What Is Sandblasting

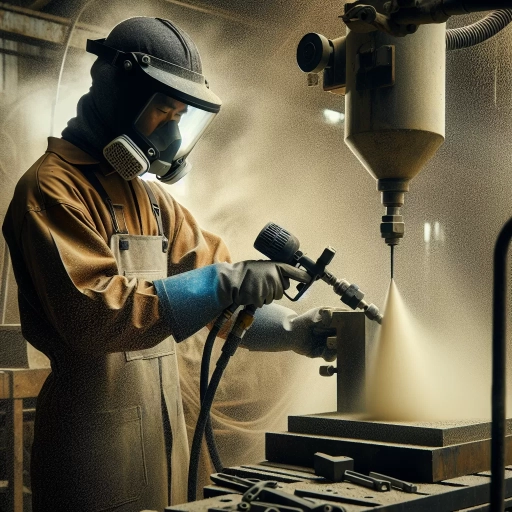
What is Sandblasting?
Sandblasting, a versatile and powerful surface treatment technique, has become an indispensable tool across various industries. At its core, sandblasting involves propelling abrasive particles at high velocities to clean, smooth, or etch surfaces. To fully understand this process, it is essential to delve into its definition and basic principles, which form the foundation of its effectiveness. Historically, sandblasting has evolved significantly from its early beginnings, adapting to technological advancements and expanding its applications. Today, it is utilized in diverse sectors such as construction, automotive, and aerospace. By examining the historical development and evolution of sandblasting, we can appreciate how it has transformed over time. Furthermore, exploring its common applications across industries highlights its versatility and importance in modern manufacturing and maintenance practices. This article will explore these facets in detail, starting with the fundamental aspects of sandblasting: its definition and basic principles.
Definition and Basic Principles
**Definition and Basic Principles** Sandblasting, also known as abrasive blasting, is a surface preparation technique that involves propelling abrasive particles at high velocities to clean, smooth, or etch surfaces. This process is widely used in various industries, including construction, automotive, and manufacturing, to remove rust, paint, and other contaminants from metal surfaces. The definition of sandblasting encompasses not only the removal of unwanted materials but also the enhancement of surface properties for better adhesion of coatings or other treatments. At its core, sandblasting operates on the principle of kinetic energy transfer. When an abrasive material such as silica sand, alumina, or steel grit is accelerated through a nozzle using compressed air or water, it gains significant kinetic energy. Upon impact with the target surface, this energy is transferred, causing the abrasive particles to chip away at the surface material. The choice of abrasive depends on the desired outcome; for instance, finer abrasives are used for delicate surfaces while coarser ones are employed for heavy-duty cleaning. The basic principles of sandblasting include the control of variables such as air pressure, nozzle distance from the surface, and the type of abrasive used. Proper adjustment of these variables ensures efficient removal of contaminants without damaging the underlying material. For example, maintaining an optimal air pressure ensures consistent particle velocity, which is crucial for achieving uniform results. Similarly, adjusting the nozzle distance helps in controlling the impact force and preventing over-blasting or under-blasting. Safety is another critical aspect of sandblasting due to the potential health risks associated with inhaling dust and abrasive particles. Operators must wear protective gear including respirators, gloves, and safety glasses to mitigate these risks. Additionally, containment measures such as blast rooms or shrouds are often used to prevent environmental contamination and ensure a controlled working environment. In summary, sandblasting is a versatile technique grounded in the principles of kinetic energy transfer and controlled application of abrasive materials. Understanding these principles is essential for effective surface preparation and ensuring safety during the process. By carefully selecting abrasives and adjusting operational parameters like air pressure and nozzle distance, practitioners can achieve high-quality results across various applications. This foundational knowledge serves as a cornerstone for mastering the art of sandblasting and leveraging its full potential in industrial settings.
Historical Development and Evolution
The historical development and evolution of sandblasting are deeply intertwined with advancements in technology and industrial processes. The concept of using abrasive materials to clean or shape surfaces dates back to ancient civilizations, where early forms of sandblasting were employed using natural materials like sand and water. However, the modern version of sandblasting began to take shape in the late 19th century. In 1870, Benjamin Chew Tilghman patented the first sandblasting machine, which used compressed air to propel sand particles against a surface. This innovation marked the beginning of a new era in surface preparation and cleaning. Throughout the early 20th century, sandblasting continued to evolve with improvements in machinery and the introduction of new abrasive materials. The development of more powerful compressors and better-designed nozzles increased efficiency and effectiveness. Additionally, the discovery of alternative abrasives such as silica, alumina, and garnet expanded the range of applications for sandblasting. These materials offered varying levels of hardness and durability, allowing for more precise control over the blasting process. The mid-20th century saw significant advancements in safety equipment and environmental regulations. As awareness about the health risks associated with inhaling silica dust grew, manufacturers began developing protective gear such as respirators and blast hoods. This shift towards safer practices ensured that sandblasting could continue to be a viable method without compromising worker health. In recent decades, technological innovations have further refined the sandblasting process. The introduction of automated systems and robotic blasters has increased precision and reduced labor costs. Advanced materials like ceramic beads and glass beads have also been introduced, offering alternatives that are gentler on surfaces while still providing effective cleaning. Moreover, the development of wet blasting techniques has reduced dust emissions significantly, making it a more environmentally friendly option. Today, sandblasting is a versatile technique used across various industries including construction, automotive, aerospace, and even art restoration. Its applications range from surface preparation for painting or coating to removing rust and corrosion from metal surfaces. The continuous evolution of sandblasting technology ensures that it remains a crucial tool in maintaining and enhancing the integrity of materials across diverse sectors. As technology continues to advance, it is likely that sandblasting will become even more efficient, safer, and environmentally sustainable, solidifying its place as a cornerstone in industrial processes for years to come.
Common Applications Across Industries
Sandblasting, a versatile and powerful surface preparation technique, finds widespread applications across various industries due to its effectiveness in cleaning, smoothing, and preparing surfaces for further treatments. In the **construction industry**, sandblasting is crucial for removing old paint, rust, and grime from metal structures, bridges, and buildings, ensuring a clean surface for new coatings or repairs. This process also helps in exposing aggregate in concrete surfaces, enhancing traction and improving the appearance of walkways and driveways. In **manufacturing**, sandblasting is used to deburr metal parts, remove scale from castings, and prepare surfaces for welding or painting. It is particularly valuable in the production of automotive parts, where it helps in achieving smooth finishes on engine components and other metal pieces. The **aerospace industry** relies on sandblasting to clean and prepare aircraft parts for painting or coating, ensuring that surfaces are free from contaminants that could compromise the integrity of the aircraft. The **marine industry** benefits significantly from sandblasting as it is used to remove barnacles, algae, and old paint from ship hulls, improving hydrodynamic efficiency and reducing drag. This process also prepares surfaces for anti-fouling coatings that prevent future marine growth. In **restoration projects**, sandblasting is a key tool for removing old paint and grime from historic buildings and monuments without damaging the underlying material, preserving their original integrity. In **art and sculpture**, artists use sandblasting to create intricate designs and textures on glass, stone, and metal surfaces. This technique allows for precise control over the blasting process, enabling the creation of detailed patterns and designs that would be difficult to achieve with other methods. Additionally, **medical device manufacturing** utilizes sandblasting to clean and prepare implantable devices such as hip replacements and dental implants, ensuring that these critical components are free from contaminants before being used in surgical procedures. The **oil and gas industry** employs sandblasting for cleaning pipelines and equipment, removing corrosion and scale that can impede fluid flow. This process is essential for maintaining the efficiency and safety of oil rigs and pipelines. Furthermore, **automotive repair shops** use sandblasting to restore car parts by removing rust and old paint, allowing for a smooth finish after repainting or recoating. Overall, the versatility of sandblasting makes it an indispensable tool across multiple sectors, offering a reliable method for surface preparation that enhances the durability, appearance, and performance of various materials and structures. Its ability to adapt to different needs and applications underscores its importance as a fundamental technique in modern industry.
The Process of Sandblasting
Sandblasting, a versatile and effective surface preparation technique, involves the use of high-pressure jets of abrasive particles to clean, smooth, or etch surfaces. This process is crucial in various industries, including construction, automotive, and manufacturing, where surface quality is paramount. To understand the intricacies of sandblasting, it is essential to delve into three key aspects: the equipment and machinery involved, the step-by-step procedure for executing the process, and the critical safety precautions and protective gear required. The equipment and machinery involved in sandblasting are sophisticated and specialized, designed to handle the intense pressures and abrasive materials used. This includes sandblasting cabinets, blast pots, hoses, nozzles, and compressors. Each component plays a vital role in ensuring the efficiency and safety of the operation. Understanding the step-by-step procedure for sandblasting is equally important. This involves preparing the surface, setting up the equipment, conducting the blasting operation, and post-blasting cleanup. Each step requires careful attention to detail to achieve optimal results. Finally, safety precautions and protective gear are indispensable in preventing injuries and health hazards associated with sandblasting. This includes wearing respirators, gloves, safety glasses, and protective clothing to shield against abrasive particles and noise. By examining these three critical components—equipment and machinery involved, step-by-step procedure, and safety precautions—readers can gain a comprehensive understanding of the sandblasting process. Let's begin by exploring the **Equipment and Machinery Involved** in detail.
Equipment and Machinery Involved
The process of sandblasting relies heavily on specialized equipment and machinery to ensure efficient and effective surface preparation. At the heart of this operation is the sandblaster itself, which can be categorized into several types based on their functionality and application. The most common types include **siphon sandblasters**, **pressure sandblasters**, and **wet sandblasters**. Siphon sandblasters use compressed air to draw abrasive material from a hopper and propel it through a nozzle, making them suitable for small-scale projects. Pressure sandblasters, on the other hand, store the abrasive material in a pressurized tank, allowing for higher pressure and more efficient blasting. Wet sandblasters combine water with the abrasive material to reduce dust and are often used in environments where dust control is critical. In addition to the sandblaster, other essential equipment includes **nozzles** and **hoses**. Nozzles are designed to focus the abrasive stream, increasing its velocity and effectiveness. They come in various shapes and sizes to accommodate different types of projects, from narrow nozzles for detailed work to wide nozzles for larger surface areas. Hoses connect the sandblaster to the nozzle and must be durable enough to withstand high pressures without compromising performance. **Compressed air systems** are also crucial for sandblasting operations. These systems provide the necessary air pressure to propel the abrasive material through the nozzle. The quality of the compressed air is vital; it must be free from moisture and oil to prevent contamination of the surface being blasted. **Abrasive materials** themselves are another key component. Common abrasives include silica sand, aluminum oxide, garnet, and glass beads, each with its own set of characteristics suited for different applications. For instance, silica sand is often used for general cleaning and surface preparation, while aluminum oxide is preferred for more aggressive blasting due to its hardness. **Safety equipment** is paramount in sandblasting operations due to the hazardous nature of the process. This includes **respirators** or **dust masks** to protect against inhaling fine particles, **safety glasses** or **goggles** to shield eyes from flying debris, and **protective clothing** such as gloves and coveralls to prevent skin abrasion. **Containment systems**, such as blast rooms or booths, are also important for controlling the environment where sandblasting takes place. These systems help in containing dust and debris, making cleanup easier and reducing environmental impact. Finally, **post-blasting equipment** like vacuum systems and dust collectors play a significant role in maintaining a clean workspace. These tools help in removing residual dust and debris from the blasted surface, ensuring it is ready for subsequent processes such as painting or coating. In summary, the equipment and machinery involved in sandblasting are diverse and specialized, each serving a critical function in ensuring the process is carried out safely and effectively. Understanding these components is essential for optimizing sandblasting operations across various industries.
Step-by-Step Procedure for Sandblasting
**The Process of Sandblasting: Step-by-Step Procedure** Sandblasting, a versatile and effective surface preparation technique, involves propelling abrasive particles at high velocity to clean, smooth, or etch surfaces. Here is a detailed, step-by-step guide to the sandblasting process: 1. **Preparation**: Begin by ensuring the workspace is well-ventilated and free from any flammable materials. Wear protective gear including a dust mask, safety glasses, gloves, and a coverall to prevent injury from flying particles. 2. **Surface Inspection**: Inspect the surface to be sandblasted for any contaminants such as grease, oil, or old paint. Clean the surface thoroughly if necessary. 3. **Setting Up Equipment**: Assemble the sandblasting unit, which typically includes a compressor, a blasting pot or cabinet, hoses, and a nozzle or gun. Ensure all connections are secure and the system is properly pressurized. 4. **Choosing Abrasive**: Select the appropriate abrasive material based on the job requirements. Common abrasives include silica sand, aluminum oxide, garnet, and glass beads. Each has different properties suitable for various tasks like cleaning, deburring, or polishing. 5. **Loading Abrasive**: Fill the blasting pot with the chosen abrasive material according to the manufacturer's instructions. Ensure the pot is securely closed to prevent leakage during operation. 6. **Setting Pressure**: Adjust the air pressure to the recommended level for your specific application. Higher pressures are often used for heavy-duty cleaning while lower pressures are better for delicate surfaces. 7. **Blasting**: Hold the nozzle at an optimal distance (usually 6-12 inches) from the surface and maintain a consistent angle to achieve uniform results. Start blasting in sections to avoid missing spots and to keep track of progress. 8. **Monitoring Progress**: Continuously inspect the surface being blasted to determine when it has reached the desired state. Adjust pressure or nozzle distance as needed to achieve optimal results. 9. **Cleaning Up**: Once blasting is complete, turn off the compressor and allow any remaining abrasive particles to settle before opening the blasting pot. Clean up any residual dust and debris from both the surface and surrounding area. 10. **Post-Blasting Inspection**: Inspect the surface again after sandblasting to ensure it meets your requirements. If necessary, repeat certain steps or switch to a different abrasive for finer details. 11. **Disposal**: Dispose of used abrasive material responsibly according to local regulations and safety guidelines. By following these steps meticulously, you can ensure a safe and effective sandblasting process that yields high-quality results whether you're preparing surfaces for painting, removing rust, or enhancing texture and appearance. This methodical approach not only safeguards against potential hazards but also maximizes efficiency and effectiveness in various industrial and DIY applications.
Safety Precautions and Protective Gear
**Safety Precautions and Protective Gear** Sandblasting, a process that involves propelling abrasive particles at high velocities to clean or etch surfaces, is inherently hazardous and requires stringent safety precautions to ensure the well-being of operators and bystanders. The primary risks associated with sandblasting include respiratory issues from inhaling dust and silica particles, eye and skin injuries from flying debris, and hearing damage due to the loud noise generated by the equipment. To mitigate these risks, it is crucial to employ comprehensive protective gear and adhere to strict safety protocols. Operators must wear a full-face respirator or a supplied-air respirator to prevent inhalation of harmful particles. These respirators are designed to filter out 99.97% of particles as small as 0.3 microns, including silica dust, which is particularly dangerous due to its potential to cause silicosis. Additionally, protective eyewear such as goggles or face shields should be worn to safeguard against flying particles that could cause eye injuries. Hearing protection, including earplugs or earmuffs, is also essential to prevent noise-induced hearing loss. Full-body protective clothing, including long sleeves, gloves, and pants, helps protect the skin from abrasions and cuts. This clothing should be made from durable materials that can withstand the abrasive nature of the sandblasting process. Steel-toed boots are recommended to protect feet from heavy objects and sharp edges. In environments where visibility is reduced due to dust, reflective vests can enhance visibility and reduce the risk of accidents. The work area itself must be well-ventilated to reduce dust accumulation and ensure that operators are not exposed to hazardous concentrations of airborne particles. When sandblasting in enclosed spaces, ventilation systems should be used to maintain safe air quality. Regular maintenance of the sandblasting equipment is also vital; worn-out nozzles and hoses can lead to reduced performance and increased risk of accidents. Training is another critical component of safety in sandblasting. Operators should undergo comprehensive training that includes understanding the equipment, recognizing potential hazards, and knowing how to respond in emergency situations. This training should also cover the proper use and maintenance of protective gear to ensure it remains effective. Finally, adherence to local and national safety regulations is mandatory. These regulations often specify minimum standards for protective gear, ventilation requirements, and training protocols. By combining rigorous safety protocols with the use of high-quality protective gear, the risks associated with sandblasting can be significantly reduced, ensuring a safer working environment for all involved. This holistic approach to safety underscores the importance of prioritizing human health and safety in every aspect of the sandblasting process.
Benefits and Uses of Sandblasting
Sandblasting, a versatile and effective technique, offers a multitude of benefits across various industries. This method involves propelling abrasive particles at high velocity to clean, smooth, or etch surfaces, making it an indispensable tool for several applications. One of the primary uses of sandblasting is in **Surface Preparation for Painting and Coating**, where it ensures a clean and even surface, enhancing the adhesion and durability of subsequent coatings. Additionally, sandblasting is highly effective in **Removing Rust, Grime, and Old Coatings**, restoring surfaces to their original state by eliminating unwanted layers and contaminants. Furthermore, it can **Enhance Surface Texture and Aesthetics**, allowing for the creation of intricate designs and finishes that add value to both functional and decorative items. By understanding these key applications, it becomes clear why sandblasting is a crucial step in many industrial and artistic processes. Let's delve deeper into the first of these benefits: **Surface Preparation for Painting and Coating**.
Surface Preparation for Painting and Coating
Surface preparation is a critical step in the painting and coating process, ensuring that the final finish adheres well, lasts longer, and maintains its aesthetic appeal. This preparatory phase involves several key steps, each designed to optimize the surface for the application of paint or coatings. First, thorough cleaning is essential to remove dirt, grime, and other contaminants that could interfere with adhesion. This may involve chemical cleaning agents or mechanical methods such as sanding or blasting. Next, any existing coatings or old paint must be stripped away to expose the raw surface. This can be done using chemical strippers, sanding, or more aggressive methods like sandblasting. Sandblasting, in particular, is a highly effective method for surface preparation due to its ability to remove rust, scale, and other imperfections while also creating a textured surface that enhances paint adhesion. The process involves propelling abrasive particles at high velocity against the surface, which not only cleans but also roughens the substrate, providing an ideal anchor for subsequent coatings. Additionally, sandblasting can be tailored to various levels of intensity depending on the material and desired outcome, making it versatile for different applications. Another crucial aspect of surface preparation is addressing any defects or irregularities. This includes filling holes or cracks with appropriate fillers and smoothing out the area to ensure a uniform finish. For metal surfaces, rust removal and application of a rust inhibitor are vital to prevent future corrosion. Finally, the surface may need to be primed before painting to further enhance adhesion and durability. Proper surface preparation significantly impacts the longevity and performance of the paint or coating. A well-prepared surface reduces the risk of peeling, flaking, or blistering over time. It also ensures that the paint adheres evenly, resulting in a smoother finish that requires less maintenance. In industrial settings, where equipment is exposed to harsh conditions, thorough surface preparation can extend the lifespan of machinery and reduce downtime due to repairs. In summary, surface preparation is an indispensable part of any painting or coating project. By meticulously cleaning, stripping old coatings, addressing defects, and using techniques like sandblasting to create an optimal surface texture, one can ensure that the final coat adheres well and lasts longer. This attention to detail not only enhances the aesthetic quality of the finish but also contributes to its durability and functionality, making it a crucial step in achieving high-quality results in various applications.
Removing Rust, Grime, and Old Coatings
Removing rust, grime, and old coatings is a critical process in various industries, including construction, automotive, and manufacturing. This task is often challenging due to the stubborn nature of these substances, which can adhere deeply to metal surfaces. However, with the advent of advanced techniques like sandblasting, the removal of rust, grime, and old coatings has become significantly more efficient and effective. Sandblasting, also known as abrasive blasting, involves propelling abrasive materials such as sand, silica, or alumina at high velocities against a surface to strip away unwanted layers. This method is particularly beneficial for removing rust because it can penetrate deep into the metal's surface, eliminating corrosion without damaging the underlying material. Unlike chemical treatments that may leave residues or weaken the metal over time, sandblasting provides a clean and residue-free surface ready for recoating or further processing. In addition to rust removal, sandblasting is highly effective in eliminating grime and old coatings. Grime can accumulate over years of exposure to environmental elements and can compromise the integrity of a surface. Old coatings, whether they are paint, varnish, or other protective layers, may need to be removed before applying new finishes. Sandblasting ensures that these layers are completely stripped away without leaving any remnants that could interfere with the adhesion of new coatings. The versatility of sandblasting also extends to different types of surfaces. Whether it's steel beams in construction projects or car parts in automotive restoration, this technique can be tailored to suit various needs. For instance, different abrasive materials can be used depending on the surface type and desired outcome. Fine abrasives like glass beads are ideal for delicate surfaces where minimal damage is required, while coarser materials like garnet are better suited for heavy-duty applications. Moreover, sandblasting offers several advantages over traditional methods such as chemical stripping or manual scraping. It is generally faster and more cost-effective, especially when dealing with large areas or complex geometries. The process also reduces labor time significantly since it can cover extensive areas quickly compared to manual methods. Furthermore, sandblasting is an environmentally friendly option when proper containment measures are taken to prevent dust and debris from spreading. In conclusion, removing rust, grime, and old coatings is an essential step in many industrial processes. Sandblasting stands out as a superior method due to its efficiency, effectiveness, and versatility. By leveraging this technique, industries can ensure that surfaces are thoroughly cleaned and prepared for subsequent treatments or applications, thereby enhancing the durability and longevity of the materials involved. As part of the broader benefits and uses of sandblasting, this capability underscores why this method remains a cornerstone in various sectors where surface preparation is paramount.
Enhancing Surface Texture and Aesthetics
Enhancing surface texture and aesthetics is a critical aspect of various industrial and artistic processes, and sandblasting stands out as a versatile and effective method for achieving these goals. By propelling abrasive particles at high velocities onto a surface, sandblasting can transform rough, uneven, or weathered materials into smooth, polished, and visually appealing finishes. This technique is particularly valuable in industries such as automotive, aerospace, and construction, where the appearance and durability of surfaces are paramount. For instance, in the automotive sector, sandblasting can restore vintage car parts to their original luster by removing rust and grime, while in aerospace, it ensures that metal components are free from contaminants that could compromise their structural integrity. In addition to its functional benefits, sandblasting also plays a significant role in artistic endeavors. Sculptors and artists often use sandblasting to create intricate designs and textures on stone, glass, and metal surfaces. The precision and control offered by modern sandblasting equipment allow for the creation of detailed patterns and engravings that would be difficult or impossible to achieve with other methods. Furthermore, the process can be tailored to produce a range of textures, from fine matte finishes to coarse, rugged surfaces, making it an invaluable tool for enhancing the aesthetic appeal of artworks. The versatility of sandblasting extends to architectural applications as well. In historic preservation projects, it is used to clean and restore stone facades without damaging the underlying material. This gentle yet effective cleaning process helps maintain the original character of buildings while removing decades of grime and pollution. Similarly, in modern architecture, sandblasting can be employed to create unique surface treatments that add visual interest to buildings and monuments. Moreover, the environmental benefits of sandblasting should not be overlooked. Unlike chemical cleaning methods that can harm ecosystems, sandblasting is an eco-friendly alternative that uses natural abrasives like silica sand or garnet. This makes it an attractive option for projects where environmental sustainability is a priority. In summary, enhancing surface texture and aesthetics through sandblasting offers a multitude of benefits across various sectors. From restoring vintage car parts to creating intricate artworks and preserving historical buildings, this technique provides a powerful tool for achieving both functional durability and aesthetic excellence. Its versatility, precision, and eco-friendly nature make it an indispensable method in modern manufacturing and artistic practices.