What Is Flannel Made Of

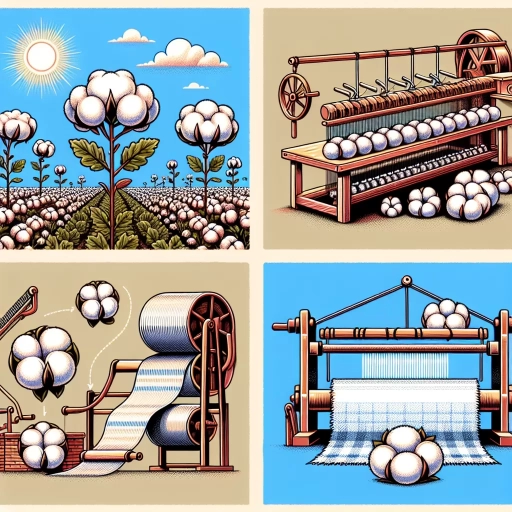
Materials Used in Flannel Fabric
Flannel is one of the most utilized fabrics in various garments due to its unique attributes of warmth and softness, and it owes these attributes to the dominant materials used in its production such as cotton, wool, and synthetic fibers. Cotton, well-known for its soft, breathable nature and high moisture-absorbing capacity, is widely used in making flannel clothing to offer comfort and freshness, especially during warm seasons. In contrast, wool, with its exceptional heat insulation property, is the preferred choice for flannel manufacturing intended for colder climates. Synthetic fibers, on the other hand, are a practical choice for manufacturers because they can be customized to combine the best qualities of cotton and wool, and are often more durable. As a result, the combination of these three fibers has led to a diversity of flannel textiles suitable to meet the demands of various climates and user preferences. Each of these materials brings a unique feel, warmth, and durability to the finished fabric, with cotton being an essential part of the majority of the blends. Let's take a closer look at cotton's role in flannel fabric production.
1. Cotton
Cotton is a crucial component in the manufacturing of flannel fabric, attributing greatly to its endearing and versatile qualities. A naturally growing plant, cotton is loved and predominantly utilized worldwide for its pureness, softness, flexibility, and incredible ability to control moisture. Cotton's fibers are spun into yarn or thread that are then used in creating a soft, breathable textile like flannel. Cotton is fundamentally known for its hypoallergenic profile, making it an ideal choice for people with sensitive skin or allergies. It does not irritate the skin and reduces the possibility of rashes and other allergies, contributing to the overall comfort of wearing flannel. Additionally, cotton's ability to regulate temperature, absorbency, and softness make it an ideal choice for flannel. In cold weather, it can trap the heat between the fabric and the skin, providing excellent insulation and keeping the wearer warm. Ironically, it also offers fantastic summer relief because of its ability to absorb sweat and release it on the surface, enabling the heat to evaporate and hold a cooling effect. The durability of cotton also sets it apart, particularly in the creation of flannel. It's an incredibly resilient fabric that withstands multiple and thorough washings without losing its shape or vibrancy. Notably, cotton flannel can stand up to years of wear and tear, resists pilling, and most importantly, it continues to soften over time, contributing to the material's comfort and coziness. Ethical and environmental considerations further enhance cotton's appeal. Cotton farming upholds sustainable agriculture because cotton fields replenish the soil's nutrient content, making it more fertile and usable for future crop cultivation. This holistic approach to fabric production is essential in today's socially and environmentally conscious world. Also, given cotton's natural properties, the flannel fabric made from it is biodegradable, giving it a lower environmental impact than synthetic materials. As a renewable resource, cotton's advantage is transformative because it continues to impact positively on flannel fabric's sustainable profile. In summary, the use of cotton in the production of flannel fabric redefines both the look and feel of the end product. It provides a perfect blend of comfort, warmth, durability, and sustainability, making flannel a beloved fabric in many casual and comfortable clothing, bedding, and upholstery. It's more than a material; it's a testament to the importance of using natural resources wisely and improving our clothing's quality and lifespan.
2. Wool
While flannel fabric can be made from various materials, wool serves as its original constituent. The intricate process of its creation dates back to the 17th century in Wales. Woolen flannel became the staple clothing for laborers as it was cost-effective, warm, durable, and easy to produce. Unlike its modern counterparts such as cotton and synthetic, woolen flannel was not brushed to create a nap; instead, it was fulled, a process that involves plucking the fibers to make them more compact, creating the fabric's characteristic thick and fluffy texture. The inherent properties of wool make it a superior resource for crafting flannel fabric. Wool, being an insulating material, is great for keeping warm during chilly weather, making woolen flannel an ideal material for winter clothing. It functions by trapping air in its tiny fibers, maintaining a layer of warm air next to the skin while concurrently drawing moisture away. This moisture-wicking capability makes woolen flannel not only a fabric for cold climates but also practical to use during warmer seasons. In terms of strength, wool fibers have a natural crimp that provides elasticity. This is an advantage as the fabric can easily return to its original form after stretching, making it resistant to wrinkling and sagging. Wool fibers are also longer compared to other materials, which contributes to the overall durability and longevity of wool flannel garments. With ongoing developments in the clothing industry, the use of wool in flannel fabric has seen innovations. Wool is often blended with other materials like cotton or synthetic fibers to bring together the best of all worlds. The introduction of these materials infuses the woolen flannel with added comfort, breathability, and softness—properties often associated with cotton—while also enhancing its strength and durability. Some also argue that blended flannel is less itchy than its pure wool counterpart, making it more appealing to the growing need for comfort in modern clothing. Although woolen flannel has been somewhat overshadowed by other materials in the contemporary market, it is steadily gaining recognition for its distinct features and benefits. With increasing awareness about sustainability and environmental consciousness, wool’s natural and renewable qualities are becoming more valued. Wool is inherently biodegradable and renewable; sheep produce a new fleece annually, which farmers can sheer to create wool. In an era of fast fashion and environmental crisis, the usage of wool in flannel fabric underscores sustainable practices alongside comfort, technology, and design. Thus, the use of wool in producing flannel fabric manifests an innovative blend of traditional production methods and modern clothing technologies. Its unique properties, when utilized effectively, create high-quality flannel that views comfort, durability, and sustainability through a new lens.
3. Synthetic Fibers
Synthetic fibers are an integral part of modern flannel fabric production due to their flexibility, durability, and cost-effectiveness. These are artificially made fibers, largely derived from petroleum products, created through a process known as polymerization. The three primary types of synthetic fibers used in the production of flannel include polyester, nylon, and acrylic. Polyester is particularly popular in making flannel due to its durability, elasticity, and resistance to wrinkles. These properties make it an excellent choice for flannel clothing, as items retain their shape and offer enhanced comfort. Moreover, polyester's capability to hold color well makes it favorite for flannel production as it guarantees vibrant and long-lasting patterns and prints. Nylon, another synthetic fiber, is known for its exceptional strength and flexibility. It is usually blended with other materials in flannel production to impart a soft and comfortable feel on the fabric. Nylon also has excellent colorfastness, ensuring that the colors on the fabric do not fade quickly. Furthermore, it dries quickly, a trait that improves the overall functionality and comfort of the flannel fabric. Last but not least, acrylic fibers bring warmth, lightness, and softness - characteristics traditionally associated with wool - to flannel fabric. This makes acrylic a popular choice for flannel beddings and winter clothing. Moreover, acrylic is resistant to moths and sunlight, properties that contribute to the longevity of the fabric. In essence, the incorporation of synthetic fibers in flannel production significantly enhances the versatility, durability, and comfort of the fabric. Whether it's polyester flannels with their wrinkle resistance and color durability, nylon flannels that amalgamate strength and softness, or acrylic flannels offering the warmth of wool without its heavyweight, synthetic fibers have helped perfect the characteristics of flannel fabric fitting for diverse uses and preferences. However, while synthetic fibers offer myriad advantages, it's worth mentioning their environmental impact. These fibers are not biodegradable and their production often involves non-renewable resources, which presents a challenge for sustainable manufacturing practices. Thus, efforts are needed to ensure the ecological footprint of flannel production is kept to a minimum.
Manufacturing Process of Flannel
Flannel, a cozy, warm, and comfortable fabric, has experienced enduring popularity due to its unique manufacturing process, which intricately combines science and art. Typically made from wool, cotton, or synthetic fibers, flannel production involves a fascinating three-stage process. The initial phase is carding and spinning, wherein the raw materials are transformed into workable threads. This phase lays the groundwork for the second step, weaving or knitting, where the threads are interlaced into fabric by utilizing various traditional or modern methods according to the desired pattern and texture. Finally, the fabric undergoes finishing treatments to improve its appearance, feel, and durability. Each of these stages demands meticulous attention to detail, making the manufacture of flannel a skilled practice. This article aims to take its readers on an enlightening journey through these three integral parts of flannel production, starting with the captivating process of carding and spinning.
1. Carding and Spinning
Carding and spinning are two crucial processes within the larger manufacturing sequence of flannel. Prior to spinning, the fabric's raw material- often cotton or wool, must undergo the carding process. Carding is a fundamental technique that disentangles, cleans, and intermingles the fabric fibers to produce a continuous web or sliver suitable for subsequent processing. This method essentially preps the raw material, removing any impurities or short fibers while aligning the remaining longer fibers parallel to each other. Besides fostering consistency, carding also helps increase the fabric's overall strength, softness, and flexibility. Once the carding process has been accomplished, the subsequent process, spinning, takes place. The aim of spinning is to draw out the fibers, creating a thread or yarn from the cleaned fibers received from the carding stage. In this crucial phase, the fibers are twisted so they come together and ultimately lock into one another, thereby creating a yarn. The thickness of the yarn is determined by how much the fibers are initially pulled or 'drawn out' before they’re twisted. The resultant yarn or thread’s strength depends entirely on how tightly it's twisted during spinning. The higher the number of twists, the stronger the yarn tends to be. Interestingly, the yarn’s twist level also affects the final look and feel of the flannel material. A loosely spun yarn results in a more plush and soft fabric, ideally sought in flannel clothes while a tighter twist gives a sturdier yet slightly less soft finish. Either way, both carding and spinning are essential in ensuring the flannel’s distinctive feel and texture. The variations in these processes uniquely contribute to differing weights, softness levels, and durability within the broad range of flannel fabrics available today. Thus, carding and spinning effectively lay the foundation for the flannel's characteristic warmth, comfort, and longevity. Despite the advent of numerous technological advancements and machinery over the years, these two processes have retained their core principles. Most modifications have mainly focused on upscaling productivity rates, enhancing efficiency and improving the workers' safety. Every flannel piece owes its existence to these twin processes, which have remained remarkably unchanged in their basic technicalities over centuries. The continued importance of carding and spinning in the production of flannel illustrates the timeless relevance of these fundamental manufacturing steps. Thus, understanding these processes goes a long way in comprehending the character and composition of the versatile and much-loved flannel.
2. Weaving or Knitting
Weaving and knitting are fundamental processes during the creation of flannel, contributing significantly to its unique texture and warmth. Both processes commence from the basic stage of spinning cotton into yarn, followed by either knitting or weaving it into fabric. It is noteworthy that weaving and knitting bring about different final products; while fabric produced through weaving inclines to have a flat appearance, knitting results in a more stretchy and flexible fabric material. The process of weaving, in the manufacturing of flannel, involves interlacing two sets of yarn - the warp (lengthwise yarn) and the weft (widthwise yarn). These yarns, woven together, form a grid pattern, crucial in offering the sturdiness associated with flannel. Typically, the warp yarns are kept taut on the loom while the weft yarn is woven over and below in an alternating pattern. However, in some cases, variations in the weaving style, including twill and herringbone weaves, can be implemented to create unique texture and designs on the fabric's surface. On the other hand, knitting in flannel production is less common, but still utilized in specific circumstances. Instead of the crisscrossing method used in weaving, knitting uses a series of interlocking loops. This process produces a fabric that is stretchy and retains more heat, making it preferable for specific wearables or bedding. Although some flannel products tout a knitted construction, they represent a minority in the market due to the higher production cost and time involved. The variation in weaving and knitting processes and their respective techniques gives flannel its diverse range and versatility. The high-quality flannel fabric gained through weaving with a denser thread count results in a product that is warm, soft against the skin and highly resilient. On the contrary, knitted flannel, although less common, provides a more elastic and snug-fitting final product that offers superior heat retention but at a higher price point. In conclusion, the weaving and knitting processes are core to the manufacturing of flannel, each bringing unique attributes to the final product. Whether woven or knitted, the multi-step manufacturing process of flannel ensures that the resulting fabric meets the general expectations of durability, warmth, and comfort that flannel enthusiasts have come to appreciate. The individual fabric characteristics will, however, depend on the manufacturing techniques employed, proving that the art of weaving or knitting is a critical element in the manufacturing process of flannel.
3. Finishing Treatments
After the flannel material has been woven together in the earlier manufacturing process, it undergoes a series of finishing treatments to enhance its distinctive properties. The first of these treatments is typically the napping process, where the fabric is brushed to raise the fine surface fibers, creating the flannel's iconic soft and fuzzy texture. This is an integral step in the creation of flannel, as it adds to its warmth by trapping body heat. The napping process can be executed on one or both sides of the fabric, depending on the desired finish and end use of the fabric. Next, the napped flannel goes through a process called shearing. During shearing, any excess fuzz or fiber is removed to create a uniform texture and finish. Shearing prevents the fabric from pilling, a common issue with flannel where small balls of fuzz form on the surface due to friction. A crucial step in the flannel finishing process is dyeing. The flannel fabric can be dyed a single color, or it can be dyed in patterns, the most traditional of which is tartan or plaid. The dye is applied through a number of different techniques, including rotary screen printing or roller printing, depending on the complexity and intricacy of the desired pattern. To enhance the durability and functional features of flannel, it may also undergo additional treatments. This includes a fire-retardant finish for flannel used in children's sleepwear, or a water-resistant finish for outdoor clothing. Other treatments may include anti-wrinkle or stain-resistant finishes, making the flannel more user-friendly and long-lasting in its different applications. Lastly, the finished fabric is thoroughly inspected for any flaws or defects before it is rolled, packed, and shipped to retailers or garment manufacturers. This meticulous quality control ensures that the flannel material that reaches the customers is of the highest possible quality, embodying the soft comfort, vibrant patterning, and tough durability that flannel is loved for. In conclusion, the finishing treatments for flannel are just as important as the initial weaving process. They play a vital role in dictating the texture, appearance, and functionality of the final fabric product. These processes help transform coarse wool or blended fibers into the warm, soft, and durable flannel material we know today.
Properties and Uses of Flannel Fabric
In the world of textiles, flannel fabric stands out for many reasons. This unique fabric, renowned for its warmth, soft feel, and versatile applications, is highly sought-after by clothing designers and homeware companies alike. It offers three distinct properties, namely an excellent level of thermal insulation, supreme softness and comfort, and versatility in its fashion and home textile uses. Each of these properties makes it a preference for many users, and they contribute significantly to flannel fabric's popularity globally. The thermal insulation feature of flannel makes it ideal for cold conditions, whether be it for clothing or bedding. Its softness is unparalleled, offering maximum comfort to wearers. This softness is not only appreciated in garments, but also in other products like blankets, bed sheets, and textiles used in babies' products. Versatility is another significant aspect of flannel fabric as it is used in many ways, from clothing to home textiles. We are about to embark on an exciting exploration of these properties, starting with thermal insulation, to understand why flannel fabric remains a favorite in the textile market.
1. Thermal Insulation
As an essential property of flannel fabric, thermal insulation significantly contributes to its widespread usage and popularity. Essentially, thermal insulation refers to a material’s capacity to reduce heat transfer between objects in thermal contact or within range of radiant influence. In terms of flannel fabric, thermal insulation property arises due to the nature of its loosely woven construction. The minutely detailed weaving generates small air pockets that aid in retaining the warmth generated from the body, creating an insulating effect against the cold external environment. Flannel's insulating traits stem from its origin as a heavyweight fabric for cold weather. Initially created from carded wool or worsted yarn, modern flannels vary in material, from organic fibers like cotton or wool to synthetics like polyester. Regardless of the fiber used, the napped surface is what provides flannel with its insulating capacity. The napping process raises the fiber ends from the tight weave, creating a fuzzier surface and millions of tiny insulated spaces that trap air and body heat. This innate thermal insulation property thrusts flannels into the limelight as a preferred choice of clothing material during winter and in colder regions. Its usage thus traverses from everyday clothing, shirts, and sleepwear to bedclothes including sheets and blankets due to their inherent warmth properties. Flannel is also extensively used by outdoor enthusiasts for camping, hiking, or other outdoor activities where warmth is a critical factor. As a testament to its insulation property, flannel is widely employed in making thermal underwear, which is designed to retain body heat to safeguard against extreme cold conditions. Interestingly, the thermal insulation aspects of flannel also hold benefits in hot conditions. Unlike common perception, the insulating air pockets also help to wick sweat away from the body during warm periods, giving flannel an edge over other fabrics. The tiny insulated spaces allow air to pass through, offering breathability and imparting a cooling effect when it's hot. Therefore, the thermal insulation property of flannel is versatile and serves a dual purpose: providing warmth in cold environments and offering breathability in warm conditions. Thus, flannel’s adaptability with its thermal insulation property, whether facing the biting chill of harsh winters or the sweaty discomfort of summer heat, makes it a popular and functional fabric choice in the textile industry. This property not only provides comfort and durability but also lends itself to a wide array of uses, revealing that the utility of flannel goes beyond its simple, cozy appeal.
2. Softness and Comfort
Flannel fabric is renowned for its softness and comfort, making it a favorite choice for many people, particularly during the colder months. Created using either a plain or twill weave, flannel's distinctive softness arises from its unique production process. Initially, the fabric is tightly woven to create a sturdy, resilient material. However, the magic of its softness appears during the brushing process. Here, a fine metal brush rubs the fabric to raise fine fibers from the loosely spun yarns, creating a plush surface that is at once soft, fuzzy and incredibly comfortable to the touch. This remarkable softness and pleasant-to-touch feel make flannel the ultimate comfort fabric. Its cozy fuzziness provides a soothing tactile sensation while efficiently retaining heat, which contributes to its noted warmth. It is often the go-to fabric for sleepwear, bed sheets, and blankets precisely because it feels so good against the skin. Even when used for upholstery or clothing, flannel offers a level of comfort that few other materials can match. It shapes and drapes well to the body for a relaxed fit, making flannel garments such as shirts, trousers, or jackets feel like a comfortable hug. Flannel's inherent softness and comfort extend to its versatility too. Not just limited to cold weather wardrobes or sleepwear, the fabric serves a multitude of uses across different applications and industries due to these properties. For instance, in the health and beauty industry, it's often used for washcloths, face towels, robes, or spa wraps. Its gentle plushness makes it suitable for sensitive skin, proving comforting and non-irritating. Moreover, flannel's comforting softness can have therapeutic value. In the crafting world, weighted blankets filled with rice or barley and made from flannel are a popular DIY project. The heaviness of the blanket combined with the tactile softness can help reduce anxiety and improve sleep quality. Even in babyware, the softness of flannel is beneficial for delicate baby skin while offering the necessary warmth. Thus, the essence of flannel fabric lies in its softness and comfort-oriented characteristics. These defining attributes make it a versatile, beloved material put to multiple uses, from cozy pajamas and linens to comfortable clothing and therapeutic aids. In its inherent softness and comfort, flannel provides not only a pleasant tactile experience but the warmth and consolation we often seek in our textiles.
3. Versatility in Fashion and Home Textiles
Versatility is perhaps one of the most appealing properties of flannel fabric, making it a preferred choice across both fashion and home textiles. In the realm of fashion, its softness and warmth make flannel ideal for winter garments. It's often used to produce high-quality shirts, trousers, jackets, and even accessories like scarves and gloves. Its breathable nature caters for comfort while offering a cozy feel against the skin, making it perfect for comfortable sleepwear and baby clothing as well. Beyond its practical uses, flannel also boasts aesthetic versatility. Its ability to hold various colors and patterns makes it an adaptive fabric for different styles and tastes, lending itself well for both traditional and contemporary designs. In home textiles, flannel is equally valued. Its insulating properties are perfect for creating warm bedding like sheets, blankets and duvet covers. The softness of flannel is comforting and inviting, hence its frequent use in making pet bedding. Upholstery and curtain materials are also made of flannel to bring a sense of warmth and coziness to interior spaces. It's also found in kitchens as tea towels and tablecloths, demonstrating its utility beyond fabric softness. Furthermore, flannel’s durability is yet another compelling factor contributing to its versatility. This fabric can withstand repeated washing and wearing, making it a cost-effective choice in the long run. Additionally, it's relatively easy to care for and doesn’t demand complicated maintenance, marking it even more appealing across diverse applications. Properly cared for, colors remain vivid and the fabric retains its soft, plush qualities even after extended use. This versatility, combined with the fabric’s comfort, durability, and ease of maintenance, solidifies flannel’s place as an immensely popular choice within both the fashion and home textile industries.