What Is Pig Iron

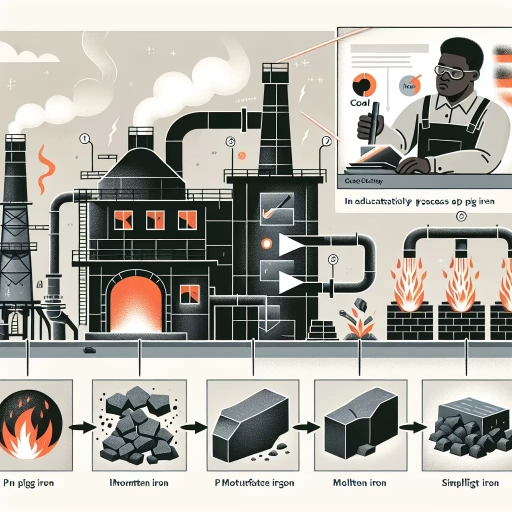
Pig iron is a fundamental material in the steel industry, playing a crucial role in the production of various steel products. This article delves into the essence of pig iron, exploring its definition and composition, production process, and diverse uses and applications. Understanding what pig iron is begins with its definition and composition, which involves a specific mix of iron, carbon, and other elements. The production process of pig iron is complex and involves several stages, from raw material extraction to smelting. Once produced, pig iron finds its way into numerous applications, ranging from steel manufacturing to cast iron products. By examining these aspects, we gain a comprehensive insight into the significance and versatility of pig iron. Let's start by defining and understanding the composition of pig iron, which sets the foundation for its subsequent production and widespread use.
Definition and Composition of Pig Iron
Pig iron, a fundamental product in the iron and steel industry, is characterized by its unique definition and composition. To fully understand pig iron, it is essential to delve into its chemical composition, physical properties, and historical context. The chemical composition of pig iron reveals its primary constituents, including iron, carbon, silicon, manganese, and various impurities. This breakdown is crucial for determining its suitability for further processing into steel or cast iron. Additionally, the physical properties of pig iron, such as its density and melting point, play a significant role in its handling and use in manufacturing processes. Historically, pig iron has been a cornerstone of industrial development, with its production dating back to ancient times and evolving significantly over the centuries. By examining these aspects, we gain a comprehensive understanding of pig iron's role in modern metallurgy. Let us begin by exploring the chemical composition of pig iron, which forms the basis of its utility and versatility in industrial applications.
Chemical Composition
Chemical composition is a critical aspect of understanding pig iron, a primary product of smelting iron ore. Pig iron is predominantly composed of iron, but it also contains significant amounts of carbon and smaller quantities of other elements. The iron content typically ranges from 85% to 90%, with the remainder consisting mainly of carbon (2.5% to 5%), silicon (1% to 3%), manganese (0.5% to 1.5%), phosphorus (0.1% to 2%), and sulfur (0.02% to 0.1%). These impurities arise from the smelting process and the raw materials used. Carbon, in particular, is a key component that affects the properties and uses of pig iron; high-carbon pig iron is more brittle and less ductile compared to low-carbon varieties. Silicon and manganese are also significant as they influence the melting point and strength of the iron. Phosphorus and sulfur, while present in smaller amounts, can have detrimental effects on the mechanical properties of pig iron, making it less desirable for certain applications. Understanding the chemical composition of pig iron is essential for determining its suitability for further processing into steel or other iron alloys, as well as for predicting its behavior during refining and manufacturing processes. This knowledge allows producers to tailor the composition to meet specific industrial needs, ensuring the production of high-quality materials for various applications.
Physical Properties
Pig iron, a crucial intermediate product in the production of steel, exhibits several distinct physical properties that are essential for its processing and application. **Density** is one of the primary physical properties, with pig iron typically having a density ranging from 7.9 to 8.1 g/cm³, which is slightly lower than that of pure iron due to the presence of impurities such as carbon, silicon, and manganese. **Melting Point** is another critical property; pig iron has a melting point around 1100-1200°C, which is lower than pure iron's melting point due to the eutectic effect of its impurities. This lower melting point makes pig iron easier to handle and process in furnaces. The **Appearance** of pig iron is often described as a dull gray or black solid with a rough, irregular surface. When freshly cast, it may have a metallic luster, but this quickly dulls due to oxidation. **Hardness** varies depending on the specific composition; however, pig iron is generally quite hard and brittle, making it unsuitable for direct use in structural applications. The **Thermal Conductivity** of pig iron is relatively low compared to pure metals, which affects its heat transfer properties during processing. In terms of **Chemical Composition**, pig iron contains significant amounts of carbon (typically between 3.5% and 4.5%), along with smaller percentages of silicon (1-3%), manganese (0.5-1.5%), phosphorus (0.1-1%), and sulfur (0.02-0.1%). These impurities influence not only the physical properties but also the mechanical properties and potential uses of pig iron. For instance, high carbon content contributes to its brittleness and hardness. Understanding these physical properties is vital for optimizing the production process and subsequent refining steps to produce steel or other ferrous alloys. For example, knowing the melting point helps in controlling furnace temperatures during smelting and refining processes. Similarly, recognizing the density and hardness allows for better handling and storage practices. In summary, the physical properties of pig iron—such as density, melting point, appearance, hardness, thermal conductivity, and chemical composition—are fundamental to its production, processing, and eventual transformation into more versatile materials like steel. These properties dictate how pig iron can be efficiently managed throughout various industrial processes to achieve desired outcomes in metallurgy.
Historical Context
Historical Context of Pig Iron is deeply intertwined with the evolution of iron production and metallurgy. The term "pig iron" itself originates from the early method of casting molten iron into a series of connected troughs, resembling a sow with piglets, hence the name. This process dates back to ancient times, but it was during the Industrial Revolution that pig iron production became a cornerstone of modern industry. In ancient civilizations such as Egypt, Greece, and Rome, iron was first extracted from ores through primitive smelting techniques. However, it was not until the Middle Ages that significant advancements in iron production were made. The introduction of the blast furnace in Europe during the 14th century marked a pivotal moment, allowing for larger quantities of iron to be produced more efficiently. The real surge in pig iron production came with the advent of the Industrial Revolution in the late 18th and early 19th centuries. Innovations like Abraham Darby's use of coke instead of charcoal in blast furnaces in 1709 significantly reduced costs and increased output. This led to widespread adoption and expansion of iron production facilities across Europe and North America. Pig iron became a crucial raw material for further processing into wrought iron and steel, which were essential for constructing machinery, railways, ships, and buildings. The Bessemer process, developed by Henry Bessemer in 1855, revolutionized steel production by allowing mass production of steel from pig iron, further solidifying its importance. Throughout the 20th century, advancements in metallurgy continued to refine pig iron production processes. Modern blast furnaces are more efficient and environmentally friendly than their predecessors, utilizing better materials and technologies to minimize waste and emissions. Today, pig iron remains a vital component in the global steel industry, with major producers located in countries like China, India, and Brazil. Its historical context underscores its role as a foundational material that has driven technological progress and economic growth over centuries. Understanding this history provides a deeper appreciation for the significance of pig iron in shaping modern society and industry.
Production Process of Pig Iron
The production of pig iron is a complex and multifaceted process that involves several critical components. At the heart of this process is the blast furnace operation, which is the primary method for producing pig iron. However, to fully understand the production process, it is essential to consider the raw materials used and the significant energy requirements involved. Raw materials such as iron ore, coke, and limestone are meticulously selected and prepared to ensure optimal results. The energy requirements for this process are substantial, as high temperatures and continuous operation are necessary to maintain the chemical reactions within the blast furnace. By examining these elements—raw materials, energy requirements, and blast furnace operation—we can gain a comprehensive understanding of how pig iron is produced. This article will delve into each of these aspects, starting with the intricacies of blast furnace operation, which sets the stage for the entire production process.
Blast Furnace Operation
Blast furnace operation is a critical component of the pig iron production process. The blast furnace, a large, vertical shaft furnace, is where iron ore, coke, and limestone are combined and subjected to high temperatures to produce pig iron. Here’s a detailed overview of the operation: 1. **Raw Materials**: The process begins with the preparation of raw materials—iron ore, coke (a form of carbon), and limestone. These materials are loaded into the top of the blast furnace through a charging system. 2. **Heating and Reduction**: Air is blown into the bottom of the furnace, known as the tuyeres, which ignites the coke. This combustion process generates a high-temperature gas that reduces the iron oxides in the ore to metallic iron. The limestone decomposes into calcium oxide and carbon dioxide, which helps remove impurities from the iron. 3. **Zone Formation**: Inside the blast furnace, different zones are formed due to varying temperatures and chemical reactions. The top zone is where raw materials are loaded; the middle zone is where combustion occurs; and the bottom zone, or hearth, is where molten pig iron and slag accumulate. 4. **Slag Formation**: The calcium oxide from limestone reacts with impurities like silica to form slag, which floats on top of the molten pig iron due to its lower density. This slag is periodically tapped off and removed. 5. **Tapping**: Once the pig iron has accumulated at the bottom of the furnace, it is tapped off through a taphole. The molten pig iron is then transported to a ladle for further processing or casting. 6. **Continuous Operation**: Blast furnaces operate continuously, with raw materials being added at the top and products being removed from the bottom. This continuous cycle ensures efficient production and minimizes downtime. 7. **Energy Efficiency**: Modern blast furnaces incorporate various technologies to improve energy efficiency, such as using pulverized coal injection (PCI) to reduce coke consumption and employing advanced cooling systems to manage heat. 8. **Environmental Considerations**: Efforts are made to minimize environmental impact through dust collection systems, gas cleaning, and recycling of by-products like slag and dust. In summary, blast furnace operation involves a complex interplay of chemical reactions, thermal processes, and material handling to convert raw materials into pig iron efficiently and sustainably. This process is fundamental to the production of pig iron, which serves as a primary feedstock for steel production.
Raw Materials Used
In the production process of pig iron, the selection and quality of raw materials are crucial for achieving the desired chemical composition and physical properties. The primary raw materials used include iron ore, coke, and limestone. **Iron ore**, which can be hematite (Fe₂O₃), magnetite (Fe₃O₄), or goethite (FeO(OH)), serves as the primary source of iron. The type and grade of iron ore significantly influence the efficiency of the smelting process and the quality of the pig iron produced. **Coke**, derived from coal through a process known as coking, acts as a reducing agent and fuel in the blast furnace. It is essential for providing the necessary carbon content to reduce iron oxides to metallic iron. High-quality coke must have a high carbon content, low sulfur content, and appropriate physical properties to ensure efficient combustion and reduction reactions. **Limestone**, primarily composed of calcium carbonate (CaCO₃), is added to the blast furnace to act as a flux. It helps in removing impurities such as silica (SiO₂) by forming a slag that can be easily separated from the molten pig iron. The purity and reactivity of limestone are critical for maintaining the optimal chemical environment within the blast furnace. Additionally, other minor raw materials may be used depending on the specific requirements of the production process. These can include dolomite, which also acts as a flux, and ferroalloys or scrap metal, which can be added to adjust the chemical composition of the pig iron. The precise control over these raw materials ensures that the pig iron produced meets the required specifications for further processing into steel or other iron products. The quality and consistency of these raw materials directly impact the efficiency of the production process, energy consumption, and ultimately, the quality of the pig iron. Therefore, careful selection and monitoring of these inputs are essential for maintaining high standards in pig iron production.
Energy Requirements
The production of pig iron, a crucial step in the steelmaking process, is highly energy-intensive. The energy requirements for this process are significant due to the high temperatures and complex chemical reactions involved. Here, we delve into the specifics of these energy demands. **Energy Sources and Consumption:** 1. **Coke and Coal:** The primary energy source in pig iron production is coke, which is derived from coal. Coke serves as both a fuel and a reducing agent in the blast furnace, where it reacts with iron ore to produce pig iron. The combustion of coke releases carbon monoxide, which reduces the iron oxides in the ore to metallic iron. Additionally, coal can be used as an auxiliary fuel to enhance the efficiency of the process. 2. **Natural Gas and Oil:** In some modern blast furnaces, natural gas or oil may be used as supplementary fuels to reduce coke consumption and lower emissions. These fuels help maintain the high temperatures required for the reduction reactions. **Process-Specific Energy Needs:** 1. **Blast Furnace Operations:** The blast furnace is the heart of pig iron production, operating at temperatures around 2000°C (3632°F). Maintaining these temperatures requires continuous fuel input, primarily from coke but also from auxiliary fuels if used. 2. **Raw Material Preparation:** Before feeding into the blast furnace, raw materials such as iron ore, coke, and limestone must be prepared. This involves crushing, grinding, and sometimes pelletizing or sintering, all of which consume additional energy. 3. **Air Blowing:** The blast furnace process involves blowing hot air into the furnace to enhance combustion and reaction rates. This requires significant electrical energy to power blowers and compressors. **Efficiency and Optimization:** 1. **Heat Recovery Systems:** Modern pig iron production often incorporates heat recovery systems to capture waste heat from the blast furnace and use it for other processes within the plant, such as preheating raw materials or generating steam for power. 2. **Energy-Efficient Technologies:** Advances in technology have led to more efficient blast furnace designs and operational practices. For example, using pulverized coal injection (PCI) can reduce coke consumption and lower overall energy requirements. 3. **Sustainability Initiatives:** There is a growing focus on reducing the carbon footprint of pig iron production through the use of alternative fuels like bio-coal or hydrogen, which could significantly alter the energy landscape in the future. **Environmental Considerations:** 1. **Emissions Control:** The energy-intensive nature of pig iron production also means that it is a significant source of greenhouse gas emissions. Implementing efficient combustion practices and using cleaner fuels are critical for mitigating these environmental impacts. 2. **Regulatory Compliance:** Producers must comply with stringent environmental regulations, which often drive the adoption of more energy-efficient and cleaner production technologies. In summary, the production of pig iron is an energy-hungry process that relies heavily on coke and other fuels to achieve the high temperatures necessary for iron ore reduction. While traditional methods dominate, ongoing efforts to improve efficiency and adopt cleaner technologies aim to reduce the overall energy requirements and environmental footprint of this essential industrial process.
Uses and Applications of Pig Iron
Pig iron, a key product of the iron ore smelting process, is a versatile material with a wide range of applications across various industries. Its primary use is in steel production, where it serves as a crucial raw material. However, pig iron's utility extends beyond this core application. It is also a vital component in the casting and foundry industry, where it is used to produce cast iron products such as engine blocks, pipes, and machinery parts. Additionally, pig iron finds other industrial uses, including in the manufacture of ferroalloys, which are essential for enhancing the properties of steel, and in the production of ductile iron, known for its high strength and durability. Understanding these diverse applications highlights the significance of pig iron in modern manufacturing. Let's delve into its role in steel production, a sector where pig iron plays an indispensable part.
Steel Production
Steel production is a complex and multifaceted process that transforms pig iron, a primary product of iron ore smelting, into one of the most versatile and widely used metals in the world. The journey from pig iron to steel involves several critical steps. First, pig iron is refined in a blast furnace or electric arc furnace to remove impurities such as carbon, silicon, and manganese. This refining process reduces the carbon content from around 3-5% in pig iron to less than 2%, which is more suitable for steel production. The next step involves alloying, where elements like chromium, nickel, and molybdenum are added to enhance the mechanical properties of the steel, such as strength, corrosion resistance, and ductility. The molten steel is then cast into various forms like slabs, blooms, or billets using continuous casting machines. These cast products are further processed through rolling, forging, or machining to produce the final steel products. Steel production also includes heat treatment processes like annealing, hardening, and tempering to achieve specific microstructures and properties. The end result is a wide range of steel grades with diverse applications in construction, automotive manufacturing, consumer goods, energy infrastructure, and more. For instance, high-strength steel is used in building skyscrapers and bridges, while stainless steel is preferred in kitchen utensils and medical equipment due to its corrosion resistance. The adaptability and strength of steel make it an indispensable material in modern society, underscoring the importance of efficient and innovative steel production techniques.
Casting and Foundry Industry
The casting and foundry industry is a cornerstone of modern manufacturing, leveraging pig iron as a primary raw material to produce a wide array of critical components. Pig iron, with its high carbon content, is ideal for casting due to its fluidity and ability to form complex shapes. In the foundry process, pig iron is melted and alloyed with other metals such as silicon, manganese, and carbon to create various types of cast iron. These alloys are then poured into molds to form parts ranging from engine blocks and cylinder heads in the automotive sector to pipes and fittings in civil engineering projects. The versatility of pig iron in casting allows for the production of components with specific properties tailored to their intended use. For instance, grey cast iron, which contains graphite flakes, is used for engine blocks and gearboxes due to its excellent vibration damping and thermal conductivity. On the other hand, ductile cast iron, characterized by its spherical graphite nodules, is preferred for applications requiring high tensile strength and ductility, such as in heavy machinery and construction equipment. The casting and foundry industry also plays a crucial role in the aerospace sector, where precision and durability are paramount. Here, pig iron is often alloyed with other metals to create high-strength, low-alloy (HSLA) steels used in aircraft components. Additionally, the industry supports the production of consumer goods like cookware and machinery parts, where the unique properties of cast iron—such as heat retention and resistance to wear—make it an indispensable material. Moreover, advancements in casting technologies have enhanced the efficiency and quality of the foundry process. Techniques such as sand casting, investment casting, and die casting allow for precise control over the final product's dimensions and surface finish. This precision is particularly important in industries like healthcare and electronics, where intricate parts require high accuracy. In summary, the casting and foundry industry relies heavily on pig iron to produce a diverse range of products that are integral to various sectors. From automotive and aerospace to consumer goods and infrastructure development, pig iron's unique properties make it an essential component in modern manufacturing processes. The industry's continuous evolution in terms of technology and material science ensures that pig iron remains a vital resource for meeting the complex demands of contemporary engineering.
Other Industrial Uses
Beyond its primary role in steel production, pig iron has a variety of other industrial uses that leverage its unique properties and versatility. One significant application is in the manufacture of cast iron products. Pig iron, with its high carbon content, is ideal for casting processes due to its fluidity and ability to fill intricate molds. This makes it a crucial material for producing cast iron pipes, engine blocks, and other machinery components that require durability and resistance to wear. Additionally, pig iron is used in the production of ductile iron, which combines the strength of steel with the castability of cast iron, making it suitable for applications such as automotive parts and heavy machinery. In the construction industry, pig iron is utilized in the production of grey iron, which is often used for making manhole covers, sewer grates, and other infrastructure components due to its excellent compressive strength and resistance to corrosion. The high carbon content in pig iron also makes it an essential component in the production of ferroalloys like ferromanganese and ferrochromium, which are critical in the manufacture of stainless steel and other alloy steels. Furthermore, pig iron plays a role in the production of abrasives and refractories. The high carbon content in pig iron can be used to produce silicon carbide (SiC), a key material in abrasives and cutting tools. In refractory applications, pig iron is used to produce high-temperature-resistant materials necessary for lining furnaces and other thermal equipment. In the automotive sector, pig iron is used in the manufacture of brake discs and drums due to its high thermal conductivity and ability to absorb and dissipate heat efficiently. This property also makes pig iron useful in the production of cookware and other kitchen utensils that require even heat distribution. Moreover, pig iron is a key ingredient in the production of certain types of cement and concrete. When pig iron is added to cement mixtures, it enhances the strength and durability of the resulting concrete, making it suitable for high-strength applications such as in the construction of bridges and high-rise buildings. Lastly, pig iron has environmental applications as well. It can be used in the treatment of contaminated soils and groundwater by acting as a reducing agent to remove pollutants such as chlorinated solvents and heavy metals. This process leverages the chemical reactivity of pig iron to neutralize harmful substances, making it a valuable tool in environmental remediation efforts. In summary, the diverse industrial uses of pig iron extend far beyond its role in steel production, encompassing various sectors from construction and automotive to environmental remediation, highlighting its multifaceted utility and importance in modern industry.