What Is Subfloor

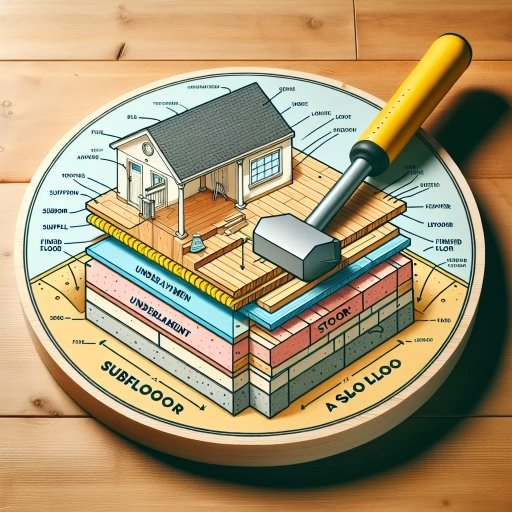
A subfloor is a critical component of any building, serving as the foundation for the entire flooring system. It plays a pivotal role in ensuring structural integrity, comfort, and durability. Understanding the concept of a subfloor is essential for both homeowners and builders, as it directly impacts the overall quality and longevity of the flooring. This article delves into the intricacies of subfloors, starting with **Understanding the Concept of Subfloor**, where we explore its definition, importance, and various types. We then examine **Components and Materials of a Subfloor**, discussing the different materials and elements that make up a subfloor, such as plywood, oriented strand board (OSB), and concrete. Finally, we address **Installation and Maintenance of Subfloors**, providing insights into the best practices for installing and maintaining subfloors to ensure they remain in optimal condition. By grasping these key aspects, readers will gain a comprehensive understanding of subfloors and their significance in construction. Let's begin by **Understanding the Concept of Subfloor**.
Understanding the Concept of Subfloor
Understanding the concept of a subfloor is crucial for any construction project, as it forms the foundation upon which the entire floor system is built. This article delves into three key aspects of subfloors: their definition and purpose, the various types available, and their importance in construction. First, we will explore the definition and purpose of a subfloor, highlighting its role in providing a stable base for flooring materials and ensuring structural integrity. Next, we will examine the different types of subfloors, including concrete, plywood, and oriented strand board (OSB), each with its own set of advantages and applications. Finally, we will discuss the importance of subfloors in construction, emphasizing how they impact the overall durability and performance of a building. By grasping these fundamental concepts, builders and homeowners can make informed decisions that ensure their floors are both functional and long-lasting. Let's begin by defining what a subfloor is and why it is essential in any building project.
Definition and Purpose
The definition and purpose of a subfloor are fundamental to understanding its role in building construction. A subfloor is the structural layer of a floor that lies directly beneath the finish flooring, such as hardwood, carpet, or tile. It serves as the base upon which the final flooring material is installed. The primary purpose of a subfloor is to provide a stable, level, and durable surface that can support the weight of the finish flooring, furniture, and occupants. This layer must be strong enough to withstand various loads and stresses without compromising the integrity of the structure. In terms of functionality, a subfloor acts as a critical interface between the foundation of the building and the finish flooring. It helps in distributing loads evenly across the foundation, ensuring that no single point bears excessive weight. Additionally, it provides a smooth surface for the installation of underlayment materials like plywood or oriented strand board (OSB), which are essential for creating a uniform base for finish flooring. The subfloor also plays a crucial role in maintaining the overall health and longevity of the building. It helps in controlling moisture levels by providing a barrier against dampness rising from the foundation or soil. This is particularly important in preventing issues such as mold growth, rotting wood, and structural damage. Furthermore, a well-constructed subfloor can enhance the thermal performance of the building by providing insulation and reducing heat loss. From an architectural standpoint, the subfloor is integral to achieving desired aesthetic outcomes. It allows for the installation of various types of finish flooring without compromising on appearance or functionality. Whether it's a residential or commercial building, the subfloor ensures that the final flooring surface is even, smooth, and visually appealing. In summary, the definition and purpose of a subfloor are centered around providing structural support, ensuring load distribution, controlling moisture levels, enhancing thermal performance, and facilitating aesthetic outcomes. Understanding these aspects is essential for appreciating the critical role that subfloors play in building construction and maintenance.
Types of Subfloors
When delving into the concept of subfloors, it is crucial to understand the various types that exist, as each has its own set of characteristics, advantages, and applications. There are primarily four types of subfloors: concrete, plywood, oriented strand board (OSB), and joist-and-deck. **Concrete Subfloors** are the most common type in commercial and industrial settings. They are durable and can withstand heavy loads, making them ideal for high-traffic areas. Concrete subfloors can be finished with various toppings such as epoxy, polyurethane, or even a thin layer of concrete to enhance their durability and aesthetic appeal. However, they can be prone to moisture issues if not properly sealed. **Plywood Subfloors** are widely used in residential construction due to their cost-effectiveness and ease of installation. Plywood is made from layers of wood veneer pressed together, offering good strength and stability. It is available in different thicknesses, with thicker sheets providing better support for heavier loads. Plywood subfloors are versatile and can be finished with a variety of flooring materials like hardwood, carpet, or tile. **Oriented Strand Board (OSB) Subfloors** are another popular choice for residential construction. OSB is made from strands of wood pressed together with adhesive, making it more affordable than plywood. While OSB offers good structural integrity, it is more susceptible to moisture damage compared to plywood. Therefore, it is essential to ensure that OSB subfloors are properly sealed to prevent water infiltration. **Joist-and-Deck Subfloors** are traditional and often found in older homes or those with wooden floor systems. This type consists of wooden joists spaced at regular intervals with a deck of boards nailed or screwed onto them. Joist-and-deck subfloors provide excellent ventilation and can be repaired relatively easily if damaged. However, they may require additional support for certain types of flooring like tile or heavy hardwood. Understanding these different types of subfloors is vital for selecting the right one for your specific needs. Factors such as load-bearing capacity, moisture resistance, budget constraints, and intended use all play significant roles in determining which type of subfloor is most suitable. By choosing the appropriate subfloor, you can ensure a stable foundation for your flooring system, enhancing both its performance and longevity.
Importance in Construction
The importance of construction in the context of understanding the concept of a subfloor cannot be overstated. A subfloor, which is the structural layer beneath the finished floor, plays a crucial role in ensuring the stability, durability, and overall quality of a building. Here are several key reasons why construction practices surrounding subfloors are vital: 1. **Structural Integrity**: The subfloor acts as a foundation for the entire flooring system, distributing the weight of the building and its occupants evenly. Proper construction of the subfloor ensures that it can support these loads without compromising the structural integrity of the building. 2. **Moisture Management**: A well-constructed subfloor helps in managing moisture effectively. This is particularly important in areas prone to dampness or flooding, as it prevents water from seeping into the finished flooring, thereby reducing the risk of mold, rot, and other forms of damage. 3. **Thermal Insulation**: In many cases, the subfloor also serves as a thermal barrier, helping to regulate temperature within the building. This can significantly impact energy efficiency and comfort levels for occupants. 4. **Soundproofing**: The subfloor can act as a sound barrier, reducing noise transmission between different levels of a building. This is especially important in multi-story buildings or residential areas where noise pollution needs to be minimized. 5. **Safety**: A poorly constructed subfloor can lead to uneven surfaces, which pose significant safety risks. Ensuring that the subfloor is level and secure helps prevent accidents such as slips, trips, and falls. 6. **Longevity**: Properly constructed subfloors extend the lifespan of the finished flooring by providing a stable base that resists wear and tear. This reduces maintenance costs over time and delays the need for costly repairs or replacements. 7. **Aesthetic Appeal**: While not immediately visible, a well-constructed subfloor ensures that the finished flooring lies flat and even, enhancing the aesthetic appeal of the space. Uneven or sagging floors can detract from the overall appearance of a room. 8. **Compliance with Building Codes**: Construction standards for subfloors are often mandated by local building codes to ensure safety and quality. Adhering to these standards is essential for obtaining necessary permits and avoiding legal issues. In summary, the importance of construction in relation to subfloors lies in its impact on structural integrity, moisture management, thermal insulation, soundproofing, safety, longevity, aesthetic appeal, and compliance with building codes. Each of these aspects underscores why meticulous attention to detail during the construction phase is crucial for creating a solid foundation that supports the entire building effectively.
Components and Materials of a Subfloor
When constructing a building, the subfloor is a critical component that provides the foundation for the entire structure. It consists of several key elements, each playing a vital role in ensuring the integrity and functionality of the floor. The subfloor is composed of joists and beams, which form the skeletal framework; subfloor sheathing, which provides a solid surface; and insulation and underlayment, which enhance comfort and performance. Understanding these components is essential for builders and homeowners alike, as they directly impact the durability, stability, and overall quality of the floor. In this article, we will delve into each of these crucial elements, starting with the foundational aspect: joists and beams. These structural members are the backbone of the subfloor, distributing weight evenly and providing the necessary support for the entire floor system. By examining joists and beams in detail, we can better appreciate how they set the stage for a robust and reliable subfloor.
Joists and Beams
Joists and beams are crucial components of a subfloor, providing the structural framework that supports the entire floor system. **Joists** are horizontal beams that run between the foundation walls or beams, typically spaced at regular intervals (usually 16 or 24 inches on center). They serve as the primary support for the subfloor decking, distributing the weight evenly across the floor. Joists can be made from various materials such as solid wood, engineered wood, or steel, each offering different strengths and advantages. For instance, solid wood joists are traditional and cost-effective but may have limitations in terms of span length and load-bearing capacity compared to engineered wood or steel alternatives. **Beams**, on the other hand, are larger and more substantial than joists. They often run perpendicular to the joists and provide additional support by spanning longer distances between foundation points. Beams can be used to support multiple joists, ensuring that the subfloor remains stable and level. Like joists, beams can also be constructed from various materials including solid wood, laminated veneer lumber (LVL), glue-laminated timber (Glulam), or steel. The choice of material depends on factors such as load-bearing requirements, span length, and budget constraints. For example, LVL beams offer superior strength and stability due to their composite structure, making them ideal for longer spans and heavier loads. The spacing and size of both joists and beams are critical for ensuring the structural integrity of the subfloor. Properly sized and spaced joists prevent sagging or deflection under load, while beams help distribute weight more evenly across larger areas. Incorrectly sized or spaced components can lead to issues such as uneven flooring, creaking sounds, or even structural failure over time. In addition to their structural role, joists and beams must also comply with local building codes and standards. These regulations specify minimum requirements for material types, sizes, and spacing to ensure safety and durability. For instance, the International Residential Code (IRC) provides guidelines for joist and beam sizing based on factors like floor load capacity and span length. In summary, joists and beams form the backbone of a subfloor system by providing essential support and stability. Their selection and installation must be carefully considered to meet both functional needs and regulatory standards, ensuring a solid foundation for the entire floor structure. By understanding the roles and requirements of these components, builders can construct subfloors that are both durable and reliable.
Subfloor Sheathing
Subfloor sheathing is a critical component of the subfloor system, providing a smooth, stable surface for the installation of finish flooring materials such as hardwood, carpet, tile, and laminate. It is typically made from engineered wood products like oriented strand board (OSB) or plywood, which offer superior strength and durability compared to traditional solid wood planks. The sheathing is installed over the joists, usually spaced 16 inches on center, and is secured with nails or screws to ensure a solid bond. This layer serves multiple purposes: it distributes loads evenly across the joists, helps to prevent squeaks and creaks by providing a continuous nailing surface for finish flooring, and acts as a barrier against moisture and air leaks. Proper installation of subfloor sheathing involves ensuring that the panels are aligned with the joists, that gaps between panels are minimal (typically 1/8 inch), and that all edges are supported by joists or blocking. Additionally, the sheathing should be checked for any defects or damage before installation to guarantee optimal performance. In regions prone to high humidity or moisture, specialized sheathing materials like water-resistant OSB may be recommended to enhance durability. Overall, high-quality subfloor sheathing is essential for creating a stable and long-lasting foundation for any type of flooring, ensuring both structural integrity and aesthetic appeal.
Insulation and Underlayment
Insulation and underlayment are crucial components of a subfloor, playing pivotal roles in enhancing the overall performance and comfort of a building. **Insulation** serves to reduce heat transfer between the subfloor and the ground, thereby improving energy efficiency and maintaining a consistent indoor temperature. It can be installed in various forms, such as foam board, fiberglass batts, or spray foam, each offering different levels of thermal resistance (R-value). Proper insulation helps in minimizing heat loss during winter and heat gain during summer, which can significantly lower energy bills. Additionally, insulation can act as a barrier against moisture, reducing the risk of mold and mildew growth that could compromise the structural integrity of the subfloor. **Underlayment**, on the other hand, is a thin layer of material placed between the subfloor and the finished flooring surface. Its primary function is to provide a smooth, even surface for the installation of flooring materials like hardwood, tile, carpet, or laminate. Underlayment materials such as plywood, oriented strand board (OSB), cement-based underlayment, or specialized underlayment sheets (e.g., cork or rubber) help in distributing loads evenly and absorbing minor imperfections in the subfloor. This ensures that the finished flooring remains stable and free from cracks or unevenness. Furthermore, underlayment can offer additional benefits like noise reduction and improved durability by acting as a shock absorber and protecting the flooring from moisture damage. In summary, insulation and underlayment are essential elements that contribute to a well-constructed subfloor. Insulation optimizes thermal performance and protects against moisture issues, while underlayment ensures a stable and even surface for the final flooring installation. Together, they enhance the comfort, efficiency, and longevity of a building's flooring system.
Installation and Maintenance of Subfloors
When it comes to ensuring the longevity and integrity of any flooring system, the installation and maintenance of subfloors are paramount. A well-installed subfloor not only provides a stable base for the final flooring material but also prevents common issues such as uneven surfaces, moisture damage, and structural weaknesses. This article delves into the critical aspects of subfloor management, starting with the meticulous **Preparation and Installation Steps** that set the foundation for a successful project. It then addresses **Common Issues and Solutions**, highlighting potential pitfalls and their remedies to help homeowners and professionals alike navigate any challenges that may arise. Finally, it offers **Long-Term Maintenance Tips** to ensure that the subfloor remains in optimal condition over time. By understanding these key components, individuals can ensure their subfloors are both durable and reliable, providing a solid base for their chosen flooring. Let's begin by examining the crucial **Preparation and Installation Steps** that lay the groundwork for a flawless subfloor installation.
Preparation and Installation Steps
When it comes to the installation and maintenance of subfloors, preparation and installation steps are crucial for ensuring a stable, durable, and long-lasting foundation. Here are the key steps to follow: **Preparation Steps:** 1. **Assess the Site:** Inspect the area for any obstructions, unevenness, or moisture issues. Ensure the ground is level and compacted. 2. **Clear Debris:** Remove all debris, old flooring materials, and any other obstacles from the site. 3. **Check for Moisture:** Conduct a moisture test to ensure the subfloor is dry enough for installation. High moisture levels can lead to warping or rotting. 4. **Lay Underlayment:** Install an underlayment material such as plywood or oriented strand board (OSB) if necessary, ensuring it is securely fastened to the joists. 5. **Inspect Joists:** Check joists for any signs of damage or rot and replace them if necessary. **Installation Steps:** 1. **Lay Joists:** If starting from scratch, lay joists at specified intervals (usually 16 inches on center) and secure them to the foundation. 2. **Install Subfloor Panels:** Place subfloor panels (such as plywood or OSB) over the joists, ensuring they are aligned with the joist centers. Secure them using screws or nails. 3. **Seal Gaps:** Fill any gaps between panels with a suitable sealant to prevent moisture intrusion. 4. **Check for Levelness:** Verify that the subfloor is level and plumb; make adjustments as needed. 5. **Fasten Perimeter:** Secure the perimeter of the subfloor to the walls using appropriate fasteners. 6. **Final Inspection:** Conduct a final inspection to ensure all panels are securely fastened and there are no gaps or uneven areas. **Additional Considerations:** - **Material Selection:** Choose subfloor materials that are suitable for your intended flooring type (e.g., hardwood, tile, carpet). - **Adhesives and Fasteners:** Use adhesives and fasteners recommended by the manufacturer to ensure a strong bond between layers. - **Ventilation:** Ensure proper ventilation under the subfloor to prevent moisture buildup. By meticulously following these preparation and installation steps, you can ensure a solid foundation for your flooring that will withstand the test of time and use. Properly installed subfloors not only enhance the durability of your flooring but also contribute to a safer and more comfortable living space.
Common Issues and Solutions
When it comes to the installation and maintenance of subfloors, several common issues can arise that necessitate prompt attention to ensure the integrity and longevity of the flooring system. One of the most prevalent issues is unevenness or sagging, which can be caused by improper installation, settling of the foundation, or water damage. To address this, it is crucial to inspect the subfloor thoroughly before installing any finish flooring. Any uneven areas should be leveled using self-leveling compounds or patching materials. Another issue is moisture damage, which can lead to warping, buckling, or rotting of the subfloor material. Regularly checking for signs of moisture and ensuring proper ventilation can help mitigate this risk. Additionally, using moisture-resistant materials such as plywood or oriented strand board (OSB) can provide better durability against damp conditions. Cracks in the subfloor are another common problem that can compromise the stability of the finish flooring. These cracks often result from shrinkage or settlement and can be repaired with epoxy-based fillers or polyurethane sealants. It is also important to address any gaps between the subfloor and walls to prevent air leaks and ensure a tight seal. Inadequate fastening is another issue that can lead to creaking floors and structural instability. Ensuring that screws or nails are spaced correctly and driven into the joists securely can prevent such problems. Pests and mold infestations are further concerns that require immediate action. Regular inspections for signs of pest activity or mold growth are essential, and any affected areas should be treated promptly with appropriate chemicals or replaced if necessary. Proper cleaning and maintenance routines, including regular sweeping and mopping, can also help prevent these issues. In terms of solutions, preventive measures play a significant role. Conducting regular inspections allows for early detection of potential problems before they escalate into major issues. Using high-quality materials that are resistant to moisture and pests can also reduce the likelihood of common subfloor problems. Additionally, following manufacturer guidelines for installation and maintenance ensures that the subfloor is set up correctly from the outset. For existing subfloors, periodic maintenance is key. This includes checking for any signs of wear or damage and addressing them promptly. Applying a protective coating to the subfloor can also help protect it from moisture and other environmental factors. In cases where significant damage has occurred, it may be necessary to replace sections of the subfloor entirely. In summary, addressing common issues in subfloor installation and maintenance involves a combination of preventive measures, regular inspections, and timely repairs. By understanding these potential problems and implementing effective solutions, homeowners and builders can ensure a stable and durable flooring system that lasts for years to come.
Long-Term Maintenance Tips
**Long-Term Maintenance Tips** To ensure the longevity and integrity of your subfloor, regular maintenance is crucial. Here are some key tips to keep in mind: 1. **Moisture Control**: Prevent water damage by ensuring that your subfloor is properly sealed and that any leaks or spills are addressed immediately. Regularly inspect for signs of moisture, such as warping or discoloration, and fix any issues promptly. 2. **Cleaning**: Maintain a clean subfloor by sweeping or vacuuming regularly to remove debris and dust. For more thorough cleaning, use a mild detergent and water, but avoid excessive moisture which can damage the subfloor material. 3. **Inspection**: Conduct periodic inspections to identify potential problems early. Check for cracks, unevenness, or signs of wear and tear. Addressing these issues promptly can prevent more serious problems from developing. 4. **Load Management**: Be mindful of the weight load on your subfloor. Avoid placing heavy objects in one spot for extended periods, as this can cause uneven wear and potential damage to the subfloor. 5. **Humidity Levels**: Maintain stable humidity levels in your home to prevent shrinkage or expansion of the subfloor material. This is particularly important for wood subfloors which are sensitive to changes in humidity. 6. **Pest Control**: Regularly check for signs of pest infestation such as termites or rodents which can compromise the structural integrity of your subfloor. Use pest control measures if necessary. 7. **Subfloor Support**: Ensure that the subfloor is adequately supported by the foundation or joists. Any sagging or unevenness should be addressed by adding additional support or repairing existing joists. 8. **Flooring Compatibility**: When installing new flooring over an existing subfloor, ensure that the flooring material is compatible with the subfloor type to avoid potential damage or uneven wear. 9. **Professional Assistance**: For complex maintenance tasks or significant repairs, consider hiring a professional who specializes in subfloor maintenance and repair to ensure the job is done correctly and safely. By following these long-term maintenance tips, you can extend the life of your subfloor, prevent costly repairs, and maintain a stable and secure foundation for your flooring. Regular upkeep not only preserves the structural integrity but also enhances the overall appearance and functionality of your home.