What Information Is Required On A Workplace Label

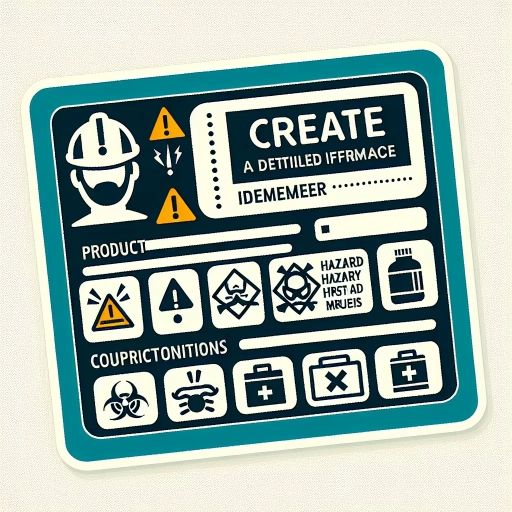
In any workplace, safety and efficiency are paramount, and one crucial tool for achieving these goals is the use of labels. Workplace labels serve as vital communication tools, providing essential information to employees, visitors, and regulatory bodies. However, the effectiveness of these labels hinges on several key factors. First, it is imperative to understand the essential information that must be included on workplace labels to ensure clarity and compliance. This includes details such as hazard warnings, instructions for use, and identification of materials. Additionally, regulatory requirements must be adhered to, as these standards dictate the minimum criteria for label content and design. Finally, best practices in creating effective workplace labels can significantly enhance their impact, ensuring that they are clear, readable, and strategically placed. By delving into these aspects, organizations can optimize their labeling systems to promote a safer and more productive work environment. In this article, we will explore these critical elements, starting with the essential information that must be included on workplace labels.
Essential Information on Workplace Labels
In any workplace, safety is paramount, and one of the most effective ways to ensure a safe environment is through the use of clear and informative labels. These labels serve as critical communication tools, providing essential information that helps prevent accidents, protect employees, and maintain compliance with regulatory standards. This article delves into the crucial aspects of workplace labels, focusing on three key areas: **Hazard Identification**, **Safety Precautions**, and **Emergency Procedures**. Understanding how to identify potential hazards through labeling is the first step in creating a safe workplace. Implementing safety precautions based on these labels ensures that employees are aware of the necessary steps to avoid risks. Finally, knowing the emergency procedures outlined on these labels can save lives in critical situations. By exploring these facets, we will uncover the essential information on workplace labels that every employer and employee needs to know to foster a safe and compliant work environment. Here, we will provide a comprehensive guide on **Essential Information on Workplace Labels**.
1. Hazard Identification
**Hazard Identification** Hazard identification is a critical component of workplace safety, and it plays a pivotal role in ensuring that employees are aware of potential dangers in their environment. This process involves systematically identifying, evaluating, and controlling hazards to prevent injuries and illnesses. On workplace labels, hazard identification is often communicated through standardized symbols, colors, and text that convey specific information about the nature of the hazard. The Globally Harmonized System of Classification and Labelling of Chemicals (GHS) is a widely adopted framework that standardizes hazard communication. Under GHS, labels must include pictograms, signal words, hazard statements, and precautionary statements. Pictograms are visual representations of hazards such as flammability, toxicity, or environmental hazards. Signal words like "Danger" or "Warning" indicate the severity of the hazard. Hazard statements describe the nature of the hazard, while precautionary statements provide advice on how to mitigate or prevent adverse effects. Effective hazard identification on labels ensures that workers can quickly recognize and respond to potential threats. For instance, a label indicating a chemical's flammability can prompt employees to take necessary precautions such as using personal protective equipment (PPE) or ensuring proper ventilation. Similarly, labels warning of toxic substances can guide workers in handling these materials safely and disposing of them appropriately. Moreover, accurate hazard identification supports compliance with regulatory requirements. Many countries have laws mandating the use of GHS-compliant labels for hazardous substances. Employers must ensure that all relevant information is included on these labels to avoid legal repercussions and maintain a safe working environment. In addition to compliance, clear hazard identification fosters a culture of safety within the workplace. When employees are well-informed about potential hazards, they are more likely to adhere to safety protocols and report any concerns or incidents promptly. This proactive approach not only protects individual workers but also contributes to overall workplace safety and productivity. In summary, hazard identification on workplace labels is essential for maintaining a safe and compliant work environment. By adhering to standardized systems like GHS and ensuring that all necessary information is clearly communicated, employers can significantly reduce the risk of accidents and promote a culture of safety among their employees. This not only protects workers but also enhances operational efficiency and compliance with regulatory standards.
2. Safety Precautions
**Safety Precautions** When it comes to ensuring a safe and compliant workplace, safety precautions are paramount. Workplace labels play a crucial role in this regard by providing essential information that helps prevent accidents and mitigate risks. Here are some key safety precautions that must be considered and reflected on workplace labels: 1. **Hazard Identification**: Labels should clearly identify potential hazards associated with the substance or equipment. This includes warning symbols, such as the skull and crossbones for toxic substances or the flame symbol for flammable materials. These visual cues are critical for immediate recognition and response. 2. **Handling Instructions**: Detailed handling instructions are vital to prevent mishaps. For instance, labels on chemicals should specify whether they need to be handled with gloves, goggles, or in a well-ventilated area. Similarly, labels on machinery should indicate proper operating procedures and any specific safety gear required. 3. **Storage Guidelines**: Proper storage is essential to maintain workplace safety. Labels should specify storage conditions such as temperature ranges, proximity to other substances, and whether the item should be stored in a locked cabinet or on a high shelf. 4. **Emergency Procedures**: In case of an accident, timely and appropriate action is crucial. Labels should include information on emergency procedures such as first aid measures, spill response protocols, and contact details for emergency services. 5. **Personal Protective Equipment (PPE)**: The use of PPE is often mandatory when dealing with hazardous materials or operating certain machinery. Labels must specify the type of PPE required, such as respirators, safety glasses, or hard hats. 6. **Training Requirements**: Some tasks require specialized training before they can be safely performed. Labels should indicate if training is necessary and provide resources for obtaining such training. 7. **Regulatory Compliance**: Ensuring compliance with local and international regulations is critical for maintaining a safe workplace. Labels should reference relevant standards and regulations, such as OSHA guidelines in the United States or EU directives in Europe. 8. **Environmental Considerations**: Workplace labels should also consider environmental impacts. For example, labels on chemicals should include information on disposal methods to prevent environmental contamination. By incorporating these safety precautions into workplace labels, employers can significantly reduce the risk of accidents and create a safer working environment for all employees. These labels serve as a constant reminder of potential hazards and the steps needed to mitigate them, thereby fostering a culture of safety and compliance within the workplace.
3. Emergency Procedures
In the context of workplace safety, emergency procedures are a critical component that must be clearly communicated through effective labeling. These procedures are designed to ensure that employees and visitors can respond swiftly and correctly in the event of an emergency, thereby minimizing risks and preventing injuries or fatalities. When creating labels for emergency procedures, it is essential to include several key pieces of information. First, the label should clearly identify the type of emergency it pertains to, such as fire evacuation, chemical spill, or medical emergency. This helps individuals quickly understand the nature of the situation and take appropriate action. Second, the label should provide step-by-step instructions on what to do in case of an emergency. For instance, a fire evacuation label might detail the nearest exit routes, assembly points, and any specific actions required before leaving the area. These instructions should be concise yet comprehensive, using simple language and visual aids like arrows or icons to enhance clarity. Third, contact information for emergency services and key personnel should be prominently displayed. This includes phone numbers for local fire departments, poison control centers, or internal emergency response teams. Additionally, labels should indicate where emergency equipment such as fire extinguishers, first aid kits, or spill response kits are located. Fourth, labels should be placed in strategic locations where they are easily visible and accessible during an emergency. This could include near exits, in high-risk areas like laboratories or warehouses, and at central gathering points like break rooms or reception areas. Finally, it is crucial that emergency procedure labels are regularly reviewed and updated to reflect any changes in protocols or personnel. This ensures that the information remains accurate and relevant over time. Training sessions should also be conducted periodically to familiarize employees with these procedures and ensure they understand their roles in responding to emergencies. By incorporating these elements into workplace labels for emergency procedures, organizations can significantly enhance their safety culture and better protect their workforce from potential hazards. Clear communication through effective labeling is pivotal in preventing confusion during critical moments and ensuring a swift, coordinated response to emergencies.
Regulatory Requirements for Workplace Labels
In the modern workplace, ensuring safety and compliance is paramount. One crucial aspect of maintaining a safe and regulated environment is the proper use of workplace labels. These labels serve as critical communication tools, alerting employees to potential hazards, providing instructions, and adhering to various regulatory standards. This article delves into the essential regulatory requirements for workplace labels, focusing on three key areas: compliance with OSHA standards, adherence to GHS guidelines, and industry-specific regulations. Understanding these requirements is vital for employers to avoid legal repercussions, reduce workplace accidents, and foster a culture of safety. By exploring these topics in depth, we will provide essential information on workplace labels that every organization needs to know to ensure a compliant and safe working environment. Transitioning into the core of this discussion, we will examine each of these critical components to offer a comprehensive guide on regulatory compliance for workplace labels.
1. Compliance with OSHA Standards
Compliance with OSHA (Occupational Safety and Health Administration) standards is a critical aspect of ensuring workplace safety and adhering to regulatory requirements for workplace labels. OSHA mandates that employers provide a safe and healthful work environment, which includes proper labeling of hazardous materials, equipment, and areas. According to OSHA's Hazard Communication Standard (HCS), employers must label containers of hazardous chemicals with specific information to alert workers about potential dangers. This includes the name, address, and phone number of the manufacturer or distributor; the product identifier; and hazard statements, precautionary statements, and pictograms that convey the nature of the hazard. For workplace labels, OSHA requires that they be clear, legible, and in English (though they may also be in other languages if necessary for worker comprehension). The labels must be durable enough to withstand the conditions of the workplace and should be placed in a manner that ensures they are easily visible to workers who may be exposed to the hazards. Additionally, OSHA's standards dictate that labels should include Safety Data Sheets (SDSs) which provide detailed information about the chemical, including its composition, first aid measures, fire-fighting measures, accidental release measures, handling and storage, exposure controls/personal protection, physical and chemical properties, stability and reactivity, toxicological information, ecological information, disposal considerations, transport information, regulatory information, and other relevant data. Compliance with these standards not only helps prevent workplace injuries and illnesses but also ensures that employers avoid legal penalties and fines associated with non-compliance. Regular audits and training programs are essential to ensure that all employees understand the importance of proper labeling and can identify potential hazards. Furthermore, maintaining accurate records of label updates and employee training sessions is crucial for demonstrating compliance during OSHA inspections. In summary, adherence to OSHA standards for workplace labels is paramount for maintaining a safe working environment. By ensuring that all hazardous materials are properly labeled with the required information, employers can significantly reduce the risk of accidents and ensure compliance with regulatory requirements. This proactive approach not only protects workers but also contributes to a culture of safety within the organization.
2. Adherence to GHS Guidelines
Adherence to the Globally Harmonized System of Classification and Labelling of Chemicals (GHS) guidelines is paramount for ensuring the safety and compliance of workplace labels. The GHS, developed by the United Nations, provides a standardized framework for classifying chemicals and communicating their hazards through labels and safety data sheets. This system ensures that chemical hazards are consistently identified and communicated, reducing the risk of accidents and improving workplace safety. When creating workplace labels, adherence to GHS guidelines involves several key elements. First, the label must include the product identifier, which is the name or number used to identify the chemical. This identifier should match the one listed on the safety data sheet (SDS) to avoid confusion. Next, the label must display hazard pictograms—standardized symbols that visually convey the nature of the hazard. These pictograms are crucial as they provide immediate visual cues about the dangers associated with the chemical, even for workers who may not speak the local language. The label should also include signal words such as "Danger" or "Warning," which indicate the level of severity of the hazard. These signal words are used in conjunction with hazard statements that describe the nature of the hazard and any necessary precautions. For example, a label might include a hazard statement like "Toxic if swallowed" or "Causes severe skin burns and eye damage." Additionally, precautionary statements are required to provide advice on how to minimize or prevent adverse effects. Another critical component is the inclusion of supplier information, which includes the name, address, and contact details of the manufacturer or distributor. This ensures that workers can quickly access additional information or seek assistance if needed. Furthermore, GHS labels must be legible and durable enough to withstand the environmental conditions in which they are used. Compliance with GHS guidelines not only enhances workplace safety but also facilitates international trade by providing a common language for chemical hazard communication. Employers must ensure that all chemicals in the workplace are labeled according to these standards to meet regulatory requirements and protect their employees from potential hazards. By adhering strictly to GHS guidelines, organizations can create a safer work environment and avoid legal repercussions associated with non-compliance. Overall, the meticulous application of GHS standards on workplace labels is essential for maintaining a safe and compliant work environment.
3. Industry-Specific Regulations
Industry-specific regulations play a crucial role in ensuring the safety and compliance of workplace labels across various sectors. These regulations are tailored to address the unique hazards and operational requirements of different industries, thereby enhancing workplace safety and reducing the risk of accidents. For instance, in the chemical industry, labels must adhere to the Globally Harmonized System of Classification and Labelling of Chemicals (GHS), which mandates specific pictograms, hazard statements, and precautionary statements to communicate the dangers associated with chemical substances. Similarly, in the healthcare sector, labels on medical devices and equipment must comply with FDA regulations, including clear instructions for use, warnings, and contraindications to ensure patient safety. In the manufacturing sector, OSHA's Hazard Communication Standard (HCS) dictates that labels on hazardous materials include information such as the product identifier, signal words, hazard statements, and precautionary statements. This standard ensures that workers are adequately informed about the risks associated with the materials they handle. Additionally, in industries involving electrical equipment, labels must meet the standards set by organizations like UL (Underwriters Laboratories) or ETL (Intertek), which verify that the equipment complies with safety standards for electrical safety. Moreover, industries such as construction and mining have their own set of regulations. For example, the Mine Safety and Health Administration (MSHA) requires specific labeling on equipment and materials used in mining operations to alert workers to potential hazards like explosive gases or falling rocks. Similarly, in construction, labels on heavy machinery and tools must comply with OSHA standards to prevent accidents and ensure that workers are aware of operational risks. These industry-specific regulations not only help in maintaining a safe working environment but also facilitate compliance with broader regulatory frameworks. By adhering to these standards, businesses can avoid legal penalties, reduce liability, and foster a culture of safety within their organizations. Ultimately, the precision and clarity of industry-specific regulations on workplace labels are critical in protecting workers' health and safety while ensuring operational efficiency and compliance.
Best Practices for Creating Effective Workplace Labels
In today's fast-paced and safety-conscious work environments, effective workplace labels are crucial for ensuring clarity, safety, and efficiency. These labels serve as vital communication tools that guide employees through various tasks, warn them of potential hazards, and maintain organizational standards. To create truly effective workplace labels, several best practices must be adhered to. First, it is essential to use clear and concise language that avoids ambiguity and ensures immediate understanding. Second, incorporating visual elements and symbols can significantly enhance the communicative power of labels, making them more accessible and intuitive. Finally, regular updates and maintenance are necessary to keep labels relevant and accurate, reflecting any changes in procedures or regulations. By focusing on these key aspects, organizations can develop a robust labeling system that not only complies with industry standards but also fosters a safer and more productive work environment. For essential information on workplace labels, continue reading to explore these best practices in depth.
1. Clear and Concise Language
When it comes to creating effective workplace labels, one of the most critical best practices is the use of clear and concise language. This principle is paramount because it ensures that the information conveyed is easily understood by all employees, regardless of their educational background or native language. Clear language avoids ambiguity and confusion, which are potential hazards in a fast-paced work environment. For instance, instead of using complex jargon or technical terms that might be unfamiliar to some workers, labels should employ straightforward vocabulary that clearly communicates the intended message. Conciseness is equally important as it prevents information overload. Labels should focus on the essential details necessary for safety and efficiency, omitting any extraneous information that could distract from the main point. For example, a label indicating a hazardous material should clearly state the name of the substance, its associated risks, and any necessary safety precautions without including unnecessary details. This approach not only saves time but also enhances comprehension and adherence to safety protocols. Moreover, clear and concise language helps in maintaining consistency across all labels within the workplace. Consistency in terminology and formatting makes it easier for employees to quickly identify and understand different types of labels, whether they are warning signs, instructional labels, or identification tags. This uniformity also aids in training new employees who need to quickly grasp the labeling system to perform their duties safely and effectively. In addition to these benefits, using clear and concise language on workplace labels is often mandated by regulatory standards. Organizations such as OSHA (Occupational Safety and Health Administration) require that safety signs and labels be easily readable and understandable to ensure compliance with safety regulations. Non-compliance can result in fines and legal repercussions, making it imperative for businesses to adhere strictly to these guidelines. In summary, incorporating clear and concise language into workplace labels is a fundamental best practice that enhances safety, efficiency, and compliance. By avoiding complex terminology and focusing on essential information, businesses can create an environment where employees can quickly understand critical information, reducing the risk of accidents and improving overall productivity. This approach not only aligns with regulatory requirements but also fosters a culture of clarity and safety within the organization.
2. Visual Elements and Symbols
When it comes to creating effective workplace labels, the strategic use of visual elements and symbols is crucial for enhancing clarity, safety, and compliance. Visual elements such as colors, shapes, and icons can significantly improve the readability and impact of labels, especially in environments where workers may not have the luxury of time to read detailed text. For instance, using standardized colors like red for danger, yellow for caution, and green for safety can instantly convey critical information. Shapes like triangles for warning signs or circles for mandatory actions also help in quick recognition. Symbols are another vital component that can be universally understood, transcending language barriers. The International Organization for Standardization (ISO) and the Occupational Safety and Health Administration (OSHA) provide guidelines on the use of specific symbols that are recognized globally. For example, a pictogram of a person wearing protective gear can clearly indicate the need for personal protective equipment (PPE) without requiring any text. Similarly, symbols indicating hazardous materials or electrical risks can be immediately recognized by workers, reducing the risk of accidents. Incorporating these visual elements and symbols into workplace labels not only enhances their effectiveness but also ensures compliance with regulatory standards. It is essential to ensure that these elements are used consistently throughout the workplace to avoid confusion. Consistency in design helps workers quickly understand the message being conveyed, whether it is related to safety procedures, emergency exits, or operational instructions. Moreover, the use of high-contrast colors and clear graphics ensures that labels remain legible even in low-light conditions or from a distance. This is particularly important in industrial settings where visibility might be compromised due to environmental factors. By combining clear text with appropriate visual elements and symbols, workplace labels become more engaging and informative, contributing significantly to a safer and more efficient work environment. In summary, integrating well-designed visual elements and symbols into workplace labels is a best practice that enhances their effectiveness by improving readability, safety awareness, and compliance with regulatory standards. By adhering to standardized guidelines and ensuring consistency in design, organizations can create labels that are both informative and engaging, ultimately contributing to a safer and more productive workplace.
3. Regular Updates and Maintenance
Regular updates and maintenance are crucial components of best practices for creating effective workplace labels. Ensuring that labels remain accurate, relevant, and compliant with evolving regulations is essential for maintaining a safe and efficient work environment. Here are several key aspects to consider: 1. **Regulatory Compliance**: Workplace labels must adhere to the latest standards and regulations set by governing bodies such as OSHA (Occupational Safety and Health Administration) in the United States or similar organizations in other countries. Regularly reviewing updates to these standards ensures that your labels comply with current requirements, reducing the risk of fines and penalties. 2. **Label Content Review**: Periodically review the content of your labels to ensure they accurately reflect current processes, hazards, and safety protocols. This includes updating chemical labels to reflect changes in formulations or new hazards identified, as well as revising instructional labels to align with updated procedures. 3. **Visual Inspection**: Conduct regular visual inspections of labels to check for wear, tear, and damage. Labels that are faded, torn, or otherwise compromised can be ineffective and may not communicate critical information clearly. Replace damaged labels promptly to maintain visibility and readability. 4. **Employee Training**: Ensure that employees are trained on any changes made to labels. This includes educating them on new hazards, updated procedures, and any modifications to existing labels. Training sessions should be conducted regularly to keep employees informed and aware of the latest information. 5. **Documentation**: Maintain detailed records of label updates, including the date of the update, the reason for the change, and who performed the update. This documentation helps in tracking compliance and provides a historical record of changes made over time. 6. **Technology Integration**: Leverage technology such as label management software to streamline the process of creating, updating, and tracking labels. These tools can automate many tasks associated with label maintenance, ensuring consistency across all labels and reducing human error. By incorporating these practices into your workplace labeling strategy, you can ensure that your labels remain effective tools for communication and safety. Regular updates and maintenance not only enhance compliance but also contribute to a safer, more efficient workplace where employees are well-informed about potential hazards and necessary procedures. This proactive approach underscores the importance of continuous improvement in workplace safety protocols.