What Is A Pneumatic System

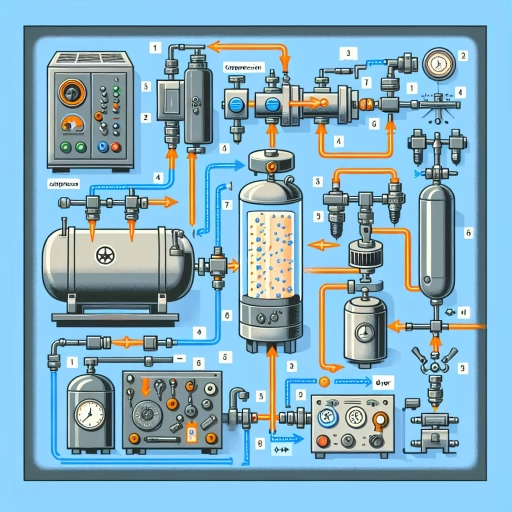
In the realm of industrial automation and mechanical engineering, pneumatic systems play a crucial role in powering a wide range of applications, from manufacturing processes to medical devices. These systems leverage compressed air to generate motion and force, offering a reliable, efficient, and safe alternative to hydraulic and electrical systems. Understanding the intricacies of pneumatic systems is essential for engineers, technicians, and anyone involved in their design, operation, and maintenance. This article delves into the fundamental aspects of pneumatic systems, starting with an **Introduction to Pneumatic Systems**, where we explore the basic principles and historical context of these systems. We then examine the **Components and Mechanisms of Pneumatic Systems**, detailing the various parts that make up these systems and how they interact. Finally, we discuss the **Design, Operation, and Maintenance of Pneumatic Systems**, providing insights into best practices for optimizing performance and ensuring longevity. By grasping these key elements, readers will gain a comprehensive understanding of how pneumatic systems function and how they can be effectively utilized in various industrial settings. Let us begin with an **Introduction to Pneumatic Systems** to lay the groundwork for this in-depth exploration.
Introduction to Pneumatic Systems
Pneumatic systems, which utilize compressed air or gas to transmit energy, are a cornerstone of modern industrial and technological advancements. These systems have evolved significantly over the years, transforming from simple tools to sophisticated mechanisms that power a wide range of applications. To fully appreciate the complexity and utility of pneumatic systems, it is essential to understand their definition and basic principles, which form the foundation of their operation. Additionally, exploring the historical development and evolution of these systems provides valuable insights into how they have adapted to meet changing industrial needs. Finally, examining their common applications across various industries highlights their versatility and importance in sectors such as manufacturing, healthcare, and transportation. This article will delve into these critical aspects, offering a comprehensive introduction to pneumatic systems that will equip readers with a thorough understanding of this vital technology. **Introduction to Pneumatic Systems**
Definition and Basic Principles
In the realm of mechanical engineering, pneumatic systems play a crucial role in various industrial and technological applications. At its core, a **pneumatic system** is defined as a network of components that utilize compressed air or gas to transmit energy and perform mechanical work. This definition underscores the fundamental principle that pneumatic systems rely on the manipulation of air pressure to achieve their intended functions. The basic principles governing pneumatic systems are rooted in the properties of gases and the laws of thermodynamics. **Compressibility** is a key characteristic; unlike liquids, gases can be compressed significantly, allowing for efficient storage and transmission of energy. The **ideal gas law** (PV = nRT) is central to understanding how pressure, volume, and temperature interact within these systems. Additionally, **Boyle's Law** and **Charles' Law** provide insights into how changes in pressure and temperature affect the volume of gases. Another essential principle is **pressure**, which is the force exerted per unit area on the surface of an object. In pneumatic systems, pressure is generated by compressors that squeeze air into smaller volumes, increasing its pressure. This compressed air is then distributed through a network of pipes and valves to various actuators such as cylinders, motors, and valves. These actuators convert the potential energy stored in the compressed air into kinetic energy, enabling tasks like lifting, moving, or rotating objects. **Flow rate** and **velocity** are also critical factors. The flow rate determines how much air is delivered per unit time, while velocity refers to the speed at which air moves through the system. Balancing these parameters ensures efficient operation and minimizes energy losses due to friction and turbulence. Furthermore, pneumatic systems often incorporate **control elements** such as regulators, filters, and lubricators to maintain optimal operating conditions. Regulators adjust the pressure to desired levels, filters remove contaminants that could damage components, and lubricators add oil to the compressed air to reduce wear on moving parts. Understanding these basic principles is vital for designing, operating, and maintaining pneumatic systems effectively. By leveraging the properties of compressed air and adhering to fundamental laws of physics, engineers can create robust and reliable systems that drive machinery in diverse industries ranging from manufacturing to healthcare. This foundational knowledge serves as a cornerstone for more advanced topics in pneumatic technology, ensuring that systems operate safely, efficiently, and with precision.
Historical Development and Evolution
The historical development and evolution of pneumatic systems are deeply intertwined with the advancement of technology and human ingenuity. The concept of using compressed air to perform work dates back to ancient civilizations, where primitive pneumatic devices were used in various forms. For instance, the ancient Greeks employed bellows to control airflow in metalworking processes around 200 BCE. However, it wasn't until the Industrial Revolution that pneumatic systems began to take shape as we know them today. In the late 18th and early 19th centuries, inventors like Joseph Bramah and William George Armstrong developed more sophisticated pneumatic tools and machinery. Bramah's hydraulic press, which used compressed air to amplify force, laid foundational principles for later pneumatic innovations. Meanwhile, Armstrong's hydraulic accumulator further refined the use of compressed fluids for industrial applications. The late 19th and early 20th centuries saw significant advancements in pneumatic technology. The invention of the pneumatic tire by John Boyd Dunlop in 1888 and the development of pneumatic tools by Charles B. Porter in the early 1900s revolutionized industries such as manufacturing and construction. These tools, powered by compressed air, offered greater efficiency and precision compared to their mechanical counterparts. The mid-20th century marked a pivotal period in the evolution of pneumatic systems with the introduction of modern air compressors and control valves. These advancements enabled more precise control over airflow and pressure, making pneumatic systems integral to various sectors including automotive, aerospace, and healthcare. The development of pneumatic cylinders, actuators, and sensors further expanded the capabilities of these systems. In recent decades, advancements in materials science and electronics have led to the creation of more efficient, durable, and intelligent pneumatic components. Modern pneumatic systems often incorporate electronic controls, sensors, and automation technologies that enhance performance, safety, and energy efficiency. This integration has enabled real-time monitoring, predictive maintenance, and optimized system operation. Today, pneumatic systems are ubiquitous across diverse industries due to their reliability, flexibility, and cost-effectiveness. From powering assembly lines in manufacturing plants to providing critical support in medical devices and aircraft systems, pneumatics continue to evolve with technological innovations. As we move forward into an era of Industry 4.0 and smart manufacturing, the role of pneumatic systems is expected to become even more pivotal as they integrate seamlessly with other technologies to drive efficiency and innovation. Understanding this historical development is crucial for appreciating the complexity and versatility of modern pneumatic systems.
Common Applications Across Industries
Pneumatic systems, which utilize compressed air or gas to transmit energy, are versatile and widely applied across various industries due to their reliability, efficiency, and safety. In **manufacturing**, pneumatic systems power tools and machinery such as drills, saws, and assembly line equipment, enabling precise and consistent operations. For instance, in automotive manufacturing, pneumatic tools are used for tasks like riveting and welding, while in food processing, they help with packaging and sorting products. In **healthcare**, pneumatic systems are integral to medical devices such as ventilators, anesthesia machines, and surgical tools. These systems ensure precise control over airflow and pressure, which is critical for patient care. Additionally, in **pharmaceuticals**, pneumatic conveyors are used to transport powders and granules safely and efficiently, minimizing contamination risks. The **construction industry** also heavily relies on pneumatic systems for powering heavy-duty equipment like jackhammers, air compressors, and concrete mixers. These tools enhance productivity and reduce manual labor, making construction projects more manageable and efficient. In **aerospace**, pneumatic systems play a crucial role in aircraft maintenance and operation. They are used in landing gear systems, brake systems, and even in some aircraft engines. The reliability of pneumatic components is essential for ensuring safety during flight operations. Furthermore, **agriculture** benefits from pneumatic systems in irrigation systems and crop processing machinery. These systems help automate tasks such as sorting and packaging produce, thereby increasing farm productivity. In **oil and gas**, pneumatic valves and actuators are used to control fluid flow in pipelines and processing facilities. Their ability to operate in harsh environments makes them ideal for this industry. Lastly, **consumer goods** manufacturing often employs pneumatic systems for packaging and assembly lines. For example, in beverage bottling plants, pneumatic machinery helps fill bottles accurately and efficiently. The widespread adoption of pneumatic systems across these diverse industries underscores their adaptability and effectiveness. By leveraging compressed air or gas as a power source, these systems offer a clean, safe, and efficient way to perform a variety of tasks that are essential to modern industrial operations. Understanding the principles of pneumatic systems is therefore crucial for anyone involved in these sectors, as it can lead to improved performance, reduced maintenance costs, and enhanced overall productivity.
Components and Mechanisms of Pneumatic Systems
Pneumatic systems, which utilize compressed air to perform mechanical work, are fundamental in various industrial and technological applications. These systems rely on a combination of key components and mechanisms to operate efficiently. At the heart of any pneumatic system are the compressors, valves, and actuators, which work in tandem to generate, control, and apply the compressed air. Understanding these components is crucial for designing and maintaining effective pneumatic systems. Additionally, pneumatic cylinders play a vital role in converting the energy stored in compressed air into linear motion, enabling tasks such as lifting, pushing, and pulling. The distribution of compressed air throughout the system is facilitated by piping and tubing systems, which must be carefully designed to ensure optimal performance and safety. This article will delve into these essential aspects of pneumatic systems, providing a comprehensive overview of their components and mechanisms. By exploring compressors, valves, and actuators; pneumatic cylinders and their functions; and piping and tubing systems for air distribution, we will gain a deeper understanding of how these elements integrate to form a cohesive and functional pneumatic system. This introduction sets the stage for a detailed exploration of the intricacies of pneumatic systems, leading us to a thorough **Introduction to Pneumatic Systems**.
Key Components: Compressors, Valves, and Actuators
In the intricate world of pneumatic systems, several key components play crucial roles in ensuring efficient and reliable operation. Among these, compressors, valves, and actuators stand out as fundamental elements that drive the functionality of these systems. **Compressors** are the heart of any pneumatic system, responsible for generating the compressed air that powers the entire setup. These machines convert electrical or mechanical energy into potential energy stored in compressed air, which is then distributed through a network of pipes to various parts of the system. Compressors come in various types, including reciprocating, rotary screw, and centrifugal models, each suited to different applications based on factors such as flow rate, pressure requirements, and operational efficiency. **Valves** serve as the control mechanisms within pneumatic systems, regulating the flow of compressed air to different parts of the system. They can be categorized into several types, including check valves that prevent backflow, ball valves that control flow direction, and solenoid valves that are electronically controlled to manage airflow precisely. Valves are essential for directing air to actuators at the right time and in the correct amount, ensuring smooth and controlled operation of pneumatic devices. **Actuators**, often in the form of cylinders or motors, are the end-effectors of pneumatic systems. They convert the potential energy stored in compressed air into mechanical energy, performing tasks such as lifting, pushing, or rotating objects. Pneumatic cylinders are commonly used for linear motion applications, while pneumatic motors are preferred for rotational tasks. Actuators are designed to handle various loads and speeds, making them versatile components that can be adapted to a wide range of industrial and commercial applications. The synergy between these components is what makes pneumatic systems so effective. Compressors provide the necessary air pressure, valves manage the airflow with precision, and actuators execute the desired actions. Together, they form a robust and reliable system capable of performing complex tasks with high accuracy and efficiency. Understanding these key components is essential for designing, maintaining, and optimizing pneumatic systems to meet specific operational needs. By selecting the right compressor, valve configuration, and actuator type, engineers can tailor pneumatic systems to achieve optimal performance in various industries, from manufacturing and automation to medical devices and aerospace. This harmonious integration of compressors, valves, and actuators underscores the sophistication and versatility of modern pneumatic technology.
Pneumatic Cylinders and Their Functions
Pneumatic cylinders are a crucial component of pneumatic systems, playing a pivotal role in converting compressed air into mechanical energy. These cylinders are essentially actuators that utilize the pressure of compressed air to generate linear motion, which is then used to perform various tasks such as lifting, pushing, and pulling. The basic structure of a pneumatic cylinder includes a cylindrical body, a piston, and two ports for air inlet and outlet. When compressed air enters the cylinder through one port, it pushes the piston in a linear direction, while the air exiting through the other port allows the piston to return to its original position. The functions of pneumatic cylinders are diverse and widespread across different industries. In manufacturing, they are used in assembly lines for tasks like clamping, pressing, and lifting heavy loads. In automation, they enable precise control over movements, making them ideal for applications requiring repetitive and consistent actions. Additionally, pneumatic cylinders are integral in material handling systems where they facilitate the movement of goods along conveyor belts and in storage facilities. One of the key advantages of pneumatic cylinders is their simplicity and reliability. Unlike hydraulic systems, which require complex fluid handling and can be prone to leakage, pneumatic systems are cleaner and easier to maintain. The use of compressed air also makes them safer in environments where sparks or electrical components could pose a risk. Furthermore, pneumatic cylinders can be easily customized to fit specific needs by adjusting factors such as stroke length, bore size, and mounting configurations. In terms of operational efficiency, pneumatic cylinders offer quick response times and high force-to-weight ratios, making them suitable for applications requiring rapid and precise movements. They are also relatively inexpensive compared to other types of actuators, contributing to their widespread adoption in various industrial settings. Moreover, modern advancements have led to the development of specialized types of pneumatic cylinders such as rodless cylinders and telescoping cylinders. Rodless cylinders eliminate the need for a rod extending from the cylinder body, allowing for more compact designs and increased flexibility in tight spaces. Telescoping cylinders, on the other hand, consist of multiple stages that extend in a telescopic manner, enabling longer strokes without the need for a single long cylinder. In summary, pneumatic cylinders are indispensable components of pneumatic systems due to their ability to efficiently convert compressed air into mechanical energy. Their versatility, reliability, and ease of maintenance make them a preferred choice across various industries for a wide range of applications. Understanding the functions and mechanisms of pneumatic cylinders is essential for optimizing the performance and efficiency of pneumatic systems.
Piping and Tubing Systems for Air Distribution
Piping and tubing systems are crucial components in air distribution within pneumatic systems, ensuring efficient and reliable transmission of compressed air. These systems consist of a network of pipes and tubes that connect various parts of the pneumatic setup, including compressors, valves, actuators, and other equipment. The design and installation of these systems are critical to maintain optimal performance, as they directly impact the overall efficiency and longevity of the pneumatic system. **Materials and Construction:** Piping and tubing materials are selected based on durability, resistance to corrosion, and compatibility with the operating conditions. Common materials include steel, copper, aluminum, and PVC. Steel pipes are often used for high-pressure applications due to their strength and durability, while copper and aluminum are preferred for lower-pressure systems due to their flexibility and resistance to corrosion. PVC pipes are commonly used in less demanding environments due to their cost-effectiveness and ease of installation. **Components:** The piping and tubing system includes several key components. Fittings such as elbows, tees, couplings, and adapters are used to connect and redirect the pipes and tubes. Valves control the flow of air, allowing for regulation and isolation of different parts of the system. Filters and dryers are essential to remove moisture and contaminants from the compressed air, ensuring clean and dry air is delivered to the actuators and other pneumatic devices. **Installation Considerations:** Proper installation is vital to prevent leaks, reduce energy losses, and maintain system integrity. This involves careful planning of the pipe layout to minimize bends and sharp turns, which can cause friction losses and reduce airflow efficiency. Support structures are necessary to prevent sagging or damage to the pipes and tubes. Regular maintenance, including inspections for leaks and corrosion, is also crucial to ensure the longevity of the system. **Safety and Efficiency:** Safety is a paramount concern in the design and operation of piping and tubing systems. Proper sizing of pipes and tubes ensures that the system operates within safe pressure limits, reducing the risk of explosions or other hazards. Efficient design also helps in minimizing energy consumption by reducing friction losses and ensuring that the compressed air is delivered at the required pressure and flow rate. This not only saves energy but also extends the life of the pneumatic equipment. In summary, piping and tubing systems are fundamental to the effective operation of pneumatic systems, facilitating the distribution of compressed air with precision and reliability. By selecting appropriate materials, using the right components, and ensuring proper installation and maintenance, these systems can optimize performance, enhance safety, and contribute significantly to the overall efficiency of pneumatic applications.
Design, Operation, and Maintenance of Pneumatic Systems
Pneumatic systems, which utilize compressed air to power machinery and tools, are integral to various industries including manufacturing, construction, and healthcare. The effectiveness and reliability of these systems depend on meticulous design, safe operation, and regular maintenance. This article delves into the critical aspects of pneumatic systems, starting with **System Design Considerations and Best Practices**, where we explore the principles and guidelines that ensure efficient and robust system architecture. We then discuss **Operational Safety and Efficiency Measures**, highlighting the protocols and technologies that safeguard personnel and optimize system performance. Finally, we outline **Maintenance Strategies for Optimal Performance**, providing insights into the routine checks and proactive measures necessary to extend the lifespan of pneumatic components. By understanding these key elements, users can maximize the benefits of pneumatic systems while minimizing downtime and risks. This comprehensive guide serves as a foundational resource, transitioning seamlessly into an **Introduction to Pneumatic Systems**, where the basics of how these systems work are detailed.
System Design Considerations and Best Practices
When designing, operating, and maintaining pneumatic systems, several key considerations and best practices must be adhered to ensure optimal performance, efficiency, and safety. **System Design Considerations** are paramount from the outset. First, it is crucial to define the system's requirements and specifications clearly, including the type of tasks it will perform, the volume of air needed, and the pressure levels required. This helps in selecting appropriate components such as compressors, valves, actuators, and piping. The layout of the system should be well-planned to minimize energy losses due to friction and ensure easy access for maintenance. Proper sizing of components is essential; undersized components can lead to inefficiency and premature wear, while oversized components can be wasteful and costly. **Best Practices** in system design include the use of standardized components to simplify maintenance and reduce the need for specialized tools. Implementing a modular design allows for easier expansion or modification of the system in the future. Additionally, incorporating safety features such as pressure relief valves and emergency shutdown mechanisms is vital to prevent accidents and protect both the system and its operators. During **Operation**, regular monitoring of system performance is critical. This involves checking for leaks, which can significantly reduce efficiency and increase energy costs. Proper lubrication of moving parts in pneumatic components is also essential to extend their lifespan. Operators should be trained on how to use the system safely and efficiently, understanding how to read gauges, operate valves, and troubleshoot common issues. In terms of **Maintenance**, a proactive approach is highly recommended. Scheduled maintenance routines should include cleaning filters, inspecting hoses for signs of wear or damage, and replacing worn-out parts before they fail. Keeping detailed records of maintenance activities helps in identifying patterns of wear and tear, allowing for more effective preventive maintenance strategies. Furthermore, using condition monitoring techniques such as vibration analysis or ultrasonic leak detection can help identify potential issues before they become major problems. By adhering to these design considerations and best practices, pneumatic systems can operate reliably, efficiently, and safely over their lifespan. This not only ensures continuous production but also reduces downtime, lowers operational costs, and enhances overall system longevity. Effective design, operation, and maintenance are interlinked aspects that collectively contribute to the optimal functioning of pneumatic systems.
Operational Safety and Efficiency Measures
Operational safety and efficiency are paramount when designing, operating, and maintaining pneumatic systems. To ensure these systems function optimally while minimizing risks, several key measures must be implemented. First, **design integrity** is crucial; engineers should adhere to industry standards and best practices to create systems that are inherently safe and efficient. This includes selecting appropriate materials, designing for redundancy where necessary, and incorporating safety features such as pressure relief valves to prevent over-pressurization. During **operation**, regular monitoring and maintenance are essential. Operators should be trained to recognize potential hazards and perform routine checks on components like air compressors, valves, and actuators. Implementing a preventive maintenance schedule helps in identifying and addressing issues before they escalate into major problems. Additionally, the use of advanced technologies such as condition monitoring sensors can provide real-time data on system performance, enabling proactive maintenance. **Efficiency measures** also play a critical role in optimizing pneumatic system performance. Minimizing air leaks through regular inspections and sealing any detected leaks can significantly reduce energy consumption. Proper sizing of components ensures that the system operates within its designed parameters, avoiding unnecessary energy expenditure. Furthermore, optimizing air pressure levels and using energy-efficient compressors can lead to substantial savings in operational costs. In terms of **safety protocols**, it is vital to establish clear guidelines for handling emergencies such as system failures or leaks. Emergency shutdown procedures should be well-documented and easily accessible to all personnel involved in the operation of the pneumatic system. Personal protective equipment (PPE) must be provided and used as required, especially when working with high-pressure systems or in environments where air quality could be compromised. Finally, **training and documentation** are indispensable for ensuring both safety and efficiency. Comprehensive training programs should be in place for operators and maintenance personnel to ensure they understand the intricacies of the pneumatic system and can perform their duties safely and effectively. Detailed documentation of system design, operation manuals, maintenance records, and safety procedures helps in maintaining consistency across different shifts and personnel changes. By integrating these operational safety and efficiency measures into the design, operation, and maintenance of pneumatic systems, organizations can significantly reduce downtime, enhance overall system reliability, and create a safer working environment for their employees. This holistic approach not only complies with regulatory requirements but also contributes to long-term cost savings and improved productivity.
Maintenance Strategies for Optimal Performance
**Maintenance Strategies for Optimal Performance** To ensure the optimal performance and longevity of pneumatic systems, a well-structured maintenance strategy is crucial. This involves a combination of preventive, predictive, and corrective maintenance approaches. **Preventive Maintenance** focuses on regular inspections and scheduled tasks to prevent failures. For pneumatic systems, this includes checking air filters, lubricating components, and inspecting hoses and fittings for signs of wear or damage. Regularly cleaning and replacing air filters, for instance, helps maintain air quality and prevents contamination that could lead to system malfunctions. **Predictive Maintenance** leverages advanced technologies such as sensors and data analytics to monitor system performance in real-time. By installing pressure sensors, flow meters, and temperature sensors, operators can detect anomalies before they escalate into major issues. This proactive approach allows for timely interventions, reducing downtime and enhancing overall system reliability. For example, monitoring pressure drops can indicate potential leaks or blockages, enabling prompt action to rectify the issue before it affects production. **Corrective Maintenance** addresses issues as they arise, focusing on swift and effective repairs to minimize downtime. This involves having a well-stocked inventory of spare parts and trained personnel who can quickly diagnose and fix problems. Implementing a root cause analysis (RCA) after each failure helps identify underlying causes, allowing for improvements in both design and maintenance procedures. Additionally, documenting maintenance activities provides valuable insights for future improvements and helps in optimizing maintenance schedules. Effective maintenance also involves **Training and Documentation**. Ensuring that maintenance personnel are adequately trained on the specific pneumatic system components and procedures is essential. Comprehensive documentation, including manuals, diagrams, and historical maintenance records, facilitates efficient troubleshooting and repair processes. Furthermore, adhering to industry standards and best practices ensures compliance with safety regulations and enhances overall system performance. Incorporating **Condition-Based Maintenance** (CBM) can further optimize the maintenance strategy. CBM involves performing maintenance based on the actual condition of the equipment rather than on a fixed schedule. This approach can be particularly beneficial for critical components like compressors and valves, where premature replacement can be costly but necessary to avoid catastrophic failures. By integrating these maintenance strategies into the design, operation, and maintenance of pneumatic systems, operators can significantly enhance system reliability, reduce operational costs, and improve overall performance. A balanced approach that combines preventive, predictive, and corrective maintenance ensures that pneumatic systems operate at their best, contributing to increased productivity and efficiency in various industrial applications.