What Does Item In Transit Mean

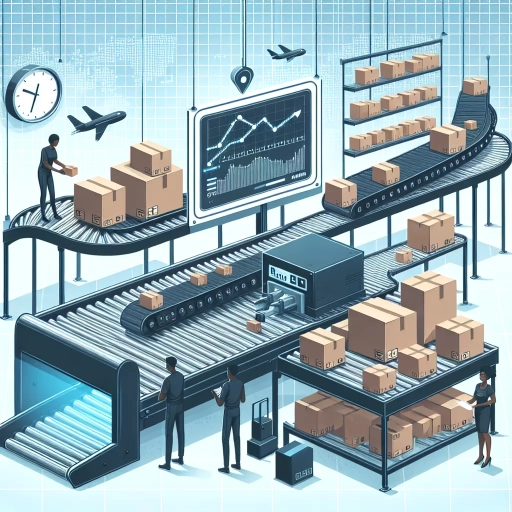
When you hear the term "item in transit," it often sparks curiosity about the journey of a product from its origin to its destination. This phrase is crucial in understanding the logistics and supply chain management that underpin modern commerce. In this article, we will delve into the concept of "item in transit," exploring what it means and how it functions. We will begin by **Understanding the Concept of "Item in Transit,"** which lays the foundation for grasping the intricacies involved. Next, we will examine **The Process of Items Being in Transit,** detailing the steps and mechanisms that ensure goods reach their intended recipients. Finally, we will discuss **Implications and Considerations for Consumers and Businesses,** highlighting the importance of this phase in the overall transaction process. By the end of this article, you will have a comprehensive understanding of what it means for an item to be in transit, starting with a clear grasp of the concept itself.
Understanding the Concept of "Item in Transit"
Understanding the concept of "item in transit" is crucial for anyone involved in logistics and supply chain management. This term refers to goods that are currently being transported from one location to another, whether by land, sea, or air. To grasp this concept fully, it is essential to delve into its definition and terminology, which will provide a clear understanding of what constitutes an item in transit. Additionally, exploring common scenarios where items are in transit will help illustrate the practical applications of this concept. Finally, recognizing the importance of items in transit within logistics and supply chain management highlights their critical role in ensuring timely and efficient delivery of goods. By examining these aspects, we can better appreciate the complexities and significance of items in transit. Let's begin by defining and understanding the terminology surrounding this concept.
Definition and Terminology
Understanding the concept of "item in transit" begins with a clear grasp of its definition and associated terminology. An item in transit refers to a product or package that is currently being transported from one location to another, typically from the seller or supplier to the buyer or recipient. This term is frequently used in logistics, shipping, and e-commerce contexts. Key terminology includes: - **Shipping**: The process of transporting goods from one place to another. - **Transit Time**: The duration it takes for an item to travel from the point of origin to its destination. - **Carrier**: The entity responsible for transporting the item, such as a courier service, postal service, or freight company. - **Tracking Number**: A unique identifier assigned to the shipment that allows both the sender and recipient to monitor its progress. - **Delivery Status**: The current state of the shipment, which can include stages like "shipped," "in transit," "out for delivery," and "delivered." - **Freight**: Goods or commodities being transported, especially by truck, train, ship, or airplane. Comprehending these terms is essential for managing expectations and ensuring smooth communication between all parties involved in the shipping process. For instance, knowing the transit time helps buyers anticipate when they will receive their items, while tracking numbers provide real-time updates on the item's location. Understanding that an item is "in transit" means it has been dispatched from the seller but has not yet reached its final destination, which can help manage customer inquiries and resolve potential issues promptly. By familiarizing oneself with this terminology, individuals can better navigate the complexities of modern logistics and enhance their overall experience with shipping and receiving goods.
Common Scenarios Where Items Are in Transit
Items in transit are goods or materials that are being transported from one location to another, often involving multiple stages and various modes of transportation. Here are some common scenarios where items are typically in transit: 1. **E-commerce Shipping**: When you order a product online, it often travels through multiple warehouses, distribution centers, and delivery services before reaching your doorstep. This entire journey is considered "in transit." 2. **International Trade**: Goods imported or exported across borders frequently spend significant time in transit due to customs clearance, shipping by sea or air, and other logistical processes. 3. **Supply Chain Logistics**: Companies often have complex supply chains where raw materials or finished products move between different facilities, such as manufacturing plants, warehouses, and retail stores. 4. **Freight Forwarding**: Businesses that specialize in arranging the transportation of goods on behalf of shippers frequently deal with items in transit as they coordinate with various carriers and logistics providers. 5. **Inventory Management**: When companies transfer inventory between different locations—such as from a central warehouse to regional stores—the items are considered in transit until they reach their destination. 6. **Returns and Refunds**: If a customer returns a product, it may be sent back through the postal service or courier companies and remains in transit until it is received by the seller. 7. **Military and Government Operations**: Military equipment and supplies, as well as government shipments, can be in transit for extended periods due to the complexity of their logistical operations. 8. **Agricultural Products**: Fresh produce and other agricultural goods may be transported over long distances from farms to markets, involving multiple stops along the way. 9. **Construction Materials**: Building materials like lumber, steel, and cement are often shipped from suppliers to construction sites, spending time in transit during this process. 10. **Pharmaceuticals and Medical Supplies**: These sensitive items may require specialized transportation and handling, leading to longer transit times due to regulatory compliance and safety measures. Understanding these scenarios helps clarify the concept of "item in transit" and highlights the importance of efficient logistics management to ensure timely delivery and maintain supply chain integrity.
Importance in Logistics and Supply Chain Management
Logistics and supply chain management are pivotal components of modern business operations, playing a crucial role in ensuring the efficient movement of goods from production to consumption. The importance of logistics and supply chain management can be underscored by several key factors. Firstly, these processes enable businesses to maintain a competitive edge by optimizing delivery times and reducing costs. Effective logistics ensure that products reach customers promptly, enhancing customer satisfaction and loyalty. Secondly, supply chain management involves the coordination of various stakeholders, including suppliers, manufacturers, distributors, and retailers, which helps in streamlining operations and minimizing disruptions. This coordination is essential for managing inventory levels, predicting demand, and mitigating risks such as supply chain disruptions or inventory shortages. Moreover, logistics and supply chain management are critical for maintaining product quality. Proper handling and storage during transit prevent damage to goods, ensuring that products arrive at their destination in pristine condition. This is particularly important for perishable items or those requiring specific storage conditions. Additionally, robust logistics systems facilitate data-driven decision-making through real-time tracking and analytics, allowing businesses to make informed decisions about their supply chains. This data can help identify bottlenecks, optimize routes, and improve overall efficiency. In the context of understanding the concept of "item in transit," logistics and supply chain management become even more pertinent. An item in transit refers to a product that is currently being transported from one location to another within the supply chain. Effective logistics ensure that these items are tracked accurately, their status updated in real-time, and any potential issues are addressed promptly. This transparency is vital for maintaining trust with customers and stakeholders, as it allows them to track the status of their orders seamlessly. Furthermore, the integration of technology such as GPS tracking, RFID tags, and blockchain enhances the visibility and security of items in transit. These technologies provide real-time updates on the location and condition of goods, reducing the risk of theft or loss. They also facilitate compliance with regulatory requirements by ensuring that all necessary documentation is in order during transit. In summary, logistics and supply chain management are indispensable for modern businesses due to their role in optimizing delivery times, coordinating stakeholders, maintaining product quality, facilitating data-driven decisions, and ensuring the secure transit of goods. These processes are particularly crucial when it comes to understanding and managing items in transit, as they ensure transparency, efficiency, and reliability throughout the supply chain. By leveraging advanced technologies and best practices in logistics and supply chain management, businesses can significantly improve their operational efficiency and customer satisfaction.
The Process of Items Being in Transit
The process of items being in transit is a complex and multifaceted journey that involves several critical stages. From the moment an order is placed, the item embarks on a path that requires meticulous planning, efficient execution, and continuous monitoring. This article delves into three key aspects of this process: **From Order Placement to Shipment**, which explores the initial steps of order processing and preparation for dispatch; **Tracking and Monitoring During Transit**, which highlights the importance of real-time tracking and monitoring to ensure timely delivery; and **Handling Delays and Issues During Transit**, which discusses strategies for mitigating and resolving any issues that may arise during the journey. By understanding these stages, businesses and consumers alike can gain valuable insights into the logistics behind item transit, ultimately enhancing the overall efficiency and reliability of the delivery process. Let's begin by examining the first crucial phase: **From Order Placement to Shipment**.
From Order Placement to Shipment
From the moment an order is placed, a series of meticulous steps ensues to ensure that the item reaches its destination efficiently. Here’s a detailed look at this process: 1. **Order Placement**: The journey begins when a customer places an order through various channels such as online platforms, phone calls, or in-store purchases. The order details are captured and verified to ensure accuracy. 2. **Order Processing**: Once the order is received, it undergoes processing. This involves checking the availability of the items, verifying payment details, and confirming the shipping address. Automated systems often handle these tasks to streamline the process. 3. **Inventory Management**: The next step involves locating the ordered items within the warehouse or inventory storage. Advanced inventory management systems help in tracking stock levels and ensuring that the items are readily available for shipment. 4. **Picking and Packing**: Warehouse staff then pick the ordered items from their respective shelves and pack them into shipping boxes. Care is taken to ensure that items are properly packaged to prevent damage during transit. 5. **Labeling and Documentation**: Each package is labeled with the correct shipping address and any relevant handling instructions. Documentation such as invoices, receipts, and customs forms (for international shipments) are also prepared. 6. **Shipping Carrier Selection**: The packaged items are then handed over to a shipping carrier such as USPS, UPS, FedEx, or DHL. The choice of carrier depends on factors like delivery speed, cost, and service reliability. 7. **Shipment**: The items are now in transit. They may travel through various hubs and sorting facilities before reaching their final destination. Tracking numbers are provided to both the seller and buyer to monitor the shipment's progress. 8. **Delivery**: Upon arrival at the local delivery hub, packages are sorted and dispatched to their final destinations. Delivery personnel ensure that packages are delivered to the correct addresses, often requiring signatures upon receipt. 9. **Post-Delivery Follow-Up**: After delivery, some sellers may follow up with customers to ensure satisfaction with their purchase and gather feedback. Throughout this process, technology plays a crucial role in enhancing efficiency and transparency. Automated systems help in tracking inventory levels, processing orders quickly, and providing real-time updates on shipment status. This ensures that items move smoothly from order placement to shipment, ultimately leading to a positive customer experience.
Tracking and Monitoring During Transit
Tracking and monitoring during transit are crucial components of the logistics process, ensuring that items reach their destinations efficiently and securely. This involves the use of advanced technologies such as GPS tracking, RFID tags, and real-time monitoring systems. Here’s how it works: 1. **Initialization**: When an item is shipped, it is assigned a unique tracking number. This number is linked to the item's details in the shipping company's database. 2. **GPS Tracking**: GPS devices attached to the shipment provide real-time location updates. This data is transmitted to the shipping company's servers, allowing both the sender and recipient to track the item's progress. 3. **RFID Tags**: Radio Frequency Identification (RFID) tags can be used to track items at various checkpoints along the transit route. These tags communicate with RFID readers at warehouses, distribution centers, and other key points. 4. **Real-Time Monitoring**: Advanced software platforms integrate data from GPS, RFID, and other sources to provide a comprehensive view of the shipment's status. This includes updates on location, temperature (for perishable goods), and any potential delays or issues. 5. **Notifications**: Automated notifications are sent to stakeholders via email or SMS when the shipment reaches certain milestones or if there are any discrepancies. This keeps everyone informed and allows for prompt action if necessary. 6. **Security Measures**: Tracking systems often include security features such as alerts for unauthorized access or tampering attempts. This helps protect valuable or sensitive items during transit. 7. **Data Analytics**: The data collected during transit can be analyzed to improve future shipments. This includes optimizing routes, reducing transit times, and enhancing overall efficiency. 8. **Customer Service**: Real-time tracking information can be shared with customers through online portals or mobile apps, enhancing their experience by providing transparency and peace of mind. By leveraging these technologies and processes, tracking and monitoring during transit ensure that items are delivered reliably and efficiently, minimizing the risk of loss or damage and improving customer satisfaction. This not only benefits the shipping companies but also enhances the overall supply chain management by providing valuable insights for continuous improvement.
Handling Delays and Issues During Transit
Handling delays and issues during transit is a critical aspect of ensuring the smooth and efficient movement of goods. When items are in transit, various factors can lead to delays or complications, such as inclement weather, traffic congestion, mechanical failures, customs clearance issues, or misrouting. To mitigate these challenges, logistics companies and shippers must have robust contingency plans in place. Firstly, real-time tracking systems are essential for monitoring the location and status of shipments. This allows for immediate identification of any deviations from the planned route or schedule, enabling swift action to be taken. For instance, if a shipment is delayed due to weather conditions, alternative routes can be quickly identified and implemented. Secondly, maintaining open communication channels with all stakeholders, including the sender, recipient, and any intermediaries, is crucial. Transparent updates on the status of the shipment help manage expectations and reduce anxiety. Automated notifications via email or SMS can keep parties informed about any changes or issues. Thirdly, having a network of reliable partners and backup options is vital. This includes multiple carriers and transportation modes (e.g., air, land, sea) that can be leveraged in case of disruptions. For example, if one carrier experiences delays, another can be swiftly engaged to ensure continuity. Additionally, proactive measures such as risk assessment and mitigation strategies should be part of the transit process. This involves identifying potential bottlenecks and developing contingency plans before they become issues. For example, understanding peak traffic times or seasonal weather patterns can help in planning more efficient routes. Furthermore, compliance with regulatory requirements is paramount to avoid delays at customs or border crossings. Ensuring all necessary documentation is accurate and complete can expedite clearance processes. In cases where issues arise despite these precautions, having a dedicated customer service team that can address concerns promptly is indispensable. This team should be equipped with the necessary tools and authority to resolve problems efficiently without escalating them unnecessarily. Finally, post-incident analysis is crucial for continuous improvement. Reviewing what went wrong during a delay or issue helps in refining processes and improving future transit operations. This might involve updating routing algorithms, enhancing training for logistics personnel, or investing in more resilient infrastructure. By combining these strategies—real-time tracking, effective communication, reliable partnerships, proactive risk management, regulatory compliance, robust customer service, and continuous improvement—logistics providers can significantly reduce the impact of delays and issues during transit. This not only ensures timely delivery but also enhances customer satisfaction and trust in the transit process.
Implications and Considerations for Consumers and Businesses
The implications and considerations for consumers and businesses in the modern logistics landscape are multifaceted and critical. As we delve into these complexities, it becomes clear that several key factors must be addressed. Firstly, the impact on delivery times and customer satisfaction is paramount, as timely and reliable deliveries directly influence consumer trust and loyalty. Secondly, insurance and liability concerns must be meticulously managed to protect both parties from unforeseen risks and financial losses. Lastly, strategies for optimizing transit times and costs are essential for maintaining competitiveness and efficiency in a rapidly evolving market. Understanding these elements is crucial for both consumers seeking reliable service and businesses aiming to enhance their operational excellence. Let's begin by examining the **Impact on Delivery Times and Customer Satisfaction**, a cornerstone of consumer-business relationships in today's fast-paced world.
Impact on Delivery Times and Customer Satisfaction
The impact on delivery times and customer satisfaction is a critical consideration for both consumers and businesses when items are in transit. Delays or inefficiencies in the delivery process can significantly affect customer satisfaction, as timely receipt of goods is often a key expectation. For consumers, delayed deliveries can lead to frustration and a negative experience, potentially resulting in lost trust and future business. On the other hand, reliable and swift delivery enhances customer satisfaction, fostering loyalty and positive word-of-mouth. From a business perspective, maintaining optimal delivery times is crucial for maintaining a competitive edge. Companies that consistently deliver products on time are more likely to retain customers and attract new ones through positive reviews and recommendations. Conversely, frequent delays can harm a company's reputation and lead to financial losses due to returns, refunds, and the potential loss of repeat business. Additionally, businesses must consider the implications of delivery times on their operational efficiency and supply chain management. Streamlining logistics processes and investing in tracking technologies can help mitigate delays and improve overall customer satisfaction. Moreover, the rise of e-commerce has heightened consumer expectations regarding delivery speed and reliability. With the advent of same-day or next-day delivery options offered by some retailers, consumers are increasingly demanding faster shipping times. This trend necessitates businesses to adapt their logistics strategies to meet these evolving expectations while balancing costs and operational feasibility. In summary, the impact on delivery times directly influences customer satisfaction, making it a vital aspect for businesses to prioritize in order to maintain a competitive advantage and build long-term customer relationships.
Insurance and Liability Concerns
Insurance and liability concerns are pivotal when dealing with items in transit, as they directly impact both consumers and businesses. For consumers, understanding the insurance options available can provide peace of mind and financial protection against loss or damage. Typically, shipping companies offer various levels of coverage, ranging from basic carrier liability to more comprehensive insurance policies. Consumers should carefully review these options to ensure they are adequately protected, especially for high-value or sensitive items. Additionally, consumers should be aware of any exclusions or limitations in the policy, such as coverage for specific types of damage or geographical restrictions. For businesses, managing insurance and liability is crucial for maintaining operational integrity and customer trust. Companies must assess their risk exposure and choose appropriate insurance coverage to mitigate potential losses. This includes considering factors such as the type of goods being transported, the mode of transportation, and the route taken. Businesses also need to comply with regulatory requirements regarding insurance and liability, which can vary by jurisdiction. Furthermore, having clear policies in place for handling claims and disputes can help businesses maintain a positive reputation and minimize legal complications. In terms of implications, inadequate insurance coverage can lead to significant financial losses for both consumers and businesses. For instance, if an item is damaged or lost during transit and there is insufficient coverage, the financial burden falls on the party responsible for the shipment. This can strain consumer budgets and impact business profitability. On the other hand, comprehensive insurance coverage can provide a safety net, allowing parties to recover from unforeseen events without substantial financial hardship. Moreover, liability concerns extend beyond financial losses to include reputational damage. Businesses that fail to ensure proper insurance coverage may face customer dissatisfaction and potential legal action if items are not delivered as promised. Conversely, businesses that prioritize robust insurance policies demonstrate a commitment to customer satisfaction and risk management, enhancing their credibility in the market. In conclusion, insurance and liability concerns are critical considerations for both consumers and businesses when dealing with items in transit. By understanding available insurance options, assessing risk exposure, complying with regulations, and maintaining clear policies for handling claims, parties can effectively manage these concerns. This proactive approach not only protects against financial losses but also fosters trust and reliability in the shipping process.
Strategies for Optimizing Transit Times and Costs
Optimizing transit times and costs is crucial for both consumers and businesses, as it directly impacts the efficiency and profitability of logistics operations. Several strategies can be employed to achieve this optimization: 1. **Route Optimization**: Utilizing advanced algorithms and real-time data, companies can identify the most efficient routes for their vehicles, reducing travel time and fuel consumption. This can be particularly effective when combined with GPS tracking and traffic updates. 2. **Consolidation**: Consolidating shipments into fewer, larger loads can significantly reduce the number of vehicles on the road, lowering costs associated with fuel, maintenance, and driver wages. This approach also helps in minimizing the environmental impact. 3. **Intermodal Transportation**: Leveraging multiple modes of transportation (such as trucks, trains, and ships) can offer flexibility and cost savings. For instance, using rail for long-distance hauls and trucks for shorter legs can optimize both time and cost. 4. **Just-in-Time (JIT) Delivery**: Implementing JIT delivery systems ensures that goods are delivered exactly when needed, reducing inventory holding costs and minimizing the risk of stockouts or overstocking. 5. **Technology Integration**: Adopting technologies like RFID tags, IoT sensors, and blockchain can enhance visibility throughout the supply chain. These tools provide real-time tracking, automate documentation processes, and improve security, thereby reducing transit times and associated costs. 6. **Partnering with Third-Party Logistics (3PL) Providers**: Collaborating with 3PL providers can offer specialized expertise in logistics management, allowing businesses to focus on their core activities while benefiting from optimized transit times and reduced costs. 7. **Peak Season Planning**: Anticipating peak demand periods and planning accordingly can help mitigate delays and additional costs. This includes hiring temporary staff, leasing extra vehicles, or negotiating better rates with carriers. 8. **Sustainable Practices**: Implementing sustainable practices such as using electric or hybrid vehicles, optimizing packaging to reduce weight and volume, and encouraging eco-friendly behaviors among drivers can lead to long-term cost savings while contributing to environmental sustainability. By implementing these strategies, businesses can streamline their logistics operations, enhance customer satisfaction through faster delivery times, and ultimately drive down costs. For consumers, this translates into quicker access to goods at potentially lower prices due to reduced operational expenses for businesses. However, it is essential for both parties to consider factors such as infrastructure limitations, regulatory compliance, and the potential for disruptions in the supply chain when optimizing transit times and costs.