Chroming What Is It

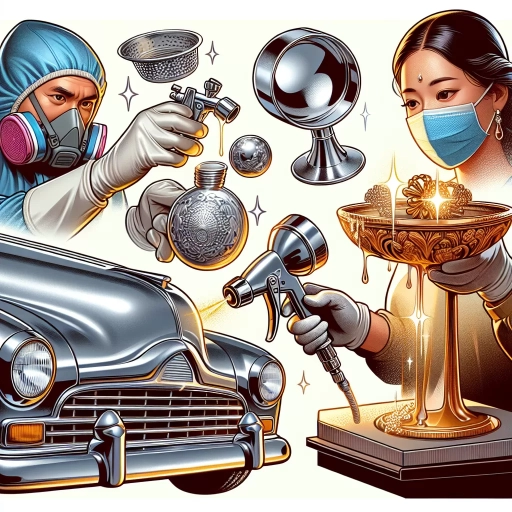
Chroming, a process that has been transforming surfaces for decades, is a multifaceted technique that enhances both aesthetics and functionality. At its core, chroming involves the application of a thin layer of chromium to metal surfaces, but its implications extend far beyond this simple definition. This article delves into the intricacies of chroming, starting with an in-depth exploration of **What is Chroming?**, where we uncover the science and history behind this process. We then examine **Types of Chroming**, highlighting the various methods and applications that cater to different needs and industries. Finally, we discuss **Benefits and Challenges of Chroming**, weighing the advantages such as corrosion resistance and visual appeal against potential drawbacks like environmental impact and cost. By understanding these facets, readers will gain a comprehensive insight into the world of chroming and its significance in modern manufacturing and design. Let us begin by answering the fundamental question: **What is Chroming?**
What is Chroming?
Chroming, a process that has been integral to various industries for decades, involves the application of a chromium layer to the surface of materials to enhance their durability, corrosion resistance, and aesthetic appeal. To fully understand chroming, it is essential to delve into its definition and origins, the chemical process involved, and its common applications. Starting with the fundamentals, **Definition and Origins** will explore how chroming emerged as a critical technique in metal finishing. This section will provide a historical context and clarify the terminology associated with chroming, setting the stage for a deeper dive into the technical aspects. The **Chemical Process Involved** will then explain the intricate steps and reactions that occur during chroming, highlighting the importance of each stage in achieving the desired outcomes. This will include discussions on electroplating, the role of chromium salts, and the environmental considerations surrounding the process. Finally, **Common Applications** will illustrate how chroming is utilized across different sectors, from automotive and aerospace to medical devices and consumer goods. This section will showcase the versatility and benefits of chroming in real-world scenarios. By examining these three key aspects, readers will gain a comprehensive understanding of what chroming entails and its significance in modern manufacturing. Let us begin by exploring the **Definition and Origins** of this vital process.
Definition and Origins
**Definition and Origins** Chroming, a process that has been integral to various industries for over a century, involves the deposition of a thin layer of chromium onto the surface of another material. This technique is primarily used to enhance the durability, corrosion resistance, and aesthetic appeal of the base material. The origins of chroming date back to the early 20th century when it was first developed as an electroplating method. The term "chroming" itself is derived from the element chromium, which is key to this process. In its earliest forms, chroming was used in the automotive industry to protect car parts from rust and wear. The first commercial application of chromium plating was patented in 1924 by Colin Fink, an American chemist who discovered that chromium could be electroplated onto other metals. This breakthrough led to widespread adoption across various sectors, including aerospace, medical devices, and consumer goods. The definition of chroming encompasses several types of chromium plating processes, each tailored for specific applications. Hard chrome plating, for instance, is used for wear-resistant coatings on industrial equipment and tools due to its exceptional hardness and durability. Decorative chrome plating, on the other hand, is commonly seen in automotive trim and household fixtures where a shiny, reflective finish is desired. The process itself involves several steps: cleaning the base material to ensure a smooth surface, applying an undercoat if necessary, and then using an electrochemical bath to deposit chromium ions onto the surface. The thickness of the chromium layer can vary depending on the intended use, ranging from a few micrometers for decorative purposes to several millimeters for heavy-duty applications. Over time, advancements in technology have refined chroming techniques, allowing for more precise control over layer thickness and uniformity. Modern methods include variations such as trivalent chromium plating, which offers environmental benefits by reducing toxic waste compared to traditional hexavalent chromium processes. Understanding the definition and origins of chroming provides a foundational insight into its significance across multiple industries. From enhancing performance in industrial settings to adding a touch of luxury in consumer products, chroming continues to play a vital role in modern manufacturing processes. Its evolution reflects ongoing efforts to balance functionality with sustainability, ensuring that this versatile technique remains relevant for years to come.
Chemical Process Involved
**Chemical Process Involved** Chroming, a process integral to various industrial and decorative applications, involves a complex series of chemical reactions to deposit a thin layer of chromium onto a substrate. At its core, chroming is an electroplating process that leverages the principles of electrolysis to achieve a durable, corrosion-resistant, and aesthetically pleasing finish. Here’s a detailed look at the chemical process involved: 1. **Preparation**: The first step in chroming is preparing the substrate. This typically involves cleaning the surface to remove any contaminants or oils that could interfere with the plating process. The substrate is then polished to ensure a smooth finish. 2. **Etching**: Some substrates may require etching to create micro-scratches on the surface, enhancing the adhesion of the chromium layer. This step is particularly important for materials like aluminum or stainless steel. 3. **Electroplating Bath**: The substrate is then immersed in an electroplating bath containing a solution of chromic acid (CrO₃) and sulfuric acid (H₂SO₄). This bath serves as the electrolyte, facilitating the transfer of chromium ions onto the substrate. 4. **Electrolysis**: An electric current is passed through the bath, with the substrate acting as the cathode (negative electrode) and an inert anode (positive electrode) such as lead or platinum. At the cathode, chromium ions (Cr³⁺) are reduced to chromium metal (Cr), depositing onto the substrate: \[ \text{Cr}^{3+} + 3\text{e}^{-} \rightarrow \text{Cr} \] 5. **Oxidation at Anode**: Simultaneously, at the anode, water molecules are oxidized to form oxygen gas and hydrogen ions: \[ 2\text{H}_2\text{O} \rightarrow \text{O}_2 + 4\text{H}^{+} + 4\text{e}^{-} \] 6. **Chromium Deposition**: The deposited chromium forms a thin, uniform layer on the substrate. The thickness of this layer can be controlled by adjusting the duration and intensity of the electric current. 7. **Post-Treatment**: After electroplating, the substrate is rinsed and dried. Depending on the application, additional treatments such as buffing or applying a protective coating may be necessary to enhance the appearance and durability of the chromium layer. This intricate chemical process ensures that the chromium coating adheres well to the substrate, providing excellent wear resistance, corrosion protection, and a reflective finish. Understanding these steps is crucial for optimizing chroming processes across various industries, from automotive to aerospace and decorative arts.
Common Applications
Chroming, a process that involves depositing a thin layer of chromium onto the surface of another material, has a wide range of applications across various industries due to its unique properties. One of the most common applications is in the automotive sector, where chroming is used to enhance the aesthetic appeal and durability of vehicle parts. Chrome-plated wheels, trim pieces, and exhaust pipes are not only visually appealing but also resistant to corrosion and wear, making them a staple in both luxury and mass-market vehicles. In the aerospace industry, chroming plays a critical role in protecting components from the harsh conditions encountered during flight. Chrome plating is applied to engine parts, fasteners, and other critical components to provide a hard, wear-resistant surface that can withstand extreme temperatures and corrosive environments. This ensures the longevity and reliability of aircraft systems. The medical field also benefits significantly from chroming. Surgical instruments and medical equipment are often chrome-plated to provide a smooth, non-reactive surface that resists corrosion and bacterial growth. This is crucial for maintaining sterility and preventing the spread of infections during surgical procedures. In addition, chroming is widely used in the manufacturing of consumer goods such as kitchen utensils, bathroom fixtures, and home appliances. Chrome-plated cutlery, faucets, and appliance handles are popular due to their attractive appearance and ease of maintenance. The chrome layer provides a protective barrier against tarnishing and corrosion, ensuring these items remain in good condition over time. Furthermore, chroming has industrial applications where high wear resistance is necessary. For example, in the textile industry, chrome-plated rollers are used in fabric production to minimize wear and tear on machinery. Similarly, in the oil and gas sector, chrome-plated components are used in drilling equipment to withstand the abrasive nature of drilling operations. Lastly, chroming is utilized in decorative arts and architecture for its reflective properties and durability. Chrome-plated fixtures and fittings are often used in high-end architectural designs to add a touch of elegance and sophistication. These elements not only enhance the aesthetic value but also require minimal upkeep due to their resistance to environmental degradation. In summary, chroming's versatility and beneficial properties make it an indispensable process across multiple sectors. From enhancing vehicle aesthetics to ensuring medical sterility and industrial durability, chroming's applications are diverse and critical to maintaining performance and longevity in various fields.
Types of Chroming
Chroming, a process that involves depositing a thin layer of chromium onto a metal surface, is a versatile technique with various applications across different industries. This article delves into the distinct types of chroming, each serving unique purposes and offering specific benefits. We will explore **Hard Chroming**, which is renowned for its durability and resistance to wear and tear, making it ideal for industrial and automotive parts. Additionally, **Decorative Chroming** will be discussed, highlighting its aesthetic appeal and widespread use in consumer goods and automotive trim. Lastly, **Electroless Chroming** will be examined, focusing on its ability to provide uniform coatings without the need for electricity, making it particularly useful for complex geometries. By understanding these different types of chroming, readers can gain insights into how each method contributes to enhancing the performance, appearance, and longevity of various products. Let's begin by diving into the robust world of **Hard Chroming**.
Hard Chroming
**Hard Chroming** Hard chroming, also known as hard chrome plating, is a specialized electroplating process that deposits a thick layer of chromium onto the surface of a metal substrate. This technique is distinct from decorative chroming due to its primary focus on enhancing the functional properties of the material rather than its aesthetic appeal. The hard chrome layer, typically ranging from 0.0002 to 0.010 inches in thickness, provides exceptional wear resistance, corrosion protection, and improved surface hardness. In industrial applications, hard chroming is often used to extend the lifespan of machinery components such as hydraulic cylinders, piston rods, and valve stems. The process involves immersing the part in a bath of chromic acid and other chemicals, where an electric current is applied to deposit chromium ions onto the surface. This results in a dense, smooth finish that can withstand high friction and abrasive environments without significant degradation. One of the key benefits of hard chroming is its ability to restore worn-out parts to their original dimensions and performance levels. For instance, in the aerospace industry, hard chrome plating is used to refurbish landing gear components and engine parts, thereby reducing maintenance costs and downtime. Additionally, the process can be applied to new parts to prevent wear and tear from the outset. The durability of hard chrome plating also makes it an essential coating in harsh environments such as those found in marine and chemical processing industries. Here, it protects against corrosion from seawater or corrosive chemicals, ensuring that critical equipment remains operational over extended periods. Despite its numerous advantages, hard chroming requires careful consideration of environmental and health impacts due to the use of hexavalent chromium, a known carcinogen. Modern facilities must adhere to stringent regulations and safety protocols to minimize exposure risks during the plating process. In summary, hard chroming is a vital industrial coating technique that significantly enhances the performance and longevity of metal components. Its unique combination of wear resistance, corrosion protection, and surface hardness makes it indispensable across various sectors where reliability and durability are paramount. As technology continues to evolve, efforts are being made to develop safer alternatives while maintaining the superior qualities that hard chroming offers.
Decorative Chroming
Decorative chroming is a specialized process within the broader category of chroming, which transforms ordinary surfaces into visually stunning and highly reflective finishes. This technique is particularly popular in automotive, aerospace, and luxury goods industries where aesthetic appeal is paramount. Unlike functional chroming, which focuses on enhancing durability and corrosion resistance, decorative chroming prioritizes visual impact. The process typically involves electroplating a thin layer of chromium onto a substrate, often after extensive preparation to ensure a flawless base. The chromium layer can range from a few micrometers to several millimeters in thickness, depending on the desired level of reflectivity and durability. For instance, in the automotive sector, decorative chroming is used to create the mirror-like finishes seen on car trim, wheels, and other exterior components. These elements not only enhance the vehicle's appearance but also contribute to its overall perceived value. One of the key challenges in decorative chroming is achieving uniformity and avoiding imperfections such as pits, scratches, or uneven plating. To overcome these issues, manufacturers employ advanced techniques like triple-plating (copper-nickel-chromium) or quad-plating (copper-nickel-chromium-chromium), which involve multiple layers to ensure a smooth, even finish. Additionally, pre-treatment processes such as polishing and buffing are crucial for removing surface defects that could compromise the final appearance. Beyond aesthetics, decorative chroming also offers some functional benefits. Chromium has inherent properties that make it resistant to corrosion and wear, which means that chromed surfaces can withstand environmental elements better than uncoated ones. However, it's important to note that the primary purpose here remains visual enhancement rather than long-term protection. In recent years, there has been a trend towards more sustainable and eco-friendly methods of decorative chroming. Traditional hexavalent chromium electroplating has been criticized for its environmental and health impacts due to the toxic nature of hexavalent chromium. In response, many manufacturers are adopting trivalent chromium processes or exploring alternative materials like nickel-free coatings that offer similar reflectivity without the associated risks. The versatility of decorative chroming extends beyond traditional applications; it is increasingly being used in art and design to create striking pieces that combine functionality with artistic expression. For example, designers might use chromed finishes on furniture or architectural elements to add a touch of luxury and sophistication. In conclusion, decorative chroming represents a sophisticated blend of technology and artistry that elevates ordinary objects into extraordinary visual statements. Its applications span multiple industries where appearance is crucial, offering not just beauty but also some level of durability. As technology continues to evolve, we can expect even more innovative approaches to this process that balance aesthetics with sustainability and safety.
Electroless Chroming
**Electroless Chroming** Electroless chroming, also known as chemical nickel plating or autocatalytic nickel plating, is a unique and highly specialized process within the broader category of chroming techniques. Unlike traditional electroplating methods that rely on an external electric current to deposit metal ions onto a substrate, electroless chroming uses a chemical reduction reaction to achieve the same result. This process involves immersing the material to be plated in a bath containing nickel ions and a reducing agent, such as sodium hypophosphite or sodium borohydride. The reducing agent catalyzes the deposition of nickel onto the surface of the material, creating a uniform, corrosion-resistant coating without the need for an electric current. One of the key advantages of electroless chroming is its ability to produce a consistent and uniform thickness across complex geometries and irregular surfaces. This makes it particularly useful for coating parts with intricate designs or those that are difficult to reach with traditional electroplating methods. Additionally, electroless chroming can be applied to a wide range of materials, including metals, plastics, and ceramics, making it versatile for various industrial applications. The properties of electroless nickel coatings are also noteworthy. These coatings exhibit excellent wear resistance, corrosion protection, and high ductility, which are crucial for components subjected to harsh environments or heavy use. For instance, in aerospace and automotive industries, electroless nickel coatings are often used to protect engine components from corrosion and wear. Moreover, the process can be tailored to produce different types of coatings by varying the composition of the bath solution. For example, adding phosphorus to the nickel bath can enhance the coating's hardness and corrosion resistance. Another significant benefit of electroless chroming is its ability to enhance the dimensional stability of parts. Because the coating process does not involve the use of an electric current, there is no risk of hydrogen embrittlement—a common issue in traditional electroplating that can lead to material weakening. This makes electroless chroming particularly suitable for applications where maintaining the structural integrity of the base material is critical. In terms of environmental impact, electroless chroming is generally considered more environmentally friendly compared to some other plating processes. The absence of an electric current reduces energy consumption, and the chemical baths used can be more easily controlled and managed to minimize waste and pollution. However, it's important to note that electroless chroming has its own set of challenges. The process requires precise control over bath chemistry and temperature to ensure consistent results. Additionally, the cost of the chemicals involved can be higher than those used in traditional electroplating methods, making it a more expensive option for some applications. In summary, electroless chroming offers a unique combination of uniformity, versatility, and performance that makes it an invaluable technique in various industrial sectors. Its ability to coat complex geometries uniformly, provide excellent corrosion and wear resistance, and maintain dimensional stability makes it a preferred choice for critical applications where reliability and durability are paramount. As technology continues to evolve, the role of electroless chroming is likely to expand further, offering innovative solutions to meet the demanding requirements of modern industries.
Benefits and Challenges of Chroming
Chroming, a process that involves depositing a thin layer of chromium onto the surface of metals, offers a multitude of benefits and presents several challenges. On one hand, chroming enhances corrosion resistance and durability, making it an essential treatment for various industrial and automotive applications. Additionally, it boosts aesthetic appeal and versatility, allowing for a wide range of decorative and functional uses. However, it also raises significant environmental and health concerns due to the toxic nature of chromium and the potential for hazardous waste generation. Understanding these aspects is crucial for harnessing the full potential of chroming while mitigating its negative impacts. This article delves into these key areas, starting with the critical advantage of corrosion resistance and durability, which underscores the foundational value of chroming in extending the lifespan of metal components.
Corrosion Resistance and Durability
**Corrosion Resistance and Durability** Chroming, a process that involves depositing a thin layer of chromium onto the surface of metals, significantly enhances the corrosion resistance and durability of the underlying material. This is particularly crucial in environments where exposure to moisture, salt, and other corrosive substances is prevalent. Chromium's inherent properties make it an excellent barrier against corrosion. When chromium is applied, it forms a stable oxide layer that protects the base metal from reacting with oxygen and water, thereby preventing rust and other forms of degradation. This protective coating not only extends the lifespan of the material but also maintains its structural integrity and aesthetic appeal over time. In industrial settings, chroming is often used on components that are subject to harsh conditions such as high temperatures, humidity, and chemical exposure. For instance, in the automotive industry, chromed parts like exhaust pipes and engine components exhibit superior resistance to corrosion compared to their uncoated counterparts. Similarly, in marine environments where saltwater can be particularly corrosive, chromed fittings and hardware last longer and require less maintenance. The durability of chromed surfaces also makes them ideal for applications where wear and tear are significant concerns. Chromium's hardness is one of its standout features; it is much harder than most base metals, which means it can withstand scratches and abrasions more effectively. This is why chromed tools and machinery parts are preferred in industries where heavy use is common. Additionally, the smooth surface finish of chromed materials reduces friction, which can lead to increased efficiency and reduced energy consumption in mechanical systems. However, achieving optimal corrosion resistance and durability through chroming requires careful consideration of several factors. The thickness of the chromium layer, for example, must be precisely controlled to ensure maximum protection without compromising the mechanical properties of the base metal. Furthermore, the preparation of the surface before chroming is critical; any imperfections or contaminants can lead to weak spots in the coating that may compromise its effectiveness. Despite these challenges, advancements in chroming technologies have made it possible to achieve highly consistent and reliable results. Modern electroplating techniques allow for precise control over the deposition process, ensuring uniform thickness and adherence of the chromium layer. Moreover, post-treatment processes such as polishing can further enhance the surface quality and improve the overall performance of chromed components. In summary, chroming offers unparalleled benefits in terms of corrosion resistance and durability. By forming a protective barrier against environmental factors and enhancing the mechanical properties of metals, chroming extends the service life of components while maintaining their functionality and appearance. While there are challenges associated with ensuring optimal coating quality, advancements in technology have mitigated many of these issues, making chroming an indispensable process across various industries.
Aesthetic Appeal and Versatility
Aesthetic appeal and versatility are two of the most compelling benefits of chroming, a process that involves applying a thin layer of chromium to the surface of materials. The aesthetic appeal of chromed surfaces is undeniable; they exude a sleek, reflective finish that enhances the visual appeal of any object. Whether it's a car bumper, a kitchen faucet, or a piece of furniture, chroming can transform ordinary items into eye-catching pieces that command attention. This is particularly evident in automotive and industrial design, where chromed parts not only add a touch of luxury but also convey durability and high-quality craftsmanship. Beyond its visual allure, chroming offers remarkable versatility. Chromium's unique properties make it an ideal coating for a wide range of applications. It is highly resistant to corrosion and wear, making it perfect for components that are exposed to harsh environments or heavy use. For instance, in the aerospace industry, chromed parts are often used due to their ability to withstand extreme temperatures and corrosive conditions. Similarly, in medical equipment, chroming provides a hygienic surface that is easy to clean and resistant to bacterial growth. The versatility of chroming also extends to its compatibility with various base materials. Whether it's steel, aluminum, or even plastics, chromium can be applied to enhance the performance and appearance of these substrates. This adaptability makes chroming a go-to solution across diverse industries, from consumer goods to heavy machinery. Additionally, the process itself can be tailored to meet specific requirements; for example, different thicknesses of chromium can be applied depending on the intended use of the component. However, achieving such aesthetic appeal and versatility comes with its own set of challenges. One of the primary hurdles is the environmental impact associated with the chroming process. Chromium plating involves the use of hexavalent chromium, a known carcinogen that poses significant health risks if not handled properly. As a result, stringent regulations and safety protocols must be adhered to during the application process. Furthermore, the cost of chroming can be prohibitive for some applications due to the complexity of the process and the need for specialized equipment. Despite these challenges, advancements in technology have led to more sustainable and cost-effective alternatives. For example, trivalent chromium plating has emerged as a safer and more environmentally friendly option compared to traditional hexavalent chromium methods. This shift towards greener technologies not only mitigates environmental concerns but also opens up new avenues for innovation in chroming. In conclusion, the aesthetic appeal and versatility of chroming make it an invaluable technique across various industries. While it presents certain challenges related to environmental impact and cost, ongoing innovations are addressing these issues. As technology continues to evolve, it is likely that chroming will remain a preferred choice for enhancing both the appearance and performance of materials, ensuring that this timeless process remains relevant in an ever-changing world.
Environmental and Health Concerns
When considering the benefits and challenges of chroming, it is crucial to delve into the environmental and health concerns associated with this process. Chroming, particularly electroplating with chromium, involves the use of toxic chemicals such as hexavalent chromium (Cr(VI)), which poses significant risks to both human health and the environment. From a health perspective, exposure to Cr(VI) can lead to severe respiratory problems, including lung cancer and other respiratory diseases. Workers in chroming industries are at high risk due to inhalation of chromium dust and fumes, highlighting the need for stringent safety protocols and protective gear. Moreover, the improper disposal of chromium waste can contaminate soil and water sources, affecting not only local ecosystems but also human populations relying on these resources for drinking water and agriculture. Environmentally, chroming processes contribute to pollution through the release of hazardous substances into air and water. The effluent from chroming operations often contains heavy metals like chromium, nickel, and cadmium, which can accumulate in aquatic life and enter the food chain, causing long-term ecological damage. Additionally, the energy-intensive nature of chroming contributes to greenhouse gas emissions, exacerbating climate change. Efforts to mitigate these impacts include the development of more sustainable chroming technologies, such as trivalent chromium (Cr(III)) electroplating, which is less toxic than Cr(VI). However, even these alternatives require careful management to prevent environmental degradation. Regulatory bodies around the world have implemented strict guidelines to control chromium emissions and ensure safe working conditions. For instance, the Occupational Safety and Health Administration (OSHA) in the United States has set permissible exposure limits for Cr(VI) in workplaces. Similarly, environmental regulations mandate proper waste treatment and disposal practices to minimize the ecological footprint of chroming operations. Despite these measures, ongoing research and innovation are essential to develop more environmentally friendly and health-conscious chroming methods that balance industrial needs with sustainability and public health. In conclusion, while chroming offers numerous benefits in terms of corrosion resistance and aesthetic appeal, it is imperative to address the associated environmental and health concerns. By adopting safer technologies, enforcing stringent regulations, and promoting sustainable practices, we can mitigate the adverse effects of chroming and ensure a healthier environment for both current and future generations. This balanced approach is crucial for harnessing the benefits of chroming while minimizing its negative impacts on human health and the environment.