What Does Lead Time Mean

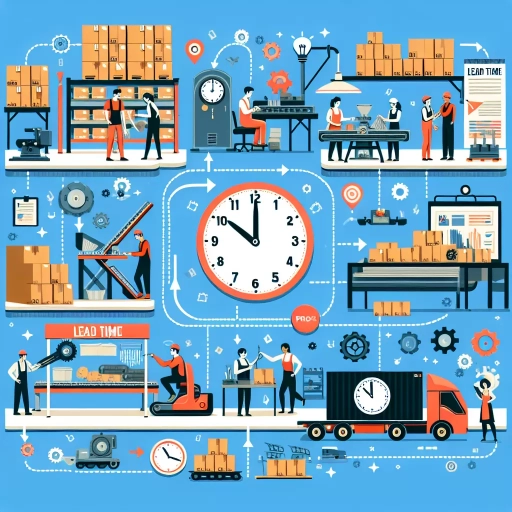
In the dynamic world of business and operations, understanding key performance metrics is crucial for optimizing efficiency and achieving strategic goals. One such metric that plays a pivotal role in various industries is lead time. Lead time, simply put, is the duration between the initiation of a process and its completion. However, its significance extends far beyond this basic definition. To fully grasp the implications of lead time, it is essential to delve into its conceptual underpinnings, explore its diverse types and applications across different sectors, and analyze its impact on operational management. This article will guide you through these critical aspects, starting with an in-depth exploration of the concept itself. By understanding what lead time means at its core, we can better appreciate its multifaceted nature and its role in shaping business outcomes. Let's begin by **Understanding the Concept of Lead Time**.
Understanding the Concept of Lead Time
Understanding the concept of lead time is crucial for any organization aiming to optimize its operations and improve efficiency. Lead time, essentially, is the duration between the initiation of a process and its completion. This concept is multifaceted and can be approached from various angles. To fully grasp lead time, it is essential to delve into its **Definition and Basic Principles**, which provide a foundational understanding of what lead time entails and how it is measured. Additionally, exploring the **Historical Context and Evolution** of lead time reveals how this concept has developed over time, influenced by technological advancements and changing business practices. Finally, examining the **Key Components and Factors** that affect lead time helps in identifying areas for improvement and optimization. By understanding these aspects, businesses can better manage their processes, reduce delays, and enhance overall productivity. Let's begin by defining and exploring the basic principles of lead time to establish a solid foundation for further analysis.
Definition and Basic Principles
**Understanding the Concept of Lead Time: Definition and Basic Principles** Lead time, a fundamental concept in supply chain management, logistics, and manufacturing, refers to the duration between the initiation of a process and its completion. It encompasses various stages, including order receipt, procurement, production, and delivery. To grasp the essence of lead time, it is crucial to delve into its definition and underlying principles. **Definition:** Lead time is defined as the total time required to complete a specific task or process from start to finish. This can include the time taken for ordering raw materials, manufacturing products, and delivering them to customers. For instance, in a manufacturing context, lead time might involve the time from when an order is placed until the finished goods are shipped out. **Basic Principles:** 1. **Order Lead Time:** This is the period from when an order is received until it is fulfilled. It includes processing time, procurement time for raw materials, production time, and shipping time. 2. **Manufacturing Lead Time:** Specifically focusing on the production phase, this is the time taken to transform raw materials into finished goods. 3. **Supplier Lead Time:** The duration between placing an order with a supplier and receiving the goods or services. 4. **Customer Lead Time:** The time perceived by the customer from placing an order until receiving the product. **Key Components:** - **Processing Time:** The administrative tasks involved in handling orders. - **Procurement Time:** The time taken to acquire raw materials or components. - **Production Time:** The actual manufacturing process. - **Shipping Time:** The duration required to transport goods from the production site to the customer. **Impact on Operations:** Understanding lead time is vital for optimizing business operations. Shorter lead times can enhance customer satisfaction by reducing wait times, while longer lead times may lead to stockouts or overstocking due to inaccurate demand forecasting. Effective management of lead time involves streamlining processes, improving supply chain visibility, and leveraging technology such as just-in-time (JIT) systems. **Strategic Importance:** From a strategic perspective, lead time influences inventory management, production planning, and supply chain resilience. Companies aiming to reduce lead times often invest in lean manufacturing techniques, automate processes, and foster strong relationships with suppliers. By minimizing lead times, businesses can respond more agilely to market changes and customer demands. In summary, lead time is a critical metric that encapsulates the entire lifecycle of a product or service from initiation to delivery. Comprehending its definition and basic principles is essential for businesses seeking to optimize their supply chains, enhance operational efficiency, and improve customer satisfaction. By focusing on reducing and managing lead times effectively, organizations can gain a competitive edge in today's fast-paced market environment.
Historical Context and Evolution
**Historical Context and Evolution** The concept of lead time, a critical metric in supply chain management and project planning, has its roots in the early days of industrialization. As manufacturing processes became more complex and global trade expanded, the need to measure and manage the time required to complete various stages of production and delivery grew. In the late 19th and early 20th centuries, pioneers like Frederick Winslow Taylor and Henry Ford introduced scientific management principles that emphasized efficiency and standardization. These innovations laid the groundwork for modern supply chain management, where understanding lead times became essential for optimizing production schedules, inventory levels, and logistics. During World War II, the importance of lead time became even more pronounced as military operations required precise timing and coordination. The war effort necessitated streamlined production processes to meet urgent demand for supplies and equipment. This period saw the development of more sophisticated planning tools and methodologies, such as the Critical Path Method (CPM) and Program Evaluation and Review Technique (PERT), which further highlighted the significance of lead times in project management. In the post-war era, globalization accelerated, leading to more intricate supply chains that spanned across continents. The advent of containerization in the 1950s revolutionized shipping by standardizing cargo handling, thereby reducing transit times and increasing efficiency. However, this also introduced new complexities in managing lead times due to increased reliance on international logistics. The 1980s saw a significant shift with the introduction of Just-In-Time (JIT) manufacturing, popularized by Japanese companies like Toyota. JIT emphasized producing and delivering products just in time to meet customer demand, minimizing inventory levels and reducing waste. This approach necessitated a deep understanding of lead times to ensure that components and finished goods were available exactly when needed. In recent decades, technological advancements have dramatically altered the landscape of lead time management. The rise of digital technologies such as Enterprise Resource Planning (ERP) systems, Supply Chain Management (SCM) software, and Internet of Things (IoT) devices has enabled real-time monitoring and optimization of supply chains. These tools provide detailed insights into every stage of production and delivery, allowing businesses to predict and manage lead times with unprecedented accuracy. Today, understanding lead time is crucial not only for traditional manufacturing but also for service industries and digital businesses. In an era marked by e-commerce growth and customer expectations for rapid delivery, companies must finely tune their operations to minimize lead times without compromising quality or increasing costs. The evolution of lead time management reflects broader trends in industrial history—from early industrialization through wartime mobilization to modern technological innovations—and continues to play a pivotal role in ensuring operational efficiency and customer satisfaction across diverse sectors. By grasping the historical context and ongoing evolution of lead time, businesses can better navigate the complexities of modern supply chains and project planning, ultimately driving competitiveness and success in an ever-changing global marketplace.
Key Components and Factors
Understanding the concept of lead time is crucial for any business or project, as it directly impacts efficiency, productivity, and overall success. At its core, lead time encompasses several key components and factors that collectively determine the duration between the initiation of a process and its completion. **Key Components:** 1. **Order Lead Time:** This refers to the time elapsed between placing an order and receiving the goods or services. It includes procurement lead time, which is the period from ordering raw materials or components to their arrival. 2. **Manufacturing Lead Time:** Also known as production lead time, this is the duration required to produce a product from start to finish. It involves various stages such as setup, processing, and quality control. 3. **Transportation Lead Time:** This component covers the time taken for goods to travel from one location to another, whether it be from supplier to manufacturer or from manufacturer to customer. 4. **Inventory Lead Time:** This factor considers the time spent in inventory management, including storage and retrieval processes. **Factors Influencing Lead Time:** 1. **Supply Chain Complexity:** The more complex the supply chain, with multiple suppliers and intermediaries, the longer the lead time tends to be. 2. **Production Capacity:** The ability of a manufacturing facility to produce goods efficiently affects lead times; higher capacity generally reduces lead times. 3. **Quality Control Processes:** Rigorous quality checks can extend lead times but are essential for ensuring product reliability. 4. **Logistics and Transportation:** Efficient logistics systems and reliable transportation methods significantly reduce lead times by minimizing delays. 5. **Demand Variability:** Unpredictable demand patterns can lead to stockouts or overstocking, both of which impact lead times negatively. 6. **Supplier Reliability:** Consistent and reliable suppliers help maintain stable lead times by ensuring timely delivery of raw materials or components. 7. **Technological Integration:** The use of advanced technologies like automation, ERP systems, and real-time tracking can streamline processes and reduce lead times. **Impact on Business:** Understanding these components and factors allows businesses to optimize their operations effectively. By identifying bottlenecks in their supply chain or production process, companies can implement strategies to reduce lead times, thereby enhancing customer satisfaction through faster delivery times and improving their competitive edge in the market. In summary, lead time is not just a simple metric; it is influenced by a myriad of components and factors that interplay within the broader context of business operations. By grasping these intricacies, organizations can better manage their resources, improve efficiency, and ultimately drive growth through reduced lead times. This holistic understanding is pivotal for strategic planning and operational excellence in today’s fast-paced business environment.
Types and Applications of Lead Time
Lead time, a critical metric in various industries, refers to the duration between the initiation of a process and its completion. Understanding the different types and applications of lead time is essential for optimizing operations, enhancing efficiency, and improving overall performance. This article delves into three key areas: Manufacturing Lead Time, Supply Chain Lead Time, and Service Industry Lead Time. In manufacturing, lead time is crucial for managing production cycles and ensuring timely delivery of products. It encompasses the time from ordering raw materials to delivering the final product, influencing production planning and inventory management. In the supply chain, lead time affects the entire logistics process, from procurement to delivery, impacting inventory levels and customer satisfaction. In the service industry, lead time pertains to the time taken to deliver services, such as response times for customer inquiries or the duration of service delivery, which directly impacts customer experience and loyalty. Each of these types of lead time has distinct implications and requires tailored strategies for optimization. By examining these different facets, businesses can better align their processes with market demands and achieve operational excellence. Let's begin by exploring Manufacturing Lead Time in more detail.
Manufacturing Lead Time
Manufacturing lead time is a critical metric in the production process, representing the duration between the initiation of a manufacturing order and the completion of the final product. It encompasses various stages, including material procurement, production planning, actual production, quality control, and packaging. Understanding and optimizing manufacturing lead time is essential for businesses to enhance efficiency, reduce costs, and improve customer satisfaction. In the context of types and applications of lead time, manufacturing lead time stands out as a key performance indicator (KPI) that directly influences supply chain dynamics. It can be broken down into several components: order receipt to production start (pre-production lead time), production start to completion (production lead time), and completion to shipment (post-production lead time). Each component offers insights into potential bottlenecks and areas for improvement. For instance, pre-production lead time can be affected by factors such as supplier reliability, inventory levels, and the complexity of the production planning process. Companies can mitigate delays by implementing just-in-time (JIT) inventory systems or partnering with reliable suppliers. During the actual production phase, factors like machine availability, labor efficiency, and process optimization play significant roles. Implementing lean manufacturing techniques can help streamline operations and reduce waste. Post-production lead time involves quality control checks, packaging, and preparation for shipment. Here, investing in automated quality control systems and efficient packaging solutions can significantly reduce delays. Additionally, integrating technology such as enterprise resource planning (ERP) systems can provide real-time visibility across all stages of manufacturing, enabling better decision-making and faster response times to any disruptions. The applications of optimizing manufacturing lead time are multifaceted. Reduced lead times allow companies to respond more quickly to market demands and changes in consumer preferences, thereby enhancing competitiveness. Shorter lead times also mean lower inventory holding costs and reduced risk of inventory obsolescence. Furthermore, faster production cycles enable businesses to offer more flexible delivery options to customers, which can be a differentiator in crowded markets. In summary, manufacturing lead time is a vital metric that impacts various aspects of business operations. By understanding its components and optimizing each stage, companies can achieve significant improvements in efficiency, cost savings, and customer satisfaction. As part of the broader discussion on types and applications of lead time, recognizing the importance of manufacturing lead time helps businesses align their strategies with operational realities to drive sustainable growth and competitiveness.
Supply Chain Lead Time
**Supply Chain Lead Time** Supply chain lead time is a critical metric that measures the duration between the initiation of a process and its completion within the supply chain. It encompasses various stages, including procurement, production, and distribution, each contributing to the overall time it takes for a product to move from raw materials to end customers. Understanding and optimizing supply chain lead time is essential for businesses to maintain competitiveness, ensure customer satisfaction, and manage inventory effectively. In the context of procurement, lead time begins when an order is placed with a supplier and ends when the materials or goods are received. This phase can be influenced by factors such as supplier reliability, transportation efficiency, and customs clearance processes. For instance, a company sourcing components from overseas may experience longer lead times due to international shipping and customs delays compared to sourcing locally. During the production phase, lead time refers to the time required to manufacture or assemble products. This includes setup times, processing times, and any necessary quality control checks. Companies can reduce production lead times by implementing lean manufacturing practices, investing in automation, and streamlining workflows to minimize bottlenecks. Distribution lead time, which follows production, involves the time it takes for finished goods to reach customers. This includes warehousing, packaging, shipping, and delivery. Efficient distribution networks can significantly reduce lead times by leveraging advanced logistics technologies such as real-time tracking and optimized routing algorithms. Effective management of supply chain lead time involves strategic planning, robust communication with suppliers and stakeholders, and continuous monitoring of performance metrics. By analyzing historical data and using predictive analytics, companies can forecast demand more accurately and adjust their supply chains accordingly to avoid stockouts or overstocking. Moreover, reducing supply chain lead times can have profound impacts on business operations. Shorter lead times enable quicker response to market changes and customer demands, leading to improved service levels and increased customer satisfaction. Additionally, reduced inventory holding times lower storage costs and minimize the risk of inventory obsolescence. In summary, supply chain lead time is a multifaceted concept that spans procurement, production, and distribution. By understanding and optimizing each stage of the supply chain, businesses can enhance their operational efficiency, improve customer service, and gain a competitive edge in the market. As part of a broader strategy to manage types and applications of lead time effectively, focusing on supply chain lead time is crucial for achieving sustainable business growth and profitability.
Service Industry Lead Time
In the service industry, lead time is a critical metric that measures the duration between the initiation of a service request and its completion. This timeframe encompasses various stages, including order receipt, processing, execution, and delivery. Understanding and optimizing service industry lead time is essential for enhancing customer satisfaction, improving operational efficiency, and gaining a competitive edge. For instance, in healthcare services, lead time can refer to the period from when a patient schedules an appointment to when they receive treatment. Reducing this lead time can significantly improve patient outcomes by ensuring timely medical interventions. Similarly, in financial services, lead time might be the time taken to process a loan application or open a new account. Streamlining these processes can enhance customer experience and reduce the likelihood of clients seeking services from competitors. In the context of customer service, lead time is often associated with response times to customer inquiries or issues. Companies that minimize this lead time by implementing efficient ticketing systems and training their support staff can foster stronger customer relationships and build trust. For example, a company like Amazon, known for its swift customer service response times, sets a high standard in the e-commerce sector by resolving customer queries promptly. Moreover, service industry lead times are influenced by several factors such as resource availability, process complexity, and demand variability. Effective management involves identifying bottlenecks and implementing strategies to mitigate them. This could include adopting technology solutions like automation and AI to streamline processes, cross-training staff to handle multiple tasks, or outsourcing certain functions to specialized providers. From a strategic perspective, reducing lead times in the service industry can also drive cost savings. Faster service delivery means lower holding costs for resources and reduced labor hours spent on each task. Additionally, quicker turnaround times can lead to higher throughput, allowing businesses to serve more customers within the same timeframe. To illustrate this further, consider a restaurant where the lead time is the duration from when an order is placed to when it is served. By optimizing kitchen workflows and implementing efficient ordering systems, restaurants can reduce this lead time, thereby increasing table turnover rates and enhancing overall dining experiences. In conclusion, service industry lead time is a vital performance indicator that directly impacts customer satisfaction and operational efficiency. By understanding the various components of this metric and implementing strategies to minimize it, service providers can deliver superior experiences, gain competitive advantages, and ultimately drive business growth. Effective management of lead times is not just about speed; it's about delivering value promptly and consistently to maintain a loyal customer base.
Impact and Management of Lead Time
In the realm of supply chain management, lead time is a critical metric that significantly influences both economic and operational outcomes. Understanding and effectively managing lead time is essential for businesses aiming to enhance efficiency, reduce costs, and improve customer satisfaction. This article delves into the multifaceted impact of lead time and explores various strategies for its management. We will examine the **Economic and Operational Implications** of lead time, highlighting how prolonged or variable lead times can affect inventory levels, cash flow, and overall business performance. Additionally, we will discuss **Strategies for Reducing Lead Time**, including process optimization, supplier partnerships, and demand forecasting. Finally, we will explore **Tools and Technologies for Lead Time Management**, such as advanced analytics, automation, and real-time tracking systems. By grasping these concepts, businesses can better navigate the complexities of lead time and implement actionable solutions to drive improvement. Let us begin by examining the **Economic and Operational Implications** of lead time, a foundational understanding crucial for any effective management strategy.
Economic and Operational Implications
The economic and operational implications of lead time are multifaceted and far-reaching, significantly influencing both the efficiency and profitability of businesses. Lead time, the duration between the initiation of a process and its completion, affects various aspects of operations, from supply chain management to customer satisfaction. Economically, shorter lead times can lead to reduced inventory costs as companies do not need to hold large quantities of stock for extended periods. This reduction in inventory levels also minimizes the risk of inventory obsolescence and reduces the need for extensive storage facilities, thereby lowering overhead costs. Additionally, quicker turnaround times enable businesses to respond more agilely to market changes and customer demands, enhancing their competitive edge. Operationally, managing lead time effectively is crucial for maintaining smooth production flows and ensuring timely delivery of products. Long lead times can result in delayed shipments, which may lead to lost sales and damaged customer relationships. Conversely, optimizing lead times allows companies to improve their just-in-time (JIT) production capabilities, reducing waste and increasing overall productivity. This optimization also facilitates better forecasting and planning, enabling firms to allocate resources more efficiently and make informed decisions about production capacity and resource allocation. Moreover, the impact of lead time on supply chain resilience cannot be overstated. Shorter lead times reduce the vulnerability of supply chains to disruptions such as supplier insolvency or natural disasters. By having a more agile supply chain, companies can quickly adapt to unforeseen events, minimizing the risk of stockouts and ensuring continuous supply to meet customer demands. This adaptability is particularly important in today's globalized economy where supply chains are increasingly complex and interconnected. From a management perspective, effective lead time management involves a holistic approach that integrates various departments within an organization. It requires close collaboration between procurement, production, logistics, and sales teams to streamline processes and eliminate bottlenecks. Implementing advanced technologies such as enterprise resource planning (ERP) systems and data analytics tools can provide real-time insights into production cycles and supply chain operations, enabling managers to make data-driven decisions that optimize lead times. In conclusion, the economic and operational implications of lead time are profound and far-reaching. By reducing inventory costs, enhancing agility in response to market changes, improving operational efficiency, and bolstering supply chain resilience, effective lead time management can significantly contribute to a company's overall performance and competitiveness. As such, it remains a critical focus area for businesses seeking to optimize their operations and achieve sustainable growth in an increasingly dynamic market environment.
Strategies for Reducing Lead Time
Reducing lead time is a critical strategy for enhancing operational efficiency and competitiveness in various industries. Lead time, the duration between the initiation of a process and its completion, directly impacts production cycles, inventory levels, and customer satisfaction. To effectively reduce lead time, several strategies can be employed. 1. **Process Optimization**: Streamlining workflows by eliminating unnecessary steps and automating repetitive tasks can significantly cut down lead times. This involves mapping out current processes, identifying bottlenecks, and implementing lean manufacturing principles to minimize waste and maximize value-added activities. 2. **Inventory Management**: Implementing just-in-time (JIT) inventory systems ensures that materials are available exactly when needed, reducing the time spent on procurement and storage. This approach also helps in avoiding overstocking and the associated costs. 3. **Supplier Partnerships**: Building strong relationships with suppliers can lead to faster delivery times. Negotiating with suppliers to reduce their lead times or implementing vendor-managed inventory (VMI) systems where suppliers manage inventory levels can be highly effective. 4. **Technology Integration**: Leveraging advanced technologies such as enterprise resource planning (ERP) systems, manufacturing execution systems (MES), and artificial intelligence (AI) can provide real-time visibility into production processes. These tools help in identifying inefficiencies, predicting demand, and optimizing production schedules. 5. **Cross-functional Collaboration**: Encouraging collaboration between different departments within an organization ensures that all stakeholders are aligned towards reducing lead times. This includes integrating sales, production, and logistics teams to create a cohesive workflow. 6. **Continuous Improvement**: Adopting a culture of continuous improvement through methodologies like Kaizen or Six Sigma encourages ongoing evaluation and enhancement of processes. Regular feedback loops and employee empowerment to suggest improvements are key components of this approach. 7. **Outsourcing Non-core Activities**: Focusing on core competencies by outsourcing non-core activities can free up resources and reduce the complexity of internal processes, thereby reducing overall lead times. 8. **Training and Development**: Investing in employee training and development ensures that the workforce has the necessary skills to operate efficiently. Well-trained employees can handle tasks more quickly and accurately, contributing to shorter lead times. 9. **Quality Control**: Implementing robust quality control measures at each stage of production helps in reducing rework and defects, which are significant contributors to extended lead times. Early detection of quality issues allows for prompt corrective actions. 10. **Customer Feedback**: Engaging with customers to understand their needs better can help in tailoring production processes to meet their expectations more efficiently. This feedback loop also aids in identifying areas where lead times can be reduced without compromising quality. By implementing these strategies, organizations can significantly reduce their lead times, leading to faster delivery of products, improved customer satisfaction, and enhanced competitiveness in the market. Effective management of lead time is crucial for maintaining operational agility and responding swiftly to changing market conditions.
Tools and Technologies for Lead Time Management
Effective lead time management is crucial for optimizing business operations, and leveraging the right tools and technologies can significantly enhance this process. At the forefront of these tools are project management software solutions such as Asana, Trello, and Jira, which enable teams to track tasks, set deadlines, and monitor progress in real-time. These platforms provide visual boards and dashboards that help in identifying bottlenecks and streamlining workflows, thereby reducing lead times. Another critical tool is time tracking software like Harvest or Toggl, which allows teams to log time spent on tasks accurately. This data can be analyzed to identify areas where time is being wasted or where processes can be improved. Additionally, workflow automation tools such as Zapier or Automate.io can automate repetitive tasks, freeing up resources for more strategic activities and reducing the overall lead time. Advanced analytics and data visualization tools like Tableau or Power BI play a pivotal role in lead time management by providing insights into historical data trends. These tools help in predicting future lead times based on past performance, enabling proactive decision-making. Furthermore, machine learning algorithms integrated into these analytics platforms can identify patterns that might not be immediately apparent to human analysts, leading to more accurate forecasting. Supply chain management (SCM) software is also essential for companies that rely on complex supply chains. Tools like SAP SCM or Oracle SCM Cloud help in managing inventory levels, tracking shipments, and optimizing logistics operations. These systems ensure that raw materials are available when needed and finished goods are delivered promptly, thereby minimizing delays in the production cycle. Moreover, collaboration tools such as Slack or Microsoft Teams facilitate communication among team members across different departments. Real-time communication ensures that issues are addressed promptly without delays caused by miscommunication or lack of coordination. In addition to these digital tools, adopting agile methodologies such as Scrum or Kanban can significantly reduce lead times by promoting iterative development cycles and continuous improvement. These methodologies encourage frequent feedback loops and adaptability to change, which are key in managing dynamic business environments. Finally, implementing a Continuous Integration/Continuous Deployment (CI/CD) pipeline using tools like Jenkins or GitLab CI/CD can automate the software development lifecycle from code commit to deployment. This automation reduces manual errors and speeds up the release process, thereby shortening the lead time for software products. In summary, leveraging a combination of project management software, time tracking tools, workflow automation platforms, advanced analytics solutions, SCM systems, collaboration tools, agile methodologies, and CI/CD pipelines can significantly improve lead time management. By integrating these technologies into their operations, businesses can streamline processes, reduce delays, and enhance overall efficiency. This holistic approach ensures that organizations remain competitive in today's fast-paced market by delivering products and services quickly while maintaining high quality standards.