In summary, the flexibility and durability of RTV silicone are fundamental characteristics that underpin its widespread adoption across various sectors. These properties not only ensure the material's ability to withstand diverse environmental and mechanical challenges but also contribute to its long-term reliability and performance. As technology continues to evolve, the unique blend of flexibility and durability in RTV silicone will remain a cornerstone of its appeal, driving innovation and application in an ever-expanding array of fields.
Practical Uses and Benefits of RTV Silicone
RTV (Room Temperature Vulcanizing) silicone is a versatile and highly beneficial material that finds extensive use across various sectors due to its unique properties. Its flexibility, durability, and resistance to extreme temperatures make it an indispensable component in industrial manufacturing processes. In the industrial sphere, RTV silicone is crucial for sealing, bonding, and protecting equipment from harsh environments. Beyond its industrial applications, RTV silicone also plays a significant role in medical and healthcare settings, where its biocompatibility and sterilizability make it ideal for medical devices and implants. Additionally, its ease of use and availability have made it a favorite among DIY enthusiasts and consumers, who utilize it for a wide range of projects from home repairs to crafting. This article will delve into these practical uses and benefits, starting with the critical role RTV silicone plays in industrial applications in manufacturing. By exploring these diverse applications, we can fully appreciate the value and versatility of this remarkable material.
Industrial Applications in Manufacturing
In the realm of manufacturing, industrial applications play a crucial role in enhancing efficiency, reliability, and product quality. One material that has revolutionized various industrial processes is RTV (Room Temperature Vulcanizing) silicone. This versatile elastomer is widely utilized due to its unique properties, such as flexibility, thermal stability, and excellent sealing capabilities. In manufacturing, RTV silicone finds practical uses in several key areas. Firstly, **sealing and bonding** are among the most common applications. RTV silicone sealants are used to create durable seals in machinery and equipment, ensuring that fluids and gases do not leak out or contaminants do not enter. This is particularly important in industries like automotive, aerospace, and chemical processing where tight seals are critical for safety and performance. Additionally, RTV silicone adhesives are employed to bond a variety of materials including metals, plastics, and ceramics, offering a strong yet flexible joint that can withstand thermal expansion and contraction. Another significant application is in **electrical insulation**. RTV silicone's excellent dielectric properties make it an ideal material for insulating electrical components. It is used to coat electrical wires, connectors, and other components to protect them from moisture, dust, and other environmental factors that could compromise their functionality. This is especially vital in industries such as electronics and telecommunications where reliable electrical insulation is paramount. **Thermal management** is another area where RTV silicone excels. Its high thermal stability allows it to maintain its integrity over a wide temperature range, making it suitable for applications involving heat transfer or thermal protection. For instance, RTV silicone is used in the production of thermal interfaces for electronic devices, ensuring efficient heat dissipation and preventing overheating. Furthermore, RTV silicone's **chemical resistance** makes it invaluable in chemical processing and pharmaceutical industries. It is used to line tanks, pipes, and other equipment to protect against corrosive substances. This not only extends the lifespan of the equipment but also ensures the purity of the products being processed. In **molding and casting**, RTV silicone is used to create molds for casting parts from various materials such as metals, plastics, and resins. Its flexibility allows for easy demolding without damaging the part, and its chemical inertness prevents contamination of the cast material. Lastly, **vibration damping** and **noise reduction** are additional benefits of using RTV silicone in manufacturing. Its viscoelastic properties enable it to absorb vibrations and reduce noise levels in machinery, contributing to a quieter and more stable operational environment. In summary, the practical uses and benefits of RTV silicone in manufacturing are multifaceted and far-reaching. From sealing and bonding to electrical insulation, thermal management, chemical resistance, molding, and vibration damping, RTV silicone enhances the performance, reliability, and safety of industrial processes across various sectors. Its unique combination of properties makes it an indispensable material in modern manufacturing practices.
Medical and Healthcare Uses
RTV (Room Temperature Vulcanizing) silicone has carved out a significant niche in the medical and healthcare sectors due to its unique properties and versatility. One of the primary reasons for its widespread adoption is its biocompatibility, which ensures that it does not react with bodily tissues or fluids, making it an ideal material for medical devices. For instance, RTV silicone is often used in the production of implantable devices such as pacemakers, cochlear implants, and joint replacements. Its flexibility and durability allow these devices to withstand the rigors of long-term use within the human body without causing adverse reactions. In addition to implantable devices, RTV silicone plays a crucial role in wound care. It is used to create flexible wound dressings that promote healing by maintaining a moist environment while protecting the wound from external contaminants. These dressings are particularly beneficial for chronic wounds, such as diabetic ulcers, where traditional dressings may not be as effective. The breathable nature of RTV silicone also helps in reducing the risk of infection and promotes faster recovery times. Another significant application of RTV silicone in healthcare is in the field of prosthetics and orthotics. The material's ability to mimic the natural texture and flexibility of human skin makes it an excellent choice for creating realistic prosthetic limbs. Moreover, RTV silicone can be formulated to match the specific needs of individual patients, providing a customized fit that enhances comfort and mobility. In medical diagnostics, RTV silicone is used in the manufacture of various diagnostic tools such as ultrasound probes and medical tubing. Its non-reactive nature ensures that it does not interfere with test results, while its flexibility allows for precise maneuverability during procedures. Furthermore, RTV silicone's resistance to sterilization methods like autoclaving makes it a reliable choice for reusable medical equipment. The use of RTV silicone extends into dental applications as well. It is commonly used in dental impression materials due to its ability to capture detailed impressions of teeth and gums accurately. This precision is critical for creating accurate dental restorations such as crowns, bridges, and dentures. In summary, the practical uses and benefits of RTV silicone in medical and healthcare are multifaceted. Its biocompatibility, flexibility, durability, and resistance to sterilization make it an indispensable material across various medical applications. From implantable devices and wound care to prosthetics and diagnostics, RTV silicone continues to play a vital role in enhancing patient outcomes and improving healthcare delivery. Its versatility and reliability have solidified its position as a cornerstone material in modern medical technology.
DIY and Consumer Projects
When it comes to DIY and consumer projects, RTV (Room Temperature Vulcanizing) silicone is a versatile and indispensable material that offers a wide range of practical uses and benefits. For hobbyists, DIY enthusiasts, and homeowners, RTV silicone provides an easy-to-use solution for various tasks, from sealing gaps and joints to creating molds and prototypes. One of the primary advantages of RTV silicone is its ease of application; it can be applied directly from the tube or mixed with a catalyst for more complex projects. This flexibility makes it ideal for sealing leaks around windows, doors, and pipes, ensuring energy efficiency and preventing water damage. In crafting and art projects, RTV silicone serves as an excellent mold-making material. Artists can create intricate molds for casting resin, plaster, or even concrete, allowing for precise replication of designs. The non-stick properties of cured RTV silicone make it easy to release the cast object without damaging the mold or the final product. Additionally, its durability ensures that the mold can be reused multiple times, making it a cost-effective option for repetitive casting tasks. For electronics enthusiasts, RTV silicone is often used to encapsulate components and protect them from environmental factors such as moisture, dust, and vibration. This encapsulation helps in extending the lifespan of electronic devices by shielding sensitive parts from potential damage. In automotive repairs, RTV silicone is commonly used to seal engine components, gaskets, and other parts that require a flexible yet durable seal. In consumer projects involving home improvement, RTV silicone is invaluable for its ability to adhere well to various surfaces including metal, glass, wood, and plastic. It can be used to seal gaps in flooring, around sinks and toilets, and even in outdoor applications like sealing patio furniture or repairing garden hoses. The fact that RTV silicone remains flexible after curing means it can accommodate slight movements between surfaces without losing its sealing properties. Moreover, RTV silicone is safe to use in food-grade applications when the appropriate type is chosen. This makes it suitable for sealing kitchen appliances or creating molds for baking and cooking. Its non-toxic nature also makes it a preferred choice for projects involving children's toys or educational materials. In summary, RTV silicone is a multifaceted material that enhances the efficiency and quality of various DIY and consumer projects. Its ease of use, durability, and versatility make it an essential tool in any DIY toolkit or workshop. Whether you are a seasoned craftsman or a beginner looking to tackle your first project, RTV silicone offers numerous practical uses and benefits that can help you achieve professional-grade results with minimal effort.