What Is Dielectric Grease

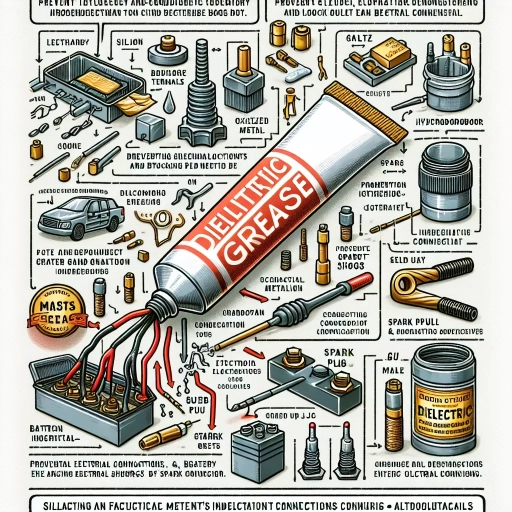
Dielectric grease, often misunderstood as just another type of lubricant, plays a crucial role in protecting electrical connections and ensuring the longevity of various mechanical and electrical systems. This versatile substance is not only essential for preventing corrosion and moisture ingress but also enhances the performance and reliability of components. In this article, we will delve into the specifics of dielectric grease, exploring its fundamental nature, the benefits it offers, and practical tips on how to apply and maintain it effectively. By understanding what dielectric grease is, you will appreciate its importance in safeguarding your equipment. We will discuss the numerous advantages of incorporating dielectric grease into your maintenance routine, highlighting how it can mitigate common issues such as rust and electrical failures. Finally, we will provide step-by-step guidance on how to apply and maintain dielectric grease to maximize its benefits. Let's begin by examining the core question: **What is Dielectric Grease?**
What is Dielectric Grease?
Dielectric grease, often misunderstood as merely a lubricant, is a multifaceted substance that plays a crucial role in various industrial and automotive applications. At its core, dielectric grease is a specialized type of silicone-based lubricant designed to protect electrical connections from moisture and corrosion. To fully appreciate its significance, it is essential to delve into its definition and composition, primary uses and applications, and key properties and characteristics. Understanding the **definition and composition** of dielectric grease is fundamental. It typically consists of a silicone base mixed with other additives that enhance its protective qualities. This unique blend allows it to serve as an effective barrier against moisture and contaminants. Beyond its composition, dielectric grease has **primary uses and applications** that are both diverse and critical. It is commonly used in automotive systems to protect electrical connectors from the elements, ensuring reliable performance. Additionally, it finds use in industrial settings where electrical components are exposed to harsh environments. The **key properties and characteristics** of dielectric grease make it an indispensable tool. Its non-conductive nature ensures that it does not interfere with electrical signals, while its water-repellent properties safeguard against corrosion. These attributes collectively contribute to its widespread adoption across various sectors. By exploring these facets, we can gain a comprehensive understanding of what dielectric grease is and why it is so vital. Let us begin by examining its **definition and composition** in more detail.
Definition and Composition
Dielectric grease, often referred to as silicone-based dielectric compound, is a specialized lubricant designed to protect electrical connections from moisture, corrosion, and wear. At its core, dielectric grease is composed of a mixture of silicone oils and thickening agents, typically silica or calcium carbonate, which provide its unique properties. The primary component, silicone oil, is a synthetic polymer that offers excellent insulation and lubrication characteristics. This oil is non-conductive, meaning it does not allow the flow of electrical current, making it ideal for use in electrical connections where maintaining insulation is crucial. The thickening agents added to the silicone oil transform it into a semi-solid paste that adheres well to surfaces without dripping or running off. This consistency ensures that the grease remains in place even under varying environmental conditions such as temperature fluctuations and vibrations. Additionally, dielectric grease often contains additives like antioxidants and UV stabilizers to enhance its durability and resistance to degradation over time. One of the key benefits of dielectric grease is its ability to seal out moisture and contaminants from electrical connections. When applied to terminals, connectors, or other electrical interfaces, it forms a protective barrier that prevents water and other corrosive substances from entering the connection. This not only helps in maintaining the integrity of the electrical circuit but also reduces the risk of short circuits and other malfunctions. Furthermore, dielectric grease acts as a lubricant that reduces friction between moving parts in electrical mechanisms. This lubricating property is particularly important in applications where components may rub against each other, such as in switches or relays. By minimizing friction, dielectric grease helps extend the lifespan of these components by reducing wear and tear. In terms of composition, while the base ingredients remain consistent across different brands and types of dielectric grease, variations may exist in terms of specific additives or concentrations of thickening agents. Some formulations may be tailored for specific applications—such as high-temperature environments or marine use—where additional properties like enhanced thermal stability or saltwater resistance are necessary. Overall, the definition and composition of dielectric grease highlight its multifaceted role in protecting and maintaining electrical systems. Its unique blend of insulating and lubricating properties makes it an indispensable tool for ensuring reliable operation and longevity in a wide range of electrical applications. Whether used in automotive systems, industrial equipment, or consumer electronics, dielectric grease plays a critical role in safeguarding against environmental factors that could compromise electrical performance.
Primary Uses and Applications
Dielectric grease, also known as silicone-based dielectric compound, is a versatile and essential material in various industries due to its unique properties. One of the primary uses of dielectric grease is in electrical applications, where it serves as an insulator and protector against moisture and corrosion. In automotive systems, for instance, dielectric grease is applied to electrical connectors and terminals to prevent rust and ensure reliable connections. This is particularly crucial in harsh environments where exposure to water, salt, and other corrosive substances can compromise electrical integrity. In the realm of electronics, dielectric grease plays a critical role in maintaining the performance and longevity of components. It is often used to seal and protect electronic connectors, switches, and other components from environmental factors such as humidity and dust. This application is vital in industries like aerospace, where reliability under extreme conditions is paramount. Additionally, dielectric grease is employed in the assembly of electronic devices to prevent oxidation and ensure smooth operation over time. Another significant application of dielectric grease is in the HVAC (Heating, Ventilation, and Air Conditioning) industry. Here, it is used to seal and protect electrical connections within HVAC systems from moisture and corrosion, ensuring consistent performance and reducing the risk of system failures. Similarly, in industrial settings, dielectric grease is applied to machinery and equipment to safeguard against electrical malfunctions caused by environmental factors. In marine environments, where saltwater and high humidity are prevalent, dielectric grease is indispensable for protecting electrical components on boats and ships. It helps maintain the integrity of electrical systems by preventing corrosion and ensuring reliable operation even under adverse conditions. Furthermore, in construction and building maintenance, dielectric grease is used to protect outdoor lighting fixtures and other electrical installations from weather-related damage. The versatility of dielectric grease extends beyond these specific applications; it is also used in DIY projects and household repairs. For example, it can be applied to door locks and hinges to reduce friction and protect against rust. In addition, dielectric grease can be used on battery terminals to prevent corrosion and improve battery life. Overall, the primary uses and applications of dielectric grease highlight its importance as a protective agent in a wide range of industries. Its ability to insulate, protect against corrosion, and maintain electrical integrity makes it an indispensable tool for ensuring the reliability and longevity of various systems and components. Whether in automotive, electronics, HVAC, marine, or industrial settings, dielectric grease plays a crucial role in safeguarding against environmental factors that could otherwise compromise performance and safety.
Key Properties and Characteristics
Dielectric grease, often referred to as silicone-based or dialectric compound, is a specialized lubricant designed to protect electrical connections from moisture, corrosion, and wear. Key properties and characteristics of dielectric grease make it an essential component in various applications, particularly in automotive and industrial settings. **Moisture Resistance**: One of the primary characteristics of dielectric grease is its ability to repel water and other moisture. This property is crucial for ensuring that electrical connections remain functional even in damp or humid environments, thereby preventing short circuits and corrosion. **Electrical Insulation**: Despite its name suggesting otherwise, dielectric grease does not conduct electricity; instead, it acts as an insulator. This ensures that it does not interfere with the electrical signals passing through the connections it protects. **Thermal Stability**: Dielectric grease maintains its integrity over a wide range of temperatures, typically from -50°C to 200°C (-58°F to 392°F), making it suitable for use in harsh environments where other lubricants might degrade. **Chemical Resistance**: The grease is resistant to many chemicals, including fuels, oils, and cleaning agents, which helps in preserving the integrity of electrical components even when exposed to various substances. **Lubrication**: While its primary function is not lubrication, dielectric grease does provide some degree of lubricity, helping to reduce friction between moving parts and preventing wear on connectors and terminals. **Non-Conductive**: Unlike conductive greases that can compromise electrical insulation, dielectric grease is non-conductive, ensuring that it does not create unintended paths for electrical current. **Viscosity**: The viscosity of dielectric grease is typically high enough to stay in place on vertical surfaces but still allows for easy application and spreading. This balance is important for ensuring that the grease remains effective without dripping off or running out of place over time. **Compatibility**: It is compatible with a wide range of materials commonly used in electrical connections, such as copper, aluminum, and various plastics, making it versatile across different applications. By combining these properties—moisture resistance, electrical insulation, thermal stability, chemical resistance, lubrication capabilities, non-conductivity, appropriate viscosity, and material compatibility—dielectric grease provides a robust solution for protecting and maintaining the reliability of electrical connections in diverse environments. Its use extends beyond automotive systems to include industrial machinery, marine equipment, and any scenario where electrical integrity must be preserved under challenging conditions. Understanding these key properties and characteristics highlights why dielectric grease is an indispensable tool for anyone working with electrical systems that require reliability and durability.
Benefits of Using Dielectric Grease
Dielectric grease is a versatile and highly beneficial substance that offers numerous advantages in various applications, particularly in electrical and mechanical contexts. This article delves into the significant benefits of using dielectric grease, focusing on three key areas: protection against corrosion and moisture, enhanced electrical insulation, and long-term durability and reliability. By understanding these benefits, users can better appreciate the value of incorporating dielectric grease into their maintenance and installation routines. Protection against corrosion and moisture is a critical aspect, as it ensures that components remain functional even in harsh environments. Dielectric grease forms a protective barrier that prevents water and corrosive substances from reaching sensitive parts, thereby extending their lifespan. This is especially important in outdoor or high-humidity settings where moisture can quickly compromise equipment integrity. Enhanced electrical insulation is another significant advantage, as dielectric grease provides a reliable barrier between electrical components, preventing short circuits and ensuring consistent performance. This is crucial in applications where electrical safety and reliability are paramount. Long-term durability and reliability are also enhanced by the use of dielectric grease. By reducing wear and tear on moving parts and protecting against environmental factors, dielectric grease helps maintain the operational efficiency of equipment over an extended period. Transitioning to the first supporting idea, **Protection Against Corrosion and Moisture**, it is clear that this benefit is foundational to the overall performance and longevity of equipment. By safeguarding against these common threats, dielectric grease plays a vital role in maintaining the integrity of various systems.
Protection Against Corrosion and Moisture
Protection against corrosion and moisture is a critical aspect of maintaining the integrity and longevity of electrical components, mechanical parts, and various industrial equipment. In environments where humidity, salt spray, or other corrosive substances are present, the risk of damage to sensitive systems increases significantly. This is where dielectric grease plays a pivotal role. By applying a thin layer of dielectric grease to connectors, terminals, and other exposed surfaces, you create an effective barrier against moisture and corrosive agents. Dielectric grease, also known as silicone-based grease or dialectric compound, is specifically designed to be non-conductive while providing excellent sealing properties. Unlike conductive greases that could compromise the electrical functionality of components, dielectric grease ensures that the electrical insulation remains intact. When applied correctly, it forms a hydrophobic (water-repelling) film that prevents moisture from seeping into the protected areas. This is particularly beneficial in marine environments, coastal regions, or any setting where high humidity levels are common. Moreover, dielectric grease offers protection against chemical corrosion by creating a physical barrier that prevents corrosive substances from coming into contact with the metal surfaces. This is crucial for extending the lifespan of equipment and reducing maintenance costs associated with frequent replacements or repairs due to corrosion-related failures. For instance, in automotive applications, dielectric grease can safeguard electrical connectors from the corrosive effects of road salt and moisture, ensuring reliable performance even under harsh conditions. In addition to its protective qualities, dielectric grease also enhances the reliability of electrical connections by reducing the risk of oxidation and fretting corrosion. Oxidation can lead to the formation of insulating layers on metal surfaces, which can disrupt electrical continuity. By preventing moisture from reaching these surfaces, dielectric grease helps maintain consistent conductivity and prevents intermittent failures that could arise from such issues. The ease of application is another significant advantage of using dielectric grease for corrosion and moisture protection. It can be applied using a simple brush or cloth, making it a straightforward solution for both preventive maintenance and repair tasks. Furthermore, its non-stick nature ensures that it does not attract dust or dirt particles, which could otherwise compromise its protective efficacy over time. In summary, incorporating dielectric grease into your maintenance routine offers robust protection against corrosion and moisture. Its unique properties make it an indispensable tool for ensuring the reliability and longevity of electrical and mechanical systems across various industries. By forming an impermeable barrier against corrosive agents and moisture, dielectric grease helps in preventing premature wear and tear, thereby reducing downtime and maintenance costs while enhancing overall system performance.
Enhanced Electrical Insulation
Enhanced electrical insulation is a critical aspect of maintaining the integrity and efficiency of electrical systems, and it plays a pivotal role in ensuring the reliability and safety of various applications. When discussing the benefits of using dielectric grease, it is essential to understand how this substance contributes to enhanced electrical insulation. Dielectric grease, also known as silicone-based dielectric compound, is specifically designed to provide superior insulation properties while also offering protection against moisture, corrosion, and extreme temperatures. The primary function of dielectric grease is to fill microscopic gaps and crevices on surfaces, thereby preventing the ingress of moisture and contaminants that could compromise electrical insulation. By creating a barrier between metal components and environmental elements, dielectric grease significantly reduces the risk of electrical shorts and corrosion. This is particularly important in outdoor or harsh environments where exposure to rain, snow, or high humidity could otherwise lead to electrical failures. Moreover, dielectric grease enhances electrical insulation by providing a stable and consistent dielectric strength. Unlike other materials that may degrade over time due to exposure to heat or chemicals, dielectric grease retains its insulating properties even under adverse conditions. This stability ensures that electrical connections remain secure and reliable, reducing the likelihood of intermittent faults or complete system failures. In addition to its insulating capabilities, dielectric grease also acts as a lubricant, which helps in reducing friction between moving parts such as connectors and switches. This dual functionality not only maintains electrical integrity but also extends the lifespan of components by minimizing wear and tear. For instance, in automotive applications where connectors are frequently exposed to vibrations and temperature fluctuations, dielectric grease ensures that connections remain tight and free from corrosion. The versatility of dielectric grease makes it an indispensable tool across various industries. In telecommunications, it protects sensitive equipment from environmental factors; in industrial settings, it safeguards machinery from moisture-induced failures; and in consumer electronics, it ensures the longevity of devices by preventing corrosion on critical components. In summary, enhanced electrical insulation achieved through the use of dielectric grease is crucial for maintaining the performance and reliability of electrical systems. By providing a robust barrier against moisture and contaminants while offering stable dielectric strength and lubricating properties, dielectric grease stands out as an essential component in ensuring the integrity of electrical connections across diverse applications. Its benefits extend beyond mere insulation; it enhances system reliability, reduces maintenance needs, and prolongs the lifespan of electrical components—making it an invaluable asset in any context where reliable electrical performance is paramount.
Long-Term Durability and Reliability
Long-term durability and reliability are paramount when it comes to the performance of electrical connections and components, and this is where dielectric grease truly shines. By applying dielectric grease to electrical contacts, connectors, and other components, users can significantly enhance the lifespan and operational integrity of these critical parts. Dielectric grease acts as a protective barrier against moisture, dust, and other environmental contaminants that can lead to corrosion and degradation. This barrier not only prevents the formation of rust and oxidation but also inhibits the growth of mold and mildew, ensuring that electrical pathways remain clear and unimpeded. Moreover, dielectric grease is formulated to withstand extreme temperatures without losing its effectiveness. Whether exposed to scorching heat or freezing cold, this grease maintains its viscosity and continues to shield the underlying components from harmful environmental factors. This thermal stability is crucial in applications where temperature fluctuations are common, such as in automotive systems or industrial settings. Additionally, dielectric grease is non-conductive, meaning it does not interfere with the electrical signals passing through the connections it protects. This ensures that the electrical performance remains consistent and reliable over time. The use of dielectric grease also reduces the need for frequent maintenance and repairs. By preventing corrosion and ensuring that connections remain clean and dry, it minimizes the likelihood of electrical failures. This translates into cost savings and reduced downtime, as fewer replacements and repairs are required. Furthermore, dielectric grease is easy to apply and can be used in a variety of settings, from consumer electronics to heavy-duty industrial equipment. Its versatility makes it an indispensable tool for anyone looking to ensure the long-term durability and reliability of their electrical systems. In summary, incorporating dielectric grease into your maintenance routine is a straightforward yet highly effective way to enhance the longevity and performance of electrical components. Its ability to protect against environmental hazards, maintain integrity across a wide range of temperatures, and ensure consistent electrical performance makes it an essential asset for anyone seeking to maximize the reliability of their electrical systems. Whether you are a professional technician or a DIY enthusiast, the benefits of using dielectric grease are clear: it offers unparalleled protection that translates into long-term durability and reliability.
How to Apply and Maintain Dielectric Grease
When it comes to ensuring the longevity and efficiency of electrical connections, dielectric grease plays a crucial role. This versatile substance not only protects against moisture and corrosion but also enhances the overall performance of electrical systems. However, its effectiveness is highly dependent on proper application, careful avoidance of common mistakes, and regular maintenance. In this article, we will delve into the essential aspects of working with dielectric grease, starting with **Proper Application Techniques**. Understanding how to apply dielectric grease correctly is foundational; it sets the stage for a reliable and durable connection. We will also explore **Common Mistakes to Avoid**, highlighting pitfalls that can compromise the integrity of your electrical connections. Finally, we will discuss **Regular Maintenance and Inspection**, emphasizing the importance of periodic checks to ensure that your connections remain in optimal condition. By mastering these three key areas, you can maximize the benefits of dielectric grease and maintain robust electrical systems. Let's begin by examining the critical steps involved in **Proper Application Techniques**.
Proper Application Techniques
When it comes to the proper application techniques for dielectric grease, precision and care are paramount to ensure optimal performance and longevity. Dielectric grease, also known as silicone-based grease, is a critical component in various electrical and mechanical applications due to its excellent insulating properties and resistance to moisture, heat, and corrosion. Here’s how you can apply it effectively: 1. **Preparation**: Before applying dielectric grease, make sure the surface is clean and free from any contaminants such as dirt, oil, or old grease. Use a soft cloth or brush to remove any debris. This step is crucial as any impurities can compromise the effectiveness of the grease. 2. **Application Amount**: Use the right amount of grease. Too little may not provide adequate protection, while too much can attract dirt and dust, negating its benefits. A thin, even layer is usually sufficient. 3. **Application Method**: Apply the grease using a clean brush or cloth. For smaller areas like electrical connectors, a small brush can be used to ensure precise application. For larger surfaces, a cloth may be more appropriate. 4. **Coverage**: Ensure that all surfaces that need protection are fully covered. Pay special attention to areas prone to moisture or high temperatures, as these are common points of failure. 5. **Avoid Overapplication**: Be cautious not to apply dielectric grease on moving parts or areas where it could interfere with mechanical operations. It should only be used on static surfaces where it can act as an insulator without causing any mechanical issues. 6. **Reapplication**: Depending on the environment and usage, dielectric grease may need to be reapplied periodically. Check the manufacturer's recommendations for reapplication intervals and follow any specific guidelines provided. 7. **Compatibility**: Always check the compatibility of the dielectric grease with the materials it will come into contact with. Some greases may react with certain plastics or metals, so it’s important to choose a grease that is compatible with your specific application. By following these steps meticulously, you can ensure that your dielectric grease application is effective in providing long-lasting protection against corrosion and electrical failure. Proper application not only extends the lifespan of your equipment but also maintains its performance under various environmental conditions. This attention to detail is crucial in ensuring that your electrical connections remain reliable and efficient over time.
Common Mistakes to Avoid
When applying and maintaining dielectric grease, it is crucial to avoid several common mistakes that can compromise its effectiveness and longevity. One of the most significant errors is using the wrong type of grease for the specific application. Dielectric grease comes in various formulations, each designed for different environmental conditions and materials. Using a grease that is not compatible with the materials involved can lead to degradation or failure of the electrical connections. For instance, some greases may not be suitable for high-temperature applications or may react adversely with certain plastics or metals. Another mistake is applying too much or too little grease. Excessive grease can attract dust and moisture, which defeats the purpose of using dielectric grease in the first place. Conversely, insufficient application may leave gaps in coverage, allowing moisture and contaminants to penetrate and cause electrical issues. It is essential to follow the manufacturer's guidelines for the correct amount of grease to apply. Improper cleaning of the surface before applying dielectric grease is another common oversight. Any dirt, oil, or other contaminants on the surface can prevent the grease from adhering properly, reducing its protective qualities. Always ensure that the surfaces are clean and dry before application. Additionally, neglecting to reapply dielectric grease at recommended intervals can lead to diminished protection over time. Dielectric grease does not last indefinitely and may need to be reapplied periodically, especially in harsh environments. Failing to do so can result in compromised electrical performance and increased risk of component failure. Furthermore, mixing different types of greases or using expired products can also be detrimental. Different greases have unique properties and mixing them could alter their intended performance characteristics. Similarly, using expired dielectric grease may not provide the expected level of protection due to degradation over time. Lastly, improper storage and handling of dielectric grease can affect its quality and shelf life. Grease should be stored in a cool, dry place away from direct sunlight and moisture. Always check the expiration date and ensure that the container is tightly sealed when not in use. By avoiding these common mistakes, users can ensure that their electrical connections remain protected and reliable, extending the lifespan of their equipment and preventing costly repairs. Proper application and maintenance of dielectric grease are key to maximizing its benefits and ensuring optimal performance in various electrical applications.
Regular Maintenance and Inspection
Regular maintenance and inspection are crucial components in ensuring the longevity and effectiveness of dielectric grease applications. This proactive approach not only prevents potential issues but also enhances the overall performance of electrical connections and components. To begin with, it is essential to establish a routine inspection schedule. This could be monthly, quarterly, or annually, depending on the environmental conditions and usage of the equipment. During these inspections, look for signs of wear, corrosion, or degradation on the surfaces where dielectric grease has been applied. Check for any visible cracks, dryness, or discoloration in the grease itself, as these can indicate a need for reapplication. Moreover, environmental factors such as temperature fluctuations, humidity levels, and exposure to chemicals or contaminants should be monitored closely. High temperatures can cause the grease to break down more quickly, while excessive moisture can lead to corrosion. In such cases, more frequent inspections may be necessary. Additionally, ensure that all tools and equipment used during maintenance are clean and free from debris to avoid contaminating the electrical connections. When performing maintenance, it is important to follow proper procedures to avoid damaging the components. Start by cleaning the area thoroughly with a suitable solvent to remove any dirt or old grease. Once clean, apply a new layer of dielectric grease according to the manufacturer's instructions. This typically involves applying a thin, even layer to ensure optimal coverage without over-saturating the area. Documentation of maintenance activities is also vital for tracking purposes. Keeping a log of inspections and maintenance tasks helps in identifying patterns or recurring issues that may need special attention. This record can also serve as a reference point for future maintenance personnel, ensuring continuity and consistency in care. Incorporating regular maintenance into your routine not only extends the lifespan of your equipment but also enhances safety. Electrical malfunctions due to poor maintenance can lead to serious hazards including electrical shocks, fires, or equipment failure. By staying vigilant and proactive through regular inspections and timely reapplications of dielectric grease, you can significantly reduce these risks. In conclusion, regular maintenance and inspection are indispensable practices when working with dielectric grease. They ensure that electrical connections remain protected and functional over time, thereby preventing costly repairs and enhancing operational safety. By integrating these practices into your maintenance routine, you can maximize the benefits of using dielectric grease while maintaining optimal performance of your equipment.